Sugarcane is one of the main agricultural crops in the world. For example, in Australia, more than 35 million tons of sugarcane are produced annually. Four and a half million tons of raw sugar, one million tons of molasses and 10 million tons of bagasse (a fibrous cane residue) can be produced each year from the sugarcane crops. Modern sugarcane varieties can produce more than 55 tons/hectare of biomass (dry weight).
Biofuel (ethanol, butanol, and acetone-butanol-ethanol blend (ABE)) is produced from edible and non-edible sources in a variety of ways. Ethanol-biofuel is already used as an additive at all Australian fuel stations: 5% ethanol blended with petrol and produced from crop sources.
In general, energy sources can be divided into two categories: dispatchable/continuous sources such as oil, gas, coal, hydropower, and biopower, and non-dispatchable/discontinuous sources such as solar and wind power. The energy extraction pipelines for continuous and discontinuous sources are nearly analogous since source extraction requires capacity orders, build, and installation, which implies a construction delay before the new capacity comes onstream. The main difference is that discontinuous sources require backup power to address the inherent unpredictability issue. Besides, some continuous sources (e.g., fossil fuels) are limited. Hence their reserves diminish gradually. A recent study has developed a novel model for continuous and discontinuous sources described above for all energy sources, including bagasse, to produce certain behaviours over time, from 1990 to 2050
[12].
The energy extraction pipeline includes four stocks and eight flows, as depicted in Figure 3. The stocks are reserves (disregarded for bagasse since they are renewable sources), capital employed, capacity under construction, and energy production capacity. The flows are new discoveries inflow, depletion outflow, CAPEX inflow, depreciation outflow, new capacity order inflow, new capacity start-up inflow and outflow, capacity retirement outflow, and capacity bankruptcy outflow. Reserves are proven reserves that are economically viable. Capital employed is the capacity’s current market value, which depreciates over many years. Capacity under construction is the current capacity under construction that enters service after some delay. Energy production capacity is the capacity used presently.
Figure 3. The energy sources extraction pipeline.
Capex refers to capital expenditure of capacity. New capacity order is the starting rate of building new capacity, which is ordered when there is high confidence in future profitability; the more confidence there is, the more capacity is established. New capacity start-up is the rate at which the new capacity comes onstream, which directly adds to the total capacity. On the other hand, capacity retirement and bankruptcy reflect the total decline of capacity
[12]. Capacity retirement is connected to the project’s lifetime, while capacity bankruptcy is the rate of business closing capacity that is in use. This relates to the profitability of the current capacity. The lower the profitability, the more capacity is closed.
Many variables are included in the extraction pipeline model, such as gross demand, surplus or shortfall, wholesale price, adjustment factor, and total supply cost. Gross demand is subject to the desired production. Surplus is the percentage through which capacity surpasses the market’s demand. When demand surpasses supply, prices are likely to surge. Furthermore, the wholesale price is subject to the supply cost and the energy demand/production rate. The adjustment factor represents the overhead expenses factor, and its value can be anywhere from 1.2 to 1.4, depending on the energy source used. This factor is important in matching demand and supply
[13]. Total supply cost combines the variable and fixed costs of production.
The study established a balance of supply-demand for all energy sources, including wood, wood waste, and bagasse (sugarcane pulp) for biomass, and found that the wholesale price for electricity generated from bagasse will be $71/MWh by 2030 compared to the current Australian wholesale electricity prices which is about $150/MWh for much of 2022
[14].
3. Properties and Chemistry of Sugarcane Bagasse
Bagasse is the fibre left over after the sugars have been extracted from sugarcane. Sugarcane bagasse (
Saccharum officinarum) is another lignin raw material source as an agro-industrial residue. Sugarcane bagasse’s complex chemical composition limits its use as fodder for cattle and ruminants in comparison to other crops such as wheat straw, rice straw, sorghum straw, etc., making sugarcane bagasse a more appealing substrate for industry commercialization
[15].
Bagasse from sugarcane has a chemical composition that is comparable to that of the cell walls of other plants. Every category of plants, including grasses, softwoods, and hardwoods, generates lignin that is primarily composed of a single variety of the phenylpropane repeat unit
[16]. The lignin found in sugarcane bagasse has a higher proportion of H-type lignin, also known as hydroxyphenyl, and as a result, a lower methoxy content than the lignin found in softwood and hardwood
[17]. An earlier study was able to successfully isolate seven lignin fractions by using alkali and alkaline peroxide. This study discovered that all the lignin fractions were of the SGH type, containing only a trace amount of esterified p-coumaric acid and predominantly etherified ferulic acid
[18]. Sugarcane lignin (SL) and lignocellulosic biomass (LB) can only be utilised for a limited number of industrial applications due to the high lignin content.
In order to transform LB into products with added value, it is unavoidable to convert the cellulosic fraction into sugars that are ready to be fermented. Because lignin content is high in the plant cell wall, converting cell wall carbohydrate fractions is difficult. Therefore, retreatment has been employed. Retreatment can assist in producing higher chemical loadings compounds with increased temperatures and reaction times. The high cost of cellulolytic enzymes and the high number of celluloses that are required both contribute to an increase in the overall cost of processing. The elimination of lignin results in an increase in the accessibility of cellulose and greater amenability of cellulose to the carbohydrate framework of the plant cell wall. Sugarcane bagasse (SB) was found to have a significantly lower ash content (2–6%), which is a significant advantage when compared to other agricultural residues such as rice straw (17.5% ash) and wheat straw (11.0% ash). When one ton of sugarcane is processed, approximately 250–280 kilo grammes of bagasse are produced, which results in annual production of approximately 54 million tons of bagasse
[19]. Only a small portion of bagasse is used in the production of pulps, board materials, and composites, whereas a significant amount of it is burned as a low-grade fuel for energy recovery.
4. Pretreatment of Sugarcane Bagasse for Industrial Applications
A suitable pretreatment is required to improve the efficiency of the hydrolysis process by assisting in the removal of lignin or hemicellulose, exposing the cellulosic component. Furthermore, for pretreatment, an efficient cellulolytic enzyme cocktail; the correct enzyme loading amount; specific conditions of hydrolysing; and the right lignocellulosic material nature are essential requirements for achieving maximum hydrolysis produced from lignocellulosic material. It has frequently been reported that using pretreated substrate results in a substantial increase in the amount of lignin removal and hemicellulose depolymerisation into simpler sugars. Some traditional pretreatment methods can be used with pretreatment lignocellulosic sugarcane materials, such as alkaline hydrolysis, biological pretreatment, and acidic pretreatment. Alkaline hydrolysis happens when alkaline substances such as NaOH, Na
2SO
3, NH
4OH, and others are added. Biological pretreatment can aid in the growth of white rot fungus or delignifying microorganisms on lignocellulosic wastes. Acidic pretreatments were carried out by introducing acidic substances (such as HCl, H
2SO
4, H
3PO
4, oxalic acid, formic acid, etc.)
[20]. Pretreatment is required to make the cellulosic material more susceptible to subsequent cellulose-mediated hydrolytic processes.
Figure 4 depicts the many types of pretreatments utilised in lignocellulosic fermentation.
Figure 4. Pretreatment types used for lignocellulosic fermentation.
The pre-treated SB has also been used as an inert support material for fungal biomass in the solid-state fermentation process and as an immobilisation carrier. Both applications take place in the solid state. The mechanistic application of pre-treated SB that has been impregnated with suitable liquid media creates homogenous aerobic conditions throughout the bioreactor, which in turn will produce high product yield titers with relatively high purity after the cultivation cycle completion. The hemicellulose fraction is broken down into several different sugar monomers when lignocellulosic substrates are subjected to acidic hydrolysis (xylose, arabinose, mannose, galactose, and glucose). In order to increase the yield of products that are desirable, it is necessary to remove these inhibitory substances from the hydrolysates before fermentation takes place. Lignin can be removed using pretreatments based on alkali as well as biodelignification techniques, which leave behind cellulose and hemicellulose. A mixture of cellulolytic enzymes can then be used to hydrolyze the material after it has been pre-treated
[18]. This results in the formation of simpler sugars. Exoglycanase, endoglucanase, glucosidase, and other accessory enzymes required for the successful breakdown of polysaccharides found in the cell walls of lignocellulosic materials should be present in sufficient quantities in the cellulolytic cocktail
[21][22].
The genus
Clostridia contains a wide variety of bacteria that produce acetone, butanol, and ethanol, such as
Clostridium butyricum [23],
Clostridium acetobutylicum [24][25],
Clostridium beijerinckii [26], and
Clostridium sporogenes [27]. This process was previously referred to as ABE fermentation. The selection of raw materials that have a high fermentable sugar content and are readily available at a low cost is essential in order to ensure that the production of ethanol and butanol through a biological process is economically viable.
An increasing amount of attention is being paid to agricultural residues like barley straws, corn stoves, and sugarcane bagasse’s as sources of fermentable sugars. These agricultural residues need to be treated using pretreatment and hydrolysis processes to convert carbohydrate polymers long chains found in lignocellulosic materials into monosaccharide sugars. These processes must be carried out for the desired result to be achieved. The method of hydrolysis has a significant impact on the fermentation sugars and their contents, both of which are factors that determine the amount of butanol that can be produced from a given agricultural residue.
5. Types of Anaerobic Bacteria Clostridia (Yeast)
By using a dilute acid solution, the fermentation sugars were extracted from the sugarcane bagasse and hydrolyzed. To evaluate the use of sugarcane bagasse hydrolysate as a substrate, the butanol fermentation was carried out with a bacterial strain chosen from a variety of
Clostridium species, including
Clostridium butyricum (TISTR 1032),
Clostridium sporogenes (TISTR 1452),
Clostridium beijerinckii (TISTR 1461), and
Clostridium acetobutylicum (TISTR 1462). The yield of sugar hydrolysate that was obtained in study
[28] was found to be the highest when compared to that was obtained in the works of several other researchers.
Numerous aspects, such as the type and concentration of the solvent, the temperature, the amount of time required for the reaction, and the enzyme biocatalyst, all play a role in the hydrolysis of various biomass materials. The amount of glucose that could be extracted through enzymatic hydrolysis was significantly higher than the amount that could be extracted through dilute acid hydrolysis. Additionally, a high temperature of 160 °C had a significant impact on the concentration of glucose. The diluted acid solution and low temperature of 121 °C were used
[29] as the hydrolysis method to save money and energy during the production process. The amount of xylose that was obtained was comparable to the amount that was obtained in other studies using dilute acid hydrolysis and a temperature of 121 °C; however, the amount of glucose that was obtained in this study was significantly higher. This high glucose content was accomplished by using H
2SO
4 at a concentration of five percent by volume
[30]. The chemical bonds that hold sugarcane bagasse’s sugars together can be broken down into sugars by increasing the acid concentration in the acid hydrolysis process. This could result in a powerful or comprehensive reaction.
6. Bioethanol Production from Sugarcane
Bioethanol is obtained mostly from agricultural leftovers, and it may be created by the fermentation of sucrose or simple sugars acquired through biomass treatment. It is possible to partition the processes of producing bioethanol into three distinct generations, and each generation is determined by the characteristics of the feedstock that was used initially. In every one of these processes, the lignocellulosic or cellulosic material is first transformed into simple sugars, and only after that is bioethanol produced. The substrate in the first generation is primarily composed of sucrose-containing feedstock grains and starchy materials (such as sugarcane, maise, sugar beet, sweet sorghum, corn, cassava, sweet potato, yam, wheat, barley, and oats), and bioethanol is produced through starch or sugar fermentation
[31][32]. In the second generation, the substrate is primarily composed of lignocellulosic biomass (such as sugarcane bagasse, stover, stems, straw, leaves, and grass), and bioethanol is produced through enzymatic hydrolysis
[33]. In the third generation, the substrates are algae biomasses, and bioethanol is produced through the fermentation of green and blue algae
[34].
Sugarcane is the second most utilised raw material in bioethanol manufacturing. Sugarcane contains 12–17% total sugars by weight and 68–72% moisture (90% sucrose and 10% glucose or fructose). The average extraction efficiency for producing cane juice by crushing is approximately 95%, with cane fibre constituting the remaining solid residue (sugarcane bagasse)
[35]. Cane juice is heated to 110 °C in plants that solely manufacture ethanol, decanted, occasionally concentrated by evaporation, and then fermented to reduce microbial contamination. Like maise, sugarcane has a well-established infrastructure for cultivation, harvesting, and processing. Sugarcane is also considered the most effective raw material resource for bioethanol production: the amount of fossil energy consumed during sugarcane processing is substantially lower than that of corn
[36][37]. Sugarcane is an annual crop whose period of growth ranges from 9 to 24 months. This growing time could be changed depending on several factors such as variety, environmental conditions, and management
[38]. After five to seven ratoon cycles, sugarcane fields are “reformed” or replanted by removing stalks (mechanically or chemically), tilling the soil, and replanting freshly cut sugarcane sprouts. Traditionally, thorough tillage is required for sugarcane soil preparation. In certain areas of Brazil and Australia, full tillage has given way to minimum tillage techniques, in which the soil is only lightly tilled in the planting row. Planting legumes during the reformation phase occasionally increases soil fertility and/or soil physical qualities
[39][40][41][42].
On the other hand, Sugarcane Bagasse (SCB) is primarily composed of lignin (20–30%), cellulose (40–45%), and hemicelluloses (30–35%)
[43]. Because of its lower ash content (1.9%)
[44], SCB offers advantages over high ash containing bagasse, such as rice straw, 14.5%
[45] and wheat straw, 9.2%
[46]. Currently, converting lignocellulosic biomass (such as sugarcane bagasse) into bioethanol entails three critical and interdependent steps: (i) pretreatment of lignocellulosic biomass to depolarise the lignocellulosic matrix, allowing carbohydrate polymers (e.g., cellulose, hemicellulose, and other carbohydrates) to be accessible for enzymatic hydrolysis; (ii) saccharification of pretreated material to liberate fermentable sugars through hydrolases such as cellulases and hemicellulases; and (iii) fermentation of monosaccharide to produce ethanol by using ethanogenic yeast/microorganism
[47].
Figure 5 shows the pathway producing bioethanol from lignocellulosic biomass.
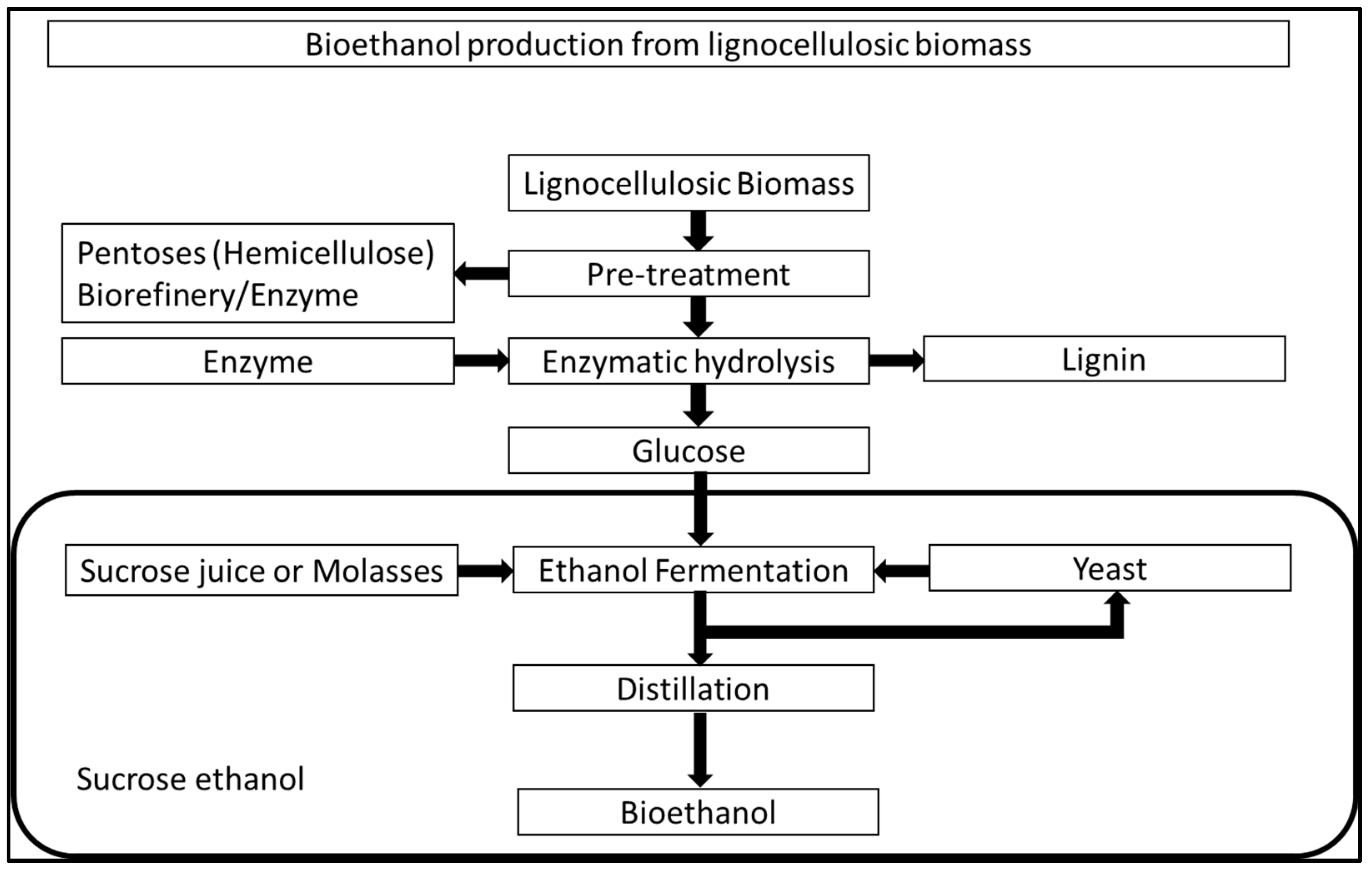
Figure 5. Bioethanol production from lignocellulosic biomass
[34].
7. Conclusion
The currently available technology for producing biofuel from biomass using sugarcane biomass cannot offer a competitive price in relation to the amount of yield produced. Therefore, developments in treatment and genetic engineering and the use of suitable and cheaper yeast to convert sugarcane bagasse into biofuel are of commercial significance for the use of ethanol and ABE. This would result in the commercialisation of ABE as a viable additive for conventional diesel, resulting in lower emissions from diesel engines and less waste.