Electrospun nanofiber-based membranes (ENMs), benefitting from characteristics such as a higher specific surface area, higher porosity, lower thickness, and possession of attracted broad attention, has allowed it to evolve into a promising candidate rapidly. According to the roles of electrospun nanofiber layers, NMs can be divided into two categories: (i) nanofiber layer serving as a selective layer, (ii) nanofiber layer serving as supporting substrate.
1. Introduction
The rapid expansion of nanotechnology, such as nanomaterials with extraordinary physical and chemical properties, could assist in satisfying the demand for high-quality purification applications. The nanomaterials include zero-dimensional nanoparticles (all three dimensions are in the range of 1–100 nm, for example, quantum dots), one-dimensional materials (one of the dimensions is on a nanometer scale, examples include nanofibers, nanorods, nanotubes, nanowires), and two-dimensional nanosheets (all three dimensions are >100 nm) [1]. Among these, nanofibers, especially synthesized by electrospinning for a predominant electroactive phase, contribute extraordinary features to nanotechnology’s development [2]. Nanofibers are unique among the numerous types of nanomaterials due to their remarkably high specific surface area and porosity. In general, there are many techniques to produce nanofibers, such as bicomponent extrusion, electrospinning, melt blowing, phase separation, centrifugal spinning, drawing, self-assembly, and template synthesis (Table 1). The electrospinning (ES) technique is a cost-effective, simple and economic strategy for nanofiber production with the most control over parameters of nanofibers varying in size, shape, and doping [3]. Relatively symmetrical and homogeneous-structured nanofiber scaffolds can be developed alongside the production of membranes with excellent performance in water purification operations [4]. Membranes mainly fabricated via a sole or integrated ES technique, typically known as electrospun nanofiber-based membranes (ENMs), consist of nanofiber layers with overlapped nanofibers of diameters ranging from several nanometers to a few microns. ENMs have been regarded as one of the most promising orientations for energy storage, health care, electricity generation, biotechnology, and environmental applications, benefiting from these features, especially water purification and desalination [5].
Table 1. Comparison of different fabrication techniques of fibers.
The efficiency of a membrane-based desalination system, particularly its permeability (water flux) and separation efficiency (solute rejection), depend considerably on the membrane properties and performance [18]. For increasingly enhanced separation requirements to be met, the ENMs require constant improvements and optimization for increased efficiency in both pressure-driven and thermal-driven processes with less consumption. Few studies have focused on the production and application of ENMs, with an eye to functionalized nanofibers for specific applications. As shown in Figure 1a, ENMs can be divided into the following two categories according to the roles of electrospun nanofiber layers: (i) nanofiber layer serving as a selective layer, (ii) nanofiber layer serving as supporting substrate. The synthesis method of ENMs can be classified as single polymers, mixed polymers, polymers with nanofiber, and surface modifications. ENMs mainly have the following application fields: microfiltration, ultrafiltration, nanofiltration, reverse osmosis, forward osmosis, pervaporation, membrane distillation, etc. Regarding applications in water purification and desalination, the position of the nanofiber layer in ENMs have suggested that there are two types of ENMs, with the nanofiber layer serving as a selective layer and a support substrate, respectively (Figure 1b,c).
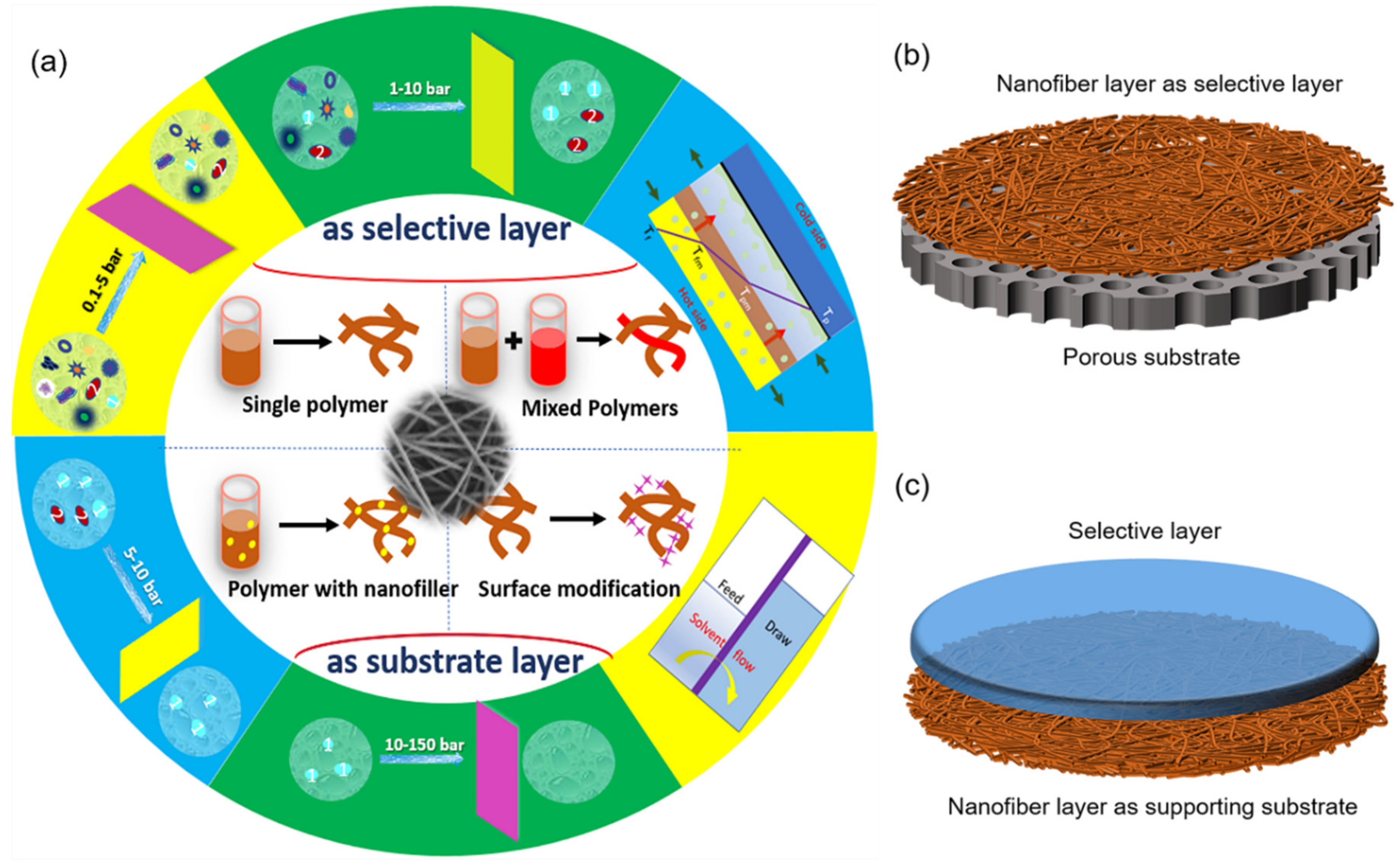
Figure 1. (a) Preparation and application of ENMs; (b,c) ENMs schematic images of two roles of nanofiber layers: served as selective layer (b) and supporting substrate (c).
2. Electrospinning Technique and Process
2.1. Electrospinning Technique
ES technology has the advantages of simple manufacturing devices, low spinning costs, a wide range of spinnable materials, and precise and controllable processes
[19][20]. Because of these advantages, ES technology has become one of the universal methods for the effective preparation of nanofiber materials. The electrospun nanofibers bear several remarkable properties such as a small diameter, large surface area, high aspect ratio, unique physiochemical properties, and flexibility
[21]. The ES technique device consists of a high-voltage supply device, a syringe tube with small diameter needles, and a metal collecting plate/roller (
Figure 2). The temperature and humidity of the environment should be kept stable. During the ES process, a superior high voltage electrical force is utilized on the polymer-solvent system (polymer solution or polymer melt). After that, the polymer solution is injected from the spinneret by overcoming surface tension of the solution under a superior high electric field force. A polymer jet is principally affected by surface tension and electrostatic force during the stretching process. In this process, the stretching of fibers is affected by various forces such as surface tension, Coulomb repulsion force, electrostatic force viscoelasticity, gravity, and air resistance
[22]. Subsequently, collectors collect a strip of fiber in a specific dimension when the jet is stretched, and the solvent evaporates through the air. During the ES process, the bending instability results in the high stretching of the fiber.
Figure 2. Schematic representation of the ES process. Reprinted with permission from Ref.
[23]. 2020, Elsevier.
2.2. Effects of Electrospinning Parameters
Nanofibers with variable dimensions or morphologies can be manufactured under different ES conditions [24][25]. The polymer fiber diameter and morphology are affected by both the polymeric solution properties as well as the process parameters. The main factors influencing the polymer solution properties include polymer weight and architecture, solution concentration, polymer viscosity, solution conductivity, and surface tension and solvent. Operating parameters include electric potential, polymer solution flow rate, the distance between the capillary and collector, needle gauge, collector, ambient temperature, humidity, and air velocity in the chamber.
3. ENMs with a Nanofiber Layer as the Selective Layer
3.1. Conventional ENMs
Polyacrylonitrile (PAN)
[26], polysulfone (PSF), polyvinylidene fluoride (PVDF)
[27], polyurethane (PU)
[28], polyvinyl alcohol (PVA)
[29], polyethersulfone (PES)
[30], fluoropolymer, poly(vinylidene fluoride-co-hexafluoropropylene) (PVDF-co-HFP, PH), polystyrene (PS)
[31], and polydimethylsiloxane (PDMS)
[32] are favored for their adjustable fiber diameters, impressive membrane porosities and uniform pore sizes
[33]. It is a universal preference that these polymers be electrospun into ENMs with the pore size range of 0.1–1.0 μm, which significantly affects the removal of particles exceeding 1.0 μm. These membranes can be regulated under different operating conditions to enhance the performance of ENMs.
The selection of polymers will affect the parameters, such as surface tension, electrical conductivity, and viscosity of the ES solution
[34]. ES needs to overcome the solution surface tension for spinning, and reducing the surface tension facilitates the formation of fibers without beads. Too low a viscosity may lead to the interruption of polymer filaments and polymer droplets, while too high a viscosity makes it difficult to extrude the polymer. The polymer solution conductivity affects the fiber diameter. The choosing of the appropriate one or mix of the polymer solutions significantly affects the properties of ENMs.
ENMs with different properties are required for various applications, and ENMs prepared from a single polymer make it difficult to meet the demand. In terms of co-blending polymers, ES is a technique to combine polymers with different properties into one reservoir, electrospun together to improve the performance of the membranes
[35]. The nanofibers made of a polymer blend can also give rise to new applications due to the integration of functions originating from individual components. Silk (SF) has excellent mechanical and binding resistance properties. Poly(ethyleneimine) (PEI) is a hyperbranched cationic polymer which was shown earlier to improve the antibacterial activity of resins. Ugur et al.
[36] combined SF, PEI, and PMMA with ES technology to successfully prepare antibacterial- and mechanically enhanced nanofiber membranes.
3.2. Mixed Matrix ENMs
3.2.1. Inorganic Metal Incorporation
Inorganic metal modification consists of metal nanoparticles (Ag, Fe) and metal oxide materials (Al
2O
3, TiO
2, MOFs)
[37]. Morphologies and structures of the composite mixed matrix ENMs are altered, hence varying from that of the original. This generates excellent water purification efficiency in heavy metal ions adsorption, organic dyes removal, antibacterial applications, oil–water separation, and some membrane distillation processes.
Ag nanoparticles of dimensions ranging from several nanometers to tens of nanometers, with their excellent properties of killing and inhibiting bacteria and microorganisms
[38], have sparked great interest in mixed matrix electrospun selective layer formation in membrane production for water desalination
[39]. However, when directly added to the polymer solution, Ag nanoparticles will agglomerate, and hardly disperse on the electrospun nanofibers. Therefore, the reduction reaction between Ag
+ and Ag nanoparticles is selected to solve this problem.
3.2.2. Inorganic Nonmetal Incorporation
Inorganic nonmetallic nanomaterials such as SiO
2 [40], carbon nanotubes (CNTs), zeolite
[41][42], graphene, and graphene oxide (GO) were incorporated into the polymeric solution for functional improvements.
Silica nanoparticles added to the polymer solution have the ability to improve the mechanical strength of nanofibers, increase the glass transition temperature of ENMs, and prevent the appearance of beads throughout the ES process
[43][44]. Hou et al.
[45] dissolved the polyvinylidene fluoride-co-hexafluropropylene (PVDF-HFP) in a cosolvent of DMF/acetone, and added SiO
2 emulsion into the reagent to obtain PVDF-HFP/SiO
2 ENMs. With the mass ratio of SiO
2 increasing, though the membrane porosity decreased gradually, the pores shrunk while the thickness of membranes was enhanced, resulting in the improvement of salt rejection efficiency. The WCA was over 150°, owing to the rougher hydrophobic surface. The highest permeate flux was up to 48.6 kg/m
2h and the rejection of NaCl was maintained at nearly 100% after 240 h of continuous operation of the membrane distillation process.
3.2.3. Organic Incorporation
In contrast to various inorganic additives, there are fewer applications of organic additives due to various rigorous conditionalities, which, in general, are covalent organic frameworks (COFs), metal organic frameworks (MOFs), poly-cyclodextrin
[46][47], β-cyclodextrin, and their modifiers
[48].
MOFs are a class of nanoporous materials composed of central metal clusters or ions and organic ligands, which possess a large specific surface area, a high porosity, a low thermal conductivity, and ordered nanopores
[49]. In recent years, MOFs have attracted significant interest for their role as nanofillers in pressure-driven liquid separations to drastically improve separation performances by providing additional water channels
[50].
COFs are a class of robust two- or three-dimensional extended network materials known for their artistic structures and for their potential for a wide range of applications
[51][52].
3.3. Surface Modification
The internal structure of the membrane, created by the random accumulation of nanofibers as well as surface modification, can affect both pore size and liquid entry pressure. A surge of composite ENMs with a modified nanofiber layer via organic grafting of additional functional groups has attracted great interest to achieve a higher separation performance.
Wang et al.
[53] grafted hyperbranched polyethylenimine (HPEI) and glycidol onto PAA ENMs to form PAA/HPEI-glycidol ENMs via the reaction between the carboxylic group on PAA with the amine groups in HPEI, followed by the ring-opening of amine terminal groups with glycidol. The formation of the complexation compound formed boron and hydroxyl groups in glycidol, which vastly improved boron adsorption. The maximum boron adsorption capacity of the optimized ENMs achieved up to 5.7 mmol/g and remained approximately 94% after 10 operation cycles.
4. ENMs with Nanofiber Layer as Supporting Substrates
4.1. With the Selective Layer via Secondary-Electrospinning
Dual-layer hydrophobic composite ENMs with two kinds of nanofiber layers were superior candidates in the water desalination process, especially membrane distillation, owing to its unique advantages of well-connected inner pores and low mass transfer resistance. It was reported that dual-layer ENMs, generally composed of hydrophobic/hydrophilic or superhydrophobic/less hydrophobic layers, exhibit better performance in membrane distillation than single-layer hydrophobic ENMs of the same thickness
[54][55]. Besides, using a hydrophobic/hydrophilic dual-layer hollow fiber membrane for long-term DCMD operation demonstrated fewer pore wetting issues
[56][57].
4.2. With the Selective Layer via Inorganic Deposition
ENMs obtained with the selective layer via inorganic deposition from the nanofiber layer can usually enhance membranes’ thermodynamic and chemical stability. Properties of such hierarchical membranes are strongly affected by the selectivity of nanomaterials, which are commonly applied to heavy metals, some toxic ions adsorption and oil–water separation
[58].
4.3. With the Selective Layer via Polymer Coating
Various materials, such as chitosan
[59], PES
[60], DETA, PVA
[61], and PDMS
[62], with or without nanoparticles such as TiO
2 incorporated, were coated as selective layers on the surface of nanofiber layers, forming new types of ENMs to be applied in ultrafiltration and oil–water separation processes specifically
[63].
4.4. With the Selective Layer via Interfacial Polymerization
Besides deposition and coating, selective layers prepared via interfacial polymerization (IP) can also be formed on the surface of nanofiber layers to fabricate ENMs, which are mainly used for osmosis and nanofiltration processes. The typical material of this selective layer is polyamide (PA), which is prepared through the reaction of polyamines and acyl chloride
[64].
5. Conclusions
ENMs, with the nanofiber layers serving as selective layers, are mainly produced in three ways: conventional ENMs, mixed matrix ENMs, and surface modification via grafting. For the production of mixed matrix electrospinning solutions, inorganic nanomaterials and organic materials are both furnished by some examples which play different roles in bacterial inhibition, dye removal, separation of oil/water systems, and so on. Such hierarchical membranes’ efficiency is apparently improved by various modifiers, nanoparticles, cross-linked organic reagents, and active biopolymers. However, nanofibers’ direct work as a selective layer has a relatively limited scope of utilization in low-pressure driven process like ultrafiltration, and microfiltration, as well as in thermal-driven process like membrane distillation, due to its poor mechanical strength. Therefore, typical nanofiber layers like PAN, PVDF, and PSF nanofibers and so on are widely installed as a supporting substrate, fixed with an additional skin layer by inorganic deposition, polymer coating, and interfacial polymerization to meet the demand of water treatment in different conditions. All of these contribute to the separation performances of organic pollutants, heavy metals, and antifouling performance in water treatment. It is considered that the ENM market has enormous potential for further development and is anticipated to boom in the immediate future for water purification.