1. Electrophoretic Deposition of a Ceramic Powder
During electrophoretic deposition (EPD), a stable deposit is created by charging particles in a liquid medium moving with an oppositely charged electrode and coagulating. This process has been mainly used for the fabrication of oxide CMC matrices and fibers, as it reduces the processing times and improves the control of green body microstructures
[1][2]. The base material matrices used for this manufacturing process are aqueous or non-aqueous suspensions of ceramic particles and non-conductive Nextel
TM or conductive fibers such as SiC-Nicalon and carbon reinforcements
[3][4]. For the manufacturing of non-conductive fibers, the fiber weave goes on the front of the deposition electrode, while the ceramic deposit is formed on the electrode and grows around and through the fiber
[5][6] (
Figure 1).
Figure 1. EPD process flowchart.
Two alternative processes, based on EPD, have been developed and evaluated, where Al
2O
3 particles and NextelTM 720 fibers were used. The first processing method presented the infiltration of single fiber mats and subsequent lamination, which led to high-density composites but with a small amount of microstructural damage during sintering
[7]. On the other hand, the second approach used simultaneous infiltration of a variety of fiber mats, exhibiting a homogeneous green microstructure with a high particle packing density, allowing for the fabrication of thick components (>10 mm thick)
[8]. The EPD technique has been used in a variety of ceramic composite systems during the decades, such as laminated composites
[9], composite coatings
[10], whisker-reinforced composites
[11], and functionally graded materials
[12].
2. Matrix Deposition/Infiltration from a Gas Phase
Chemical vapor infiltration (CVI) is considered one of the most attractive manufacturing processes for creating fiber-reinforced CMCs
[13]. In this process, the porous preform is added in a surrounding of a reactive gas mixture, which decomposes and yields a solid deposit that is concentrated in the pores of the preform when the mixture is thermally activated. This process allows for the creation of preform complex net shape components, at low temperatures, without occurring any damage to the textile structure, which results in controlling and modifying the microstructure of the final matrix
[13]. CMCs such as SiC/SiC and C/C composites are fabricated using this process, allowing for excellent high temperature, strength, modulus of elasticity, creep, and corrosion resistance properties, compared with other unreinforced SiC composites
[14].
There are several different CVI techniques developed for different composites, with the most well-known one being the isothermal one (I-CVI), used for non-oxide CMCs beginning with Cf/C and moving to SiCf/SiC composites. This process was initially created for the densification of refractory composites
[15]. In recent decades, it has been used for the densification of Cf/C for aircraft brakes and SiCf/SiC for aerospace components
[16]. Some of the most fabricated matrices with CVI are SiC, C, Si
3N
4, BN, Al
2O
3, B4C, TiC, and ZrO
2 (
Figure 2).
Figure 2. Chemical Vapor Deposition processing techniques.
I-CVI is introduced as thermal-gradient CVI (modified CVI) and is used for the manufacturing of large individual parts, such as rocket nozzles
[17]. In this method, the preform is heated more uniformly due to the increase in thermal conductivity of the infiltrated preform
[18][19]. The thermal gradient F-CVI deposition has been introduced as a replacement for the I-CVI while working on SiC and Si
3N
4 matrices with different porous preforms, where the mass transfers occurred by forced convection due to a pressure gradient
[14]. Bussmann et al. researched the practicality of the manufacturing of SiC/SiC components by using the F-CVI process
[20]. Furthermore, it has been researched that the infiltration times of the F-CVI process, reporting that the SiC matrix fabrication times were reduced even though the preforms were 2.5 mm thick
[21].
Another alternative technique called microwave-heated CVI (MW-CVI), is used for controlling the inverse temperature profile of a ceramic fiber preform while heating
[21]. It can produce a controllable temperature profile inside a preform
[22]. It allows the creation of a temperature gradient from the center of the preform to the outside layers, meaning that the deposition of the ceramic matrix occurs from the inside to the outside, without connecting to the sealing of the outer pores of the preform, that might cause any structural problems
[23]. Research on scaling up this process and designing a pilot-scale reactor has been recently published
[24].
Further research shows the evolution of an improved film boiling CVI process for manufacturing large-size Cf/C CMCs using kerosene as a precursor. The result of this process was a composite produced with rapid CVI with a homogeneous microstructure and density that allowed for good feasibility of the film boiling CVI procedure for large components
[25]. Rapid-CVI is particularly applied to C/C composites and is considered to have two different types of fabrication methods. The first method is called boiling film, in which the porous fiber preform is absorbed inside the liquid state precursors
[26]. The second method is rapid vapor-phase densification, in which the porous preform is added to a furnace and is isothermally heated by a graphite tool, offering a forced flow to the precursor gas that exists beside the preform and the graphite tool
[26].
3. Melt Infiltration
The melt infiltration process has been successfully used for the creation of reaction-bonded ceramics for ultra-high-temperature applications. C/SiC and SiC/SiC CMCs are mainly fabricated with this process, where Si melts are infiltrated in the porous carbon-based preforms for SiC to be formed
[27]. MI produces a dense matrix in a shorter cycle time than other infiltration applications, although the needed temperatures are relatively high (up to 1414 °C)
[28]. SiC fiber tows are coated with boron nitride fiber interface and silicon nitride coating. Both the unidirectional fiber and matrix types are created by using a filament winding process and have polymer binders along with commercial SiC and Cf powders. After the tape layup is finished, lamination occurs in a part preform, leading to pyrolysis. After the polymer is turned into carbon, densification of the pyrolyzed preform with SiC and melt infiltration (
Figure 3).
Figure 3. Flowchart of Melt Infiltration Process for CMC materials.
Research shows the fabrication of carbon fiber with SiC-ZrC matrix CMCs. This resulted in the creation of a SiC-ZrC matrix with the SiC matrix adjusting to the carbon film coating fibers, allowing for high bending strength, oxidation resistance, and better ablation resistance in oxyacetylene flame, better than the one that ZrC CMCs have
[29]. In addition, investigations for a multi-physics MI process model for SiC/SiC CMCs, where unsaturated flow and chemical reactions in between the porous matrix and the infiltrant material occurred. This resulted in high permeability/low permeability laminates, tested in a two-dimensional rectangular-shaped CMC preform, but there are no specific estimations of the success of the modeling or the values that occurred through the MI process.
Furthermore, other researchers have developed a multi-physics fully integrated computational model by using the MI process. A porous CMC preform was mixed with an unsaturated fluid flow, to create a porous matrix with a molten silicon infiltrant. This resulted in a mechanical and thermal properties estimation comparison with previous literature for the manufacturing of CMC microstructures with the MI process, allowing for high strength and good oxidation and corrosion resistance.
Other research shows the fabrication of carbon fiber-reinforced C-SiC-Ti
3SiC
2 hybrid matrix composites by implementing TiC slurry and molten Si infiltration processes. This resulted in a successful CMC manufacturing process due to the use of high stability and low viscosity of TiC ball milling. The mechanical properties of the fabricated CMCs were increased with the conversion of TiC to Ti
3SiC
2. On the downside, the research demonstrated that using Ti
3SiC
2 grains in the CMC matrix led to fiber-matrix decohesion, intergranular cracking, and delamination
[30].
Polymer infiltration pyrolysis is a low-cost fabrication process for SiC (from silicon-derived polymer precursors) reinforcements and nanoparticles CMCs and plays a key role in the oxidation resistance of the resulting composite
[31]. There are several steps that the reinforcement fiber and base ceramic material must undergo to create an efficient composite
[32]. The first step is to impregnate the reinforcing fibers with a resin and apply partial curing. In continuous, the preparation is shaped into a mold. The mold is combined with a flexible upper mold, pressed against the prepreg with atmospheric pressure (vacuum bag) or high air pressure (gas pressure bag), and turned into an autoclave
[33]. Then the infiltration of the pre-ceramic polymer occurs while the preform is added into it, vacuum or pressed assisted. Subsequently, the pyrolytic decomposition of the preceramic polymer takes place in an Argon atmosphere at high temperatures, manufacturing the final material composition. Different atmospheres can be introduced into the pyrolysis, resulting in different matrices. After the final matrix is fabricated, the infiltration pyrolysis is repeated up to ten more times to minimize the porosity of the ceramic matrix (
Figure 4).
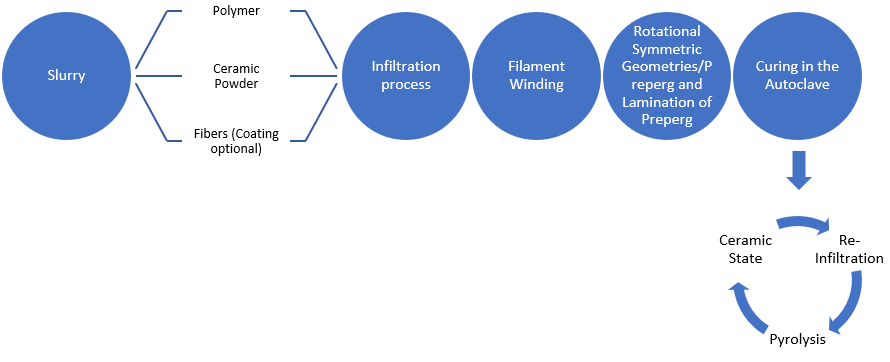
Figure 4. Polymer Infiltration process steps.
The preceramic polymer field has been developed, producing the Si-C-N-O system, focusing exclusively on non-oxide ceramic fibers
[34]. Further investigation on the fabrication of Grade Niclon SiC fiber and HI-Nicalon SiC fiber CMCs, with the PIP process, has been reported, indicating that these fiber-reinforced CMCs could be effectively used in high temperature (up to 1200 °C) structural applications for long periods
[35]. Furthermore, it has been shown that pyrolysis can be performed between 1000–1200 °C under nitrogen flow. The effect of lower pyrolysis temperature, with higher ramp rates, by using SiC/SiC CMCs, has been researched. This allows for a cheaper industrial production cost; high residual porosity and microcracks occur due to the relative density and bending strength being lower. It was concluded that to achieve higher density, the used preform must be evacuated before the polymer solution is added into the mix, which is not feasible to happen for the fabrication of large components
[32].
Sol-Gel infiltration is a valuable fabrication method of CMCs, using fibrous preforms as the precursor materials, including better homogeneity, near-net shape fabrication, and low processing temperatures (<600 °C)
[36]. Although, sol-gel needs to repeat the infiltration process several times, using intermediate heat treatment, to surpass the excessive shrinkage of the matrix while sintering and drying take place
[37].
In sol-gel infiltration, a chemical precursor is hydrolyzed into a gel, then dried and fired to create a ceramic composition. The precursor materials come in the form of water, alcohols, and metal oxides to commercially stabilize colloids which include discrete ceramic particles. The hydrolysis reactions allow for an organometallic solution, including polymer- chains that have metallic ions and oxygen. The amorphous particles are formed from the solution, producing a rigid gel, which is continuously dried and fired to allow for the sintering and densification of the last ceramic part
[38]. For a successful sol-gel infiltration process, the sol should include high ceramic content, low viscosity, and small particle size, which allows it to be processed at low (room) temperature for several hours
[39].
Many attempts have been made to examine the effects of sol-gel processing parameters using different types of oxide fiber preforms such as mullite, aluminosilicate, and zirconia
[40]. The results indicated that sol-gel is mostly effective for the fabrication of near net shape CMCs by using discontinuous mullite fiber preforms but also can be applied in multiple infiltrations in other oxide fillers for the development of CMCs with pseudo ductile characteristics
[37].
Sintering and pyrolysis processes are used to fill a ceramic matrix in between fibers. More specifically, sintering can take place in an oxygen atmosphere, but temperature control and temperature uniformity in the furnace for heating and cooling allows for better results. Sintering for powdered materials occurs at high temperatures according to the application and atmosphere (oxidizing/non-oxidizing) that is being used
[41].
The sintering process of powdered materials is created at elevated temperatures, occurring in an oxidizing environment. Automated powdered metal sintering furnaces allow for better reliability and operating costs. These automated systems include a preheat section, a heating section, and a cooling section
[42].
There are various types of sintering techniques that allow for a similar outcome depending on the precursors used. These different types include diverse hot presses, hot-isostatic presses, pressureless sintering, microwave sintering, and SPS. Furthermore, research showed that long-lasting and high-temperature sintering allowed for the enlargement of the grain size, causing the number of micropores that emanated from the materials to decline in the mechanical properties
[43].
SPS is the most preferred sintering technique for the densification of ceramic composites in comparison with conventional sintering. This is due to densification times being reduced (<15 min) and sustaining a comparatively small grain size, influencing the suppression of uncontrolled grain growth and eliminating porosity. This allows for better mechanical properties
[44] (
Figure 5).

Figure 5. Sintering of an oxide precursor (Al2O3) mixed with oxide filler (fiber) flowchart.
Figure 5 shows a flow diagram of the chemical processing of ceramic oxide fibers, where an oxide ceramic precursor is mixed with inorganic additives (silica precursor, etc.), allowing the preparation of a viscous liquid used for fiber spinning. Then the fiber is processed as a dilute solution to be filtered and avoid particulate contamination. When filtering is finished, the precursor is added in a vacuum to remove any solvent and spin dope. In continuous dry spinning is used by using water as a spin dope solvent, this vaporated while spinning, producing a rigid fiber. The filaments are pyrolyzed at 300oC to 500oC, to clear volatile components of the precursor, leading to ceramic fibers. If the temperature surpasses 800oC, crystallization of the fiber into the alumina occurs.
Liquid Silicon Infiltration (LSI) process is created by combining processed C/C with melted silicon carbide fibers, allowing for the creation of thin-walled and lightweight CMC components. It is characterized as a three-step process, starting with the manufacturing of carbon fiber-reinforced polymer, followed by carbonization and finishing with liquid silicon infiltration
[45]. More specifically, the first step consists of the manufacturing of the CFRP composites with polymer matrices with high carbon yield, which allows for conducting the pyrolysis of the green bodies in one attempt. The second step includes the treatment of the CFRP composites in an inert atmosphere/vacuum, with temperatures ranging from 900 to 1650 °C
[46]. Then, the pyrolysis of the matrix allows for a volumetric construction of 50–60% of the original polymer, and if hindered, this leads to a lower shrinkage of the macroscopical composite, which is almost zero
[47]. In addition, bidirectional reinforced composites and in-plane reinforcing fibers, such as woven fabrics, impede the shrinkage without interacting with the plane of the laminate
[47][48]. Furthermore, the lower the fiber volume percentage and the higher the fiber/matrix bonding in the green body, the higher the transverse shrinkage of the composite. This results in providing C/C composites with an interconnecting pore structure that leads to a translaminar crack system, where the cracks showcase the open porosity of the composite material. After this step is completed, the third and final step is the capillary effect of this open porosity in between C/C laminate and low viscosity of melted silicon at 1420 °C, allowing for a quick composite filling. The continuous exothermic reaction of the C/C and liquid silicon results in silicon carbide encapsulated fiber bundles, offering an increase of 30–50% of the mass for the two-dimensional reinforcements. The final composite consists of three phases which include two-thirds of carbon, one-third of silicon carbide, and a small amount of unreacted silicon
[45] (
Figure 6).
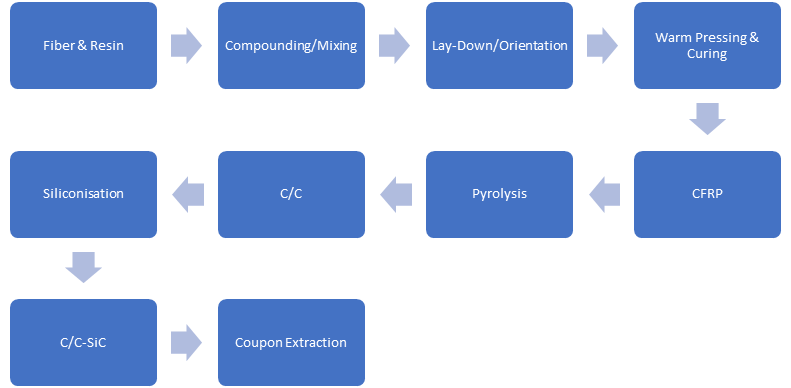
Figure 6. Liquid Silicon Infiltration Process Flowchart.
The LSI process allows for the compact bundles of short carbon fibers to remain intact while the infiltration process with liquid silicon takes place. This happens by creating a green body that includes short fiber bundles and a matrix of phenolic resin. Furthermore, the usage of polymeric precursors with high carbon yields allows for the formation of the characteristic microstructure of the porous C/C preform after the pyrolysis process takes place, leading to discrete translaminar capillary channels where the good penetration of the preform is achieved due to liquid infiltration. This offers the creation of stronger bonds between the matrix and fibers and enhances the overall performance of the final composite material
[46].
8. Selecting the Most Appropriate Manufacturing System
According to the literature presented in this section, the main fabrication processes used for CMCs include CVI, polymer infiltration, pyrolysis, and hot press sintering techniques. Polymer infiltration and pyrolysis are the most commonly used ones. The main aim is to be able to control the thermal and mechanical properties of the fabricated CMC, but several factors, such as the distribution of the final phase formed and the processing route applied from the synthesis of the composite, are very important aspects. These aspects can be manipulated from the correct choice of composite fabrication processes. Every process has different positive and negative attributes, as shown in Figure 7.
Figure 7. Fabrication procedure steps for CMCs.
A major criterion is the price per unit volume of the ceramic matrix and fiber used, as well as the environmental impact of the material (going all the way back to the extraction of the constituting materials, their processing, and delivery to the CMC fabrication plant). This environmental impact can be quantified through the use of embodied energy, which accounts for the energy consumed by all manufacturing processes used. As can be seen in Figure 8, aluminosilicate CMCs have the highest embodied energy as they have some of the more complex material compositions. This indicates that the manufacturing process used to compose this type of CMCs (sol-gel infiltration, sintering) requires a lot of energy and time, increasing the final cost of the production of aluminosilicate-based applications. On the other hand, carbon matrix, alumina oxide, and silicon carbide CMCs have lower embodied energy, meaning that these materials are easier to be produced at larger production rates with lower overall costs and faster time scales. This is because their process materials have fewer complex compositions as they include smaller amounts of fibers and matrix materials (Figure 9).
Figure 8. Embodied energy and price per unit volume of CMCs.
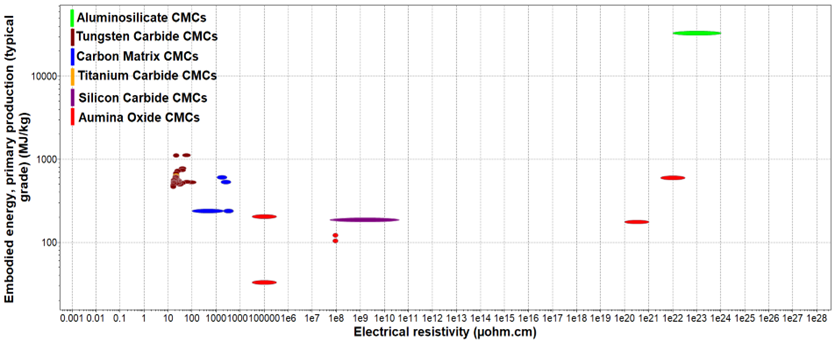
Figure 9. Embodies Energy vs Electrical Resistivity of CMCs.
Figure 10 shows the embodied energy and the electrical resistivity of different ceramic matrix composite categories. As it can be observed from the figure above, aluminosilicate CMCs have the highest embodied energy and electrical resistivity values as they have some of the more complex material compositions. This indicates that the manufacturing process used to compose this CMC (sol-gel infiltration, sintering) requires a lot of energy and time, increasing the final cost of the production of aluminosilicate-based applications. On the other hand, carbon matrix, alumina oxide, and silicon carbide CMCs have lower embodied energy and electrical resistivity, meaning that these materials are easier to be produced at larger production rates with lower overall costs and faster time scales. This is because their process materials have less complex compositions as they include smaller amounts of fibers and matrix materials.
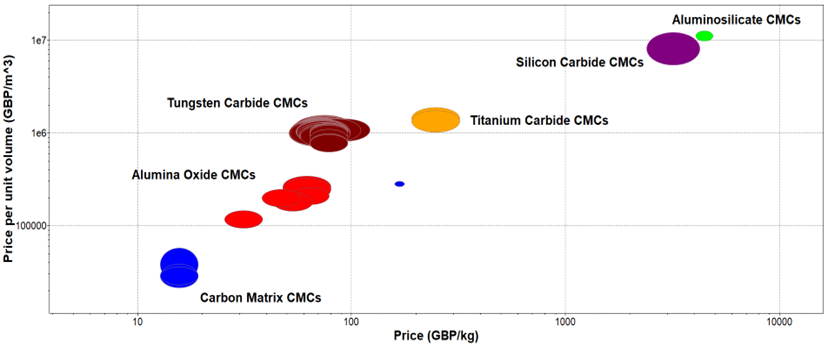
Figure 10. Price Per Unit Volume vs Price of CMCs.
The material comparison in Figure 9 justifies the material comparison in Figure 10 where aluminosilicates are the most expensive composites to produce from both oxide and non-oxide CMCs. On the other hand, alumina oxide composites are much more cost-effective to produce from the oxide CMCs allowing a wider range of materials submerged into the final matrix without having an excessive price increase in manufacturing processes. Finally, carbon matrix CMCs have the lowest production and manufacturing cost as they use the least amount of embodied energy and electrical resistivity and they are also cost-effective to extract and purchase. Although some of the manufacturing techniques used for the production of these materials are not the most cost-efficient and time-consuming such as PIP, MI, and CVI processes.
It must be mentioned that manufacturing processes differ in processing time and processing stages before finalizing the finished material. As a result, the process runs at a higher cost and with longer times than other processes. For example, manufacturing processes that have more complex process technology and complex composite preparation, such as CVI and EPD, are more expensive to run. Although, as mentioned before, the more complex the material composition, the more embodied energy and electrical resistivity are spent. Hence it has been found that infiltration processes and, more specifically, PIP, CVI, and MI are less cost-efficient and more time-consuming, although their final composite outcome has very good mechanical and thermal properties
[49]. This could also be justified by conducting a comparison of the price per unit volume against the price of the available oxide and non-oxide CMCs, which includes both the material production and manufacturing cost, allowing for an estimation of the final manufacturing procedure’s cost outcome. Aluminosilicates are the most expensive composites to produce from both oxide and non-oxide CMCs. On the other hand, alumina oxide composites are much more cost-effective to produce from the oxide CMCs allowing a wider range of materials submerged into the final matrix without having an excessive price increase in manufacturing processes. Finally, carbon matrix CMCs have the lowest production and manufacturing cost as they require the least amount of energy while being cost-effective to extract and purchase.