1. Introduction
Silicon is the second most abundant element (about 26.9% by mass) in the Earth’s crust, mainly in the form of oxide, which is the source for obtaining metallurgical elemental silicon in the reduction process. Low-grade silicon with a purity of 15–90% and metallurgical silicon (MG) with a purity of 99% (2N) are mainly used in the aluminum, steel, and chemical industries. Silicon (6N) has a purity of 99.9999% and is applied mainly as solar-grade, while Si 99.9999999% (9N), electronic-grade, is widely used in photovoltaics and microelectronic industries. Semiconductor silicon is widely used for electronic elements such as diodes, rectifiers, transistors, and integrated circuits. In recent years, new materials (e.g., graphene, perovskite) have been identified as potential alternatives to replace silicon in electronics and photovoltaics. However, there have been no reports indicating the possibility of replacing Si in these industries in the near future, for practical and economic reasons, such as the availability of raw materials, etc. Devices manufactured based on silicon are used to detect photons of nuclear, visible and infrared radiation. Due to the spike in demand for semiconductor silicon (mainly to produce photovoltaic cells), the beginning of the 21st century saw a significant increase in prices and a surge in silicon production.
Based on the latest available reports (2022), China is the largest producer of silicon, and its production volume was estimated at 6 million metric tons in 2021. The second largest silicon producer in the world is Russia, which produced 580,000 metric tons in the same year, which is one order of magnitude less. The total global production of silicon in 2021 was approximately 8.5 million metric tons. Countries by silicon production in 2021 are presented in Figure 1.
Figure 1. Countries by silicon production in 2021 based on USGS figures.
Silicon is used in silicon wafers for production of microprocessors and other very large-scale integration circuits, including memory chips, which are currently used in everyday products such as mobile phones/smartphones, desktop computers, notebooks, industrial products, and other electronic products. The greatest overall demand comes from the use and production of mobile phones/smartphones. In 2018, the demand for silicon wafers for mobile phones and smartphones was 21.9 billion square centimeters. Desktops, notebooks, and server PCs followed at 11.3 billion square centimeters
[1]. The ‘World–Silicon–Market Analysis, Forecast, Size, Trends and Insights’ report from April 2022
[2], showed that the global silicon market in 2021 increased by about USD 10 billion (total revenues of producers and importers) compared to 2020, which is by over 4.1%. The average annual growth of the market in the period from 2007–2021 is 2.8%. The countries with the largest silicon consumption in the world include China, Japan, and Germany. In 2021, the silicone market exceeded USD 16.7 billion. Market analysis indicates that by 2030 it may increase by 6.0%
[3]. According to market analyses CARG (“Compound Annual Growth Rate”) (2022–2030) is >6% for fluids and >6% for resins segment. In 2030, the silicon market value for industrial process application will be >$7.5 billion (
Figure 2).
Figure 2. Silicone Market.
The most important producers of semiconductor-grade (SG) silicon are: Hemlock Semiconductor Corporation, Wacker Chemie, Renewable Energy Corporation Silicon, Tokuyama Corporation, Daqo New Energy
[4]. The largest silicon wafer manufacturers are GlobalWafers Singapore Pte. Ltd., Okmetic Oy, Shanghai Simgui Technology Co. Ltd., Shin-Etsu Chemical Co., Silicon Materials Inc., Siltronic AG, SK Siltron Co., Ltd., Sumco Corporation, Tokuyama Corporation, Virginia Semiconductor, Inc., Wafer Works Corporation
[5]. The global silicon wafer market size reached US$ 11.6 billion in 2022. The top 10 polysilicon manufacturers for 2021 include: Tongwei (China), GCL (China), Daqo New Energy (China), Wacker (Germany/United States), Xinte Energy (China), Xingjiang East Hope New Energy (China), OCI (South Korea/Malaysia), Asia Silicon (China), Hemlock (United States), TianREC–joint venture of Shaanxi Non-Ferrous Tianhong New Energy and REC Silicon (China)
[6]. The presented data and analyses indicate that the silicon market, due to its wide application, is characterized by high demand and supply with a continuous upward trend.
The development of industrial organosilicon chemistry, and thus the development of silicon chemistry, is partly related to the discovery of the direct process of organosilanes synthesis in the 1940s, which allowed the production of organosilanes and silicone polymers on a large scale, and resulted in the development of new technologies to produce organosilicon monomers and polymers. The direct synthesis process, also known as the Müller–Rochow process, is one of the best-known industrial processes for obtaining organosilicon compounds, and has been the basis of the silicone industry
[7][8]. The first report of direct synthesis was in 1941, when Eugene Rochow filed a patent application
[9]. However, because of World War II, it was not released until 1945. At the same time, Richard Müller, independently from Rochow, discovered the same direct reaction of elemental silicon and alkyl chlorides, applying for a patent in 1942
[10], which is why the direct synthesis is commonly called the Müller–Rochow process
[11]. In the photo (
Figure 3), a cordial welcome of the two authors of the fundamental reaction of contemporary organosilicon chemistry is captured: Eugene Rochow (left) and Richard Müller (right) at the International Symposium on Silicon Chemistry in Poznan (Poland), 1993. Between them, in the back, is a co-author of this
presea
perrch (B.M.).
Figure 3. E. Rochow and R. Müller–International Symposium on Silicon Chemistry, Poznan, Poland, 1993.
Until the 1940s, the synthesis of organosilanes and other organosilicon derivatives was a multi-stage and complicated procedure, which is why Müller–Rochow’s discovery was a breakthrough in the development of silicon chemistry
[12]. Before this discovery organosilicon compounds were prepared by reacting organometallic compounds with silicon halides or orthosilicic acid esters
[13]. The process included the preparation of an organometallic compound (conducting a series of syntheses, because often a subsequent reagent was obtained from the previously obtained one), preparation of silicon halide or its additional esterification, and then carrying out the synthesis in solvents or in excess reagents. Müller–Rochow’s discovery had a significant impact on the development of organosilicon compounds. The direct process allowed the introduction of an effective and cost-effective synthesis of organosilanes and silicone polymers on industrial scale, which resulted in further development of technology to produce organosilicon monomers and polymers with special properties and led to organosilicon compounds applications in almost every area of life. It is estimated that about 90% of the monomers to produce silicones are obtained by the Müller–Rochow process
[11]. Direct synthesis process described in literature is a reaction between silicon and hydrogen chloride (
Figure 4a), methyl chloride (
Figure 4b), ethyl chloride (
Figure 4d) and higher alkyl halides, organic halides whose molecules contain more than one halogen atom, aryl halides (
Figure 4c), ethyl alcohol (
Figure 4g) (less often) and methyl alcohol (
Figure 4f) and other organic compounds
[14]. Direct chlorination of metallurgical grade silicone to produce silicone tetrachloride is also known (
Figure 4g)
[15]. The synthesis of alkoxysilanes and their derivatives, as well as the production of semiconductor silicon, is based on the Müller–Rochow process.
Figure 4. Examples of reactions in the direct synthesis between silicon and: (a) hydrogen chloride, (b) methyl chloride, (c) chlorobenzene, (d) ethyl chloride, (e) ethanol, (f) methanol, (g) chlorine.
Methylchlorosilanes obtained by the direct reaction, are substrates to produce polydimethylsiloxanes, other organochlorine monomers or silicon derivatives
[16]. A major use for trichlorosilane was the production of polycrystalline ultra-pure silicone (through the 1960’s and 70’s)
[17].
Figure 5 shows possible products obtained in the direct process. The first route leads to the preparation of organofunctional chlorosilanes and alkoxysilanes (in the hydrosilylation reaction), or further it can be used in manufacturing of semiconductor-grade silicon. The second pathway shows the synthetic possibilities of obtaining organofunctional polysiloxanes
[18]. Silicon reactions with hydrogen chloride and organic chlorides are widely described in literature and used in industry, however, in line with the trend of green chemistry and sustainable development, direct reactions of chlorine-free synthesis with alcohols are currently one of the most significant challenges.
Figure 5. Possible paths of silicon-related processes.
2. State of the Art–Direct Synthesis of Alkoxysilanes
2.1. Mechanism and Catalyst
The direct synthesis reaction was discovered independently in the 1940s by Richard Müller and Eugene G. Rochow, while later Kenrick Lewis (Momentive Performance Materials) and Harry Morten Rong (Elkem ASA) contributed greatly to the understanding of the mechanism and to the development of direct synthesis. Dr. Kenrick Lewis received the 2015 Distinguished Scientist Award from the Westchester Chemical Society for his significant contributions to the understanding of the synthesis and performance of silicones. Harry Morten Rong’s doctoral thesis described the use of silicon for the direct process of obtaining methylchlorosilanes
[19]. The direct synthesis reaction is a complex and very specific process of heterogeneous catalysis. Because its reaction substrate is a solid, and so is the active phase of the catalyst, it is not quite possible to isolate the catalyst from silicon substrate as a separate phase, in fact they are intertwined. Several factors contribute to the complexity of the process and the difficulty in recognizing its nature, including: the three-phase “gas-solid-solid” reaction; the catalyst, to be exact its active phase, occurs in the system in phase equilibria of the alloys present on the surface and in the bulk of silicon; the reaction progresses on the micrometric scale, while the active site has a nanometric scale; presence of impurities in the solid Si powder that affect the direct reaction; extensive decomposition of the product (formation of significant amounts of by-products). The mechanisms of the direct process, both the formation of the surface metallic copper layer and the subsequent implications of this phenomenon in the context of the so called silylene mechanism, have been extensively described in literature. Many authors have been concerned with the role of promoters and the effects of various forms of copper (its purity, crystallinity, type of copper compound).
The complexity of the direct process renders the reaction mechanisms not fully understood and explained as yet, despite many years of research work, scientific publications and patent applications on that topic
[20]. The simple mechanism of direct synthesis of tri- and tetramethoxysilane is presented in
Figure 6. It is generally accepted that the catalyst must create active sites for the reaction to take place. Literature data indicate that copper catalysts in the first stage interact with silicon to form various copper silicides (called copper alloys) Cu-Si (in particular Cu
3Si), which are considered to be the actual active components
[21]. However, Cu
3Si and other silicides are not direct catalysts, but they are responsible for mediating the transport of silicon from the inside of the grains to their surface, as well as for the stabilization and formation of the surface copper layer. Silylene, i.e., a transient and reactive entity, is accountable for the formation of active copper as a surface layer of silicide. Okamoto et al.
[22], in 1993, described the formation of methoxysilanes in the reaction of silicon with methanol in the presence of a copper (I) catalyst (CuCl). The key stage is the formation of silylene active centers, that are generated as a result of the interaction of silicon with copper (catalyst). A copper-rich region of silicon is formed at the silicon surface. Silicon migration into this region yields silylene species (silicon atom with free electron pair)
[22]. Methanol reacts with silylene (I) to form a saturated surface entity. Subsequent insertion of three methanol molecules, cleavage of two CuSi bonds and release of hydrogen result in the formation of trimethoxysilane that is desorbed from the surface active site. The intermediate silylene is regenerated by the diffusion of silicon atoms into the thin copper layer on the surface. Some of the copper layer coagulates to metallic copper, and the solidification deactivates the catalyst. Tetramethoxysilane as a by-product is formed by the reaction of methanol with trimethoxysilane still undesorbed from the surface of metallic copper.
Figure 6. The simple mechanism of direct synthesis of tri- and tetramethoxysilane.
In another paper
[23], the authors determined the temperature effect in the pre-treatment of the silicon-copper chloride mixture and the influence of the reaction conditions on the direct synthesis reaction selectivity towards HSi(OMe)
3. As mentioned, tetramethoxysilane is a by-product of the reaction. High temperatures (>603 K) of the Si-CuCl mixture pre-treatment led to low selectivity of trimethoxysilane (60–70%). A decrease in temperature (<553 K) increases the formation of HSi(OMe)
3 and its selectivity exceeds 98%. At high temperatures, a Cu
3Si phase is formed, however, XRD analysis indicates the formation of metallic copper as well, which implies that on the surface, the Cu
3Si phase may be partly converted back to Cu. At lower temperatures, formation of neither Cu
3Si phase nor metallic copper (or insignificant amounts) was observed. Copper (Cu) catalyzes the transformation of HSi(OMe)
3 towards Si(OMe)
4, therefore, at lower temperatures the selectivity towards trimethoxysilane is high
[23]. Nicolay Yu. Adonin et al.
[23] described the process of active centers formation during the activation of the so called “contact mass” (a reactive Si-Cu alloy with catalytic additives), which are formed during a two-stage pre-treatment in the flow of hydrogen and argon. The authors revealed that both topochemical and heterogeneous chemical reactions as well as diffusion and sorption-desorption processes are involved in the active sites formation
[23].
Literature most often presents two mechanisms of active site formation in the synthesis of chlorosilanes and alkoxysilanes, which assume that copper-silicon and copper metal phases occur because of the interaction of CuCl with silicon. The first mechanism is that active copper and active silicon are formed and react with each other, resulting in Cu
3Si (
Figure 7)
[24]. In the assumed mechanism, the SiCl
4 volatile phase is also formed.
Figure 7. The reaction sequence proposed by Tamhankar et al.
The second assumption is that the Cu
3Si phase is formed directly from silicon and CuCl and then transformed into metallic copper by subsequent interactions with CuCl
[25]. Analyses of Weber et al.
[25] indicated that Cu is a final product as a result of several phase transformations and reactions (
Figure 8). According to these authors, Cu
3Si, Cu
15Si
4 and Cu
5Si are intermediates that react with CuCl.
Figure 8. The reaction sequence proposed by Weber et al.
Nicolay Yu. Adonin et al.
[23] have shown that the interactions between CuCl and Si are more complex. For direct synthesis to occur, there must be a physical contact between them. It has been proved that the reaction starts when the CuCl and silicon molecules come into contact, followed by redistribution of chlorine on the Si surface. The reaction lasts until copper nanoparticles are formed, and they are partially stabilized with chlorine adsorbed at their surface. Another issue discussed by the above authors is the role of hydrogen as a component in the direct synthesis. Hydrogen is a stabilizer of the copper nanoparticles, however, an argon flow after the hydrogen treatment is necessary. Hydrogen probably cleans out the oxygen from the silicon surface, that may be present as an adsorbed gas or may be chemically bonded to Si as a silica. Using EXAFS, the authors found that hydrogen adsorption causes copper segregation and the formation of chlorine-coated metallic copper nanoparticles, so hydrogen must be removed with argon. The study shows that in order to create active centers, metallic copper and a clean silicon surface with appropriate atom concentrations are needed. Acker et al.
[26] studied the reactivity of the CuCl-Si system in relation to the activation of silicon in the direct synthesis. The reaction between CuCl and Si is a model reaction of contact mass activation in a direct process. The authors conducted calorimetric studies of two CuCl charges, one was obtained from the elements at high temperature and the other by reduction in aqueous solution. The CuCl obtained by the latter method was characterized by higher reactivity, which resulted in lower reaction start temperatures, as well as 100% conversion of CuCl with respect to the former one. The reaction of silicon and copper (I) chloride in the initial stage of the process was found to take place in the solid state, therefore, it occurred only when these two entities were in a direct physical contact. The gas phase, which is also formed, i.e., SiCl
4, according to the researchers, does not play any role in the initial stage. Acker’s team proposed a model of the reaction initiation stage
[26], which was based on various interactions between CuCl and Si. The CuCl (I) is one of the “conductors” of copper ions (interstitial diffusion of copper cations) and exhibits a high degree of Frenkel-type disorder. The Cu
+ at low temperatures allows enrichment in chlorine at the CuCl/Si interface, resulting in formation of a space charge layer at that interface. The forming isolated Si-Cl bonds inject electrons into the silicon conductivity band. Electrons can be transferred from Si via the interface to CuCl, resulting in metallic copper at the interface, which diffuses into Si to form solid solutions and stoichiometric phases. Another possibility is that the Cu
+ ions supported by the electric field penetrate the charge layer towards the silicon. Silicide nuclei or Si nuclei in Cu are formed on the silicon surface and become the reaction center due to weaker Cu–Si bonds and the electron buffer capacity of the silicides. The authors compared it to a corrosion model in electrochemistry. The reaction is affected by both interferences that hinder ion mobility or charge transfer, i.e., CuCl covered with Cu(OH)Cl, and those that may favorably affect its course (direct reaction promotors)
[26]. Another work of J. Acker’s team reviewed the thermodynamic studies of the direct synthesis of copper-catalyzed methylchlorosilanes
[27]. The authors specified three main kinetically determined pathways: (1) the formation of carbon, hydrocarbons, hydrogen and hydrogen chloride as a result of cleavage of the C–H bond in methyl chloride, (2) the formation of hydrogen-containing methylchlorosilanes that occurs only in the presence of hydrogen or hydrogen chloride, (3) competition between thermodynamically favored chlorosilanes and kinetically favored methylchlorosilanes
[27].
Figure 9 shows a generalized cross-section of the hypothetical structure of the active phase with four characteristic bands highlighted. The polycrystalline silicon grain region is 500 nm–20 μm thick, the next one is the alloy interphase consisting of a copper silicide of hundreds of nanometers thick and with the concentration gradient of silicon atoms (in relation to copper ones) decreasing towards the upper contact surface. At the top there is a metallic copper phase at which reactive silylene species occur, and the last (gas phase) is gas diffusion phase. Silicon can occur in at least seven chemical forms in the system, ranging from the silicon diffusing from the bulk (1–polycrystalline silicon lattice) through interfacial forms of silicon-copper alloys (3) to molecular forms present in the gas phase (7). All the above-described stages of direct synthesis taking place at and inside of the silicon grain refer to the synthesis of both, chlorosilanes and alkoxysilanes.
Figure 9. Possible chemical forms of silicon in the contact mass during the operation of the catalytic system.
Figure 10 shows a schematic progress of alkoxysilanes synthesis in the presence of a copper catalyst. The reaction was divided into four main steps, i.e.,
- (1)
-
catalytically active copper precursor dispersion (CuCl (I) was used as an example),
-
- (2)
-
an induction period when a catalytically active phase is formed,
-
- (3)
-
direct synthesis catalytic reaction,
-
- (4)
-
deactivation stage.
-
Figure 10. The four stages of direct synthesis process occurring in a silicon grain; (1) catalytically active copper precursor dispersion, (2) an induction period, (3) direct synthesis catalytic reaction, (4) deactivation stage.
-
-
In the second step, the catalytically active phase is being formed [
39], containing highly dispersed copper, copper silicide and chlorine ions. In the third stage, the silylene (surface form of silicon) reacts with alcohol. During this stage, the surface layer is being depleted of silicon, that allows the successive transport of Si atoms to the surface via its alloy phases, often with a complicated structural composition (Cu
3Si, Cu
5Si) and with admixtures of other elements regarded as the process promoters. The main reaction stage is associated with the formation of characteristic pits in the silicon grains. The last, fourth stage, shows deactivation of the catalytic system, which is characterized by the transformation of dispersed forms of copper into surface crystallites forming a layer blocking the diffusion processes of silicon from the bulk of the silicon grain to its surface.
Figure 11 schematically shows the stages of formation of characteristic pits related to the depletion of the substrate (silicon) during the reaction on the polycrystalline grain.
-
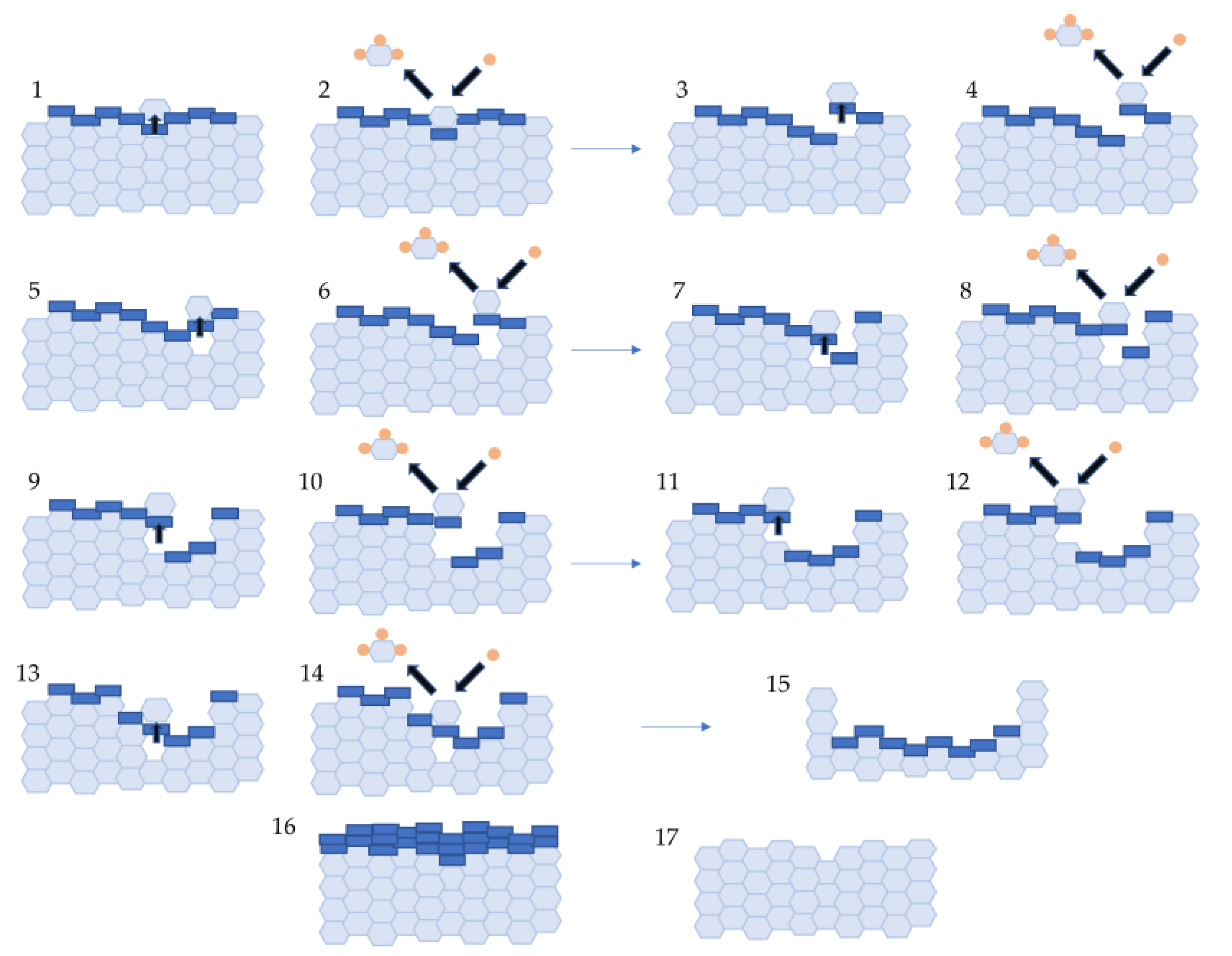
Figure 11. Transport of substrates in solid and gas phase (1–15) and deactivation processes (16,17).
The catalysts of direct synthesis are mainly copper-based (e.g., Cu, CuCl, Cu
2O, CuO, Cu-Cu
2O-CuO)
[28][29][30][31][32]. The efficiency of catalysts is affected by their particle size, method of synthesis, degree of fragmentation, crystallinity, and type of copper compound. Wang et al.
[33] presented in their work a new one-step method for the synthesis of a cupric chloride catalyst from CuSO
4·5H
2O with NaCl at different temperatures (45°C, 50°C and 60°C). The XRD and SEM results suggest that the prepared powder is highly crystalline and has a pure 2D flake structure. The highest selectivity towards HSi(OMe)
3 was observed for the catalyst content of 5 wt.%. From the results these authors concluded that CuCl decomposes into copper ions and chlorine ions in the first stage, then silicon and copper ions combine to form a Cu-Si alloy
[33]. Su et al.
[34] studied the direct synthesis with high selectivity towards triethoxysilane and tetraethoxysilane in the presence of CuCl and Cu (0) catalysts in a fixed bed reactor. After pretreatment of the CuCl/Si mixture under N
2 flow, the metallic Cu (0) phase appeared at 260–500 °C, and the Cu
3Si phase at 280–500 °C. The pretreatment of CuCl/Si at 240–300 °C resulted in the formation of a higher amount of triethoxysilane (with 80% selectivity) than tetraethoxysilane. On the other hand, a pretreatment at even higher temperature resulted in increased selectivity towards tetraethoxysilane (to above 92%). According to the authors, Cu-Si-Cl was probably the active site involved in triethoxysilane formation, while the Cu (0) metal crystallite was the active site involved in tetraethoxysilane formation. These authors also studied the influence of particle size on catalytic activity: CuCl powder showed higher catalytic activity towards triethoxysilane formation compared to that of the commercially available one of larger particle sizes
[34]. Wang et al.
[35] studied the synergic effect in a two-component CuCl/metallic copper catalyst in the direct synthesis of methylchlorosilane in a stirred bed reactor. A two-component catalyst increased the catalytic efficiency of the reaction. Another advantage was a high selectivity towards dimethylchlorosilane (above 88% at 320 °C, at atmospheric pressure)
[35].
2.2. Promotors
Direct synthesis is catalyzed mainly by copper compounds; however, numerous literature reports indicate a significant influence of promoters on the process. The most known promoters added to copper catalysts are zinc, tin, phosphorus, and aluminum
[36]. Their addition in ppm amounts can increase the rate of the reaction, and can also contribute to higher selectivity towards dichlorodimethylsilane, the most desirable reaction product. Let us keep in mind that raw (metallurgical) silicon is contaminated with many other elements, e.g., Fe, Ca, Mg, Zn, Al, Ti, Cr, Ni, Mn, Ba, Cu, Zr, V, Ag, B, Co, P, S (in a wide range of concentrations, from ppm up to several weight percent for iron). This can affect, both positively as well as negatively, the direct process. The presence of the contaminants may lead to lowering the reaction temperature, increasing conversion, or may affect the process selectivity
[37][38][39]. According to recent literature, the most important additives (metals) referred to as promoters of direct synthesis, both in the preparation of chlorosilanes and alkoxysilanes, include zinc, tin, phosphorus, and aluminum
[11][40]. Literature and patent databases contain numerous reports on the use of various direct synthesis promoters, but there is no clear explanation of the impact, mechanism, nature of such additives. Besides, they appear in some reports in mutually exclusive and contradictory roles
[41]. The varieties of direct synthesis process catalysts and reaction conditions along with a diversity of promoters do not facilitate explanation of their effect and operation mechanisms. Most authors describe a selected narrow aspect of the effect of a single promoter on the reaction course with respect to thermodynamics, kinetics, electronic structures of the catalytic system, the effects of the catalyst-promoter systems themselves and so on, while there only a few papers whose authors are concerned with the synergy effect between the promoters. It is generally assumed that the addition of zinc (0.1–1.5 wt.%) increases the selectivity towards DMDCS and slightly increases the reaction rate. Moreover, zinc-tin co-promotion significantly increases the reaction rate and directs the reaction selectivity towards DMDCS (up to 95%). Judging from the low ratio of MTCS to DMDCS, one of the probable explanations of this fact is that zinc is acting as a methylating agent
[42]. It is also assumed that zinc improves the selectivity, but does not influence the reaction rate, and tin addition (in the absence of zinc) improves both these parameters
[43].