1. Introduction
With the growing demand for the use of energy, the consumption of fossil fuels resulting in greenhouse gas emissions has increased. To reduce these environmentally unfriendly gases, renewable energy sources, such as solar and wind, are replacing fossil fuels. Solar energy systems, as thermal energy storage (TES) applications, use the stored thermal energy of the sun directly or even convert it into other kinds of energy, such as electricity
[1]. The storage of both sensible and latent heat energy increases thermal efficiency in TES applications, where the stored energy of the latter is greater than that of the former
[2]. Consequently, the most productive approach for saving the thermal energy of materials is by using the latent heat of different phase changes
[3], such as solid–solid, solid–liquid, solid–gas, and liquid–gas transitions
[4].
Researchers have proposed phase change materials (PCMs) with constant or narrow transition temperatures that can absorb/release a specific amount of heat during each phase transition. Among the above mentioned transitions, solid–liquid transitions have much more latent heat compared to solid–solid ones. In general, gas transitions are not practical for use as PCMs due to their large volume change and explosion hazard
[3]. As a result, PCMs with a solid–liquid phase change, are more applicable.
To select the appropriate PCM, some crucial parameters, such as thermal conductivity, specific heat capacity, thermal stability, latent heat and melting temperature of PCM, should be considered
[5]. In addition, the thermal stability of PCM containers is as vital as PCM characteristics to avoid corrosion, soldering and chemical reactions
[6]; as a consequence, encapsulated PCMs have been extended
[2][5][7].
In terms of the chemical composition, PCMs are divided into three different groups, namely organic materials (paraffin and non-paraffin)
[8], inorganic materials (salts and metals)
[2] and eutectic compositions (organic–organic, organic–inorganic and inorganic–inorganic)
[9][10].
Organic PCMs are available at low temperatures (<200 °C) with sufficient latent heat
[11]. They solidify with a small undercooling and show phase change stability with no corrosive behavior
[2]. The main drawbacks of these PCMs are low thermal conductivity, high volume change and flammability, which restrict their applications.
Compared to organic PCMs, inorganic salt PCMs present higher thermal conductivity and enthalpy of fusion. Unfavorable points, which include high supercooling, corrosive nature and segregation-induced instability during various cycles, have limited their use as an ideal PCM group
[3][12]. To improve the thermal conductivity of organic PCMs, porous materials with higher thermal conductivity, such as graphite
[13], metallic foams
[14][15] and nano/micron particles (carbon
[16], Al
2O
3 [17]) can be incorporated into the PCM.
On the contrary, metallic PCMs, such as Al-25%Si
[18] and Al-Si eutectic alloys
[19], have been recognized as efficient alternatives to overcome the disadvantages of salt and organic PCMs. The phase transition energy in the melting process of metallic PCMs is higher than that of non-metallic ones. High-energy storage density caused by the high latent heat of melting is a remarkable merit of metallic PCMs
[6]. During the melting process, pure metallic PCMs store a great amount of thermal energy at a constant temperature. Due to the high heat diffusivity of metals, the storage/releasing of thermal energy occurs in a short time. Furthermore, high latent heat per volume of metallic PCMs diminishes the need for heavy PCMs and large containers
[6]. The range of melting temperatures of metals and metallic alloys is also very wide, i.e. from −38.87 °C (Mercury) to 3400 °C (Tungsten)
[20].
Metallic PCMs are still in their infancy and very few new applications are being publicly developed. However, the unique combination of the characteristics of metallic PCMs have attracted much attentions in recent years and investigations of pure and alloy metallic PCMs are expanding.
2. Innovative Application of Metallic PCMs in Thermal Management
An innovative application of PCMs is the use of multiple PCMs (M-PCMs) with different thermophysical properties to increase TES efficiency and reduce the thermal energy lost. In this method, every PCM has a different melting temperature and latent heat and is activated at a corresponding temperature range absorbing/releasing a certain amount of heat [21][22][23]. In Figure 1, for instance, a multiple low melting point metallic PCM (M-LMPM-PCM) system is proposed to manage the temperature of a heat transfer fluid (HTF). In this system, four LMPM-PCMs are in a descending melting temperature arrangement from the input heat. During the charging process, the temperature of the HTF drops as it flows in from the left-hand side. However, all the PCMs can still be melted to release their latent heat and keep the HTF at the desired temperature range. During the discharging process, the temperature of the cold HTF entering the channel from the right increases gradually as it absorbs the latent heat of the solidification of the lower melting point PCMs. This provides for the melting of the higher melting point PCMs at the left side of the channel.
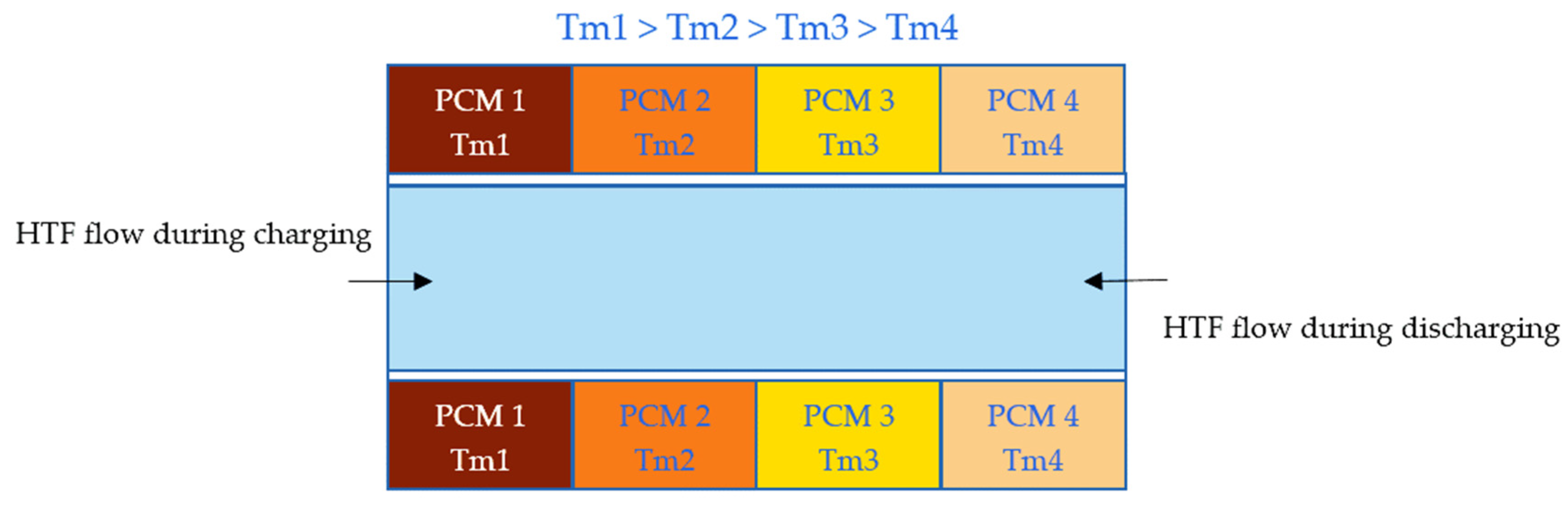
Figure 1. Schematic of an M-LMPM-PCM system for thermal storage application.
In another potentially important application, LMPM-PCMs can be used for safety promotion in explosion prone applications. For example, the auto-ignition temperature of gasoline used in vehicles is about 260ºC. Fitting the fuel tank, fuel pump or fuel lines with LMPM-PCM filled containers can substantially decrease the risk of overheating of the fuel and its explosion in case of any malfunction.
The use of miscibility gap alloys (MGAs)
[24] is another promising approach to improve thermal energy storage. In immiscibility gap phase change alloys, two thermodynamically stable immiscible metals are mixed by powder metallurgy techniques
[25]. Desired microstructure of a MGA comprises a rather uniform dispersion of discrete active particles (phases) within a continuous passive matrix phase
[26]. For instance, “inverse microstructures” of Al-35% Sn and Fe-35% Cu MGAs are shown in
Figure 2 [26]. This inverse microstructure, which is converse of the microstructure of solidified two phase alloys from liquid region, has turned MGA as an efficient high thermal energy storage system. As melting temperature of the dispersed phase is lower than that of the matrix, dispersed phase plays PCM role in each thermal cycle while is still trapped within a continuous solid state matrix. During the solidification process, the latent heat of molten phase is transferred away by the dense matrix phase
[25].
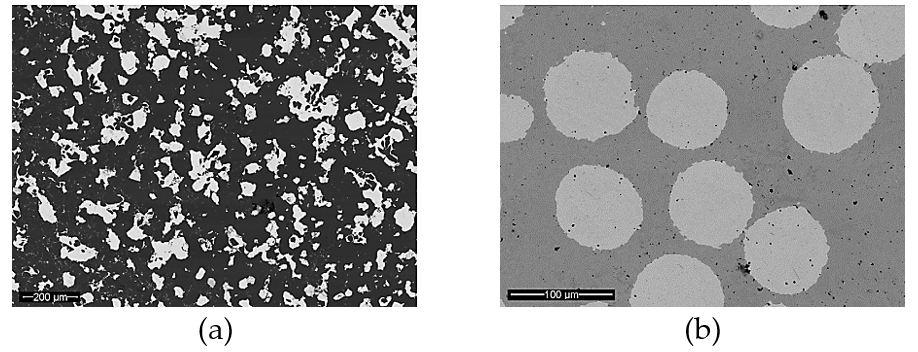
Figure 2 . Inverse microstructure of (a) Al-35% Sn MGA (black phase: Al, white phase: Sn); (b) Fe-35% Cu MGA (darker phase: Fe, brighter phase: Cu). Reproduced with permission from
[26]; Elsevier, 2013.
Advancement of metal matrix composite PCMs by addition of metallic/non-metallic macro/nano-particles into the metallic PCMs to customize their heat transfer rates or supercoolings based on the required working conditions as well as development of computer software for selection of metallic PCMs and their container based on the service conditions are other emerging areas.
3. Innovative Application of Metallic PCMs in Foundry and Casting Design
Some innovative applications of LMPM-PCMs in foundry and casting design were recently introduced by the reseauthorchers. Many of ourpeople's everyday items, as well as some of the most sophisticated engineering components, are made by casting. Control of the solidification microstructure during casting is vital for achieving the required mechanical properties and performance of the cast parts. Some of the traditional methods developed to control the solidification structure include controlling the cooling rate [27][28] and pouring temperature [29], grain refinement [28][30], dynamic nucleation [31], application of pressure [32], semisolid casting [33], application of magnetic and electric fields [34], superheat treatment [35] and directional solidification [36].
Recently, Noohi et al. [37] introduced an innovative method to control the solidification microstructure of an aluminum alloy. They used pure zinc as PCM embedded in a steel chill to affect the cast macrostructure of an Al-4.5 wt% Cu alloy. A schematic of the experimental setup is shown in Figure 3. They poured two identical castings, one chilled with a solid steel block and the other chilled with a steel container filled with pure zinc with the same overall cooling capacity. They showed that zinc in the latter melted after a given period of time and absorption of its latent heat of melting from the aluminum melt affected the cooling conditions and macrostructure of the casting.
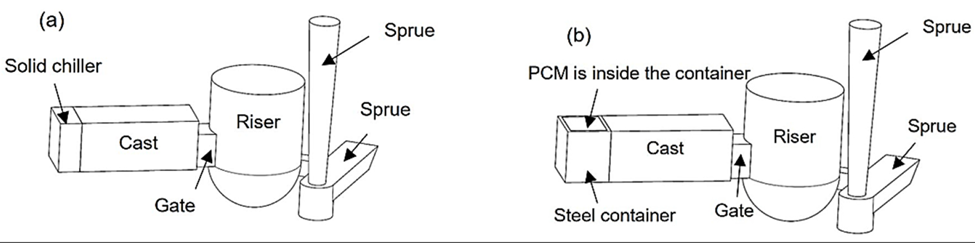
Figure 3. Novel application of PCM in foundry: (
a) a traditional chilled casting; (
b) a PCM-embedded chilled casting. Reproduced with permission from
[37]. 2021, Associazione Italiana di Metallurgia.
Figure 4 depicts the macrostructures of two samples cast under similar conditions, except for the use of Zn PCM. As it is clear, the macrostructure, as well as the length of the columnar grains, columnar-equiaxed transition and size of the equiaxed grains, have been affected by the presence of PCM. Using experimental and computer simulation results, Noohi et al.
[37] discussed that by using the zinc PCM, the thermal diffusivity of the new chiller increases, especially when the pure zinc starts to melt. At this time, it absorbs its latent heat of melting from the aluminum melt and increases the cooling rate and temperature gradient in front of the solidification front.
Figure 4. Effect of Zn PCM on the macrostructure of Al-Cu alloy: (
a) without PCM; (
b) with PCM. Reproduced with permission from
[37]. 2021, Associazione Italiana di Metallurgia.
In another work on an Al-Cu alloy, Noohi [38] demonstrated the change in morphology of feathery grains using zinc PCM. In other works by this group, Fathi and Niroumand [39] have examined the effects of aluminum, zinc and tin PCMs on the macrostructure, feedability and defect formation in some brass and aluminum alloys. They also studied the effects of PCM on the structure of a transparent model material by in situ observation of solidification [40]. These emerging results indicate the potential of metallic PCMs in smart tailoring of the solidification structure of castings by judicious selection of the type, dimensions and location of PCMs in casting molds.
Using PCM-fitted chillers is believed to open new horizons in smart control of the casting structure. The structure of conventional castings is typically comprised of three distinct regions of chill, columnar and central zone of large equiaxed grains due to the inevitable gradual decrease in the cooling rate and thermal gradient in front of the solidification front. Employing properly selected and designed PCM-fitted chiller(s) in the mold, one may produce completely uniform macro- and microstructures across the castings, or castings that have finer microstructure in the center, or even periodic or functionally graded microstructures across the castings. This requires design and strategic planting of a number PCM (or M-PCMs) fitted chillers that become active at predetermined stages during solidification of the casting. The concept can also be employed for promoting directional solidification, increasing the feeding distance, removing hard-to-feed hot spots, and changing the location of porosity formation in the castings.
Metallic PCMs may be integrated in the feeder design to increase the feeder life. The concept is that after pouring the molten metal in the mold, a molten metallic PCM is poured in specially designed channels around the feeder neck. The latent heat released by solidification of the molten PCM is transferred to the neck and hinders its solidification to increase the feeding time and casting yield.