where
b is the Stokes drag factor,
εp is the dielectric constant of the particle,
εo is the electric permittivity of free space, ζ is the particle zeta potential,
E is the applied electric field,
η is the medium viscosity,
mp is the particle mass, and
ω is the angular frequency of the field. Electrophoresis is frequently used to deposit colloidal particles onto surfaces to create functional materials by a process known as electrophoretic deposition
[64,65][64][65].
In one demonstration of electrophoretic deposition for fabricating particle-polymer composites, poly [3-(3-
N,
N-diethylaminopropoxy)thiophene] (PDAOT) was dissolved in an acetic acid, water, and ethanol mixture
[66]. The mixture was blended with a dispersion of single-wall carbon nanotubes (SWCNTs) and placed in an electrochemical cell, where a 3–15 V direct current (DC) potential was applied over a period of time that varied from 1 to 10 min. The process was used to control the particle-polymer deposition rate for the fabrication of metal oxide nanoparticle-polymer films with a thickness that varied from 100 nm to 15 μm
[67,68][67][68]. Another polymer, poly (3-octylthiophene) (P3OT), has been blended with SWCNTs to fabricate particle-polymer films with enhanced current density
[69]. In these experiments, a 40 V DC potential was applied to create a control particle-polymer film. An alternating current (AC) signal was superimposed onto the input DC signal, resulting in a 12% improvement to current density capacity. The current capacity of electrophoretically deposited particle-polymer films was used as the basis for a sensor which measured changes in resistivity due to in-plane shear stress
[70].
Electrodes can also be patterned using photolithography to better concentrate deposition material. Electrode patterning allowed for the fabrication of a conductive particle-polymer film that resulted in a 344% improvement of current density as compared with films fabricated using a DC potential
[69]. Photolithography has also been used as part of a process to create a substrate where electrophoretic deposition was applied to Ni fibers dispersed in a polyurethane-modified epoxy resin
[71]. An unmodified resin was measured, and its Young’s modulus was 285 MPa after curing, while an electrophoretically deposited Ni fiber resin composite’s Young’s modulus was 6.8 GPa.
When a non-uniform electric field is used, particles migrate towards field minima or maxima depending on particle and medium properties
[72,73,74][72][73][74]. This mechanism, known as dielectrophoresis, affects particles with a force that depends on the gradient of the applied electric field
[75]:

where
εm is the medium dielectric constant,
Vp is the particle volume, and
fcm is the Clausius–Mossotti factor. The parameter,
fcm, is a factor that compares the relative contribution of particle and medium properties to the force acting on the particle. This contribution is as follows:
where the operator, Re, is used to find the real component of the Clausius–Mossotti term and ε˜=εεo−iσ/ω is the complex dielectric permittivity of the particle or the medium. In the DC limit, where ω = 0, fcm is dominated by conductivity values, while dielectric constants are important at high frequencies (ω→∞)[76].
Dipolar chains also form in response to electric field-induced polarization of the particles in solution. The dipolar chain energy acting on a single pair of particles in an electric field is
[77]:
where p=3εmεoVpfcmE is the dipole moment of the particle pair, r is the center-to-center separation distance between particle pairs, P2 is a Legendre polynomial of order two, and θ is the angular orientation of the particle pair with respect to the direction of the applied electric field. The force representation of Equation (4) is [78]:

where
er is a unit vector that connects the particle pair and
ez is a unit vector that points in the direction of the electric field.
In uniform electric fields or electric fields with weak gradients, dipolar chain structures are observed in the resulting composite. These dipolar chains assemble with structures oriented in the primary direction of the applied electric field and, with particle loadings in sufficiently high concentrations, bridge the gap between electrodes, forming a percolated network.
Spirulina, a microscopic organism with a spring-like structure, is coated with silver and dispersed in polydimethylsiloxane (PDMS)
[79]. The
Spirulina structures are used to create microcoils, as shown in
Figure 2A. These microcoil particles assemble into chains between electrodes to form a composite with a conductivity of 10 S/m, which is eight orders of magnitude larger than non-aligned
Spirulina samples (
Figure 2B). Carbon nanocones dispersed in an acrylated urethane form chain structures that improve the electrical conductivity of the polymer from 10
−7 to 10
−3 S/m
[80].
Figure 2. (
A) SEM image of a metallic Spirulina-templated microcoil. The inset shows a cross-section of the microcoil particle; (
B) the application of a 5 wt% electric field-aligned microcoil/PDMS composite in a functional LED integrated circuit. Reprinted with permission from
[79], copyright 2017 American Chemical Society; optical micrographs showing (
C) the top view and (
D) side view of a thermally cured carbon nanocone film (0.2 vol%), which was assembled by DC field alignment; (
E) inset shows an SEM image of the nanocone used in this process. Reprinted with permission from
[80], copyright 2011 John Wiley and Sons; (
F) hollow glass microspheres dispersed in Norland optical adhesive initially chain before (
G) migrating towards an electrode. Reprinted with permission from
[81], copyright 2017 Elsevier; (
H) an acrylate polymer composite consisting of (
I) SWCNT aligned using an AC electric field. Reprinted with permission from
[82], copyright 2014 John Wiley and Sons.
3. Magnetic Fields
Similar as with electric fields, particles respond to magnetic fields by migrating towards magnetic field minima or maxima depending on the intrinsic properties of the particle and the medium in which they are dispersed
[93][83]. The magnetophoretic force responsible for this migration is given as follows:

where χp and χm are the magnetic susceptibilities of the particle and medium, respectively, and μo is the magnetic permeability of free space. The magnetic induction, B, is related to the applied magnetic field, H, by the expression [84] [94] B=μo(1+χm)H. In addition to magnetophoresis, multiple particles also form dipolar chains in the direction of the magnetic field. The interaction energy between a single pair of particles in a magnetic field is [95][85]:

where m=(χp−χm)VpB/μo is the magnetic moment of the particle and θ is the angle the pair forms with respect to the direction of the magnetic field. The force representation of Equation (7) is [96][86]:

where
er is a unit vector that connects the particle pair and
ez is a unit vector that points in the direction of the magnetic field.
The use of magnets as a mechanism for composite fabrication has a long history due to the ease of the process and simplicity of blending para- or ferromagnetic particles with a polymer medium
[97,98,99,100,101][87][88][89][90][91]. When magnetically sensitive particles are crosslinked in a polymer, the composite forms a magnetoelastomer that deforms in the presence of a magnetic field
[102,103][92][93]. An alternative method for creating magnetoelastomers was suggested by the authors of this review
[104][94]. In this alternative approach, a sacrificial scaffold was created in PDMS. The scaffold was dissolved, and a magnetorheological fluid was introduced to the evacuated channel, rendering the structure sensitive to magnetic field-induced deflections.
Magnetoelastic soft actuators (sometimes referred to as ferrogels) are designed by coupling magnetic properties of filler particles and elasticity of the polymer matrix. Understanding the deformation and mechanical properties of such actuators is crucial for optimizing their performance
[105][95]. The deformation of these composites in the presence of a magnetic field is analogous to muscle constriction
[106][96], which makes these types of composites ideal for actuation applications such as haptic control surfaces for steering
[107][97].
Magnetite (Fe
3O
4) is one of the most frequently used filler material due to its high magnetic susceptibility
[108][98], which makes it easy to pattern structures in polymers using externally directed magnetic fields
[109][99]. Fe
3O
4 can be adsorbed on cellulose nanocrystals to fabricate magnetic cellulose nanocrystals (MGCNCs). The MGCNCs, shown in
Figure 3, then are aligned in different configurations (parallel or perpendicular directions) in the polylactic acid matrix through a tunable magnetic field which result in fabrication of particle-polymer nanocomposite with anisotropic electrical and magnetic properties. The percent elongation improvement of the resulting nanocomposite is in the range of 60% to 240%
[110][100]. This use of magnetic fields to locally pattern magnetite-PDMS composites led to a reduction in local elastic modulus by as much as 50% depending on filler particle concentration. While local elastic properties of the composite may see a reduction due to magnetic field-induced concentration, the bulk storage moduli of a magnetite-based composite are observed to increase by a factor of two depending on the field magnitude used to align particles
[111][101]. Magnetite can also be functionally bound to materials that are not ferromagnetic, such as cellulose
[112][102] or glass
[113][103], to create materials with anisotropic mechanical properties or functional structures, like the circuit shown in
Figure 4A,B.
Figure 3. Energy dispersive x-ray images show magnetic cellulose nanocrystals (MGCNC) without (
A) an applied magnetic field, (
B) a horizontally aligned magnetic field, and (
C) a vertically aligned magnetic field. Insets diagrammatically show the field alignment for each case. Reprinted with permission from
[113][103]. Copyright 2011 American Chemical Society.
Figure 4. A nanocomposite magnetic switch: (
A) a gap between an aligned CNT coated composite and a nonmagnetic Pb is (
B) closed when a magnet is placed underneath the Pb sheet, which lights an LED. Reprinted with permission from
[112][102]. Copyright 2019 Elsevier. Environmental scanning electron microscopy images show the morphology of an epoxy composite sample processed at (
C) no applied magnetic field and (
D) at 15 T. The arrow represents the direction of the corresponding magnetic field. Reprinted with permission from
[114][104]. Copyright 2004 John Wiley and Sons. (
E) A complex pattern formed in a composite by the superposition of two separate magnetic fields. Reprinted with permission from
[115][105]. Copyright 2017 Springer Nature.
Aside from magnetite, carbon nanotubes (CNTs) are also extensively used with magnetic fields to create aligned composites
[116,117,118][106][107][108]. When a magnetic field is applied to anisotropic particle like CNT, the particle rotates with a torque of
[119][109],

4. Acoustic Fields
An acoustic source, such as a piezeoelectric transducer, generates an acoustic radiation force that can be used to transport particles. The acoustic radiation force responsible for transporting particles is dependent on the gradient of the pressure field generated by the acoustic source
[135,136,137][110][111][112]:
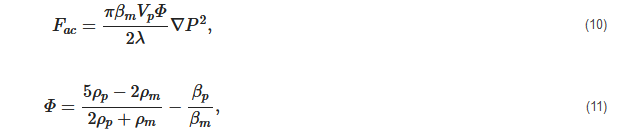
where β = 1/ρc2 is the compressibility, ρ is density, c is the speed of sound, Φ is the acoustic contrast factor, λ is the wavelength of the acoustic field, and P is the pressure distribution. The subscripts p and m refer to particle and medium properties, respectively. The pressure distribution for a one-dimensional standing wave is [113] [138] P=Pocos(2πfx/cm), where Po is the pressure amplitude and f is the applied frequency.
Acoustic nodes are created when the acoustic wave is reflected. The resulting superposition of incident and reflected waves interfere with each other [139][114]. This phenomena, known as standing acoustic waves (SAW), has long been recognized as a method for separating small particles or drops dispersed in a fluid [135,140,141,142][110][115][116][117]. The relative difference in particle density and compressibility dictates whether particles migrate towards or away from the acoustic pressure node where the wave interference leads to a local pressure of zero. Particles that are more dense and less compressible than the medium, such as polystyrene [143][118] or cells [144][119], migrate to acoustic pressure nodes. Particles such as microbubbles [120] [145] or PDMS [121] [146] are less dense or more compressible than the medium in which they are dispersed, leading to migration towards the acoustic pressure antinode, where the pressure gradient is highest.
To demonstrate the utility of SAWs as a method for particle-polymer composite fabrication, early studies used polysiloxane as the polymer medium due to its ease of use and low cost [147][122]. The composite was prepared by blending the polysiloxane with a curing agent at a ratio of 20:1. Ten-micron acrylic spheres were dispersed in the polysiloxane fluid to act as filler particles. The acoustic field frequency was adjusted to create multiple acoustic nodes for filler particle assembly and allowed to set for 8 h. Adjusting the orientation and number of transducers can lead to different internal microstructures, such as lines or lattices [148][123]. Diffraction experiments showed that acoustic fields were excellent for localizing particles around the acoustic node [149][124]. Diamond nanoparticles with diameters of 5 nm were successfully arranged in ethanol-diluted epoxy matrix using acoustic standing wave to produce polymer nanocomposite. The radiation force of standing waves in a rectangular chamber was used to pattern clusters of nanoparticles. During the epoxy curing cycle of 5 min, the standing wave was activated and diamond nanoparticles migrated toward the nodes due to acoustic radiation force and formed quasi-parallel planes of particle clusters (Figure 5A) [150][125]. Complex particle-polymer composite structures can be formed using SAWs if the acoustic signal is first passed through a pattern that acts like a “hologram” for the desired structure (e.g., Figure 5B) [151,152,153][126][127][128].
Figure 5. (
A) An X-ray microtomographic rendering of ~5 nm diamond nanoparticles assembled in an epoxy composite using a 1 MHz ultrasound standing wave. Reprinted with permission from
[150][125], copyright 2011 AIP Publishing; (
B) holographic tweezers used acoustic fields to assemble silicone particles to form complex, nonsymmetric structures. Reprinted with permission from
[153][128], copyright 2011 John Wiley and Sons; (
C,
left) acoustically assembled fibers assembled at an acoustic node in an epoxy; (
C,
right) the composite is deposited on a substrate at a rate of 3.7 mm/s to form a printed line. Reprinted with permission from
[154][129], copyright 2016 Elsevier; (
D) lock (1 mm square) and key (200 μm circle) microgel assemble before excitation (left) and after acoustic excitation (right). Reprinted with permission from
[155][130], copyright 2011 Elsevier; (
E) iron oxide nanoparticles (50–100 nm) assemble in a hydrogel through vibrational excitation of the medium. Reprinted with permission from
[60], copyright 2018 Elsevier.