1. Introduction
CCS captures carbon dioxide (CO
2) from industrial processes, transports it to storage, and injects it into underground formations for long-term storage
[1]. Carbon storage is used to prevent CO
2 from entering the atmosphere and causing climate change (
Figure 1)
[2]. The key components of CCS include capture, transport, and storage
[3]. Capture separates CO
2 from other gases released during industrial processes, transport transports the captured CO
2 to storage, and storage injects the CO
2 into geological formations for long-term storage
[4].
Figure 1. The CCS industry chain and its driving factors.
There are several methods of carbon storage, including geological storage, ocean storage, and mineral storage
[5]. Geological storage, as the most popular approach, involves injecting CO
2 into subterranean geological formations like coal seams, deep saline formations, and depleted oil and gas reserves
[5][6].
Different carbon storage methods work in different industries, with the oil and gas industry being one of the major sectors using CCS
[7]. CCS can be very helpful in lowering carbon dioxide emissions because the industry is a substantial producer of greenhouse gas emissions
[8].
The different stages of carbon storage include site selection, characterization, injection, and post-injection monitoring
[9]. Site selection involves identifying suitable geological formations for CO
2 storage, characterization includes assessing the properties of formations to ensure safe and effective storage, injection comprises injecting CO
2 into the formations, and post-injection monitoring encompasses monitoring the storage sites to ensure the injected CO
2 remains stored underground
[1].
CCS can also be used as an alternative for water injection into oil reservoirs, a technique known as carbon capture, utilization, and storage (CCUS) or enhanced oil recovery (EOR)
[10]. This involves injecting CO
2 into oil reservoirs to increase oil recovery while simultaneously storing the CO
2 underground
[11].
While CCS is used to lower greenhouse gas emissions, negative environmental impacts, such as the risk of CO
2 leakage and potential impacts on groundwater resources, must also be considered
[12].
The technologies used in CCS, especially in petroleum engineering, include various methods of capture, such as post-combustion capture, pre-combustion capture, and oxy-fuel combustion
[13]. Transport methods include pipelines, ships, and trucks, while storage methods include geological storage, ocean storage, and mineral storage
[14][15].
Carbon storage supports reducing greenhouse gas emissions from the oil and gas industry, the enhancement of energy security, and the transition to a low-carbon economy
[16][17][18]; however, there are still technical and operational challenges associated with CCS technology, including the high cost of operation, the need for regulatory frameworks and incentives to promote CCS deployment, and the public perception of CCS as a viable solution for climate change
[19][20][21].
This text provides a systematic review of the application of CCS technology in different aspects of the oil and gas industry. The key components of CCS, including capture, transport, and storage, as well as the different methods and challenges associated with each stage, have been discussed. The different methods of carbon storage, such as geological storage, ocean storage, and mineralization, have been investigated, as has how they work in different industries, especially the oil and gas industry. The stages of carbon storage, including site characterization, injection, and monitoring, and post-closure activities have been outlined, along with the technical and operational challenges associated with each stage. The potential benefits and challenges associated with using the CCS method as an alternative method for water injection in oil reservoirs have been discussed. The environmental impacts of CCS, such as potential risks to groundwater resources and local ecosystems, have also been considered, along with the measures that can be taken to mitigate these risks. Additionally, the technologies used in the CCS method, especially in petroleum engineering, have been investigated, as has the potential for innovation in and the improvement of these technologies. The advantages and disadvantages of the carbon storage method have been discussed, including its potential benefits for reducing greenhouse gas emissions and enhancing energy security, as well as the potential risks and uncertainties associated with the long-term storage of carbon. Finally, CCS and EOR, as well as the potential for combining these technologies to enhance oil production while reducing greenhouse gas emissions, have been explored. The policy and regulatory issues associated with CCS deployment, including the need for supportive policies and incentives, as well as the potential for international cooperation and collaboration in promoting CCS technology, have also been considered.
2. Background
2.1. The Purpose of CCS in the Oil and Gas Industry
The primary objective of carbon storage, especially in the oil and gas industry, is to lower greenhouse gas emissions and reduce their impact on climate change
[22]. Carbon storage methods, like geological storage and bioenergy with carbon capture and storage (BECCS), can help reduce the carbon footprint of oil and gas operations, while also providing opportunities for enhanced oil and gas recovery
[22][23]. By capturing and storing CO
2, these methods can prevent its release into the atmosphere, which contributes to climate change
[2].
Implementing carbon storage methods would extend the lifetime of existing oil and gas reservoirs by enhancing recovery and reducing the amount of CO
2 emitted during production
[24]. This can provide economic benefits for oil and gas companies, while also reducing the environmental impact of their operations
[24][25].
CCS is a critical technology for the heavy oil industry
[26]. Heavy oil production typically involves injecting steam into a reservoir to heat oil and reduce its viscosity, making it easier to extract. This process, referred to as thermal EOR, requires a significant amount of energy to generate steam
[27].
The majority of this energy comes from burning natural gas or other fossil fuels that release CO
2 into the atmosphere
[28]. This issue becomes problematic because CO
2 is a greenhouse gas that adversely contributes to climate change
[29][30].
CCS is a technology that allows for capturing the CO
2 emitted during heavy oil production and storing it underground instead of releasing it into the atmosphere
[31]. The process involves capturing CO
2 at the source, such as a gas plant or a boiler, and transporting it via pipelines to a storage site
[32].
Xu et al.
[33] discussed the effects of lean zones on steam-assisted gravity drainage (SAGD) performance, which is a common method used in the heavy oil industry to extract bitumen from reservoirs. A significant amount of steam is required to heat reservoirs and reduce the viscosity of the bitumen for extraction
[33][34][35]. In the presence of lean zones even more steam needs to be injected to maintain the desired temperature and pressure for effective extraction
[34][36]. The heavy oil industry consumes a lot of energy in the form of steam to extract bitumen
[37].
In the case of heavy oil production, the captured CO
2 can be used for EOR. This approach can reduce the amount of fresh steam that needs to be injected
[38][39]. It, in turn, reduces the amount of fossil fuels needed for generating steam, and, thereby, helps to lessen greenhouse gas emissions associated with heavy oil production
[40].
2.2. Key Components of CCS
CCS consists of four key components: capture, transport, storage, and utilization
[3]. These components are critical to the success of the technology
[41]. The capture process involves separating CO
2 from other gases emitted during industrial processes. There are several capture technologies available, including post-combustion, pre-combustion, and oxy-fuel combustion captures
[42]. Post-combustion capture removes CO
2 from the exhaust gas after combustion, while pre-combustion capture converts fossil fuels into a gaseous mixture of hydrogen and CO
2 before combustion
[43][44]. Oxy-fuel combustion involves burning fossil fuels in a mixture of oxygen and recycled flue gas, producing a flue gas stream that is primarily composed of CO
2 [45].
Post-combustion capture involves capturing CO
2 from power plant flue gases, which is the easiest and most widely used technology
[46]. The efficiency of this technology is relatively low compared to that of the other techniques, with capture rates between 85 and 90%, but it is cost-effective compared to other capture methods
[47].
Pre-combustion capture is used in gasification processes that turn fossil fuels into gas that can be burned cleanly
[48]. This technology can capture roughly 95% of the CO
2 produced, making it very efficient; however, it is expensive to use
[49].
Oxy-fuel combustion capture involves burning fuels with pure oxygen, producing flue gas with a high concentration of CO
2, which is easy to capture. It has the highest capture efficiency, up to 99%, and is a cost-effective method
[50].
Overall, while pre-combustion capture is the most efficient capture technology, it is expensive to implement
[51][52]. Post-combustion capture is the most cost-effective and widely used method, but its efficiency is lower than that of oxy-fuel combustion capture
[53].
The transport process involves moving the captured CO
2 from the capture site to a storage site. CO
2 can be transported via pipelines, ships, or trucks. Pipeline transportation is the most common method of CO
2 transport and is cost-effective over long distances
[54][55]. Ships and trucks are typically used for short distances or in areas where pipelines are not feasible
[56][57].
During storage, CO
2 is injected into a formation for long-term storage
[58]. Several types of geological formations can be used for CO
2 storage, including depleted oil and gas reservoirs, saline formations, and deep coal seams
[58][59]. Depleted oil and gas reservoirs are the most common storage option, as they have already been explored and developed for hydrocarbon production. Saline formations are large underground formations that contain brackish water and are not suitable for drinking or agriculture. Deep coal seams are another potential storage option, as they can adsorb CO
2 and release methane
[60][61][62].
The fourth component, utilization, refers to the process of utilizing the captured CO2 for various purposes. Instead of simply storing the CO2 underground, it can be put to beneficial use in different applications. Some common utilization methods include the following:
- EOR: The captured CO2 is injected into oil reservoirs to enhance oil production. CO2 helps reduce the viscosity of the oil, making it easier to extract.
- Industrial processes: CO2 can be used as a raw material in various industrial processes, such as chemical manufacturing or the production of synthetic fuels.
- Mineralization: CO2 can be reacted with certain minerals to form stable carbonates, which can be used in construction materials or other applications.
- Agricultural applications: CO2 can be used in agricultural practices, such as greenhouse farming or enhancing plant growth.
- Direct air capture (DAC): Using this technique, CO2 is extracted from the air and utilized for different purposes, such as carbon-neutral fuel production or carbon removal [60][61][62].
2.3. Different Methods of Carbon Storage
There are several methods with which to accomplish a carbon storage project, which are listed below:
- Geological storage: CO2 is stored in this method in formations such as depleted oil and gas reservoirs, saline aquifers, and coal beds [58].
- Ocean storage: This method involves storing CO2 in deep ocean water, where it can be dissolved and stored for long periods [63].
- Mineral carbonation: This method involves converting CO2 into stable carbonates through chemical reactions with minerals [64][65].
- BECCS: This method involves capturing CO2 emissions from biomass power plants and storing them in geological formations [66].
- DAC: This method involves capturing CO2 directly from the air using specialized equipment and storing it in geological formations [67].
- Industrial use: This is another important component of carbon dioxide utilization. CO2 can be used as a raw material in various industrial processes, such as chemical manufacturing or the production of synthetic fuels. This enables the conversion of CO2 into useful products, lowering emissions and fostering the development of a more sustainable future [67].
These methods, as shown in Figure 2, have their advantages and disadvantages and require careful consideration when implementing carbon storage projects [68].
Figure 2. Different methods of carbon capture storage and utilization.
2.3.1. Geological Storage
Geological storage involves injecting CO2 into geological formations such as depleted oil and gas reservoirs, aquifers, and coal seams [69]. This method is considered to be the most viable and widely used method for carbon storage due to the abundance of geological formations that can be used for storage [70].
Capturing CO2 from industrial processes, compressing it, and injecting it into underground geological formations are steps involved in the process of geological storage. Once trapped by cap rock or other geological features that prevent it from escaping into the atmosphere, the CO2 is permanently stored in the geological formations [1]. After this process, the storage location is monitored to make sure the CO2 is kept in place and does not escape into the environment.
Advantages of geological storage include the following:
- Large storage capacity: Geological formations have the potential to store large amounts of CO2, making them ideal for large-scale carbon storage projects [71].
- Proven technology: Geological storage has been used for decades to store natural gas and other substances, making it a proven and reliable technology [72].
- Permanent storage: CO2 stored in geological formations is trapped permanently, reducing the risk of emissions into the atmosphere [73].
- Synergies with existing infrastructure: Geological formations used for carbon storage are often located near existing oil and gas infrastructure, making it easier to transport and store CO2 [74][75].
Disadvantages of geological storage include the following:
- Potential for leakage: While geological formations are designed to trap CO2, there is a risk of leakage that could result in environmental damage and health risks [76].
- Limited availability of suitable sites: Not all geological formations are suitable for carbon storage, and finding suitable sites can be challenging [77].
- High costs: Geological storage can be expensive due to the costs of capturing, compressing, and transporting CO2, as well as the costs of monitoring and maintaining storage sites [73].
Geological storage has a larger capacity than other methods, such as ocean storage and mineral carbonation [78][79][80]; however, the decision to use this approach will be influenced by several considerations, including the cost of the process, the accessibility of storage locations, and the environmental concerns associated with this method [5][81].
2.3.2. Ocean Storage
Ocean storage involves capturing CO2 from industrial processes, compressing it, and transporting it to the sea. CO2 is then injected into deep ocean water, where it can be dissolved and stored for long periods [63]. The stored CO2 is then monitored to ensure that it remains dissolved and prevent it from escaping into the atmosphere [82]. This method is still in the experimental phase and requires further research to determine its feasibility and potential environmental impacts [83].
Advantages of ocean storage include the following:
- Large storage capacity: The deep ocean has the potential to store vast amounts of CO2, making it an attractive option for large-scale carbon storage projects [63].
- Natural carbon sinks: The ocean is a natural carbon sink, and storing CO2 in ocean water could potentially enhance the ocean’s ability to adsorb carbon from the atmosphere [84][85].
- Reduced risk of leakage: Unlike geological formations, the ocean is constantly in motion, which reduces the risk of CO2 leakage [86].
Disadvantages of ocean storage include the following:
- Environmental risks: Injecting large amounts of CO2 into the ocean could potentially have negative environmental impacts, such as ocean acidification and harm to marine life [63].
- Technological challenges: Injecting CO2 into the ocean requires specialized equipment and infrastructure, which can be expensive and challenging to implement [87].
- Uncertainty: The long-term effects of ocean storage on the environment and marine life are not yet fully understood, and further research is needed to determine its feasibility [88].
Compared to other methods of carbon storage, ocean storage has the advantages of a large storage capacity and reduced risk of leakage [79]. Nevertheless, the choice of this method will depend on a variety of factors, including the accessibility of suitable storage locations, the cost of the process, and the environmental risks associated with each method [89][90].
2.3.3. Mineral Carbonation
Mineral carbonation is a method of carbon storage that involves converting CO
2 into stable carbonates through chemical reactions with minerals
[91]. This method is still in the experimental phase and requires further research to determine its feasibility and potential environmental impacts
[83]. The process of mineral carbonation involves capturing CO
2 from industrial processes and exposing it to naturally occurring minerals that react with CO
2 to form stable carbonates. These carbonates can then be stored permanently in geological formations, such as depleted oil and gas reservoirs or deep saline aquifers
[1][71].
Advantages of mineral carbonation include the following:
-
Permanent storage: Carbonates formed by the carbonation of minerals are stable and can be stored permanently in geological formations
[71].
-
Potential for carbon-negative processes: Mineral carbonation has the potential to be a carbon-negative process, i.e., it removes more CO
2 from the atmosphere than it emits
[92].
-
Use of abundant minerals: The minerals used in mineral carbonation are abundant and widely available, reducing the cost and environmental impact of the technology
[93].
Disadvantages of geological storage include the following:
-
Technological challenges: Mineral carbonation requires specialized equipment and infrastructure, which can be expensive and challenging to implement
[65].
-
Slow reaction rates: The reaction rates involved in mineral carbonation are slow, which can limit the storage capacity and efficiency of the technology
[94].
-
Uncertainty: The long-term effects of mineral carbonation on the environment and geological formations are not yet fully understood, and further research is needed to determine its feasibility
[79].
Compared to other methods of carbon storage, mineral carbonation has the potential to be a carbon-negative process and utilize abundant minerals
[95][96]. Nevertheless, the choice of this method will depend on a variety of factors, including the accessibility of suitable storage locations, the cost of the process, and the environmental risks associated with each method
[90].
2.3.4. Bioenergy with Carbon Capture and Storage (BECCS)
BECCS, as another method of carbon storage, involves producing energy from biomass (such as plants) and capturing the CO
2 emissions generated during the process
[97][98]. The captured CO
2 is then stored underground or underwater
[15].
The advantages of BECCS include the potential for negative emissions, as the process removes CO
2 from the atmosphere, and the generation of renewable energy. Additionally, BECCS can be implemented using existing infrastructure, such as power plants; however, there are also some disadvantages to consider
[99][100]. The process of producing biomass requires land use, which can compete with other uses, like food production. Additionally, the technology is still in the early stages of development, and there are concerns about the cost and efficiency of the process
[101].
BECCS can be used in combination with other storage methods to address the climate crisis issue, though further research is needed to fully evaluate its potential
[102][103].
2.3.5. Direct Air Capture (DAC)
CO
2 is captured in this method directly from the air using chemical processes and stored underground or underwater
[15][103][104].
The advantages of DAC include the ability to capture CO
2 from any source, not just industrial processes, making it a potentially valuable tool for reducing atmospheric CO
2 concentrations
[105]. Additionally, DAC can be used in combination with other carbon storage methods to achieve greater emission reductions
[106]; however, there are disadvantages to consider. DAC is currently a very energy-intensive process, i.e., capturing and storing CO
2 requires a large amount of energy
[107]. Additionally, the technology is still in the early stages of development, and there are concerns about the cost and scalability of the process
[108].
DAC can be used in combination with other storage methods to address the climate crisis issue, though further research is needed to fully evaluate its potential
[105][108][109][110].
2.4. CCS Deployment Projects through Time
A chronological overview of the deployment of CCS projects has been provided in Table 1.
Table 1. An overview of the deployment of CCS projects over time.
Early development (2000s) [2][3] |
-
In the early 2000s, various pilot and demonstration projects were initiated to test the feasibility and effectiveness of CCS technologies.
-
Notable projects during this period include the Sleipner field project in Norway (started in 1996) and the Weyburn–Midale project in Canada (started in 2000).
|
Expansion and demonstration (2010s) [109] |
-
In the 2010s, there was an increase in the number of large-scale CCS projects, focusing on demonstration and commercialization.
-
The Boundary Dam CCS project implemented in Canada (started in 2014) and the Petra Nova project in the United States (started in 2016) showcased the viability of CCS technologies on a larger scale.
|
Government support and initiatives [6][44] |
-
Many countries started implementing supportive policies and funding programs to encourage the deployment of CCS projects.
-
Notable initiatives include the United Kingdom’s CCS Commercialization Program, the United States’ 45Q tax credit, and the European Union’s Innovation Fund.
|
International collaboration [2][3] |
-
Various international collaborations and partnerships were formed to advance CCS deployment globally.
-
The Carbon Sequestration Leadership Forum (CSLF), established in 2003, promotes information sharing and collaboration among governments, industry, and research organizations.
|
Current developments [3][14] |
-
Presently, CCS projects continue to be developed and implemented worldwide, with a focus on scaling-up deployment and reducing costs.
-
Countries like Norway, Canada, Australia, the United States, and the United Kingdom continue to lead in CCS deployment, while other nations are also actively exploring and implementing CCS projects
|
2.5. Leading Countries in the Field of CCS
Table 2 provides a list of countries that are considered leaders in the field of CCS, along with their storage methods and storage capacity.
Table 2. Leading countries in the field of CCS.
Country |
Storage Method |
Storage Capacity |
Norway [6] |
Norway primarily focuses on offshore storage in geological formations, specifically within the North Sea. |
Norway has significant storage potential, with an estimated offshore storage capacity of up to 70 billion tons of CO2. |
Canada [42] |
Canada has been exploring both onshore and offshore storage options. Onshore storage involves utilizing deep saline aquifers, while offshore storage is being studied in depleted oil and gas reservoirs. |
Canada has substantial potential for CO2 storage, with an estimated storage capacity exceeding 600 billion tones. |
Australia [63] |
Australia has been investigating various storage options, including onshore storage in deep saline aquifers and offshore storage in depleted oil and gas fields. |
Australia has significant storage potential, with an estimated capacity exceeding 400 billion tones. |
United States [69] |
The United States has been actively studying both onshore and offshore storage options. Onshore storage primarily focuses on deep saline aquifers, while offshore storage is being explored in depleted oil and gas fields. |
The U.S. has substantial storage potential, with an estimated capacity exceeding 13,000 billion tones. |
United Kingdom [15] |
The UK has been investigating offshore storage in depleted oil and gas fields beneath the North Sea. |
The UK has significant storage potential, with an estimated offshore storage capacity exceeding 70 billion tones. |
China [59] |
China has been increasing its efforts in CCS deployment and has several ongoing projects. |
The volume of CO2 storage in China is expected to reach approximately 8 million tons per year. |
Saudi Arabia [2] |
Saudi Arabia has also started investing in CCS technology and has plans for underground CO2 storage facilities. |
The volume of CO2 storage in Saudi Arabia is estimated to be around 5 million tons per year. |
Japan [54] |
Japan has been exploring CCS technology and has initiated pilot projects for underground CO2 storage. |
The volume of CO2 storage in Japan is projected to be approximately 4 million tons per year. |
South Korea [3] |
South Korea has shown interest in CCS and has started implementing pilot projects for underground CO2 storage. |
The volume of CO2 storage in South Korea is expected to be around 3 million tons per year. |
United Arab Emirates [74] |
The United Arab Emirates has also joined the CCS movement and has plans for underground CO2 storage facilities. |
The volume of CO2 storage in the United Arab Emirates is estimated to be approximately 2 million tons per year. |
2.6. Historical Data on CCS Capacity
Figure 3 shows the historical data on CCS between the years 2000 and 2023. The implementation rate is calculated by dividing the number of CCS projects implemented to develop a field by the total number of projects. The increasing trend suggests an improved general perception regarding CCS technology.
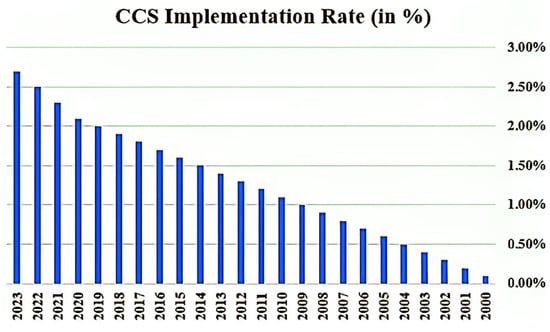
Figure 3. Historical data on CCS capacity.
As for the outlook until 2050, there are varying predictions depending on the global efforts and policies undertaken to mitigate carbon emissions. It is expected that the implementation of CCS technology will significantly increase in the coming years to help combat climate change; however, due to the rapidly changing nature of environmental policies and technological advancements, it is challenging to provide precise future predictions
[108].
Nonetheless, many experts and organizations are hopeful that CCS will play a crucial role in achieving global climate targets. It is anticipated that, by 2050, the implementation of CCS could rise to levels above 10
[108].
Table 3 tabulates the historical data provided in Figure 4, with a perspective on its application in petroleum engineering.
Figure 4. CCS as an alternative method for water injection.
Table 3. Historical data on CCS capacity, with perspectives on its application in petroleum engineering
[2][3][6][14][44][103][104][105][106][107][108][109].
Year |
CCS Implementation Rate (in %) |
Applications in Petroleum Engineering |
2000 |
0.10% |
Limited implementation in CO2-EOR [2]. |
2001 |
0.20% |
Continued use in CO2-EOR projects, with a slight increase in implementation [4]. |
2002 |
0.30% |
Further utilization of captured CO2 for enhanced oil recovery application [3]. |
2003 |
0.40% |
Ongoing use in CO2-EOR projects, contributing to increased oil production [14]. |
2004 |
0.50% |
The gradual growth of CCS implementation in CO2-EOR projects positively impacts oil production [6]. |
2005 |
0.60% |
Continued utilization of captured CO2 for enhanced oil recovery applications [74]. |
2006 |
0.70% |
Application of CCS in CO2-EOR projects, aiding in increased oil extraction from reservoirs [12]. |
2007 |
0.80% |
The steady growth of CCS usage in CO2-EOR operations supports enhanced oil recovery efforts [65]. |
2008 |
0.90% |
Continued implementation of CCS for enhanced oil production in certain reservoirs [44]. |
2009 |
1.00% |
The cumulative increase in CCS application contributes to enhanced oil recovery and carbon management [5]. |
2010 |
1.10% |
Further integration of CCS in CO2-EOR projects, aiding in sustainable oil production and emission reductions [1]. |
2011 |
1.20% |
Increasing implementation of CCS in CO2-EOR projects, supporting oil recovery and carbon mitigation strategies [104]. |
2012 |
1.30% |
Continued adoption of CCS in CO2-EOR for enhanced production and carbon management in petroleum engineering [103]. |
2013 |
1.40% |
Steady utilization of CCS for enhanced oil recovery, enabling sustainable oil production and reducing emissions [85]. |
2014 |
1.50% |
The growing incorporation of CCS in CO2-EOR projects to optimize reservoir management and reduce carbon footprints [78]. |
2015 |
1.60% |
Increasing implementation of CCS in CO2-EOR projects, supporting oil recovery and carbon mitigation strategies [7]. |
2016 |
1.70% |
Increased deployment of CCS technology, facilitating efficient CO2 utilization and improved reservoir performance [9]. |
2017 |
1.80% |
Advancements in CCS methods for reservoir monitoring, optimizing CO2-EOR projects in petroleum engineering [2]. |
2018 |
1.90% |
Continued integration of CCS in CO2-EOR, enhancing oil production and minimizing the environmental impact [6]. |
2019 |
2.00% |
Expanding the use of CCS for sustainable oil recovery, addressing emissions, and maximizing reservoir potential [44]. |
2020 |
2.10% |
Growing global focus on CCS for CO2-EOR, fostering sustainable practices in petroleum engineering [14]. |
2021 |
2.30% |
Increasing adoption of CCS to optimize oil recovery, meet emission targets, and support responsible petroleum operations [109]. |
2022 |
2.50% |
Maturing technology and wider implementation of CCS in petroleum engineering to ensure sustainable oil production [22]. |
2023 |
2.70% |
Continued growth of CCS in CO2-EOR projects, enhancing production efficiency and mitigating greenhouse gas emissions [86]. |
Moving towards 2050, the future of CCS in petroleum engineering is projected to be increasingly vital. As the industry strives for decarbonization and sustainable practices, CCS is expected to see further advancements and wider deployment. The integration of CCS with various reservoir management techniques, together with enhanced monitoring and innovative CO2 utilization methods, will contribute to maximizing oil recovery while minimizing the environmental impact. This comprehensive approach is anticipated to drive the development of efficient and sustainable petroleum engineering practices [108].
3. Typical Global CCS Science and Technology Infrastructures
Some typical global CCS science and technology infrastructures include the following:
- CCS research centers: These infrastructures focus on conducting scientific research and technological development related to CCS. They typically have advanced laboratories equipped with state-of-the-art equipment for analyzing and testing various aspects of CCS technologies.
- Large-scale CCS demonstration projects: These infrastructures are designed to showcase the viability and effectiveness of CCS technologies at a commercial scale. They involve capturing CO2 emissions from power plants or industrial facilities and storing them underground. These projects often involve collaborations between governments, research institutions, and industry partners.
- CCS monitoring networks: These infrastructures consist of a network of sensors and monitoring stations that track the movement and behavior of stored CO2 They provide real-time data on factors such as CO2 leakage, pressure changes, and geological stability to ensure the safety and effectiveness of CCS operations.
- CCS simulation and modeling facilities: These infrastructures utilize advanced computer simulations and modeling techniques to predict the behavior and performance of CCS systems under different scenarios. They help optimize design parameters, assess potential risks, and guide decision making in the deployment of CCS technologies.
- CO2 transport infrastructure: This infrastructure includes pipelines and transportation networks specifically designed for the efficient and safe transport of captured CO2 from capture sites to storage sites. It requires careful planning and engineering to ensure the integrity of the pipelines and minimize leakage during transportation.
- Geological storage sites: These infrastructures consist of suitable underground formations where captured CO2 can be safely stored for long periods. They require detailed geological surveys and assessments to identify appropriate storage sites with characteristics such as permeability, porosity, and containment capacity.
- CO2 utilization facilities: In addition to storage, some infrastructures focus on developing technologies for utilizing captured CO2 in various industrial processes. These facilities explore avenues such as converting CO2 into valuable products or using it for enhanced oil recovery.
Characteristics of these infrastructures include the following:
- Interdisciplinary collaboration: CCS infrastructures often involve collaboration between scientists, engineers, policymakers, and industry experts to address the complex challenges associated with CCS technologies.
- Long-term planning: Developing and maintaining these infrastructures require long-term planning and funding commitments due to the scale and complexity of CCS projects.
- Regulatory compliance: CCS infrastructures need to adhere to strict environmental and safety regulations to ensure the protection of human health and the environment.
- International cooperation: Many CCS infrastructures involve international collaboration and knowledge sharing to accelerate technology development and deployment globally.
- Continuous improvement: CCS infrastructures focus on continuous improvement and innovation to enhance the efficiency, cost-effectiveness, and environmental performance of CCS technologies [109][110].
4. Applicability of Carbon Storage Methods in the Oil and Gas Industry
Methods of carbon storage have been discussed in Section 2.3. This section focuses on the applicability of these methods in the oil and gas industry.
-
Geological storage: This method can be used to enhance oil and gas recovery, a process known as EOR
[24]. By injecting CO
2 into depleted reservoirs, the CO
2 can help mobilize and extract remaining oil and gas reserves that would otherwise be difficult to recover. This process can also help reduce the carbon footprint of the oil and gas industry by storing CO
2 underground
[111].
-
Ocean storage: This method is not commonly used due to the environmental risks and technological challenges involved in ocean storage
[54].
-
Mineral carbonation: This method is not commonly used due to the technological challenges and slow reaction rates involved in mineral carbonation
[94].
-
BECCS: This method can be used to generate renewable energy and reduce the carbon footprint of oil and gas operations
[112]. Biomass can be produced from different sources, including agricultural waste and dedicated energy crops, and the resulting energy can be used to power oil and gas operations
[113].
-
DAC: This method is currently not widely used as it is a very energy-intensive process requiring large amounts of energy to capture and store CO
2 [114][115].
Overall, the oil and gas industry can benefit from the use of carbon storage methods, such as geological storage and BECCS, to reduce its carbon footprint and enhance oil and gas recovery
[116]; however, additional research is required to adequately assess the potential of this technique and develop new as well as innovative approaches to carbon storage in the industry
[114][117].
5. Advantages and Disadvantages of the Carbon Storage Method
The main advantages of CCS are lowering greenhouse gas emissions and reducing the adverse effects of climate change
[118]. CCS can assist in lowering the amount of CO
2 released into the atmosphere by capturing and storing CO
2 emissions, which can help lower global warming
[2][119].
CCS can also help improve the environmental performances of industrial processes by reducing their carbon footprints
[120][121]. This can be particularly beneficial for industries that are highly dependent on fossil fuels, like the oil and gas industry, which is a significant contributor to global emissions, by reducing their carbon emissions and improving their sustainability
[120].
CCS can assist in decreasing the industry’s reliance on fossil fuels and boost the accessibility of low-carbon energy sources, like renewable energy, by capturing and storing CO
2 emissions
[122][123]. The shift to a low-carbon economy can also be assisted by CCS
[124]. CCS can also provide a bridge between traditional fossil fuel-based energy systems and renewable energy systems
[125]. By capturing and storing CO
2 emissions, CCS can pave the way for a more sustainable energy future
[126][127].
However, there are also some challenges and concerns associated with CCS. One of the main challenges is the cost of implementing the technology, which can be high due to the need for specialized equipment and infrastructure
[128]. Additionally, there are concerns about the safety and security of storing large volumes of CO
2 underground or subsea, as well as the potential for CO
2 leakage and environmental damage
[129][130].
Despite these challenges, CCS has the potential to provide significant economic and social benefits
[131]. For example, the implementation of CCS can create new job opportunities in the development and operation of the technology and its associated infrastructure
[132]. Additionally, by reducing the carbon footprint of industrial processes, CCS can help improve the competitiveness of industries by reducing their operating costs and increasing their efficiency
[133][134]. This can be particularly beneficial for large industries, such as oil and gas, which can benefit from improved environmental performance and increased profitability
[135][136][137].
6. CCS and EOR
Water flooding has limitations, like the amount of water available, the cost of water treatment, and the potential for formation damage
[138]. In this regard, CCS can be used as an alternative method to water flooding in oil reservoirs by injecting CO
2 into the reservoir (
Figure 4), with potential cost-saving and efficiency benefits
[138][139][140].
The advantages of using CCS as an alternative to water flooding include the following:
-
Reduced water usage: CCS does not require large amounts of water, which can be a significant cost-saving method for oil producers in regions with water scarcity
[141].
-
Improved oil recovery: Oil recovery could be improved with the injection of CO
2 through a reduction in oil viscosity and an increase in reservoir pressure
[142].
-
Reduced formation damage: The injection of CO
2 is less likely to cause formation damage than water flooding, as CO
2 does not directly react with the reservoir rock
[143][144].
-
Reduced environmental impact: Climate change can be mitigated through CCS by lowering the amount of CO
2 emissions into the atmosphere
[2].
However, there are also challenges associated with using CCS as an alternative to water flooding, such as the following:
-
High costs: CCS involves significant upfront costs for capturing, compressing, and transporting CO
2, making it more expensive than other water injection methods
[145].
-
Logistics and infrastructure requirements: CCS requires significant infrastructure and transportation systems, which can make its implementation difficult in some locations
[146].
-
Environmental risks: Any potential risks to the environment, such as CO
2 leakage, must be carefully considered and mitigated
[147].
Quantitative data can be used to demonstrate the potential benefits and challenges associated with using CCS for oil recovery. For example, it was shown that using CO
2 for oil recovery can increase the amount of oil that can be extracted from a reservoir by up to 20%. In addition, CCS can reduce greenhouse gas emissions by up to 90%
[148][149].
There are also quantitative data that show the challenges associated with using CCS for oil recovery
[150]. A study conducted by the International Energy Agency found that the cost of implementing CCS for oil recovery can range from USD 30 to USD 70 per ton of CO
2 captured
[151]. The risk of CO
2 leakage from storage sites can range from 0.01% to 1% per year
[152].
6.1. Potential Use of CCS and EOR as a Combined Approach
The combined approach of CCS and EOR has the potential to significantly reduce carbon emissions and increase oil recovery in the petroleum industry
[24]. With CCS, CO
2 emissions from industrial processes are captured and fed into underground reservoirs. EOR, on the other hand, injects fluid into a reservoir to increase oil recovery
[153].
By combining CCS and EOR, CO
2 emissions can be captured and stored underground while also being used for EOR
[154]. The injected CO
2 can help mobilize and displace oil, increase recovery rates, and reduce the need for additional drilling
[155]. This not only increases oil production but also reduces the carbon footprint of the petroleum industry by preventing emissions from being released into the atmosphere
[134].
The potential benefits of this combined approach are numerous. It can help extend the lifetimes of mature oil fields, increase the amount of oil recovered from existing wells, and reduce the need for new drilling operations
[156]. Additionally, it can provide a solution for reducing carbon emissions from industrial processes in the petroleum industry
[98][157].
However, there are also challenges associated with this approach. The cost of implementing CCS and EOR technologies can be high, and there may be technical challenges associated with storage and injection processes
[54][158]. There may also be regulatory barriers and public perception issues that need to be addressed
[159].
6.2. Economic Feasibility of CCS and EOR
The economic feasibility of CCS and EOR technologies is an important consideration for the petroleum industry
[160]. These technologies can be costly to implement, and their economic viability depends on a variety of factors, including the cost of the technology, the price of oil, and the regulatory environment
[101].
Depending on the individual technology being used and the geological features of the reservoir, the cost of CCS and EOR technologies can vary
[161]. CCS technologies involve capturing, transporting, and storing CO
2, which can be expensive
[162]. EOR technologies require injecting fluids into a reservoir, which can also be costly. The cost of these technologies may be offset by the increased oil recovery rates and potential revenue from the sale of captured CO
2 for use in other industries
[24].
The potential benefits of CCS and EOR technologies are numerous. EOR technologies can increase the amount of oil that can be recovered from a reservoir, which can lead to increased revenue for petroleum companies
[24][163]. CCS technologies can help reduce carbon emissions and allow petroleum companies to comply with regulations and avoid potential penalties
[24]. Additionally, the captured CO
2 can be sold to other industries for use in enhanced oil recovery, the carbonation of concrete, or other industrial processes
[164].
The economic feasibility of CCS and EOR technologies also depends on the price of oil. When the price of oil is high, the economic benefits of EOR technologies can be significant
[165]; however, when the price of oil is low, the economic feasibility of EOR technologies may be more challenging. CCS technologies, on the other hand, may be more economically feasible in the long term, as regulations and carbon pricing mechanisms are implemented
[166].
The regulatory environment is also an important consideration for the economic feasibility of CCS and EOR technologies
[54]. Government incentives, such as tax credits and grants, can help offset the cost of implementing these technologies. Additionally, regulations that limit carbon emissions can create a market for captured CO
2, making it more economically feasible for petroleum companies to invest in CCS technologies
[167].
6.3. Technical Challenges and Opportunities Associated with CCS and EOR
CCS and EOR are two related technologies that offer opportunities and challenges for the petroleum industry
[105]. CCS involves removing CO
2 from industrial sources and storing it in geological formations such as coal seams, deep saline deposits, and depleted oil and gas reservoirs
[58][168]. EOR involves injecting CO
2 into oil reservoirs to enhance oil recovery by reducing oil’s viscosity and increasing its mobility
[153].
One of the technical challenges associated with CCS and EOR is the design and construction of storage reservoirs. The reservoirs must be able to contain large volumes of CO
2 and maintain the pressure required to keep CO
2 in a liquid or supercritical state
[169]. The reservoirs must also be located in areas that are safe and accessible for injection operations
[170].
To address these challenges, researchers are exploring novel injection techniques, such as foam injection, which can improve the mobility of CO
2 in the reservoir and reduce the risk of CO
2 breakthrough
[171]. Other techniques include the use of surfactants and polymers to improve the sweep efficiency of CO
2 and the use of nanoparticles to enhance the wettability of the reservoir rock
[156].
Foam injection is a technique that involves injecting CO
2 mixed with a foaming agent into the reservoir
[172]. The foaming agent creates bubbles in the CO
2 that increase the viscosity of the mixture and improve its mobility in the reservoir
[173]. This technique has been shown to increase the amount of CO
2 that can be injected into the reservoir and reduce the risk of CO
2 breakthrough
[174].
Surfactants and polymers are chemicals that can be added to the CO
2 injection stream to improve its sweep efficiency
[175]. Surfactants reduce the surface tension between the CO
2 and fluids within a reservoir rock, allowing the CO
2 to flow more easily through the rock pores
[176]. Polymers can increase the viscosity of the CO
2 plume, helping it to sweep more effectively through the reservoir
[177]. These techniques have been shown to increase the amount of oil that can be recovered from the reservoir and improve the overall efficiency of EOR operations
[178][179].
Nanoparticles are tiny particles that can be added to the CO
2 injection stream to enhance the wettability of the reservoir rock
[180]. By modifying the surface properties of the rock, nanoparticles can improve the contact angle between the CO
2 and oil, leading to an increase in oil recovery rates
[181]. This technique is still in the early stages of development, but initial results have been promising
[182][183].
Overall, these techniques represent state-of-the-art solutions for improving the efficacy of CCS and EOR operations
[184]. While each technique has its unique advantages and limitations, they all have the potential to significantly increase the amount of oil that can be recovered from existing reservoirs while reducing greenhouse gas emissions
[177].
Another technical challenge is the management of safety and security in the CCS process
[158]. CO
2 is a greenhouse gas and can pose a risk to human health if released in large quantities
[119]. Therefore, it is important to ensure the safe and secure storage of CO
2 in reservoirs
[1]. This involves monitoring reservoirs for leaks, developing emergency response plans, and implementing security measures to prevent the intentional or accidental release of CO
2 [185].
6.4. Environmental Impacts of CCS and EOR
Technologies like CCS and EOR have the potential to lower greenhouse gas emissions while also enhancing air quality
[186][187]. CCS can lessen the quantity of greenhouse gas emissions discharged into the atmosphere by capturing and storing CO
2 emissions from industrial sources, hence preventing climate change
[188][189]. EOR, on the other hand, can reduce the need for new oil exploration and production, which can reduce greenhouse gas emissions associated with these activities
[190].
CCS and EOR can improve air quality by lowering harmful pollutants like sulfur dioxide, nitrogen oxides, and particulate matter, in addition to lowering greenhouse gas emissions
[187]. These pollutants can have significant impacts on human health and the environment, and their reduction can lead to improved air quality and public health
[191].
However, there are also potential environmental impacts associated with CCS and EOR technologies. For example, injecting large amounts of CO
2 into a reservoir can change the physical and chemical properties of a reservoir’s rocks, affecting local ecosystems
[5]. Additionally, the transport and storage of CO
2 may pose risks to the environment and human health if not properly managed
[192].
The solutions for mitigating the potential environmental impact of CO
2 injection include conducting thorough risk assessments before the process, analyzing geological properties, and detecting potential leakage pathways as well as ecosystem impacts
[193]. Ongoing monitoring programs can also be implemented to promptly address any environmental impacts. Additionally, using enhanced oil recovery techniques may reduce the amount of CO
2 for underground storage
[194].
CO
2 can be transported via pipelines or ships with proper safety measures in place. Geological formations can be used for CO
2 storage, but continuous monitoring is required to ensure safety
[195]. Carbon capture and storage technologies can also be implemented to minimize CO
2 transport and storage needs
[196].
To integrate CCS and EOR technologies in a safe and environmentally responsible manner, industry experts and researchers are developing best practices and standards
[197]. This entails carrying out exhaustive environmental impact studies, implementing monitoring as well as mitigation measures, and interacting with local stakeholders as well as communities to make sure their concerns are heard and taken seriously
[198].
6.5. Regulatory and Policy Landscape Surrounding CCS and EOR
The regulatory and policy landscape surrounding CCS and EOR technologies is complex and varies widely depending on the country and region
[166]; however, many governments around the world have implemented incentives and regulations aimed at promoting the adoption of these technologies
[19].
The implementation of carbon pricing mechanisms, such as carbon taxes or cap-and-trade systems, is one of the most important incentives for CCS and EOR. These policies impose a cost on carbon emissions, encouraging businesses to cut emissions and spend money on low-carbon technology like CCS and EOR
[199]. Governments occasionally offer additional financial incentives to businesses that invest in this technology, such as tax credits, grants, or loan guarantees
[200].
In addition to incentives, many governments have also implemented regulations aimed at promoting the adoption of CCS and EOR
[201]. For instance, the Environmental Protection Agency (EPA) in the US has enacted regulations, under the Clean Air Act, mandating the incorporation of CCS technology into new power plants to lower carbon emissions. Similarly, the European Union has established regulations, under the Emissions Trading System, that require large emitters to reduce their emissions or purchase emission credits
[202].
Other governments have implemented policies aimed at promoting the development of CCS and EOR infrastructure
[203]. For example, the United Kingdom has established a network of CO
2 pipelines and storage sites, and Canada has implemented regulations that require oil producers to reduce their emissions and invest in CCS and EOR technologies
[204][205].
6.6. Role of Public Perception and Stakeholder Engagement in the Successful Implementation of CCS and EOR
Public perception and stakeholder engagement play crucial roles in the successful implementation of CCS and EOR technologies
[206]. These innovations could boost oil recovery and decrease greenhouse gas emissions, but they also face significant challenges related to public perception, stakeholder engagement, and social acceptance
[206][207]. Many people are skeptical of these technologies and view them as risky or unnecessary. This skepticism can be attributed to a lack of understanding of how these technologies work, as well as concerns about their safety and potential environmental impacts. For example, some people may be concerned about the possibility of CO
2 leaks from storage reservoirs or the impact of injecting chemicals into oil reservoirs
[208][209].
CO
2 leaks from storage reservoirs can pose a risk to both human health and the environment
[185]. Exposure to high levels of CO
2 can cause asphyxiation and other health problems, and if a leak were to occur in an area with a high population density the consequences could be catastrophic
[210][211]. In addition, the emission of a large amount of CO
2 into the atmosphere can contribute to climate change
[212] and compromise the time as well as capital invested in CCS projects
[213].
To mitigate these risks, there are several strategies that can be employed
[214]. First and foremost, it is important to select storage sites that are geologically stable and secure, with a low risk of leaks
[214][215]. Storage sites should also be monitored regularly to detect any leaks early and address them quickly
[216]. Furthermore, emergency response plans must be in place to ensure a rapid and effective response in the event of a leak
[217].
The injection of chemicals into oil reservoirs can also pose risks, particularly in terms of the potential contamination of groundwater or the release of harmful substances into the environment
[218][219]. To mitigate these risks, it’s important to use chemicals that are proven to be safe and have a low risk of causing harm
[220]. Additionally, injection operations should be monitored closely to detect any leaks or incidents as early as possible. Proper well construction and maintenance can also help to prevent leaks or accidents
[221].
To address these concerns and increase public acceptance of CCS and EOR technologies, it is important to engage stakeholders and communicate the benefits and risks of these technologies clearly and transparently
[222]. This includes engaging with communities near storage and injection sites, as well as with environmental and community groups, industry representatives, and government agencies
[223].
Stakeholder engagement should be a collaborative process that involves listening to and addressing concerns, sharing information about the benefits and risks of these technologies, and involving stakeholders in the decision-making process
[224]. This can help to build trust and increase public acceptance of CCS and EOR technologies
[223].
In addition to public perception and stakeholder engagement, there are also technical and economic challenges associated with the implementation of CCS and EOR technologies
[127][225]. These include the design and construction of storage and injection sites, the cost of implementing these technologies, and the availability of suitable geologic formations for storage and injection
[226].
6.7. Application of CCS and EOR in Different Geological Settings
CCS and EOR technologies have the potential to be applied in a variety of geological settings, including unconventional reservoirs and offshore fields
[227]; however, there are some unique challenges associated with applying these technologies in these settings
[228].
Unconventional reservoirs, such as shale gas and tight oil formations, have lower permeability and porosity than conventional reservoirs, which can make it more difficult to inject CO
2 and recover oil
[229][230]. In addition, the geology of these formations is often more complex, which can make it more difficult to predict the behavior of injected fluids
[231].
Despite these challenges, there is significant potential for CCS and EOR in unconventional reservoirs. For example, CO
2 injection can help to enhance the recovery of oil and gas from these formations, which can increase production and reduce the need for new wells
[24]. In addition, CCS can help reduce greenhouse gas emissions from unconventional oil and gas production, which is a significant source of emissions
[189].
Offshore fields also present unique challenges for CCS and EOR. One of the main challenges is the distance between an injection site and a production platform, which can make it more difficult and expensive to transport CO
2 and other fluids
[232]. In addition, the harsh environment of offshore fields can make it more difficult to design and construct storage and injection facilities
[233].
Despite these challenges, there is also significant potential for CCS and EOR in offshore fields
[234]. For example, offshore fields often have significant CO
2 storage capacity, which can help to reduce emissions from offshore oil and gas production
[235]. In addition, EOR can help increase oil recovery from offshore fields, hence reducing the need for new wells
[236].
6.8. Integration of CCS and EOR with Other Renewable Energy Sources
The integration of carbon CCS and EOR technologies with other renewable energy sources has the potential to create a more sustainable energy system
[237][238]. Together, these technologies can reduce greenhouse gas emissions from fossil fuel production and increase the use of wind and solar as renewable sources of energy
[239].
One way to integrate CCS and EOR with renewable energy sources is to use CO
2 captured from power plants or industrial processes for EOR
[24]. This process involves injecting CO
2 into oil reservoirs to improve oil recovery while also storing it underground
[240]. By using CO
2 from renewable energy sources, such as biogas or biomass, it is possible to create a closed-loop system that reduces greenhouse gas emissions and increases oil production
[241].
Another way to integrate CCS and EOR with renewable energy sources is to use renewable energy to power CCS and EOR operations
[242]. For example, wind and solar power can be used to generate electricity to power CO
2 capture and compression, as well as EOR operations
[243][244]. This can help to reduce the carbon footprints of these operations and make them more sustainable in the long term
[245].
Additionally, the integration of CCS and EOR with other renewable energy sources, such as geothermal and hydroelectric power, is a possibility
[246]. For example, geothermal power can be used to generate steam for EOR operations, while hydroelectric power can be used to power CO
2 capture and compression
[90]. These linkages could contribute to the development of a more environmentally friendly energy system that uses more renewable energy sources and emits less greenhouse gases
[247].