Machine learning algorithms, namely- linear regression, logistic regression, support vector machines, discriminant analysis, naïve bayes, decision trees, and artificial neural network, will significantly influence the lubricant industry in coming decades, enabling the development of predictive models for lubricant performance, wear analysis, and formulation optimization. These algorithms have shown promise in leveraging complex datasets to provide insights into tribological behavior, paving the way for more efficient and tailored lubricant solutions.
1. Introduction
The modern world is dependent on versatile machinery that is susceptible to continuous friction and wear. As a result, numerous lubricants and additives have been developed to reduce the cost associated with friction and wear
[1]. As per the literature, effective use of lubricants could contribute from 1% to 1.55% of the yearly gross domestic product (GDP) of the United States
[2][3][4]. Therefore, effective lubrication is extremely important to strengthen the national economy. Lubricants can be categorically divided into three types: liquid, solid, and gaseous
[5][6]. Each type has its own application, but overall the purpose is the same: optimizing friction and wear.
Among all lubricants, liquid lubricants have unique functional features that have helped them expand their applicability over many years
[7][8]. Solubility, viscosity, heat capacity, wettability, dampening ability, resistance to corrosion, wear, and friction are typical characteristics of liquid lubricants
[9][10][11]. Engineers have added solid particles to liquid lubricants and utilized their synergy to reduce friction and wear
[12]. Tribologists have also developed superior lubricants that can provide high thermal stability, exhibit low volatility, and have a broad liquid range
[13][14]. Therefore, the list of lubricants and their properties has become innumerable nowadays. As a result, it became difficult even for an expert to choose the best lubricant or simply predict the optimum condition for a chosen lubricant without going through a series of trials and errors. In addition, oil analysis is important to maintain the reliability of the equipment and enhance its lifespan. However, using conventional techniques, a data analyst can observe the tribological failure and take steps. But if an earlier prediction could be made, that could minimize the breakdown time. Therefore, tribologists have left their footprints in the computational field and found a wide potential to utilize ML algorithms to predict the optimum lubricant for tribological applications
[15].
Machine learning is the study of algorithms that can train and improve themselves through observation. It can be carried out in two ways: (1) supervised learning and (2) unsupervised learning. Both of these types have their pros and cons. As a result, they need to be chosen wisely. Due to the complexity of parameters and methods, computer scientists and tribologists are working together to develop unique tools to predict optimum lubricants and optimum parameters to reach superior performance. Therefore, this approach’s success opens up wide potential to minimize the time and money associated with trial and error, which could strengthen the economy to a great extent
[15]. At the current status quo, many tribological studies are devoted to the estimation of the marginal life of lubricants
[16][17][18][19]. In practice, the prediction of the limit state for a lubricant is dependent on the manufacturer’s recommendation. When a pre-estimated service life is finished, an oil change is needed. However, the actual health of oil might be better to go on or could be already much worse even before the pre-estimated timeline. Therefore, to optimize the usage of lubricants, continuous monitoring of oil is a strong tool to save machine life and maintenance costs. By monitoring the performance of a lubrication system in real time, it is possible to detect potential issues before they become more serious problems. This can improve the reliability of the lubricants and the performance of the equipment. Therefore, with the development of accurate and efficient models, ML is poised to revolutionize the industry in the coming years
[15]. Companies that adopt these technologies will be better positioned to deliver high-performance lubrication solutions that are optimized for specific applications while also reducing downtime and maintenance costs.
2. Machine Learning
Machine learning could be simply addressed as a computer program that can learn from experience (“E”), with respect to some tasks (“T”), and performance measures (“P”). As per Tom Mitchell, the performance of ML at tasks in “T”, as measured by “P” improves with experience “E”
[20]. ML is a subset of artificial intelligence (AI), which helps computers act without explicit programming and instead utilizes the concept of statistics. ML has been widely utilized to find data patterns to make predictions. Nowadays, ML has advanced from pattern recognition studies and is capable of focusing on the recognition of patterns and regularities in data
[21].
2.1. Machine Learning Types and Processes
Machine learning techniques can be categorically divided into supervised learning and unsupervised learning
[22][23]. Each of these types consists of different processes and algorithms, as shown in
Figure 1.
Figure 1. Categorical classification of machine learning applications as per Mathworks.
In the case of supervised learning, the model has access to both the training data and their labels, and the model can be trained on the labeled data to perform prediction tasks on any unseen data. The supervised learning task can be formulated as a classification or a regression problem
[24]. Classification provides discrete-valued output. It is helpful to predict a characterization for a particular case; for a naive example, machine learning in tribology can predict if wear is coming from a specific type of coated surface or an uncoated surface, which is a discrete-valued output
[25].
Regression, on the other hand, provides a continuous numerical value. It is helpful to estimate any relationship between variables. Some of the common regression algorithms are linear regression and logistic regression, to name a few. One example of regression could be the investigation of the relationship between the coefficient of friction (COF) and surface roughness in sliding contact
[26][27]. For instance, let us consider a study where different sample surfaces with varying roughness values are subjected to sliding against a counter material. The COF is measured under controlled conditions, and the corresponding surface roughness parameters (Ra, Rq, Rsk, and Rku) are quantified for each sample. A regression analysis could then be performed to determine the correlation between the COF and surface roughness, allowing for the formulation of a predictive model. Such a model could help estimate the friction behavior of similar materials with known surface roughness, aiding in the design and optimization of tribological systems.
For unsupervised learning, no labeled data is provided to the model; rather, an unlabeled data set is fed, and the capabilities of the model are utilized to find the hidden structures in the dataset. Under the unsupervised learning category, cluster analysis is helpful to group a similar set of objects in one group while grouping another set of similar objects in another group. The wear particle data obtained from the lubricated system could be analyzed using this technique. Clustering can form distinct clusters of data that share similarities
[28]. Such clustering can provide insights into the wear mechanisms, lubricant effectiveness, or the presence of any irregular wear conditions.
2.2. Machine Learning Algorithms
There are multiple algorithms available to utilize the characterization of a dataset. Each such algorithm needs a unique approach to learning. The choice of one algorithm for favoring a particular benefit could cause a tradeoff of other benefits, including accuracy, complexity, and speed
[24]. Therefore, the success of an algorithm depends on the specific nature of the problem, its complexity, cost, and often trial and error.
Currently, there are different platforms to utilize ML algorithms, such as Matlab, Python, C, and C++, to name a few. In
Figure 1, different algorithms are presented that are compatible with the Matlab platform
[15].
2.3. Explored Machine Learning Algorithms
Machine learning is a process that involves computer programs using software such as MATLAB and Python and needs to be structured following some algorithms. Scientists have explored many fundamental algorithms for lubrication, and a few of them have repeatedly appeared in tribological studies, such as linear regression, logistic regression, support vector machines, discriminant analysis, Naïve Bayes, decision trees, and artificial neural networks.
3. Application of Machine Learning Algorithms for the Lubricant Industry
The lubricant industry is heading towards automation through condition monitoring and useful life prediction. This shift is not only happening on the experimental side to choose a lubricant; rather, it starts with the extraction of the crude oil from the oil bore
[29]. The geological data and drill bit condition monitoring were a primary focus for safe oil extraction. When the crude oil is purified and assigned as lubricants, monitoring is very important to ensure a safe operation for the machine with minimum breakdown. For that, the condition of the lubricant is critical. In addition, at the design phase, the prediction of COF and wear is important to avoid unwanted machine breakdown due to lubrication failure. If the algorithm is trained well, it will predict with higher accuracy, which would be beneficial to designing lubricants with superior qualities. In addition, there have been studies where experimental parameter prediction was a key concern to identify failure conditions. Also, ML algorithms have been utilized for film thickness prediction, which dictates lubricant performance significantly. Overall, the recent progress of ML algorithms for lubrication could be segmented into the following four categories:
-
Predicting experimental parameters;
-
Predicting film thickness;
-
Predicting COF and wear;
-
Lubricant condition monitoring.
3.1. Predicting Experimental Parameters
Experimental parameter prediction is an important aspect where ML could be utilized. In a few earlier expeditions, wear profiles were inspected and trained against their operating conditions in order to enable the algorithm to predict the experimental conditions for any similar wear profile. This prediction is important because it can tell if any experimental condition has gone wrong. If there is significant wear observed, then the prediction can illustrate the condition behind that wear so that the operator can improvise such extreme conditions quickly to minimize that condition deliberately. Also, performing tests under critical conditions might be more convenient for computer simulation than real experiments.
In the recent past, Gong et al.
[30] proposed an approach for simulating the tribochemistry, wear, and stress of a general fully formulated oil and found that tribofilm growth can be promoted by temperature and shear. Information from such simulations could be helpful in training ML models to predict experimental conditions. Also, molecular dynamic simulation can help predict the lubricant’s performance and evaluate its lubrication mechanisms. These techniques have been proven helpful to complement experimental observation to evaluate lubricant performance to some extent. Therefore, parameters from simulations are often used as descriptors to evaluate lubricant performance
[31].
3.2. Predicting Film Thickness
ML has been implemented to predict the film thickness of lubricants. This is important for gearboxes, where oil lubrication restricts the real contact between gear teeth and reduces friction, heat buildup, vibration, and corrosion. Ali et al.
[32] prescribed a lambda ratio (λ) to predict the fatigue life of the gears, where λ is the ratio between film thickness and RMS surface roughness. Basically, the factors that affect the λ ratio are load, temperature, surface roughness, and gear speed
[33]. The film thickness could be derived using the following equation
[32]:
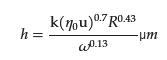
Here,
η0 is the dynamic viscosity of the lubricant in Pa·s,
k = 1.6 α
0.6 E
0.03, α = pressure-viscosity co-efficient in mm
2/N,
R = equivalent radius in m, and
ω = load applied normal to the line of contact in N/m. It was reported that gears usually operate in the elastohydrodynamic and boundary regimes
[32]. In the boundary regime, the film thickness becomes lower, and contact between the tribo-pairs is likely to happen
[3][34][35]. Therefore, knowledge about film thickness is very important to design and monitor oil performance. As per their studies, the network simulation conducted by MATLAB Simulink attained 100% success in predicting and classifying at high speed
[32].
3.3. Predicting COF and Wear
The prediction of COF and wear rate is important from a research and development point of view. A lubricant may provide good performance at one operating condition but may not be effective at other conditions. Predicting their best fit-in situation is important to formulate novel lubricants with superior performances. ML has started to ease this task by helping to predict the COF and wear values for extreme conditions, provided that the algorithm is trained with the data that was obtained from tests previously.
3.4. Lubricant Condition Monitoring
Lubricant plays an important role in reducing friction, wear, and associated costs in machinery. Therefore, it is crucial to monitor the lubricant’s conditions regularly. In small-scale applications, periodic checks by maintenance technicians can ensure the safe usage of a lubricant. However, on sites such as wind turbines or in space, regular checking might be difficult. Also, the opportunity cost of inspection could be higher if the lubricant condition is monitored periodically by the shutdown of the running machines. In order to reduce these costs, lubrication condition monitoring (LCM) plays a very vital role. Manghai et al.
[36] reviewed brake fault monitoring and highlighted the significance of ML in that process. For lubricant fault monitoring, a few classes of parameters hold significance.
Continuous lubrication condition monitoring is especially important for large-scale machine tribo-pairs, wind turbine gearsets, and large plants where regular maintenance might be difficult or may interrupt operating hours. Such interruption could lead to a significant reduction in production, and therefore, automatic condition monitoring could be a great tool to implement. In recent years, companies like SKF have offered remote diagnostic services for machinery that help monitor machine health regularly
[37]. Schaeffler Group also offers condition monitoring services for customers, where vibration and temperature are used
[38]. A vibration and temperature monitoring system involves a set of tools to measure one or more parameters in order to identify changes in the behavior of machinery. The key advantage of such monitoring is that it helps schedule maintenance activities based on predictive analysis. In addition to temperature and vibration, other parameters such as load, material hardness, and lubricant properties also play an important role and can help predict the service life of lubricants. In some recent research articles in this area, ML algorithms such as ANN, decision trees, Naïve Bayes, and SVM have been utilized.
4. Future of ML in the Lubrication Industry
Lubricant design and development over the last century were somewhat dependent on trial and error
[39]. Now that ML has been introduced in the lubricant industry, future prospects will undoubtedly be influenced by this technique. Lubricant performance depends on the operating conditions, lubricant properties, and material-pair properties. Therefore, there is scope to incorporate a variety of parameters under machine learning other than those that have already been considered. In recent studies, it was observed that friction and wear can be correlated not only to sliding speed, sliding distance, and normal load but also to properties such as hardness, yield strength, tensile strength, and ductility
[40]. It is very likely that ML descriptors will incorporate these variables to project COF and wear and may be able to further predict the associated real-time cost of energy due to such interaction.
Moreover, it is known that to reduce friction and wear, lubricant is introduced between tribo pairs, where the shear strength of the lubricant needs to be less than that of the mating surfaces. Otherwise, there will be abrasion due to the lubricants. Therefore, when using additives or solid lubricants, the shear modulus could be an important parameter. Similarly, the hardness of both mating surfaces is critical to determining the adhesive or plowing wear. ML can be utilized to identify correlations between different properties of lubricants, such as film thickness, viscosity, and COF, which can then be used to optimize lubrication performance for specific applications. As such, the use of ML in tribology has initiated a new branch of studies called “Triboinformatics”
[41]. Triboinformatics aims to enhance understanding, prediction, and optimization of tribological processes through the utilization of innovative data-driven approaches. It involves the development of models, algorithms, and databases to capture, store, analyze, and visualize tribological data for various applications, such as lubricant design, material selection, and predictive maintenance. For instance, ML can be used to predict the lubrication properties of a specific set of lubricants under different operating conditions and can help determine the most effective lubricant to use for a particular application. Recent trends in ML for the lubrication industry include the development of efficient models that can forecast the performance of lubricants with a high degree of accuracy
[42]. These models can be trained using large datasets, which allows for more accurate predictions of the performance of lubricants in real-world applications. Overall, by using ML algorithms, it is possible to gain insights into lubricant properties that could otherwise be difficult to predict and analyze
[43][44][45].
In addition to lubricant design, ML can play a significant role in the predictive maintenance of machines and equipment that require lubrication. The analysis of machine data is one of the fastest-growing areas in the industrial Internet of Things (IoT) and data analytics
[46]. By analyzing real-time sensor data, machine-learning algorithms can predict when a machine requires lubrication or maintenance. Another exciting prospect of ML in the lubrication industry is its potential to reduce environmental impact. With the growing concern about climate change, companies are looking for ways to reduce their carbon footprint. ML can be used to optimize lubricant use, minimize waste, and reduce the environmental impact of manufacturing processes. By identifying patterns in data and analyzing performance, ML algorithms can optimize lubrication systems to minimize waste and improve efficiency. Furthermore, with the rise of Industry 4.0, the lubrication industry is rapidly moving towards a more connected, digital future
[47]. Companies can leverage the vast amounts of data generated by sensors and equipment to optimize performance, reduce costs, and improve quality using ML techniques. As a result, valuable insights into the operations are possible, which not only predict failures but also make data-driven decisions to improve the bottom line.
In summary, ML is transforming the lubrication industry by providing a more accurate and efficient way of designing lubricants, optimizing lubrication systems, predicting maintenance needs, reducing waste, and improving environmental sustainability
[48]. As the technology continues to evolve, ML will play a critical role in the future of lubrication, helping companies to remain competitive and reduce their carbon footprint.