Thermoplastics and thermosetting plastics are two major classes of polymers that have recently become materials that are indispensable for humankind. Regarding the three basic needs of human beings—food, shelter, and clothing—polymers and polymer-based materials have gained pre-eminence. Polymers are used in food production, beginning with farming applications, and in the health sector for the development of various biomaterials, as well as in shelter and clothing for a variety of applications. Polymers are the material of choice for all modern-day applications (transportation, sporting, military/defence, electronics, packaging, and many more). Their widespread applications have created many negative challenges, mainly in the area of environmental pollution. While thermoplastics can be easily reprocessed to obtain new products, thermosetting plastics cannot.
1. Introduction
Since the first synthesis of polymers in the early 1900s, the emergence of life and technological advancements has been exceptional due to the vast applications of polymers in every area of life. Polymers have also been used as alternative materials for major traditional materials, such as plywood, metals, glass, and ‘light’ ceramics in, the production and fabrication of consumer products over the last few decades. This change has occurred because of the excellent properties of polymers, as they are light in weight and durable, good insulators, low thermal conductors, have high impact and corrosion resistance, are resistant to most chemical attacks, are easy to form, are diverse in application, and have a low cost of production. Polymer-based products have provided alternative options due to their unique properties, and they are responsible for reductions in the cost of production
[1][2]. The development and fabrication of polymers have significantly increased over the past decades due to their exceptional physiochemical properties, which are suitable for a variety of products for different forms of technological development
[3]. The polymer revolution, in which chemists have developed new methods to overcome polymer limitations, has resulted in exponential growth in polymer production and applications
[4]. Consequently, the continued development of polymer technologies is observed each year. Recent statistical data show that, during the last decade, global production of polymers grew by an average of 37%, which is equal to an increase at a level of about 100 million metric tonnes of polymeric materials. Financial data indicate that the size of the global plastic market in 2020 was approximately 579.7 billion US dollars, indicating a value growth of approximately 15.5% over the last five years. According to estimations, by 2028, the value of the global plastic market should reach 750.1 billion US dollars, with a compound annual growth rate of 3.4% between 2021 and 2028
[5][6].
However, one major concern for polymer-based materials is disposal because it takes a long time for polymeric materials to degrade. Thus, their long-lasting existence often causes environmental pollution. Although the most cost-effective way to dispose of these polymeric wastes is to recycle and reuse them in the development of secondary materials, this process has not been widely promoted by researchers. While various studies have been performed on the development of biodegradable plastic-based composites using natural fibers as reinforcement, damaged polymeric materials are often incinerated, and the burning process causes the release of toxic gases into the environment. Despite this challenge, the advantages of polymers combined with the incessant increase in the population will increase demand for them for various applications
[7]. Thus, the emergence of recycling processes with the introduction of additives to help replenish the physical and mechanical properties of the recycled polymer is a good initiative. It has been emphasized that recycling helps to overcome the environmental problems associated with incineration and ensures the recovery of materials and energy
[8].
The first step in the recycling of polymers is the suitable classification, separation, and cleaning of the waste materials. A comprehensive review of the possibility of applying turbo-charging and electrostatics for the separation of polymers was reported by previous researchers
[9][10]. As a result, having a basic understanding of how to process waste from thermoplastics and thermosetting plastics is critical in today’s world for effective handling and processing.
The characteristic features of polymers are solely determined by the degree of polymerization and their structural properties. Elastomers, thermoplastics, and thermosets are the three main classes of polymers based on their behaviour. However, based on their widespread applicability as composite materials, thermoplastic- and thermoset-based composites are predominant. Hence, researchers focuse on these two major polymers, from which most polymer-based waste products emanate. Thermoplastics have a linear or branched structure and become soft when heated, whereas thermosetting polymers have a cross-linked and network structure and become stronger and harder when heated. The major distinction between thermoplastics and thermosetting polymers occurs due to their molecular structures and processing routes. The classification of polymer materials based on their molecular structures and fabrication techniques greatly affects the procedures undertaken before and after recycling. Because each step of recycling necessitates a different methodology to maximize recovery potential, major considerations must be made when recycling polymers
[11][12].
A lot of researchers have reported the use of recycled thermoplastics for the development of polymer-based composites
[8][13][14], with less emphasis on the use of only waste materials. Hence, this research was performed to advance the development of new composite materials (matrix and reinforcement) predominantly from waste as raw material, as proposed by some researchers
[15]. This process is expected to promote a more innovative approach to curbing the negative environmental impact of improperly disposed waste plastics and the conversion of such materials into sustainable materials, thereby finding alternative applications and promoting zero tolerance for waste
[15]. Normally, it is expected that the recycled material must be processed in ways that reduce contamination
[16]. Thus, more advanced methods to process other waste thermoplastics and thermosetting plastics are essential for the development of eco-friendly products.
Recycling of Waste Thermoplastics
Thermoplastics in the present have no doubt become not only an essential part of technological development but an indispensable aspect of promoting domestic and home comfort in human lives
[17]. Hence, the suitable solution that should be implemented to mitigate thermoplastic pollution is to maximize the four Rs, that is, by reducing, recovering, recycling, and reusing thermoplastic wastes
[18]. Recycling seems to be the most rational, economic, and ecological way of mitigating the damage caused by thermoplastic waste materials. To mitigate thermoplastic waste through recycling, the cycling procedures are grouped into four sequential techniques, as shown in
Figure 1.
Figure 1. Sequential technique for thermoplastic recycling
[8].
Primary recycling is generally known as a closed-loop system; secondary recycling is known as downgrading; tertiary recycling is chemical or feedstock recycling, which applies when the polymer is depolymerized to its chemical constituents; and quaternary recycling is energy recovery from waste or valorization
[8][19][20]. Although these methods have their limitations, they are being adapted in various industrial applications to a definite level. They have, however, improved the recycling of plastics and reduced the incineration of plastic wastes, which usually presents difficulties such as the production of poisonous gases and residue ash, which contains lead and cadmium
[21].
Figure 2 shows the possible life cycle of thermoplastic materials from the first production level to the recycled product.
Figure 2. Life cycle of thermoplastic materials
[22].
Current and Conventional Methods of Recycling
Photo-degradation, thermo-oxidative degradation, hydrolytic degradation, and bio-degradation by microorganisms are the four mechanisms by which thermoplastic materials degrade in the environment (Figure 3).
Figure 3. The four mechanisms of recycling
[19].
Table 1. Four techniques for recycling
[20].
ASTM D5033 Definitions |
ASTM D5033 Definitions |
Other Equivalent Terms |
Primary recycling |
Mechanical recycling |
Closed-loop recycling |
Secondary recycling |
Mechanical recycling |
Downgrading |
Tertiary recycling |
Chemical recycling |
Feedstock recycling |
Quaternary recycling |
Energy recovery |
Valorization |
Recycling is a viable solution for reducing the need for new raw materials and decreasing the materials discarded in landfills. Other beneficial effects of waste recycling are preventing environmental pollution from the extraction of raw materials, saving energy, and even providing domestic jobs. The life cycle of waste polymeric materials is shown in Figure 4.
Figure 4. The life cycle of waste polymeric materials
[23].
As noted regarding the three basic recycling methods (mechanical, chemical, and incineration), they are all limited by one factor or another, hence the need for an advanced method. Since the mechanical and incineration processes have simple and somewhat fixed steps, more attention can be focused on advances in the chemical recycling methods listed among the tertiary recycling methods due to the greater likelihood of modifying the process.
Table 2 presents summaries of some recent developments from various chemical recycling methods to overcome these limitations
[23].
Table 2. Summary of the chemical recycling processes for waste plastics
[23].
Chemical Process |
Main Degradative |
Temperature (C) |
Advantage |
Disadvantage |
Hydrolysis (alkaline) |
NaOH, KOH |
120–200 |
High purity |
Requires chemical substances, longer times, and higher temperatures than the acidic method |
Hydrolysis (acid) |
concentrated sulphuric, nitric, or phosphoric acid |
70–120 |
High purity |
Requires a large amount of acid separation of ethylene glycol from acid, which is difficult |
Hydrolysis (neutral) |
|
200–300 |
Environmentally friendly |
Low purity; requires high temperatures |
Glycolysis |
ethylene glycol, diethylene glycol, propylene glycol, butylene glycol, and dipropyleneglycol |
180–250 |
|
Slow reaction in the absence of a catalyst |
Methanolysis |
zinc acetate |
180–280 |
|
Low purity; requires high pressure and temperature |
Alcoholysis |
methanol, ethanol |
180–250 |
CO2 free |
Requires high pressure; only applicable for plastics without dyes |
Aminolysis |
methylamine, ethylenediamine, ethanolamine, and butylamine |
20–100 |
High purity; Applicable at low temperatures |
Longer reaction time at low temperatures (10 to 85 days) |
A comprehensive review of the state of the art about recycling thermosets and thermoplastics was performed by Kazemi et al.
[23] with an emphasis on the application of recycled polymers in the construction of built environments. The study revealed amylolysis as the most promising method for thermoplastics, while irradiation recycling was found to be the most common method for thermosets. It was discovered from each group that there are innovative approaches, such as aminolysis and biological recycling, which have not yet been scaled up for market usage, hence the need to consider these methods. Among the major factors rendering one method more prevalent than others are processing costs, the quality of recycled products, ease of recycling, and amount and type of post-recycling waste. All of these factors led to the need to understand the science of polymer functionalization to be able to tune the recycled granules’ surface properties for targeted applications.
Based on life cycle assessment studies, mechanical recycling has shown lower emissions than other approaches, making it the most suitable method for environments. However, the mechanical properties of recycled products are much more degraded than virgin plastics; hence, the revolutionary plastic mechanical recycling process was introduced using a new type of twin-screw extruder with the addition of a molten resin reservoir unit applied under various extrusion conditions. As a result, the mechanical properties of recycled products were recovered from their original materials. It was found that steady shear, which is a conventional process, affected the degradation of mechanical properties, while re-extrusion using a new type of twin-screw extrusion with a suitable processing condition is related to the regeneration of mechanical properties and lamellar structures similar to those of virgin plastics. Thus, this method introduces the recent advances in the plastic mechanical recycling process and proposes future directions for plastic recycling technology
[24].
Availability of Waste Plastic as Raw Material for Product Development
In 2020, more than 29 million metric tonnes of post-consumer plastic waste were collected, but more than 23% was discharged to landfills, and more than 40% was applied in energy recovery operations, while only approximately 34% was recycled
[25]. Sources of waste plastics are industrial, commercial, and municipal waste. Industrial, or primary, waste is acquired primarily from the plastic processing, manufacturing, and packaging industries. Commercial waste is typically post-consumer waste from industries, such as packaging, building and construction, automobiles, electrical and electronics, household, leisure, sport, and agriculture, typically obtained from farms and gardens in rural areas. Municipal waste plastics are also obtained from residential areas, streets, parks, collection depots, and waste dumps
[11].
Figure 5 shows the distribution of the percentages of plastic waste from different areas of application in Europe, where it was discovered that most of the plastic products are from packaging, as well as building and construction. Due to the large amount (41%) of plastic products used for packaging and the indiscriminate disposal of products after use, these products have been responsible for major problems in the environment. There is, therefore, a need to intensify efforts regarding how to handle plastic waste coming from packaging.
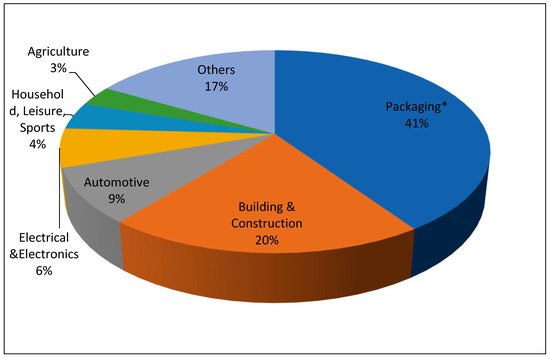
Figure 5. Percentage distribution of waste plastics in Europe
[25]. * Including commercial and industrial packaging. Total 49.1 Mt.
Increasing consumption of plastic products in various fields concomitantly generates much plastic waste material. Thus, the predominant availability of plastic waste materials makes it a potential source of raw materials for future product development. In contrast to the previous opinion about waste plastics, these materials need to be researched and used for the development of suitable products for various applications. This research has become necessary due to their ready availability. In contrast to metals, waste plastics are beneficial materials to humanity because they serve as the leading low-cost and readily available materials with future benefits.