1. Introduction
Within the last few decades, there has been a tremendous increase in demand for lightweight materials, such as aluminum (Al), magnesium (Mg), and titanium (Ti), in the automotive and aerospace industries. The primary focus of these industries is to manifest their technological advancements in energy efficiency to attain the goal of ‘net-zero’ emissions by 2050
[1][2]. Leading a pathway to net zero involves steps taken by governments and industries worldwide to decrease carbon-based fuel consumption, which leads to a reduced carbon footprint
[3][4]. Canadian emissions of greenhouse gases (GHGs) have been recently projected by the government up to 2030 with several climate action amendments in the act as shown in
Figure 1a
[3]. With an expected reduction of 40% in GHG emissions by 2030 from the 2005 level, the Pan-Canadian Framework (2016) and Strengthened Climate Plan (2020) represent the newer measures and strategies undertaken by the government. Altering the materials and manufacturing of fuel-driven vehicles, automotive industries have redirected their attention to the development of hybrid or battery-powered electric vehicles (BEVs) in the last decade
[5]. Premier auto-giants such as Audi, GM, Nissan, Volkswagen, Chevrolet, Tesla, etc., have shown an eminent shift towards the manufacturing of EVs
[6]. A recent study summarized by Ducker Frontier 2020
[7] showed a statistical increase in the use of cast Al alloys from 1979 to 2020, with further projections up to 2030. By looking at the global metal casting production of 109 million metric tons (MT) in 2019, Al alloys constituted about 17 million MT
[2]. It was shown that the global market for automotive Al products will reach $ 109.7 billion by 2026, with a compound annual growth rate (CAGR) of 8.30%
[8][9][10]. A recent study confirmed the progress of Al alloys in the global market, which was already estimated to be $ 131 billion in 2022, crossing the mark set previously as shown in
Figure 1b. Furthermore, it is projected to increase at a CAGR of 8.1% to $ 287 billion by 2032
[11]. Over the coming years, the growth of electric vehicles will increase the demand for cast Al alloys, such as Al-Si, Al-Si-Cu, Al-Si-Ag, and Al-Si-Sn alloys, in the market
[12]. Surging investments in housing activities globally has been identified as a potential trend that would drive sales of high-strength Al-Si alloys, especially in the high-growth region of Asia Pacific. The global Al-Si alloy market is also projected to grow at a CAGR of 2.84% during the forecast period of 2022−2030
[13].
Developments in casting technology, solidification fundamentals, and process control parameters for Al-Si alloys have been well-documented in several handbooks and articles since the 1960s
[14][15][16][17][18][19][20][21][22]. Al-Si alloys are known to have low density, high specific strength, high ductility, good castability, high thermal conductivity, high corrosion resistance, cosmetic surface quality, resistance to hot tearing, etc., which makes them suitable for large-scale automotive and aerospace applications
[23][24].
Figure 1c shows the global market share of Al die-cast alloys based on their application in different sectors
[9]. The transportation sector is a major consumer of such alloys, with building and construction, securing the second spot
[9]. Apart from conventional casting techniques, a significant rise in the production of Al-10%Si-Mg or Al-12%Si alloys in the additive manufacturing sector has gained popularity in recent years
[25]. Though these processes have not yet overcome some shortcomings, such as mass production relative to die-casting, intense research is still ongoing.
A recent review by Li et al.
[26] summarized Al-Si alloys manufactured through conventional casting processes with high electrical conductivity, based upon the International Annealed Copper Standard (IACS). The chemical modifications, alloying additions, electrical properties, and thermal stability of Al-Si alloys have been well documented in
[27][28]. A lot of discussion on automotive, aeronautical, and aerospace applications of Al-Si alloys, along with manufacturing and mechanical properties, is presented in a book by Hernandez et al.
[29]. However, only limited literature surveys are available on the fatigue behavior and deformation mechanisms of these alloys
[30][31].
2. Applications of Al-Si Alloys
2.1. Automotive Applications
In a typical passenger vehicle, such as a car, minivan, or light truck, Al castings can be found in several parts, such as the roof brackets, door handles, engine blocks, pistons, powertrain, battery compartments, wheels, chassis, space frames, etc. These components after manufacturing need to satisfy ASTM specifications for mechanical properties, porosity limit, roughness, dimensional stability, and corrosion resistance. As the growth of electric vehicles (EVs) clouds over conventional internal-combustion-engine models, Al-Si alloys have been able to find their applications prominently in these sectors.
Internal Combustion Engine Vehicles
Replacing heavier cast iron and steel components with Al-Si alloys in North American vehicles has led to the satisfaction of Corporate Fuel Average Economy (CAFE) standards. This allows customers to experience vehicles with reduced weight and increased fuel economy
[32]. Powertrain components such as the V8 engine block, which is made out of Al-Si castings, weigh ~30–50 kg, compared to gray cast iron parts, weighing ~70–120 kg
[33][34]. Recent developments have shown that the addition of transition metals and rare-earth elements, such as Zr, Ti, Sc, V, etc., to Al-Si alloys, can improve the high temperature and wear performance of the engine component
[27][35][36][37][38]. The increased power rating of powertrain components is possible with the help of Al alloys, leading to higher thermal and electrical conductivity
[27][39]. Controlled process parameters have allowed engineers to manufacture alloys such as the low-iron-containing Silafont
®-36 alloy, which has higher castability and ductility and is suitable for suspensions and space-frame members
[40].
Figures 2a–d,f–i show some specific components, such as steering columns, engine cradle, shock tower, and front sections fabricated with Al-Si alloys, such as Aural
TM-2, Castasil
®-37, Silafont
®-36, Mercalloy
TM-367, and Alcoa’s C601/611 alloys
[2][41][42][43]. Emerging manufacturing processes, such as high-pressure die-casting, can streamline the production of thinner and thicker parts with high integrity and stability. It is expected that the usage of such processes will increase towards 2040 for automotive Al castings
[44].
Hybrid and Electric Vehicles
The market for hybrid and fully electric vehicles has grown exponentially within the last decade, which has resulted in the downsizing of internal-combustion-engine parts, such as engine blocks and the number of cylinders. New structural components to house batteries are being designed to satisfy safety and reliability demands.
Figure 2e shows the powertrain components for an Audi EV model fabricated with structural Al alloy die-castings
[45]. Companies such as Volvo are trying to replace extruded and stamped sheets into a single giant piece of Al casting, also known as mega-giga casting technology
[44]. It has been reported that Al-using EVs emit 1.5 tons fewer GHGs over their complete life cycle than steel- or cast-iron-using EVs
[46]. Gomes et al.
[47] studied Ag-containing Al-Si alloys to replace normal Al-Si castings for EVs, which improved the electrical conductivity, another beneficial property needed for battery-driven vehicles. Tesla™ has been trying to create alloys with high yield strength and conductivity while being resistant to hot tearing for usage in newly developed EVs as die-casting drive unit components
[48]. Studies leading to the development of Al-Si alloys with the addition of Cu, Mg, Mn, Ni, Sr, etc., which increase electrical conductivity along with strength and ductility, are some of the major foci for automotive industries and researchers
[26].
2.2. Aeronautical and Aerospace Applications
Aerospace Al-Si alloy castings generally have a longer life than those used in automotive applications due to higher fatigue resistance and corrosion resistance. Other traits of Al-Si alloys include improved static strength, resistance to crack growth, damage tolerance, stress corrosion, and fracture toughness
[49]. The Advisory Council for Aeronautics Research in Europe (ACARE) reported a significant 38% reduction in CO
2 emissions and a 37% reduction in the perceived noise against a goal of 50% for both criteria by 2020
[50]. The common fabrication methods to make complex structural Al-Si alloy components used by aerospace giants such as Boeing, Airbus, Bombardier, etc., are precision sand casting and investment casting processes. This helps to reduce wrought Al alloy welding, which leads to a 50% weight reduction and lower component cost
[24].
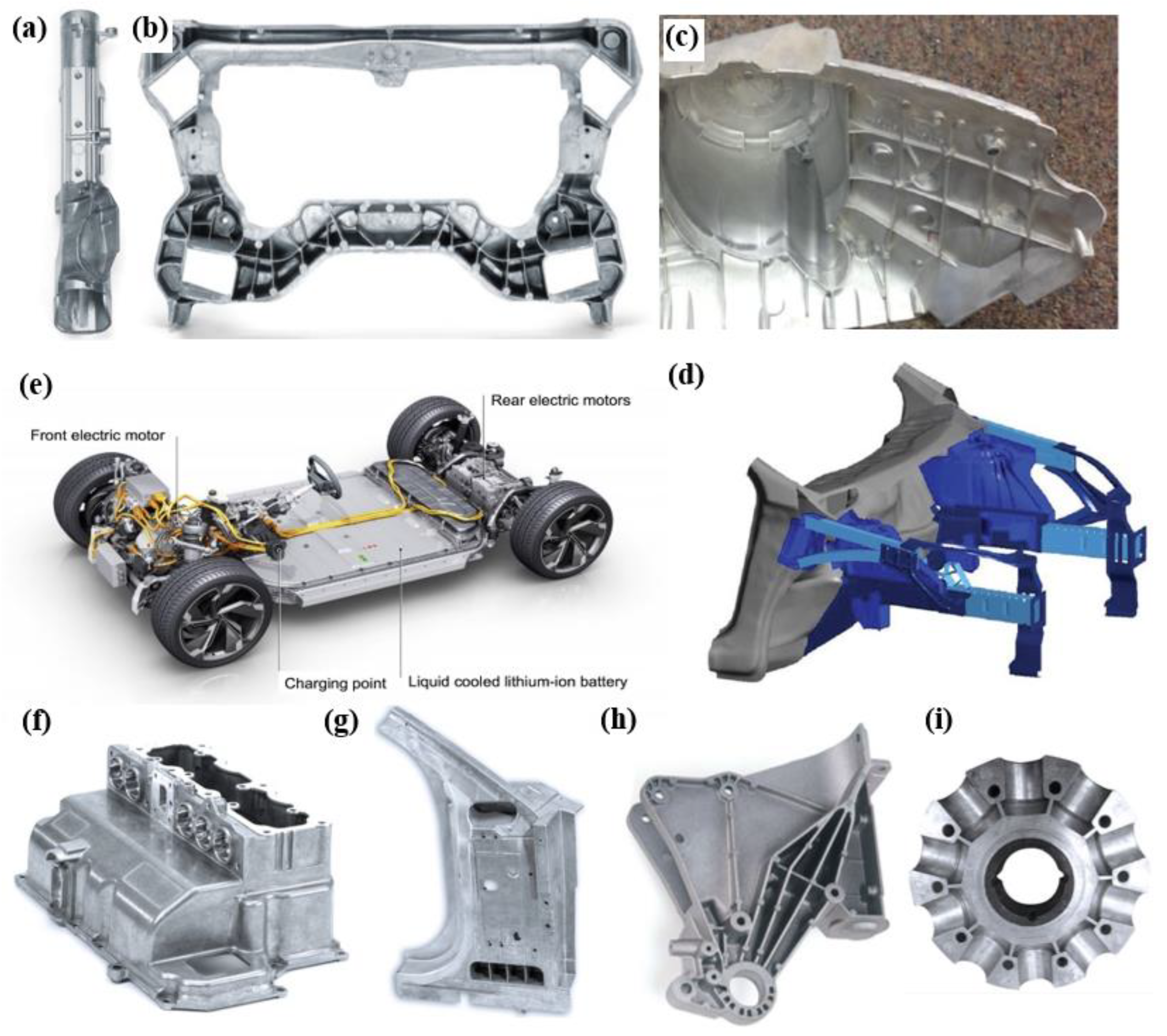
Figure 2. Automotive applications for Al-Si alloys, such as (
a) steering column, (
b) engine cradle
[40], (
c) shock tower
[2], (
d) front section
[43], (
e) Li-ion battery compartment for Audi e-tron
[45], (
f) upper safety housing for high-voltage heat plug connectors, (
g) A-pillar, (
h) truck cab tilting joint, and (
i) ventilator hub
[40]. Reproduced with permission from Elsevier and open-access websites.