Shellac, an insect-derived material, has received the least attention due to its scarcity in south Asia. Currently, Shellac is used in various applications, such as furniture polish, glazing agent for candies and pharmaceutical pills, coating on fruits to increase shelf life, primers, smart sensor, 3D printing, and green electronic. However, the limitations of Shellac such as: brittleness with time, self-esterification, low transparency, solubility in alkaline medium and in most organic solvents have limited its usage in the packaging application. Many of these problems can be improved by physical blending or chemical reaction with other materials to make Shellac more durable, impede self-esterification, and facilitate the film-forming ability, which suggests the potential usage of Shellac in packaging applications.
1. History of Shellac
Shellac is a hydrophobic, water-insoluble, edible biomaterial with the E number E904, which is used as a glazing ingredient in sweets and pharmaceuticals, as well as a coating substance on fruits to extend shelf life
[1]. Shellac’s history goes back 5000 years, suggesting it is one of the oldest resins mankind has ever known (
Figure 1). According to the Indian mythology “Mahabharata”, dried Shellac was mentioned as a material for constructing a palace that was intentionally built to burn down, suggesting the usage of Shellac 5000 years ago
[2][3]. Three thousand years ago, the usage of Shellac was evident as “Laksha”, and it was used as a source of dyeing agent
[4]. In the 11th century, the use of Shellac was mentioned as a source of artist pigment
[4][5], whereas Shellac was also utilized as a varnish for cassone
[6] and sealing waxes
[7] in the 16th century. The highest consumption of Shellac was recorded in the 20th century to produce gramophones
[8]. Around 50% of the Shellac was produced to press on the gramophone records in that era.
Figure 1. History of usage of Shellac and its byproducts
[3][9][10][11][12][13].
2. Source, Extraction, and Production of Shellac
Shellac is a resin secreted by Kerria Lacca, an insect type of the lac bug
[14][15]. Lac means lakh in the Hindi language, which is the root word for Shellac. The word lakh means 100,000 or 0.1 million, which signifies that around 0.1 million lac bugs are required to produce 1 kg of Shellac
[16][17]. These lac bugs produce a sticky resin containing Shellac but require various stages to purify it to remove larvae and dyes from it. The intermediate stages of producing Shellac involve the production of resin on the tree (Sticklac) by the lac bug, processing of Sticklac to produce Seedlac, and finally, purifying Seedlac to Shellac.
2.1. Production of Resin by Lac Bug on the Tree (Sticklac)
The lac bugs move into specific host trees to consume the sap from the trees to produce the resin. It has also been found that the lac bug, when fed on the Kusum tree (
Schleichera), produces the least colored Shellac. Other commercial host plants for these lac bugs are Palash (
Butea monosperma), Ber (
Ziziphus mauritiana), Kusum (
Schleicher oleosa), and Semialata (
Flemingia semialata)
[16][18][19][20]. In the larvae form, the lac bugs move onto the host tree or plant’s soft shoots to survive. For 2 to 3 days, they insert their proboscis in the trees to reach the sap. The lac bug then sucks the tree sap to survive and complete its cycle. Meanwhile, the male bug moves out of its cells, and the female bug continues to live in the trees. In order to adhere to the trees for longer, the female lac bug produces a resinous compound as a protective coating around its body. The male bug fertilizes the females and then dies within a few days. The fertilized female continues to secrete the resinous compound and produces 200–500 larvae. This resinous compound is removed by knife, sickle, or stick; therefore, it is termed “Sticklac”
[18]. This Sticklac contains resin, wax, dyes, and impurities, such as crusted insect and wood particles.
2.2. Processing of Sticklac to Seedlac
The Sticklac is processed to remove impurities with the help of various processes, such as crushing, washing, drying, cleaning, and grading. The crushing of Sticklac is performed and then sieved with the help of a fine sieve to remove the wood chips. After crushing, the Sticklac is washed with water, and most impurities, such as lac eggs, float on the water. The lac that settles at the bottom is called Seedlac, which will be used to produce Shellac
[16][18][21].
2.3. Production of Shellac by Purification of Seedlac
Seedlac can be transformed into Shellac by two processes, i.e., using thermal and solvent extraction (Figure 2). In the case of the heat process, the Seedlac is placed into a huge cotton bag and heated by charcoal fire to heat it evenly from all sides. The lac resin is melted, squeezed out of the bag, and scraped off the bag’s surface. It is then put into hot water to keep the lac molten and distributed into thin sheets. In industries, the Seedlac is melted by heated steam, and molten lac is pressed with the help of the hydraulic press through the filter. This filtered lac is then stretched into long sheets with the help of sheet rollers. In the case of solvent extraction, the Seedlac is dissolved in ethanol, either cold or hot. The soluble resin is dissolved in ethanol, and the insoluble solid is collected from the bottom. The solvents are evaporated, and the remaining viscous Shellac is stretched using a sheeting roller . The solvents are further distilled and can be reused. The sheets obtained through either the thermal process or the solvent process become brittle once dried and form or break in the shape of flakes. Hence, they are sometimes called Shellac flakes.
Figure 2. Various production methods of Shellac from Seedlac via thermal and solvent methods
[22].
3. Structural Composition and Structure of Shellac
From Sticklac to Shellac, the main component of Shellac is resin, which is purified in each process. The amount of resin in Sticklac is generally 68%, and it is increased to 90.9% in Shellac after processing, while other components, such as dye, wax, and impurities decrease upon purification.
The chemistry of the Shellac resin is very complex, yet captivating. The chemistry of resin has been studied since the 1960s by various techniques, such as column chromatography, thin-layer chromatography, gas chromatography, and spectroscopic methods. Shellac is a complex polyester resin composed of long-chain hydroxy-fatty and sesquiterpene acids. It contains inter- and intra-esters of polyhydroxy carboxylic acids. The backbone of Shellac comprises long-chain fatty hydroxy acids known as Aleuritic acids, which comprise 35% of Shellac and impart hydrophobicity. This backbone is connected with many cyclic terpene acids (hydrophilic) with ester bonds. Although most of the constituents of Shellac resin are known, its structure is entirely unknown
[18]. However, some researchers have tried to conclude that in pure Shellac resin, aleuritic acid and terpenic acids are present in a 1:1 ratio, where there are three jalaric/epishellolic acids and one laccijalaric/epilaccishollolic acid
[18][23]. The chemical structure of Shellac concluded as the most possible structure is shown in
Figure 3.

Figure 3. Chemical structure of Shellac.
4. Physicochemical Properties of Shellac
Shellac has unique properties due to its complex structure. Shellac is commercially obtained in the form of flakes. It is generally yellow to brown, depending on the dyes, which are determined by the tree. It has a refracted index in the range of 1.521 to 1.527, near that of glass. Upon storage, the acid value decreases due to the reaction between its free hydroxyl groups and carboxylic acid
[24]. This phenomenon of Shellac is called self-esterification or self-polymerization, due to which Shellac becomes hardened as it ages; therefore, the high quality of Shellac can be estimated with the help of its acidic value
[16][25]. With aging, Shellac becomes stiff, brittle, and insoluble in solvents due to the inter-esterification of the free hydroxyl groups with the free acids groups
[26], which limits its consumption for several applications. It was also reported that higher temperatures accelerate the aging of Shellac. During the aging process, the Shellac is melted from the solid state and flows readily, but with time, the molten Shellac forms a rubbery state, an intermediate stage of aged Shellac. After some time, the rubbery state converts to a hard and brittle structure. This agingis shown in
Figure 4. Therefore, the usage of Shellac is limited by its storage condition.
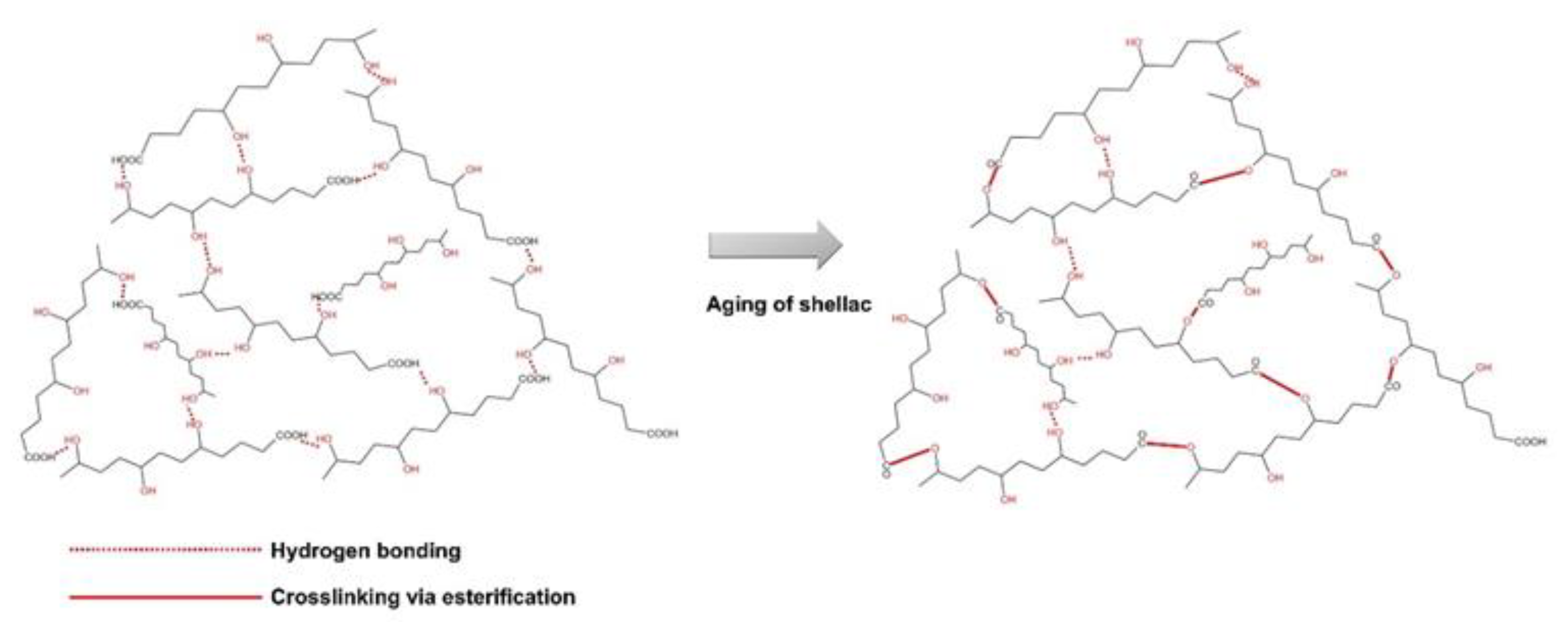
Figure 4. Aging of Shellac by cross-linking or inter-esterification.
5. Potential in the Packaging Application
Shellac is a resin primarily used in varnishes nowadays, but its applications are not limited. The benefit of Shellac as a primer, binder, coating, glaze enhancer, adhesive, cosmetics, food, pharmaceutical products, textiles, adhesives, plastic, rubber, leather, fertilizers, seeds, fruits, wood, pyrotechnics, printer inks, paints, and confectionery depends on the properties and grade of Shellac, which is best suited for the specific products. Aside from these applications, Shellac has been researched for packaging applications, but this has been limited to 20 publications till 2022, as shown in Figure 5. Those 20 publications account for 1.56% of the articles covering bio-based polymers for packaging applications. However, although the publications are few in number, they are increasing year by year.
Figure 5. Increase in number of publications on Shellac usage in packaging. The search was limited to TOPICS in Web of Science, and the keywords used were Shellac and Packaging.
Shellac has been blended with various biopolymers to impede the aging the shellac; these biopolymers includes pea starch/guar gum
[27], KGM
[28], CMC
[29], and SPI
[30], Shellac has been used as reinforcement to strengthen the water barrier, oxygen barrier, and mechanical properties, which are crucial for the majority of food packaging applications. Shellac, a useful reinforcement material for food packaging, also boosted the temperature tolerance of the packaging film
[28]. To retain the integrity of the packaged product, Shellac has been researched in active packaging alongside olive leaf/grape pomace extract
[31] and pine needle essential oil
[32] as a coating solution. Eggs were coated with Shellac and pine needle essential oil to preserve the eggs, improve the ultraviolet resistance, and increase the water and oxygen barrier performance
[32]. Additionally, eugenol was added to PVP/shellac fiber films for the packaging of strawberries
[33]. Moreover, to extend the shelf life of fruits, 1-Methylcyclopropene was applied on paper as a coating material using Shellac as a base matrix
[34].
Shellac’s potential among traditional crude-based polymers and conventional bio-based polymers must be demonstrated by properties critical to packaging, such as melting temperature, tensile stress, elongation at break, contact angle, and WVPC. Table 1 compares Shellac to different polymers and indicates that Shellac has mixed qualities when compared to other traditional crude-based and bio-based polymers. Shellac has a melting point of roughly 75 °C, similar to polycaprolactone (PCL). Because of this lower melting temperature, Shellac is suitable for solid packaging products or cold liquids. In terms of mechanical properties, the tensile strength of shellac film is similar to that of Polyethylene (PE). The elongation at break is only 3.05%, making it unsuitable for flexible packaging applications. However, the literature has shown that the addition of PEG 35,000 increases the elongation at break to 170%, which is better than PET, polylactic acid (PLA), and poly(3-hydroxybutyrate)-co-(4-hydroxybutyrate) (P3HB4HB). Shellac’s intrinsic hydrophobicity makes it more competitive with other biopolymers, such as PLA, P3HB4HB, and PCL. The contact angle of Shellac is comparable to that of PE, PET, and polypropylene (PP). The contact angle provides information regarding surface wettability; good water barrier qualities, such as WVPC, are required for the package to preserve the goods. When comparing the WVPC, Shellac has a greater WVPC (lower barrier) than standard PE and PP. However, the barrier is equivalent to PET in other crude-based polymers. Compared to bio-based polymers, Shellac has two times and six times greater barriers than PCL and PLA.
In addition to PCL, PLA, and P3HB4HB, other edible bio-based polymers, such as starch, gelatin, pectin, chitosan, and guar gum, are compared to Shellac in Table 2. In terms of tensile strength, shellac film is better than starch and pectin. However, gelatin, chitosan, and guar gum have higher tensile strength. Shellac, when modified with acrylic, has a similar tensile strength to chitosan but can reach a tensile value similar to guar gum or gelatin. However, Shellac has a similar elongation at break to gelatin but has smaller values than the other edible bio-based polymers mentioned. However adding PEG 35,000 increases the elongation at break to 170%, which is better than starch, gelatin, pectin, chitosan, and guar gum. Shellac’s intrinsic hydrophobicity makes it highly competitive with these edible polymers. The contact angle of Shellac is more than the other edible polymers mentioned, and it is worth noting that the WVPC of Shellac is 33 to 44 times lower than guar gum and 8 to 10 times lower than gelatin, showing superior hydrophobicity when compared to all the other edible bio-based polymers mentioned. Therefore, Shellac has untapped potential for packaging applications, including food packaging, due to its non-toxic nature.
Table 2. Comparative analysis of Shellac with edible bio-based polymer used in packaging.