Fe-SMAs with superb SMEs can generate huge recovery stress, which is very important for the reinforcement of RC bridges.
Generally, the stress-induced deformation of Fe-SMAs will be completely or partially restored to their original shape under heating. If the recovery strain is limited, considerable recovery stress is generated, which can be applied for structural reinforcement as a prestress. The process of recovery stress generating is shown in Figure 2.
Fe-SMAs are stretched to pre-strain ε
p (2~6%) by an external force at ambient temperature, as shown in path 1, and after the stress is released, the elastic strain ε
e and superelastic strain ε
pe are recovered, but the residual deformation (ε
r + ε
p) is retained, as shown in path 2. At this time, if the Fe-SMAs are heated to a temperature above A
s, which is the so-called “activation”, the strain ε
r of alloy will recover due to SME, as shown by the blue arrow in
Figure 2a; if the strain ε
r of Fe-SMAs is constrained due to anchoring or bonding with adjacent structures, the prestress will be generated in the alloy, as shown in path 3 and 4 of
Figure 2.
Figure 2b shows the temperature–stress curve of this process, and the stress will slightly reduce at the early stage of heating due to the thermal expansion of the material. Therefore, it is usually necessary to apply a prestress to the alloy, about 50 MPa
[36] before the recovery stress test. When the temperature exceeds the A
s temperature of Fe-SMAs, the temperature-induced reverse martensite transformation starts, and the recovery stress gradually increases. Considering the limitations of the application environment, the heating temperature is generally stopped when the heating temperature reaches or is slightly greater than the A
f temperature. At this time, the martensite in the alloy is almost completely transformed into austenite, and the reverse martensite phase transformation is finished.
The second reinforcement technology generally includes near-surface mounting (NSM) technology and embedding the ribbed Fe-SMA bars into the shotcrete layer, and the cross sections of reinforced beams with two methods are shown in Figure 7.
4. Reinforcement Applications of RC Beams with Fe-SMAs
4.1. Application on Reinforcement of Small-Scale Specimens
The feasibility of Fe-SMAs in the domain of civil engineering has been confirmed by early research
[2][36][37][38][40], and some scholars attempt to apply it to the reinforcement of small-scale specimens
[2][34][43][52][59][60].
Watanabe et al.
[59] studied the flexural performance of plaster prism specimens reinforced by Fe-27.2Mn-5.7Si-5Cr (in mass %) fibers with a diameter of 1 mm in 2002. Before application, the fibers were subjected to pretension with strains of 1%, 2%, and 3%, respectively, and embedded into a plaster matrix, and then were heated up to 250 °C. The test result revealed that the improvement of bonding strength was due to compressive residual stress rather than the fiber reinforcement effect. Moreover, the bending strength of specimens improved with the increasing level of pre-tensile strain (see
Figure 8), except for the 3% composite which might be attributed to a lack of bonding strength. Five years later, the Fe-Mn-Si-Cr SMAs machining chips generated during the fabrication of SMAs pipe joint, were added to the plaster matrix by Watanabe et al.
[60]. The result of the three-point bending test showed a similar trend to the above results on mechanical property characterization and proved that the low-cost composite material can be applied in civil engineering.
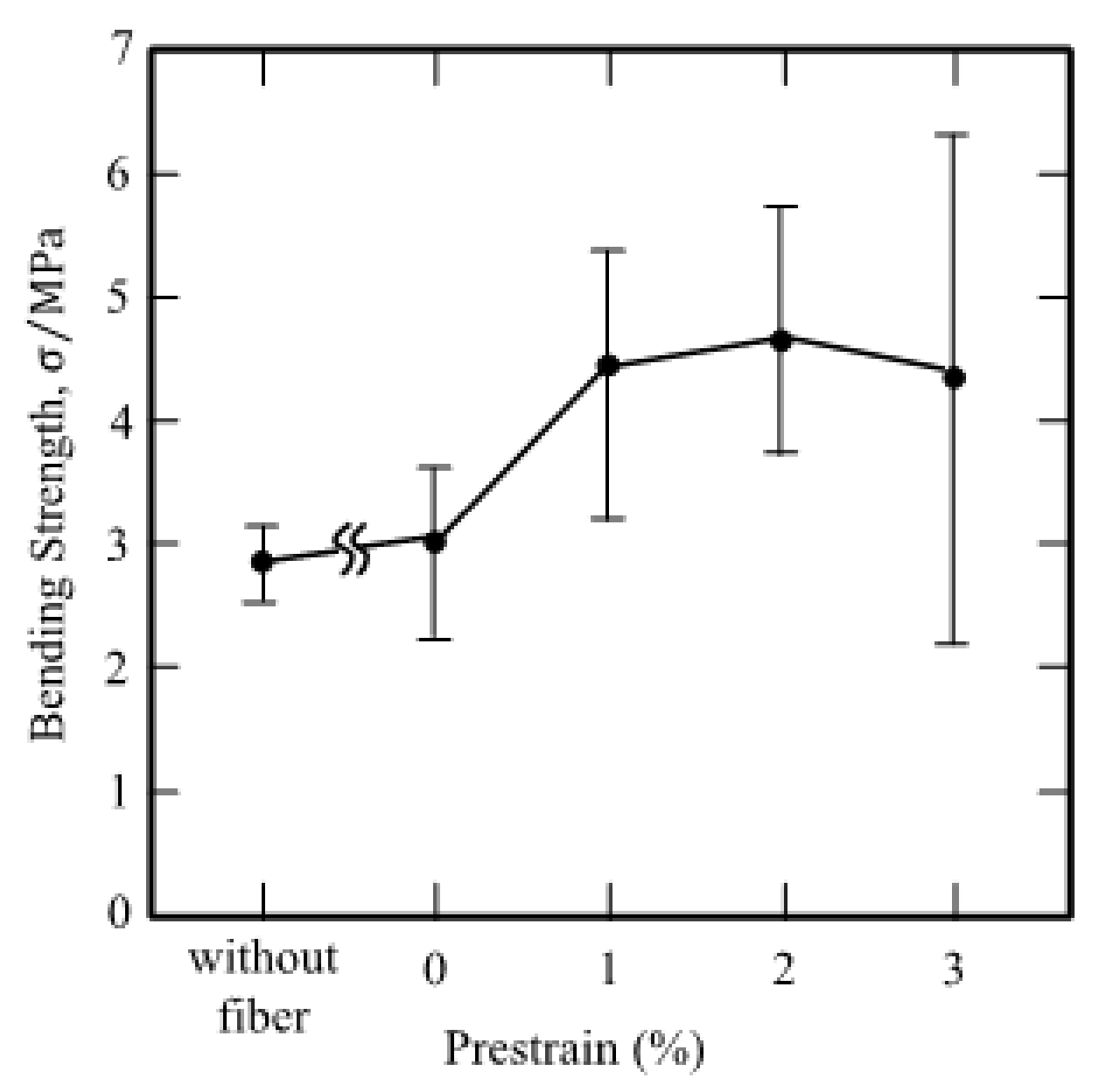
Figure 8. Bending strengths of the plaster prism specimens [59].
Sawaguchi et al.
[34] introduced the fine NbC precipitates into Fe-Mn-Si alloys, Fe-28Mn-6Si-5Cr-0.53Nb-0.06C (in mass %), which need not thermomechanical treatment. Square bars processed by shape memory alloys were embedded in the mortar specimens and activated by autoclave, which increased the bending strengths and cracking stresses of prestressed mortar matrices. Czaderski et al.
[2] introduced the feasibility of using ribbed Fe-SMA strips instead of FRP strips for near-surface mounted reinforcement and found that the activated Fe-SMA strips could generate recovery stress of 200~300 MPa and had sufficient bond stress with grouting mortar. Recently, Choi et al.
[52] reported the flexural failure modes and crack patterns of the three-point bending test of mortar beams reinforced with activated and unactuated Fe-19Mn-4Si-8Cr-4Ni-0.01C (at.%) alloy wires. The cracking load and ductility of the activated reinforced beam increased by 45% and 2.1 times compared to the unactivated reinforced beam, respectively.
The above studies have proved that the small-scale specimens reinforced by Fe-SMAs exhibit superior performance, including bending stress, cracking load, and failure mode, which lays the foundation for the application of Fe-SMAs to full-scale RC beams.
4.2. Application on Reinforcement of Full-Scale Beams
4.2.1. Flexural Performance
NSM technology is the most common strengthening technique utilized for deteriorated concrete beams
[49]. This method can increase the stiffness and load-bearing capacity of concrete beams, reduce deflection, and delay the generation of cracks. Furthermore, it also can improve the maintainability and durability of the whole structure
[40][44][45][67].
Shahverdi et al.
[48][68] reported the four-point bending test results of RC beams with two ribbed Fe-SMAs. The results show that the concrete cracking load (P
crack), the serviceability limit state load (P
δmid = 4 mm), and the maximum load (P
max) of the RC beam are increased by 80%~125%, 97.5%, and 72.4%, respectively, compared to that of the reference beam. Kinam et al.
[44] studied the influence of the section area and pre-strain level of Fe-SMA strips on the bending performance of RC beams. They found that the ultimate load increased by an average of 30% when the section area increased by 30 mm
2, and the increase in the level of pre-strain significantly enhance the cracking load of the RC beam, which increased by 15.89% and 35.41% with 2% and 4% pre-strained of strips, respectively, but had no obvious influence on yielding load. The four-point bending test of RC beams was examined under deflection control by Shahverdi et al.
[47] in 2016. The result revealed that the cracking load and mid-span deflection at P = 8 kN of NSM Fe-SMA strengthened beam were, respectively, increased by 80% and declined by 75%. Furthermore, the experimental results pointed out that the slope of the mid-span displacement curve was slightly affected by the cyclic loading at the serviceability but significantly by the condition of reinforcement. In 2019, Abouali et al.
[69] analyzed the above RC beams by developing a 3D nonlinear finite element model in ABAQUS and then used the validated model to evaluate the effects of design parameters on the performance of NSM Fe-SMA strengthened beams. The analysis results indicated that this reinforcement method significantly improved the rigidity of RC beams with low steel reinforcement ratios.
Another advantage of the NSM Fe-SMA reinforcement method is that it does not alter the failure mode of the concrete beam. The failure mode of reinforced beams shows obvious ductile damage characteristics
[6][49][62][67][68], which differs from the brittle failure modes of beams reinforced with FRP laminate
[70][71].
The load–deflection curve of beams strengthened with Fe-SMA bars and CFRP strips is shown in
Figure 9. As reported by Rojob et al.
[50], the ductility index (the ratio of deflection at ultimate load to that at yield load) of the NSM Fe-SMA reinforced RC beam was significantly improved with a 52% increase compared to CFRP reinforced beam, and the energy dissipation was increased by 76%. Moreover, NSM Fe-SMA reinforced beams exhibited good ductility when it fails
[63] and had been validated by the 3D FE model
[71]. The failure behavior of three concrete beams reinforced by activated NSM Fe-SMA was researched by Shahverdi et al.
[68]. It concluded that the failure of strengthened beams normally was concrete damage after yielding of Fe-SMA strips and longitudinal bars.
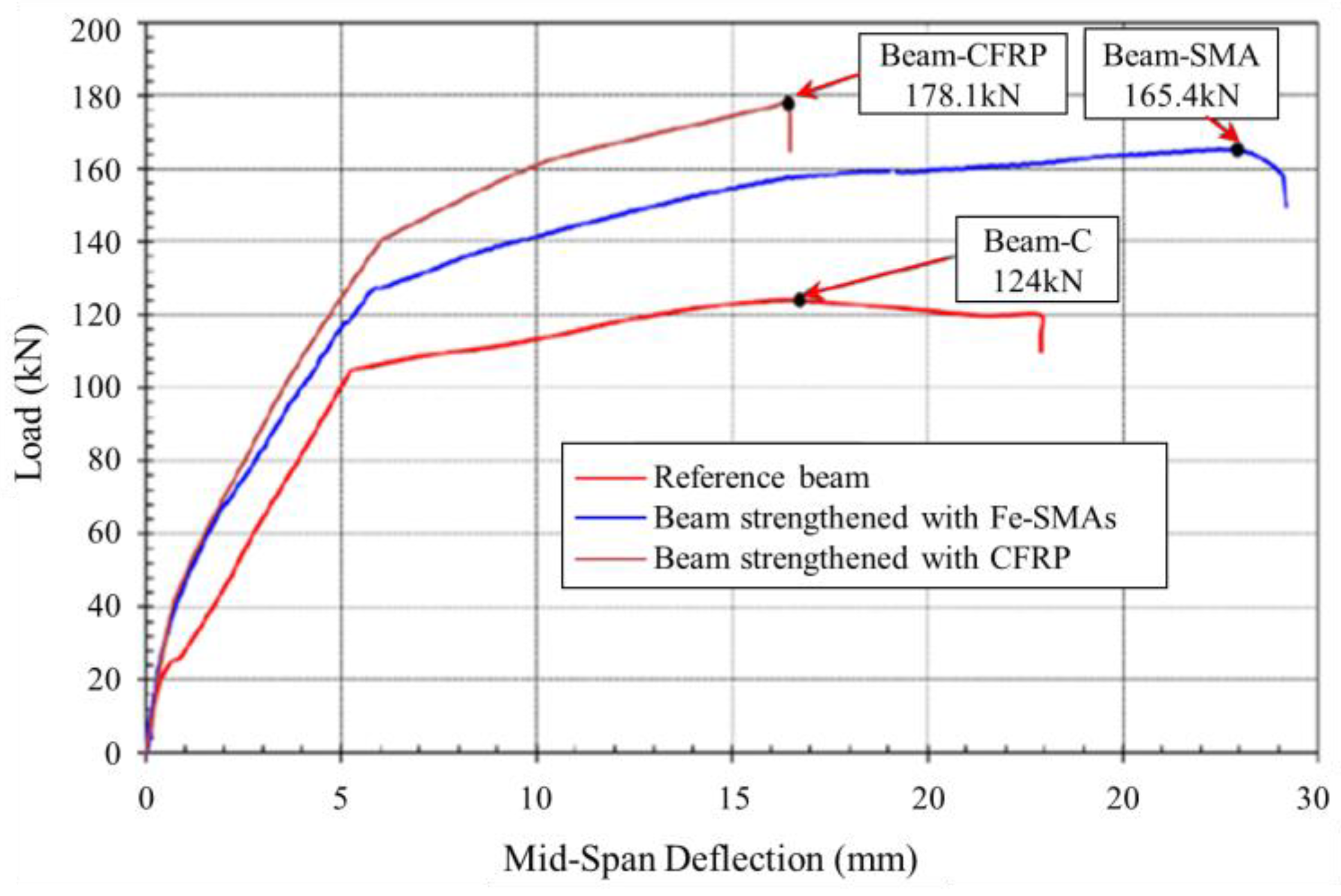
Figure 9. Load–deflection curves of beams [50].
Embedding ribbed Fe-SMA bars in the shotcrete layer is another promising technique to improve the flexural performance of RC members. Shahverdi et al. [45] first introduced this reinforcement method into RC beams and studied bending behaviors by a four-point bending test. The cracking load of the beam embedded with two ribbed Fe-SMA bars was up to 9.5 kN, which is 76% higher than the reference beam with normal steel. In another study [48], they pointed out that the prestressing force of the Fe-SMA bars can be completely transferred to the concrete beam through the shear stress in the interface.
4.2.2. Shear Performance
Shear failure is one of the common failure modes of RC beams, showing the characteristics of brittle failure which do not have obvious signs before failure. Therefore, it is essential to strengthen the RC beams to avoid shear failure, especially in beams bearing seismic loads or new loads.
[35][66][72].
The shear strengthening of RC beams is another popular application of Fe-SMAs
[3][32][39][58][64][73][74], and it can be tracked to 2001. Fe-Mn-Si-Cr SMA bars were first successfully used by Soroushian et al.
[32] to strengthen a concrete bridge in Michigan, where some shear cracks appeared in the negative moment area of the bridge’s T-beam. The load-bearing capacity of the reinforced structure was restored to its original level after strengthening, and the average crack width was greatly reduced by about 40% to 0.32 mm. Unfortunately, to the best knowledge, there is no follow-up research on the shear reinforcement of concrete beams for the long term.
It was not until 2017 that Zerbe et al.
[64] used external Fe-SMA strips with sectional dimensions of 0.5 × 50 mm to actively strengthen the T-beam. Although the experimental results were affected by anchors, the shear capacity and ductility of reinforced beams were significantly improved compared to the control beam, and the shear strength increased by 20~25%. Recently, Luis et al.
[39] studied the mechanical properties of Fe-SMA strips and surrounded the strips on the outer surface of concrete beams without internal stirrups. Surprisingly, the failure mode of shear RC beams shows flexural failure rather than shear failure. Subsequently, nonlinear finite element modeling of RC beams was established by Joaquín et al.
[73], and the numerical results of the FE analysis showed a very good correlation with the experimental behavior observed during the tests. A series of concrete T-beams with lengths of 5.5 m and heights of 0.55 m were experimentally researched by Cladera et al.
[3]. The results revealed that the activated prestressed U-shaped Fe-SMA strips effectively delay the appearance of cracks and improve the shear capacity (about 30%).
Analogous to the flexural reinforcement, embedding ribbed Fe-SMA stirrups in the shotcrete layer was proven by Shahverdi et al.
[74] to be a kind of feasible shear reinforcement method. Moreover, the bending of the Fe-SMA steel bars at the corners of the beam had no impact on the normal operation of the reinforcement system. More recently, Czaderski et al.
[58] found that prestressing the Fe-SMA stirrups with sprayed mortar layer (see
Figure 10) significantly reduced the strain and stress of internal steel stirrups, which was especially propitious to the applications in RC beams subjected to fatigue loads. Furthermore, the maximum load of the T-beam reinforced with five activated Fe-SMA strips was increased by 86%, whereas its mid-span deflection was reduced by 39%.
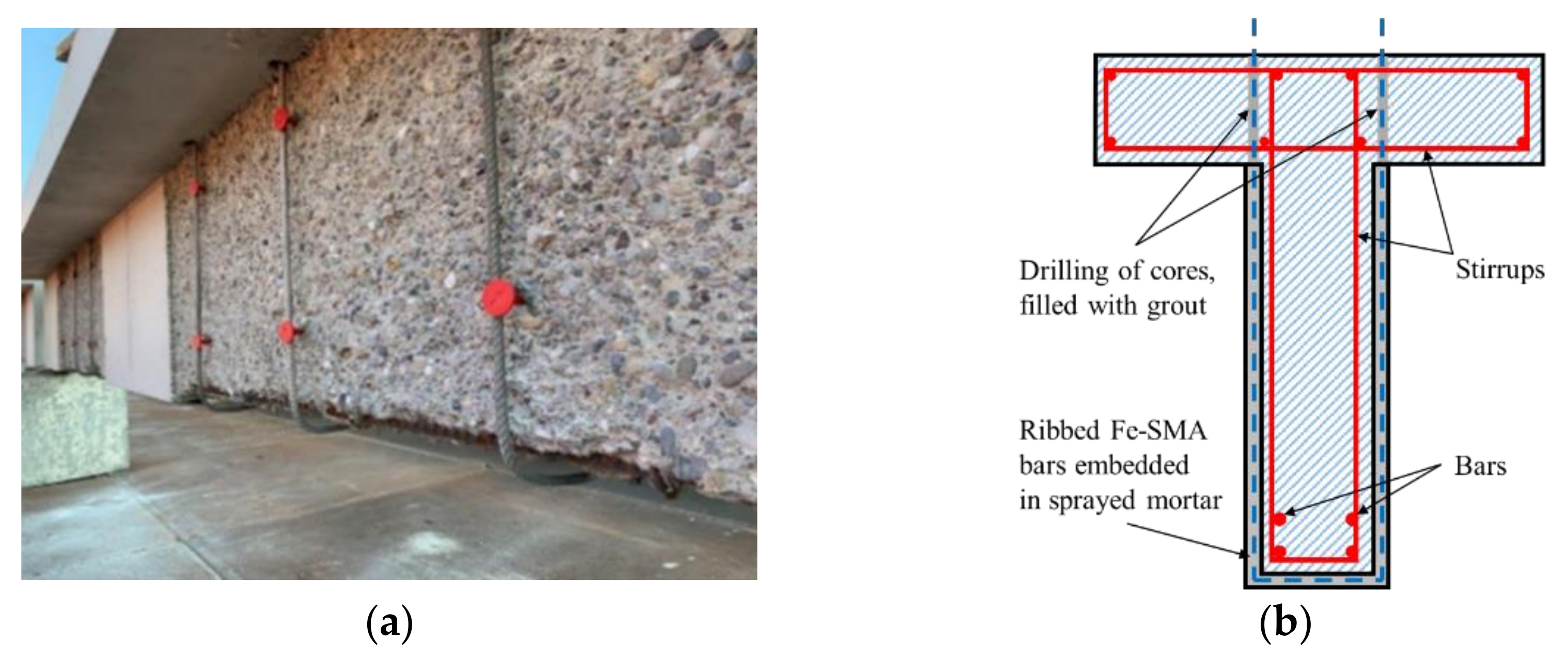
Figure 10. Shear reinforcement with Fe-SMAs embedded in sprayed mortar layer (adapted from [58]): (a) installed memory-steel stirrups on-site; (b) cross-section of reinforced beam.
4.2.3. Other Performances
Recently, some scholars have tried to further study other performances of Fe-SMA-reinforced beams, such as fatigue performance
[51], fire resistance
[57], durability
[46][74][75][76][77], etc., which are also the pioneer field of Fe-SMAs application research.
The fatigue performance of RC beams reinforced by NSM Fe-SMA bars was researched by Rojob et al.
[51] in 2018. The reinforced beam showed much better fatigue performance than the reference beam at relatively low levels of cyclic load. However, under higher fatigue load levels, the bonding performance between Fe-SMA bars and grouting materials deteriorated. Finally, the Fe-SMAs reinforcement at the anchor end broke after about 5.5 million loading cycles.
In another case, Rojob et al.
[49] reported research on the freeze–thaw and durability performance of RC beams strengthened with activated Fe-SMA bars. After exposure to 650 freeze–thaw cycles under sustained loading, the deterioration of the reinforced beam was insignificant, and the yield and ultimate capacities decreased by 19% and 12%, respectively, while serious spalling and cracking of concrete appeared on unreinforced beams. Furthermore, superior bonding behavior between Fe-SMA bars and grout as well as a reliable anchorage system was conducive to enhancing the performance of RC beams in a harsh environment.
An interesting experimental investigation was reported by Shahverdi et al.
[76], in which two NSM RC beams with activated and inactivated Fe-SMA strips were exposed to an outdoor environment under sustained loading and monitored their behavior for about four years. The mid-span deflection of the two beams showed similar trends and the deformation mainly happened in the first three months. Moreover, the final deflection of the beam with activated Fe-SMA strips was reduced by 22.7% than another one due to the existing prestress.
The structural fire behavior of RC beams with activated Fe-SMA strips was first systematically studied by Ghafoori et al.
[57]. To research the fire behavior of SMA material, transient total deformation tests were carried out on Fe-SMA strips with thicknesses of 1.5 mm and 0.5 mm under different load levels and heating rates. The result showed that the mean creep onset and failure temperatures of 1.5 mm strips were higher than that of 0.5 mm strips, and the two temperatures were reduced with increasing service load levels.
5. Prospects of Future Development
The identified future potential for Fe-SMAs’ application:
(1) Fe-SMAs have not yet been widely accepted by the market, because their cost is higher than other reinforcement materials, such as CFRP, which is mainly caused by a backward production process. Therefore, improving the manufacturing technology of Fe-SMAs is meaningful to reduce the cost and promote their applications in civil engineering.
(2) Compared with other SMAs, the good weldability of Fe-SMAs is a significant advantage in civil engineering applications, which can greatly reduce the cost of connection. However, previous studies are very limited to investigate the weldability of Fe-SMAs. Therefore, developing weldability, including welding methods and processes, of Fe-SMAs with dissimilar alloys, especially constructional steels, is worth considering.
(3) Fe-SMAs as reinforcement materials are subjected to the humid and variable environments, even corrosive conditions (sea water, chemical waste liquid, etc.). Improving the corrosion resistance of Fe-SMAs should be highlighted, especially for the rehabilitation of
(4) Bridges constantly undergo the traffic load in service life; hence, the shrinkage and creep of concrete inevitably occur due to the varying of temperature or humidity, resulting in prestress loss of Fe-SMAs. Therefore, the prestress loss should be considered in the design stage.
(5) Most studies in the field of reinforcement by Fe-SMAs have mainly focused on the component level, but few studies concern the application of in-service bridges that are undergoing multi-factor effects, such as cyclic loads, elevated temperatures, and corrosive environments. In the future, applying Fe-SMAs to strengthen the existing deteriorative structures may be a promising research direction.
6. Conclusions
This research introduces the classification, mechanism of SME, and development history of shape memory alloys, especially Fe-Mn-Si alloys. The development of the mechanism, techniques, and applications of Fe-SMAs in enhancing RC bridges in the past two decades have been summarized, and some perspectives for future potential development have been put forward. The following conclusions can be drawn:
(1) Fe-SMAs represented by Fe-Mn-Si alloys have the advantages of low cost, wide thermal hysteresis, excellent SME, and high elastic modulus, which guarantee great potential for their application in civil engineering.
(2) The SME of Fe-Mn-Si alloys is caused by the γ → ε martensite transformation and its reverse transformation can produce huge recovery stress (400~500 MPa) which can be used as prestress in reinforcement.
(3) Activation methods of Fe-SMAs are varied, including thermal resistance heating, climate chamber heating, flexible tape heating, infrared radiation heating, heat gun heating, flame heating, inductive coil heating, electric furnace heating, autoclave heating, and so on. However, resistance heating is the most widely used activation method in the application, especially in civil engineering.
(4) NSM Fe-SMA technique is the most common method to strengthen RC beams and can effectively protect Fe-SMA strips from damage. Moreover, embedding ribbed Fe-SMA bars in the shotcrete layer is another promising method.
(5) The strengthening of RC beams with Fe-SMAs has achieved great application effect on flexural performance, shear performance, fatigue performance, durability, etc., hence it deserves to be promoted worldwide in the rehabilitation of RC bridges in the near future, especially under the global goal of carbon neutrality.