The continuum–discontinuum method (CDM) is a promising tool for the study of the rock fracture and fragmentation process under static or dynamic loading conditions, e.g., blasting. The hybrid/combined finite element method (FDEM) might be the most widely used continuum–discontinuum method. Based on the FDEM, many tools are developed for modelling the entire rock fracture process, e.g., Y-2D, Y-GUI, Y-GEO, Y-Slope, Y2D/3D IDE, and the commercial software ELFEN.
1. Introduction
The fast development of modern society results in a variety of geotechnical activities, some of which require the excavation of rock cuts. Those actives, e.g., embayment, open-pit mining, and highway and urban contraction, can form many slopes.
The slope stability is always seen as critical, since even the tiniest slope failure may be costly in terms of monetary damage and human lives. It is essential to understand the geological, geomorphological, and hydrogeological characterization of a slope before the reconstruction of any structure. More importantly, a comprehensive understanding of the impacts of the external factors, e.g., external loading, seismicity, and groundwater, is crucial for preventing and controlling slope instabilities. In addition, the rock characteristics of the slope, e.g., faults, folds, and discontinuities, are significant factors influencing the stabilities of the rock slopes. The stability analysis of the rock slope is always associated with the factor of safety, which is the most well-known performance indicator in slope stability. The factor of the safety of the rock slope is a ratio of the average shear strength of a specific slip face to the average applied shear stress. If the ratio, i.e., the factor of the safety F=1, it represents the “critical equilibrium” or “limiting equilibrium”, and this implies that a slope is on the verge of collapse or sliding, or complete failure. In this scenario, the rock slide is imminent along a certain slip surface. If the factor of the safety F>1, the slope is stable and it is not on the verge of sliding. If the factor of the safety F<1, it represents instability, and in this case, the slope design cannot be constructed.
In general, the rock slope has four categories in terms of failure types, i.e., plane failures, wedge failures, toppling failures, and circular failures. The rock slope stability analysis is essential for many engineering projects, e.g., road cuts and open-pit mining. The main purposes of the rock slope stability analysis are to determine the stability of the rock slope, to investigate the different support options, and to optimize the slope in terms of reliability. There are many techniques available for performing the analyses, which can be in general classified into the conventional methods and numerical methods. The conventional methods include limit equilibrium techniques and the kinematic method. Limit equilibrium techniques are popular methods for the analysis of the plane or the toppling failure of the rock slope. This technique can provide a factor of safety or it can provide shear strength parameters for a rock slope. There are also lots of computer programs used for slope instability analysis, which are made based on the limit equilibrium concept
[1]. The limit equilibrium approach has traditionally been used to test the stability of rock slopes, which are confined to the analysis of planar or wedge instabilities, while other complicated failure kinematics, such as toppling, are often not addressed by these methodologies.
The numerical methods are significant tools utilized during the slope design stage. As for the numerical techniques, there are mainly two categories, i.e., the continuum method and the discontinuum method. The representative continuum methods for modelling the rock slopes are the finite element method
[2], failure-process analysis method (RFPA)
[3], numerical manifold method (NMM)
[4], and finite difference method (FDM)
[5]. Jin, Yin and Yuan (2020) used the smooth-particle finite element method to simulate the rock slope failure process
[2]. The smooth-particle finite element method is an updated Lagrangian approach with frequent re-meshing by the Delaunay triangulation method
[2]. To employ continuum modelling, the rock mass in the slope is considered as a continuum material. In addition, the finite element method is widely used to study the failure mechanisms of the unsupported conical slope by the implementation of various rock failure models and criteria
[6][7][8][9][10], e.g., the anisotropic undrained shear (AUS) model
[9] and the Hoek–Brown failure criterion. However, for a real rock slope, there are unavoidable pre-existing planes of weaknesses, e.g., schistosity, joint sets, and faults. Those weaknesses in the rock slope might be the key issues that result in the instability of the rock slope. The continuum technique has limits in explicitly simulating complicated discontinuities, progressive failure, substantial deformation, and complex rock movement during the whole failure process due to the continuum assumptions
[11]. There is also a variety of discontinuum methods applied for the simulation of the rock slope failure process. The distinct element method (DEM)
[12] might be the most widely used discontinuum method. Jiang and Murakami (2012) employed the distinct-element method to model the full-process slope failure. The particle flow code (PFC)
[3] and the discontinuous deformation analysis method (DDA)
[13] are widely used to model the slope failure process. As the hybrid finite–discrete element method (FDEM) is one of the most popular approaches to modelling the rock fracture process, and
Table 1 lists the representative study on the FDEM modelling of rock slope failure processes.
Table 1. Summary of FDEM modelling of the rock slope failure process.
Numerical Code
|
Modelled Results
|
Reference
|
Y-Slope
|
Y-Slope considers the tensile and shear failure. The failure is caused by gravity. By decreasing the strength parameters, the cracks initiate from the toe of the slope and propagate further into the slope. Finally, the cracks form a discontinuity surface. The crack initiation, propagation, colliding, fragmentation, and piling are modelled.
|
[14]
|
FDEM realized using ABAQUS/Explicit
|
The FDEM framework is implemented in the ABAQUS/Explicit. The cohesive zone model (CZM) is employed to model the fracture occurring along the bulk elements boundary. The gravity increase method is implanted in the ABAQUS/Explicit-based FDEM program to model the slope failure process. The failure processes of the laboratory-scale slope with various joint inclination surfaces are modelled.
|
[15]
|
Y-Geo
based on Munjiza’s Y-code
|
Y-Geo is used to model the evaluation of a rock slide that occurred in Italy in 1997. The modelled results in terms of the runout profiles and evaluation of the slopes agree well with the site observation.
|
[16]
|
ELFEN
|
A modified Mohr–Coulomb elastoplastic model is implemented in ELFEN to model the material softening, and deal with both the tension and shear states. Then, the ELFEN was employed to model the 1991 Randa rockslide. Due to strength degradation, the rock mass breaks into blocks and are modelled using ELFEN.
|
[17]
|
Y-2D with Y-GUI
|
The failure process of the rock avalanche is modelled. The weak interface in the slope was firstly produced, then, the rock avalanche was initiated. A large volume of rock mass started to move, which further fragmented. During the process, the blocks were progressively broken into smaller fragments.
|
[18]
|
2. Combined Finite–Discrete Element Method
The continuum–discontinuum method (CDM) is a promising tool for the study of the rock fracture and fragmentation process under static or dynamic loading conditions, e.g., blasting
[19][20][21][22][23][24][25]. It has been successfully applied in many geotechnical engineering problems associated with the transition from continuum to discontinuum through fracture and fragmentation over the last two decades
[26][27][28][29]. Compared with the continuum method or discontinuum method, the CDM can not only model the rock damage, fracture initiation, coalescence, and propagation as most of the continuum-based methods do, but it also can model the interaction of the fracture rocks and even the muck-pilling of the rock fragments during a rock blasting process
[25]. Many CDM methods have been proposed for overcoming the shortcomings of the continuum-based method or discontinuum method in simulating the entire rock fracture process, e.g., the combination of the boundary element method with the finite element method (BEM/FEM), the combination of the discrete element method with the finite element method (DEM/FEM), and the combination of the discrete element method with the boundary element method (DEM/BEM)
[30].
The hybrid/combined finite element method (FDEM) might be the most widely used continuum–discontinuum method. Based on the FDEM, many tools are developed for modelling the entire rock fracture process, e.g., Y-2D
[31], Y-GUI
[32], Y-GEO
[25], Y-Slope
[14], Y2D/3D IDE
[25], and the commercial software ELFEN
[33][34]. Y-slope models the crack initiation, propagation, colliding, fragmentation and pilling process during the rock slope failure process
[14]. Y2D/3D IDE has been implemented to model the entire fracture, fragmentation, and muck-pilling process induced by the blast
[25], and has also been used to study the excavation damaged zone (EDZ) induced by blasting in deep tunnels
[24]. Y-GUI is a graphical user interface developed for Y2D, as Y2D setting up Y2D modes is a time-consuming and error-prone process
[18]. The GUI is developed to setup Y-2D modes graphically and minimize the possibility of erroneous input files
[18]. Y2D has modelled the slope failure process where rock avalanches occur
[18].
As the FDEM has been used in many geotechnical problems, the fundamental principles and FDEM applications have been introduced in detail. For a FDEM mode, it can have one discrete body or many discrete bodies.
Sun et al. (2022)
[14] gave the rock mass with fracture and its equivalent FDEM model meshed by three-node finite element and four-node joint elements. The rock model is meshed using finite elements and the cracks are modelled using the broken joint elements, i.e., crack elements. The stress and strain of the individual body are described using the continuum law. The fracture of the rock, i.e., the transition from continuum to discontinuum, is modelled by the breakage of the joint element among the three-node finite elements. The motion of each node of the discrete body is updated using Newton’s second law (Equation (1)
[35]).
where M is the mass of the discrete body while C is the damping diagonal matrices, X is the nodal displacement and F is the node force vector.
Contact detections of the discrete elements or discrete bodies are essential for the FDEM, as there might be thousands or even millions of discrete elements or discrete bodies. Thus, many algorithms for automatic contact detection are proposed
[31][36], e.g., the no-binary search, buffer zone, binary tree, and alternating digital tree. After the coupled discrete elements or discrete bodies are detected, the contact forces between the coupled discrete elements or bodies are calculated.
Most of the FDEMs use the penalty method to calculate the contact forces in the tangential and normal directions
[21][31]. The two bodies are called the target and contactor, respectively. The penetration of the contactor into the target causes contact force. An infinitesimal contact force due to the penetration can be calculated using Equation (2)
[31], while the total contact force due can be calculated using Equation (3)
[31].
where df is the infinitesimal overlap dA force and the φc and φt are potential functions.
During the contact interaction, the discrete element or bodies are deformable and the joint elements can be distorted to perform the continuum of the rock mass. The distortion in the vertical and normal direction will finally result in the shear and tensile failure, which perform the transition of the intact rock from continuum to discontinuum through the rock fracture and fragmentation. Bonding stress is induced during the distortion or the separation of the joint elements. The bonding stress in the normal direction can be obtained according to Equation (4)
[37]:
The tensile fracture or the Mode-I fracture process is governed by the Mode-I fracture energy release, and the value can be calculated as follows (Equation (5)
[37]).
where the GfI is the Mode-I fracture energy release rate.
The shear stress
τ increases with the increase of the sliding
δs and the shear strength corresponds to the sliding displacement of
δsp, which indicates the shear fracture occurs. After that, the boding stress in the tangential direction or the shear stress decreases. As it decreases to a residual stress
δsr according to a mechanical damage model, the shear fracture finishes. The bonding stress in the tangential direction can be expressed as Equation (6)
[37] according to the sliding displacement of the adjacent finite elements.
where
D is the damage variable and
g(D) is the function of the damage
[38], and
∅f is the joint residual friction angle.
When Equation (7)
[37] is satisfied, the mixed-Mode I–II occurs.
It should be noted that although most of the FDEMs, e.g., Y-FDEM
[22] and Y-Slope
[14], are implemented based on the open-source combined finite–discrete element libraries Y2D and Y3D originally developed by Munjiza (2004)
[31] and Xiang et al. (2009)
[39] and programmed using C++ or VC++, the C program is not the only platform for the implementation of the FDEM. Other platforms can be used for the implementation of the FDEM framework. Zhou, Yuan et al. (2016)
[15] proposed a cohesive zone model-based on a combined finite–discrete element method to simulate the rock sliding process at the laboratory scale. The Mohr–Coulomb model with a tension and cut-off is impended for the FDEM to model both the tensile and the shear failure. Then, the FDEM is implanted into the ABAQUA to perform the transition from continuum to discontinuum through fracture and fragmentation during the rock slope sliding process.
3. Calibration of Hybrid Finite–Discrete Element Method for Modelling the Rock Slope Failure Process
The FDEM has been calibrated by many typical rock mechanism tests, e.g., the Brazilian tensile strength test
[22], uniaxial compressive strength test
[23], three-point test
[21], and four-point test
[19]. Those modelling results indicate that the FDEM can effectively model various fracture types, i.e., tensile, shear, and combination failures. To better indicate the capability of the FDEM in modelling the entire rock failure process of a rock slope, the FDEM has been employed to model the typical rock slope failure process
[40], and it is even used for the back analysis of the rock slope in which the failure has occurred
[16].
Grasselli, Lisjak et al. (2011) modelled the toppling failure of the rock slope, which is one of the main rock slope failure types
[40], to calibrate and show the capabilities of the FDEM method in modelling the entire rock failure process of the rock slope. The rock mass on the stable section is not significantly influenced by the slope failure process, as there is no interaction between adjacent blocks and the force along the sliding face induced by gravity is not big enough to cause the blocks to slide, due to the friction on the discontinuity face.
Sun, Liu et al. (2022) developed the Y-slope to model the entire failure process of rock slopes from initiation and transportation to deposition
[14]. The Y-slope is developed based on the Y-code. The Y-slope considered the shear and tensile failure conditions by the implementation of the strength reduction methods. To calibrate the Y-slope, the equilibrium state of a benchmark is modelled.
Thus, the FDEM can model the transition of the rock slope from continuum to discontinuum through the rock fracture initiation, propagation and sliding, or rotation. In addition, it can effectively demonstrate the stress distribution and displacement distribution.
4.New Insight into GPGPU-Parallelized FDEM Modelling of Rock Slope Failure Process
Numerical methods have been implemented to model the fracture process and the FDEM is considered as a promising tool. However, the computing power limited the FDEM, not only with 3D modelling but also in carrying out large-scale 2D modelling with a small mesh size in the past. The recently developed general purpose graphic processing unit (GPGUP) accelerators have dramatically improved this situation. Thus, this section gives a brief insight into the GPGUP-parallelized FDEM in modelling the rock slope failure process.
For the modelling of the rock slope failure process using GPGUP-parallelized Y-HFDEM, the strength reduction method (SRM) is implemented in the proposed method. Then, a typical rock high slope is modelled to gain insight into the GPGUP-parallelized Y-HFDEM on the rock slope stability analysis. More details including input parameters and the slope size can be found in [41].
Figure 1 illustrates a typical rock slope failure process using the proposed method with the implementation of the SRM. The left part of Figure 1 indicates the stress distribution while the right part shows the fracture initiation and propagation. Figure 1a indicates the stress equilibrium state after the gravity of the rock mass is applied to the model. The stress concentration can be observed at the toe of the slope, where fractures initiate (Figure 1b). Then, the fractures propagate into the slope (Figure 1c) and form a sliding failure surface (Figure 1d). The rock mass slides along the newly formed sliding surface. Due to the sliding, rotation, and colliding, the rock mass breaks into fragments and finally piles at the lower bench of the slope (Figure 1e).

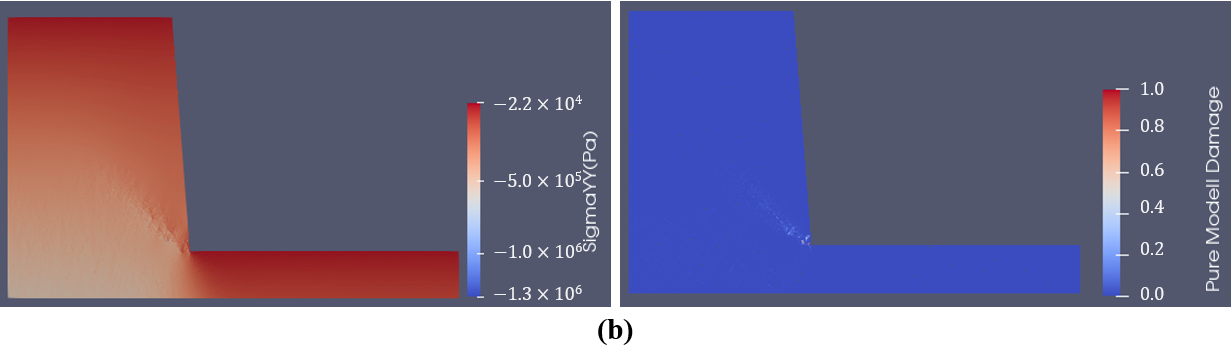
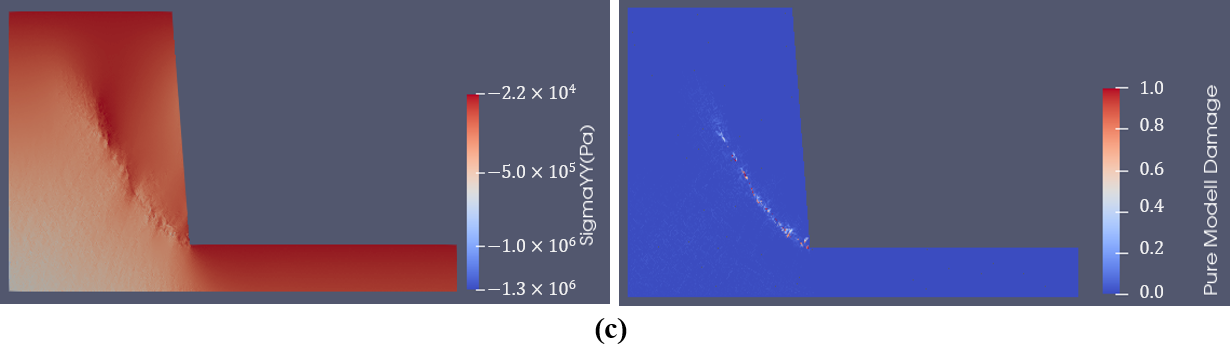
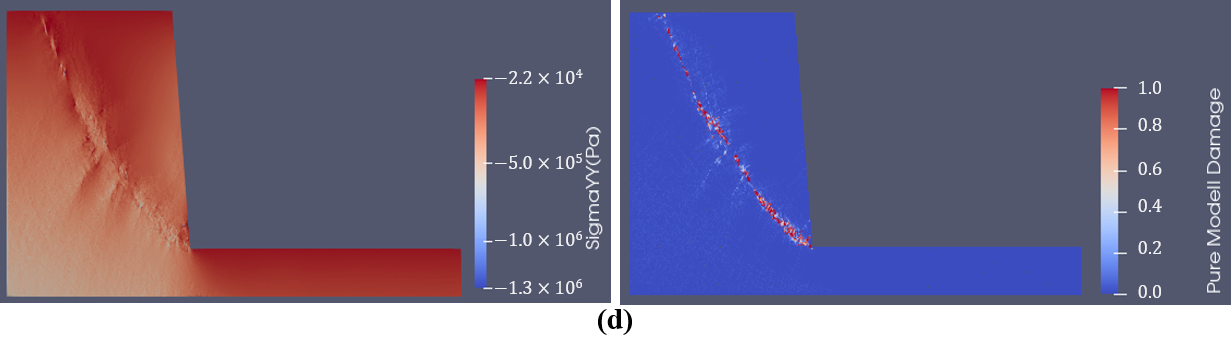
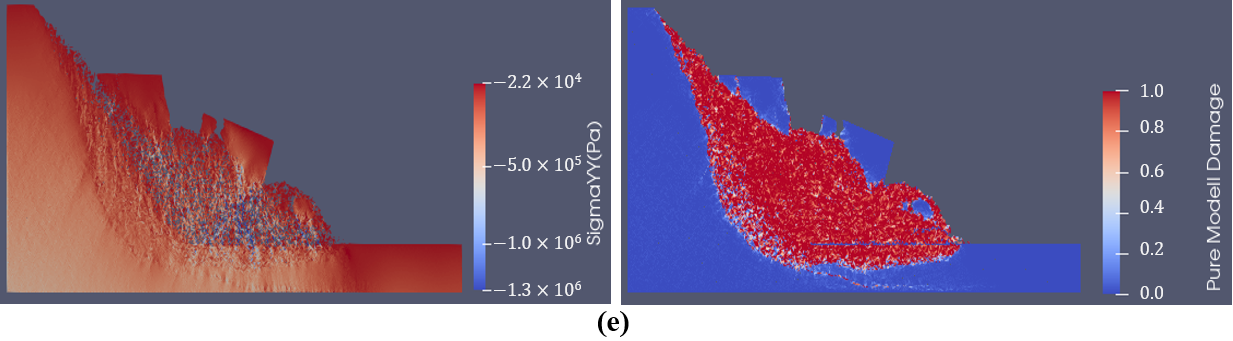
Figure 1. GPGUP-parallelized Y-HFDEM IDE modelling of rock slope failure process. (a) Stress equilibrium state; (b) 1 s; (c) 3 s; (d) 10 s; (e) 25 s.
The Figure 1 illustrates that the GPGUP-parallelized Y-HFDEM can effectively model the entire slope failure evolution process due to the implementation of the SRM in the proposed method. The GPGUP-parallelized FDEM with the implementation of SRM is a promising technique in the back analysis and prediction of the slope failure process, as it combined the advantages of the continuum methods and discontinuum methods, and it can naturally model the transition for rock from continuum to discontinuum through fracture and fragmentations.