Lignin is a complex, amorphous, natural polymer, and one of the most abundant in nature, only behind cellulose. Technical lignins are co-products of the manufacture of cellulose pulp for paper. Some examples of technical lignins that will be addressed in this study are lignosulphonates alongside kraft, soda and organosolv lignins.
1. Introduction
Although lignin is the main by-product of the paper pulping processes, it is usually burned as fuel
[1].
Out of the 50 to 70 million tons of the lignin that is produced annually, only 1 to 2% is actually used for the production of value-added products. Therefore, it can be concluded that lignin is an underutilized material
[2].
In plants, cellulose is present in the form of bundled fibrils that are bound together by hemicellulose and lignin, providing rigidity to the cell wall
[3]. Lignin performs the following functions in plants: providing mechanical support, slowing down decomposition, forming a barrier towards water evaporation, and helping to transport water to vital areas of the plant
[1]. In vitro studies have shown that lignin and lignin extracts display antimicrobial and antifungal activity, act as antioxidants, absorb UV radiation, and exhibit flame-retardant properties
[4].
Lignin is the main renewable source of phenolic compounds of natural origin. This has been increasingly researched as a more eco-friendly alternative to the petroleum-based counterparts
[5]. The molecule is comprised of several types of methoxylated phenylpropanoid units (C9). The three primary precursors of lignin are:
p-coumaryl, coniferyl, and sinapyl alcohols, as shown in
Figure 1. These monolignols are also known as
p-hidroxyphenyl (H), guaiacyl (G), and syringyl (S) units, respectively
[5][6][7].
Figure 1. Monomeric lignin precursors:
p-coumaryl alcohol, coniferyl alcohol, and sinapyl alcohol (adapted from
[5]).
These monolignols differ in the number of methoxy groups that are attached to the aromatic moiety: sinapyl alcohol has two methoxy groups, coniferyl alcohol has one methoxy group, and
p-coumaryl alcohol has none
[5]. Different types of plants display different degrees of participation of the major monolignols. As shown in
Table 1, the main monolignols in softwood and hardwoods are coniferyl and sinapyl alcohol, respectively
[8].
Table 1. Percentages of the monolignols in lignin in different plants
[8].
Plant Type |
p-Coumaryl Alcohol (%) |
Coniferyl Alcohol (%) |
Sinapyl Alcohol (%) |
Coniferous; softwoods |
<5 a |
>95 |
0 b |
Eudicotyledonous; hardwoods |
0–8 |
25–50 |
45–75 |
Monocotyledonous; grasses |
5–35 |
35–80 |
20–55 |
a Higher amount in compression wood. b Some exceptions exist.
Researchers admit that no plants contain lignin that is only derived from the three primary precursors
[5]. Noncanonical subunits that have been identified include caffeoyl alcohol, which was discovered in the seeds of some Vanilla and Cactaceae species
[9]. Other subunits are ferulic acid, ferulates (which form linkages between hemicellulose and lignin), coniferaldehyde, sinapaldehyde, and acylated monoglinols
[5]. Intermediate free radicals are generated from these lignin precursors through the dehydrogenation of phenolic OH groups by the plant’s peroxidase and laccase enzymes. The polymerization process then occurs as follows: firstly, two radicals are coupled forming a dimer, and the process progresses with the coupling of monomeric radicals with dimer, trimers, and oligomers resulting in a complex branched polymer (lignification)
[10][11].
The great complexity of the lignin structure is due to the variability of the linkages found in it, such as ether, esters, and carbon-carbon, the most abundant being the bond β-O-4, β-β, and β-5, as seen in
Figure 2 [5][12].
Figure 2. Model of lignin’s structure with the important linkages and units (adapted from
[6]).
Lignin has a great variability of functional groups in its complex structure. The main ones are shown in
Figure 3. Their abundance in the structure also depends on the source of lignin
[12][13][14]. The frequency and type of the most common linkages in softwood and hardwood lignins are described in
Table 2.
Figure 3. Main functional groups in lignin’s structure (adapted from
[13]).
Table 2. Types and frequencies of linkages in softwood and hardwood lignins [10].
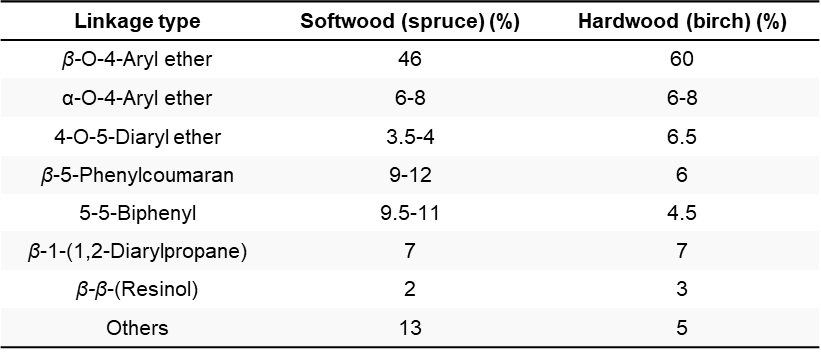
2. Technical Lignins
Technical lignins are mostly obtained as co-products of the manufacture of cellulose pulp for paper, through wood pulping (delignification) processes
[15][16]. The main objective of wood pulping is to liberate the cellulose fibers from the lignin binder and other non-fibrous compounds. The most common commercial processes can be grouped into four types: chemical, semichemical, chemimechanical, and mechanical
[17].
In chemical pulping, delignification occurs until most of the lignin in the middle lamella of the woody cell is removed. This results in an easy separation of the fibers. Most of these processes are currently based predominantly on the sulfate (kraft) process and, less frequently, on the sulphite process
[17].
On the other hand, in semichemical processes only a partial dissolution of lignin is achieved, as the wood chips are cooked during shorter periods of time or under milder conditions. Chemimechanical pulps are produced by pretreating the wood chips usually at elevated temperatures in alkaline solutions of sodium sulfite before defibration
[17]. Lastly, mechanical pulping uses no chemicals, only mechanical abrasion combined with water or steam. Thermomechanical pulping has become the most important method of this kind. In this procedure, the refiners are first pressurized with steam at high temperatures in order to promote fiber liberation and operate at ambient temperature in a second stage
[18].
During pulping lignin’s structure is inevitably modified. Therefore, the type of pulping process determines the type of lignin that is industrially obtained. Some examples of lignins derived from chemical pulping that will be addressed in this study are sulphite (lignosulphonates), kraft, soda, and organosolv lignins
[5][15].
Although there is a great diversity of technical lignins, this article will focus mainly on lignosulphonates.
2.1. Lignosulphonates
Most of the pulp in the world was produced through the sulphite process until the 1950s. After that, the kraft process has been the dominating method. However, the sulphite process is still important in some countries and for certain pulp qualities
[17].
Currently, the total annual global production of lignosulphonates is approximately 1.8 million tons. These technical lignins account for 90% of the total market of commercial lignin since the kraft process yields relatively small quantities of usable lignin
[2][15].
This consists in the digestion of wood at 130–180 °C with an aqueous solution of a sulphite or bisulphite salt of sodium, ammonium, magnesium, or calcium
[15][17]. There are several modifications of the sulphite method, which are designated according to the pH of the cooking liquor, as shown in
Table 3 [17].
Table 3. Different modifications of the sulphite method
[12][17].
|
Acid (bi)Sulphite |
Bisulphite |
Neutral Sulphite |
Alkaline Sulphite |
pH range |
1–2 |
3–5 |
6–9 |
9–13 |
Base alternatives |
Ca2+, Mg2+, Na+, NH4+ |
Mg2+, Na+, NH4+ |
Na+, NH4+ |
Na+ |
Active reagents |
HSO3−, H+ |
HSO3−, H+ |
HSO3−, SO32− |
SO32−, HO− |
Max. temp. (°C) |
125–145 |
150–170 |
160–180 |
160–180 |
Time at max. temp. (h) |
3–7 |
1–3 |
0.25–3 |
3–5 |
Softwood pulp yield (%) |
45–55 |
50–65 |
75–90 a |
45–60 |
During the digestion process the linkages between lignin and carbohydrates are cleaved, as well as the carbon–oxygen bonds that connect lignin units. However, the sulphonation of the lignin aliphatic chain is the most important reaction as it lends the resulting LS their main characteristics
[15].
This reaction consists in the attack on lignin’s structure by the negatively charged sulphite or bisulphite ions. The targets of this nucleophilic attack depend on the pH of the sulphite delignification. At high pH, quinone methide structures of phenolic units are the targets. However, at low pH, carbenium (benzylium) ions of phenolic or non-phenolic units are sulphonated at the position of the side chain, as shown in
Figure 4 [15].
Figure 4. Main reactions for lignosulphonate formation during acid sulphite pulping (adapted from
[15]).
During pulping, about 4–8% sulphur is incorporated into lignin’s structure, making lignin water-soluble and preventing its recondensation, which would result in the redeposition of lignin on the cellulose fibers
[15][19].
The resulting fiber pulp is separated from the spent pulping liquor through filtration and washing. This liquor contains 50 to 80 wt% of lignosulphonates, as well as hemicelluloses and residual pulping chemicals. The structures of these lignosulphonates may vary significantly due to the wide range of conditions under which sulphite pulping can be operated
[2][15].
Purified forms of lignosulphonates are more valuable and have broader applications than crude spent sulphite liquor. The purification process can be performed according to a variety of techniques
[4][15].
Ultrafiltration has been applied on an industrial scale to recover lignosulphonates from spent sulphite liquors. The higher molecular weight of lignosulphonates in comparison to other components in the spent liquors allows this method to be applied effectively. The result is a sugar-rich permeate and a retentate with up to 95% of lignosulphonates
[2][4][15].
Alternatively, the spent sulphite liquor can be purified through alcoholic fermentation of the sugars. Lignosulphonates exhibiting a purity over 90% can then be recovered resorting to ultrafiltration
[2][4][15].
The cation (or base) originally present in the pulping liquor can influence the physicochemical properties of lignosulphonates. For example, sodium sulphite produces longer lignin chains that are more suitable as dispersants. However, the use of calcium sulphite results in a more compact lignin
[4]. Changing this cation may therefore be required for certain applications and can be achieved through the use of ion-exchange resins
[15].
Lignosulphonates are soluble in water, have high molecular weights with a broad distribution, and a high ash content. These compounds also contain a variety of functional groups including phenolic hydroxyl and carboxylic groups and sulphur containing groups
[19].
2.2. Kraft Lignin
The kraft process is the leading pulping process worldwide. Kraft pulp mills have a highly engineered incorporated system for recovery of pulping chemicals and energy. This system is crucial for the economic and environmental performance of these mills and relies on the combustion of the black liquor. Thus, the quantity of kraft lignin recovered for chemical use is low in comparison to lignosulphonates
[11][15].
Kraft pulping uses a solution composed of sodium hydroxide and sodium sulphide, named white liquor, to cleave lignin’s ether bonds
[4][17]. This process has a total duration of approximately 2 h and the temperatures range from 150 to 170 °C
[20].
Kraft lignin is hydrophobic, highly modified, and displays a lower molecular mass than native lignin
[21]. It is also not soluble in water and mostly solvent insoluble except for in highly alkaline mediums (pH > 11)
[22].
2.3. Soda Lignin
Soda pulping was introduced in the 1850s as the first chemical pulping method
[4][15][17]. Kraft pulping originated from this process and has almost completely replaced it, due to having better delignification selectivity which results in pulp with higher quality
[17]. However, the soda process is currently becoming the main chemical pulping method of non-wood fibers such as bagasse, wheat straw, hemp, flax, kenaf, and sisal
[4][15][19].
The soda process differs from the kraft process mainly in the cooking liquor that is sulphur-free
[15][19]. Both kraft lignin and lignosulphonates can be classified as sulphur containing lignins, which are associated with environmental concerns
[22]. Soda lignin, on the other hand, is sulphur-free, meaning that its chemical composition is closer to that of native lignin
[19][23]. Soda lignins also differ from lignosulphonates in their low molecular weight, low levels of sugar and ash contaminants, and in being water insoluble. Thus, they are more similar to kraft lignins
[15].
Soda lignins from non-wood plants differ from wood lignins since they contain more
p-hydroxyl units, as well as high silicate and nitrogen
[15][19].
2.4. Organosolv Lignin
With the environmental concerns associated with sulphur, many sulphur-free extraction processes have been developed, including the organosolv process
[22]. Thus, lignin is extracted from plant-tissues with an aqueous solution of organic solvents at high temperature and pressure
[11][21]. These solvents include methanol, ethanol, acetic acid, butanol, phenol, peroxiorganic acids, ethyl acetate, and formic acid
[4][11][19][22].
The main advantages of this type of lignin is the absence of sulphur, as well as a less modified and more hydrophobic structure than kraft lignin, combined with lower ash content, higher purity, and usually lower molecular weight
[4]. Organosolv lignins also contain many reactive side chains available for further chemical reactions
[19]. However, this delignification process is not used widely, since it is expensive, requires a high amount of organic solvents, produces pulp fiber with low quality, and causes extensive corrosion of the plant equipment
[4][11][22].
2.5. Comparison of Technical Lignins
As discussed, the lignin’s final structure and composition is highly influenced by its origin and extraction method
[22]. Therefore, technical lignins display a wide range of properties
[19].
Applications of these compounds require them to possess tailored properties. These include molecular weight, purity, homogeneity, and the presence of certain functional groups. The main chemical properties of technical lignins are summarized in
Table 4 [19].
Table 4. Main chemical properties of technical lignins
[19].
Parameter |
Lignosulphonates |
Kraft Lignin |
Soda Lignin |
Organosolv Lignin |
Ash content (%) |
4.0–8.0 |
0.5–3.0 |
0.7–2.3 |
1.7 |
Sulphur content (%) |
3.5–8.0 |
1.0–3.0 |
0 |
0 |
Molecular weight, Mw |
1000–50,000 (up to 150,000) |
1500–5000 (up to 25,000) |
1000–3000 (up to 15,000) |
500–5000 |
Polydispersity |
4.2–7.0 |
2.5–3.5 |
2.5–3.5 |
1.5 |
It is important to note that the information collected in
Table 4 includes lignin from different sources. As seen in the table, lignosulphonates have the highest ash, sulphur content, molecular weight, and polydispersity
[19].
Studies have shown that the molecular weight of LS also depends on wood species. Thus, hardwood LS displayed a lower weight than softwood LS
[24].
All the lignins described in
Table 4 contain a low amount of β-O-4 linkages (below 10%) and high amounts of C-C bonds, unlike native lignin. However, LS are water-soluble for most of the pH-range, which is not the case for kraft lignin
[22].