During recent decade, the pavement sustainability has received much attention by road
agencies, companies, governments and research institutes. The aim of this paper is to introduce and
evaluate the sustainability of the technologies developed or underdeveloped to address environmental
issues of asphalt mixtures, and the waste materials and by-products that can be recycled and reused
in asphalt production. Warm Mix Asphalt (WMA) technology, the most popular waste materials to
substitute neat binder (crumb rubber modifier (CRM), recycled plastic (RP), vacuum tower bottoms
(VTB)) and/or virgin aggregates (reclaimed asphalt pavement (RAP), reclaimed asphalt shingles
(RAs), construction and demolition (C and D) wastes, steel and copper slags), and bio-binders were
evaluated with respect to their environmental and economic benefits and engineering performance
as the main components of pavement sustainability. The performance evaluation was carried out
by examining rutting, moisture susceptibility, thermal and fatigue cracking resistance. Two main
environmental impacts, greenhouse gas (GHG) emission, and energy consumption were considered to
study the environmental effects of these technologies and materials. Additionally, the economic effect
was investigated considering initial cost and long-term benefit. Results of investigation illustrated
that although each individual technology and waste material is valuable in terms of performance
and/or the environment, specific combinations such as WMA + RAP, WMA + CRM, RAP + CRM,
and WMA + CRM + RAP lead to further benefits. Notably, these combinations suffer from a lack of
comprehensive economic analysis, thus, their sustainability cannot be fully assessed and is prone to
future studies.
Introduction
Sustainability is the fulfillment of human needs and technological advancement with the least possible environmental and economic costs. Transportation is the primary need of human beings and developing sustainable transportation facilities is of main concern. Having about 83.5% of total pavement, asphalt is the dominant element of road network assets in the United States [
1]. For having a sustainable pavement, it is vital to take environmental impacts, economic benefits, and performance into account.
From the environmental perspective, researchers have sought remedies to minimize air pollution as well as natural resource exploitation for asphalt. Recently, the Mauna Loa Observatory recorded a first-ever CO
2 reading more than 410 parts per million (ppm) [
2]. Such a vast quantity requires all industrial sectors’ attempts to lower the amount of greenhouse gas (GHG) emissions to tackle the accelerated catastrophic phenomenon of global warming. Asphalt pavement manufacture is an industrial section in which materials production, construction, service, maintenance and end-of-life are the phases that energy consumption and GHG emissions occur. Among them, materials production and construction are the major phases [
3]. Materials production involves raw material procurement, transport of raw materials, and asphalt mixture manufacture [
3]. In 2007, roughly 1.6 billion metric tons of asphalt was produced worldwide [
4], which resulted in 14.4 × 10
6 m
3 of fuel, 1.28 × 10
4 GWh of electrical consumption and 46.08 million tons of CO
2 emissions, accounting for 0.15% of global CO
2 emissions. Construction of pavements, on the other hand, involves three sub-phases of transport, paving, and compaction of asphalt mixtures. Just the last sub-phase has the potential to reduce emissions if modification applied for better compactability. Moreover, the energy consumptions and emissions occur within service, maintenance, and end-of-life can be reduced via improved performance of asphalt mixtures. Another environmental aspect of asphalt mixture production is waste management. Use of recycled aggregate and asphalt modification by waste polymers and by-products are remedies to preserve natural resources and avoid dumping environmentally harmful and hazardous wastes [
5]. However, for sustainable pavement, economic and performance limitations of these environmental remedies should also be considered.
The economy plays a crucial role in the industry, and any environmental enhancement should satisfy economic restrictions. Since road pavement is energy demanding and natural reserve consuming, any environmental improvement leads to certain economic advantages. Although it might be discouraging to have an initial cost increase due to environmental considerations, the long-term benefit assessment could justify it. Various aspects of asphalt mixture performance are the influential factors on life-cycle analysis (LCA) which decree the environmental-economical profitability. Better performance guarantees longer lifespan as well as higher serviceability, which, in turn, reduces reconstruction, maintenance, and rehabilitation costs. Additionally, less natural resources, including fuel, aggregate and asphalt binder, are consumed in the long-term. Therefore, the optimal balance between engineering (performances), environmental, and economic aspects brings sustainability to pavement assets (). The typical sustainability studies usually focus on three components: economic development, social development, and environmental protection [
6]. However, in this study, the social development criterion is substituted by performance to better evaluate the engineering sustainability of the studied asphalt mixtures and technologies.
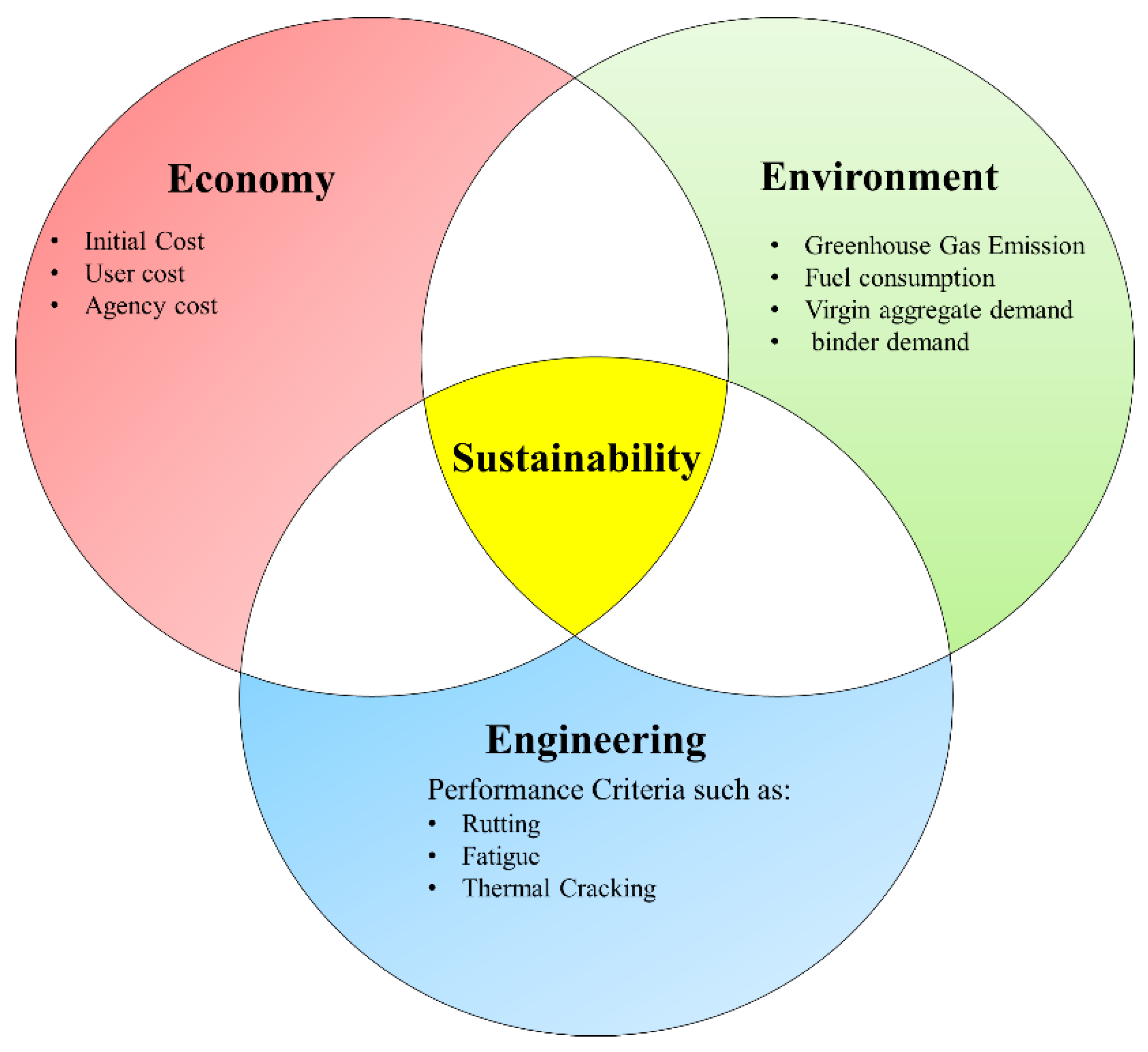
Figure 1. Engineering sustainability of pavements.
The decrease in energy consumptions and GHG emissions, life cycle extension, and better serviceability can be achieved by the exploitation of waste materials, such as reclaimed asphalt pavement (RAP), reclaimed asphalt shingles (RAS), and crumb rubber modifier (CRM) and/or adoption of warm mix asphalt (WMA) technologies. Therefore, in this research, WMA technologies employment and application of the most popular and approved waste materials (RAP, RAS, and CRM) were evaluated regarding environmental, economic, and engineering performance in
Section 2. In
Section 3, the less popular waste materials, such as construction and demolished (C and D) waste, copper and steel slag, recycled plastic (RP), vacuum tower bottoms (VTB), and bio-binder modifiers were investigated regarding, mainly, engineering performance aspects due to the lack of comprehensive environmental and economic studies. Finally, the most popular combinations of the mentioned waste materials and technologies were also evaluated based on recent studies in
Section 4. illustrates the structure of this study adopted for investigation of sustainability escalation in the asphalt industry.
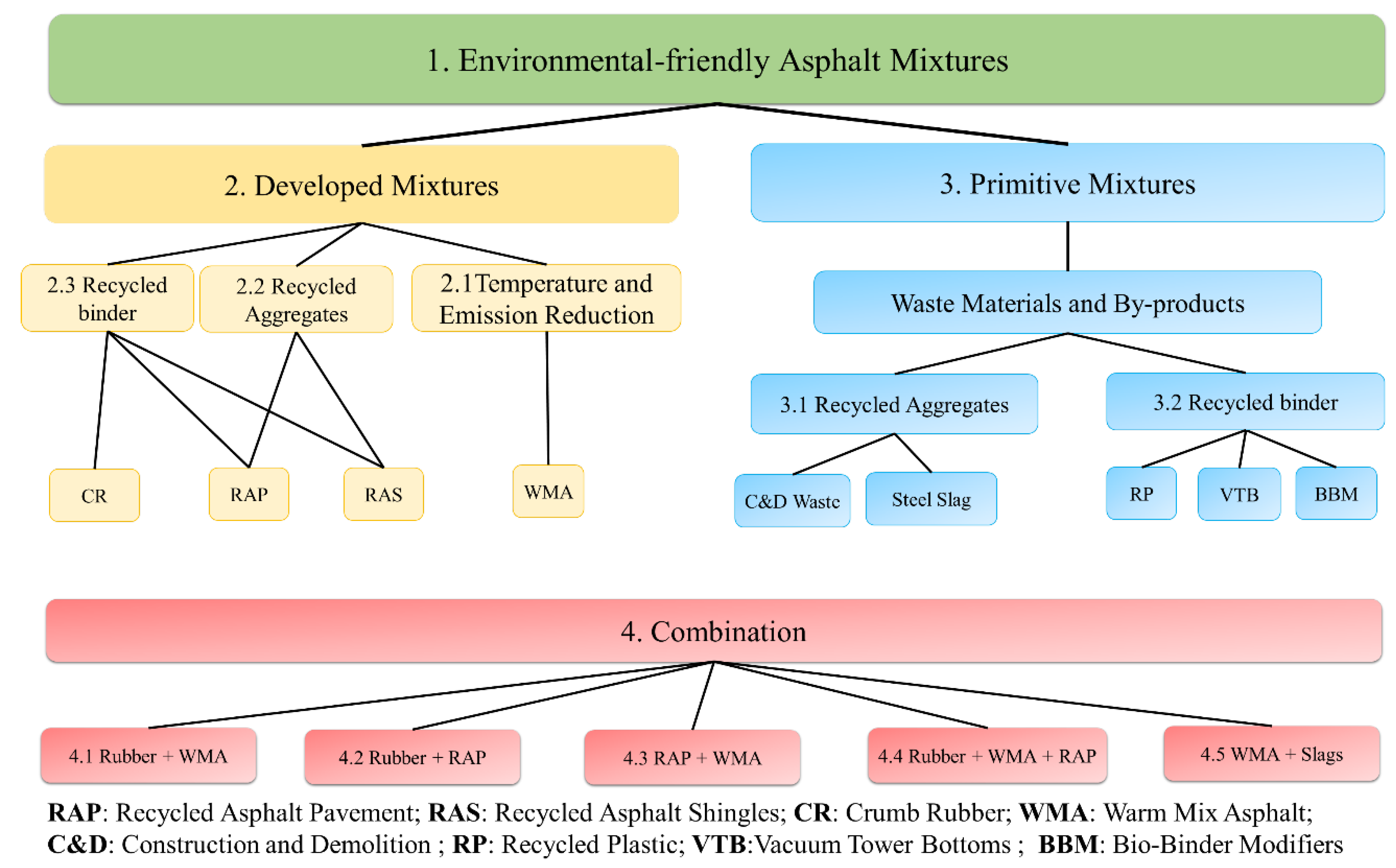
Figure 2. Flowchart of the research content.
Developed Mixtures
Temperature and Emission Reduction (WMA)
Warm mix asphalt mixtures (WMA) are those asphalt mixtures with lower mixing and compaction temperatures that are more environmentally-friendly compared to conventional hot mix asphalt (HMA) mixtures. The conventional HMA mixtures have a production temperature of 150–190 °C while WMA mixtures can lead to a temperature reduction between 14–50 °C depending on the used warm mix technology [
7]. As the most important benefits of WMAs, they reduce fuel consumption and GHG emissions, improve working conditions for paving crews due to less harmful emissions, decrease binder aging, increase hauling distance, potentially increase the field densities (better compactability), and extend paving seasons.
However, compared to conventional HMA, a high change in pavement performance can be expected due to the reduction in production temperatures and modifications of binder characteristics. For example, although low binder oxidation may increase the pavement cracking resistance, it may decrease the moisture and rutting resistance [
8]. There are also other technologies, namely half warm mix asphalt (HWMA), which can lower the production temperature to 60–100 °C [
9]. However, because of their poor performance, they have not drawn attention as WMAs.
WMA Technologies
As presented in , WMA technologies are divided into three main categories: (1) foaming (e.g., Astec Double Barrel Green and Advera); (2) organic additives (e.g., Sasobit); and (3) chemical additives (e.g., Evotherm). Foaming involves using the introduction of water or water-containing additives into hot binder during production. Water then turns into bubbles that facilitate the flow of the binder and provide sufficient low viscosity to coat the aggregate at lower temperatures. Consequently, due to the bubble generation, the volume, and viscosity of binder increases and decreases, respectively. In general, the characteristic of the foamed binder is a function of source, date of production, and type of polymer modification (Newcomb et al., 2015). In case of binder properties, the results of NCHRP report 807 showed that although the increase in the water content results in higher expansion ratios (ER), it can reduce the rate of collapse (k-value), foam-ability index (FI), and bubble surface area index (SAI). Furthermore, increasing water content reduces workability and coat-ability of the foamed binders. The better workability and coat-ability can be achieved by applying higher mixing temperatures and foaming at the optimum water content, respectively [10].
Table 1. Products used in warm mix technologies (After [
9]).
WMA Processes |
Product |
Description |
Additive Dosage |
Production Temp. (Reduction Range) |
Foaming |
Water-containing |
Aspha-Min |
Water-containing technology using zeolites |
0.3% by total weight of the mix |
(20–30 °C) |
Advera |
Water-containing technology using zeolites |
0.25% by total weight of the mix |
(10–30 °C) |
Water-based |
Double Barrel Green |
Water-based foaming process |
2% water by mass of bitumen; anti-strip agent |
116–135 °C |
Ultrafoam GX |
Water-based foaming process |
1–2% water by mass of bitumen |
Not specified |
LT Asphalt |
Foam bitumen with hydrophilic Additive |
0.5–1% by mass of bitumen |
90 °C |
WAM-Foam |
Soft binder coating followed by foamed hard binder |
2–5% water by mass of the hard binder |
100–120 °C |
Low Energy Asphalt |
Hot coarse aggregate mixed with wet sand |
3% water with fine sand |
<100 °C |
Low Emission Asphalt |
Hot coarse aggregate mixed with wet sand, combined with chemicals |
3% water with fine sand; 0.4% bitumen weight |
90 °C |
LEAB |
Direct foam with binder additive. Mixing of aggregates below water boiling point |
0.1% of bitumen weight of coating and adhesion additive |
90 °C |
Organic additives |
Sasobit |
Fischer-Tropsch (F-T) wax |
Approx. 2.5% by weight of binder in Germany; 1–1.5%, in the USA. |
(20–30 °C) |
Rheofalt LT-70 |
Fischer-Tropsch wax |
1–3% |
110–140 °C |
Asphaltan B |
Refined Montan wax with fatty acid amide for rolled asphalt |
2.0–4.0% by mass of bitumen |
(20–30 °C) |
Licomont BS |
Fatty acid amide |
3.0% by mass of bitumen |
(20–30 °C) |
3E LT or Ecoflex |
Proprietary |
not specified |
(30–40 °C) |
RH |
polyethylene wax |
1–3% by mass of bitumen |
(30 °C) |
Chemical Additives |
Evoterm Technologies |
Chemical packages, with or without water |
0.5% of the mass of bitumen emulsion. The emulsion contains 70% of bitumen |
85–115 °C |
Cecabase RT |
Chemical package |
0.2–0.4% by mixture weight |
(30 °C) |
Rediset |
Cationic surfactants and an organic additive |
1.5–2% of bitumen weight |
(30 °C) |
Revix |
Surface-active agents, waxes, processing aids, polymers |
Not specified |
(15–25 °C) |
Iterlow T |
|
0.3–0.5% by mass of bitumen |
120 °C |
Zycothem |
Nanomaterial liquid anti-strip agent |
0.1–0.15% by mass of bitumen |
(~20 °C) |
Organic additives are waxes including Fischer-Tropsch wax, fatty acid amide, and Montan wax with melting temperatures (80–120 °C) lower than the HMA production temperature and higher than in-service temperature. Having lower viscosity compared to the binder at similar temperatures, waxes can decrease the viscosity of binder once they substitute a small portion of the binder content, 2–4% of the weight of the binder [
9].
Chemical additives are another category of WMA technology that improves the bonding between aggregates and binder, compaction, coating, and workability. They can be a surfactant, anti-stripping agents, polymers, or a combination of them [
11,
12,
13,
14].
Increases in the application of WMA mixtures during the past two decades makes them an essential asphalt technology for the 21st century. For example, in the United States, a dramatic increase in adoption of WMA technology (tripled) was observed from 2009–2011. The federal highway administration (FHWA) also reported that more than 40 states have used WMA mixtures to pave the roads and at least 14 state highway agencies have implemented specifications to use WMA mixtures [
15]. As a part of NCHRP report 843, results of a survey about application of WMA technologies from 18 department of transportation (DOT) in United States revealed that foaming technologies (53.2%) were more popular than the other two technology (organic and chemical additives with 16.9% and 29.9%, respectively) [
16]. However, this survey was conducted for the WMA mixtures with minimum 40 °C reduction in the production temperatures compared to conventional HMAs. Additionally, among of the used additives, Evotherm with 23.4% was the most widely used additive, followed by Sasobit (16.9%), Astec DBG (15.6%), and Advera (10.4%). The other survey conducted by the national asphalt pavement association (NAPA) presented that about 77% of WMA used foaming technology, followed by chemical and organic additives (21.1% and 1.9%, respectively) in the U.S [
1].
The main reason for the popularity of foaming technologies is that they have a lower production cost than other WMA technologies (see ). NAPA also reported that 31.2% (116.8 million tons) of the total produced asphalt mixture used in the United States was WMA in 2016. However, 68% of WMA was produced at HMA temperature [
1]. Therefore, although it cannot be environmentally beneficial at all, some other advantages of WMA, such as better compactability, extended construction season, and hauling distance are still available.
Table 2. Production Cost of WMA [
17].
Fuel Source |
Price of Additive (USD per Ton) |
Reduced Energy Costs (USD per Ton) |
Increased Production Cost (USD per Ton) |
Oil Fuel (Iceland) |
Diesel (HI, USA) |
Natural Gas (IL, USA) |
Oil Fuel (Iceland) |
Diesel (HI, USA) |
Natural Gas (IL, USA) |
WMA 20% (Sasobit) |
1.3–2.6 |
1.3 |
1.7 |
0.6 |
0–1.3 |
−0.4–0.9 |
0.6–2 |
WMA 30%(Aspha-min) |
3.96 |
1.9 |
2.6 |
0.83 |
2.06 |
1.36 |
3.13 |
WMA 40% (Foam) |
0.3 |
2.6 |
3.5 |
1.1 |
−2.3 |
−3.2 |
−0.8 |
I. Environmental Evaluation
Burning fossil fuels and heated binder are the two sources of GHG emissions during the production phase. Any production temperature decrease leads to cleaner production since less fuel is consumed and there is lowered binder temperature. WMA results in asphalt mixtures with 20–40% reduction in fossil fuel consumption in comparison to conventional HMA [
17]. As shown in , WMA technologies are very effective in terms of the GHG emissions decrease. These results were extracted from the stack emissions tests for 15 projects worldwide and showed that although the reduction in carbon dioxide (CO
2), oxides of nitrogen (NO
x), and carbon monoxide (CO) is significant, in some projects, an increase in sulfur dioxide (SO
2) was observed. Furthermore, as a part of NCHRP report 779, results of an investigation on stack emissions of three multi-technology projects in Michigan, Indiana, and New York States indicated that application of WMA results in a 20% reduction in CO
2 emission compared to the corresponding HMA due to a 21% reduction in fuel usage [
7]. However, there was an insignificant difference between the CO emissions for the WMA and the corresponding HMA mixtures. In the case of volatile organic compounds (VOC) emission, although a 50% reduction in VOC emissions was reported for a Michigan plant, the higher VOC emissions were observed for the New York project. The high variation in VOC emission can be justified by the difference between the burner design, fuel type, maintenance, and tuning of the studied plants. For NO
x emission, results of this study showed a slight reduction while the significant reduction in SO
2 was observed for the only plants that used reclaimed oil as fuel. Temperature reduction and, consequently, less harmful gasses production provide a better working condition for workers, especially in the case of paving in a covered area like tunnels. Results of total organic matter (TOM) in breathing zones of paving crews for some projects indicated that the WMA mixtures have at least a 33% reduction in TOM compared to conventional HMA mixtures [
7].
Table 3. Percentage of gas emissions reduction due to WMA from different countries’ data.
Emission Component |
Oliveira et al. [18] |
Middleton and Forfylow [19] |
Vaitkus et al. [20] |
Powers [21] |
D’Angelo et al. [6]; Capitão et al. [22] |
McIver [23] |
Davidson and Pedlow [24] |
Larsen et al. [25] |
De Groot et al. [26] |
CO2 |
32 |
10.9 |
30–40 |
13.8 |
15–40 |
46 |
17.4 |
31.4 |
31 |
SO2 |
24 |
−14.3 |
35 |
- |
20–35 |
81 |
−17.2 |
- |
- |
VOC |
- |
- |
50 |
31.9 |
50 |
30 |
20 |
- |
- |
CO |
18 |
10.4 |
10–30 |
- |
10–30 |
63 |
19.5 |
28.5 |
29 |
NOX |
33 |
8.3 |
60–70 |
16.1 |
60–70 |
58 |
20 |
61.5 |
62 |
Dust |
- |
- |
20–25 |
- |
25–55 |
- |
- |
- |
- |
Concerning the construction phase, using WMA technology, a decrease in compaction effort and fewer passes of the roller to reach a target air void adds more environmental and economic benefits by reduced fuel consumption [
27,
28]. However, some WMA technologies require further mixing effort for asphalt production that can increase the energy consumption. Thus, to assess the overall environmental effect of WMA, the additional amount of energy incorporated into WMA production and its environmental impacts must be considered. Such comprehensive evaluation can reveal the real environmental influence of WMA production. Additionally, accomplishing companion tests using the same mixture, fuel, and production rate can help to reach better and meaningful comparisons between the GHG emissions of HMA and WMA.
II. Economic Evaluation
Economic evaluation (cost vs. benefit) of each new technology is one of the main factors that control its acceptance into conventional practice. Compared to conventional HMA mixtures, the use of WMA mixtures have some certain economic costs and potential benefits. The type of WMA technology is the main factor that affects the costs of WMA mixtures because some WMA technologies require modification processes that makes initial costs increase. The initial cost for WMA technologies can be affected by some factors, such as modifications to the plant’s control system, installation of mechanical equipment, additives, and mix design costs. Additionally, like other products, the initial cost is a function of the freight costs and can be varied during the times. For example, the primary water-injection foaming systems cost around $80,000 while their cost has reduced to $30,000 in the last decade [
7]. It is reported that adding the WMA additive can increase the total cost of production by approximately $2.00 to $3.50/ton [
29]. Furthermore, implementation of newly developed mix design specifications for WMA mixtures, such as NCHRP Report 691, may result in increasing mix design costs by $1500–$2000 due to conduct compactability, coating, and flow number tests [
7,
30]. However, the results of the cost analysis for some WMA technologies proved that the initial cost due to some plant modifications and equipment installation could be deprecated over 5–7 years and additive and mix design costs may be compensated by the following benefits of WMA [
7]:
-
Reduction in energy consumption at the plant;
-
Increase in payments due to achieving higher in-place densities;
-
Extended paving seasons; and
-
The possibility of removing antistripping additives for some WMA additives.
shows an example of the estimated costs and potential economic benefits for using WMA. This illustrates that the only energy savings could offset the cost of water-injection foaming systems. Another study also revealed that the implementation of foaming technologies could decrease the energy consumption up to 30–40%, while using Aspha-min and Sasobit can lead to energy reduction by 30% and 20%, respectively [
31]. Superposing the reduced cost due to less energy consumption and price of WMA additive, there are increased production costs for Sasobit and Aspha-min (with the Asphamin having greater values), while foaming technology reduces them [
31]. Additionally, results of a comprehensive study on the effect of WMA on the plant energy in the US revealed that, on average, a 27 °C decrease in the mix production temperature results in burner fuel savings of 22%, which is equal to 1100 British Thermal Unit (Btu)/°F/ton in energy savings [
7]. In general, it can be concluded that, regarding WMA technology and the additive dosage, the reduced energy consumption can be between 20% and 40%.
Table 4. A summary of cost and economic benefit for WMA technologies (after [
7]).
Cost and Potential Economic Benefits |
WMA Type |
Water Injection Foaming |
Additive |
Typical technology cost ($/ton) |
$0.08 |
$2.50 |
Assumed temperature reduction (°C) |
13 |
25 |
Typical energy savings ($/ton) |
Natural Gas |
$0.16 |
$0.31 |
Recycled fuel oil (RFO) |
$0.39 |
$0.79 |
Typical incentive/disincentive spec. savings ($/ton) |
Density improvement |
0 to $1.13 |
0 to $1.13 |
Possible savings from eliminated antistripping agent |
Hydrated lime |
0 |
0 to $1.50 |
Liquid ASA |
0 |
0 to $0.75 |
It is important to note that, here, the initial costs decrease or increase needs to be justified with respect to long-term cost-benefit analysis incorporating service, maintenance, and end-of-life phases. For example, although the foaming technologies have shown a significant energy saving, some studies have reported that they have inferior moisture sensitivity performance that can lead to earlier rehabilitation and/or reconstruction due to premature distress formation [
7,
27].
III. Performance
With respect to service, maintenance, and end-of-life phases weak performance might diminish the environmental and economic benefits of WMA technologies in production and construction phases. Based on the literature, the performance of WMA mixtures has been studied in three levels: laboratory, short-term, and long-term field evaluations (see ). Additionally, other studies have focused simultaneously on both laboratory and field evaluations as well as mix design and best practices of WMA mixtures [
8,
30,
32,
33,
34]. Moisture susceptibility, rutting, fatigue, and thermal cracking resistance are the main aspects of performance that have been evaluated for WMA mixtures. Moisture susceptibility is the main cause of premature distress formation. Incomplete drying of aggregate due to lower mixing temperature weakens the moisture damage resistance of the WMA [
9]. However, some anti-striping agents, such as Zycotherm and polyamines, can act as WMA additives to solve the problem with moisture susceptibility [
12]. From some trial projects in Europe, the results of the moisture susceptibility for WMA mixtures with different additives and virgin binders indicated that the WMA mixtures could show equal, or even better, adhesion compared to the HMA control mixtures [
6]. Moreover, a study at the University of California, Davis reported no moisture damage for the saturated pavement sections tested under a heavy vehicle simulator (HVS) [
32]. Another study (NCHRP report 779) on the short-term performance of WMA pavements with less than 10 years old revealed that none of the field projects showed any sign of moisture damage [
7]. In this study, cores were taken from the projects after 1–2 years of traffic. Furthermore, as a part of NCHRP Project 9–49, a recent web-survey from state DOTs and contractors in the US was accomplished to recognize WMA pavement moisture susceptibility based on the mix design, construction, production, or quality assurance (QA) data [
8]. Results of this survey from the WMA pavements with ages of 3–8 years (short-term) revealed that no moisture-related distress had been observed for 90% of the states. However, it is important to note that the low percentage (10%) of moisture-related distress in this survey does not necessarily guarantee the long-term moisture damage resistance of the WMA pavements. Based on NCHRP report 83, results of the Hamburg wheel tracking (HWT) demonstrated that most of the WMA mixtures without an anti-stripping agent showed stripping inflection points (SIP) [
16]. Therefore, application of anti-stripping agents can significantly reduce the stripping potential of WMA mixtures in a long-term period.
Table 5. Some studies at three different performance evaluations.
Evaluation Type |
References |
Laboratory |
[8,35,36,37,38,39,40,41,42] |
Short-term |
[7,43,44,45,46] |
Long-term |
[6,16] |
Rutting performance of WMA mixtures have been evaluated under heavy loading conditions in some accelerated pavement testing (APT) facilities in the United States: the National Center for Asphalt Technology (NCAT) Test Track, the University of California Pavement Research Center (UCPRC), and MnROAD [
7,
32,
47]. Results of these studies confirmed that rutting performance (structural response) of the WMA test sections were comparable to the companion HMA sections. Additionally, results of a survey in Europe demonstrated that the rutting performance of the variety of WMA technologies was equal or even better compared to corresponding HMA mixtures [
6]. As one of significant findings from NCHRP report 779, the short-term field evaluation of rutting performance for 28 WMA projects revealed that the rutting performance of WMA pavements was comparable with that of the companion HMA pavement [
7]. In this study, the companion HMA pavements were defined as those were like WMA pavements regarding pavement structure, climate, and traffic conditions. In another study, NCHRP Project 9-49A, investigation of the long-term rutting performance for WMA mixtures showed that most of the WMA and companion HMA pavement sections have comparable rutting [
16]. Additionally, among of different WMA technologies (foaming, organic, and chemical additives), no statistical difference regarding rutting was observed. Most of the non-foaming WMA technologies had a positive effect on high-temperature rheological properties of asphalt binder [
40].
In case of fatigue resistance, results of two laboratory studies showed that although the chemical additives and foamed mixtures have a lower fatigue resistance compared to conventional HMA [
48], Sasobit as a wax additive can improve fatigue performance especially when the modified asphalt mixtures are compacted at lower temperature (100–115 °C) [
49,
50]. Additionally, the laboratory evaluation of fatigue life for foamed WMA mixtures using four-point beam fatigue tests exhibited higher fatigue life compared to HMA mixtures [
51]. Among different WMA technologies, results of laboratory studies have shown that chemical additives are more contributive on thermal cracking mainly due to the reduced stiffness while foamed and warm wax asphalt have a minor negative impact on it [
52,
53]. In terms of large-scale tests, evaluation of fatigue performance of WMA pavements using a heavy vehicle simulator (HVS) showed insignificant fatigue cracking for all test sections due to strong pavement structure [
32]. Furthermore, in Florida State, an early field study (three years after construction) conducted by Sholar et al. [
54] revealed that there was no statistically significant difference between fatigue performance of WMA and the companion HMA pavement sections. The laboratory and field evaluation of fatigue cracking in some projects across the Europe countries also exhibited that the fatigue performance of WMA mixtures was equal, or in some cases better, than the companion HMA mixtures [
6].
In terms of transverse and longitudinal cracking, the analysis of long-term performance indicated that although the various WMA technologies had a comparable performance compared to the companion HMA pavements, among those technologies, the foaming and chemical WMA pavements showed better performance compared to the organically-modified WMA pavements due to a more noticeable effect of aging on organically-modified WMA pavements [
16].
A summary of the recommended determinants and corresponding test methods and specifications for better evaluation of performance and engineering properties of WMA mixtures is shown in . Generally, as a result of the limited studies around the long-term performance of WMA mixtures, it seems that still many transportation agencies and pavement construction contractors are hesitant to employ these technologies due to the initial costs. However, the current WMA technologies are more environmental-friendly than conventional HMA, and they show a comparable performance with HMAs. For example, using life cycle assessment (LCA) to address both environmental and performance aspects of pavements, it is reported that the WMA mixtures are more environmentally friendly and economically competitive to conventional HMA [
55,
56,
57].
Table 6. Recommended determinants for performance evaluation of WMA mixtures (after [
7,
16]).
Performance |
Determinant Parameter |
Specification/Reference |
Moisture Susceptibility |
Tensile strength ratio (TSR) |
AASHTO T 283 |
Rutting |
Rutting resistance index (RRI) |
Hamburg wheel tracking (HWT), AASHTO T 324 |
Dynamic modulus (E*) at 30 °C |
AASHTO TP 79 |
Creep compliance at 30 °C |
AASHTO T 322 |
Binder Performance Grade (PG) |
AASHTO T 315 |
Multiple Stress Creep Recovery parameter (Jnr) |
AASHTO TP70 and AASHTO MP19 |
transverse cracking |
Fracture work density value at −10 °C |
Indirect tensile (IDT), AASHTO T 322 |
Dynamic modulus (E*) at −10 °C |
AASHTO TP 79 |
Indirect tensile strength at 20 °C |
ASTM D6931 |
Creep compliance at 0 °C |
AASHTO T 322 |
Vertical failure deformation at 20 °C |
[58] |
Longitudinal cracking. |
Indirect tensile strength |
IDT test at 20 °C |
Vertical failure deformation at 20 °C |
[58] |
Horizontal failure strain from the IDT test at 20 °C |
[58] |
Creep compliance at −10 °C |
AASHTO T 322 |
2.2. Waste Materials and By-Products
Recycled Aggregate
The asphalt pavement production and construction need a substantial amount of energy and non-renewable materials. Therefore, use of recycled materials seems to be necessary to create a more sustainable future for asphalt concrete pavement construction. The well-known recycled aggregates that have been used in asphalt pavements can be categorized into three groups [
59]:
-
Existing pavement byproduct such as reclaimed asphalt pavement (RAP) and reclaimed asphalt shingles (RAS) materials;
-
Construction and demolition (C and D) waste materials such as tiles and bricks; and
-
The byproduct from industry, such as copper or steel slags.
Using all these recycled aggregates are environmentally beneficial as it deals with solid waste management. Nonetheless, they can have both positive and negative impacts on asphalt performance; the negative impacts are intensified with recycled aggregate (RA) percentage increase and most agencies and DOTs impose a threshold dosage. For more preservation of natural resource, researchers have been seeking solutions to increase the amount of RA that can substitute virgin aggregates with insignificant negative impacts on performance. The first group materials (RAP and RAS) are evaluated in this section, and the other two groups are investigated in
Section 3.
Reclaimed Asphalt Pavement (RAP)
On a mass basis, around 95% of asphalt mixture is composed of aggregates and the rest 5 percent is asphalt binder. An irreversible oxidation reaction occurs between asphalt and air since the first day of the pavement service. As the oxidation continues, a fading of asphalt’s flexibility, adhesive capability (bonding between asphalt and aggregate) and cohesive capability (bonding inside asphalt) damage the performance of asphalt concrete. Although this process is irreversible, the materials in a heavily aged pavement are not worthless. Recycling HMA is known as reclaimed asphalt pavement (RAP).
The idea of reusing RAP material in asphalt mixtures back to the 1973 oil crisis [
60,
61]. As the asphalt prices started falling in the early 1980s, most asphalt producers returned conservative, only applying low RAP content of less than 20%. Toward the beginning of the 1990s, the amount of RAP recycled was severely reduced. The whole industry was waiting for new technologies, which could increase the RAP content and decrease pavement cost, more importantly, without compromising asphalt concrete performance. The early 2000s saw the price rise of pavement materials increase and this trend also increased the interest in the use of RAP [
62].
Although the amount of available, and the use of, RAP materials is a function of construction activities at all levels, the National Asphalt Pavement Association (NAPA) reported that usage of RAP in asphalt mixtures reached 76.9 million tons in 2016 in the United States, which shows a 3.6% and 37% increase in using of RAP in 2015 and 2009, respectively [
1] (). Additionally, in Europe, reusing RAP in asphalt mixture production started more than 40 years ago, and currently it has an increasing trend in many European countries. shows the percentage of total available RAP materials that have been used in the production of HMA, WMA, HWMA, and cold recycling for some European countries from 2007–2017 [
63]. Additionally, based on the average value of total used RAP for each year, the trend of using RAP in the production of different types of asphalt mixtures is upward, but has a low slope (see ). However, some obstructions limit the use of RAP material to make high-quality asphalt mixtures with most environmental and economic benefits [
64]:
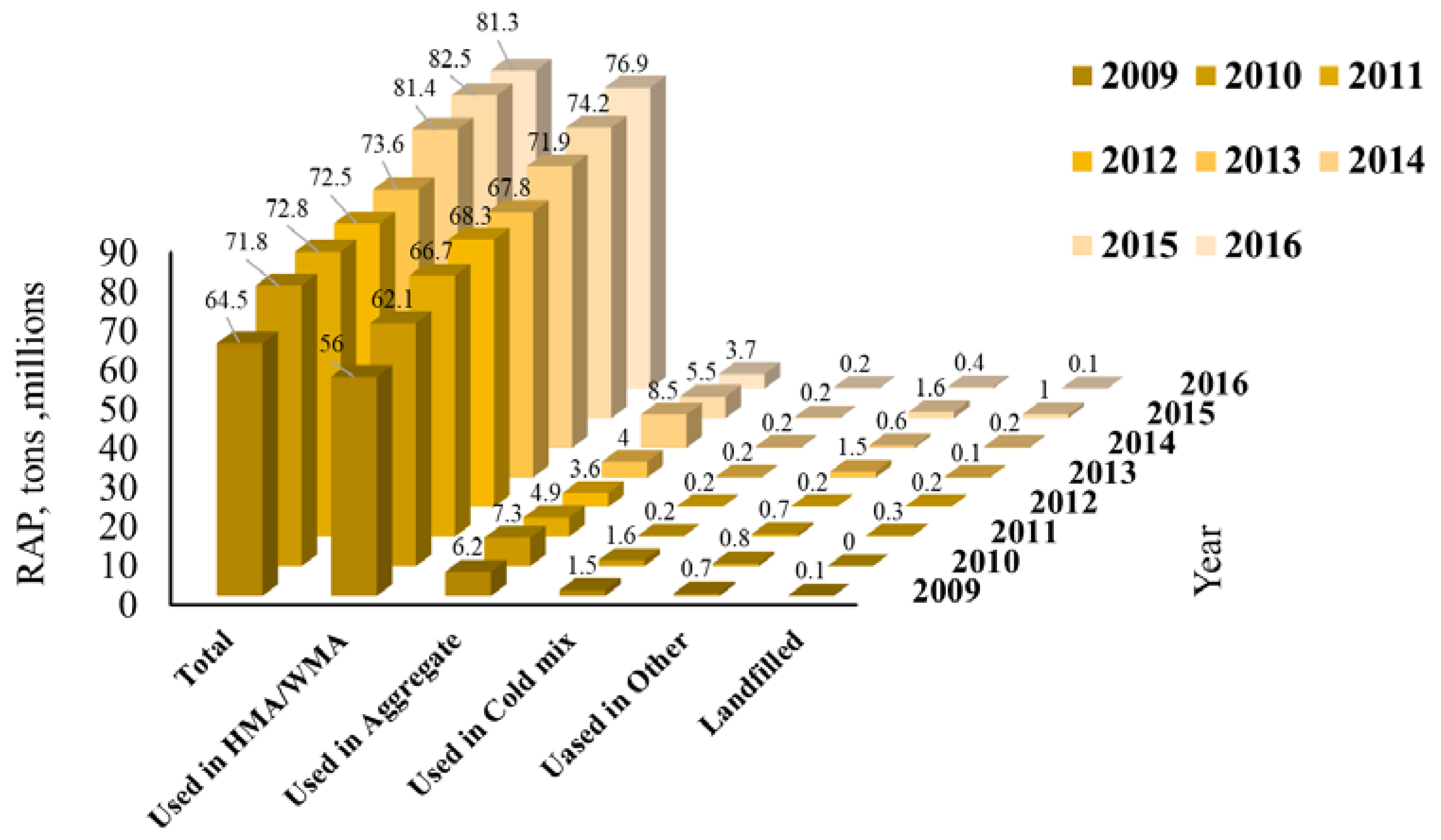
Figure 3. Summary of RAP usage data in the U.S during 2009–2016 [
1].
Figure 4. Change in average of using RAP in production of asphalt mixtures in Europe from 2007–2017.
Table 7. Total percentage of RAP used to hot and warm recycling for European countries during 2007–2017.
Country |
% of Available RAP Used in Asphalt Mixture |
2017 |
2016 |
2015 |
2014 |
2013 |
2012 |
2011 |
2010 |
2009 |
2008 |
2007 |
Austria |
60 |
40 |
45 |
- |
98 |
98 |
95 |
88 |
90 |
- |
25 |
Belgium |
95 |
81 |
64 |
72 |
61 |
61 |
65 |
57 |
57 |
55 |
50 |
Czech Republic |
34 |
47 |
52 |
46 |
43 |
52 |
49 |
50 |
50 |
55 |
85 |
Denmark |
67 |
65 |
100 |
54 |
83 |
77 |
80 |
56 |
55 |
59 |
57 |
France |
70 |
70 |
90 |
64 |
64 |
62 |
45 |
40 |
41 |
25 |
15 |
Germany |
85 |
87 |
28 |
90 |
90 |
87 |
84 |
82 |
82 |
82 |
82 |
Hungary |
95 |
90 |
100 |
90 |
90 |
100 |
100 |
27 |
66 |
44 |
- |
Italy |
23 |
50 |
50 |
20 |
20 |
20 |
20 |
20 |
20 |
20 |
20 |
Netherlands |
82 |
82 |
80 |
85 |
76 |
95 |
98 |
75 |
74 |
83.5 |
90 |
Norway |
31 |
37 |
38 |
23 |
26 |
21 |
18 |
40 |
24 |
21 |
34 |
Slovakia |
98 |
98 |
99 |
99 |
95 |
95 |
94 |
93 |
- |
- |
- |
Slovenia |
39 |
43 |
100 |
25 |
46 |
50 |
50 |
50 |
100 |
100 |
60 |
Spain |
83 |
68 |
96 |
100 |
93 |
77 |
83 |
81 |
66 |
70 |
60 |
Sweden |
- |
93 |
95 |
90 |
90 |
85 |
80 |
80 |
95 |
95 |
95 |
Turkey |
15 |
4 |
2 |
6 |
4 |
7 |
23 |
19 |
3 |
2 |
- |
Average |
64 |
64 |
69 |
62 |
65 |
66 |
66 |
57 |
59 |
55 |
56 |
-
High variability in RAP due to different RAP sources;
-
Demolition and milling processes; and
-
Aged asphalt binder of RAP.
Moreover, according to a state asphalt pavement associations (SAPA) survey, specification limits (38.5%), RAP availability (18.5%), asphalt plant capabilities (15.4%), volumetric requirements (13.8%), and mixture performance (6.2%) were the top five factors that limit the use of RAP in the U.S [
65]).
I. Environmental Evaluation
Before production, preparation of raw materials including aggregate and asphalt binder also demands energy that should be looked into when conventional virgin aggregate and/or asphalt binder are replaced by other materials. Generally, the following factors have significant effects on the environmental impact of asphalt mixture production using RAP: moisture content, HMA discharge temperature, RAP content, transport process, and quality of RAP [
66,
67,
68,
69,
70,
71].
Currently, there are two approaches to add RAP to virgin materials for asphalt mixture production. In the first approach, RAP is added cold to the overheated virgin materials in the drum mixer. Although as an advantage, this approach can be easily implemented in an asphalt plant, it needs a higher temperature for virgin materials and a longer mixing time especially at a high percentage of RAP. On the other hand, the second approach is adding preheating RAP materials to the asphalt mixture. The preheating process can be usually done using a parallel drum and, therefore, it increases the cost of production because using a parallel drum requires high investment for modification of plant. Compared to the virgin aggregates, RAP materials have higher moisture content because milling of the old pavements needs water [
69,
70,
72].
Therefore, using this approach, the better control of RAP moisture content can be achieved. A study reported an increase in energy consumption up to 14% and 17% could be observed when 15–30% and more than 45% RAP, respectively, were used in new asphalt mixtures [
73]. However, the other studies stated that producing asphalt binder consumes 3,110,090 MJ of energy and releases of 226,870 kg of GHG and replacing 50% of RAP as binder replacement can result in 17–28% reduction of energy consumption as well as emissions [
74,
75].
Using 10–20% RAP in the HMA mixtures, Giani et al. [
71] indicated that there was 6.8% and 6.4% reduction for greenhouse gasses (ton CO2
eq) and the single score endpoint impact, respectively, for a 15 years lifespan analysis. Furthermore, 40% reduction in emission of the CO2
e was reported when 75% RAP was in a production of HMA mixtures. The comparison between GHG emissions for virgin and 20% RAP mixtures () revealed that adding RAP can result in averagely 8.3% reduction in air pollutant parameters such as carbon monoxide (CO), oxides of sulfur (SOx), oxides of nitrogen (NOx), volatile organic compound (VOC), and particulate matter (PM) [
75].
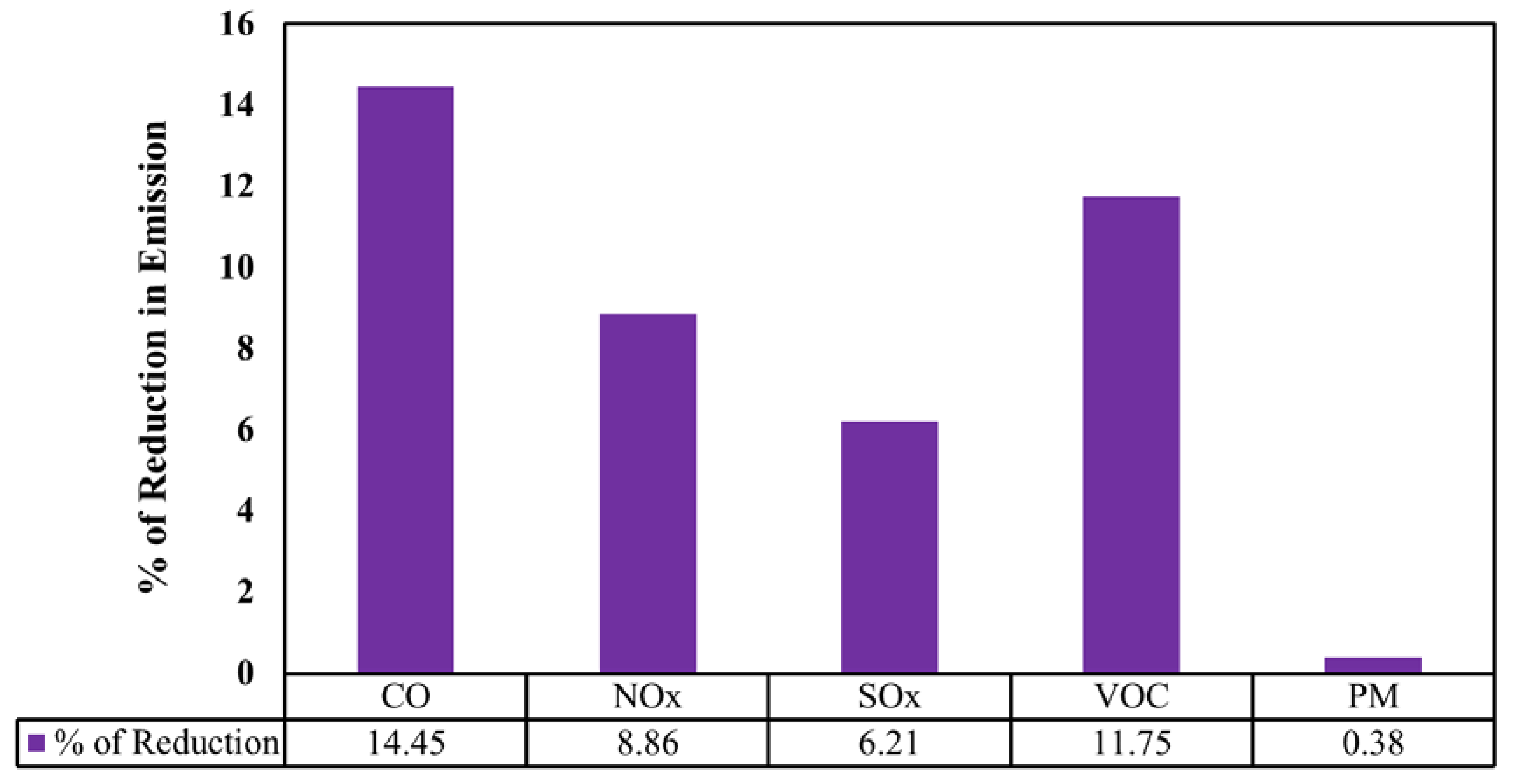
Figure 5. Percentage of reduction in the emission of air pollutants for using 20% RAP.
Adding up the energy and emissions due to plant production, transportation, and construction, which are equal for conventional mixtures and those containing RAP, as well as road maintenance, and illustrate the total energy consumptions and emissions per km per lane for different RAP percentage. In , Carbon dioxide equivalent (CO
2eq) is a global warming potential (GWP) unit to measure the environmental impact of one ton of different other greenhouse gases compared to the impact of one ton of CO
2. It can be observed that there is a reduction in both energy consumptions and emissions with RAP content increase. Based on the midpoint (climate change and fossil depletion) and endpoint (human health, ecosystem diversity, resource availability) environmental impacts, results of a study revealed that adding 15% RAP to HMA or WMA mixtures could result in 13–14% reduction on the most of midpoint and endpoint impacts [
70]. Moreover, a decreasing trend of environmental impacts (midpoint, endpoint, and cumulative energy demand) was observed as the rate of using RAP increased [
66].
Figure 6. Energy consumption for different RAP content [
75].
Figure 7. GHG emissions for different RAP content [
75].