Vehicles have become more fuel efficient, and hybrid electric vehicles are becoming more common. One of the fastest growing alternative energies in vehicles is electricity. As with conventional energy sources such as petroleum and coal, electricity is not a primary energy source. A fully charged battery is an energy carrier. Battery electric vehicles (BEVs) are highly efficient at converting energy from the grid into tractive force, and they can recover energy during drives by utilizing regenerative braking. One major drawback of BEVs is that they usually have a limited range due to the size and the cost of batteries necessary for vehicle power and energy requirements. The “refueling” of the battery systems can also take several hours, rather than a few minutes with a conventional vehicle (CV). To use advantages of both electric and conventional vehicles and to bridge the gap between CVs and BEVs, an alternative is considered. Hydrogen is a chemical energy carrier that has the capability to produce electricity up to 39.39 kWh/kg, which surpasses the energy density of most batteries. A fuel cell (FC) has a direct analogy to an internal combustion engine (ICE). An ICE converts chemical energy stored in the fuel supplied to the engine to produce rotational mechanical energy [6]. The rotational energy produced is then either used to propel a vehicle or focused through a generator and converted into electrical energy. An FC acts much in the same way as an ICE in that chemical energy is directly converted into electrical energy in the FC, but in an environmentally friendly process [7,8,9,10,11,12]. Unlike a battery that drains while it is used to power electrical components, internal combustion engines and fuel cells act as continually operational power sources as long as fuel is being provided to them [13]. Hence, it is projected that the hydrogen fuel cell can overcome the disadvantages of BEVs, making hydrogen the transportation fuel of the future.
Hydrogen storage is the one of the most important research issues in the development of FCVs. Hydrogen storage systems are under development to introduce new methods to meet the needs of customers. Due to hydrogen’s low energy-density, it is difficult to store enough on-board a vehicle to obtain adequate driving-range without the storage container being too large or too heavy. shows a hydrogen FCV with on-board storage of compressed gas [29]. Hydrogen storage techniques and the required research in this area are summarized in the following points.
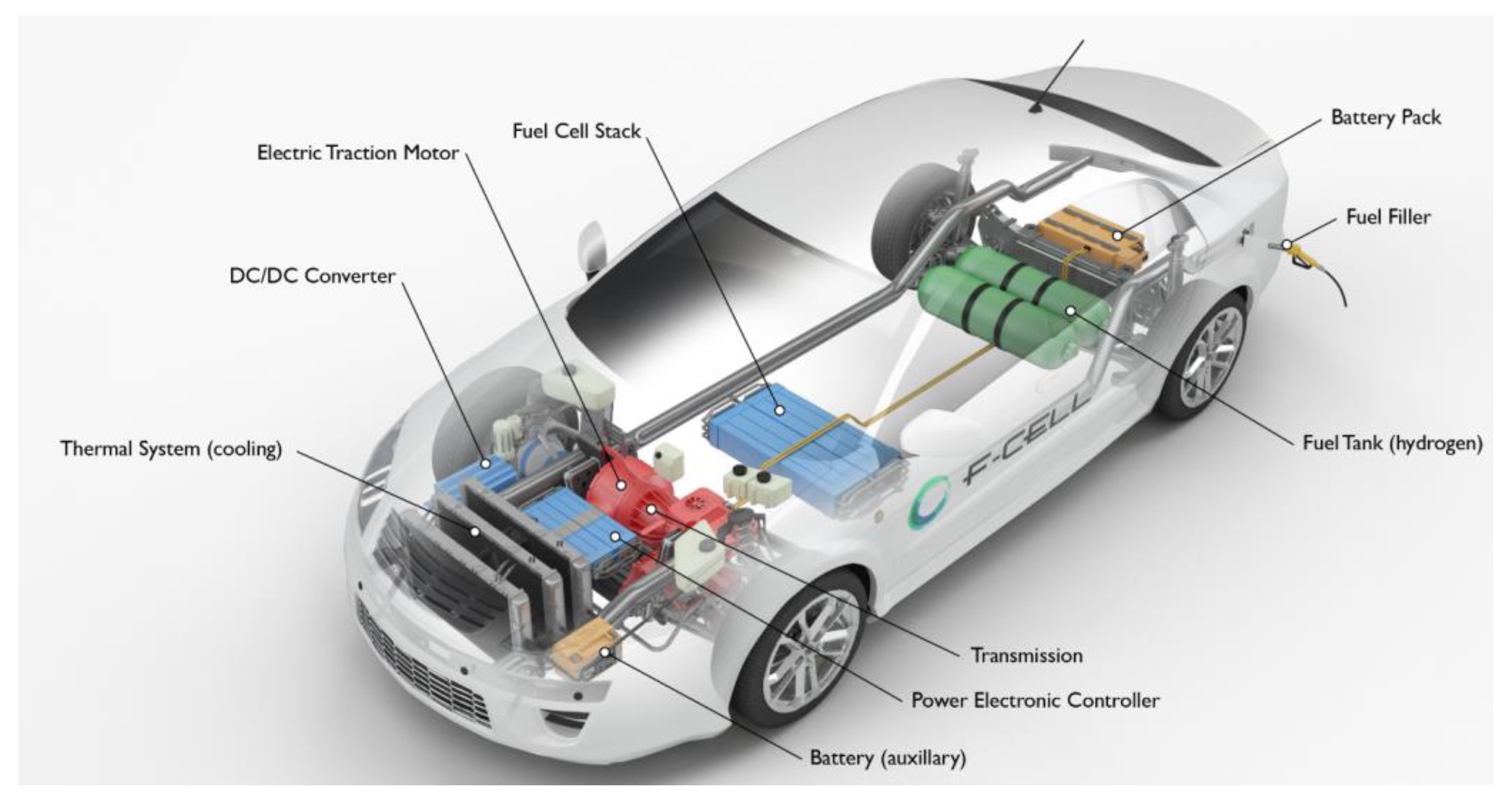
Figure 1. Fuel cell vehicle with on-board storage [
29].
The development of one important aspect of the fuel cell vehicle—the electric motor—dates back to the early 19th century. Although electric vehicles were a strong contender in the early 20th century to become a mainstream transportation method, the ICE vehicle eventually won out due to the short range and the high cost of electric vehicles. Additionally, the discovery of Texan oil reduced the price of gasoline, thus it became affordable to the average consumer, which caused fuel cell and electric vehicles to take a backseat to the ICE vehicle for most of the last 100 years [
47]. The oil embargo in 1973 kick-started a renewed interest in FC power for personal transportation applications, as governments looked to mitigate their dependence on petroleum imports. In the early 1970s, K. Kordesch [
52] modified a sedan to operate from a 6-kW FC and a lead acid battery pack. The automobile was driven on public roads for about three years. In 1993, Ballard launched a fuel cell-powered light-duty transit bus using a 120-kW FC system, followed by a heavy-duty transit bus using a 200-kW FC system in 1995. In 1994 and 1995, H-Power built three fuel cell-battery hybrid buses, each using a 50-kW FC and a 100-kW nickel-cadmium battery [
53]. The importance of these releases was to make FC technology understandable to key decision makers in industry and government. These buses helped to prove that fuel cells would work in the real world. Fleet-vehicle operations, such as buses and delivery services, were early adopters of fuel cell technology due to the ease of centralized refueling and the reduced requirement for a high range capability between fill-ups. Trials of FC powered buses have occurred in Vancouver and Chicago, as well as in other cities in Europe and North America [
54]. In July 2005, the first FC vehicle was leased to a family in California as an important step in getting more fuel cell vehicles on the road. However, many obstacles remain to be overcome before the FC vehicle can become a mainstream form of transportation. An obvious issue is the need for a hydrogen infrastructure to enable refueling of the vehicles. Hydrogen filling stations currently exist in many countries around the world, such as Canada, the USA, Iceland, Japan, Singapore, and Germany. Though these stations are currently not widespread enough to allow large numbers of people to begin driving FCVs, it is expected that more hydrogen infrastructure will be built as more FCVs become commercially available. Hydrogen FCVs have evolved significantly; currently, they can drive between 311 to 597 miles on a full tank. The development of these vehicles is increasing, but they still require significant improvements [
14].
It should be noted that FCEVs are more promising in city bus applications due to two reasons—the supply of hydrogen is not crucial, because the buses refuel in one place, hence only one refilling point is required, and the price of FCs. FCs are still expensive, therefore it makes more sense to buy them for vehicles that are in use for many hours each day [
55]. As of June 2018, there have been more than 6500 FCVs delivered to consumers. California was the leading market for FCVs, with nearly 3000 vehicles being delivered due to it having the largest network of hydrogen refueling stations (HRS) [
56]. In Europe, Germany’s Linde AG and France’s Air Liquide have been working together to increase Germany’s stations from 15 to 100 by 2017 and to 400 by 2023. About 1000 HRS would be required to provide full coverage in countries such as Germany or France, with a cost of 1.5 to 2 billion euro [
57,
58].
FCV sales volumes are projected to be significant, but only in the long term, even with a favorable climate-policy scenario. shows FCV sales volume anticipations based on a long-term powertrain mix scenario (million annual units) [
59]. Considering a similar scenario, the international energy agency (IEA) anticipates an FCV market share of about 17% by 2050 (35 million annual unit sales) [
60].
Figure 2. Fuel cell vehicle (FCV) sales volume. Source: IEA. All rights reserved. [
59].
Another option to increase the HRS prevalence is to use electrolysis at refueling stations to convert electricity from the grid into hydrogen. This idea could be extended to residential applications, where people would have a hydrogen refueling station in their own homes [
61,
62,
63]. The obstacles associated with developing an adequate hydrogen infrastructure brings up another important question—where will the hydrogen come from? Although hydrogen is the most abundant element in the universe, it rarely exists alone in nature. Today, hydrogen is mostly produced by reforming natural gas. In this way, pollutants can be captured if the reforming is done at a central plant. However, other options, such as direct solar hydrogen from methane at landfills and hydrogen from bacteria [
64], are continually being explored. If electrolysis is used to generate hydrogen, there may have to be an increase in electricity generation to satisfy the need for hydrogen, though the increase may be small, since hydrogen can be produced during off-peak times (e.g., overnight). Methods to generate electricity that have a minimal impact on the environment include nuclear, wind, solar, hydro, and geothermal. It is often said that, at the beginning of the hydrogen economy, most of the hydrogen will still be reformed from natural gas, but as time goes by, society will move towards more ideal sources of energy, such as wind and solar [
65]. Although generation and transportation of hydrogen is a major issue in the deployment of fuel cell vehicles, many diverse ideas are being developed to solve the problem. Other obstacles for fuel cell vehicles include improving on-board hydrogen storage, improving fuel cell and battery durability, and increasing the efficiency and the performance of a fuel cell vehicle. The last barrier to commercialization is cost—a true challenge—as fuel cells are still extremely expensive today. Many parts used to work with fuel cells (e.g., power electronic converters) must be custom-made and can be very expensive as a result [
66]. However, these costs will decrease as technological processes are improved and components are mass-produced.
Parallel Hybrid
One of the earlier hybrid drive train designs was the parallel hybrid architecture. In this configuration, both the internal combustion engine and the electric motor can be used to power the vehicle independent of one another. The ICE has a low torque output at low speeds, therefore in stop-and-go drive cycles, the ICE is extremely inefficient. However, electric motors provide almost instantaneous torque, making them ideal for stop-and-go drive cycles. Implementing a parallel hybrid system allows each power source or both to operate at varying degrees when it is most efficient in the drive cycle [
35]. For example, during low speeds and stop-and-go cycles, the electric motor would primarily be used, and the internal combustion engine would be mostly off for efficiency reasons. Conversely, during steady-state highway conditions, the electric motor would be off, while the ICE would power the vehicle to induce a long driving range by utilizing the high energy density of the fuel [
65]. In the parallel configuration, one can also operate both the ICE and the electric motor together when the torque demand is greater than the torque produced by either the ICE or the electric motor independently [
66]. Since both power sources can be operated in unison when torque demands are high, it allows both the engine and the motor to be scaled down in size, since most of the time the drive cycle will not have a high torque demand. Reducing the size of both motors can further increase the overall efficiency of the parallel design. Another advantage to the parallel hybrid drive train architecture is the ability to harvest energy through deceleration in the drive cycle with the implementation of regenerative braking. Regenerative braking is not exclusive to parallel hybrid architecture, rather, almost all hybrids can deploy regenerative braking to harvest what would otherwise be wasted heat energy from the mechanical brakes [
67]. Regenerative braking works by converting the electric motor into a generator during stops and decelerations in the drive cycle; this energy then gets stored in the batteries of the vehicle to be used later in the drive cycle [
68]. A visual representation of a parallel hybrid drive train is depicted below in [
69].
Figure 3. Parallel hybrid configuration [
69].
Series Hybrid
A series hybrid drive train architecture differs from a parallel hybrid drive train in that the two power sources are no longer independently able to power the vehicle. In this configuration, generally the ICE will act as a charger for the batteries that supply electricity to the electric motor—the only source to propel the vehicle [
70]. One of the advantages of this design is that there is no need for a transmission, since the ICE is not powering the vehicle directly. Eliminating the transmission from the engine system reduces the weight of the vehicle, which directly correlates to increased efficiency. In a series configuration, the ICE does not have to account for any of the transient dynamics in the drive cycle as it would in a parallel configuration. Because of this, the engine can be operated at a steady state at its most efficient rpm, further increasing its efficiency. In a series configuration, there is more flexibility regarding the implementation of alternative energy devices. For example, for this project, the ICE was replaced with a hydrogen FC. In a series hybrid, the ICE converts chemical energy to mechanical energy and then to electrical energy, thus it is actually more efficient to use an FC to convert directly from chemical energy to electrical energy to charge the battery pack. This is one of the main reasons the decision was made to implement a series configuration in this project. It should be noted that a fuel cell can be used in a parallel configuration as well. However, to achieve parallel use, the fuel cell would need to be robust enough to handle the transient dynamics created by the drive cycle. Most fuel cells have high enough power density to handle transient dynamic loading well. Usually, fuel cells are required to operate near steady-state conditions, which makes them ideal for series hybrid architectures [
71,
72,
73,
74,
75]. An example of a series hybrid configuration with an ICE is depicted below in .
The series hybrid design can also support regenerative braking to recover energy during stops and decelerations the same way the parallel hybrid does by converting the motor into a generator during these instances in the drive cycle. A drawback to the series hybrid design is that the motor is required to be larger, since there is no way to use both power sources during a hard acceleration.