1. Introduction
Polymers are often reinforced with fillers to improve their thermomechanical properties. Especially when the fillers are derived from natural resources, they help to achieve optimal properties such as biodegradability and biocompatibility. In addition, increasing urbanisation has led to a huge increase in agricultural, industrial and household waste. The synthesis of bio-based fillers from these resources at the nanoscale enables the hybridisation of bio-based fillers with synthetic and natural polymers
[1][2]. Many natural plant fillers are extracted from agricultural by-products and consist of a mixture of different biopolymers such as cellulose, lignin and hemicellulose, which are components of plant parts (e.g., leaves, seeds, fruits, grasses)
[1]. Biofibres are generally considered organic and sustainable due to their versatility, eco-friendly design, low cost, renewability and local supply compared to synthetic fibres
[3]. As in nature, these fibres are hollow and have very good thermal and acoustic insulation properties. The mechanical properties of biofibres are generally lower than those of synthetic fibres, but careful surface preparation can improve these properties
[1][3]. However, the main disadvantages of biofibres are their hygroscopicity and incompatibility with the hydrophobic matrix
[1][4][5].
Researchers involved in the development of a natural fibre for FDM are listed in
Table 1 [6]. Typical natural fibres used for biocomposite production are oil palm, banana, kenaf, walnut shell, rice, rice straw, wood, Hedysarum, agave, sugarcane, astragalus, bamboo, almond hull powder, etc. The inclusion of processing makes the print accurate.
Table 1. Summary of biomass materials used for 3D printing.
Biomass polysaccharides are macromolecules composed of repeating sugar units linked by glycosidic bonds to form a crystalline and amorphous material. They are abundant in nature and many have a complex structure consisting of numerous intramolecular and intermolecular hydrogen bonds. The most representative components of this class are cellulose, hemicellulose, lignin, chitosan, starch and alginate
[63]. Polysaccharides have been used as reinforcing agents in the form of pure fibres (e.g., cellulose, lignin or hemicellulose) or as mixtures extracted from plants (e.g., flax, bamboo, hemp) of which they are the main constituents. Other sources of polysaccharides are process waste from plant matrices, such as coffee. Proteins
[64] are complex macromolecules made up of amino acids linked by peptide bonds. They are abundant in nature and have beneficial properties such as biodegradability and biocompatibility. However, they are mainly used in the 3D process to build soft materials such as hydrogels or scaffolds for tissue engineering. Proteins used for 3D printing include gelatin, keratin, collagen, silk and soy proteins
[65].
2. FDM 3D Printing with Natural Fibers
The most common of the various 3D printing techniques is FDM, and its success depends on the availability of materials that can be processed with it
[66]. Different types of fibres are available, including biological (natural) fibres.
Natural fibres are a very popular choice due to their low cost, abundant availability, high strength-to-weight ratio and high aspect ratio and modulus of good strength and elasticity. These properties make biocomposite filaments a good substitute for synthetic fibres
[5]. The general process for obtaining biocomposite polymer parts from FDM is shown in
Figure 1. They can also be obtained from mixed biomass and petroleum sources. Commonly used biopolymers are PHA, PEG, PCL and PLA
[6].
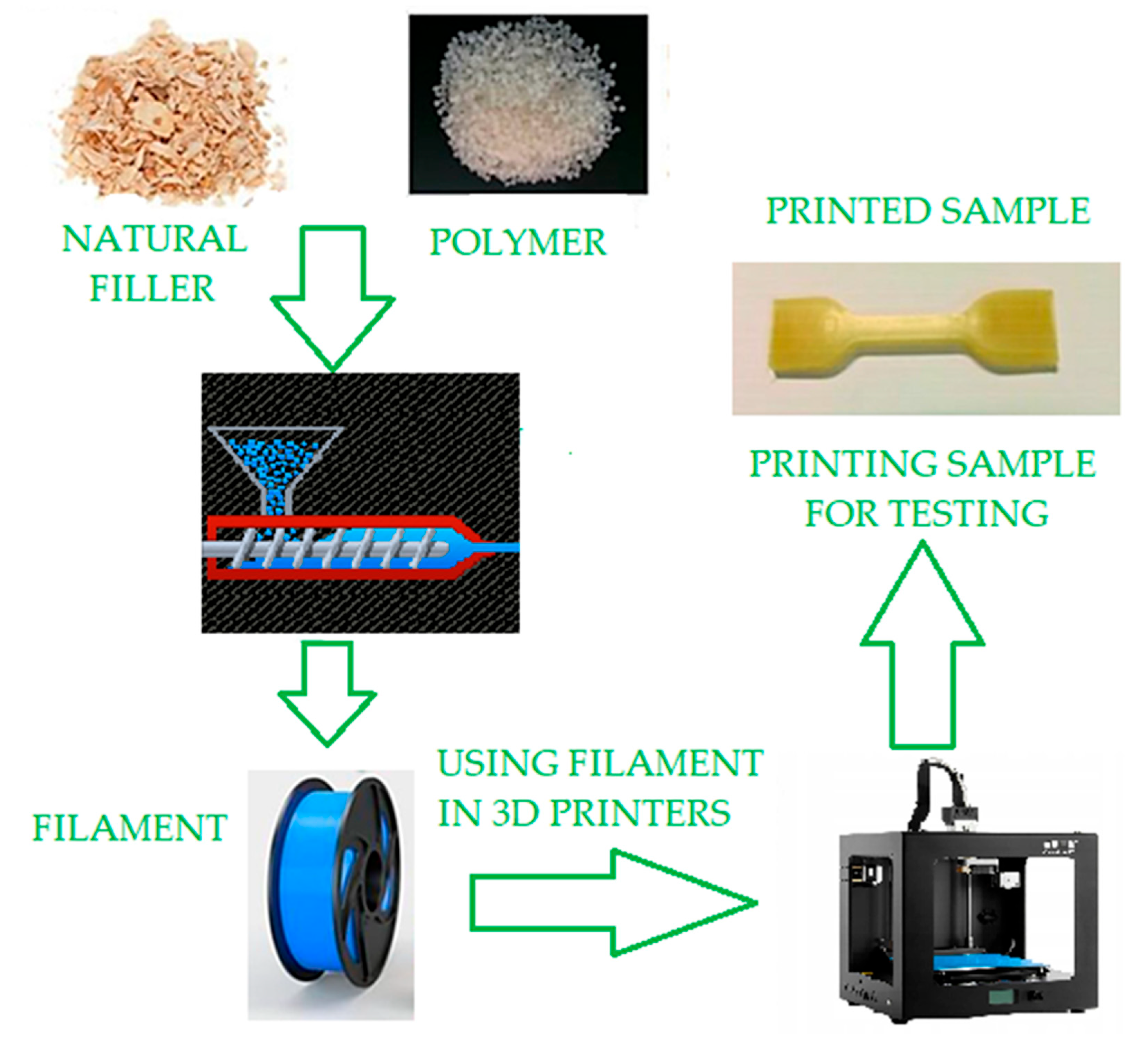
PLA is one of the most widely used biodegradable plastics for FDM. Synthesised from agricultural resources such as corn and tapioca, PLA is biocompatible, compostable, recyclable, gas permeable and degradable by hydrolysis and enzymatic action. PLA is well suited to FDM printing due to its low melting point, low coefficient of thermal expansion and lack of odour during processing. However, it is significantly more expensive per unit than petroleum-based plastics such as polyethylene and polypropylene. It also has a longer degradation time. Therefore, there is an urgent need to reduce the cost of PLA and improve its degradability
[67]. Biofibre reinforced PLA composites have received much attention in recent years. By mixing a biodegradable matrix with a biofibre reinforcement, it is practically possible to produce a biocomposite, a fully biodegradable material
[6]. Work on biofibre-based PLA composites has shown some advantages such as high processability, high specific elasticity, compostability, high durability, renewability and recyclability
[6][67].
According to Hu and Lim et al., the mechanical properties of the harakke composite were superior to those of conventional PLA
[68][69]. Harakeke was added to PLA at 30, 40 and 50 wt%, and the results indicated that the 40 wt% composite had the highest mechanical properties. Le Duigou et al.
[68][70] experimented with a PLA/continuous fax fibre (CFF) composite. PLA/jute fibre and PLA/fax fibre composites were investigated by Hinchclife et al.
[68][71]. The size of the jute fibre composite was 2 mm and that of the fax fibre was 0.5 mm. The results showed that the tensile strength increased by 116% and 26%, respectively. The stiffness of the product increased by 12% and 10%, respectively. The effect of different l/d ratios of PLA/bamboo fibre and PLA/flax fibre was investigated by Depuydt et al.
[21][68] and an increase in stiffness was found. Le Duigou et al.
[68][72] investigated and demonstrated the feasibility of printing a hygromesh biocomposite from a PLA/wood fibre composite with a specific bilayer microstructure. The mechanical properties and potential of polypropylene reinforced hemp and harakke were investigated by Milosevic et al.
[13][68]. They reported improvements in tensile strength and Young’s modulus of 50% and 143%, respectively, compared to pure polypropylene. The mechanical properties of thermomechanical pulp (TMP) reinforced with BioPE composite were analysed by Tarrés et al.
[68][73], who reported an improvement in printing quality. Thibaut et al.
[68][74] investigated the mechanical properties and anisotropic shrinkage of carboxymethyl cellulose (CMC) with natural cellulose fibre during drying. The result showed that 30 wt% of the composite had better mechanical properties and lower shrinkage. Several studies have been carried out to improve and analyse the performance of cellulose fibres as textile composites. Cellulose nanofibrils (CNFs) and nanocrystals (CNCs) have been widely used as a modern collection of nanomaterials in 3D printing
[5][63][68]. The incorporation of CNCs into PLA improves mechanical and thermal properties as the cellulose nanoparticles act as nucleating agents for crystallisation. The load is absorbed by the CNC particles, which are oriented in the polymer chains, resulting in improved tensile properties
[5][63]. Cellulose nanocrystals, obtained by acid hydrolysis of plum seed shells, were successfully incorporated into the PLA/PHB matrix through a reactive mixing process, resulting in improved adhesion and subsequent thermal stability and mechanical properties. Nanocellulose was obtained from the microcellulose using ultrasound treatment to break the aligned structure to produce fully biodegradable 3D printed nanocomposites based on biopolyesters such as PLA, poly(3-hydroxybutyrate-co-3-hydroxyhexanoate) (PHBH) and nanocellulose. The inclusion of nanocellulose in the fibre samples improved the thermomechanical properties of the composites
[5][63].
Filaments for 3D printing with improved mechanical strength have been produced from low-density polyethylene reinforced with nanofibrillated cotton (NFC) particles synthesised from cotton material derived from recycled T-shirts
[75]. PLA/lignin biocomposites for 3D printing applications have been developed using lignin synthesised from the cooking liquor of common spruce chips using a soda boiling technique. The PLA/lignin biocomposites prepared in this way showed good printability without agglomeration. Due to the antioxidant effect of lignin, these composites also showed enhanced uptake activity. Carbon nanoparticles synthesised from waste coconut shell powder are incorporated into Bioplast to develop biodegradable fibres for 3D printing
[5]. In addition to the nanofillers mentioned above, several other industrial and plant by-products are used as fillers for polymer composites
[5].
Carbon fibre from coffee beans acts as a thermal insulator
[5]. Ox-SCG and PLA composite filaments can be produced using a single-screw FDM filament extruder. In addition to PLA, Ox-SCG has also been used with other materials. For example, Huang et al. used coffee grounds with a polyethylene matrix, resulting in an overall increase in modulus and thermal properties
[5][76], while Moustafa et al. used coffee grounds with polybutylene adipate catheterephthalate. Hung et al.
[76] prepared the filaments by mixing powdered PLA with Ox-SCG at concentrations of 0, 5, 10, 15 and 20 wt% with a total weight of 100 g per mixture. The mixture was prepared in a standard V-type powder granulation mixer for 4 h. The mixture was then held in a vacuum oven at 40 °C to remove moisture from the mixture. The resulting mixture was fed into the hopper of a single-screw extruder at 165 °C. The composite was extruded to a diameter of 1.75 mm and then coiled. The resulting filament was suitable for 3D printing. Hung et al.
[76] reported that Ox-SCG was uniformly dispersed and distributed in the PLA matrix by mixing and single-screw extrusion. They also reported that increasing the concentration of Ox-SCG in the PLA matrix increased the strength. At 20 wt% Ox-SCG loading, an improvement in impact strength of 418.7% was reported
[5].
Wood and lignocellulosic components can also be used as additives and reinforcements in composites
[68]. The search for fillers such as wood, bamboo, sugarcane, kenaf with PLA and other base materials is ongoing. Ayrilmis et al.
[68][77] investigated PLA with 30 wt% wood using FDM. They investigated the absorption and changes in mechanical properties at different layer thicknesses: 0.05 mm, 0.1 mm, 0.2 mm and 0.3 mm. The results indicate that increasing the layer thickness increases the porosity and decreases the mechanical properties of the sample. PLA/raw sugar cane and PLA/raw sugar cane fibre were investigated at different compositions of 3, 6, 9 and 12 wt% by Liu et al.
[78] and found to have the best properties for industrial scale applications. A study on the preparation of bamboo/PLA composites using FDM was carried out by Zhao
[68][79]. It was found that the addition of bamboo powder to the PLA polymer reduced nozzle clogging and had better biodegradation properties. Daver et al.
[68][80] investigated the morphological, mechanical and thermal properties of PLA filled with cork at different filling percentages. The tensile strength and yield strength of the printed parts were low compared to the compression moulded composites, but the elongation at break was higher. A PLA/wood flour composite was investigated by Tao et al.
[22]. Their results indicate that the addition of 5 wt% wood flour to PLA does not change the melting point of the composite. Vaidya et al.
[68][81] analysed the warpage of the composite in relation to the addition of polyhydroxybutyrate (PHB) fillers and Pinus radiata wood chips. A 20 wt% filler added to PHB changes the melt viscosity and improves warpage from 34 to 78% compared to parts printed from pure PHB. Tran et al.
[82] investigated the thermal and mechanical properties of a polycaprolactone (PCL)/cocoa husk composite. Varying the composition of cocoa husks added to PCL resulted in a low temperature composite suitable for printing biomedical scaffolds and toys. Frone et al.
[83] investigated the morphostructural and thermomechanical properties of nanocrystalline cellulose added to a polylactic acid (PLA)/polyhydroxybutyrate (PHB) composite and dicumyl peroxide (DCP) as a crosslinking agent. Good adhesion and thermomechanical properties of the sample were reported.
Thermoplastic starch (TPS)
[84], as a cheap, readily available and fully biodegradable and renewable polysaccharide, has found its application as an additive in composites with degraded polymers, i.e., PLA, PBS and PCL. TPS is obtained by subjecting starch to the appropriate moisture, mechanical shear stress and heat. Research
[85] has shown that the resulting material is susceptible to ageing and brittleness. In addition, the mechanical properties and hydrophobicity of TBS are poor compared to traditional materials such as polyethylene or polypropylene. This is due to the large number of hydroxyl groups, which contribute to strong intermolecular interactions
[67]. Various strategies have been developed over the years to improve these properties, including the use of plasticisers, reinforcement with reactive modifiers and chemical modification of starch and blending starch with other polymers
[86]. Combining starch with other polymers in FDM 3D printing has proven to be an effective way to overcome the limitations of thermoplastic starch. According to the available literature, numerous studies have been carried out on the use of TPS as a matrix in FDM printing, and the resulting blends, e.g., TPS/PLA, have proven to be an excellent solution for obtaining new and inexpensive materials with good performance. Other advantages of these composites include renewability, biodegradability, low density and high heat resistance. The only drawback is poor durability, which has become a key element in further research by scientists
[86].
Haryńska
[84] started her research with the preparation of a composite based on thermoplastic starch (TPS) and PLA in the proportion of 60 wt% PLA and 40 wt% TPS. The TPS granules were prepared from potato starch, vegetable glycerine and ESO soybean oil in the following proportions 65.7% starch, 33.3% glycerine and 1% ESO. The resulting material was used for FDM 3D printing and then its mechanical properties were tested (
Figure 2).
Figure 2. Block diagram showing the steps of PLA/TPS 3D printing. Developed based on
[84].
Ultimately, the researchers were able to increase the biodegradability and plasticity of PLA. The improvement in printability was also demonstrated by producing personalised 3D anatomical specimens and prints with complex shapes and high structural porosity. Researchers
[85] produced composites based on mTPS/PLA in a ratio of 75 wt.%. PLA and 25 wt% mTPS using the ESO additive in the preparation of TPS in the amount of 0.5–2%. The results obtained showed that the use of 25% thermoplastic starch increased the impact strength of the composites from 13.70 kJ/m
2 to 16.69 kJ/m
2 and the elongation at break from 2.6% to 8.8% compared to pure PLA. The authors showed that the use of an additive for the production of TPS with ESO, in the obtained composite with the weight composition TPS/PLA (2% ESO) (25 wt.%/75 wt.%), improved the water resistance and increased the impact strength to over 16 kJ/m
2. In addition, the thermal and rheological properties, as well as the biodegradability and compostability (according to the PN-EN 14806:2010 standard
[87]) of the obtained 3D printed samples were determined. In conclusion, it can be clearly stated that the addition of 25% TPS with ESO to the structure of the PLA composite allows not only to reduce the production costs of the obtained material, but also to maintain the mechanical properties at the level of pure PLA and additionally to improve the biodegradability and compostability of the obtained materials.
Qing Ju
[86] prepared three-component blends containing PLA, TPS and PBAT (poly(butylene adipate-co-terephthalate)). In addition, the functional polymer CE (ADR4468) was introduced in different proportions to reduce the brittleness of the obtained composites. The tests were carried out on a composite prepared in the following proportions: 50% TPS, 40% PLA and 10% PBAT. The main component that increases the flexibility of the composites produced is PBAT, which is characterised by high flexibility due to its high molecular weight and branched molecular structure. It also has a density similar to LDPE and is biodegradable. Due to its excellent flexibility, it can be successfully used for rigid two-component TPS/PLA composites. The studies carried out by
[86] also found that the mechanical properties improved with increasing chain extender (CE) content, with the addition of CE increasing the elongation at break of the samples by 113% and the impact strength by 190%. However, the maximum viscosity and strength of the samples from the composite obtained were obtained with 1% w/w CE. Furthermore, the addition of CE not only increased the relative molecular weight of PLA and PBAT, but also increased their degree of branching, thereby improving the matrix strength of the four-component composite. At the same time, the applied CE improved the adhesion and compatibility between the two-component blend of PLA and PBAT, which increased the stress and strain efficiency and improved the flexibility of the printed samples.
In the work of Zhao
[88], the researchers prepared composites consisting of poly-caprolactone (PCL) and starch in different proportions (from 1 g to 10 g) with the aim of using the material in low temperature FDM printing in a temperature range of 80–90 °C. As a result, it was also possible to introduce PHMB into the matrix of the composite. Polyhexanide (PHMB) is a water-based primer based on acrylic resin dispersion. It reduces and balances the absorbency of the substrate and stabilises and strengthens dusty substrates. It is mainly used as a disinfectant and antiseptic. PHMB has been shown to be effective against
Pseudomonas aeruginosa,
Staphylococcus aureus,
Escherichia coli,
Candida albicans,
Aspergillus brasiliensis,
Enterococci and
Klebsiella pneumoniae. The use of PHMB contributed to the production of antibacterial and biocompatible materials using FDM 3D printing.
Kuo
[89] prepared composites based on ABS (70 wt%) and TPS (30 wt%) with the addition of a compatibiliser in the form of a styrene-maleic anhydride copolymer (SMA); an impact modifier, i.e., methyl methacrylate-butadiene-styrene (MMA); and pigments, i.e., titanium white (TiO
2) and carbon black (CB). The twin screw extruder produced white and black filaments, all 1.75 mm in diameter. Tests were carried out using the FDM 3D printing method to determine their physical properties. The results of the research, which included flexural modulus, tensile and flexural strength, HDT, MI and impact strength, showed that it was not possible to produce composites with better physical properties than pure ABS. However, the researchers showed that the addition of various amounts of SMA improved the thermal stability, flowability and mechanical properties of the samples obtained, which means that SMA is an effective compatibiliser in the case of a two-component blend of TPS and ABS. In addition, the researchers showed that the addition of CB contributed to better thermal stability, flowability and mechanical properties in the produced ABS/TBS composites compared to the addition of TiO
2.
Research into the use of starch in FDM 3D printing technology is still giving scientists sleepless nights. They are still trying to expand the use of starch, which is readily available and cheap, and to improve the biodegradability of composites produced by FDM printing.
In summary, there are only a few cases where the addition of natural fibres has led to an improvement in all the mechanical properties of the composites produced. In most cases, a decrease in mechanical properties was observed with increasing biomass filler. The materials used in the FDM process have different ranges of strength and modulus. A wide range of materials have a maximum tensile strength of 40 to 70 MPa and a Young’s modulus range of 0.5 to 2.5
[68]. It is difficult to evaluate each of the composites and biocomposites obtained in this way because they have found applications in different areas of human life. From biomedicine, electronics and construction to furniture, food and textile industries. The technique is still evolving and further research is needed to realise the potential of readily available and inexpensive natural fibres in FDM printing.
3. SLS 3D Printing with Natural Fibres
The most commonly used materials for SLS 3D printing are nylon, polycaprolactone, sand, metal and wax, which are non-renewable resources. According to the literature, there is a need to find low cost, environmentally friendly and biocompatible materials that could be successfully used with common polymers in SLS 3D printing
[90][91].
The authors Guo et al.
[92] successfully developed a plastic composite powder (RPC) from rice husk and plastic hot melt adhesive (PMA). Rice husk is a green and biological material and its main advantage is its low cost. The authors developed a special method to mix the substrates and finally obtained a composite that met the requirements of SLS processing in terms of mechanical properties and dimensional accuracy of the prints.
Li et al.
[93] prepared composites suitable for SLS by mixing pine wood powder with phenolic resin. The content of pine powder in the mixture varied from 30 to 50 wt%. The authors attempted to find a correlation between pine meal content and electrical conductivity and mechanical properties. The physical properties, microstructure, pore distribution and electrical conductivity of the printed porous carbon electrodes were investigated by scanning electron microscopy, X-ray diffraction and electrical conductivity tests. The results showed that pine wood composites can be fabricated into highly tailored carbon electrodes with high porosity using the SLS 3D printing process. In addition, it can be reported in the literature that Zeng et al.
[94] investigated the effect of laser intensity on the mechanical properties of wood plastic composite (WPC) mouldings. As the laser intensity increased from 226 W/mm
2 to 311 W/mm
2, the tensile strength improved by 191% and the flexural strength by 17%. Similarly, as the laser intensity increased from 226 W/mm
2 to 340 W/mm
2, the impact strength of the raw parts improved by 543% and the impact strength of the wax-impregnated parts improved by 147%. However, the authors also showed that at laser intensities above 311 W/mm
2, tensile and flexural strength decreased.
Zhang et al.
[90][95][96] aimed to address the low strength and low relative density of carbon nanotubes (CNTs) and wood-plastic composites. Microwave processing was used to post-treat the SLS moulded parts. Results showed that microwave treatment for about 60 s could improve the flexural strength of CNT/WPC by 4.2–64.2%. Adding a small amount of Al powder as a reinforcing material in WPC to accelerate heat transfer can solve the problem of low mechanical properties of WPC. Keratin-based materials have unique biological and mechanical properties due to their molecular structure and protein organisation. It is extracted from a variety of common natural sources (wool, chicken feathers and horns) and has numerous beneficial properties including biocompatibility, biodegradability and mechanical strength
[4]. Singamneni et al.
[97] prepared keratin composites from polyamide and polyethylene for SLS processing. Mechanical characterisation of the samples sintered at the best laser energy densities showed that the presence of keratin significantly weakens the intermolecular bonding achieved by sintering for the keratin-PA combination, while there is a marginal loss for the keratin-PE composite. The results showed no significant improvement in the mechanical properties of the composites.
4. SLA 3D Printing with Natural Fibres
The raw materials used for SLA are mainly derived from petroleum-based substrates
[90]. In order to meet the change in incremental SLA production towards sustainability, the study of renewable raw materials has become as important a research element as for other 3D printing methods. Unfortunately, there are not many options that can be used for photopolymerisation. However, some vegetable oils can be modified to be suitable
[98][99] Vegetable oils are renewable raw materials with high performance, biodegradability, low toxicity and surface modifiability that are very promising and applicable to SLA
[90]. The authors Anda et al.
[98] investigated acrylated epoxidised soybean oil (AESO) and blends of AESO with vanillin dimethacrylate (VDM) and vanillin diacrylate (VDA) as photosensitive resins for optical 3D printing without photoinitiator and solvent. With a higher yield of the insoluble fraction, they obtained better thermal and mechanical properties of the pure AESO polymer. They subjected the plant-derived resins to ultrashort pulse laser polymerisation by multiphoton absorption and avalanche-induced crosslinking without photoinitiator. They confirmed for the first time that pure AESO and blends of AESO and VDM can be used for 3D microstructuring using direct laser lithography.
In
[98], the authors carried out an extended study using FTIR measurements and photoreology on the UV curing of epoxidised acrylates from soybean oil-based formulations (AESO). The study showed that by adding appropriate functional comonomers, such as trimethylolpropane triacrylate (TMPTA), and adjusting the photoinitiator concentration in the range of 1% to 7%, the UV exposure time could be reduced by up to 25%. Thermal and mechanical properties were also investigated using TGA and DMA measurements, which showed significant improvements in mechanical parameters for all formulations. The properties were further improved when reactive diluents were added. After thorough testing, the prepared vegetable oil-based resin ink formulations with reactive diluents were found to be suitable inks for UV-assisted AM, giving them the appropriate viscosity (
Figure 3).
Figure 3. Printed M-AESO-3. Developed based on
[99].
Tour’s team and Lin’s team
[100] jointly synthesised inks with light-curing, biodegradable and renewable properties using soybean oil, natural polyphenols and luminescent graphene. They also successfully recycled inks from printed products and upgraded biocomposites into luminescent graphene.