Nanobubbles (NBs), also known as ultrafine bubbles, are extremely small (finer than 1 µm) and have several unique physical and physicochemical properties, making them very different from sub-micron (SMBs < 50 µm), micro- (MBs, 50–1000 µm) and conventional air bubbles (CBs, >1000 µm). They can be categorized into surface NBs (formed at solid–liquid interfaces), bulk NBs (exist in bulk liquid and are spherical with a typical diameter of 100–200 nm), and micro-pancakes (quasi-two-dimensional gaseous domains).
1. Introduction
Nanobubbles (NBs), also known as ultrafine bubbles, are extremely small (finer than 1 µm) and have several unique physical and physicochemical properties, making them very different from sub-micron (SMBs < 50 µm), micro- (MBs, 50–1000 µm) and conventional air bubbles (CBs, >1000 µm) [
1]. They can be categorized into surface NBs (formed at solid–liquid interfaces), bulk NBs (exist in bulk liquid and are spherical with a typical diameter of 100–200 nm), and micro-pancakes (quasi-two-dimensional gaseous domains) [
1,
2].
The concept of NBs was first proposed in 1954 to explain the growth of NBs as gas nucleic during cavitation [
3]. An analysis of the fast flotation kinetics claimed by the developed flotation cells in the early 1990s led to the initiation of a research program at McGill University to explore the role of gas nucleation and cavitation in flotation [
4]. The research not only experimentally justified the benefits of applying the two-stage particle–bubble attachment model for the accelerated flotation kinetics but also developed the cavitation tube concept for generating an abundance of NBs in flotation to complete the requirements of the two-stage attachment model [
4,
5,
6]. In 1997, improved flotation rates were reported when the NBs co-existed with CBs [
5]. Later in 2000, the existence of NBs was reported using atomic force microscopy (AFM) by Lou et al. [
7], when the first image of NBs on the hydrophobic solid surface was obtained. Since then, NB-adapted technologies have been applied as a problem-solving alternative for different challenges [
7,
8]. During recent years, liquids containing NBs have attracted attention in industry and academia because of their special properties and wide range of applications, such as nanoscopic cleaning [
9], controlling slip in microfluidics [
10], mineral flotation [
11,
12,
13,
14], chemical industries [
15], and wastewater treatment [
16]. Additionally, numerous studies have been conducted to investigate NB size, shape, surface charge properties, stability, and kinetics [
17,
18,
19]. A historical overview of developments in theoretical and practical investigations regarding ultrafine bubbles is given elsewhere [
20,
21].
The generation of NBs is a complex physicochemical process that depends significantly on several parameters, including temperature, electrolyte concentration, dissolved gas content in solution as well as type and concentration of reagents [
17,
18,
22,
23,
24,
25]. Many methods, such as hydrodynamic cavitation [
26], chemical reaction [
27], ultrasonic oscillation [
28], and electrolysis [
29], have been used to generate either MBs or NBs. However, one of the rarely addressed critical points of using NBs is related to energy consumption and electrical expenses of their generators. In practice, the high energy consumption, installation inconvenience and maintenance difficulty encountered in ultrasonic and electrolysis methods have prevented them from being used in flotation [
30]. Among these methods, hydrodynamic cavitation is considered the most promising method for large-scale mineral flotation applications due to its simple design and high throughput [
31,
32,
33,
34,
35].
2. Generation Techniques
2.1. Power Ultrasound
A commonly used approach for generating bubbles is via acoustic methods, which are relatively simple and applicable in large liquid samples of optically non-accessible media [
79]. Ultrasound generators are compact, simple in operation, have a short generation time, and are contamination-free. Furthermore, the number of bubbles can be controlled by an appropriate selection of ultrasonic frequency and power [
79]. For example, Leroy and Norisuye [
80] proposed that ultrasound is an ideal tool for investigating the existence of bulk NBs because (i) it is sensitive to minute quantities of gas; (ii) it allows one to determine the bubble size distribution; and (iii) it discriminates unambiguously between gaseous and solid/liquid inclusions. Nevertheless, analyzing literature data clarifies that there is generally no unified statement regarding the creation of NBs by acoustic waves. Such contradiction is mainly related to the utilization of different experimental apparatus, studied parameters, and various purposes of the experimental setups [
81]. Further in-depth information regarding the sonication parameters and their effects on the bubble size distribution can be found elsewhere [
81]. Chen et al. [
82] classified the ultrasonically created bubbles into three zones based on the ultrasonication time and frequency, i.e., low (20–50 kHz), medium (200–1000 kHz), and high (>1 mHz). They found that the NBs were unstable at low frequencies, owing to the transient cavitation effect, while the medium range of frequency was selected as the optimum range for acoustic-assisted flotation processes regarding the formation of stable NBs. Power ultrasound (20–100 kHz) penetrates into the medium and creates acoustic cavitation bubbles [
83]. In this method, the pressure sharply decreases below the saturated vapor pressure and leads to considerable dissolving of air and its conversion to bubbles [
28,
84]. Miastkowska et al. [
85] showed that NBs form from bubble nuclei when the ultrasound irradiates into water, and grow to resonance size under acoustic pressure fluctuations and collapse (acoustic cavitation). Thus, ultrasound’s time, frequency, and power substantially impact the size of acoustically generated bubbles. Additionally, Cho et al. [
17] concluded that the effective diameter of NBs generated by ultrasound in pure water was maintained at 750 nm, without significant change within one hour. In addition to the creation of ultrafine bubbles, a positive effect of ultrasonic-assisted flotation either as a pretreatment or simultaneous process has been extensively reported by many researchers on a wide variety of metallic and non-metallic minerals [
83,
86,
87]. Scientists partially related such improvements to the presence of NBs leading to an increase in the hydrophobicity of solid surfaces (expressed as a water contact angle) [
88,
89].
2.2. Solvent Exchange
One of the simplest methods used to create ultrafine bubbles is solvent exchange, which applies an exchange of two solutions with different gas solubilities such as ethanol and water. This method is usually used for the production of NBs on a laboratory scale [
7,
22,
75].
The solvent-exchange process includes a few steps, where at first, a hydrophobic substance should be contacted with water. Then, ethanol replaces water, and NBs are formed and cover the substance’s surface. Gas molecules do not diffuse into the atmosphere and stay in the water during the replacing water of with ethanol. Organic solvents such as ethanol, methanol, and 2-propanol can be applied to produce NBs [
90,
91]. Because the air has a higher solubility in ethanol than water, the exchange process leads to gas supersaturation, and consequently, NB nucleation. These NBs form a huge number of interfaces in the solution. These interfaces can cause the directed arrangement of ethanol molecules due to their amphiphilic nature [
91]. Further, other methods such as exchanging cold water against warm water and ethanol solution against salt solution have been applied for producing NBs [
75]. Ethanol–water exchange was used for the first time on the surface of mica by Lou et al. [
7] to generate ultrafine bubbles. Some researchers found that the number of NBs was enhanced with an increase in the alcohol concentration up to 70%, and above this concentration, the bubbles disappeared [
92]. Xiao et al. [
91] applied molecular dynamic (MD) simulations for predicting the NBs generation by the solvent-exchange method. They showed that there is an interface between exchanging solvents with different gas solubilities, and the interface gradually moves towards the substrate, forming NBs in the bulk solution and/or on the hydrophobic solid surface.
Although the solvent exchange is used for generating bubbles, the exact mechanism of processing the gas saturation is yet unknown. Furthermore, the solvent-exchange method cannot control bubble formation precisely because several factors such as the exchange rate, liquid shear, saturation level of gas, and flow boundary conditions, cannot be controlled during the experiments [
91].
2.3. Temperature Change
Another technique for producing ultrafine bubbles is the temperature difference method. Changing temperature is one of the important physical and chemical factors related to bubble generation at the solid–water interface [
93,
94]. In this method, the gas solubility in water and heat diffusion reduce due to increased temperature. Through this, water becomes supersaturated with air, and releasing gas induces the production of fine bubbles on the solid surface [
22,
75]. Some researchers have reported that the increase in the liquid temperature leads to the formation of in situ NBs [
22]. They showed that NBs generated during immersion and at high-water temperatures remain stably on the surface at low water temperatures. Moreover, such bubbles were sensitive to the cleaning process used to prepare the substrates [
22]. Zhang et al. [
95] and Yang et al. [
22] showed that when the temperature was enhanced to 30 °C, the density of bubbles was enhanced very slowly, but was boosted sharply when the temperature increased further. They also indicated that the generated bubbles did not disappear when the water cooled down to ambient conditions, and they were remarkably stable.
2.4. Hydrodynamic Cavitation
In recent years, one of the most critical methods for generating NBs has been hydrodynamic cavitation [
5,
12,
53]. This is the process of creation and growth of gas bubbles in a liquid due to the rupture of either a liquid–liquid or a liquid–solid interface under the influence of external forces [
96]. In other words, when rapid changes in pressure in a liquid occur in places where the pressure is relatively low, vapor-filled cavities are formed, and this phenomenon is called cavitation [
32,
34,
97].
The first study of cavitation was carried out in the 1710s, but the term cavitation was introduced in 1895 by Thornycroft and Barnaby [
98]. The first stage of cavitation is defined as nucleation, which is the formation of cavities. In this process, the liquid structure is ruptured to form a hole by external forces. Additionally, rupture starts at a weak location where the intermolecular forces approach zero [
99,
100]. The nucleation of a bubble on a particle surface increases bubble–particle collision, which is often a rate-limiting step in flotation with CBs. Hence, cavitation and gas nucleation provide a suitable mechanism for the collection in flotation [
101]. Hydrodynamic cavitation is well-described by Bernoulli’s equation [
5]:

where U is the water flow velocity at a point where the pressure is P, and ρ is the liquid density.
Cavitation number (
K) is normally used for calculating the onset of cavitation in either equipment or components with flow constrictions, and is defined as follows [
4]:
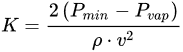
where
Pmin is the minimum pressure occurring in the vicinity of the restriction,
Pvap is the vapor pressure of the liquid,
ρ (kg/m
3) is the density of the liquid, and
v (m/s) is the flow velocity through the restriction. The cavitation phenomenon occurs when the cavitation number is less than 1.5 [
102].
Cavitation is affected by many factors, which include geometric parameters, operational conditions, dissolved gas content, reagent concentrates, and the addition of solids [
101,
103]. A venturi tube is typically used as a hydrodynamic cavitation device. The liquid in the cylindrical throat is higher in flow velocity and lower in pressure than the liquid in the entrance cylinder, resulting in cavitation. The differential pressure between the entrance cylinder and the cylindrical throat measured by the manometers is indicative of cavitation behavior [
5,
96,
101]. Different designs of cavitation tube technologies have emerged and become commercially available for laboratory research, flotation machines, and commercial flotation operations. For example, Eriez Manufacturing Co., (Erie, PA, USA) has sold more than 200 flotation columns using CavTubes for sparging, and has retrofitted many other columns with the cavitation tube technology [
104].
Some companies, such as Canadian Process Technologies (CPT), Coalberg seam coal in West Virginia [
59], CSIRO Energy Technology, and Novatech Consulting [
105], have applied high-shear cavitation to improve flotation of fine coal, iron ore, phosphate, fluorite, niobium, feldspar, mica, and molybdenum. They illustrated that recovery of fine and coarse particles was low by CBs, which was improved by applying hydrodynamic cavitation. Some researchers have used this mechanism as a pulp pretreatment method before flotation [
6,
51,
64,
106]. Other studies have employed it in flotation separation processes; the tests were carried out in mechanical and column flotation cells [
13,
51,
53,
107,
108]. Additionally, recent tests have shown the potential of its application to recover/remove residual bitumen from oil–sand mature fine tailings [
102].
Some researchers have also investigated the effect of different types of gases (e.g., air, O
2, N
2, Ar, and CO
2) on NBs generation [
97,
103]. The results confirmed that the sizes of ultrafine bubbles were well-correlated to the gas solubility in water. Indeed, larger bubbles were obtained with gas of a higher solubility, accompanied by more ultrafine bubbles generated. Li [
109] reported that a linear correlation was found between the volume of generated cavity bubbles and air saturation pressure, further confirming that NBs generation and stabilization are proportional to the dissolved gas concentration.
2.5. Electrolysis and Chemical Reaction
An alternative method to produce NBs is water electrolysis. In this technique, oxygen and hydrogen bubbles can be generated at the hydrophobic surface–water interface by producing oxygen and hydrogen gases at the electrolysis electrodes when the surface acts as a negative electrode. Changing voltage and reaction time affects the formation, growth, and size of NBs. The type of gas applied is also an essential factor in controlling the generation and properties of NBs. The results illustrated that the number of oxygen bubbles generated was substantially smaller than the hydrogen ones, because oxygen solubility in water is approximately two times the solubility of the hydrogen during the electrolysis process [
110]. Further, oxygen bubbles are more stable than air bubbles, which in turn are more stable than other NBs [
46]. This method is mainly applied in electro-flotation techniques [
110,
111].
The supersaturation of dissolved gas can further produce bubbles by chemical reactions, which liberate a gaseous species. This can be applied as a potential method for generating ultrafine bubbles. For example, carbon dioxide generated by mixing acid with carbonate was applied in a reactive flotation technique [
100,
112]. In this method, the concentration of reactants and the solution conditions were controlled by the rate of a chemical reaction that can be enhanced using catalysts. Thus, gas supersaturation by the chemical reaction provides relatively appropriate conditions for the generation of NBs. Some researchers have investigated the electrochemical nucleation of bubbles on solid nano-electrode surfaces [
113,
114]. The reduction of protons in acidic solutions [
113] and oxidation of N
2H
4 [
114] and H
2O
2 [
115] generated gaseous products (hydrogen, nitrogen, and oxygen). In another study, the chemical reaction between ammonium chloride and sodium nitrite created bulk nitrogen NBs with diameters of 200–300 nm [
116]. They concluded that these bubbles formed only when they were trapped between two carbon films.
This entry is adapted from the peer-reviewed paper 10.3390/min12040462