Among all biomimetic materials, nacre has drawn great attention from the scientific community, thanks to superior levels of strength and toughness and its brick-and-mortar (B&M) architecture. However, achieving the desired performances is challenging since the mechanical response of the material is influenced by many factors, such as the filler content, the matrix molecular mobility and the compatibility between the two phases. Most importantly, the properties of a macroscopic bulk material strongly depend on the interaction at atomic levels and on their synergetic effect. In particular, the formation of highly-ordered brick-and-mortar structures depends on the interaction forces between the two phases. Consequently, poor mechanical performances of the material are associated with interface issues and low stress transfer from the matrix to the nanoparticles. Therefore, improvement of the interface at the chemical level enhances the mechanical response of the material.
1. Introduction
1.1. Mimicking Nature: Nacre-Inspired Materials
Among all biomimetic materials, nacre has drawn great attention from the scientific community, thanks to superior levels of strength and toughness and its brick-and-mortar (B&M) architecture. Nacre is the iridescent inner shell layer of some molluscs. It consists of a 3D assembly of hard lamellar aragonite tablets glued together with a low amount (5 vol%) of soft organic materials (proteins and polysaccharides). This hierarchically organized microstructure and the small fraction of biopolymers are responsible for the unique mechanical behaviour. In addition, the mineral bridges that connect the different tiles at the nanoscale level are capable of preventing crack extension and providing toughness and impact resistance
[1][2]. Although nacre is composed of fragile material, it exhibits a ductile behaviour, allowing plastic deformations. Its peculiarity is the high toughness, which is three orders of magnitude higher than its main constituents. Nevertheless, it is associated with different mechanisms acting at the nanoscale: (i) nanoasperities of the aragonites tiles; (ii) organic layer acting as viscoelastic glue after the elongation of biopolymer; (iii) mineral bridge relocking after fracture; (iv) tile interlock due to the microscale waviness and dovetail of tiles
[1].
1.2. Engineering Materials Based on 2D Nanoparticles
Inspired by nacre, several synthetic materials with brick-and-mortar structure. have gathered the attention of scientists worldwide. In particular, several systems have been studied and various platelet/polymer structures have been investigated. Particular attention has been devoted to paper-like materials reinforced with lamellar fillers, which can reproduce on the macroscopic scale the mechanical characteristics of the nanoscale reinforcement. The mechanical and functional properties of this class of material can be designed according to the filler and matrix nature
[3], as described in
Table 1. The mechanical performances in terms of strength and stiffness are regulated by the filler properties, while the energy dissipation is regulated by the matrix brittle or ductile behaviour. However, the overall behaviour depends on the quality of stress transfer between the two phases and on their interactions. On the other hand, thermal and electrical properties depend only on the nature of the filler, due to the low amount of polymer, and are characterized by high anisotropy between in-plane and cross-plane conductivities
[4][5].
Table 1. Mechanical and functional behaviour of composites with high content 2D nanofiller according to reinforcement nature.
Filler |
Matrix Type |
Composite Mechanical Behaviour |
Composite Conductivities |
Graphitic (GO, RGO, GNP, Pyrolytic Graphite…) |
Brittle |
Pseudo-elastic |
Electrically Conductive in plane High ratio in plane/trough thickness thermal conductivity |
Ductile |
Plastic |
Ceramic (MTM, Alumina, Silica…) |
Brittle |
Pseudo-elastic |
Isolating |
Ductile |
Plastic |
Several attempts have been made to mimic and design artificial nacre. For this purpose, different materials have been employed as bricks and mortar. The most employed nanoparticles used as reinforcement are listed in Table 2, and a comparison in terms of costs, mechanical properties and thermal and electrical conductivities is presented.
Table 2. Comparison between 2D nanoplatelets employed as reinforcement in B&M composites.
Particle |
Costs |
Geometry |
Elastic Modulus |
In Plane—Therm. Cond. |
Elec. Cond. |
Graphene |
EUR 200–300 per flake |
Monolayer |
1 TPa [6] |
5000 W/mK [6] |
107–108 S/m [6] |
GO |
2–5 layers 48 EUR/g |
2–5 layer BET 420 m2/g |
250 GPa [7] |
72 W/mK with an oxidation degree of 0.35 [8] |
270 S/m [9] |
RGO |
2–5 layers 68 EUR/g |
2–5 layer BET 1562 m2/g |
250–350 GPa [10] |
670 W/mK with an oxidation degree of 0.05 [8] |
4480 S/m [11] |
GNP |
6–10 EUR/g |
>10 layer BET 30 m2/g |
25–40 GPa [12] |
300–470 W/mK [5] |
2 × 106 S/m [13] |
MTM |
<1 EUR/g |
BET 750 m2 very high (nm × µm) aspect ratio |
207 GPa [14] |
16 W/m [15] |
25 to 100 mS/m [15] |
1.3. Technologies Enabling Industry Applications
By combining the knowledge of biological materials with processing techniques, synthetic materials with remarkable mechanical and functional properties can be designed. Several methods have been used for the production of nacre-like materials, capable of reproducing the hierarchical well-organized microstructure of nacre, with lamellar nanoparticles aligned in the longitudinal direction and bonded together by a thin matrix layer 1
[16][17].
Generally, production methods follow two different approaches: top-down and bottom-up. For a definition, top-down methods go from a general to a specific level, while bottom-up methods begin at a specific level and move to the general one. More specifically, in top-down technologies the material is fabricated starting from a mixture of nanoparticles and polymer, which is assembled in such a way as to ensure a layered structure (Figure 1a). Conversely, in bottom-up technologies, the material is specified in great detail, by alternatively arranging the two phases and building up a layered structure (Figure 1b).
Figure 1. Top-down (a) and bottom-up (b) approaches for manufacturing of composites with B&M architecture.
2. Mechanical Performances
Figure 2 shows an Ashby plot of strength and elastic modulus of artificial nacre with bricks of various nature. Graphene oxide (GO) nanoparticles, and in particular reduced graphene oxide (RGO), guarantee the best performances in terms of strength of the material, while exhibiting elastic moduli in the range of 15–40 GPa and 3–15 GPa, respectively. On the other hand, composites made with ceramic bricks, such as montmorillonite (MTM), show low values of strength but high elastic moduli (10–35 GPa). Finally, composites reinforced with graphene nanoplatelets (GNPs) exhibit the lowest values of strength but discrete elastic moduli in the range of 20–30 GPa. The low number of points indicates that they are not widely used as reinforcement in brick-and-mortar composites because of the difficulty of the nanoplatelets to be well dispersed in polymers.
Furthermore, these ranges are wide and depend on different factors, such as volumetric filler content, range of motion of the polymeric chains and the filler/matrix compatibility. The best performances can be achieved by improving the compatibility between nanoparticles and the polymers and their interactions, for example by chemically functionalizing the nanoplatelets or improving crosslinking. In fact, in
Figure 2 the highest values of elastic moduli are achieved when the chemical affinity between the two phases is improved, for example by using glutaraldehyde (GA)
[18][19], boric acid (BA)
[20] or water (H
2O)
[21], or by functionalizing GO with polydopamine (P-GO)
[22].
The mechanical properties of composites reinforced with lamellar nanoparticles usually depend on alignment and interfacial properties. At high filler content, the bricks tend to be extremely oriented in-plane because the available volume for nanoparticle rotations or displacement is limited, with a consequent waviness reduction and alignment improvement. Thus, for nacre-like materials, the mechanical performances mainly depend on the stress transfer between filler and matrix. The efficiency of reinforcement is strictly related to the interfacial properties, i.e., to the chemical affinity between the two phases, to the matrix wettability and to the molecular interactions that occur between adjacent nanoplatelets.
2.1. Influence of Filler Content
From a critical analysis of the mechanical behaviour of composites with nano-lamellar reinforcement at relatively high filler content, it emerges that the elastic modulus of these systems drops after a critical concentration deviating from the expected behaviour, which dictates that the higher the filler content the higher the macroscopic elastic modulus.
2.2. Influence of Matrix—Effect of Matrix Molecular Weight
In particular, the matrix choice can be discriminatory for the optimal mechanical performance of the material. The higher the molecular mobility of the polymer and the capacity to intercalate between nanoplatelets, the better the stress transfer at the interface and thus the performance of the material even at high filler content. Short polymer chains are able to diffuse between nanoparticles during assembly, while very long polymer chains’ ability to navigate around the layered nanosheets is more limited
[31][52]. Evidence of this behaviour can be found by comparing the volumetric filler fraction at which the drop of efficiency occurs and the matrix molecular weight (
Figure 3). For high molecular weights (150–300 kDa), the drop of efficiency occurs for very low volumetric filler content (20–30 vol%), whereas for low molecular weight (<100 kDa), the drop occurs for filler content greater than 40 vol%.
Figure 3. Dependence of drop off point on matrix molecular weight.
This indicates that the matrix molecular mobility affects the efficiency of reinforcement, which decreases as the molecular weight increases. The dependence of the efficiency of reinforcement from the matrix molecular weight is also shown in Figure 4 for a system reinforced with different nanoplatelets, especially in the case of MTM and GO. In the case of RGO, there is little evidence of this behaviour since the efficiency is very low (<10%) (Figure 4c).
Figure 4. Efficiency of reinforcement vs. molecular weight for composite reinforced with: (a) MTM; (b) GO; (c) RGO.
2.3. Filler/Matrix Compatibility—Chemical Bonding
As shown so far, the best mechanical performances are achieved when the chemical interactions between the two phases are improved
[53]. It was found in the literature that functionalizations with glutheraldeyde (GA)
[18], boric acid (BA)
[54], water (H
2O) or polydopamine are very efficient, as can be seen in
Figure 2. This effect can also be observed in GO films without a binder.
Figure 5 reports the efficiency of reinforcement for GO films with chemical bonds of various strength: covalent bond using BA
[54], hydrogen bond using H
2O
[31] and ionic bond using Al
3+, Mg
2+ ions
[55] and GA
[56]. As expected, BA crosslinking creates strong covalent bonding, which significantly improves the elastic modulus by 240% with respect to not functionalized GO films. On the other hand, functionalization with H
2O slightly increases the modulus by 25%, while ions lower the mechanical properties of the material due to the increase of the spacing between nanosheets.
Figure 5. Effect of nanoparticle functionalization on the elastic modulus of GO films without binder.
However, the strength of chemical bonds also depends on the nature of the filler. For example, graphitic nanoplatelets, such as GO, RGO, GNP, are very different from a chemical point of view. Specifically, GO contains oxygen atoms on the surface, which interact with the polymeric matrix establishing covalent, ionic or hydrogen bonds. After oxidation, the oxygen content of RGO reduces significantly and with it the possibility to create strong chemical bonds with the polymeric matrix. As a consequence, the mechanical performances are very poor, as demonstrated previously (Figure 4c). The same discussion can be carried out for GNPs, which can interact only with weak vdW bonds and π–π interactions.
Consequently, the efficiency of reinforcement sharply decreases with increasing carbon/oxygen ratio (C/O), as shown in
Figure 6. Typical values of the C/O ratio lie around 2 for GO and increases in the case of RGO being greater than 4
[57].
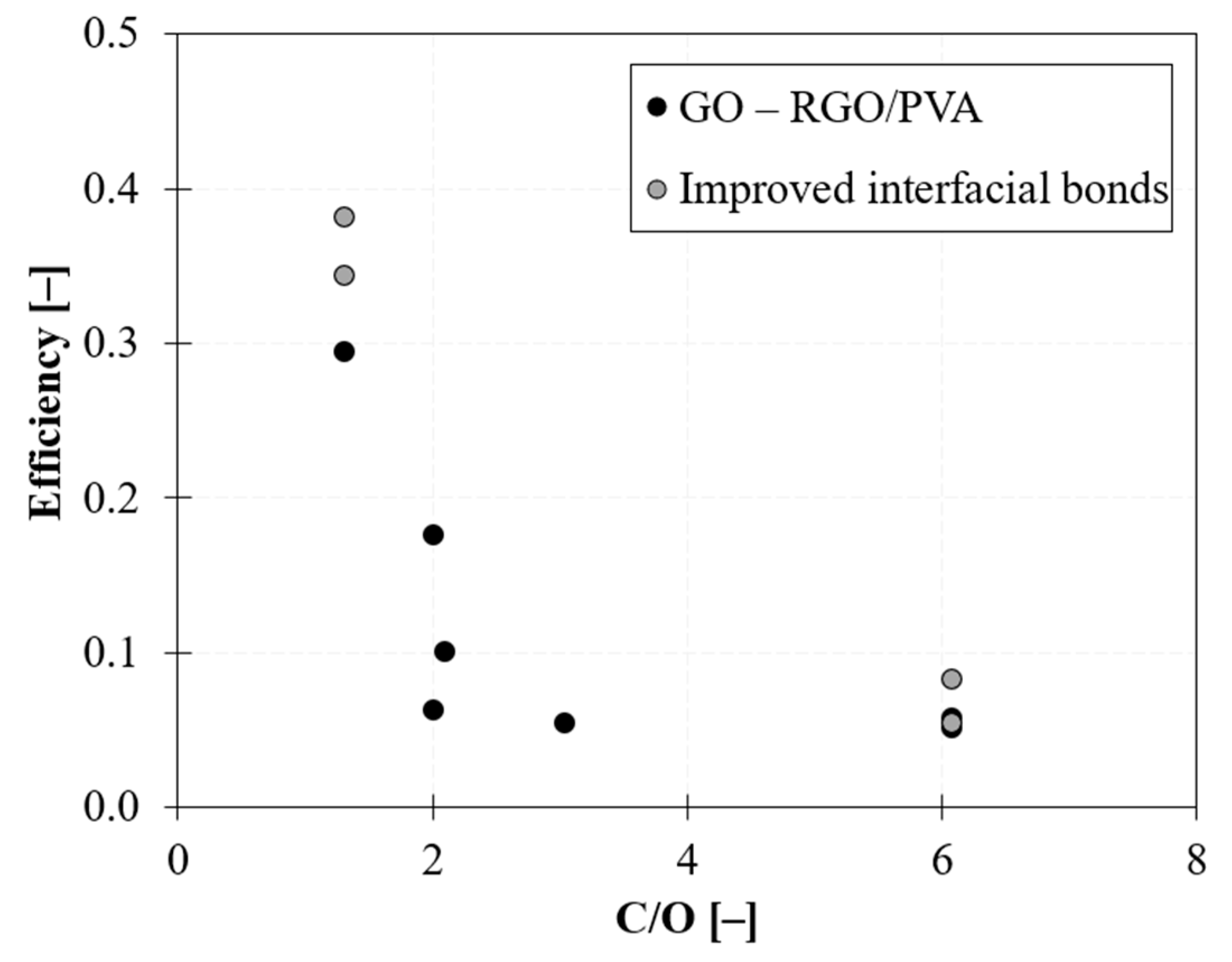
Figure 6. Influence of chemical interactions between filler and matrix: efficiency of reinforcement vs. C/O ratio in GO/PVA and RGO/PVA films.
2.4. Interfacial Shear Strength
The efficient matrix–nanoplatelet stress transfer is essential to take advantage of the very high Young’s modulus and strength of the reinforcement. To assess the efficiency of reinforcement in nanocomposites, the interfacial property, which includes wetting, stress transfer and adhesion, should be thoroughly examined.
The experimental evaluation of the interfacial shear strength (IFSS) in a direct way is a challenging task, due to the technical difficulties involved in the manipulation of nanoscale objects. In carbon nanomaterials, the interfacial mechanics can be investigated by integrating scanning probe methods with spectroscopic techniques, such as tip-enhanced atomic force microscopy (AFM)
[58] and Raman spectroscopy.
Experimental techniques able to quantitatively evaluate the IFSS at the nanoscale level are still demanding.
To overcome the issues associated with the direct evaluation of IFSS, indirect methods, such as Raman spectroscopy, are widely used
[59]. Raman spectroscopy gives information about the quality of stress transfer between the matrix and the reinforcement
[60]. It is a valuable tool for understanding the relationship between macroscopic deformation and the deformation mechanism at the molecular or microstructural level. When the material is subjected to an external load, the nanoparticles and their chemical bonds are stressed and the interatomic distance changes, resulting in a translation of the spectrum peaks
[61][62]. Thus, by monitoring the wavenumber shift of the Raman bands when a macroscopic stress/strain is applied (Raman shift rate), it is possible to identify the stress level within the nanoparticles and thus the capability of the matrix to transfer load
[63][64].
3. Analytical Models for the Prediction of Mechanical Properties
At high filler content, the material architecture involves complex deformation mechanisms. The coexistence of a soft domain (polymeric layer) and a hard domain (bricks) could affect molecular mobility, leading to an increase in ductility and energy dissipation.
Actual biological and engineering structures, such as nacre, display spatial variations in overlap lengths, with different distributions which can be relatively narrow, as in the case of columnar nacre, or very wide and even uniform, as in the case of sheet nacre.
However, modelling these complex microstructures with a single unit cell gives a reasonable representation of the mechanical response of the material, which is sufficiently reliable to examine trends and establish broad design guidelines.
Composites with brick-and-mortar architecture can be schematized as depicted in Figure 7. They consist of a uniform assembly of bricks glued together by a uniform matrix thin layer (mortar).
Figure 7. Schematic illustration of brick-and-mortar composites.
The behaviour in tension is described in
Figure 8. At small strain both bricks and mortar move in the elastic field and the behaviour is linear. Then, four different failure mechanisms can occur
[65]. If the brick is weaker than the matrix, there is an instant failure, which leads to a fragile behaviour of the structure. Otherwise, the matrix in the vertical interface yields, making the behaviour more ductile. In this case, for linear elastic matrices, the composite exhibits a pseudo-elastic behaviour and failure is attributed to the vertical junctions, whereas for matrices with elastic–plastic behaviour, yielding in the horizontal direction occurs, allowing sliding between bricks. The composite failure can be attributed to the mortar break either in the vertical junctions or in the horizontal interfaces. In both cases, large strains are reached with consequent sliding between bricks and the final pullout mechanism.
Figure 8. Stress–strain behaviour in tension of B&M composites.
In modelling brick-and-mortar composites, it is assumed that the bricks behave elastically, while the mortar can have both elastic and elastoplastic behaviour. Small plane strain deformations are assumed with zero strain in the z-direction, and zero stress in the y-direction. In addition, under uniaxial deformation, the horizontal interfaces experience pure shear according to the relative displacements between adjacent bricks in different rows, while the vertical interfaces experience pure tension according to the relative displacements between adjacent bricks in the same rows. Finally, the horizontal mortar layer is considered very small, such that the shear strain is uniform. The representative volume elements (RVE) are accurately chosen according to the analytical model.
The mechanical performance of these composites is regulated by the efficacy of the thin polymeric layer to transfer load, via the shear transfer mechanism
[66]. Thus, models
[65][67][68][69] and design strategies
[70][71][72] to predict the elastic modulus and strength of brick-and-mortar composites, based on the shear lag theory, have been proposed in the literature. These models assume perfect bonding between the two phases, efficient load transfer to the particles and the existence of a continuous uniform matrix layer between the bricks.
4. Conclusions
Although composites with brick-and-mortar architecture are promising from a theoretical point of view, in reality, it is challenging to achieve the desired mechanical performances. The target is to assemble 2D nanoparticles in order to achieve a macroscopical material able to reproduce the unique properties of the 2D nanoparticle:
vf →1 ↔ Ec ≈ E2D particle
This condition can be achieved when the matrix arranges as a continuous nanometric film on the nanoplatelets’ surface and the complete stress transfer at the interface is guaranteed, according to the shear lag theory. However, the mechanical response of the material is influenced by several factors: volumetric filler content, matrix molecular mobility and compatibility between the two phases. Thus, the efficiency of reinforcement:
- Drops at high filler content. Starting from a critical volumetric fraction, the elastic modulus B&M composites deviate from the expected behaviour dictated by the rule of mixture due to the partial coverage of the nanoplatelets at the nanoscopic level.
- Decreases as the molecular weight increases.The higher the molecular mobility of the polymer and the capacity to intercalate between nanoplatelets, the better the stress transfer at the interface.
- Improves when a high interfacial attraction between nanoparticles and the surrounding matrix is guaranteed. Strong chemical bonding and molecular interactions between nanoparticles and the polymer ensure self-assemblies with a tendency toward forming intercalated morphologies, with a stable layer of polymer between flakes.
This entry is adapted from the peer-reviewed paper 10.3390/nano12081359