Several obstacles remain in the way of widespread hydrogen use, most of which are related to transport and storage. Dilute formic acid (FA) is recognized asa a safe fuel for low-temperature fuel cells. FA is examined as a potential hydrogen storage molecule that can be dehydrogenated to yield highly pure hydrogen (H2) and carbon dioxide (CO2) with very little carbon monoxide (CO) gas produced via nanoheterogeneous catalysts.
1. Introduction
Transportation and other energy-related sectors will be highly needed as safe and sustainable energy carriers in the future. Researchers are working in various sectors such as geothermal power, lithium-ion batteries, solar energy conversion, and nuclear energy, all of which have the potential to solve the energy crisis in the foreseeable future
[1][2][3][4][5][6][7]. Hydrogen (H
2) is a viable medium-term energy storage option. It is expected to contribute significantly to the future energy system as a supplementary fuel and energy carrier
[8][9][10]. Hydrogen has a high specific energy of 33.30 kWh kg
−1 than diesel, which holds only about 12–14 kWh kg
−1. On the other hand, a hydrogen economy is unlikely to emerge unless major integrated technological advancements in H
2 generation, storage, and delivery systems are achieved
[11].
Figure 1 summarizes the key advantages of hydrogen gas as an energy carrier
[8][12].
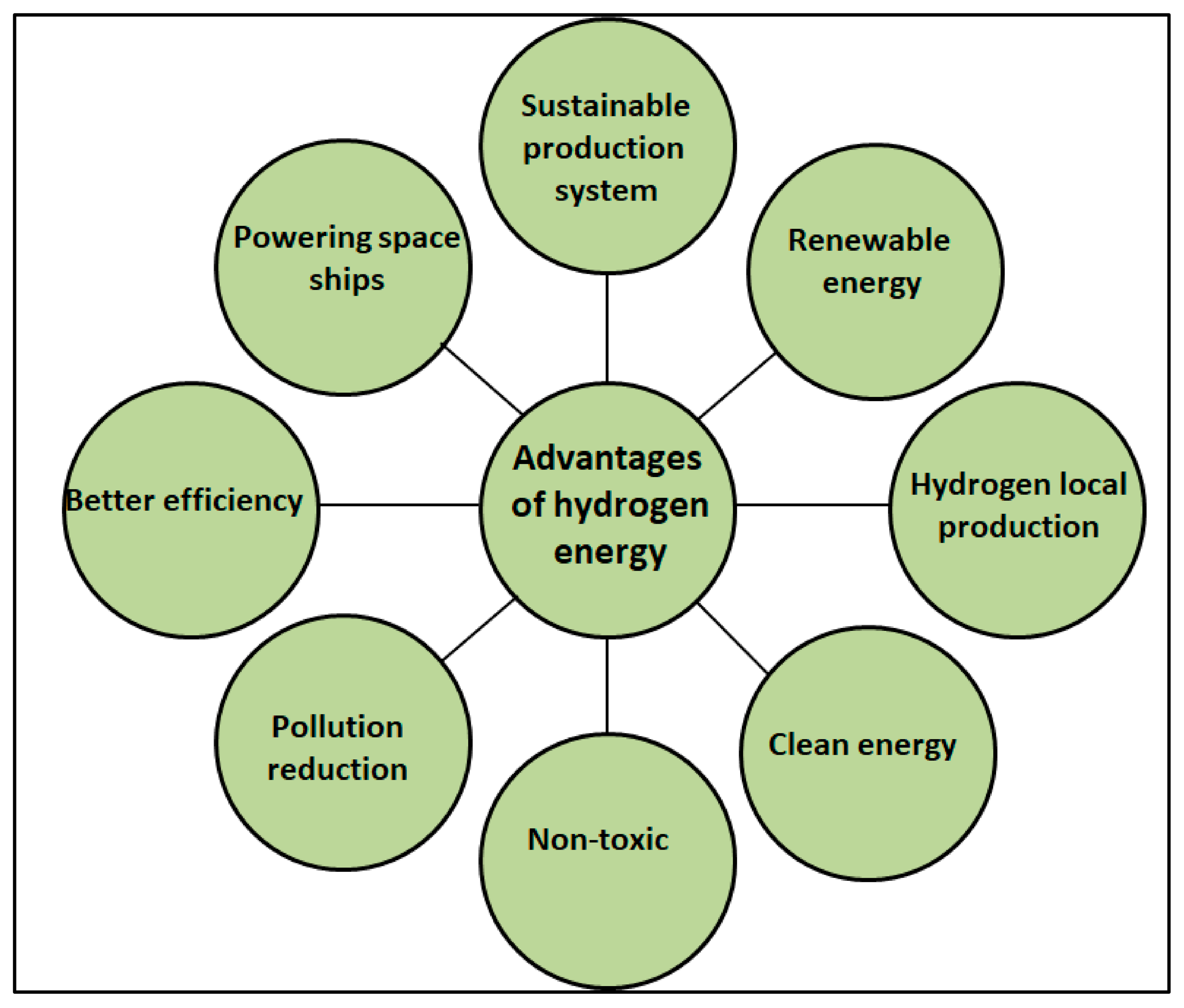
Creating a safe and effective hydrogen storage system is a major problem
[13][14]. Accordingly, various sophisticated research techniques to create novel materials that store and distribute hydrogen at satisfactory rates have been developed to utilize hydrogen as a green energy source and solve the challenges of its efficient and safe storage. Physical or chemical storage can be classified according to the methods used. In the physical storage technique, H
2 can be held in its diatomic molecule state in a covered vessel under low temperatures and high pressure, such as in the case of cryo-compression and tanks of high pressure
[15], or adsorbed on high surface area materials, such as metal-organic frameworks
[3][16][17][18][19], clathrate hydrates
[20], zeolites
[21][22] and various carbon materials
[23][24][25][26]. In the chemical storage technique, H
2 is stored in a chemically bonded state rather than in a molecular state. Typically, certain appropriate compounds have been selected because they have greater hydrogen content and can release hydrogen effectively at ambient conditions (temperature and pressure) by catalytic or non-catalytic methods. Examples of such compounds include hydrous hydrazine, metal amidoborates, metal borohydrides, ammonia borane, sodium borohydride and formic acid (HCOOH; FA)
[27][28][29][30][31]. However, because of their poor kinetics for reversible hydrogen adsorption-desorption interactions, low intrinsic thermal conductivity, thermodynamic stability, toxicity, and high price, the practical applicability of several of these hydrogen storage compounds is greatly limited
[32].
Organic liquid molecules such as formic acid (FA) have attracted interest because of their high energy density, low toxicity, and ease of handling
[33][34]. Formic acid is one of the primary products generated during biomass processing, containing 4.4 wt.% hydrogen. In addition, pure FA contains 52 g H
2/L or 43.8 g H
2/kg, which makes it one of the important liquid organic hydrogen carriers (LOHC)
[35]. Furthermore, FA transportation and refilling are simple because FA is liquid at room temperature; this allows it to be handled similarly to diesel and gasoline
[36].
Formic acid is a highly promising hydrogen storage substance available nowadays. It outperforms most other state-of-the-art hydrogen storage materials in terms of usable/net capacity. In addition to its advantages, FA is highly stable at ambient temperature without catalysts. Besides its inherent properties, another significant advantage of using FA as a hydrogen storage substance is that even the carbon dioxide (CO2) produced during FA dehydrogenation can be hydrogenated later; this regenerates FA molecules in a carbon-free release process. Moreover, FA can serve as a connection between renewable energy and hydrogen fuel cells. Progress can only be achieved with the right catalysts.
Other liquid organic compounds, commonly known as liquid organic hydrogen carriers (LOHC)
[37], such as methanol carbazole, cycloalkanes, and others, have been intensively explored in addition to formic acid. However, these compounds have several drawbacks that make them unsuitable as hydrogen storage materials, including toxicity, expense, poor stability, slow dehydrogenation kinetics, and low regeneration efficiency
[38][39].
2. Formic Acid Decomposition
Fuel cells have remained unpopular because of the high cost of creating, storing, and transporting hydrogen. Rather than delivering hydrogen gas, having a chemical hydrogen storage substance or hydrogen-containing substance which can be decomposed under ambient circumstances to create H2 gas whenever needed is more practical.
Using a catalytic dehydrogenation process can release the hydrogen contained in FA through two main pathways (i) dehydrogenation/decarboxylation yielding H
2 and CO
2, and (ii) dehydration/decarboxylation yielding H
2O and CO (Equations (1) and (2))
[40][41][42].
The CO-free degradation of formic acid in the pathway (i) is essential for formic acid-based hydrogen storage, whereas pathway (ii) produces CO, which is an undesirable product that deactivates fuel cell catalysts. Therefore, pathway (ii) should be avoided. Based on this, and depending on the catalysts, reaction temperatures and pH values of the solutions, carbon monoxide (CO), a deadly poison to fuel cell catalysts, can also be produced by an undesired dehydration pathway (Equation (2)). High temperatures generally enhance dehydration during the reaction
[43][44]. Fuel cell systems require ultrapure hydrogen to generate energy, and because CO poisons them, intake CO concentrations should be kept below 20 ppm to avoid long-term performance loss.
The dehydrogenation of FA (Equation (1)) produces only gaseous products (H
2/CO
2), with no accumulation or formation of by-products, making it advantageous compared to other alternative hydrogen carriers, particularly for portable usage. The gas combination produced is used as a feed-gas for an H
2/air fuel cell directly
[45]. Because such fuel cells are intended to deliver energy to portable devices with limited heat management capabilities, mild temperatures are crucial.
Figure 2 presents a plausible mechanism for producing hydrogen from formic acid using metal nanoparticle (MN) catalysts. The following reactions would occur as a result of the mechanism:
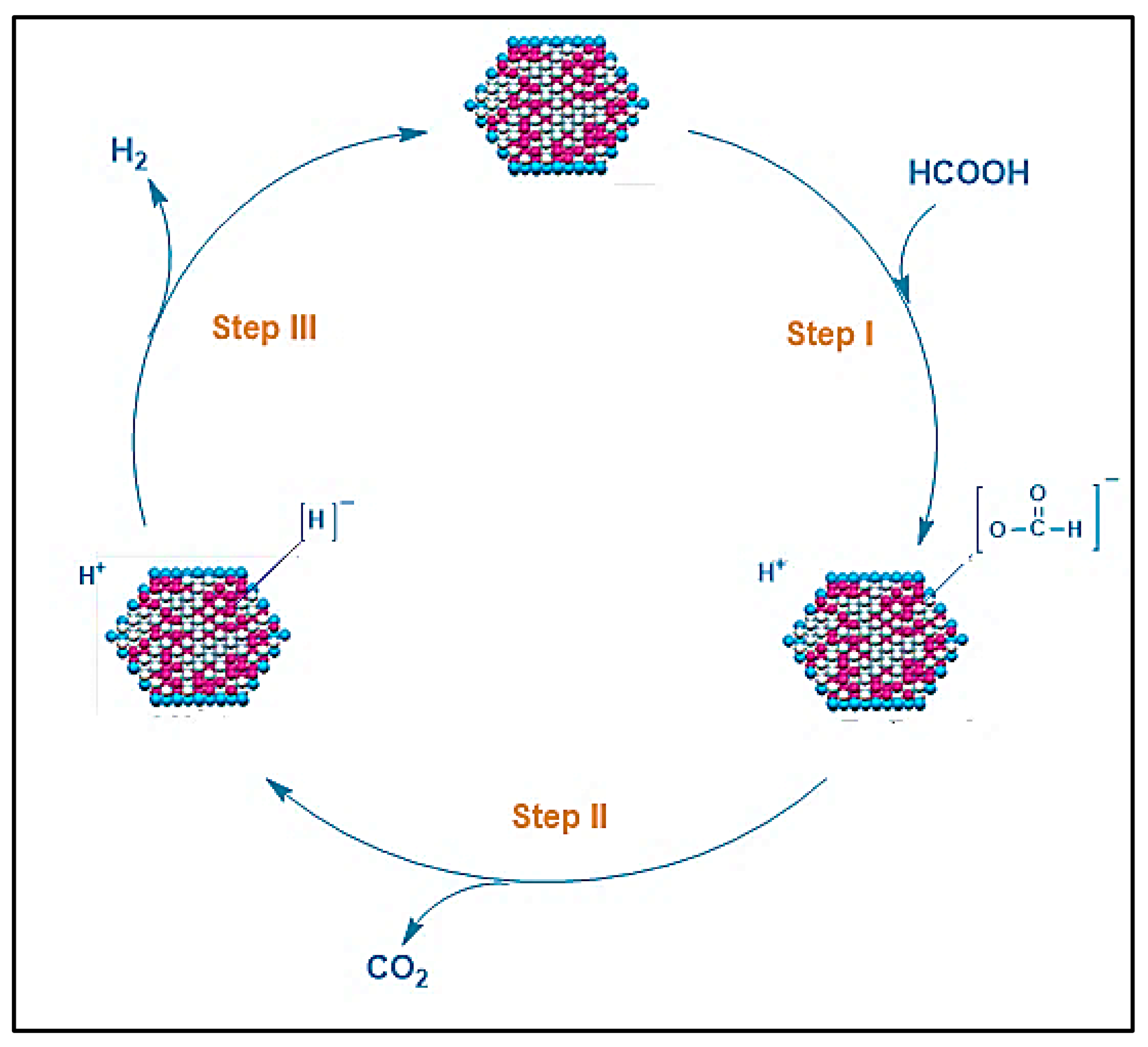
3. Heterogeneous Catalysts
Studying FA decomposition using heterogeneous catalysts has occurred since the 1930s, yet optimizing the catalysts, and measuring the CO produced by the FA dehydration-side reaction were not fully examined in early research
[46]. In that state, the reaction was mostly examined in the gas phase, necessitating temperatures greater than 100 °C (formic acid’s usual boiling point) or using an inert carrier gas that dilutes FA under its saturated vapor pressure; both would add to the setup’s complexity. Because of their large surface area/mass ratio, nanoparticles are particularly well suited to act as catalysts in fuel cells. As a result, their utilization saves time and money. Developing heterogeneous catalysts for liquid-phase FA dehydrogenation is therefore crucially required
[47]. A number of publications on nanoheterogeneous catalysts with different support materials for the dehydrogenation of aqueous FA have been published, emphasizing H
2 selectivity and low-temperature activity.
3.1. Monometallic Heterogeneous Catalyst
Several studies have been published recently on monometallic noble metal nanoparticles (NPs) based on different catalysts for FA dehydrogenation in an aqueous medium
[48][49][50][51]. Bi et al.
[52] used hyper-dispersed subnanometric gold NPs on ZrO
2 as catalysts to show the moderate and selective dehydrogenation of an FA/amine mixture. Under ambient conditions, the catalytic processes happen effectively and selectively (100%), with high TOFs/catalyst turnover numbers (TONs), and without generating any undesirable by-products such as CO. At ambient temperature, very efficient hydrogen was obtained from the production, from aqueous solution, of formic acid/sodium formate catalyzed via in situ-produced Pd/C with citric acid. Surprisingly, the addition of citric acid in the middle of the synthesis and development of Pd NPs on carbon improves the catalytically activity of the resultant Pd/C, on which the greatest conversion and turnover frequency for the breakdown of formic acid/sodium formate system can be achieved at ambient temperature
[53].
3.2. Bimetallic Heterogeneous Catalyst
It is generally known that adding a secondary metal to the active phase can change the electrical characteristics and adsorption behavior and the metal dispersion/particle size. Presently, supported Pd-based nanocatalysts are shown to be active for the dehydrogenation of aqueous FA
[48][54][55][56][53]. Adding Au or Ag to Pd NPs in an aqueous medium significantly enhances their stability and catalytic activity
[35][57][58][59][60]. The enhanced catalytic activity of bimetallic Pd-Au/C and Pd-Ag/C catalysts was attributable to the greater tolerance to CO poisoning of Ag and Au. The addition of CeO
2(H
2O)x increased catalytic activity even more because CeO
2 forms cationic palladium species with strong activity in CO oxidation
[61] and methanol decomposition
[62]. An alternative justification is that CeO
2(H
2O)x on the Pd surface can trigger FA breakdown via a more effective mechanism, resulting in less poisoning intermediates
[63].
3.3. Trimetallic Heterogeneous Catalyst
Trimetallic NPs have lately acquired increased attention, particularly in catalytic systems, because of their novel physicochemical features (e.g., catalytic, electrical, optical, and magnetic) which are caused by their monometallic counterparts’ synergistic effects
[64]. Yurderi et al. used a simple and repeatable wet impregnation followed by a simultaneous reduction method at room temperature to synthesize Pd-Ni-Ag (trimetallic nanoparticles) with various metal ratios, as well as their Pd-Ni, Ni-Ag, and Pd-Ag (bimetallic) and Pd, Ni, and Ag (monometallic) counterparts, loaded on active carbon
[65]. Under mild reaction conditions, all composites produced were used as nanoheterogeneous catalysts to break down FA.
4. Formic Acid Fuel Cells (DFAFCs)
FA’s hyper-gravimetric capability was recognized, and using FA as a secondary fuel in direct FA fuel cells (DFAFCs) was suggested and investigated
[66]. While DFAFCs suffer from significant problems, hydrogen fuel cells perform a role in a well-established technology that has been commercialized in fuel cell vehicles (FCVs) with outputs of over 140 kW and ranges of over 600 km. As a result, producing H
2 selectively from FA to power hydrogen fuel cells is a potential strategy with a speedy time-to-market. As a traditional fuel, energy discharge includes FA consumption, resulting in a massive release of CO
2 (
Figure 3).
Direct formic acid fuel cells work in the same way as other fuel cells. They create electricity by oxidizing FA and reducing O
2. FA and O
2 (or air) are supplied to the anode and cathode, respectively, in the electrochemical cell. Protons can pass across an electrolyte membrane
[67].
5. Formic Acid Production
Formic acid is a crucial component created from a variety of chemical molecules. FA is found in the venom of ants in nature
[68] and is emitted into the atmosphere as a result of forest emissions. Various chemical techniques can be used to prepare it. The most frequent industrial procedure is the synthesis of methyl formate from a mixture of carbon monoxide and methanol in the existence of a strong base at 80 °C and 40 atm, followed by hydrolysis of the methyl formate to yield FA
[69]. FA can also be synthesized as a by-product of acetic acid production, biomass oxidation, CO
2 hydrogenation and biosynthesis via carbon dioxide reduction mediated by the enzyme formate dehydrogenase
[70][71]. Despite the enormous progress that has been made in nano-chemistry and nanotechnology over the last two decades, and that forming FA from carbonates (primarily Pd-based) has been a subject of research for some time, few instances of supported metal catalysts at the nanometer scale for direct hydrogenation of carbon dioxide have been reported. These primarily involve Au, Pd, and Ru.
6. Conclusions
The benefits of a hydrogen economy are obvious, even if significant research is required to accomplish the essential technological advancements. Formic acid is an environmentally-benign hydrogen storage substance because of its easy storage and lack of poisonousness. Its production through dehydrogenation releases only gaseous products (H2/CO2). Interestingly, CO2 can be converted back to formic acid using catalysts under moderate conditions, resulting in a CO2-neutral hydrogen storage cycle. Noble metals, such as Au and Pd, can serve as nanoheterogeneous catalysts that work in aqueous formic acid solutions and ambient temperature (20–50 °C). The Pd nanoparticles are employed in most nanoheterogeneous catalysts used in the formic acid dehydrogenation process. However, chemical intermediates adsorb on the nanoparticle surfaces and deactivate Pd monometallic systems. The situation with heterogeneous formic acid decomposition catalysts is identical to that with homogeneous systems. While the activity and H2 selectivity have not yet been achieved homogeneous system levels and most heterogeneous systems tested still have some degree of decarbonylation activity, this gap is narrowing. The recent use of state-of-the-art nanoparticle synthesis techniques has resulted in a variety of high-performance catalysts, including bimetallic and trimetallic Pd and Au combinations that produce high-quality H2 with minimal CO concentration. The direct formic acid fuel cell (DFAFC) example marks significant progress toward prototype development, scale-up, and commercialization. Furthermore, CO2 may be converted back to formic acid using catalysts under moderate conditions, resulting in a CO2-neutral hydrogen storage cycle.
This entry is adapted from the peer-reviewed paper 10.3390/catal12030324