New synthetic hybrid materials, with an inorganic and organic nature, have been developed to promote their application as protective coatings and/or structural consolidants for several substrates in the construction industry and cultural heritage field. In this background, the scientific community paid attention to geopolymers and their new hybrid functional derivatives to design and develop innovative and sustainable composites with better chemical resistance, durability and mechanical characteristics.
1. Introduction
The preservation and restoration of cultural heritage is considered by modern society to be a great responsibility toward future generations. This is due to the continuous damage and deterioration of artworks and monuments caused by the increasing air pollution in industrialized areas
[1]. Although many monuments and works of art require minimal restoration interventions, most historic buildings and archaeological finds show conservation problems that need primary renovation operations. In the current practice, the restoration processes are guided by preliminary diagnostic analyses on the artworks under study, in order to discover materials with characteristics as similar as possible to those of the historical finds
[2][3]. Compatible products are chosen based on their comparable physico-chemical and mechanical properties and their similar aesthetic characteristics. Moreover, other different factors can influence the choice of the restoration material, such as thermal resistance, adequate ductility, low creeping and penetration ability, in addition to suitable mechanical properties to decrease the risk of collapse phenomena
[4]. In the last decades, new synthetic materials have been developed to promote their application as structural consolidants and protective coatings for different substrates, such as ceramic, wood, steel, concrete walls, textiles, and paintings. Furthermore, these inorganic or organic materials are used to restore historical and cultural interest assets, as well as being employed in the modern and sustainable building and architectural engineering sector
[5]. In this scenario, the attention toward geopolymers arises from the interest in creating and developing innovative materials with better chemical resistance, and mechanical and durability properties
[6]. Geopolymers are aluminosilicate-based amorphous inorganic materials obtained through a polymerization process, starting from natural or waste materials with a high content of aluminum or silicon, such as slag from blast furnaces from steel mills, clays, flying and volcanic ashes or other aluminosilicate sources, such as laterite deriving from tropical areas, which offers acceptable mechanical properties to geopolymerization products
[7][8][9][10][11]. The reaction of the precursor powder with an activating alkaline solution, consisting of sodium and/or potassium hydroxides and silicates, at a temperature below 100 °C, produces this alkali-activated material, which is the amorphous analog of the zeolite. Geopolymer studies, nowadays, have considerably grown since their extensive use in many applications and industrial fields
[7][8][12]. These applications are found in the automotive and aerospace industries, non-ferrous foundries and metallurgy, civil engineering, cements and concretes, ceramics and plastics industries, waste management, retrofit of buildings, and, as already mentioned, in art and decoration
[13]. As concerns their use as cement and concretes, the main present challenge is to produce new structural materials or optimize the existent ones with reducing consumption during production, the emission of greenhouse gases and environmental impact
[7][14]. Moreover, ordinary concretes show disadvantages, such as low thermal and fire endurance, little chemical resistance against acids and salt and significant worldwide carbon dioxide emissions
[15]. Therefore, as a source of innovation in the engineering field, alternative construction materials are constantly being developed and tested by the academic and scientific community.
According to Provis and van Deventer
[16], Pudron was the first to show the synthesis of building materials using alkaline activation starting from high-calcium blast furnace slags. However, the interest in this new technology began to mature in the 1950s when Glukhovsky demonstrated, through an investigation on ancient Roman and Egyptian structures, the possibility of preparing new materials through the reaction of aluminosilicate raw materials with solutions containing alkaline compounds, such as carbonates, hydroxides, and silicates
[17]. However, geopolymers were developed only in 1976 with the findings of the French engineer Joseph Davidovits, who patented several aluminosilicate formulations
[13][18].
In 1997, Krivenko named these binders “geocements”, since the formation and features of their hydration products were similar to those of some natural minerals
[19]. From the first Davidovits patent to the present day, the interest in these materials has greatly grown, especially since the early 21st century, with a relative increase in scientific publications and conferences on this topic. Several alkaline activation studies deal with the chemical reaction between a solid aluminosilicate precursor and an alkaline activator, at room temperature, resulting in a robust composite
[20]. These materials can be used in high-performance concretes and in ceramics strengthened with fibers, with features that are comparable or even higher than ones related to the conventional Portland cement or other composite materials produced by traditional techniques. Granulated blast furnace slag (from the steel industry), fly ash (from coal combustion) and natural clays (metakaolin and haloysite or kaolinite fired at 700 °C), since their low cost and availability, are employed as main precursors for producing alkali-activated materials
[21][22][23][24], even if their production process allows to obtain a non-homogeneous products, which could cause problems in the geopolymer synthesis
[16]. At this time, volcanic tuffs are the best materials for producing geopolymer cement
[16][25]. Another problem linked to the synthesis is the alkali activation of the alumina–silicate precursors, whose process was not fully described yet. As previously mentioned, alkali-activated materials have shown excellent eligibility to preserve and restore ancient and modern constructions. According to their reaction conditions and composition, especially precursors, these materials can be versatile and easily adaptable on site
[26].
Nevertheless, geopolymers are featured by scarce rheological properties due to their low viscosity, making them almost inapplicable in restoration works mostly of vertical buildings
[9][27]. To overcome this problem, researchers have recently tried to improve the chemical, physical and mechanical properties of these compounds by formulating hybrid organic–inorganic systems. These new binders, consisting of geopolymers with an organic component, are synthesized through a cross-link reaction between the inorganic phase and the organic one, such as polysiloxane oligomers, alkoxysilane agents or epoxy resin precursors
[5][28][29]. The functionalization of the alkali-activated material with the organic component improves the system’s performance, as it allows an increase in the mixture’s viscosity, making the hybrid material more versatile in architectural and artistic restoration
[28][30]. The synthesis process of these hybrid materials occurs via the sol–gel method, which is generally employed to produce a wide variety of materials, from inorganic glasses to organic–inorganic compounds, such as the ones described above
[5][30]. Through this method, which allows producing multi-component materials, it is possible to obtain compounds that show peculiarities deriving from the synergy of the two components having different nature, rather than from the addition of individual contributions
[5][28].
2. Synthesis of Functional Geopolymeric Hybrid Materials
For over 30 years, the study of organic–inorganic hybrid materials has aroused enormous interest in academia and industry. The synthesis mechanism can be described as polymerization or insertion into the inorganic matrix of nanoparticles or organic molecules, such as alkoxides, polysiloxanes and, more generally, polymeric precursors that can lead to a polycondensation
[31]. The great attention in these multifunctional hybrid materials is associated with their peculiar chemical and physical properties deriving from the synergistic interaction between the organic and inorganic moiety, which does not depend on the simple sum of the individual contributions, but on the formation of a broad hybrid interface
[31][32]. These organic–inorganic systems play a crucial role in developing and improving several features for the newly created material, such as mechanical, optical, chemical and thermal properties. These complex systems can be divided into two groups based on the interface nature, named class I and class II materials, respectively. The first ones are characterized by weak interactions between the components, such as Van der Waals forces and hydrogen bonds. The second ones are featured by strong interactions at the interface with covalent or ionic bonds. These hybrid materials can be processed employing several engineering methodologies, such as spin coating, dip coating, micro-emulsion, extrusion, aerosols and printings, which can lead to complex systems with different forms (thin films, foams, fibers, powders and monoliths), based on the type of use that they undergo.
The synthesis of these complex systems can follow different routes: (i) the intercalation of an organic precursor into an inorganic matrix previously formed (e.g., insertion in clays or aluminosilicates, such as geopolymers or the handling of the inorganic compound, after drying, by applying a sol–gel dispersion on the monolith surface); (ii) the dispersion of an inorganic compound in a polymeric matrix; and (iii) the concurrent polymerizations of the inorganic and organic phase, which lead to a co-reticulation process with the formation of a hybrid network (e.g., the addition of alkoxysilane reagents in a geopolymeric matrix, such as (RO)
4Si or (R’O)
3SiR)
[5][32]. In more detail, the first method, also known as grafting, can be developed using organosilanes, RSi(R’O)
3, silazanes NH(SiR
3)
3 or chlorosilanes SiR
3Cl reactions with free silanol groups present on the inorganic component surface
[33]. This route shows advantages, such as the ability to retain the initial siliceous structure and the diminution of the porosity of the hybrid material, which depends on the size of the organic components. Nevertheless, the organic fractions are more evenly arranged in the simultaneous polymerization process of the inorganic and organic phase than in the grafting one
[33]. In
Table 1, the most recent studies on functionalized geopolymers are listed.
Table 1. Organic–inorganic hybrid geopolymers present in literature.
Inorganic Substrate |
Organic Agent |
Ref. |
Metakaolin-based geopolymer |
(3-Aminopropyl)triethoxysilane (APTES) |
[34] |
Geopolymer concrete waste |
Vinyl trimethoxy silane (VTP) + recycled polypropylene (rPP) |
[35] |
Metakaolin-based geopolymer |
Polypropylene fiber (PP), polyvinyl alcohol fiber (PVA) |
[36] |
Metakaolin-based geopolymer |
Unsaturated orthophtalic polyester resin |
[37] |
Metakaolin-based geopolymer |
polyacrylate |
[38] |
Fly ash- based geopolymer |
Oligomeric dimethylsiloxane |
[32] |
Kaolin-based geopolymer |
Methyl-polysiloxane (MK), methyl-phenyl-polysiloxane (H44), tetraethyl-ortho-silicate (TEOS) and 3-amino-propyl-triethoxysilane (APTES) |
[39] |
Metakaolin-based geopolymer |
Polyurethane powders wastes (polyurethane foam and polyisocyanurate foam) |
[40] |
Metakaolin-based geopolymer |
Commercial oligomeric dimethylsiloxane mixture and epoxy resin |
[28] |
Fly ash-based geopolymer |
Organic molecules deriving from the decomposition of rice husk: D-glucose, native cellulose, phenolic compounds and sucrose |
[41] |
Metakaolin-based geopolymer |
Polyethylene glycol (PEG) |
[42] |
Metakaolin-based geopolymer + sepiolite |
Methylene blue (MB) and methyl red (MR) |
[43] |
Metakaolin-based geopolymer |
Polyethylene (PE) |
[44] |
Metakaolin-based geopolymer |
Commercial epoxy resin |
[29] |
Metakaolin-based geopolymer |
Epoxy resins formed by N,N-diglycidyl-4-glycidyl-oxyaniline with bis-(2-aminoethyl)amine and N,N-diglycidyl-4-glycidyl-oxyaniline with bis-(2-aminoethyl)amine and 2,4-diaminotoluene) |
[45] |
Metakaolin-based geopolymer |
Polyethylene glycol (PEG) |
[46] |
Kaolin-based geopolymer |
Epoxide matrix constituted by bisphenol a diglycidyl ether |
[47] |
2.1. Functionalization by Sol–Gel Technique
The sol–gel technique is widely employed in developing hybrid geopolymeric based materials
[5][48][49][50][51]. Moreover, as it is well known, this process is one of the primary approaches for manufacturing ceramic materials and glasses at low temperatures
[52].
The main goal of this method is to control the surface and interface of the designed materials during the first step of their production. It is also considered an effective coating process
[53]. The most relevant feature of the sol–gel technique is the ease of homogeneously coating the entire surface of different materials, which find employment in various industrial fields, such as optical and sensing applications or powder synthesis of raw materials used as precursors in innovative concrete formulations
[53][54][55][56][57][58][59]. Moreover, micro and mesoporous ceramics obtained through this method are widely employed in extraction technology, such as waste removal and drug delivery
[60][61]. Nevertheless, sol–gel systems are affected by a low process rate, which can cause cracks inside the solidified gel
[53]. Three ways allow to obtain a monolith from the sol–gel method: (a) gelation process starting from a colloidal solution; (b) hydrolysis and polycondensation reactions using alkoxides as precursors, such as Si(OR)
4, where R is an alkyl chain, with hypercritical drying; (c) hydrolysis and polycondensation reactions, using alkoxides as precursors with drying at room temperature
[62][63]. In more detail, the synthesis route of a monolith through this method consists in mixing the precursor materials in the liquid phase, with the consequent development of hydrolysis and polycondensation reactions, which lead to the formation of a low viscosity sol inside the solution. After that, a series of polycondensation reactions occur, forming a three-dimensional network structure gel with a continuous inorganic lattice containing an interconnected liquid phase, which will become a xerogel with a porous space structure after removal of the solvent by a drying process
[59]. A schematic example of the sol–gel mechanism is shown in
Figure 1.
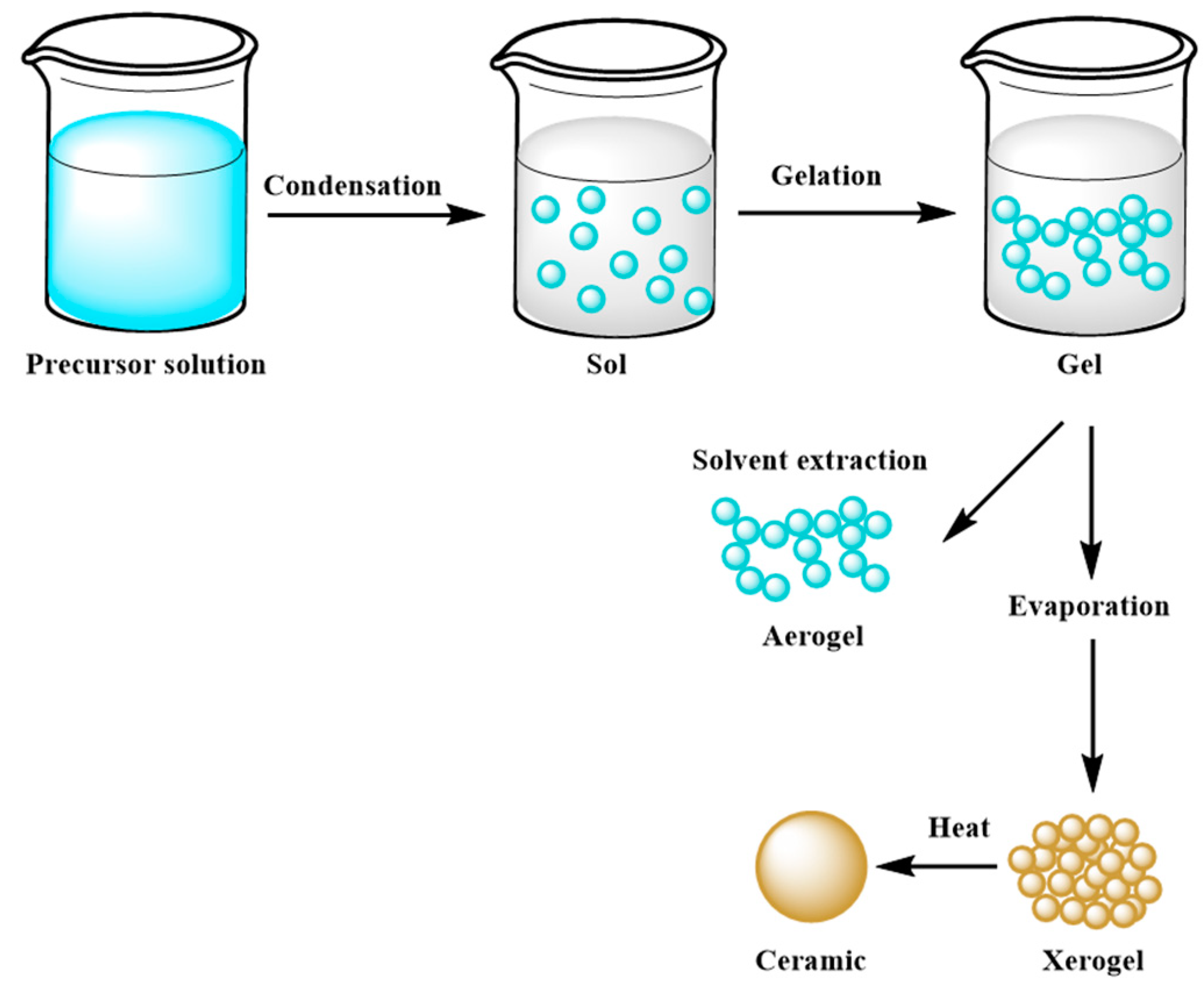
Figure 1. Scheme of the sol–gel mechanism.
2.2. Functionalization with Nanoparticles (NPs)
Recent studies showed that the addition of nanoparticles to the geopolymer matrix improves the chemical–physical, mechanical and structural characteristics of the alkaline-activated products. Nanomaterials can create intelligent materials with improved rheological and mechanical properties, thanks to their small size and high surface-to-volume ratio
[64]. The addition of these agents, such as nano-silica, nano alumina, TiO
2, ZnO and graphene oxide, plays a key role in the consolidation of the innovative material, acting as nanofillers, and leading to a reduction of the inner water together with an increase in the compressive strength
[65][66][67][68][69][70]. Recently, a study investigated the effect of a geopolymer treated with Al
2O
3 and multi-walled carbon nanotubes (MWCNT) functionalized with hydroxyl groups
[64].
The results reported by Alvi et al. showed an enhancement of the mechanical properties in the treated product compared to the neat one, as the addition of these nanomaterials provided a more malleable structure with higher compressive and tensile strength
[64]. Furthermore, as reported in
Figure 2, the functionalization of the material under study was possible, thanks to forming a hydrogen bond between the hydroxyl group of the MWCNT and the oxygen atoms of the geopolymer 3D structure.
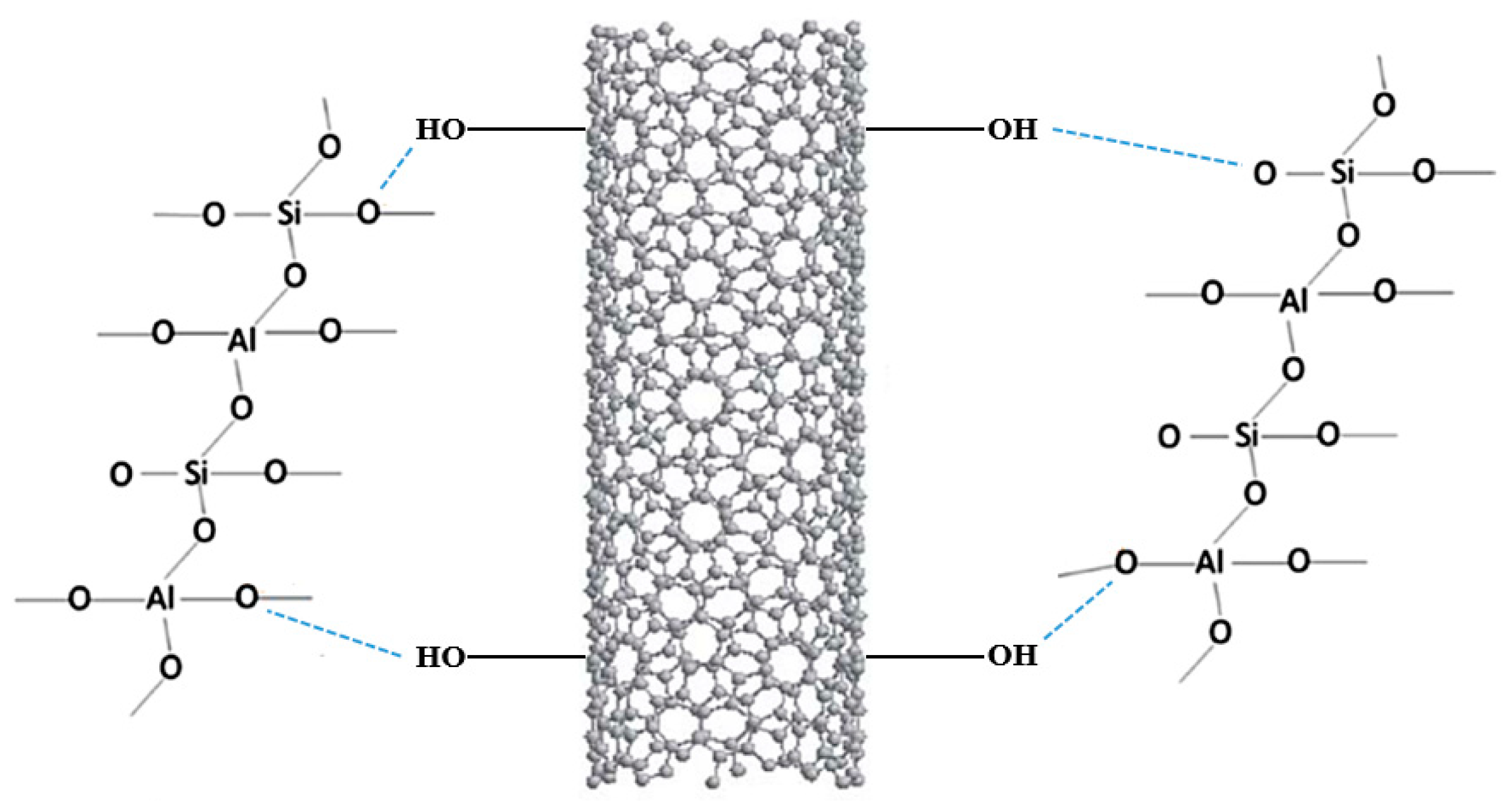
Figure 2. Scheme of the sol–gel mechanism.
3. Conclusions
In the last decades, geopolymer mortars have captured the attention of an increasing number of researchers because of their particular features and potential application in many industrial fields, particularly as a good sustainable alternative to cement. In particular, since the development of unconventional and eco-friendly materials in substitution of the Portland cement has become a crucial research line worldwide, geopolymers production seem to play a crucial role in order to reduce the pollution of gas emissions and provide significant energy savings. Nevertheless, although the growth made on these new alternative materials has improved in recent times, thanks to their potential employment in many applications and to their different advantages (i.e., sustainability, simple synthetic procedures, and improvement of their surface properties by proper functionalization techniques), their performance and the factors affecting them are still unclear.
Here is intended to provide a comprehensive summary starting from these alkaline-activated materials to their hybrid compounds functionalized with organic compounds, polymeric matrices and nanoparticles, focusing on purposes in the cultural heritage field and building application fields. In particular, focusing initially on the development, the composition, the polymerization reaction mechanism and the influencing factors of performance of the developed geopolymers, herein offers an overview of new functional geopolymeric matrix and hybrid sol–gel or opportune nanomaterials used to improve their potential hydrophobic, anti-abrasive, antibacterial and antifouling properties. Pre-treatment methods are aimed at improving the mechanical and physical properties of the geopolymer; the matrices mentioned above mainly include chemical agents, such as sodium or potassium hydroxide (NaOH, KOH), sodium silicate (Na2SiO3), silane and alkoxysilane agents, and metal nanoparticles. Furthermore, the combination of matrix pre-treatments, such as hardening before polymer coating, show synergistic effects on cementitious composites. The reinforced geopolymer materials generally show promising structural performance, such as interface strength, thermal stability, and improved mechanical properties.
Moreover, the influence of the alkaline agent in terms of concentration and the different raw materials used as precursors on the properties of the geopolymer, such as compressive strength and hardness of the synthesis product obtained, is also discussed. In fact, a key role in the preparation of geopolymer binders is played by the nature and the dosage of alkali activators, which show a significant effect on the hydration, microstructure, and performance of these new mortars, and still represent the only non-sustainable factor and disadvantage in the geopolymerization process. However, further studies on their chemical and physical properties are needed to develop materials with greater mechanical strength and longer life.