Process intensification (PI) is defined as an innovative principle applied in chemical reaction engineering and process design. The first definitions were given in 2000, when the pioneering work of Stankiewicz and Moulijn began this means of novel enthusiastic definition of chemical processes, which can bring significant benefits in terms of process and efficiency, higher quality of products, lower capital and operating expenses, less waste, and improved process safety. Starting from that moment, several roadmaps, books, and scientific papers were published in the field, focused on PI in the chemical industry.
1. Overview of Strategies for PI
Efficiency in terms of atoms, mass and energy, along with process profitability, mainly depend on the selection of a proper chemical transformation, a suitable catalyst, and a favorable reactor type. More active and long-term stable catalysts are one route for significant improvement. For a synthesis with an already optimized catalyst, the productivity and selectivity of the process can be remarkably affected by the choice of the reactor type and operating conditions, because thermodynamic equilibrium as well as reaction kinetic properties are fixed in this case. Although the reactor typically represents only 5% to 15% of the capital and operating costs of the plant, it mainly dictates the number of up- and downstream process units, and therefore the costs and efficiency of the whole process
[1][2]. For improvements in reactor technology, chemical reaction engineers have focused on the integration of multiple unit operations in one apparatus, enhanced transport properties, and alternative process fluids and energy sources
[3].
Van Gerven and Stankiewicz (2009)
[4] provide four guiding principles for PI:
-
Maximize the effectiveness of intramolecular and intermolecular events (example: dynamically changing conditions to attain kinetic regimes with higher conversion and selectivity).
-
Provide all molecules the same process experience (example: plug flow reaction with uniform, gradientless heating).
-
Optimize driving forces at all scales and maximize the specific surface areas to which they apply (example: increase transfer surface area through microchannel designs).
-
Maximize synergistic effects from partial processes (example: multifunctional reactors).
The principles and the main concepts are accepted worldwide, and are today considered common practice and theory. The four principles above lead to practical application. Changing the structure of a conventional reactor means focusing both on the catalyst and on the reactor’s shape and dimension. The synergy between chemical reaction and separation unit leads to the design of more compact and cheaper plants, reducing the amount of equipment and thus simplifying the control systems of the chemical plant. The pursuit of novel energy sources leads to more efficient mixing and heating systems, allowing for optimal heat and mass transfer properties. Alternative time use and optimization can be reached by implementing dynamic operations or using alterative fluids that enhance the global conversion of a reaction network.
A summary of the main idea, including the four principles and their means of application, is shown in Figure 1.
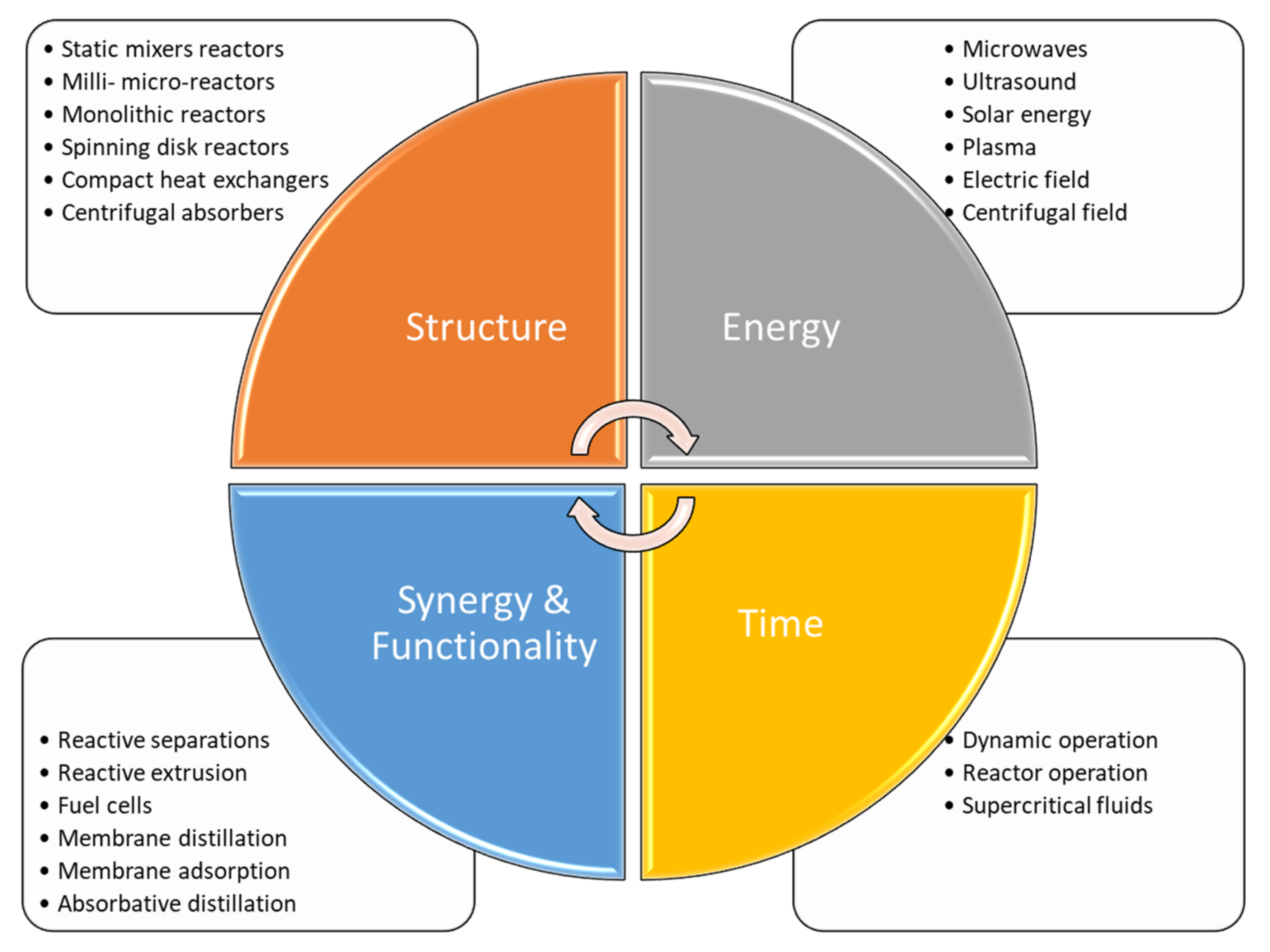
Figure 1. Principles of Process Intensification: definition of the main concepts of PI with application examples, adopted from
[4][5].
Starting from these concepts, Process Intensification allowed for the opening of
Novel Process Windows, making possible the achievement of process performances in terms of conversion, selectivity, and safety issues
[6]. As reviewed by Illg et al.
[6], it is possible to achieve good performances for reactions characterized by strong limits (e.g., high exothermicity, low miscibility of the reactants) by going beyond the classical protocols and applying PI concepts, permitting excellent mixing and thermal control when using milli- and microreactors. This aspect clearly led to the possibility of working in harsh conditions with respect to the element of safety; for instance, explosive conditions that cannot be achieved in a conventional apparatus (e.g., Kolbe–Schmitt synthesis or the bromination of 3-nitrotoluene
[6]), as well as the development of one-pot processes, reducing waste compared to classical methods for the synthesis of chemical intermediates (e.g., synthesis of phenyl boronic acid
[7]). Fast reactions can be handled and studied, as residence times can be on the order of magnitude of milliseconds; thus, it is possible to achieve very precise kinetic information to optimize the chemical process.
Writing a review article on PI is a rather difficult task today, as several books and reviews have been published already. Therefore, the aim of this paper is to give the reader both the basic tools of PI, including definitions and the explanation of the primary strategies. Moreover, an evaluation of intensification potential, including guidelines to help a chemist to choose an intensification pathway, are be reported here as well. The review is accompanied with PI examples; it must be remembered that the application examples reported within this review article are only a small selection of chemical processes, as the volume of PI literature is exploding in the most recent years. The main trends can be seen in the Scival Analysis shown in Figure 2.
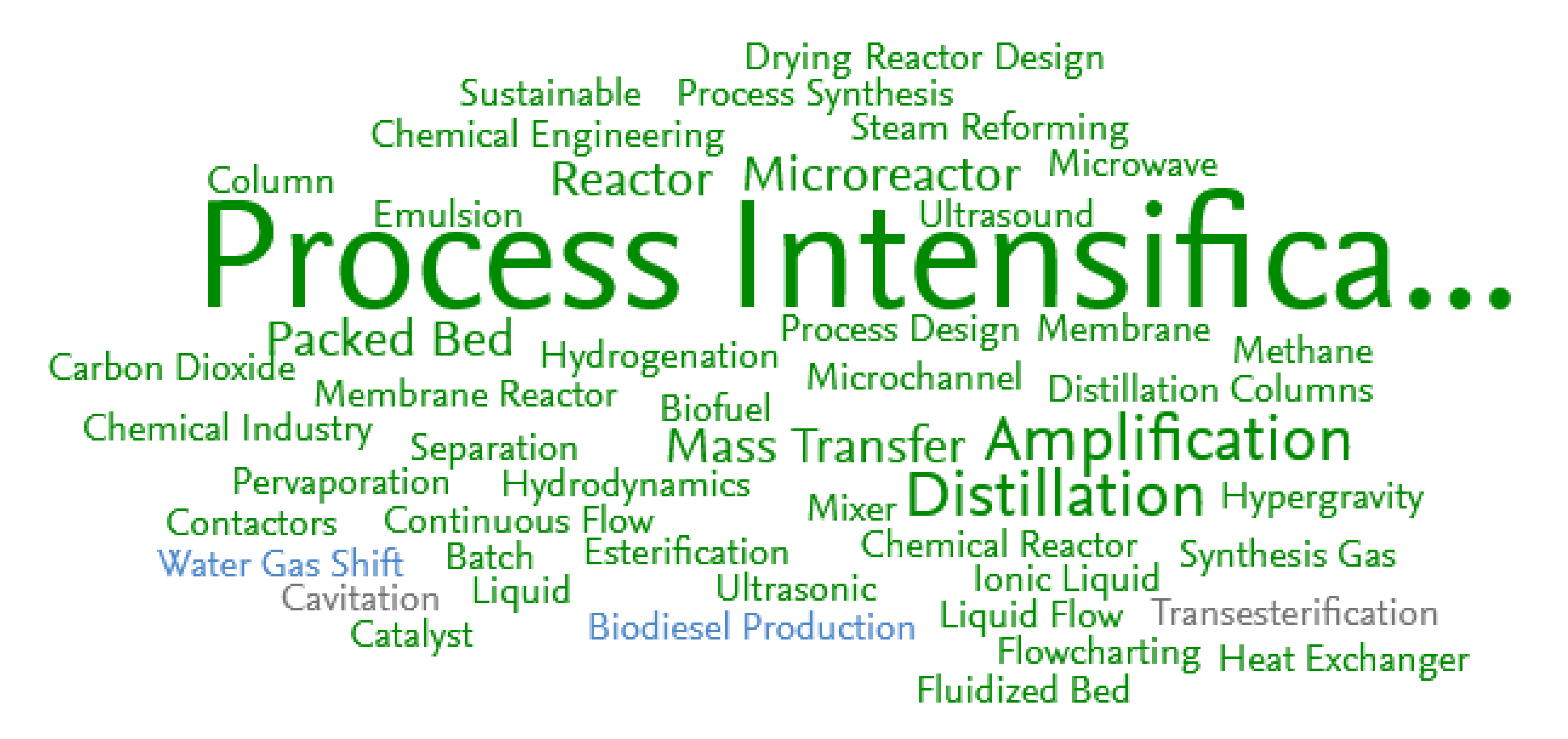
Figure 2. Scival Analysis trends obtained using Process Intensification as keyword.
As revealed, the trends are very clear, suggesting that researchers are exploring PI alternatives in every field of chemical reaction engineering, starting with reactor design and including, among others, mixing science, catalysis, unit operation design, and alternative energy sources.
2. Process Intensification: Potentials and Guidelines
In this paragraph, the potential of the PI strategies described in the previous section will be described and discussed. Moreover, some guidelines are provided to help the researchers choose between the different available options for intensification of a given chemical process.
In Table 1, the main benefits and drawbacks of the different PI strategies are reported, together with some common application areas. This table may be of interest for a reader who is starting his or her scientific journey in the field of PI.
Table 1. Main benefits and drawbacks of different PI strategies and potential application areas.
PI Strategy |
Pros |
Cons |
Application |
Equipment |
Miniaturisation and structurisation |
- –
-
Alternate packings may be integrated in existing reactors
- –
-
Additive manufacturing enables tailoring the packing according to the process needs
- –
-
Enhanced temperature control
|
- –
-
No industrially-proven catalysts available
- –
-
Challenging phase distribution if radial mixing is suppressed
- –
-
Elevated blocking risk
|
- –
-
- –
-
Ethylene oxide synthesis [9]
- –
-
Alcohol oxidation to aldehydes [10]
|
Integrated mixing elements |
- –
-
Alternate packings may be integrated in existing reactors
- –
-
The eventually costs is rather cheap
|
- –
-
Lowering the volume of the reactive unit, leading to lower residence times per reactor volume
- –
-
Temperature control if the elements are non-conductive
|
- –
-
Biodiesel synthesis [11][12]
- –
-
|
Multifunctional reactors |
- –
-
Two operations in one unit (reaction and separation)
|
- –
-
Difficult to design and model
- –
-
Unit control is crucial
|
- –
-
Levulinic acid esterification [14]
- –
-
|
Energy |
Microwave |
- –
-
Enhancing mass transfer between phases
- –
-
Rapid, selective heating/hot spots
- –
-
Extraction processes
- –
-
Low heating eventually costs
|
- –
-
The equipment has intrinsic risks
- –
-
Scale-up cumbersome
- –
-
Not applicable to every fluid
|
- –
-
Rapid synthesis of catalysts [16]
- –
-
Rapid HMF synthesis from glucose [17]
|
Ultrasound |
- –
-
Enhancing mass transfer between phases
- –
-
Can be an inexpensive, simple, and efficient alternative to conventional extraction techniques, especially with solids
- –
-
Excellent for cleaning, i.e., of catalyst surfaces
|
- –
-
Not applicable to every fluid
- –
-
Effect of ultrasound waves varies depending on transmitter position
- –
-
Scale-up cumbersome
|
- –
-
Ultrasound Biodiesel production [18]
|
Plasma |
- –
-
Mild operating conditions
- –
-
Unique advantages in activating inert molecules
|
- –
-
Cost of the equipment
- –
-
May lack selectivity as it can produce a diversity of activated species, radicals, and ions
|
- –
-
Dry reforming of Methane [19]
- –
-
Cleaner ammonia production [20]
|
Operation |
Dynamic/transient operation |
- –
-
Implementable without changes in catalyst and reactor
|
- –
-
Complex process control required
- –
-
Phase composition may vary at reactor outlet
|
- –
-
|
Alternate fluids |
- –
-
The operation can be conducted potentially in one liquid phase (if heterogeneous catalyst is not used)
- –
-
High reaction rates due to the high local concentration
|
- –
-
Conditions far from room temperature and pressure
- –
-
eventually costs of the alternative fluid (if Ionic Liquids)
- –
-
Separation of the fluid (if Ionic Liquids)
|
- –
-
- –
-
|
The main benefits were already discussed in the previous paragraph; thus, it may be worthwhile here to underline some important drawbacks of these operations.
Miniaturized and structured systems seem to be the best alternative in PI, as they allow to work in ideal conditions in terms of fluid dynamics, allowing achievement of high selectivity and low chemical risks and reducing operation volumes. Therefore, operation is difficult to scale at industrial level, as numbering up is an expensive procedure due to the high price of a single reactor. Moreover, there is an elevated blocking risk as microchannels can be blocked by even small traces of microparticles contained in the reactant vessels.
Static mixers are easy to be set up, as the operation consists of packing a standard pipe. Therefore, even if good mixing can be achieved the reactor volume can decrease dramatically, leading long pipes to achieve the reasonable residence times needed for operation.
Multifunctional reactors are very efficient when selectivity problems are the main issue in the process; however, their operation can be expensive and sophisticated in terms of process control. Membranes are usually expensive, and must be maintained and replaced frequently overall when the reaction leads to heavy byproducts. A simulated moving bed needs a sophisticated control logic to control the switch between the feed and withdrawal positions.
MW, US and Plasma are very good options when thermal control is an issue; therefore, the equipment is expensive and characterized by an intrinsic risk, i.e., exposure to irradiation, which requires additional attention to the management of the chemical plant.
Dynamic operations are useful to optimize product selectivity; however, complex process control is required to ensure reproducibility; thus, phase composition may vary at the reactor outlet from test to test, which must be avoided during the operation of the industrial plant.
Alternative fluids are well-suited to replace standard solvents, and ensure high mixing of reactant and products as well as their subsequent separation. Therefore, these liquids are often very expensive, and their recovery and relayed purification is a major issue.
A second question to be answered is how to choose between the different PI strategies. In Table 2, the most frequently encountered process limitations and the suitability of different PI strategies are reported. This table can be considered a conceptual map where the reader should detect the correct PI strategy once the limitations of the chemical process of interest are defined.
Table 2. Commonly-encountered process limitations and suitability of different PI strategies.
PI Strategy |
Limitations by |
Reaction Kinetics |
Internal Mass Transfer |
External Mass Transfer |
Product Selectivity |
Process Complexity |
Thermal Control |
Mixing |
Equipment |
Miniaturisation and structurisation |
X |
X |
X |
X |
|
X |
X |
Integrated mixing elements |
X |
|
X |
X |
|
X |
X |
Multifuctional reactors |
|
|
|
X |
X |
|
|
Energy |
Microwave |
|
|
|
|
|
X |
X |
Ultrasound |
|
|
|
|
|
X |
X |
Plasma |
|
|
X |
|
|
X |
X |
Operation |
Dynamic/transient operation |
X |
|
X |
X |
|
|
|
Alternate fluids |
|
|
|
|
X |
X |
X |
5. Conclusions
There is no a single choice, nor a simple choice, to intensify a chemical process. The PI strategy must be tailored to the chemical and physical application by investing time, passion, and energy in trying to find the best solution to achieve the PI goal. Possible alternatives, routes, and strategies are numerous, and new technologies will definitely emerge along with the need to reducing energy and loss of resources. Herein have summarized the main definitions and the strategies for PI in an attempt to provide order to the enormous literature published on this topic to date.
This entry is adapted from the peer-reviewed paper 10.3390/pr10010099