Lithium-ion batteries (LiBs) with high energy density are receiving increasing attention because of their environmental friendliness and are widely used in electric vehicles (EVs) worldwide. Battery degradation problems, such as capacity fading and internal resistance increasing, inevitably occur with time and use. These cause great trouble to users and manufacturers.
1. Introduction
A clear understanding of how batteries age in EVs is urgently needed to: (i) optimize the battery materials, (ii) improve battery cell production, and (iii) guide the design of automotive battery systems.
At present, scientists from different fields have researched, from different perspectives, the aging of LiBs. Some scientists specifically discussed the impacts of environmental and operational factors on battery degradation [1], while others studied the battery aging mechanism through the post-mortem analysis of the internal components of the battery cell [2]. However, a close connection between the battery operation and degradation in EV applications and the corresponding aging mechanism has not yet been established. Thus, a review is necessary in order to systematically and comprehensively describe the aging of LiBs in EVs.
Many reviews on battery aging have been published presenting the battery degradation and aging mechanisms. The main contents of these reviews are summarized in Table 1 . These reviews are mostly based on analyzing laboratory accelerated aging test results, which are mainly obtained using constant charging/discharging current and are significantly different from the battery operation in EVs. Besides, most of them lack the connection with the battery operation scenarios, and focus only on the degradation behavior of the battery itself; in reality, the influential factors on battery charging, discharging and standby are different, and aging should be described independently based on the operation status. Moreover, the battery chemistries reviewed in these works mainly involved stable LiCoO 2 and LiFePO 4, which are more stable and mature and are not considered to be state-of-the-art technology for EVs. Therefore, the aging mechanisms of widely EV-used Ni-rich battery chemistries ( LiNi 1− x M x O 2 , M = Co, Mn and Al. (NMC) and (NCA)) need further study.
Table 1. An overview of the published literature related to battery aging.
References |
Topic |
Chemistries |
Operation |
Degradation |
Aging Mechanism |
Han et al., 2019 [3] |
|
√ |
√ |
LMO, LCO, LFP, NMC |
Tian et al., 2020 [4] |
|
√ |
|
LMO, LFP, NMC |
Mocera et al., 2020 [5] |
|
|
√ |
LFP |
Woody et al., 2020 [6] |
|
√ |
√ |
LCO, LMO, LFP, NCA, NMC |
Vetter et al., 2005 [7] |
|
|
√ |
LCO, LMO, NMC |
Broussely et al., 2005 [8] |
|
|
√ |
LCO, NMC |
Barre et al., 2013 [9] |
√ |
|
√ |
LCO |
Birkl et al., 2017 [10] |
|
√ |
|
LCO |
Palacin et al., 2018 [11] |
|
|
√ |
LMO, LCO, NMC, NCA |
Xiong et al., 2020 [12] |
|
√ |
√ |
LFP, NCA, NMC |
Teichert et al., 2020 [13] |
|
√ |
|
NMC |
Alipour et al., 2020 [14] |
|
√ |
√ |
LCO, LFP, NMC, NCA |
Chen et al., 2021 [15] |
√ |
√ |
|
LCO |
Yang et al., 2021 [16] |
√ |
√ |
|
NMC, NCA |
2. Aging on Lithium-Ion Batteries
2.1. Aging at the Cathode
Changes in the cathode, such as phase transition, cracking in particles, transition metal dissolution (TMD), CEI film formation, binder decomposition, and loss contrast with collector have an evident influence on the aging of LiBs
[3][6].
The loss of active materials on the cathode is a common aging process and is reflected in many aspects. The cathode structure is prone to changes during both standby, charging and driving aging
[10]. Especially in high current rate operations, many Li
+ achieve intercalation or de-intercalation from the cathode in a short time, which influences the irreversible disorder phase transition in the cathode structure. Even worse, battery long-term cycling under high voltage or high current will lead to cracks in the cathode material. The generated fractures hinder the diffusion of Li
+ and lead to severe capacity fade
[17]. Furthermore, the appearance of cracks will result in an unstable structure of the cathode, which by prolonged cycling, will further cause powdering and collapse of the cathode materials
[18]. If the cracks are distributed inside the cathode, the diffusion of Li
+ is difficult to achieve due to the lack of contact with the electrolyte, this may result in some cathode materials being in an “isolated” state. Moreover, the battery operation at a high voltage (at high SOC level) or high environment temperature will accelerate the dissolution of the transition metal (TMD), especially for the Mn element, which dissolves in organic solvents, producing water and HF
[19]. The produced HF continues to dissolve the transition metals and the Li
+ on the surface of the cathode, leading to significant capacity fade
[20].
The loss of the Li
+ in the cathode is mainly attributed to the formation of the cathode-electrolyte interface (CEI) film. The CEI film, which is similar to SEI film, consists of lithium alkyl carbonates, lithium alkoxides (ROLi), Li
2CO
3, etc.
[21]. These compounds result mainly from the side reaction between cathodes and electrolytes. Operation of the battery at a high voltage (SOC) will accelerate the decomposition of electrolytes and produce more HF which erodes the cathode, resulting in more CEI ingredients
[19]. Furthermore, when the battery is in charging and driving with high current rates, the side reactions will also be enhanced because large currents increase the temperature significantly. The electrolyte is easily decomposed at high temperatures, and this will accelerate CEI production
[22]. Operation at high temperatures will also lead to binder decomposition and the current collector dissolution. The degradation of the binder will lead to the structure of the positive electrode being unstable, as a loss of contact in the electrodes results in an internal resistance rise in battery
[23].
All these main degradation mechanisms, corresponding to the cathode, are presented in Figure 13.
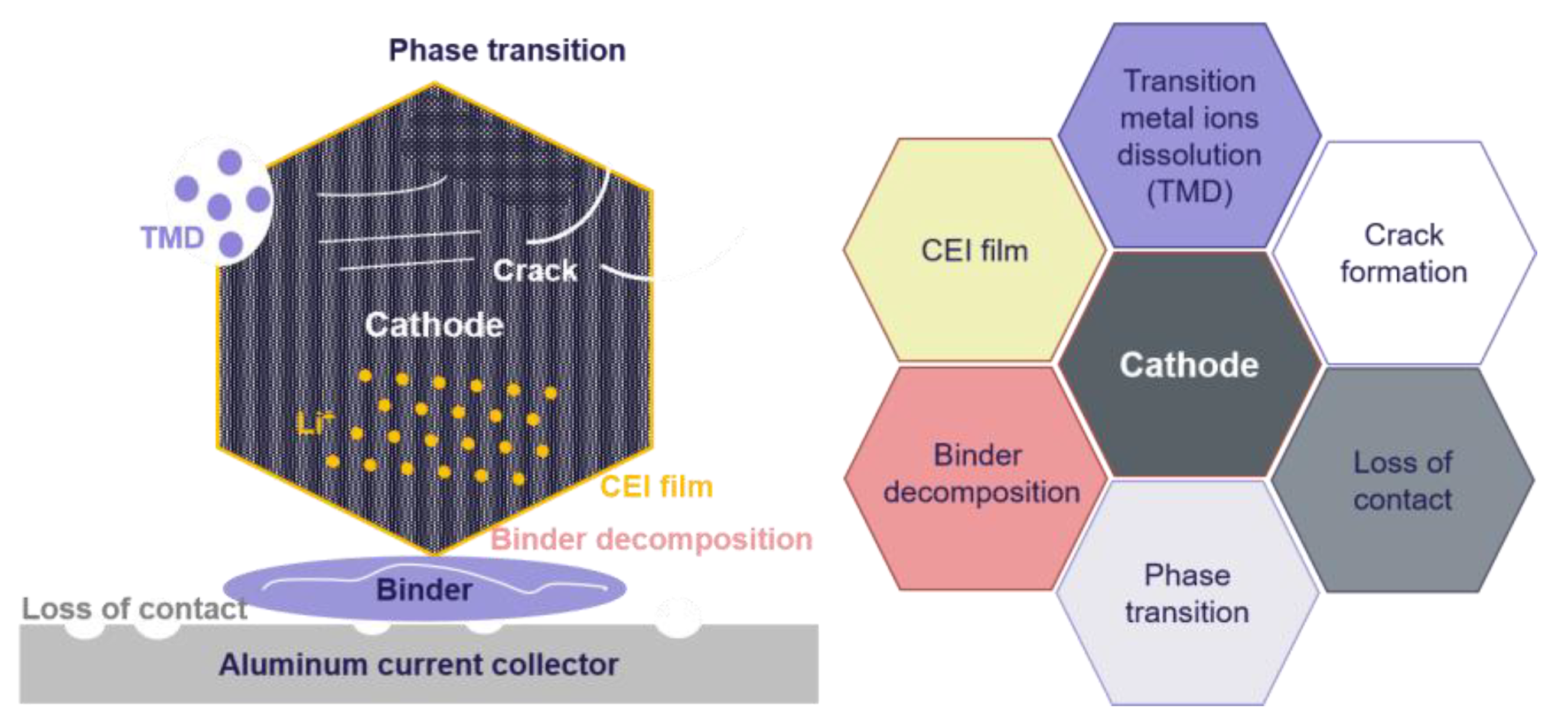
Figure 13. The main degradation mechanisms at the cathode of a lithium-ion battery.
2.2. Aging at the Electrolyte
The electrolyte transports Li
+ between the cathode and anode, and it is an important part of LiBs. The cycle stability, capacity, safety, and operating condition of LiBs are dependent on the electrolyte
[24]. Conventional electrolytes usually consist of lithium hexafluorophosphate (LiPF
6) and other organic carbonates, such as ethyl methyl carbonate (EMC), dimethyl carbonate (DMC), and diethyl carbonate (DEC).
The LiPF
6 is not stable, and it can be easily decomposed into LiF and PF
5 [25]. The electrolyte aging starts with the reaction of organic carbonates and PF
5. From the electrochemical reaction at the charged anode, these products will then form a surface film on the anode, known as SEI film
[26]. At the same time, a CEI film will form on the cathode surface. The stable and dense surface film can inhibit the electrode’s surface exposure to electrolytes, effectively reducing the reaction between the electrolytes and electrode
[27]. However, the continuous rupture and regeneration of the SEI and CEI films during the battery cycling will continue to consume Li
+. This will result in reduced battery capacity. At present, some electrolyte lithium additives have been added to the electrolyte to form a more stable SEI film
[28][29][30].
Especially in the charged state or at high temperatures, the electrolyte decomposition is an inherent risk, leading to gas formation inside batteries; this may lead to severe developments, such as a rise in the inner pressure of the battery cell, fire, or even explosions. In
[31], Gerelt-Od et al. investigated the overcharging of battery cells from 4.2 to 4.4 V in moderate temperatures of 35–45 °C, which are the normal operating conditions in real life. Four main gases (i.e., H
2, CH
4, CO
2, and CO) were detected when cells were exposed to the aforementioned electrical and thermal conditions. With the increase in battery voltage, more H
2 will be produced.
2.3. Aging at the Anode
The major aging mechanisms at the anode of LiBs are solid electrolyte interphase (SEI) formation, anode volume expansion, lithium metallization, loss of contact, and transition metal ions reduction.
The process of SEI film formation is complex and mainly happens during the first several charging and driving process. In those processes, firstly, the Li
+ from the cathode and the organic compounds from the electrolyte reacts with the graphite anode producing an SEI film with a thickness usually estimated between a few angstroms up to tens of nanometers
[32]. The formation of SEI film consumes Li
+, resulting in the loss of the lithium inventory, and, subsequently, capacity fade. The SEI formation can consume up to 10% of the initial battery capacity
[33]. A stable SEI film is beneficial to the anode, as it coats the anode surface and inhibits the direct contact between the electrolyte and the anode, reducing further side reactions. Furthermore, the SEI film also has high selective permeability for Li
+. However, the SEI growth is difficult to control, because it is highly dependent on the type of material and morphology of the anode, battery temperature, electrolyte composition, and electrochemical conditions
[6]. Moreover, the SEI film is easy to corrode after the long-term operation of the battery. Subsequently, the cracked SEI film will expose the anode to the electrolyte, leading to additional SEI growth and capacity loss. Electrolyte decomposition and side reactions will produce gas and exacerbate this degradation process. Even worse, during charging and driving, the graphite volume expands by approximately 10%
[7]. Cracking of the SEI film is accelerated by cycling at high DOD levels and/or idling the battery at elevated SOCs. All of these processes will consume Li
+ to generate the SEI film, resulting in capacity fade and resistance increase.
The formation of lithium metal is also a common aging mechanism at the anode side. When the LiBs operate at high SOC, the anode will be intercalated with a lot of Li
+, resulting in a low potential of the anode (i.e., the redox potential of Li/Li
+ close to 0 V)
[34]. When the partial anode polarization potential is below this voltage, the Li
+ will deposit on the anode surface, forming metallic lithium. Especially during cycling at a high DOD or during long-term idling at a high SOC, lithium dendrites will grow on the anode
[35]. The formation of lithium dendrites not only reduces the usable Li
+, but also destroys the anode structure and, possibly, pierces the separator leading to short circuits and thermal runaway
[36]. Finally, charging the battery with high current rates, which are greater than the speed of Li
+ diffusion to the anode, will lead to lithium plating. Moreover, the operation of the LiBs at low temperatures will lead to a slow Li
+ diffusion, producing more lithium plating and dendrite on the anode
[37].
A high SOC state results in a high
QNMC/SiC, which is related to the side reactions at the anode, including the dissolution of the Cu current collector and oxidation of the electrolyte. At the same time, a high temperature will accelerate this process. When the battery is stored in a high SOC, the self-discharge occurs significantly. Driven by the potential difference between the cathode and anode, the dissolved transition metal ions move from the cathode to the anode and are reduced by the charged anode forming metals deposits
[38]. As a result, the deposited metals in an inactive state (e.g., “dead lithium”) appear in the anode or on the copper current collector surface. The deposited metals, as cathode, then combine with the anode to form a micro-battery, which greatly reduces the current efficiency and aggravates the available capacity fade of the LiBs
[39].
All the aforementioned anode aging mechanisms are illustrated in Figure 14.
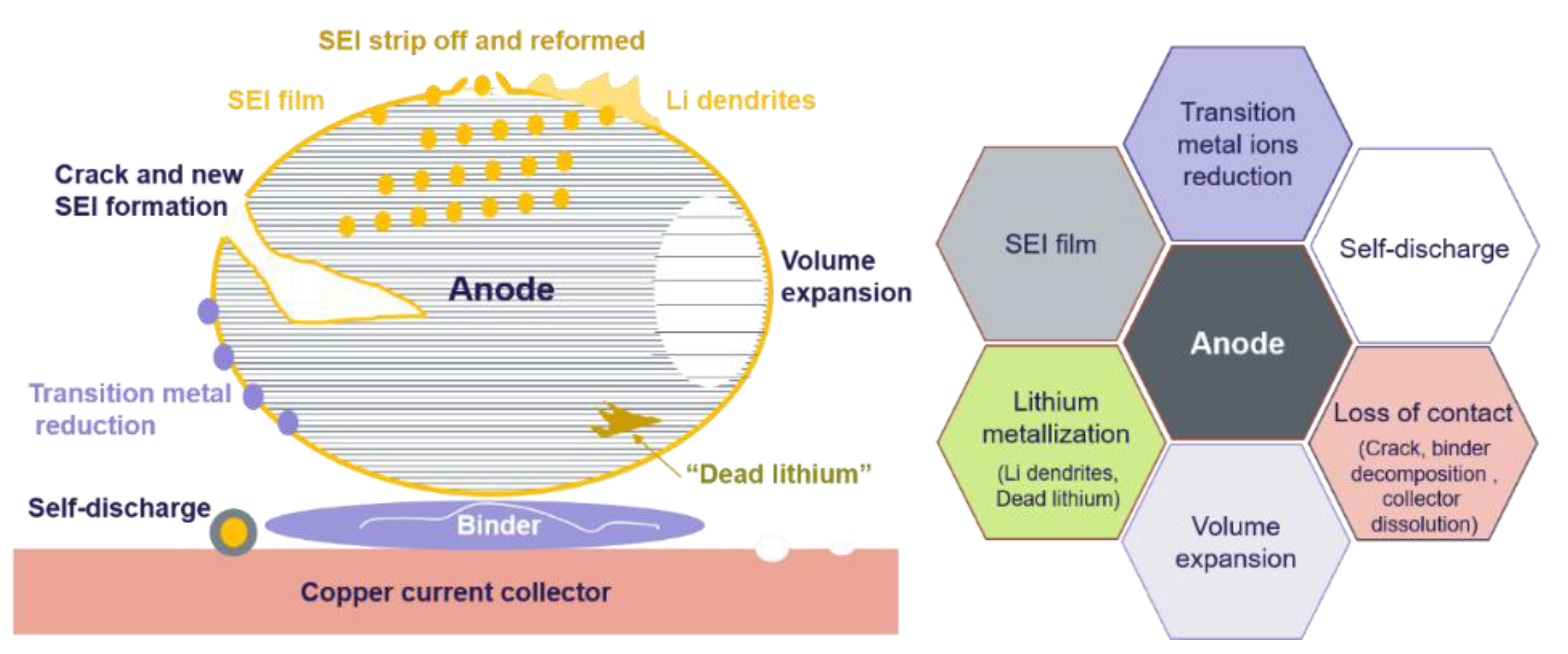
Figure 14. The main degradation mechanism at the anode side of a lithium-ion battery.
3. Conclusions
Because of their intrinsic properties, such as higher energy densities and low cost, Ni-based LiBs chemistries (i.e., NMC and NCA) are the preferred choices for powering EVs. As such, this work is mostly focused on reviewing the aging mechanisms and degradation behavior of these chemistries when used in various EV applications.
The long-term operation of LiBs in EVs involves many complex aging mechanisms. According to different application scenarios, this paper analyzes the battery aging behavior under EV charging, standby, and driving conditions, respectively. For all of the aforementioned conditions, we have individually linked the battery stress factors (e.g., temperature, cut-off voltage, etc.) to the battery performance and degradation behavior in EV applications. The effect of these stress factors (i.e., temperature, SOC, current, cut-off voltage, and DOD) on the degradation of the battery cathode, electrolyte, and anode is then fully analyzed. Therefore, this article provides a comprehensive review of the degradation of the battery performance parameters under EV operation, using driving cycles.
By minimizing exposure to the conditions that most accelerate battery aging, the life-span of the battery can be prolonged. High-temperature operation will cause side reactions in the battery, while lithium metalization on the anode is accelerated at low temperatures. Furthermore, a high charging current reduces the EV charging time but accelerate the battery aging to a significant extent. Finally, the high SOC operation (e.g., high cut-off voltage, idling at high SOC, and/or cycling at high DOD) also lead to accelerated degradation on the battery. All of these factors, which are specific to the EV battery operation, the triggered degradation mechanisms, and the effect on the battery performance parameters, are illustrated in Figure 15.
Figure 15. The main degradation mechanism of batteries in EV applications.
However, the battery degradation problem still needs further research, especially regarding EVs operation. At present, the literature regarding battery performance-degradation and subsequent aging mechanism identification is very limited and, frequently, is based on data that is obtained using standardized driving cycles, which do not always reflect the real-life battery operation in EVs.
This entry is adapted from the peer-reviewed paper 10.3390/en14175220