1. Solid Polymers Electrolytes (SPEs)
Solid polymer electrolytes (SPEs) have garnered significant attention owing to their appealing properties, including their ease of transformation into thin films, good mechanical behavior, electrochemical stability, well-defined electrode/electrolyte interface, safety, and no leakage
[1]. These characteristics are in stark contrast with those of liquid electrolytes. Notably, the concern towards the safety of lithium-based rechargeable batteries is related to the use of flammable liquid electrolytes. Although the lithium ion transference number is low for liquid electrolytes, they are endowed with a higher ionic conductivity and assure an appreciable interfacial contact with the electrode materials. However, there are disadvantages in addition to potential leakage, such as electrode/electrolyte reactions, which leads to an increase in battery temperature with consequent generation of flammable and hazardous gases
[2][3][4]. Enhanced mechanical stability is imparted by the polymer backbone, and this characteristic is especially required for batteries in wearable devices
[5]. SPEs are widely used in the fields of sensors and electrochemical energy storage devices such as batteries and supercapacitors, fuel cells, and electrochromic displays
[6][7][8][9].
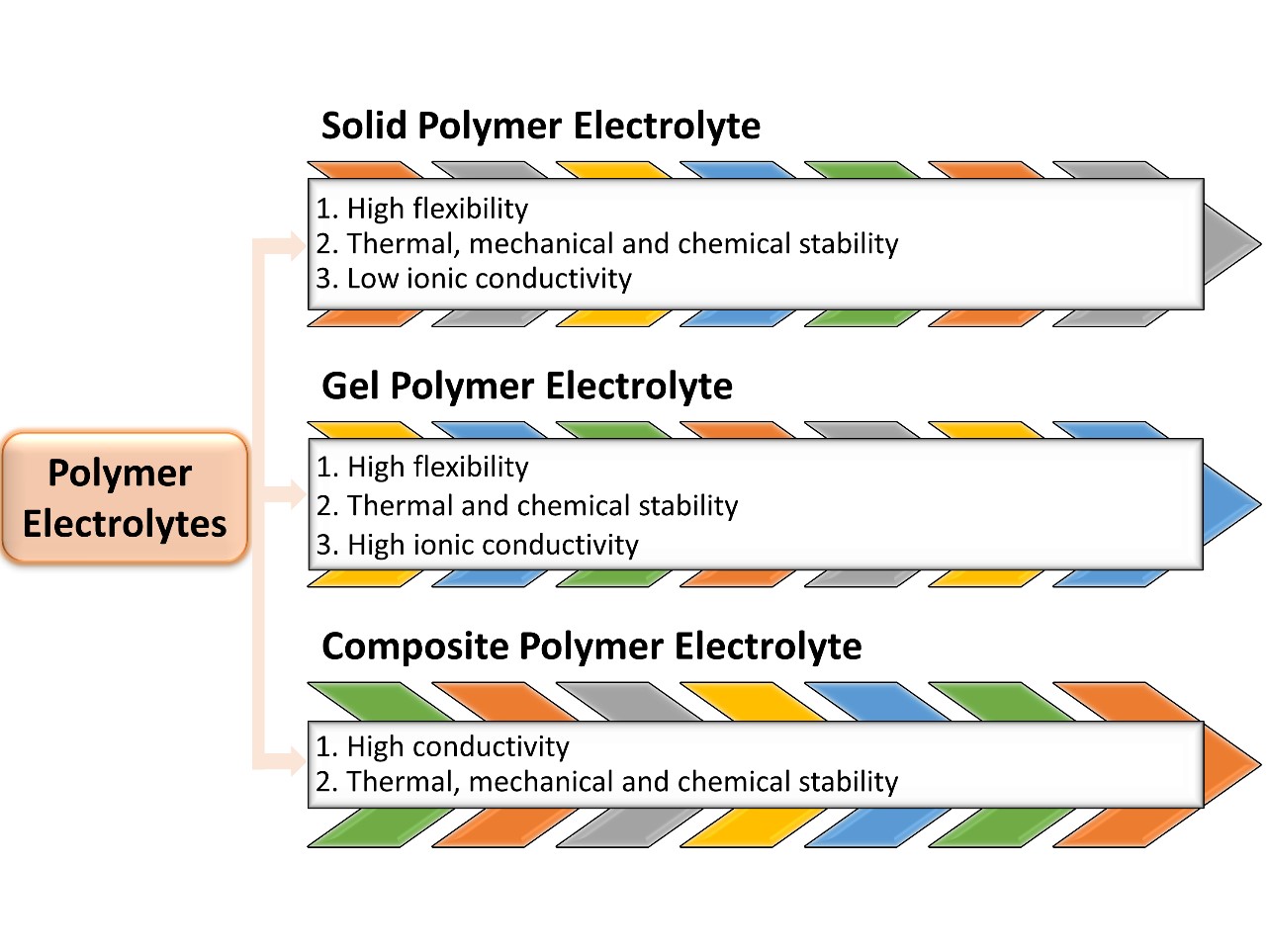
Figure 1. Classifications of polymer electrolytes.
SPEs have garnered extensive research attention due to their combination of a relatively high ionic conductivity, cost-effectiveness, and mechanical stability
[10]. In 1995, Hashmi et al.
[11] investigated PEs based on PEO and NaPF
6 sandwiched between Pt electrodes. This PE system exhibited the best conductivity of 5 × 10
−6 S·cm
−1 at room temperature. In 1999, Sreekanth et al.
[12] reported a PEO and NaNO
3 PEs measured between Na electrodes. Alternatively, the cathode was chosen to be a mixture of molecular iodine, carbon, and PE. The discharge characteristics were recorded at a constant load of 100 kΩ, and the conductivity of the PEs was as high as 2.83 × 10
−6 S·cm
−1. In 2001, Chandrasekaran et al.
[13] reported a PE based on PEO and NaClO
3 with PEG, Na, and MnO
2 as the plasticizer, anode, and cathode, respectively. The authors concluded that the plasticizer activated the polymer chain relaxations, favoring an ion hopping mechanism within the polymer matrix. A higher conductivity value was observed with a lower salt concentration, measured at 9.47 × 10
−4 S·cm
−1.
In 2005, Anantha et al.
[10] reported studies of PEO-NaNO
3 PEs with different compositions of the ether oxygen to sodium ratio (O/Na). These PEs were formed into thin films using the solution casting method. Based on characterization studies, it was found that a decrement in crystallinity occurs with increasing salt concentrations. The highest conductivity of 3.5 × 10
−6 S·cm
−1 was observed at room temperature. In 2006, Kumar et al.
[14] prepared a PE based on PEO and NaClO
3 using a solution casting technique and studied its properties in a cell with a Na anode, PE, and a mixture of I
2, with carbon and PE as the cathode. The PE was found to exhibit a conductivity value of approximately 10
−7 S·cm
−1.
In the years 2006 and 2007, Mohan et al.
[15][16] examined ion transport and battery discharge behavior in PEs derived from PEO and either NaFeF
4 or NaLaF
4. The optical and electrical properties were studied for pure PEO and PEO doped with the salts. Both the sodium compounds were prepared using a solid-state diffusion method by mixing NaF with La(NO
3)
3 and Fe(NO
3)
3, respectively. The conductivity of the PEs was shown to increase with rising temperatures using cells comprised of Na as the anode and a mixture of I
2 and C soaked with the electrolyte as the cathode. The maximum conductivity was found to be 1.37 × 10
−7 S·cm
−1 using NaFeF
4 and 3.9 × 10
−7 S·cm
−1 using NaLaF
4.
Consecutively, in the years 2006 and 2007, Bhide et al.
[17][18] reported a new PE system using PEO, NaPO
3, and different ratios of ethylene oxide and NaPO
3 with and without PEG as a plasticizer. NaPO
3 was synthesized by gradually cooling the molten mixture of Na
2CO
3 and (NH
4)H
2PO
4 within the temperature range of 900 °C down to room temperature. This PE exhibited a peak conductivity of 2.8 × 10
−8 S·cm
−1. Upon plasticization with PEG, the conductivity substantially increased to 8.9 × 10
−7 S·cm
−1. In 2012, Sasikala et al.
[19] reported their investigation of PEs composed of PEO and NaF. The conductivity demonstrated an upward trend with increasing NaF concentration, reaching a maximum value of 4.73 × 10
−7 S·cm
−1 at a PEO:NaF ratio of 70:30.
In 2017, Ma et al.
[20] introduced a new PE incorporating sodium (fluorosulfonyl)(
n-nonafluorobutanesulfonyl)imide (Na [(FSO
2)(
n-C4F
9SO
2)N], NaFNFSI) and PEO. This PE exhibited a conductivity of 3.36 × 10
−4 S·cm
−1 at 80 °C. Another contribution was reported in the same year by Heratha et al.
[21], who investigated the electrical and thermal characteristics of a PE system based on PEO and NaI, examining various PEO:NaI ratios. The highest conductivity recorded was 7.1 × 10
−5 S·cm
−1 at room temperature.
In 2019, Arya et al.
[22] reported PEs based on PEO and NaPF
6 and studied their structural, morphological, electrochemical, and dielectric properties. These PEs, plasticized by succinonitrile, were found to exhibit a maximum conductivity of 2 × 10
−5 S·cm
−1. The same authors reported on PEs comprised of a blended mixture of PEO, PVP, and NaNO
3 [23]. Their study centered on the dielectric relaxations and transport characteristics of this innovative polymer blend. A peak conductivity of 2.90 × 10
−4 S·cm
−1 at a temperature of 100 °C was observed. Again, in 2020, they reported a Na ion-conducting PE system based on a PEO and polyethyleneimine (PEI), which exhibited a conductivity of 5.2 × 10
−4 S·cm
−1 at 100 °C
[24]. In 2020, Zhang et al.
[25] reported on a PEO-NaPF
6 PE which exhibited a conductivity of 6.3 × 10
−4 S·cm
−1 at 80 °C. In that same year, Youcef et al.
[26] reported on PEs based on PEO and a Na(FSI-ethyl cellulose) system which exhibited good electrochemical and mechanical properties, with a conductivity value of approximately 10
−4 S·cm
−1 at 80 °C.
In 2022, Kim et al.
[27] published their findings regarding an anode-less seawater battery. This innovative battery utilizes an SPE based on a PEO polymer, facilitating energy storage from power to metal and metal to power. The precursors NaFSI, PEO, and Pyr
14FSI were dried at 70 °C, 50 °C, and 90 °C, respectively, in a dry room for 24 h, followed by dissolution of benzophenone (a cross-linking agent) in Pyr
14FSI to form a homogeneous solution. This mixture was added to PEO/NaFSI powder, mixed, sealed, and aged at 100 °C overnight. This material was then pressed into a thin polymeric film at 100 °C and treated with UV light. A peak conductivity of 1 × 10
−3 S·cm
−1 was recorded at room temperature. The SPE was integrated with a Na superionic conductor (NASICON) to achieve effective physical separation.
Chandra et al.
[28] reported on their study of a PE based on PEO and NaCl with a ratio of 70:30. A peak conductivity of 4.5 × 10
−6 S·cm
−1 was recorded at room temperature. In 2006, Reddy et al.
[29] studied the conductivity and discharge characteristics of a PE system based on PVC and NaClO
4. A viable solid-state electrochemical cell with a Na anode, the highest-conductivity PE, and a mixture of I
2, carbon, and PE as the cathode was fabricated. In 2017, Muhammad et al.
[30] reported the properties of a PE based on PVC and NaI. The conductivity was 2.9 × 10
−8 S·cm
−1 at room temperature.
In 2006 and 2007, Bhargav et al.
[31][32] reported on PE films based on PVA doped with NaBr and NaI salts. They studied the characteristics of PVA films with or without NaI or NaBr. It was found that as the concentration of the salts was increased, the films became more amorphous and, therefore, more conductive. Electrochemical cells were assembled using these electrolytes and characterized. The maximum conductivities obtained were 1.02 × 10
−5 S·cm
−1 and 1.12 × 10
−6 S·cm
−1 for NaI and NaBr, respectively. In 2018, Duraikkan et al.
[33] studied the structural, thermal, and electrical properties of PEs comprised of PVA/PVP and NaNO
3. Similar to previous works, the amorphicity was found to increase, which in turn resulted in an increase of the conductivity to 1.25 × 10
−5 S·cm
−1 at room temperature. In 2021, Aziz et al.
[34] reported on their study of a PE blend based on PVA and NaI using glycerol as a plasticizer, which was found to exhibit a maximum conductivity of 1.17 × 10
−3 S·cm
−1 at room temperature.
In 2013, Tiwari et al.
[1] reported on starch-based sodium PEs. Potato starch was mixed with NaI, NaSCN, and NaClO
4 salts, and the effects of different anions were studied. The highest conductivity was measured for NaSCN at 1.12 × 10
−4 S·cm
−1. In 2015, Khanmirzaei et al.
[35] reported a PE based on the ionic liquid 1-methyl-3-propylimidazolium iodide (MPII) and rice starch (RS) for use in dye-sensitized solar cells. TiO
2 was coated on a fluoride/tin oxide (FTO) sheet and used as the anode, whereas platinum-coated FTO was used as the cathode, with RS:NaI:MPII as the electrolyte. This system was found to exhibit a peak conductivity at 1.20 × 10
−3 S·cm
−1. In 2017, Ahmad et al.
[36] carried out an electrical analysis of PEs based on cornstarch (CS) and NaCl. This simple PE exhibited the highest conductivity at 1.72 × 10
−5 S·cm
−1 for a weight ratio of 70:30 for CS:NaCl. In 2021, Awang et al.
[37] studied the impact of adding sodium bisulfite, NaHSO
3, to cornstarch. The maximum observed conductivity was 2.22 × 10
−4 S·cm
−1 at room temperature. Similarly, in the same year, Asnawi et al.
[38] reported the effects of adding NaCF
3SO
3 to a chitosan/dextran polymer blend. The resulting PE was found to exhibit a maximum conductivity of 6.10 × 10
−5 S·cm
−1 at room temperature.
In 2014, Rani et al.
[39] conducted a comprehensive examination of the structural, thermal, and electrical attributes of PEs derived from hydroxypropyl methylcellulose (HPMC) doped with NaI. The best conductivity was recorded for the ratio of 5:4 for HPMC:NaI at 40 °C as 1.126 × 10
−6 S·cm
−1. An enhanced amorphicity was accompanied by a high conductivity. In 2015, Abiddin et al.
[40] reported on the conductivity and electrical properties of methylcellulose (MC) salted with NaI. The maximum conductivity that was observed was 2.7 × 10
−5 S·cm
−1 at 60 °C. Again, in 2015, Bella et al.
[41] reported on the fabrication of a photo-PE based on a sodium ion methacrylate for secondary battery applications. This was the first report for a photopolymerized sodium ion PE. This material was found to exhibit a thermal stability greater than 100 °C, a high specific capacity, excellent chemical stability, and a high conductivity of 5.1 × 10
−3 S·cm
−1 at 20 °C. In 2020, Sayed et al.
[42] studied the influence of different metal acetates on carboxy methylcellulose (CMC) in CMC-Na/PVP PEs by comparing their spectroscopic, optical, and dielectric properties. Initially, the metal acetates of interest were added to PVP and then mixed with CMC-Na to form the PEs. The maximum conductivity was measured at 1.81 × 10
−4 S·cm
−1. In 2020, Shetty et al.
[43] conducted a study investigating the electrical and optical properties of CMC mixed with NaBr at various mass ratios. The highest conductivity, reaching 5.15 × 10
−4 S·cm
−1, was achieved for the PE containing 20 wt% NaBr at room temperature. Similarly, Aziz et al.
[3] reported a similar PE based on methyl cellulose (MC) doped with NaI, which demonstrated a maximum conductivity of 3.01 × 10
−3 S·cm
−1 with 50 wt% NaI.
In 2016, Singh et al.
[44] reported PILEs based on an ionic liquid, 1-butyl-3-methylimidazolium methylsulfate (BMIM-MS), PEO, and sodium methylsulfate salt. Various weight percentages of BMIM-MS were employed to formulate these electrolytes, which exhibited a maximum conductivity of 4 × 10
−4 S·cm
−1 at 75 ºC. In 2017, Zhang et al.
[45] described the in situ formation of a PEG–divinyl ether PE. This ionic conductor was examined as a film on a polysulfonamide support alongside an Na
3V
2(PO
4)
3 cathode and a layered MoS
2 anode. The polymer, tri(ethylene glycol) divinyl ether, was polymerized in situ using LiBF
4 as an initiator, achieving a maximum conductivity of 1.2 × 10
−3 S·cm
−1 at ambient temperature. In 2017, Pan et al.
[46] reported an SIB utilizing a single ion-conducting sodium ion PE composed of poly(
bis(4-carbonyl benzene sulfonyl)imide-co-2,5-diamino benzesulfonic acid) (NaPA). The highest conductivity recorded for this system was 4.1 × 10
−4 S·cm
−1 at 80 °C. The cathodic material, Na
3V
2(PO
4)
3/AC was synthesized from the precursors H
3PO
4, NH
4VO
3, Na
2CO
3, and acetylene black. In 2018, Chen et al.
[47] introduced a PE based on hyperbranched
β-cyclodextrin (H-
β-CD). The
β-CD was modified using multiple oligo(methyl methacrylate)-block-oligo(ethylene glycol) methyl ether methacrylate short chains and complexed with NaTFSI, resulting in a self-standing, transparent, and flexible SPE film. This electrolyte exhibited its highest conductivity of 1.3 × 10
−4 S·cm
−1 at 60 °C. In the same year, Hassan et al.
[8] investigated the structural and electrical spectroscopy of a PE composed of sodium 4-styrenesulfonate combined with ammonium nitrate. This PE displayed its highest conductivity at room temperature, reaching 3.16 × 10
−4 S·cm
−1 with a 30 wt% ammonium nitrate content.
In 2019, Janakiraman et al.
[48] reported an electrospun fibrous PE based on PVDF combined with NaPF
6 for battery applications. In this technique, different concentrations of PVDF dissolved in DMSO and acetone were loaded into hypodermic syringes and were then subjected to electrospinning under an applied DC voltage. The resulting electrospun fibers were then soaked in an NaPF
6 solution and stretched for further analysis. This fibrous electrospun PE provided a maximum conductivity of 1.08 × 10
−3 S·cm
−1 at ambient temperature. In 2019, Yang et al.
[49] reported a flame-retardant quasi-solid PE for battery applications. Poly(methyl vinyl ether-
alt-maleic anhydride) (P(MVE-
alt-MA), bacterial cellulose, and triethyl phosphate/vinylene carbonate (TEP/VC)/sodium perchlorate (NaClO
4) were used as the host, reinforcement, plasticizer, and salt, respectively. This PE was found to exhibit a flame-retardant nature and longer cycle stability. This system had a maximum conductivity of 2.2 × 10
−4 S·cm
−1 at room temperature. In 2021, Liu et al.
[50] reported the synthesis of a single ion-conducting PE based on sodium
bis(fluoroallyl)malonato borate salt NaBFMB photocrosslinked to a tri-thiol(trimethylolpropane tris(3-mercapto propionate) (TMPT) using a click thiol-ene reaction. This electrolyte exhibited a maximum conductivity value of 2 × 10
−3 S·cm
−1 at 30 °C. It is unclear to what extent the ILs were purely part of the 3D structure and whether there was some plasticizing effect due to the non-crosslinked IL.
In 2022, Law et al.
[51] reported a hybrid dual-salt sodium PE for SIB applications. NaTFSI and NaDFOB salts were mixed together, followed by the addition of PVDF powder to form a blended SPE. This electrolyte was found to exhibit a maximum conductivity of 3.1 × 10
−4 S·cm
−1 at 23 °C.
Cisneros et al. proposed solvent-free sodium polymer batteries based on cross-linked PEs
[52]. These electrolytes are formed through the polycondensation of α, ω-dihydroxy-oligo(oxyethylene) with an unsaturated dihalide, resulting in the formation of amorphous networked electrolyte films upon further curing. Utilizing NaClO
4 and NaCF
3SO
3 at varying O/Na ratios, the optimal PE exhibits cationic conductivity (σ
+) surpassing 1 mS·cm
−1 at 90 °C while maintaining mechanical integrity up to at least 120 °C.
Martínez et al. explored blends of PEO and poly(sodium 1-[3-(methacryloyloxy)propylsulfonyl]-1-(trifluoromethanesulfonyl) imide) (PNaMTFSI) in various proportions
[53]. The blend composition significantly influenced the ionic conductivity, with the most notable results observed for blends containing 15 and 30 wt% PNaMTFSI. At elevated temperatures, specifically 85 °C, the highest ionic conductivity values were recorded, reaching 5.84 × 10
−5 and 7.74 × 10
−5 S·cm
−1, respectively. Furthermore, these compositions exhibited sodium ion transference numbers exceeding 0.83 and demonstrated electrochemical stability within the range of 3.5 to 4.5 V versus Na/Na
+. These findings suggest the potential use of these blends in sodium batteries.
The Na PEs explored thus far have been mostly based on PEO. Therefore, ethereal oxygens in a helical conformation appear to be the most reliable way to loosely coordinate and mobilize cations, including Na+. Unfortunately, PEO, while enabling a relatively high conductivity (~10−4 S·cm−1), is typically associated with a low transport number (below 0.5). An interesting alternative choice in polymer host has been that of cellulose derivatives, which provide the opportunity for using materials of biological origin. It remains unclear to what extent OH-rich phases can be fully dried of water traces and become thermally stable upon prologued cycling. At the same time, the knowledge transfer of Li to Na as it pertains to salts (e.g., NaPF6, NaTFSI, and NaFSI) did not present any particular surprises or improvements. Based on general cation solubility principles, it is doubtful that further fine tuning may come from structural modifications of already available anions.
2. Gel Polymers Electrolytes (GPEs)
Gel polymer electrolytes (GPEs) have gained significant importance due to their ability to combine the advantageous characteristics of both solid and liquid electrolytes
[54]. Feuillade et al.
[55] conducted pioneering research on GPEs for Li batteries in 1975, the first of such studies on record. In their work, they explored cross-linked gel membranes composed of materials like polyvinyl butyral (PVB), epichlorohydrin with titanium/silicon alkoxy compounds, PVDF and dicinnamylidene hexanediamine dissolved in methyl ethyl ketone. Additionally, they investigated thermoplastic gels consisting of PAN, PC, and NH
4ClO
4. GPEs are produced by over-plasticizing the polymeric phase with low-molecular-weight molecules, usually organic solvents. As a result of its interaction with the plasticizer, the polymer expands and mostly becomes amorphous while maintaining adequate mechanical strength. The plasticizer’s presence enables new avenues for ionic movement. These reasons explain why SPEs without plasticizers often have lower conductivities than GPEs
[56][57]. The precise ion-conduction mechanism and the nature of the interactions between the polymer, plasticizer (solvent), and salt have yet to be fully elucidated
[58][59]. GPEs have recently attracted attention due to their superior characteristics over liquid electrolytes
[60]. Their most attractive quality is their free-standing consistency, which facilitates handling, cell design, modularity, and dependability in many electrochemical devices
[61].

Figure 2. Polymer electrolyte of Sodium polymer.
In order to enable the functionality of GPEs, it is necessary to incorporate plasticizers or solvents possessing elevated dielectric constants. These are blended with different salts and fixed within the structure of polymer matrices, including materials such as PMMA, PAN, PVDF, and PVDF-HFP, among others
[62][63][64][65]. GPEs can develop when appropriate ionic salts and small-sized organic solvents like EC, PC, and DEC are enclosed within the polymer hosts
[66]. The co-polymer PVDF-HFP is widely used in high-performance GPE systems among the many host polymers because of its advantageous properties such as its low glass transition temperature (−35 °C), high dielectric constant (8.4), and structural uniqueness. GPEs have a strong ionic conductivity, exhibit increased safety, are inexpensive, and are simple to fabricate into the desired shapes and sizes. The thermal, mechanical, chemical, and electrochemical stability of GPEs are adequate. Further improvements in GPEs would require electrolyte salts with a superior solubility and high liquid holding capacity.
Room-temperature ionic liquids (RTILs) have been employed as substitutes for organic additives in GPEs to enhance their thermal, mechanical, and electrochemical durability. ILs are molten salts composed primarily of organic cations and inorganic anions. They are appreciated for their versatility and their effective roles as plasticizers and suitable solvents. Their distinctive attributes include their robust ionic conductivity (0.01 S·cm
−1), elevated thermal stability up to 400–500 °C, non-flammability, non-volatility, and impressive electrochemical window spanning the range of 4.0–6.0 V
[67].
Wang et al.
[68] assembled Na-conducting GPE membranes using Na
2Zn
2TeO
6 as a filler, and their use in SIBs was shown to be effective. The incorporation of Na
2Zn
2TeO
6 filler led to a composite GPE (CGPE), with a substantial enhancement in ionic conductivity. This improvement can be attributed to the filler, which also functions as an ionic conductor, causing a reduction in the crystalline structure and an increase in the porosity within the polymer membranes. Consequently, the modified GPE membranes exhibit an impressive ionic conductivity of 2.52 × 10
−3 S·cm
−1 at room temperature, along with an extremely low activation energy of approximately 0.040 eV. The assembled Na
3V
2(PO
4)
3/C|GPE|Na battery showcases excellent performance metrics, including a notable initial discharge capacity of 93.3 mAh·g
−1 at 0.5 C, a promising capacity retention rate of 98.4% after 100 cycles, and outstanding high-rate performance, achieving 83.5 mAh·g
−1 at 5 C.
This research establishes that ionic conductors such as Na2Zn2TeO6 can be used to improve GPE performance. Using a conventional solid-state reaction approach carried out using high-energy ball milling, Na2Zn2TeO6 filler was produced. PVDF-HFP/PMMA-based GPEs membranes with Na2Zn2TeO6 were prepared using the solution casting process. X-ray diffraction was employed to examine the phase structure of the as-prepared Na2Zn2TeO6 filler and the filer within the GPE membranes. Field emission scanning electron microscopy was used to analyze the microstructure and elemental distribution of the GPE membranes. Thermogravimetric analyses were performed from room temperature to 700 °C.
Wang et al.
[69] synthesized a new polymeric material termed polymeric sodium tartaric acid borate (PSTB), which was combined with poly(vinylene carbonate) to produce a single-ion-conducting GPE referred to as PSP-GPE. This PSP-GPE exhibited several notable characteristics, including a high sodium ion transference number of 0.88, an oxidation threshold of 4.5 V, and excellent compatibility with the sodium anode. Furthermore, it showed remarkable ionic conductivity, registering at 1 × 10
−4 S·cm
−1, surpassing the performance of a room-temperature liquid electrolyte based on NaClO
4. A Na/PSP-
10-GPE/Na
3V
2(PO
4)
3 battery was found to exhibit a 98.6% capacity retention and >99% coulombic efficiency for 200 cycles at 0.5 C, 25 °C. The same assembly at 60 °C exhibited an approximately 100% capacity retention and >99.3% coulombic efficiency for 50 cycles at 0.5 C.
Wang et al.
[70] prepared a novel CGPE membrane by blending PVDF-HFP/PMMA with Ti
3C
2T
x MXene. They then investigated the electrochemical performance of this membrane in SIBs. The presence of the Ti
3C
2T
x MXene filler, which is multilayered, significantly enhanced the electrochemical performance of the battery. This improvement was attributed to the filler’s ability to increase the contact sites for Na ions and enhance the porosity of the polymer membranes. Furthermore, the distinctive parallelly arranged layered structure of the MXene promoted uniform sodium nucleation and growth on the surface of the sodium electrode while inhibiting the formation of sodium dendrites during the sodium deposition process. The CGPE membrane containing 8 wt% Ti
3C
2T
x MXene exhibited impressive properties, including a maximum ionic conductivity of 3.28 × 10
−3 S·cm
−1, excellent thermal stability, a relatively high sodium ion transfer number of 0.558, and a wide electrochemical window of 5.25 V. A Na
3V
2(PO
4)
3/GPE/Na battery after 300 room temperature cycles at 0.5 C showed a remarkable 95% capacity retention. The Na
3V
2(PO
4)
3 cathode was prepared using a sol-gel process
[2].
To achieve good sodium ion conductivity at room temperature, Vo et al.
[71] prepared GPE films employing a PVDF-HFP matrix. Microporous PVDF-HFP membranes were swelled and filled with various liquid electrolytes comprised of NaClO
4, NaPF
6, and NaTFSI salts dissolved in mixtures of carbonate solvents such as PC and fluoroethylene carbonate (FEC) or ionic liquids such as 1-ethyl-3-methylimidazolium
bis(trifluoromethane). The influences of the different electrolytes on the structure, morphology, electrolyte absorption, and sodium ionic conductivity of the resulting membranes were examined by the authors. The “sponge-like” structure of the GPEs was endowed with a high porosity (80–85%) and large pore sizes. At ambient temperature, the ionic conductivity of the GPEs was 1–2 mS·cm
−1. DSC, TGA, XRD, and FE-SEM were used for characterization. By employing GPEs as the ion-conduction layer, sodium intercalation into an Na
0.44MnO
2 cathode was carried out in a coin-cell configuration. At room temperature, the cycling data of a sodium cell using PVDF-HFP/NaClO
4 1 M-PC:2%FEC showed a consistent specific capacity of 100 mAh·g
−1. The best ionic conductivity was 1.91 mS·cm
−1 for NaClO
4 1 M PC:2%FEC/PVDF-HFP. The temperature-dependent ionic conductivity exhibited VTF behavior, indicating the assistance of the backbone and polymer segmental mobility in the gel medium. The higher temperature of liquid electrolyte degradation when compared to the unsolvated microfiber membrane imparted a higher thermal stability to the final GPEs. Due to the high oxidation limit of 4 V ca. vs. the Na
+/Na potential, the electrochemical stability window of the GPEs was compatible with 4 V sodium cathode materials. The assembly of a Na/GPE/Na
0.44MnO
2 cell allowed the authors to demonstrate a reversible intercalation/deintercalation of Na
+, as well as a steady discharge capacity in a cyclic voltammogram and charge–discharge test. After 20 cycles, the specific capacity of NaClO
4 1 M—PC:2%FEC/PVDF-HFP remained constant at 100 mAh.g
−1, with no sign of capacity fading.
Harshlata et al.
[72] demonstrated that a liquid electrolyte composed of sodium trifluoromethanesulfonate (NaCF
3SO
3) dispersed within an IL named 1-butyl-3-methylimidazolium trifluoromethanesulfonate (BMImCF
3SO
3) can be effectively immobilized using a porous membrane crafted from PVDF-HFP. The manufacturing process for these porous GPE membranes involved a phase-inversion technique. Various physical and electrochemical methods were utilized to characterize these electrolyte membranes. Notably, in the CGPE systems, the incorporation of TiO
2 nanoparticles led to interactions with the anion of the liquid electrolyte (CF
3SO
3−) and resulted in an increased amorphicity of the polymer network. As a result, the improved membrane exhibited enhanced electrochemical stability, with a window of approximately 4.3 V, a maximum room temperature ionic conductivity of 0.4 mS·cm
−1, and a Na
+ ion transport number of roughly 0.27. This upgraded membrane was employed in the construction of a prototype sodium battery, which displayed a consistent open-circuit potential of 2.2 V and delivered a discharge capacity of 200 mAh·g
−1 at a drain current of 25 mAh·g
−1. To investigate the structural properties of the membrane, various characterization techniques were employed, including scanning electron microscopy (SEM), X-ray diffraction (XRD), and Fourier transform–infrared spectroscopy (FTIR).
Utilizing the highest-performing composite PILE membrane denoted as PEM0.5, a prototype sodium battery was assembled featuring a sodium–mercury (Na-Hg) anode and a phosphorus–carbon (P-C) cathode. When compared to pure sodium metal, Na-Hg serves as a superior reducing agent and is easier to handle. Phosphorus red, with a theoretical capacity of 2596 mAh·g
−1, emerges as an excellent candidate for the electrode material in a sodium battery, while carbon contributes the electronic conductivity
[73].
Chen et al.
[74] synthesized a flexible GPE (PGT32-5%) based on poly(poly(ethylineglycol)methacrylate) (PPEGMA) that was plasticized with nonflammable triethyl phosphate (TEP). The GPE was then stabilized by glass fibers using an in situ thermal curing process. A high ionic conductivity (9.1 × 10
−4 S·cm
−1 at 27 °C) and wide electrochemical window are two characteristics of the improved flame-retardant electrolyte, PGT32-5% (4.8 V). To ensure excellent cycling stability of the quasi-solid-state Na
3V
2(PO
4)
3|PGT32-5%|Na battery (capacity retention of 91% after 400 cycles), an artificial interface between the GPE and Na metal anode was formed. It was found that trace FEC on a hard-carbon anode can generate a stable SEI
[75]. Furthermore, the interfacial modification and its impact on the discharge behavior were thoroughly examined, paving the way for the development of future PEs that exhibit superior performance parameters. The sol-gel process was followed to produce the Na
3V
2(PO
4)
3/C cathode
[76].
3. Composite Polymer Electrolytes (CPEs)
SPEs consist of a polymer matrix containing sodium salt and no liquid solvent. Unfortunately, SPEs suffer from a low ionic conductivity. The advancement of this field relies on the following approaches: (1) reducing the percentage of liquid plasticizers
[77] and (2) adding inorganic fillers
[78]. As explained above, researchers consider plasticized polymer electrolytes (PPEs) to be separate from CPEs, which include inorganic fillers. The physical properties of the components used in these types of CPEs are displayed in
Figure 1. The use of these strategies in some cases comes at the price of sacrificing part of the mechanical, thermal, and chemical stability of SPEs. The addition of inorganic ceramic fillers seems to be the most promising route, as it usually increases ionic conductivity.
Figure 3. Composite polymers electrolytes.
An ideal CPE should have a high ionic conductivity (up to the order of 10
−3 S·cm
−1) in a wide temperature range to enable SIBs with a high cycle and rate performance (
Figure 2). The following list of targeted requirements are desirable characteristics in CPEs. (1) In order to prevent sluggish reactions with the electrodes during the processes of sodium insertion and extraction, it is crucial for CPEs to possess a wide electrochemical stability range of up to 5 V. (2) To prevent deformation while operating at high temperatures, CPEs should have a strong dimensional stability and superior thermal stability of up to at least 150 °C. The deformation of PEs in SIBs generally results in significant risks including short circuits and thermal runaway due to the poor thermal stability of conventional PEs. (3) In order to achieve optimal power performance and mitigate issues related to ionic concentration polarization, CPEs should exhibit a high sodium ion (t
Na+) transference number, ideally close to 1. Additionally, these CPEs need to possess substantial mechanical strength to effectively deter the penetration of sodium dendrites. (4) Mechanical robustness is a crucial attribute for CPEs, especially when considering their applications in wearable and flexible energy storage devices. (5) CPEs in SIBs ought to be cost-effective for a wide range of energy storage applications. (6) To ensure the safe and long-term supply of SIBs, CPEs should exhibit a low toxicity and should be comprised of materials that are abundant on Earth. It is important to bridge the gap between the actual performance of a practical electrolyte and the structural, chemical, and functional qualities of an ideal CPE
[79].
Figure 4. Characteristic properties of composite polymers electrolytes.
It was discovered that GPEs filled with various inorganic oxides, including SiO
2, Al
2O
3, TiO
2, ZrO
2, BaTiO
3, etc.
[80][81][82] showed enhanced mechanical strength, higher ionic conductivity, and improved electrochemical stability of the Li/electrolyte interface compared to those without filling. These systems were labelled CGPE in the previous section. Similarly, the direct dispersion of active or inert inorganic oxide fillers within PEs without plasticizers leads to the formation of CPEs. Given that active fillers directly participate in the ion conduction process, their incorporation generally leads to increased conductivity and a greater mobile ion transference number compared to inert fillers.
This entry is adapted from the peer-reviewed paper 10.3390/batteries10030073