The high-voltage battery is a crucial element for electric vehicles (EVs) traction systems. It is the primary energy source that must be regularly recharged to reach the autonomy declared by the manufacturer. Therefore, an EV charging system is required to ensure the battery charging process.
12. Classification and Topologies of EV Charger
1.1. EV Chargers Classification
2.1. EV Chargers Classification
The high-voltage battery (HVB) is vital for
electric vehicles (EV
s) traction systems. It is the primary energy source that must be regularly recharged to reach the autonomy declared by the manufacturer. Thus, an EV charging system is required to ensure the battery charging process. This vital component, based principally on power conversion stages, allows the electrical energy transfer between the power grid and EV batteries. Therefore, these EV chargers can be classified according to several criteria, including the charger location, the energy transfer direction, the charger structure, the connection type, and the number of power conversion stages
[1][2][30,31]. Accordingly, the options for each classification type are described in
Table 1 (Figure 1).
Table 1.
EV charging systems classification.
EV Chargers |
Description |
Offboard chargers |
All the components required for the EV charging and discharging process are inside the public EV charging station [3][4]. | All the components required for the EV charging and discharging process are inside the public EV charging station [32,33]. |
On-board chargers |
Some components required for the battery-charging process are embedded inside the EV. |
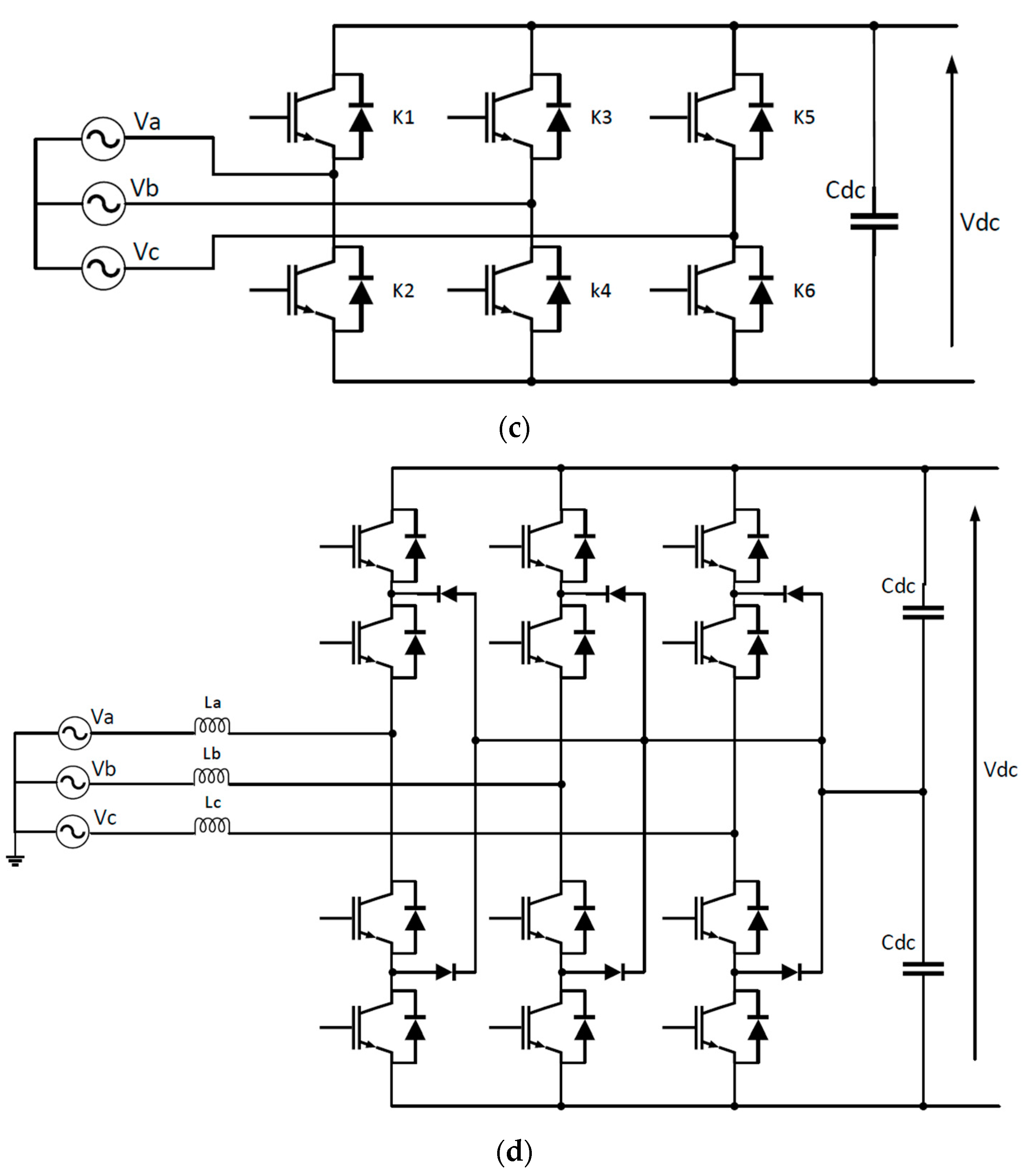
Figure 38. The electrical schematics of the commonly used bidirectional ac-dc power conversion stage in EV chargers: (
a) Bidirectional half-bridge single-phase ac-dc power converter; (
b) Bidirectional full-bridge single-phase ac-dc power converter; (
c) Bidirectional three-phase ac-dc power converter; (
d) Bidirectional three-level diode-clamped ac-dc power converter.
Figure 49 shows the most used dc-dc power circuitry for EV charging applications with V2X technology. However,
Figure 49a illustrates a non-isolated bidirectional half-bridge dc-dc power converter, while
Figure 49b presents its interleaved version.
Figure 49c illustrates an isolated bidirectional dual-active bridge (DAB) dc-dc power converter, while
Figure 49d shows its contactless version. It is a structure used for bidirectional inductive EV chargers; the left bridge is situated in the EV charging station, while the right one is embedded into the vehicle
[25][60].
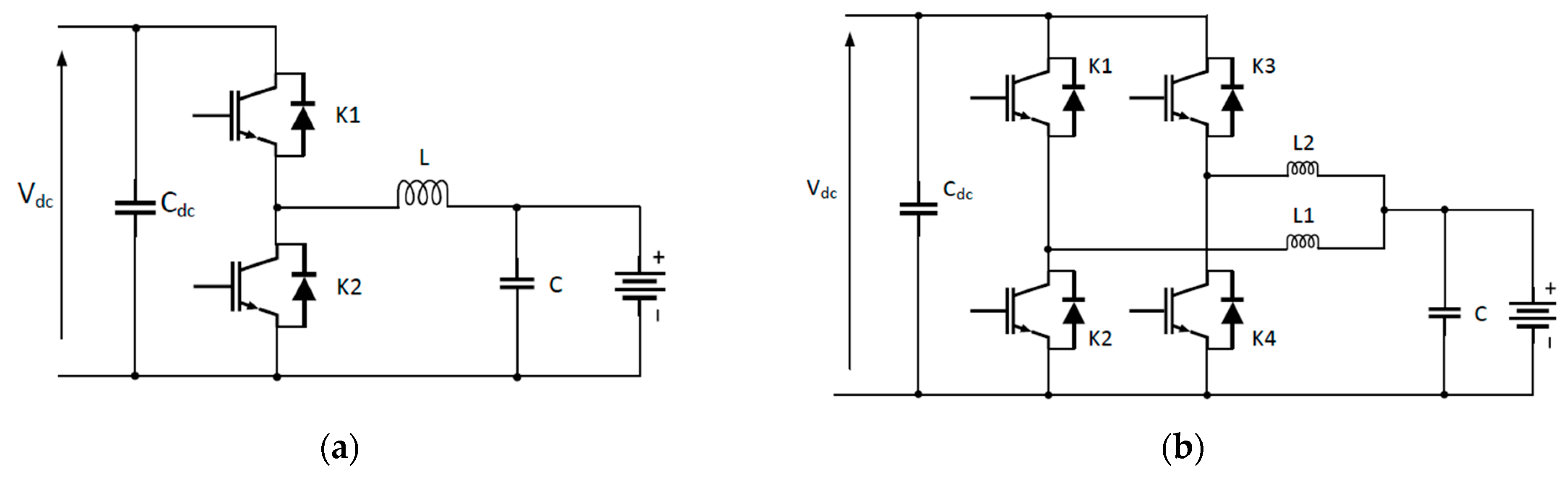
Figure 49. The electrical schematics of the most used dc-dc power conversion stage in EV chargers with V2X technology: (
a) non-isolate bidirectional half-bridge dc-dc power converter; (
b) Bidirectional interleave dc-dc power converter; (
c) Isolated bidirectional dual-active bridge dc-dc power converter; (
d) Inductive bidirectional dual-active bridge dc-dc power converter.
3. EV Charging Standards
3.1. SAE J1772 Standard
SAE J1772 is a standard published by SAE International that encompasses the general physical, electrical, functional, and quality criteria for EVs’ conductive charging process in North America
[26][69]. This standard provides available conductive charging methods for EVs and electric vehicle supply equipment (EVSE), including the operational, functional, and dimensional requirements for the vehicle inlet and mating connector
[27][70]. In addition, the SAE International terminology “Charging Levels” is utilized to classify the rated currents, voltages, and powers of the charging systems currently offered in North American markets
[28][29][71,72]. Accordingly, the October 2017 revision of the SAE J1772 standard outlines four charging levels: AC Level 1, AC Level 2, DC Level 1, and DC Level 2
[30][65].
Table 2 lists and describes their charging configuration settings and ratings
[31][73].
Table 2.
Levels charging available in SAE J1772 (2017) configuration.
Charging Level |
Specifications |
AC Level 1 |
|
- -
-
EV includes an on-board charger
- -
-
AC Single-phase Supply from a household outlet:
-
120 V @ 12 A ⇒ 1.44 KW
-
120 V @ 16 A ⇒ 1.92 KW
- -
-
Estimated charge-time for 1.92 KW:
|
|
AC Level 2 |
|
- -
-
EV includes an on-board charger
- -
-
208–240 V AC Single-phase
- -
-
Supply from residential installation or EVSE
- -
-
Charging power up to 19.2 KW (Typ. 7.2 KW)
- -
-
Charging current up to 80 A (Typ. 30 A)
- -
-
Estimated charge-time for 3.3 KW:
- -
-
Estimated charge-time for 7 KW:
|
Unidirectional chargers |
The electrical energy transfer is one-way from the EV charging station to the EV battery. Therefore, only the G2V operation mode is possible. |
Bidirectional chargers |
The electrical energy flow can be from or to the EV battery. Thus, V2X technology can be ensured by this type of charger [5]. | The electrical energy flow can be from or to the EV battery. Thus, V2X technology can be ensured by this type of charger [34]. |
Dedicated chargers |
All equipment making up the charger is exclusively utilized to guarantee the EV charging or discharging process. |
Integrated chargers |
When the EV is linked to the electricity network, the traction system constituents (Motors, inverters, etc.) are used to guarantee the EV charging or discharging process [6]. | When the EV is linked to the electricity network, the traction system constituents (Motors, inverters, etc.) are used to guarantee the EV charging or discharging process [35]. |
Conductive chargers |
A dedicated electrical cable links the EV to the electricity network. |
Wireless Power
Transfer Chargers [7] | Wireless Power
Transfer Chargers [36] |
It is a contactless charging technology. No cables are utilized between the EV and the electricity network [8]. Instead, the electrical energy transfer is based on electromagnetic induction [9]. | It is a contactless charging technology. No cables are utilized between the EV and the electricity network [37]. Instead, the electrical energy transfer is based on electromagnetic induction [38]. | Figure 6 illustrates the concept of this EV charger type [10]. Compared with conductive chargers, these inductive chargers present various advantages [11]. Especially the convenience for the user and the intrinsic galvanic insulation, while the cost and the need for custom hardware inside the EV are the main drawbacks [12][13]. | illustrates the concept of this EV charger type [39]. Compared with conductive chargers, these inductive chargers present various advantages [40]. Especially the convenience for the user and the intrinsic galvanic insulation, while the cost and the need for custom hardware inside the EV are the main drawbacks [41,42]. |
Single-stage
&
Dual-stage chargers |
The first one consists of a single power conversion: only one ac-dc or one dc-dc power converter. The second one involves double power stages: ac-dc and dc-dc power conversions. |
Figure 16.
EV wireless charger overview diagram.
1.2. EV Charger Topologies
2.2. EV Charger Topologies
Figure 27 illustrates available structures which can be implemented for EV charger applications
[14][15][50,51].
Figure 27.
Possible structures for EV charger solutions.
In the dual-stage case, a bidirectional EV charger includes a dc-dc power stage following an ac-dc one. The first performs a power factor control (PFC) function and provides a regulated high dc-bus output voltage. In contrast, the second connects the EV battery to the high dc-bus voltage and ensures the energy exchange during G2V and V2G modes. In the G2V mode, the reversible ac-dc stage functions as a boost power rectifier with a unity power factor (UPF), whereas the bidirectional dc-dc converter works in buck mode to ensure the EV charge operation
[16][52]. In V2G mode, the reversible ac-dc stage functions as a power inverter with a possible reactive energy injection into the electricity network, whereas the bidirectional dc-dc stage starts operating in a boost converter to ensure the energy exchange from the EV battery to the dc-bus
[17][18][23,53]. In the single-stage case, the EV charger has only one ac-dc or one dc-dc stage
[19][20][19,54].
Figure 38 shows the electrical schematics of the commonly used bidirectional ac-dc power conversion stage in EV chargers.
Figure 38a shows a bidirectional half-bridge single-phase ac-dc power converter.
Figure 38b shows a bidirectional full-bridge single-phase ac-dc power converter
[20][21][54,56].
Figure 38c shows a bidirectional three-phase ac-dc power converter. Finally,
Figure 38d shows a bidirectional three-level diode-clamped ac-dc power converter
[22][57]. It is worth noting that bidirectional multilevel three-phase ac-dc power converters are recommended for high-power EV chargers
[23][58]. These converters afford a high level of energy quality with a high-power factor, low total harmonic distortion (THD) rate, and lessened electromagnetic interference noise on the grid side. Besides, they offer a high level of dc voltage that is ripple-free, tightly regulated, and impervious to load and source disturbances on the dc-side
[24][59].
|
|
|
-
|
|
Charging power up to 400 KW (Typ. 50 KW)
|
-
|
- -
-
Charging current up to 400 A (Typ. 50 A) -
- -
-
Estimated charge-time for 100 KW: -
|
|