3D printing (3DP) is a manufacturing technology that produces 3D objects from a design file using layer-by-layer deposition of material. It has already found applications in the healthcare and pharmaceutical industries. There are potential uses for 3DP in the cosmetic field.
1. Introduction
Stratum corneum (SC) acts as an efficient barrier against physical, chemical, and microbiological xenophobes, preventing their penetration into the skin. However, this excellent barrier is a limiting factor for the penetration of cosmetic active ingredients (also known as actives) into the skin. Skin delivery from topical formulations is known to be very inefficient, with typical bioavailability of less than 2% of the applied dose
[1]. A good example is caffeine, a well-studied cosmetic and pharmaceutical active ingredient, also a model hydrophilic compound in skin toxicology. Summarising a series of studies conducted with different topical caffeine formulations, a review article
[2] has established that the highest penetration from conventional ointment formulations was only 0.0062%.
Therefore, it is crucial to explore all available means for more efficient delivery of topical (cosmetic and pharmaceutical) active ingredients into the skin. Many technologies have been studied and developed so far, including penetration enhancers, supersaturation, and a wide range of skin delivery systems (e.g., liposomes, niosomes, transfersomes, lipid nanoparticles, polymeric microparticles and nanoparticles, patches, and microneedles). One of the relatively recent approaches is the use of 3D printed platforms (carriers).
3D printing (3DP) is a manufacturing technology that produces 3D objects from a design file using layer-by-layer deposition of material. It offers some advantages over traditional manufacturing techniques, such as one-step fabrication and customisation
[3]. In addition, 3D printing has shown potential in increasing skin delivery efficacy and user compliance
[4].
The healthcare and medical industry has already benefited from 3DP with versatile applications, from 3D printed pharmaceuticals in solid and semisolid forms
[5][6][5,6], to those with complex release profiles
[7]. In addition, there are 3D printed medical devices, such as patient-specific implants and hydrogel grid wound dressings
[8][9][8,9], many of them approved by the United States Food and Drug Administration (FDA)
[10].
However, the number of applications of 3DP in skin delivery is relatively low, with limited choice of 3DP-specific materials being the biggest obstacle. This is because specific physico-chemical properties, such as photosensitivity or thermal sensitivity, are required for the solidification process of the inks during 3D printing in order to provide the structure of 3D objects; in addition, some 3D printing technologies require the ink to be within certain viscosity range
[11]. Another obstacle is high initial investment necessary to increase the production output. Extensive studies in skin delivery have only been carried out in the last two decades
[12], and have demonstrated a considerable potential of 3DP in this area.
2. Types of 3D Printing Technologies
Based on the process involved, the American Society for Testing and Materials (ASTM) has classified 3DP technology into seven types, the overview of which is given in several articles
[13][14][16,17]. Among these methods, fused deposition modelling (FDM) and stereolithography (SLA) have been the most popular 3DP technologies for the fabrication of skin delivery platforms. In recent studies, digital light processing (DLP) and two photon-polymerisation (TPP) were also used
[15][16][18,19]. In addition, ink jet printing is applied for the loading of active ingredients in the post-platform fabrication processes
[17][18][20,21].
All currently used types of 3D processes could be classified into three broad categories: ink jet printing, extrusion-based and photopolymerisation-based, and are summarised in
Table 1.
Table 1. Three categories of common 3DP technologies [13][14][19]. Three categories of common 3DP technologies [16,17,24].
3DP
|
Schematic Diagram
|
Ink
|
Printing Method
|
Ink jet printing
|
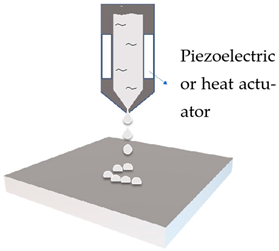
|
Emulsion
|
Drop-on-demand controlled by the actuated printhead
|
Extrusion based printing
|
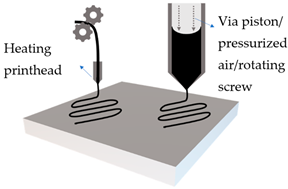
|
Solid filament
|
Mechanical roller with heating, to extrude solid filament
|
Viscous emulsion
|
Pressure or mechanical extrusion of viscous emulsion
|
Photopolymerisation
|
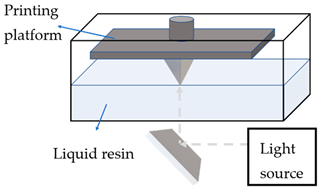
|
Photopolymerisable liquid resin
|
Solidifying polymer via photopolymerisation,
with either moving light source or moving printing platform
|
3. Types of 3D Printed Delivery Platforms
Skin patches and microneedles (MNs) have emerged as the two main types of 3D printed platforms. Due to the same principles of skin delivery of cosmetic and topical pharmaceutical formulations, the developments in both will be reviewed in this section.
Skin patches are the most used and studied among all device-based skin delivery systems. They have a long history for treating skin conditions
[20][42] and have also been used for transdermal delivery. A recent review article reported research work conducted on conventional skin patches, in terms of their active ingredients, materials, delivery enhancers, characterisation methods, and results
[21][43]. Standard methods for the fabrication of skin patches include solvent, hydrogel, and hot melt-based means
[22][44].
Patches closely adhere to the skin and could be designed with or without separate adhesive support, which will be either loaded with active ingredients or saturated with active ingredients from the reservoir
[23][45], as demonstrated in
Figure 1. The adhesive property of patches strongly affects the delivery of active ingredients, and in turn their efficacy
[24][25][46,47]. They create a continuous occlusion which increases skin penetration by providing a strong driving force for the diffusion of active ingredients
[26][48].
Figure 1.
Schematic diagram of three types of conventional multi-layered skin patches.
Theoretically, cosmetic patches have the potential to tackle many cosmetic skin problems, such as wrinkles, pigmentation, and the effects of aging
[27][49]. The main disadvantage of conventional patches is the low quantity of active ingredients that could be loaded and delivered. The mechanism of drug absorption from a patch-like device starts with its release from the patch, its penetration and then storage in the stratum corneum, at which point it might crystalise and prevent further transport
[28][50]. The next stage is diffusion of the active to the deeper layers of skin, and, if applicable, into the systemic circulation, causing a controlled delay of the therapeutic effect
[28][50]. Another disadvantage is a possible inconsistent diffusion rate of the active ingredient from skin patches, which depends on the skin condition of individuals. This includes skin hydration state, age, and ethnicity, with the SC being a rate-limiting barrier. In addition, the delivery strongly depends on the type and physicochemical properties of the active
[3].
Conventional adhesive patches have multilayer structures and are classified by the layer in which the drug/active has been loaded
[24][25][29][30][46,47,51,52], as shown in
Figure 1. Therefore, the fabrication involves a multi-stage process
[31][53]. In contrast, 3D printed patches are mostly made of one material in a single layer, although there is a potential for the multi-layered printing. Due to the flexible nature of the 3D printed patches, researchers have been exploring the potential of drug-loaded 3DP mesh or 3DP grid patches for implantation within tissues and to support organs
[32][54].
Overall, the development of 3DP patch platforms is an ongoing research area, with a potential to improve current skin delivery designs.
Microneedles (MNs) have evolved as a hybrid of two conventional skin delivery systems, skin patches and hypodermic injection needles, with some advantages of both, such as ease of administration, being minimally invasive, and enabling high bioavailability of active ingredients
[33][55]. An MN platform is typically composed of micro-sized, needle-like structures attached to a patch (backing) for ease of application. This delivery platform is sometimes referred to as a MNP (microneedle patch). In comparison to patches and semisolid topical formulations, microneedles are more versatile and more efficient in delivering active ingredients into deeper layers of the skin. Instead of relying on passive diffusion, microneedles can actively enhance the delivery by piercing the epidermis (0.1–0.2 mm) and, if so designed, the dermis (1–2 mm), creating microscopic channels
[34][56]. These microscopic punctures could overcome the skin barrier and provide an alternative route for enhanced transport of drug or cosmetic active in a painless, minimally invasive manner
[35][57].
Table 2 provides a summary of the common types of MNs. Some novel MNs not only serve as a delivery platform, but also as a wearable therapeutic device for real time monitoring
[36][58].
Table 2. Classification of MNs [37][38][39][40]. Classification of MNs [59,60,61,62].][47][67,68]: the perforations they create could induce elastin and collagen expression and deposition, stimulating the metabolism in the upper skin layers, as well as the natural healing of the skin.
Table 3 illustrates the mechanism of skin delivery of different types of 3D printed solid MNs, including coated MNs, dissolving/swellable MNs (DMNs), and hollow MNs. Further details and diagrams could be found in several review articles which focus on microneedle skin delivery platforms, including their characteristics and their typical delivery mechanisms
[39][48][49][61,69,70].
Table 3.
Schematic diagrams of common types of 3D printed MNs before and after application.

|
| —MN loaded with active ingredients;
|
 |
|
| —solid needle; |
|

|
—dissolving/swellable needle;
|

|
—stratum corneum.
|
There is an argument that dissolvable MNs (DMNs) might not be an ideal platform for cosmetic use, due to the potential loss of hydration through the perforations made in the skin. However, it has been shown that a novel design of DMNs, loaded with a barrier-restoring active ingredient, horse oil, has significantly improved dermal density, skin elasticity and moisturisation level
[50][71].
Very few published studies have reported a detailed 3DP manufacture of the dissolving MNs, and none has studied the use of sugar-based biopolymers
[51][72]. It remains challenging to fabricate DMNs with 3DP other than by micro-moulding methods, due to the lack of the printability of dissolvable polymers.
3.1. Fabrication Methods
Fabrication Methods
Conventional MN fabrication methods can be classified into several categories: (1) moulding method, (2) lithography, (3) droplet-born air blowing (DAB) method, some followed by coating or deposition process to produce coated MNs
[33][49][52][53][54][55,70,73,74,75].
As described by Kim et al., DAB was a popular DMN fabrication method
[55][76], adopted by many researchers who have successfully fabricated DMNs and assessed their effects in improving skin delivery of cosmetic active ingredients
[56][57][58][59][77,78,79,80]. This method was gradually abandoned with the development of centrifugal lithography (CL)
[60][81] for DMN fabrication. Due to the self-shaping nature of viscous polymer solution, continuous transformation under centrifugal force is induced in the CL process. Polymer drops dispense on the inner plate of two parallel fixed plates, and, upon the separation of plates, DMNs with two different shapes have been formed on the top and bottom plates, respectively. Morphological observation, fracture force analysis, and in vitro skin penetration tests have shown that both DMNs platforms could achieve an efficient diffusion and permeation of active ingredients through the skin
[61][82]. It is worth mentioning that no additional environmental stimulation is required for producing DMNs using CL. The usual problems related to other fabrication methods, such as the loss of activity of cosmetic ingredients when exposed to UV irradiation, heat, and air, do not exist in CL. However, CL-produced MN shapes are extremely limited, with little variation of the natural droplet shape, which points to the necessity of studying the use of 3DP technology in the fabrication of DMNs.
Apart from the use of FDM and SLA, the two most common 3DP technologies, microneedles have also been successfully produced using some novel 3DP technologies, including DLP, CLIP, and TPP.
An investigation on the use of high precision DLP for the 3D printing of hydrogel MNs in terms of the process parameters were performed by Yao et al.
[15][18]. A dye rhodamine B was used as the model compound for the platform characterisation. Its loading was achieved through soaking of the DLP printed MN in the dye solution. The authors have concluded that the long exposure time enhances the stiffness of MNs, and that with the use of hydrogel, the drug loading capacity was greatly increased. There was also a significant decrease in the fabrication time, which only took a few minutes
[15][18].
The DLP printing of personalised and flexible MN patches has been extensively studied by Lim et al.
[62][83], e.g., the MN patches to treat the trigger finger, which is not achievable with conventional MNs
[62][83]. Their more recent studies on printing MN periorbital patch focused on the relationship between geometries of these microneedles to their mechanical strength and skin penetration efficiency
[63][64][84,85]. The fabrication involves two steps: the DLP printing of flat MN patches, which are then compressed against a FDM-printed curved substrate to generate flexible, curved MN patches. Acetyl-hexapeptide 3 (AHP-3) is a small peptide and anti-aging active, with very poor skin penetration due to its hydrophilicity and high molecular weight. With the aid of the optimised DLP-printed MN periorbital patch, enhanced anti-wrinkle effect was achieved with significantly improved AHP-3 delivery
[63][64][84,85].
Different materials and geometries with various aspect ratios of MNs were attempted by Johnson and co-workers
[65][37], using CLIP technology. Square pyramidal needle shape was found to be the most suitable design for encapsulating and delivering a wide range of active ingredients. That shape has been shown to effectively pierce the skin and achieve controlled release of drug, based on the fabrication process of less than 10 min
[66][86]. Another more recent work successfully demonstrated a rapid fabrication method of DIP coating CLIP microneedles for transdermal delivery of therapeutic proteins, achieving a high degree of control over microneedle design parameters
[65][37].
The recent study by Cordeiro et al.
[16][19] has shown that highly precise and reproducible MNs could be successfully manufactured using TPP technology to make silicone MN moulds. MNs with various needle shapes and lengths were then produced by a micro-moulding method. Polyvinylpyrrolidone (PVP) and polyvinyl alcohol (PVA) liquid blend and Polyvinyl methyl ether/maleic acid (PVM/MA) copolymer and poly(ethylene glycol) (PEG) liquid blend were prepared and poured in the silicone moulds to produce dissolvable and ‘super-swellable’ MNs, respectively
[16][19].
The above 3DP technologies generally have high printing resolution and precision, producing micro-sized needle shapes highly suitable for MN-type skin delivery systems. Although significant development in this area has been made, the research is still not widely carried out due to the cost and the need of specialist equipment. It is envisaged that more extensive research will be carried out with further development of 3DP technologies.
4. Materials Used in 3DP Platforms
Common 3DP ink materials adopted for cosmetic-relevant application are listed in
Table 4.
Table 4.
3DP materials (via direct fabrication only) relevant to cosmetic applications.
Material
|
Characteristics
|
Cosmetic Benefits
|
3D Printability
|
Carrageenan (sulphated anionic polysaccharide)
|
Simple cold-setting gelation, biodegradable, renewable, safe, low cost, viscoelastic properties, so it can be modified easily.
No addition of additives or initiators required.
|
As stabiliser and thickener for emulsions, to achieve desired product consistency, hydration.
|
Extrusion method: gel strength linearly increases by decreasing printing speed and layer height, at printing temperature below ~80 °C [67][88]. Addition of crosslinkers, methylcellulose and cellulose nanocrystal, can improve rheological behaviour and compressive mechanical strength [68][89]. The pore size of 3D printed structure is adjustable, produces soft and flexible structure [69][90].
|
Chitosan (synthetised cationic polysaccharide from deacetylation of chitin)
|
Low-cost production, biodegradable, hydrogel can be produced by various ways (both physical and chemical crosslinking). Controlled release of actives is possible. Low water solubility at neutral pH and low mechanical integrity of 3D printed structure.
|
Absorbs UV, used in sunscreens; has intrinsic antimicrobial and antifungal properties, moisture absorbing properties, acts also as emulsion stabiliser [70][91]. |
From coated layers on the surface of MNs
|
|
Extrusion method and photopolymerisation method, widely used for studies on 3D-printed wound dressing due to bioactivity, flexibility, and self-adhesion properties of 3D printed patches. The addition of other biomaterial could increase the printability [71][92]. Chitosan was also studied as a coating for MNs, where it increased drug loading capacity
Efficient drug delivery with precise amount
|
[72][93].
Low drug loading
|
Dissolving/separable
|
|
Hyaluronic acid
(linear, weak polyanion, non-
sulphated glycosaminoglycan)
| Poke and release
|
Hydrophilic, biocompatible, and biodegradable, viscoelastic.
Encapsulated within hydrophilic polymer matrix
|
It possesses skin regenerating and collagen stimulating efficacy, with hydrating, anti-wrinkle, and anti-aging effects [73][94]
Dissolve upon insertion after minutes
|
Extrusion based: widely used in wound healing [74][95]. 3D printed hydrogel can achieve controlled release of actives [75][96]
Safer, larger dose, no biohazardous waste, facilitate rapid delivery of macromolecules
|
Clogging, can be resolved by side opening on the tip
|
Hollow
|
Cellulose (nano-
cellulose, bacterial cellulose, and other derivatives; polysaccharide)
|
Poke and flow
|
Most abundant biopolymer, sustainable, biocompatible, high strength, high elasticity.
Within liquid reservoir
|
Produces facial masks for prolonged release of actives [76][97]. Used as UV filter [
Pressure-driven delivery of liquid formulations
|
77
Large amount of formulation loading
|
Possibility of blocking by skin tissue, complex design
|
Swellable (hydrogel-forming)
|
Poke and release
|
Within voids of polymer matrix
|
Upon absorption of skin interstitial fluid, forming continuous unblockable microchannels for active delivery
|
Intact removal of MNs array after use, leaving no polymer residues
|
Limited drug loading, low ability to perforate skin, weak mechanical strength.
|
A recent review paper
[41][13] has provided a comprehensive report on the studies on cosmetic application of microneedles. It summarises MN materials and categorises MN studies in terms of the targeted skin problems.
3D printing could be used in three different ways in the manufacture of an MN platform: (1) to develop ‘male’ master moulds; (2) to coat active ingredients onto previously prepared MNs and (3) to print complete MN structures.
Research on 3D printed cosmetic microneedles is still in its early age. However, several published papers and patents have shown the feasibility of delivering both hydrophilic and lipophilic active ingredients by microneedles that are fabricated by methods other than 3DP
[42][43][44][63,64,65], proving that this concept is viable. One study has compared the wrinkle improvement by two different delivery platforms (dissolving MNs and standard formulation, both containing hyaluronic acid); after eight weeks of treatment, the MNs have shown higher effectiveness
[45][66].In general, all MNs enhance skin delivery via micro-channels they create, partly bypassing the skin barrier. In the case of wrinkle improvement, there is a second mechanism
[46140]. Using the printing angle of 45°, the MNs appeared not only sharper but also without defects. However, the optimisation of printing quality and geometry accuracy differs significantly between the 3DP technologies, so it remains challenging to print sophisticated micro-sized needles.
The process of insertion of NMs into the skin has been evaluated by several methods. The penetration test using the membrane that mimics human skin was employed to determine the rate of piercing and the rate of needle breakage after the insertion
[101][31]. Another approach used dye solution applied on the surface of the skin sample, before applying and removing MNs, and analysed the coloured holes produced. In the same study, when the insertion speed was kept constant at 0.5 mm/s, the predicted minimum insertion force through a multilayer skin structure obtained through modelling by Finite Element Analysis for each MN was above 0.03 N. This was consistent with their experimental result of 0.069 N and the literature
[103][34].
Texture analyser has also been employed with skin samples to quantify the insertion of the MN platform, by reporting the continuous force and displacement of microneedle arrays fixed on the top of a moving probe
[108][141]. The mechanical strength or fracture point of MNs were measured in various ways. Transversal, axial, and bending forces were exerted on the MN array to determine the point of mechanical failure by mechanical testers; the shear resistance was also measured
[84][105]. It was found that the 3D printed MNs could be refined post-printing via etching (when using FDM)
[101][31] and post-curing (when using SLA)
[107][140].
Since transepidermal water loss (TEWL) reflects the integrity of the skin barrier, changes in TEWL have also been used to evaluate the effects of MNs penetration
[97][109][29,142].
Comprehensive evaluation on the physico-mechanical properties of 3D printed platforms is important for their development and optimisation. For FDM-produced 3DP hydrogel patches and dissolving MNs, the addition of actives may significantly change rheological properties of the formulation, leading to a varied mechanical strength of the MNs after solidification process. In such cases, rheological characterisation is being used to evaluate and regulate their viscosity
[47][84][68,105]. For developing dissolving MNs, it is vital to understand the process of MNs degradation, since the actives are released during this process. SEM provides information on any change in porosity and formation of cracks in the MN structure, while DSC and X-ray diffraction measure the change of crystallinity of the polymer. Since the crystalline region of the MN is where the integrity of the polymer structure was maintained, amorphous regions start to degrade or dissolve first
[110][30].
6. Release and Skin Delivery of Actives Used in 3DP Platforms
This section presents a review of the release and penetration studies that have been performed on 3DP platforms in order to study them as carriers for pharmaceutical and cosmetic active molecules.
Even though a series of examples of 3D printed patches for wound healing have been discussed, the delivery mechanism is different from the one occurring in cosmetic application, since the application sites normally do not have a functioning skin barrier.
All published studies related to the use of 3D printing for the delivery of cosmetic active ingredients are summarised in
Table 5, including potential ones. The use of standard delivery platforms (patches and MNs) is widely studied
[27][41][85][111][13,14,49,106], but very few attempts have been made with 3D printed skin delivery platforms. Some methods normally used for tissue engineering, wound dressing, and food industry might be transferable for cosmetic applications.
Table 5.
An overview of cosmetic benefits, active ingredients and 3DP platforms investigated so far.
Cosmetic Benefits
|
Active Ingredient
|
Characteristics
|
3D Printed Delivery Platforms
|
Anti-wrinkle
|
Acetyl-hexapeptide 3 (AHP-3)
|
Peptide, hydrophilic, large MW.
|
DLP 3D printing of polyethylene glycol diacrylate (PEGDA) and vinyl pyrrolidone (VP) to produce personalised MN patch. AHP-3 was loaded by mixing in pre-polymer resin, but not incorporated in the polymer structure, aiming for easy release from the printed MNs [64][85].
|
|
Alginate |
|
(anionic linear polysaccharide) |
|
| Biocompatible, biodegradable. High strength.
|
Anti-acne (anti-microbial)
|
Salicylic acid
|
Obtained from plant extract. Beta-hydroxyl acid, small MW, potentially good skin penetrant.
|
Salicylic acid was loaded to polylactic acid by hot melt extrusion. 3D printed nose patch made by FDM failed due to its complex structure.
Flexible nose patch was successfully fabricated with PEGDA and PEG using SLA printer [112][27].
|
Moisturising. Used for production of biodegradable cosmetic patches.
|
Extrusion based: studied for wound healing [84] |
Anti-aging and anti-acne (antioxidant and anti-inflammatory properties); skin-whitening
|
Resveratrol
|
Obtained from plant extract, polyphenol phytoalexin. Skin permeation from aqueous was better than from oily system [113][143].
|
][98].
|
Extrusion-based [78][99]. Direct ink writing 3DP and freeze drying to produce versatile aerogels [79][100].
|
| Extrusion based method followed by freeze-drying for the fabrication of 3DP edible oleogel from emulsion containing gelatin and gellan gum. The bioactivity of actives has improved. The method has potential to produce cosmetic soft patch with resveratrol. |
|
Skin-whitening/lightening
|
Hydroquinone
|
Inhibits melanin synthesis, side effects related to long-term application [114][144]
|
It has been used an initiator for SLA 3D printing in producing wound dressings [115][145]
|
Collagen (protein)
|
Biocompatible, low antigenic, biodegradable, highly soluble at neutral pH.
|
Derivatives are antioxidant, UV protective, anti-aging, moisturising.
|
Extrusion-based, studied for wound healing. Due to the porous nature of the 3D printed structure, actives could be easily coated [80][101].
|
Gelatin
(derived from collagen)
|
Low toughness, various modification methods available to improve its low melting point and poor stability.
|
Reduces the effect of photo aging and oxidative damage. UV protection [81][102].
|
Photopolymerisation with the addition of photo initiator [82][103]; UV exposure time and shape affect the release; both can be controlled [83][104].
|
[105].
|
Polylactic acid
(PLA, thermoplastic polylactide)
|
Biocompatible, high elasticity, may cause inflammation.
|
As makeup products additive. For development of biodegradable novel cosmetic delivery platform [85][106] and for packaging [86][87][107,108]. For producing novel cosmetic emulsion [88][109].
|
Extrusion method (FDM) to produce 3D printed specimen of cosmetic container [86][89][107,110], also used for coated microneedles [90][32].
|
Polyvinyl alcohol
(PVA, synthetic polymer)
|
Biocompatible, water soluble, stable to temperature variations, film forming.
|
Producing cosmetic delivery platforms and peel-off masks [91][111], also nanoparticles for cosmetic emulsions [92][112].
|
Extrusion method and photopolymerisation method (DLP).
|
Poly(vinyl pyrrolidone) (PVP, linear polymer)
|
Low toxicity, inert and biocompatible, brittle, low reactivity towards photopolymerisation, can be adjusted by addition of another photopolymer.
|
Produce metal-coated [93][113] and dissolving [94][114] cosmetic MNs.
|
Photopolymerisation method (DLP) [64][85].
|
5. Characterisation of 3DP Platforms
Testing for stability, safety, and efficacy is a fundamental requirement and must be carried out for both cosmetic and pharmaceutical products. In addition, there is a wide range of physico-mechanical characterisation methods, which could help formulators in their development work, enabling predictions of how products will behave during their production, storage, and use. Some of these methods have the potential to reveal the interactions between active materials and the components of the base. This in turn could explain the observed stability issues, the rate and extent of active ingredient release and ultimately the product efficacy.
Due to the novel nature of the 3DP platforms, a possible interaction (or the lack of it) between the carrier and the active is particularly important. Two aspects of 3DP platforms should be considered: characterisation of finished 3D printed products and characterisation for optimisation of printing process (including intermediates, such as printing filaments).
In terms of the final product, researchers normally report basic physical parameters of the 3DP platforms, including their morphology, geometry, density, and mechanical strength (patch stiffness). For optimising the printing process with extrusion-type 3D printers, the most commonly listed properties for filament polymers include molecular weight, which is measured by gel permeation chromatography (GPC)
[95][124], as well as thermal properties and crystallinity, which are measured by differential scanning calorimetry (DSC) and X-ray diffraction, respectively
[96][135]. These methods are used in addition to well-established standard characterisation techniques for active molecules via in vitro/in vivo permeability studies.
Regarding the 3DP patches, few characterisation methods have been used. Rheological properties, gel strength and bio-adhesive properties are key to an effective 3DP patch. Texture analysers and rheometers are mostly used to determine the printability of active -loaded ink, especially important for extrusion-based 3DP technologies
[69][90]. In addition, the pH of the 3DP patch must be suitable for topical use and its pH value, when in contact with moisture, should be close to the pH of human skin
[97][29].
For 3DP microneedles, the two properties that have drawn most attention are their geometry and their mechanical properties, which can be further divided into insertion force and mechanical strength (failure test), performed by theoretical simulation and/or experiments
[53][74].
Various geometries of MNs have been studied to achieve more defined tip of microneedles, which directly relate to the ability to perforate the SC
[98][136]. The most common shape of MNs are cones, with different aspect ratio, height, interspace, tip diameter and base diameter
[99][121]. There is no standard for the best geometry; in addition, the performance of MNs vary depending on the materials and 3D printers used. Therefore, each parameter must be studied in relation to various ink formulations and 3DP parameters in order to be optimised. Pyramid, cross and spear shapes are also studied, obtained by SLA or other 3DP technologies that have higher resolution
[100][26]. Although FDM printers are easy to use, fast and cost-effective, the technique is generally not suitable for printing the fine structures of MNs. The extrusion manner of printing makes it difficult for printed layers to adhere to one another when the printing area is very small (for sharp tips). Therefore, only shapes that gradually change from the bottom to top could be printed by the FDM method.
The observation of platform morphology and the measurement of their dimensions have been carried out using optical microscopy
[101][102][31,137], scanning electron microscopy
[102][103][34,137] and in vivo imaging techniques
[104][138]. Image analysis is particularly useful, because it visualises the shape and uniformity of the MN array, allowing checking for any defects
[105][132].
MN platforms are normally applied by pressing them into the skin with a thumb, hence MNs must have sufficient mechanical strength to provide efficient delivery of the actives into the skin
[106][139]. The upper surface of the skin experiences viscoelastic deformation while being perforated with an increasing force. There is a minimal force necessary to punctuate the intact skin, which must not exceed the maximum force that an individual micro-sized needle can withstand, otherwise the needle will break or fracture before piercing the skin
[105][132]. Therefore, it is important to consider mechanical properties of MNs when designing MN platforms.
A study by Davis et al.
[98][136] first quantified the effect of geometry to the fracture force of MNs. Their theoretical and experimental analysis both led to the same conclusion: the insertion force varies linearly with the interfacial area of the needle tip
[98][136]. It has been proven by many further studies that the smaller the tip diameter, the easier the perforation
[103][34]. However, the tip diameter is limited by the resolution of the 3D printer, particularly for those using FDM technology. A recent study has shown that, by varying the tilted angle of the MN arrays during the SLA printing process, the tip diameter could be significantly changed
[107][