Figure 6. Scheme of the general formula of polyol, adapted from
[2].
The hydroxyl number (I
OH) represents the amount of hydroxyl groups available for the reaction with isocyanates. The number can be determined by the reaction of the terminal hydroxyl groups using organic anhydrides (acetic anhydride or phthalic anhydride)
[3]. The range of I
OH values of polyols required for the production of PUs is quite wide, e.g., polyether polyols used to produce rigid foams have I
OH values between 300–800 mg KOH/g, while for PU adhesives production the range of I
OH values is usually lower
[3][48].
The acid number is related to the amount (in mg) of potassium hydroxide needed to neutralize one gram of sample
[49]. The importance of the acid number is due to the fact that the presence of residual acidity decreases the catalytic activity of the tertiary amines used in the reaction of polyols with isocyanates to produce PUs. For polyurethane formulations, the acid number should be around 0.05–0.1 mg KOH/g for polyether polyols, and 2 mg KOH/g for polyester polyols
[26].
Water content is also an important issue since isocyanate groups are highly reactive towards water; thus, it competes with the hydroxyl groups of polyols during the synthesis of PUs. The determination of this characteristic is carried out by the classical Karl Fischer method, and the required values for producing PUs are between 0.05–0.1%
[3].
Viscosity indicates the processability of a polyol, which can be determined using a Brookfield viscosimeter or a rheometer. Furthermore, it can provide an indication of the reactivity of a polyol with an isocyanate to afford the final PU. It was observed that polyols with low reactivity (0% primary hydroxyl, i.e., having only secondary hydroxyl groups) have the lowest viscosity increase over time. In turn, highly reactive polyols, having 85–100% primary hydroxyl content, have the highest viscosity increase over time
[3]. For the production of PUs, the range of viscosities can be wide, depending of the type of PU, but must be below 300 Pa.s
[26].
The molecular weight (MW) and polydispersity of polyols can be rigorously determined by size exclusion chromatography (SEC), also known as gel permeation chromatography (GPC). The molar mass sensitive detection is based on both viscometry and universal calibration
[50]. The MW is an important parameter because this feature will impact the network structure and crosslinking density, which influences the physical properties of PUs. Generally, for use in the production of polyurethane foam (PUF), polyols that have large MW will lead to amorphous regions that impart flexibility to Pus, whilst polyols with low MW will lead to rigid PUs
[3]. Regarding the required values for PU production, in general, polyols have MW in the range of 400–5000 Da, depending on the type of PU product
[51].
Since lignin has a very complex structure and variable characteristics, LBPs must be well characterized in order to better predict the behavior of the ensuing PUs and understand the relationship between the structure of the polyol and the properties of PUs. The difficulty in characterizing these structures has led many researchers to characterize only the most essential features of LBPs such as the I
OH, viscosity, and MW, as is normally performed for petroleum-based polyols, as mentioned earlier. Nevertheless, the characterization of LBPs can be quite complex and can present some challenges. Hence, it must be performed carefully, and sometimes different methods need to be used when compared to their petroleum-based counterparts. For example, the determination of the number of terminal hydroxyl groups of petroleum-based polyols involves the esterification of the alcohols with acetic anhydride or phthalic anhydride using solvents/catalyst such as pyridine or N-methylimidazole
[52]. However, the dark color of LBPs can induce significant errors during the conventional titration using phenolphthalein as an indicator. Potentiometric titration circumvents the problem, but sterically hindered alcohols and phenolic alcohols present in LBPs can result in some inaccuracies. The alternative is to use
1H NMR and
13C NMR spectroscopies to quantify the number of hydroxyl groups
[53].
GPC is one of the most commonly used techniques to determine the average molecular weight of polyols. The eluents used can be organic solvents (THF, DMF, or DMSO)
[54]. Polystyrene standards are frequently used to obtain the calibration curve, though in the case of lignosulfonates, polystyrene sulfonates standards have also been used. With regard to the detectors and characteristics of the columns, the ultraviolet (UV) or refractive index (RI) detectors are the most common, whilst the type of column depends on the molar mass range of the polymer and eluent compatibility. Yet, care should be taken for lignin-derived polyols because the UV detector is not always accurate, due to the different extinction coefficient of lignin fractions. Typically, mixed pore columns are preferred due to the larger range of linear calibration. However, LBPs can present some issues due to their complex structure.
5. Lignin as a Building Block to Synthesize Polyurethanes
The use of lignin in the production of PUs can be carried out in different ways: unmodified, being directly incorporated into polyol formulations, after fractionation, or after chemical modification (in order to make it more reactive), alone, or in combination with other polyols [24][25][55][56][57][58][59][60]. Depending on its interaction with the isocyanate, lignin can act as filler or as reagent, i.e., as polyol, also referred to as cross-linker. Although the use of lignin without any treatment is widely reported, if its OH groups do not react with the isocyanate and become chemically bonded to the PU network, it should not be described as a building block. The direct exploitation of lignin, as a polyol on its own or blended with industrial polyols, is energetically and environmentally advantageous [61], and the ensuing biomass-based PUs are more biodegradable than those derived from petroleum-based polyols. Even though the direct use of lignin as the only polyol can be very appealing, generally, lignin macromonomers have low reactivity towards isocyanate groups yielding products without the desirable performance, and end up acting essentially as fillers [24][62][63].
Recent advances to circumvent the drawbacks of direct incorporation of lignin as polyol in the production of PUs include (1) the use of diols and glycerol as compatibilizer and cross-linker, and (2) lowering the lignin molecular weight using solvent fractionation. Since kraft lignin is the most commonly produced technical lignin, most of the studies are focused on this type of lignin. For example, Haridevan et al. [64] recently evaluated the dispersion and solubility of kraft lignin in different types of polyols at room temperature for the production of polyurethanes based on microscopic, gravimetric, and rheological analyses. The study demonstrated that kraft lignin has different degrees of dispersion in various polyols, depending on the structural characteristics such as solubility parameter, molecular weight, and monomeric unit type. In fact, it was observed that a higher degree of dispersion of kraft lignin was achieved in the lower-molecular-weight diethylene glycol (106.1 g/mol) than in polyethylene glycol (400 g/mol). Although the low dispersibility of lignin in polyols has not yet been solved, systematic studies such as this one are important contributions to increase lignin dispersion. In addition, the performance of PUs can be improved by heating the polyol/lignin dispersions at 120 °C prior to the reaction, which enhances the disaggregation of lignin microparticles, yielding a better lignin dispersion within the polyol system [65][66]. On the other hand, reducing the kraft lignin molecular weight by solvent fractionation can enhance its miscibility and dispersion in the PU matrix, and consequently can improve some properties of the resulting PU such as the mechanical properties [67]. The use of binary organic solvent mixtures such as acetone–methanol [68], aqueous two-phase systems (ATPSs) composed of (NH4)2SO4 and ethanol [69], and the use of ionic liquids [70] are examples of strategies used to reduce the molecular weight of lignin as well as its heterogeneity. However, it is important to take into account that commercializing low-molecular-weight lignin has been economically unfeasible until now.
In addition to PUF, different types of lignins and LBPs have also been used to prepare other forms of Pus, such as adhesives [71][72][73], elastomers [74][75][76], coatings [77][78], and films [79]. Elastomeric PUs are a class of PU materials that have the characteristics of rubber, and their application has increased in recent years due to the high demand for advanced applications such as in biomedicine, shape memory materials, self-healing materials, and gel materials. Mechanical properties such as toughness, tensile strength, and high elongation at break are highly desirable for the production of PU elastomers, and the use of modified or unmodified lignin in the synthesis of PU elastomers has shown that it plays an important role in improving these properties, where a percentage of lignin up to 40 wt.% (based on mass of polyol) did not jeopardize their mechanical properties [80][81][82].
In conclusion, the properties of lignin have a profound impact on the resulting PU product performance, e.g., foams, elastomers, coatings, and films, regardless of the lignin source and isolation process [77][78][80]. Nevertheless, with the exception of a few examples, the exact role of the structural features of lignin during the reaction with isocyanates is hardly discussed. Instead, the mixture of unmodified lignin with other polyols or of LBPs is treated globally as the polyol component of the PU. Yet, with the advancement of fractionation methodologies, a better understanding of the role of structural features of this renewable OH-rich aromatic material will certainly become clearer and bring further insights.
6. Lignin as a Building Block to Synthesize Non-Isocyanate Polyurethane (NIPU)
The industrial synthesis of isocyanates involves the reaction between primary amines and phosgene at high temperatures (100–200 °C). The latter is a highly toxic gas, produced by the reaction between carbon monoxide and chlorine gas. In turn, diisocyanates cause acute adverse health effects, such as irritation of the respiratory tract, eyes, and skin, being a major cause of occupational asthma in workers employed by the polyurethane industry [83][84][85][86][87]. Moreover, the two most widely used isocyanates in the PU industry, MDI (methylene diphenyl diisocyanate) and TDI (toluene diisocyanate), are highly reactive chemicals that bind to DNA and are probably genotoxic [88]. Furthermore, various household PU products, such as mattresses, pillows, cushion packaging, and insulating materials in building construction, among others, exhibit detrimental environmental impact on aquatic life, soil health, plants, and humans due to the presence of toxic components such as isocyanates, flame retardants, and amine-based catalysts [89]. Additionally, some compounds, such as carbon dioxide, carbon monoxide, hydrogen cyanide, acetaldehyde, and methanol, are released when PU products are burned and/or landfilled at their end-life, contributing to the greenhouse effect and having toxic effects on human health [90][91]. All these reported issues led the European Union to adopt the regulation where it was proposed to reduce the content of isocyanate, with the main goal being to ban its use in the future [92].
There are a few routes described in the literature to synthetize NIPU, but the main ones are the rearrangement of acyl azide, the ring-opening polymerization of cyclic carbamates, the polycondensation (or transurethanization) between polycarbamate and polyol, and the polyaddition between bis-cyclic carbonate and diamines. Recently, some works
[90][93][94][95] dedicated to exploring the synthesis of NIPU were published, which identified that the most promising routes to produce NIPU are polycondensation and polyaddition (
Figure 7).
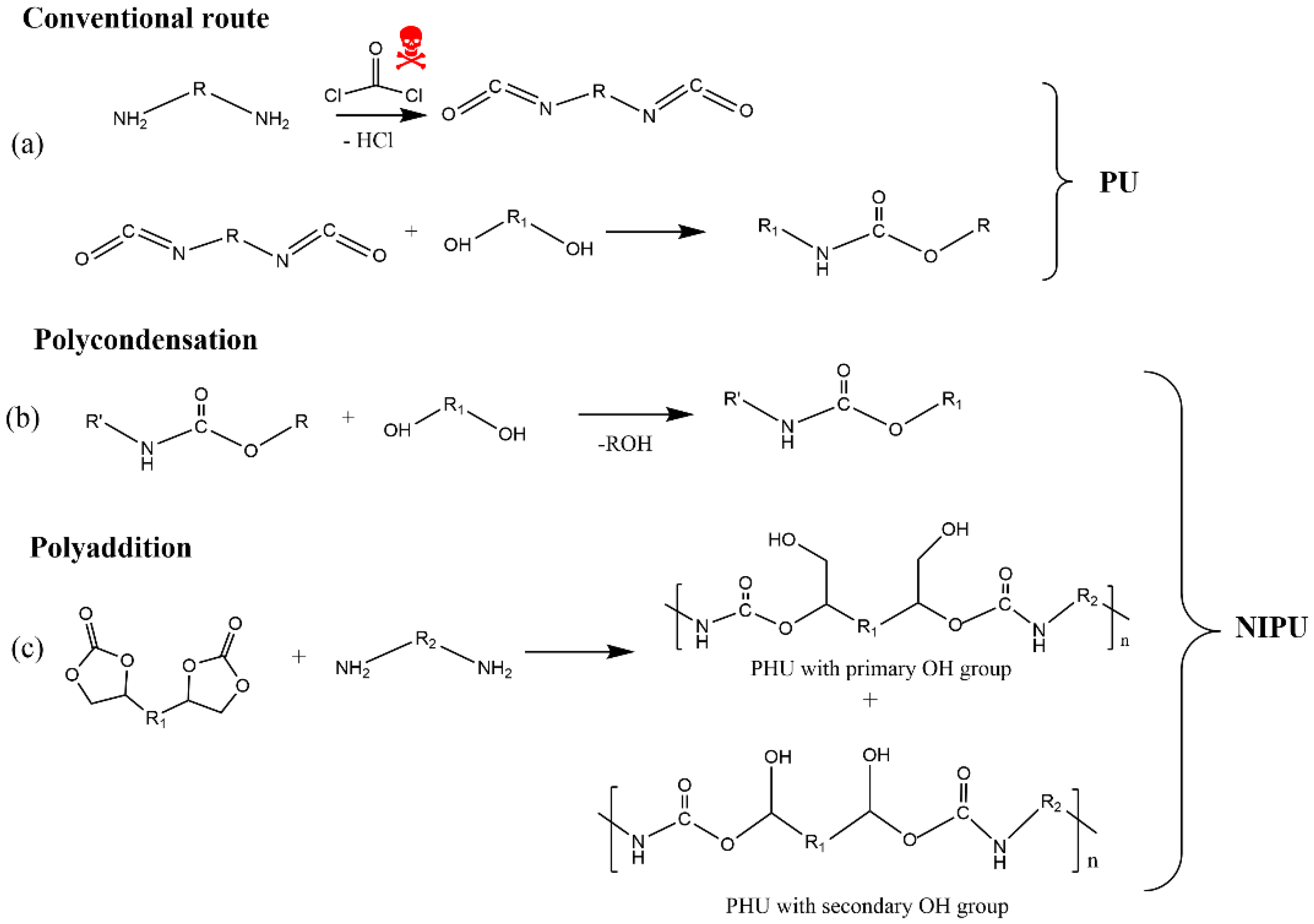
Figure 7. Chemical routes to produce PU by (
a) conventional route, NIPU by (
b) polycondensation, and (
c
The polycondensation reaction between carbamate monomers (bis-alkylcarbamates or bis-hydroxyalkylcarbamate) and a polyol affording urethane linkages have similar features compared to conventional PU. However, the polycondensation between bis-alkyl carbamates and polyol requires longer reaction times (over 24 h), higher temperatures (100–200 °C), and involves the formation of low-molecular-weight byproducts (i.e., methanol). Altogether, this has limited the extension of polycondensation on a commercial scale
[96].
Another approach to obtaining NIPU involves the polyaddition of di- or polyamines to bis-cyclic carbonate, yielding poly(hydroxy urethane)s (PHUs). The most common cyclic carbonates used to synthetize PHUs are five-membered cyclic carbonates, such as EC, PC, GC, and VEC (mentioned in
Section 4.1), and are already commercially available. Nowadays, the main route used to produce these cyclic carbonates is the carboxylation of epoxides, which is a less environmentally aggressive approach when compared to the previous synthetic route involving phosgene.
Beyond the strategies using phosgene-free routes to replace isocyanates, renewable resources have been extensively investigated to produce NIPU to obtain safe and green products. Recently, interesting papers were published, mainly focused on the synthesis of intermediate cyclic carbonates derived from renewable resources and their reaction with polyamines to produce bio-based NIPU
[97][98][99].
An alternative to the isolation of specific aromatic compounds from lignin is its use as a macromonomer in the synthesis of NIPU.
Kraft lignin powder was also reacted directly with DMC and then with a diamine (e.g., HDMA) to yield NIPU. The products obtained were tested as coatings on the surface of beech wood
[100]. In the same line of research, Arias et al.
[101] prepared NIPU bio-adhesives for wood panels, reacting kraft lignin, organosolv lignin, tannin, and soy protein with DMC, and the intermediate products were reacted with hexamethylenediamine (HDMA). The research group evaluated the environmental profiles of these novel adhesives using the life cycle assessment (LCA) methodology and compared them with formaldehyde-based resins. The results showed that these bio-adhesives have the potential to replace synthetic resins, as they have a lower damage score than phenol-formaldehyde resin.
Although it is clear that lignin has high potential to be used as a macromonomer in the synthesis of cyclic carbonates or even in the direct production of NIPU, its application still requires much research to further tailor the process and properties of these novel cyclic carbonates and NIPU.
7. Concludsion
On the one hand, technical lignin is a byproduct of the pulp and paper industry that consists of natural aromatic polymers with high carbon content and is a valuable energy source. For example, in the kraft pulp industry, lignin is used entirely for energy recovery. On the other hand, technical lignin has great potential to replace, at least partially, petroleum-based polyols used in the formulation of PU products. Yet, at the moment, to obtain an LBP that is competitive with petroleum-based polyols in terms of characteristics and price is still a challenge. Indeed, there is an old saying among the lignin experts: “you can make anything out of lignin, except money”. This is due to the difficulties involved in obtaining technical lignin with homogenous reproducible characteristics, the cost to convert the solid lignin in a liquid polyol or other chemicals, and the poor compatibility of lignin with many synthetic polymers. However, the pulp and paper industry, in cooperation with the chemical industry, have shown that it is possible to earn money from lignin, otherwise companies would not be investing in it. Although LBPs are not yet on the market, polyurethane foams with added lignin (20–25 wt.%) in the formulations are already a reality in the market. Furthermore, developments regarding the depolymerization and fractionation of lignin into well-defined oligomonomers are required to avoid the need for chemical modification. Indeed, these developments will also contribute to a better understanding of the relevance of the structural features of lignin during the reaction with isocyanates and/or other chemicals, as well as their exact impact on the properties of the ensuing PUs. Likewise, in-depth studies regarding the dissolution of lignin into polyols, especially those obtained from renewable resources, show that this is also a challenge, and an opportunity exists to make the use of this rich and versatile material economically and environmentally viable. As final recommendations on the development of lignin-based polyurethanes, researchers and industry should pay attention to LCA studies and technical–economic assessments. These studies are of paramount importance to find solutions regarding current challenges, such as technology scaling up for lignins and LBPs, high process and product cost, and different environmental and social impacts, as well as regulatory and policy implications.
Beyond the development of bio-based polyols to produce polyurethanes, significant efforts have also been made to replace the toxic isocyanate, developing non-isocyanate polyurethane. The main chemical route employed is the reaction between cyclic carbonates and diamines. Moreover, in recent years, lignin has been studied as a building block in the synthesis of cyclic carbonates for the development of new isocyanate-free polyurethanes. It is evident that there are still many challenges to be overcome, but what is expected is that in the future, technical lignin will be used as a raw material for the production of polymeric products such as polyurethanes, and not just burnt for energy, thus contributing to a more sustainable society.