The electrocoagulation process can be used for agro-based wastewater treatment. The performance of the electrocoagulation process is based on several parameters, including the electrode materials, electrolysis time, current density, and electrolyte support. Agro-based industrial wastewater (AIW) treatment processes depend on the characteristics of the wastewater. The removal of organic content from various sources of AIW can reach up to more than 80%.
1. Fundamental
1.1. Coagulation Principal
Coagulation is a traditional physicochemical treatment using phase separation for the pollutants of wastewaters before they are released to the environment
[1][42]. The addition of inorganic or organic compounds to the coagulation process destabilizes the particles, affecting the electrical double layer (EDL). The impact to the environment from the coagulation process in the generation of sludge makes the concern more serious in terms of management, treatment and operational cost
[2][43]. The sludge also contains residual metal ions from the coagulation process
[3][44].
Chemicals known as coagulants lower the energy barrier between particles. As a result of the weak bond, the particles can agglomerate more easily
[4][45]. Aluminium and iron metal salts are common coagulants used in wastewater treatment. Both metals can produce multivalent ions such as Al
3+, Fe
2+, and Fe
3+, as well as a variety of hydrolysis products. Because it oxidizes to Fe (III) during the coagulation process to increase efficiency, Fe (II) is a poor coagulant
[5][46]. Simple aluminium, iron sulfates, and chlorides are the most commonly used salts
[6][47]. The non-hydrolyzed metal coagulants include Al
2(SO
4)
3, FeSO
4, AlCl
3 and FeCl
3 [7][48]. Meanwhile, there is another metal coagulant that comes with several advantages, which is named pre-hydrolyzed metal coagulant
[8][49]. Examples of pre-hydrolyzed metal coagulants are polyaluminum chloride and sulfates
[9][50]. The pre-hydrolyzed metal coagulants have advantages such as being more effective than non-hydrolyzed metal coagulants and less sensitive to changes in pH and temperature
[10][51].
1.2. Electrocoagulation
Electrocoagulation by using metal hydroxide has a high ability to adsorb pollutants
[11][52]. The electrode materials commonly use Al and Fe. When the electricity is supplied into the electrode, the electrode will generate ions (Fe
2+, Fe
3+, and Al
3+) and produce the coagulant. The electrocoagulation reaction is usually followed by an electro-flotation reaction
[12][53]. The aluminium anode generates cationic forms such as Al
3+ and Al(OH)
2+ in acidic conditions. However, in alkaline conditions, these species are transformed into Al (OH)
3, dimer compounds such as Al
2(O)(OH)
4 and Al
2(OH)
24+. They can also can be transformed into a more complex compound
[13][54].
Figure 1 shows the schematic diagram of electrocoagulation. Several reactions happen during electrocoagulation for the production of hydroxides. For the electrode materials using aluminium, the oxidation takes place at the anode, as follows:


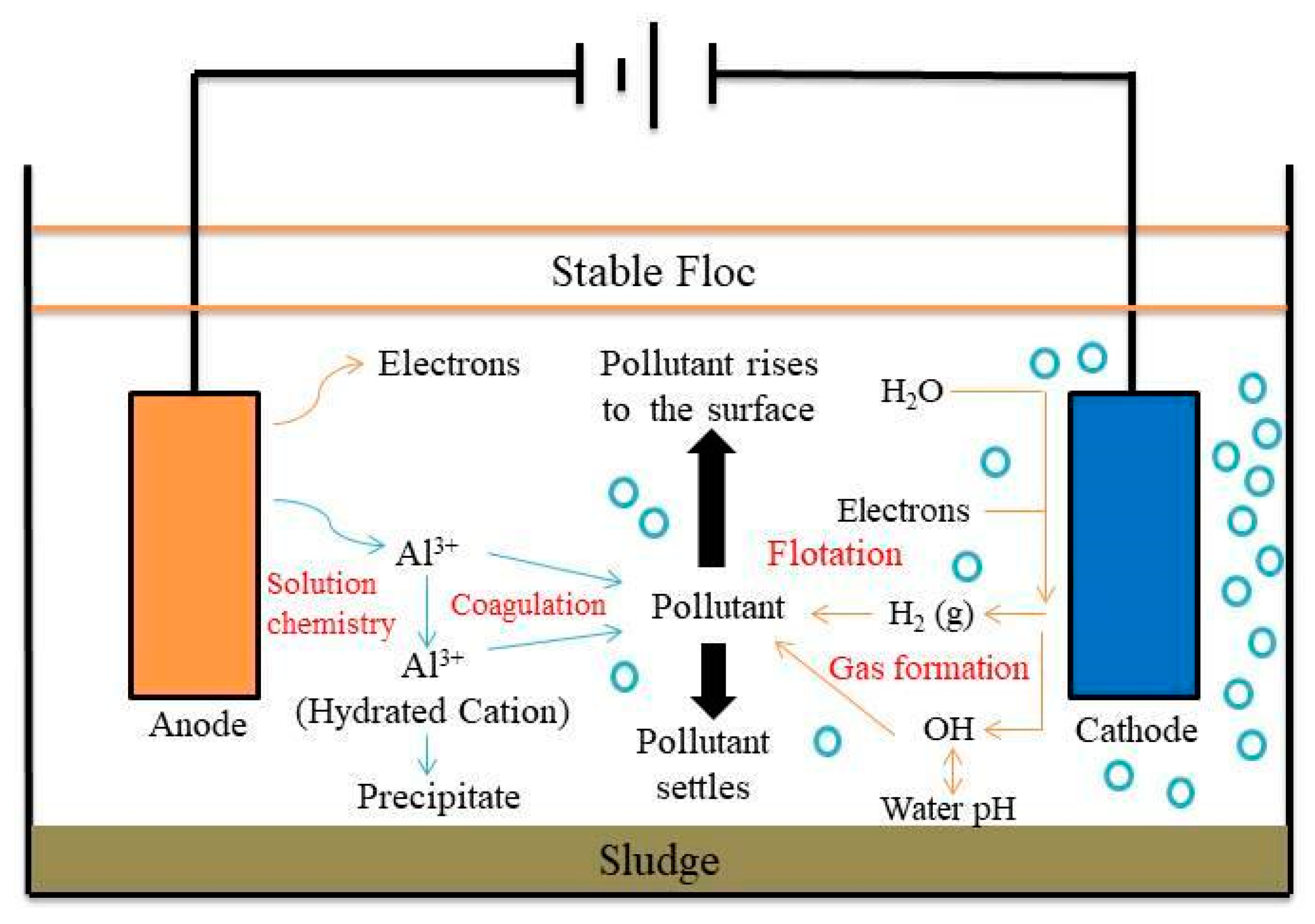
Figure 1. Schematic diagram of the electrocoagulation process.
In addition, a secondary reaction possibly occurs during the oxidation process. The formation of oxygen by the electrolysis of water is divided into two conditions: acidic and basic media.

The reaction that happened in the cathode is a reduction in water based on different conditions, as follows.
In Equations, the Al3+ produced on the electrode react to form several species, including:
-
monomeric species such as Al(OH)2+, Al(OH)2+, Al2(OH)24+, and Al(OH)4−;
-
polymeric species such as Al6(OH)153+, Al7(OH)174+, Al8(OH)204+, Al13O4(OH)247+ and Al13(OH)345+;
-
amorphous species with very low solubility, such as Al(OH)
3 and Al
2O
3 [14][55].
The formation of amorphous Al(OH)
3, also called sweep flocs, needs surface areas which are useful for the adsorption of soluble pollutants and the trapping of the colloidal compounds
[15][56]. The polymerization of flocs is as follows:
The flocs can be easily removed from an aqueous medium using the sedimentation method and H
2 flotation. However, aluminium hydroxide usually acts as an adsorbent or traps the pollutants. It would be a great composition for the removal of the organic compound from the solution
[16][57].
2. Type of Agro-Based Wastewater
2.1. Olive Oil Mill Wastewater
In general, olive oil mill wastewater (OOMW) consists of 80–83% water, 15–18% organic compounds, and 2% inorganic compounds
[17][78]. OOMW has the characteristics of being dark in color, having an acidic pH (~5), and having highly toxic components including tannins, phenols and acid compounds making up about 37% of the total mass
[18][19][79,80]. It has been reported that more than thirty types of phenolic compounds have been identified.
The electrocoagulation process can be used for OOMW because it decomposes the organic compound and is commonly used for OOMW treatment
[20][84]. Electrocoagulation has stability for colloids, suspension and emulsion, which is affected by electric charge. When an electric charge is supplied into a suitable electrode, the compound will be neutralized and the rest of it will aggregate together into a larger and separable compound
[21][85].
A study showed that electrocoagulation can remove COD by up to 78% after 1 h of electrolysis time using Fe as the electrode. The energy consumption reaches 55 kWh m
−3. However, using Al as the electrode, the removal of COD has a lower value than that using Fe. The removal efficiency is only 55% for 1 h of electrolysis time. It also acquires higher energy consumption until 62 kWh m
−3 [22][86]. The reduction of the energy consumption using Al as an electrode can be acheived by diluting the sample 10 times. The study reported that the energy consumption was decreased to 1 kWh/L with 57% COD removal
[23][87]. The kinetic model of the electrocoagulation process using the one-factor method increases the performance of COD removal to 99% with conditions of 60 min electrolysis time, with the current density at 12.5 mA/cm
2 and the addition of 400 mg/L NaCl
[24][88]. The study conducted by Benekos
[25][89] compared the performance of electrocoagulation on a laboratory scale and pilot scale. The results show on the laboratory scale that the COD and color removal (50% and 100%, respectively) is higher than that at the laboratory scale (42.5% and 85.3%, respectively).
The electrocoagulation process on OOMW is useful as a pre-treatment for biofuel production
[21][85]. The methane production reaches 1902 kJ/L
OOMW. The treatment of COD removal also produces biogas, as reported by a previous study. The result shows that the COD removal of OOMW using the electrocoagulation process produces biogas around 0.741 g/L
COD [26][90].
2.2. Sugar Industry Wastewater
The sugar industry categorized as one of the largest agro-based industries. It uses about 1500–2000 dm
3 water and produces about 1000 dm
3 wastewater per ton of processing
[27][91]. The wastewater mainly results from the process of floor washing, condensation, leakage, and spillage of solutions from the pipeline and valve
[28][92]. The sugar wastewater industries (SIWW) have a high concentration of organic materials due to the presence of sugar and organic material in the cane or beet. SIWW contains organic compounds including COD ranging between 2300 and 8000 mg/dm
−3, BOD of about 1700–6600 mg/dm
−3, and TSS of about 5000 mg/dm
−3 [29][93]. In addition, SIWW also possibly contains pesticides, herbicides and pathogens from the contaminated material and processes which are produced
[27][91].
The electrocoagulation process becomes one of the choices to be considered for SIWW treatment when the conventional method can not reduce the pollution
[30][94]. The previous study reported that COD removal on SIWW treatment can reach 86.36% for 8 h of electrolysis time. The 12 V voltage is applied to the system without any pre-treatment. Using iron as an electrode increases the COD removal of SIWW, which reaches up to 84% for 2 h electrolysis time. The color reduction is about 86% with the current density of 178 A/m
2. The lowest energy consumption utilized is 16.75 kWh/L. However, the performance of COD removal decreases to 62%. This result does not suffice for the final discharge of wastewater; therefore, further advanced methods could possibly be applied to bring the wastewater to meet the final discharge
[31][95].
Different cases happened with simulated sugar industrial effluent using the research surface method to study the effects of various parameters using the research surface method (RSM). The maximum COD removal of about 83.94% is obtained with the energy consumption of 6.64 kWh kg
−1. This system requires less energy.
This study suggested that electrocoagulation potentially can be applied for the treatment of real sugar effluent [96].
2.3. Pulp and Paper Mill Wastewater
The pulp and paper industry produces highly polluted wastewater
[32][97]. It forms black liquor as the main by-product, which contains about 50% lignin. The pulp and paper industry discards lignin to make a good quality of paper
[33][98]. The release of lignin comes from the process of alkaline extraction at the bleaching stage. Lignin is a heterogeneous three-dimensional polymer that consists of oxy phenylpropanoid components. The contamination of phenolic compounds to the environment could damage the underground water and receiving water bodies
[2][43].
The electrocoagulation process is one of the great alternatives to treat pulp and paper mill wastewater. Aluminium and iron are widely used as electrodes for the electrocoagulation process. A study showed that iron has greater efficiency for BOD and COD removal compared to aluminium. The performance of iron can reach up to the complete removal of COD and 90% removal of BOD within a 60 min reaction
[34][99]. Other concerns for pulp and paper mill wastewater are lignin and phenol. By using iron as an electrode material, the electrochemical process can degrade lignin and phenol by up to 90%
[29][93].
2.4. Palm Oil Mill Effluent
Palm oil mill effluent (POME)’s typical liquid waste results from the extraction of fresh fruit bunch (FFB) in the palm oil industry
[35][36][100,101]. The characteristic of POME is a thick brownish liquid color due to the decomposition of lignocellulosic materials
[37][38][102,103].
Some studies have found the performance of the electrochemical process for POME treatment. Using Al as the electrode shows little removal of COD and BOD. The percentage of COD and BOD removal is 30% and 38%, respectively
[39][105]. However, the addition of NaNO
3 could improve the performance of the electrochemical process using Al. The efficiency of COD removal increases by 64%. Using NaNO
3 as the electrolyte support is also beneficial for subsequent biological treatment
[40][106].
Another method uses iron for the electrochemical process. The performance of iron is quite great, with 89.2% removal of COD in 15 min of electrolysis time. For another good value, using iron as an electrode could remove the color by up to 90.4%
[41][110]. In addition, steel wool can be used as an electrode. It could remove COD by up to 74% and BOD by up to 70% with the improvement of the electrode arrangement
[42][111].
2.5. Coffee Industry Wastewater
Coffee is one of the world’s most well-known beverages, and it is the world’s second-most-traded commodity after petroleum
[43][112]. The wastewater produced from the coffee processing industry ranges from 40 to 45 L for every kg of coffee
[44][113]. The process requires large amounts of water for every step; therefore, the wastewater produced is high
[45][114]. Coffee fruits themselves are rich in caffeine, sugars, phenolic compounds, fatty acids, lignin, cellulose, pectic substances and other macromolecules
[46][115]. Those compounds are not suitable to be released into the environment due to their toxicity
[47][116].
Coffee processing wastewater (CPWW) is characteristically black in color. It is high in persistent compounds known as melanoidins, which are toxic, recalcitrant and non-biodegradable
[48][117]. Releasing the untreated CPWW to the water body can promote eutrophication, reduce Secchi depth and prevent sunlight penetration. The concentration of oxygen in the water body will be depleted
[49][118]. The electrocoagulation process can be used for the decolorization of CPWW treatment
[50][119]. The addition of electrolyte support such as sodium chloride affects the removal efficiency due to the generation of active chlorine during the electrolysis process interacting with substances such as melanoidins
[51][120]. Other than meloinidins, the mineralization of proteins and lipids are adsorbed on the surface of the precipitated hydroxides
[52][121].
Previous studies reported that the use of a combination of iron and stainless steel as electrodes achieves 87% COD removal and 97.1% color removal
[53][122]. When using iron alone as an electrode material, it removes 97% of COD and 89% of color
[54][123]. The electrocoagulation process can also be used for caffeine recovery that reaches 96% recovery performance
[55][124]. However, there is still no report for polygalacturonase characterization and production in the coffee industry using the electrocoagulation process.
2.6. Vegetable Oil Refinery Wastewater
Vegetable oil refinery wastewater (VORW) has a high amount of COD, phosphorus, sulphate, oil and grease
[56][125]. The sources of vegetable oil manufacture are soybeans, groundnut, rapeseed, sunflower, safflower, cotton, sesame, coconut, mustard, rice bran, watermelon, and neem, etc.
[57][126]. Another characteristic of VORW is that it has a low ratio of BOD/COD; therefore, it is not useful for the biodegradation method. Based on some studies, electrochemical technology could overcome that limitation
[58][127].
A previous study reported that using iron as the electrode could remove 93.3% of COD after 60 min electrolysis time
[59][128]. However, when aluminium is used as an electrode, the COD removal increases up to 98.9%, with 100% color removal in 90 min
[60][129]. Another study using the Box-Behnken design for optimization attained 70.8% COD removal. Aluminium was used as an electrode, and the electrolysis time was 60 min
[61][130]. On the other hand, another study reported that using the Box-Behnken design for the optimization of the electrocoagulation process of sunflower oil refinery could achieve 95% COD removal with a shorter time (18 min)
[62][131].
2.7. Nuts Processing Wastewater
The nut processing industry includes many various types, including pistachio, almond, and cashew nut, etc. Pistachio is a kind of nut rich in organic nutrients. It contains 5.6% water, 19.6% protein, 53.2% fat, 19% carbohydrate, and 2.6% ash
[63][132]. The pistachio industry produces approximately 1 Mm
3 of wastewater and 50,000 tons of solid waste per year. Pistachio processing wastewater (PPW) has high COD, phenolic compounds and turbidity, which can cause harm to the aquatic ecosystem and terrestrial environment if no treatment of the PPW is performed
[64][133].
Several processes are required in the almond processing industry, including cracking and blanching
[65][134]. In the blanching step, the resulting product contains high levels of organic compounds, suspended solids, turbidity, COD and color
[66][135]. The effect of the blanching time on the moisture content is inversely proportional. This means that when the blanching time is longer, it results in a decreased moisture content. Meanwhile, the effect of the blanching time on the lipid content and color intensity is directly proportional. The longer blanching time will increase the lipid content and color intensity
[67][136]. A previous study reported that the polyphenol content recovery in the almond industry using the blanching process acquired 0.53 g gallic acid equivalents (GAE)/kg
[68][137], while the use of the microwave process recovered 0.42 g gallic acid equivalents (GAE)/kg
[69][138]. Based on these studies, the polyphenol content recovery is higher using the blanching process. The use of blanching and microwave processes is recommended according to a previous study.
The kinetic study showed that the sonicated almond acquires higher total phenolic compounds than non-sonicated almonds after 20 min extraction at room temperature (25 °C)
[70][140].
Table 1 shows the performance of the electrocoagulation process on different types of nut processing wastewater. The electrocoagulation process has been shown to be a suitable method for the reduction of pollutants from cashew nut processing wastewater, as was reported in a previous work where COD reduced it by up to 80%
[71][141]. According to a previous study, even though the COD removal for PPW is categorized as low, the phenolic compound removal shows greater efficiencies. In addition, using graphite as the electrode material on PPW could achieve the complete removal of phenolic compounds and the 99.79% removal of COD
[72][142].
Table 1. Performance of the electrochemical process on nut processing wastewater.
Type of Nuts |
Electrode Material |
Electrode Type |
COD removal |
Phenolic removal |
References |
Pistachio processing industry wastewater |
Al |
Unipolar |
60.1% |
77.3% |
[73] | [143] |
Pistachio processing industry wastewater |
Graphite |
Unipolar |
99.79% |
100% |
[74] | [144] |
Pistachio processing industry wastewater |
Al |
Unipolar |
57.4% |
- |
[65] | [134] |
Pistachio processing industry wastewater |
Al and stainless steel |
Unipolar |
60% |
95% |
[74] | [144] |
Cashew nut processing industry wastewater |
Fe, BDD (Boron Doped-Diamond) and stainless steel |
Multipolar |
80% |
- |
[75] | [145] |