NR latex is useful for a wide range of products due to the ability of the rubber particles to coalesce and form a coherent polymer layer impenetrable to air and water. The vulcanization process in the latex transforms the materials into a highly versatile raw material for the manufacture of a variety of rubber goods via dipping, molding, casting, or spreading operations. However, the film cast from NR latex is soft and tacky; thus, the latex must be prevulcanized using a sulfur, peroxide or radiation technique to give a higher grade output
[4]. To achieve the elastic qualities of the rubber, the latex was treated with many chemicals that act as preservatives, anticoagulants, vulcanizing agents and antioxidants
[3]. NR latex products outperform synthetic counterparts due to their excellent strength properties along with low modulus and high wet gel strength, elasticity, resilience, heat dissipation and abrasion resistance characteristics which cannot easily be mimicked by synthetic polymers.
Synthetic latex is primarily produced using emulsion polymerization and can be synthesized from a variety of monomers, including acrylates, styrene, vinyl acetate and butadiene
[5]. The properties of synthetic rubber such as high-temperature resistance, good resistance to abrasion, high strength is depending on the composition of the copolymers. Both NR and synthetic rubber are different in microstructure but contain isoprene as the main chain
[3]. Even though NR latex products can biodegrade in the soil, the process is slow due to the large molecular weight of NR latex macromolecules with additional chemical cross-linking that formed through the vulcanization process. These cross-linkages are stable under ambient conditions and can withstand the soil environment for a prolonged period of time. Another factor that may conduce to the delayed degradation rate is the use of additives such as antioxidants in vulcanized NR latex, which is intended to limit microbial growth upon disposal
[6].
Currently, the majority of rubber waste is burned or disposed of in landfills. Microbes play a role in the biodegradation process by releasing extracellular enzymes that cleave polymer chains into tiny molecules, which are then absorbed into the microorganism’s cell to be used as a source of carbon and energy. CO
2, H
2O and other metabolic products are released at the end of the process and can be utilized by other living creatures. Therefore, biodegradation is another way of degrading rubber waste that has the potential to resolve environmental problems. Microbial breakdown of polyisoprene rubber, on the other hand, is a very sluggish process that can take months or even years
[7]. The addition of compounding ingredients such as reinforcing fillers, accelerators and sulfur increased the resistance of the latex towards microbial degradation caused by the decrease of access for microorganisms to the rubber matrix
[8].
Biodegradation is an environmentally benign alternative to conventional disposal methods in which microorganisms biologically break down complex organic chemicals in commercial items into cell biomass and less complex molecules, as well as water and either carbon dioxide or methane. For microbes to use polymers as a nutrition source, polymers must first be oxidized through an abiotic process, such as exposure to ultraviolet (UV) irradiation, heat and/or chemicals in the environment. Some microbes, such as rubber degraders, can commence the oxidation process on their own, with secreted enzymes causing polymer biofragmentation followed by bio assimilation of small cleavage pieces
[3].
The global demand for natural source NR rubber gloves has been growing in recent years. Due to an increase in NR glove consumption, the formation of a significant volume of NR latex-based solid waste is unavoidable. The use of chemical agents such as fillers, antioxidants, accelerators, vulcanizing agents and inhibitors during the manufacturing process has a significant impact on the chemistry of NR latex, decreasing its inherent degradability. An excessive amount of solid waste has been generated due to increased consumption of NR latex products and their low degradation, which has negatively impacted the sustainability of the environment. The development of biodegradable NR latex composites has been widely investigated in order to reduce the environmental issues caused by rubber waste disposal
[6][9][10][11][12][6,9,10,11,12].
Natural polymer composites made from filler have received much attention in recent years due to the benefits of natural filler and environmental concerns. In order to reduce the greenhouse effect, the composite material based on renewable and biodegradable materials is progressively replacing the synthetic fiber-reinforced composite. The strength of a natural fiber composite is determined not only by the interfacial strength, but also by the fiber’s basic strength. The fiber quality is determined by the crop’s location and climate, as well as the fiber age, plant species, transit mode, storage time and inventory condition. Chemical treatments of natural fibers are used to change the physical, mechanical and thermal properties of composites to address this problem. Chemical treatments may reduce the hydrophilicity of plant fibers, clean the surface of fibers, improve the roughness of fibers and reduce the moisture content of fibers, resulting in better reinforcement–matrix interactions
[13].
The growth of agricultural industries also leads to an increase in the production of biomass from the agricultural sector. Agro-waste production is generated on an ongoing basis and produced in large quantities. Excessive agricultural waste creates a disposal problem through waste management problems, pollution problems and also becomes a waste of primary resources. In order to deal with this problem, recycling and reusing this waste is more important. Agricultural waste is used as feedstock, biochemicals, biomaterials and also as fuel to produce heat and electricity
[14]. However, due to poor fuel properties, the usage of agro-waste as fuel is still minimal. Agro waste also can be beneficial if it is used properly. There are research has been done on agro-waste as an alternative filler to synthetic filler in order to obtain renewable and environmentally friendly products. The agro waste can be generated from various sources such as date palm waste
[15][16][15,16], cocoa pod husk
[17], cotton
[18][19][20][18,19,20], coconut
[21][22][23][21,22,23], rubberwood and kenaf bast
[24]. Basically, agro waste, contains three main constituents which are cellulose, hemicellulose and lignin.
Cellulose is the most abundant polymer produced in nature and microorganisms. The major conventional resources of cellulose can be obtained from cotton and wood. Cellulose and its derivatives have been utilized for years in industrial applications such as textile, paper and medical due to its unique properties, biodegradable and come from renewable resources
[25][26][25,26]. Cellulose is polysaccharides with a chemical formula of (C
6H
10O
5)
n composed of repeating units of β-
d-glucopyranose with the covalent links between the OH group of C4 and C1 carbon atoms
[27]. Properties of cellulose is depending on its degree of polymerization which depends on the source of the cellulose. However, due to the high number of hydroxyl groups on the glucose ring along with the skeleton; thus, there is hydrogen bonding between the chains. The crystallization of the chain and the presence of the two regions in cellulose, which is crystalline and amorphous, result in the general properties of cellulose such as high strength, stiffness, durability and biocompatibility. The hydroxyl group in the cellulose gives hydrophilicity, chirality and biodegradability to the cellulose; in addition, these hydroxyl groups allow the chemical modification of the cellulose
[28]. However, the characteristics of cellulose are highly dependent on the plant sources and the extraction process
[29][30][29,30]. There are a few types of cellulose that are extracted from natural resources, which are microcrystalline cellulose (MCC), cellulose nanowhiskers (CNW) and cellulose nanofibers (CNF). MCC has the properties of biodegradable, insoluble and biopolymer
[31]. CNW is needle-like cellulose, having at least 1 dimension equal to or less than 100 nm and highly crystalline. CNF can be divided into two categories which are nano-fibrillated cellulose and microfibrillated cellulose
[29]. CNF is a long, flexible nano-string consisting of alternation crystalline and amorphous. CNF has a large surface-to-volume ratio, high mechanical properties and the ability to form a highly porous mesh
[32].
2. Preparation and Characterization of Latex-Based Waste Natural Filler Composite
Metroxylan sago pith waste (MSPW) is utilized as a new biodegradable filler in NR latex films. MSPW is a residue from the starch extraction process. It contains a high number of sago starch granules and high cellulose: up to 60%. The obtained results from incorporating MSPW with NR latex showed a reduction in tensile strength due to lignin, which hinders the formation of chains between rubber particles and creates distance between NR latex colloidal particles. A decreasing trend was also noted at the elongation at the break results and the modulus, due to the interparticle integration effect, which decreases the ability of the NR latex films to retain their stiffness. However, the tear strength increased with the addition of MSPW, due to the ability of the particle to deviate cracks, indicating a good cementing mechanism in NR latex films
[12].
The presence of the glucopyranosyl group of starch, which consists of three hydroxyl groups, tends to form a strong hydrogen bond which results in filler agglomeration when incorporated with the XNBR latex. To solve this problem, amino-functional starch was produced by grafting the acrylonitrile monomer on the starch. This modification also helps increase the homogeneity of the filler dispersion in the latex compound. The addition of the ANS, however, reduces the mechanical properties of the ANS/XNBR composites. This occurs due to the reduction in crosslink density between the rubber molecules, which was hindered by the formation of the ANS-rich region. As biodegradation continues, further reductions in the mechanical properties are recorded due to the microbial activity in the ANS-rich region, which was spotted in the SEM and optical micrograph. The formation of micro-voids was also detected in the XNBR latex films during the biodegradation process. It was proved by the FTIR analysis that the reduction in the starch aliphatic chain at peak 1607 cm
−1 and stretching of the N-H bond at peak 3302 cm
−1 can be observed
[11].
Another study was carried out using the acid hydrolyzed method in order to improve the mechanical properties of the latex-sago starch composite,
[33][60]. This method was able to induce the formation of the sulfate ester group on the surface of starch, which can increase the interaction between the rubber and starch. The XNBR latex mixed the compounding ingredients and acid hydrolyzed sago starch and formed into films using the coagulant dipping technique. AHSS-latex composite showed that the swelling percentage and mechanical properties strength improved compared to native sago starch, due to the increase of surface activity from smaller particles and the presence of sulfate ester, which creates the C-O-C bond, hence improving the rubber–filler interactions. The mass loss in AHSS-XNBR latex composite shows the highest value due to the loss of the amorphous region after acid hydrolysis, which led to microorganism attacks on rubber and glycosidic chains.
Un-crosslinked NBR latex, which was added with nanocellulose from cottonseed linter pulp (CN), shows an increase in its viscosity, indicating the strong reaction between the CN and NBR chains. The foamed rubber produced has a smaller size, which provides better mechanical properties. Increasing the content of CN showed an improvement in tensile strength, which increased from 3.72 MPa to 6.54 MPa. The increment of tensile strength can be justified due to good interaction between CN and NBR matrix. This is supported through the SEM image shown in
Figure 15; here, it can be observed that the CN was embedded in the NBR matrix, which indicates a good interfacial adhesion. CN functioned as a physical crosslinking point with NBR chains and created hydrogen bonding and, hence, enhancing the crosslinked network of the composites. The possible scheme of the crosslinked network between the NBR and CN is shown in
Figure 26. CN also serves as a tensile stress carrier by transferring stress and preventing cracking and flaws from enlarging
[34][61].
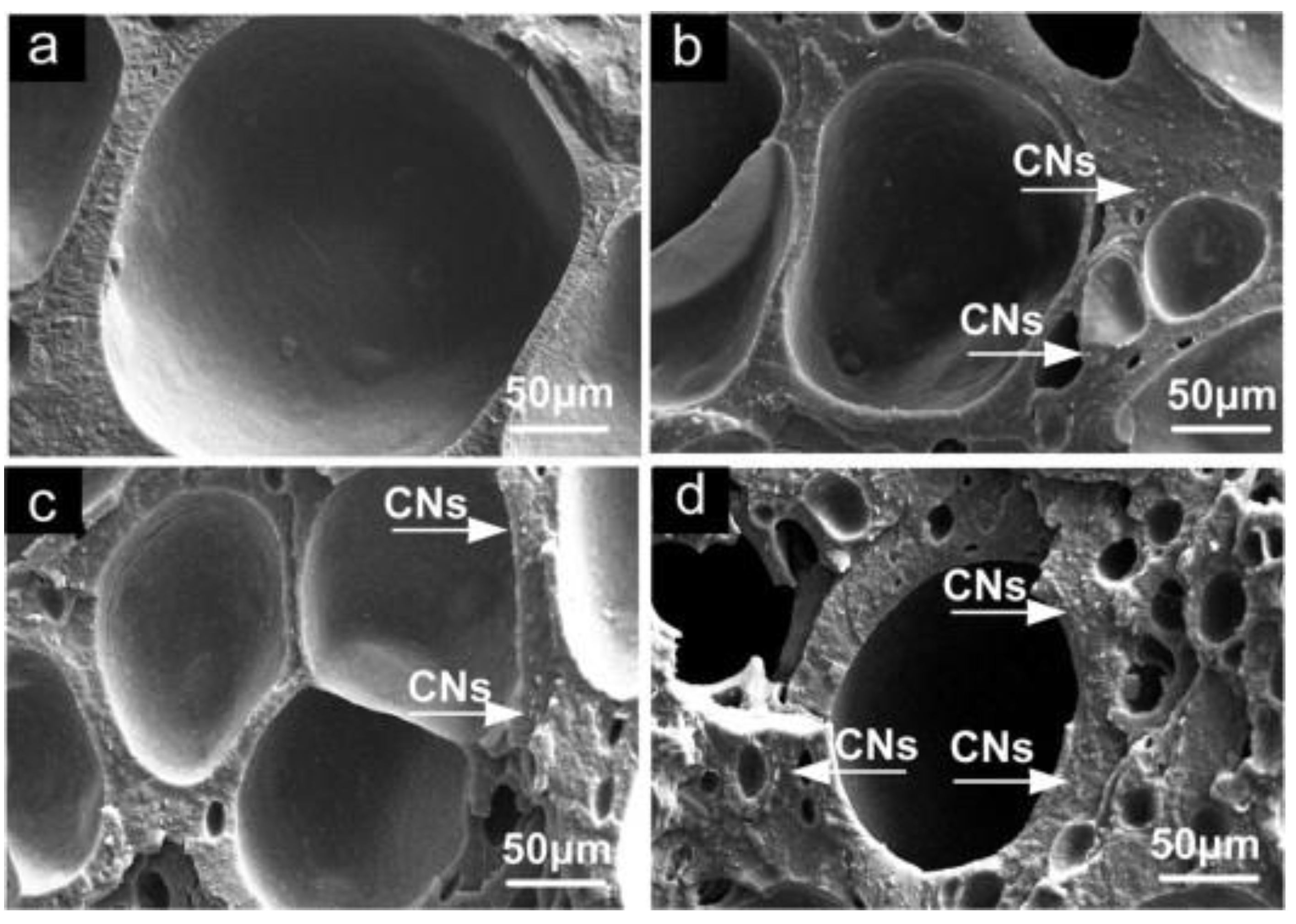
Figure 26. A possible scheme of crosslink network between NBR and CNs
[34][61].
The incorporation of the nanocellulose fiber (CNF) from coconut spathe with NR latex was studied by Gopalakrishnan et al.
[21]. The SEM result of the nanocellulose isolation showed that the diameter of nanocellulose is 40–50 nm; this is supported by the TEM results, where the diameter is around 30–60 nm. The optimum cure time of the NC/NR composite decreased with the increase of CNF content. Tensile, tear, modulus at 300 and hardness increase with an increase of CNF, which indicates the high reinforcement of an NR matrix by well-dispersed CNF. However, elongation at the break decreased with the increase of CNF, due to strong interaction between the rubber and filler, which increases its ability to resist the deformation of the NR chains. On the fracture surface, CNF was found to be embedded in the matrix, showing good compatibility between fiber and matrix with the presence of bonding agents. There were no voids or pull-out cracks observed, which indicates good interfacial adhesion. The thermal properties of the maximum degradation remain the same, as suggested: that the thermal stability was not affected by the addition of CNF. The DMA modulus is directly proportional to the elastic nature of the composite. The modulus increased with the increase in CNF loading at the low strain level, due to hydrodynamic reinforcement and the interactions of the filler–filler and filler–polymer. Solvent resistance towards toluene uptake decreased with higher loading CNF; this is due to the increase in the interfacial reaction between the NR chains and cellulose in the presence of the bonding agent, which increases the crosslinking point, hence preventing the penetration of the solvent into the rubber matrix.
Kenaf bast and kenaf core are used to determine their effect toward incorporation with NR latex. Kenaf/NR composite was prepared using the Dunlop method
[35][62]. From the results, it can be observed that the tensile strength reduced with the increase in filler for both types of filler used. This happened due to kenaf core form agglomeration and led to a higher stress concentration, while kenaf bast has a larger pore size and is less interconnected with the matrix. Elongation at the break was also found to decrease with the increase in loading, due to the increase in the rigidity of the foam. The high loading fillers resulted in an NR latex foam with higher stiffness, where the kenaf aggregates and stack acts as a filler network. Kenaf bast/NR foam has a higher stiffness than kenaf core due to its high cellulose content. The highly crystalline compact structure promotes higher stiffness. From the SEM image, the kenaf core has an irregular and particulate shape, and a tendency to agglomerate, making it less interconnected with rubber; meanwhile, bast has a fibrous shape and a higher length to cause the physical interaction between the filler and rubber. As incorporated with NR, the kenaf core forms an agglomeration, which forms a weak interaction between rubber–filler. Meanwhile, bast is in a fibrous shape, which tends to cause a strong adhesion with rubber.
In the study on the effect of oxidization and hydrolyzation of corn starch, it can be noted that the particle size of the cornstarch was reduced by hydrolysis under alkali conditions at elevated temperature and high shearing force
[36][63]. This can be explained by both the amide bond in protein and the ether bond in starch, which can be hydrolyzed under acid and base conditions in order to break up the polymer into smaller segments. The treatment shows that the CF has a size reduction of 33 times. The decrease in particle size helps improve the tensile strength, modulus and toughness, but there is a reduction in the elongation at the break. This occurs due to the increase in the filler–matrix contact area and an increase in the number of particles for filler network formation. Since corn flour has a greater modulus than NR, the rigidity of the connected article network penetrating throughout the NR matrix contributes to an increase in the modulus. The agglomeration effect can be explained through the Kraus plots in
Figure 37. As the filler content of hydrolyzed CF composite was increased to 20%, it caused agglomeration, which led to the reduction of the restriction of polymer motion and, hence, increased the swelling ratio.
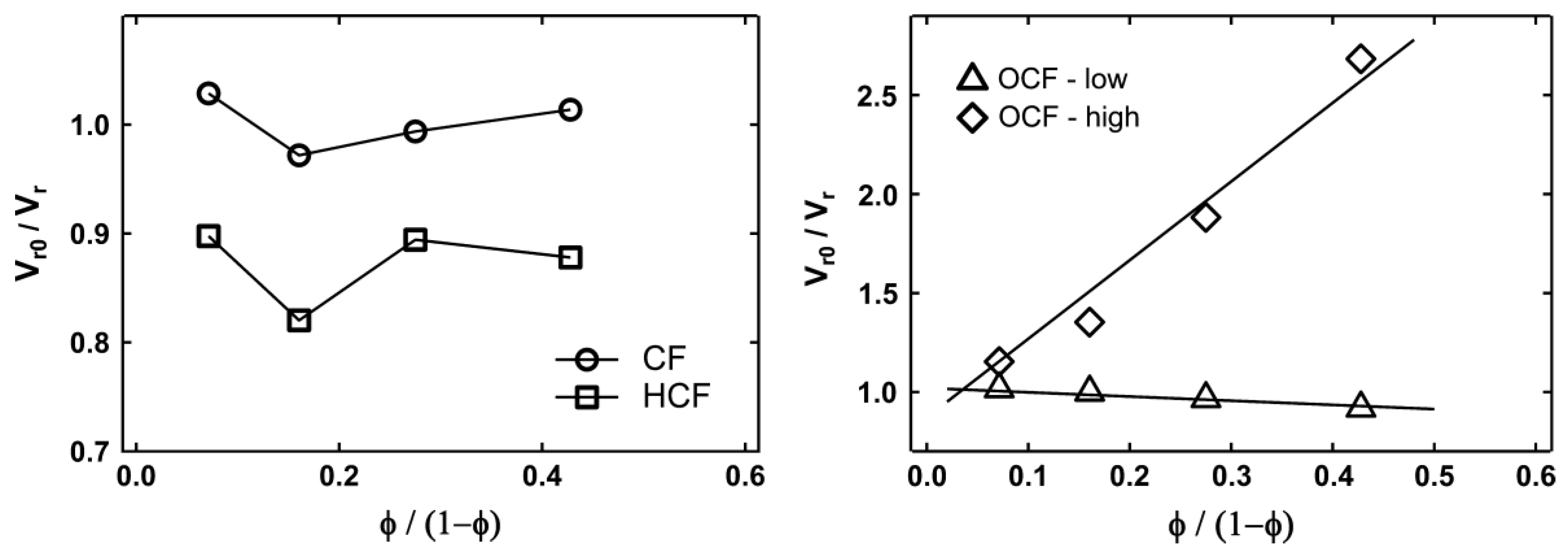
Figure 37. Kraus plot for corn flour (CF), hydrolyzed corn flour (HCF), oxidation corn flour-low oxidation level (OCF-low) and oxidation corn flour-high oxidation level (OCF-high)
[36][63].
3. Conclusions
Natural filler-based composites have been widely used in order to preserve nature. Owing to their good mechanical properties, such as high strength, stiffness, durability and cellulose, they have caught the attention of many researchers aiming to fully utilize the potential of this natural resource. However, in comparison to synthetic fibers, these natural cellulosic fibers have poor mechanical properties, due to poor compatibility with the composite matrix. They are hydrophilic, which means that they disperse in the presence of hydroxyl, and the polar groups make the cellulose hydrophilic, which tends to form a strong network and agglomerates, making it difficult to uniformly dispersed in the latex matrix. As a result, natural fibers should be surface treated to increase the thermodynamic miscibility and interface bonding strength before being used as reinforcement materials in polymer composites. Through surface modification, the hydrophobicity of the cellulose can be improved and helps improve the dispersibility of the cellulose in the latex matrix. After surface modification, the mechanical and thermal properties of the composite were improved, and at the same time, provide biodegradability to the final products. The improvement in the dispersibility and properties of waste/raw natural filler in latex-based composite provides a wide range of potential applications in industries including biodegradable gloves, flexible display, sensor, medical application, agriculture and the construction industry.