Cosmic radiation belongs to the challenges engineers have to deal with when further developing space travel. Besides the severe risks for humans due to high-energy particles or waves, the impact of cosmic radiation on electronics and diverse materials cannot be neglected, even in microsatellites or other unmanned spacecraft. Here, we explain the different particles or waves found in cosmic radiation and their potential impact on biological and inanimate matter.
1. Cosmic-Ray-Shielding Materials
Generally, particles such as protons or neutrons can be shielded by materials containing hydrogen, while photons in the X-ray or gamma-ray range need high-electron-density materials, such as lead.
The challenging problem of shielding cosmic radiation to protect astronauts is the production of secondary particles inside the materials used as shields. Such secondary products of the interaction of cosmic rays are, as mentioned above, neutrons, protons, pions, and other particles influencing human DNA. From that elementary particle perspective, materials built from light atoms like hydrogen and carbon are advantageous (i.e., polymeric materials). This is why, for example, polyethylene-based structures are more effective in protection than alumina or lead, combining high hydrogen content with structural integrity
[1]. On the other hand, water is not necessarily an ideal solution since it contains oxygen, which is heavier than carbon.
Spillantini et al. mention in their review about active and passive shielding methods the problem of bulky, heavy shielding
[2]. They point out that light, highly hydrogenated materials—especially polyethylene—are thus ideal to perform shielding from cosmic irradiation. Polyethylene belongs to the materials already used in the ISS crew sleeping quarters
[3]. Recent radiation shields often contain ultra-high-molecular-weight polyethylene (UHMWPE) due to the combination of good shielding and mechanical properties
[4].
Shielding against galactic cosmic radiation, secondary neutrons, and solar energetic particles can generally be performed by materials which contain hydrogen, boron, and nitrogen
[5]. In a simulation study by NASA, boron nitride materials containing hydrogen were shown to have superior shielding properties as compared to polyethylene, which is broadly used for this purpose.
Bennington et al. filed a patent for a spacecraft and spacesuit with radiation shields, also based on hydrogen-containing material, stored in a polymer, reaching a higher hydrogen content than polyethylene
[6]. They mention hydride or borohydrides as possible forms of hydrogen and suggest electrospinning, casting, or sintering as possible methods to form fibers or solid casts, fulfilling these requirements.
The focus of this entry is an overview of recent fiber-based passive shielding materials that offer protection from cosmic radiation, starting with UHMWPE, as one of the most often applied materials, and going further to other polymers, polymer blends, and fibrous nanocomposites, including inorganic material to further support the shielding efficiency.
2. UHMWPE as Fibrous Shielding Material
UHMWPE belongs, as mentioned before, to the recently strongly investigated and already applied materials for shielding humans and instruments from cosmic radiation. UHMWPE is semicrystalline, that is, it consists of amorphous parts with crystalline lamellae embedded. In fibrous form, it can be used to prepare usual textile fabrics by weaving, knitting, or even producing nonwovens
[7]. Their high strength and stiffness is reached by extreme stretching during the gel spinning process, resulting in highly aligned polymer chains in the crystalline regions
[8]. In this way, a tenacity of approximately 10× the value of steel fibers is reached
[9]. While UHMWPE fibers usually suffer from low melting temperatures, drawing with ratios larger than 20 can be used to increase the melting temperature to approximately 150 °C, which is sufficient for many applications
[10].
Besides these good mechanical properties, making it also useful to shield spacecraft from space debris
[11], UHMWPE is also highly interesting for the shielding of cosmic rays. Typically, composites from a resin in which UHMWPE fibers are embedded are applied for this purpose. However, the fiber–matrix interface in these composites is highly problematic due to the chemically highly inert UHMWPE fibers, often reducing the required shielding as well as the mechanical properties. This is why some groups have investigated possibilities to modify the fiber surface, aiming at a better adhesion, but usually at the cost of reduced mechanical properties
[12][13][14][15].
The other way is to modify the matrix. In the group of Zhong, the possibility to use a reactive nano-epoxy matrix containing reactive graphitic nanofibers to improve wetting and adhesion to UHMWPE fibers was investigated
[16][17][18]. Using
35Cl ions with 1 GeV/nucleon, they performed radiation tests mimicking the heavy ions of the galactic cosmic ray field and found no negative influence of the additional graphite nanofibers
[17].
Similar UHMWPE/nano-epoxy composites were investigated in comparison with hybrid UHMWPE/glass/nano-epoxy as well as pure epoxy as the matrix in radiation tests at the NASA Space Radiation Laboratory at Brookhaven National Laboratory
[4]. Here, beams of 1 GeV/nucleon
35Cl were used in the alternating gradient synchrotron accelerator, representing the heavy ion component of galactic cosmic rays. Both UHMWPE/epoxy and UHMWPE/nano-epoxy showed a slightly higher dose reduction than pure polyethylene, while the hybrid composites showed a clear reduction of the radiation shielding properties by more than 25%.
Another new resin was suggested by Iguchi et al., who developed a hydrogen-rich benzoxazine resin, in this way supporting the shielding properties of the pure UHMWPE
[19]. For this, they developed different bifunctional benzoxazines from meta-substituted alkoxy phenols and diamines with varying hydrocarbon chain lengths. Using differential scanning calorimetry (DSC) and thermogravimetric analysis (TGA), they found an influence of the diamine chain length on the reactivity of the developed benzoxazines, with larger chain lengths leading to an increase of the polymerization temperature and decrease of the thermal stability. The optimum resin, depicted in
Figure 1 as a monomer, was shown to have much higher shielding properties than epoxy using NASA’s On-Line Tool for the Assessment of Radiation in Space (OLTARIS), making this UHMWPE/benzoxazine composite favorable in comparison with common epoxy.
Figure 1. Molecular structure of the optimized 3BOP-daC12 benzoxazine monomer. From
[20], originally published under a CC-BY license.
Investigating the optimized benzoxazine polymer in terms of mechanical and shielding properties, they found especially high ultimate tensile strength and tensile modulus at low temperatures of −50 °C, as compared to room temperature
[20]. Combined with thin carbon fiber skin layers, the mechanical properties could be further enhanced, however, at the cost of reduced shielding and higher mass. Simulations with OLTARIS
[21] showed significantly better shielding properties for all sandwich panels in comparison with aluminum, while the shielding of the whole composite was only 2% lower than the value for pure UHMWPE, making this composite well suited for cosmic shielding.
Cummings et al. concentrated on the effect of proton radiation on pure UHMWPE
[22]. They applied proton irradiation at doses of 0–35 Gy at a rate of 0.54 Gy/min using a 155 MeV proton beam to different UHMWPE grades and found changes in different material properties, depending on the UHMWPE grade. These irradiation doses were chosen to simulate cumulative exposure during a ten-to-twenty-year space flight. The authors mention, however, that low doses in particular cause more oxygen to diffuse into the material, which may lead to higher material degradation than high-dose-rate events. Similar experiments were performed by NASA, simulating expected radiation dosages for space suit softgoods during a Mars reference mission as well as equivalent dosages at 2×, 10×, and 20× the predicted dose, and finally a simulated 50-year exposure
[23].
Due to the aforementioned advantages of polyethylene materials, and especially UHMWPE, composites including UHMWPE or other polyethylenes can now be regarded as references for lightweight shielding materials
[24][25][26]. Nevertheless, combining UHMWPE with other low-Z materials can be supportive to reduce the aforementioned degradation of polyethylene upon exposure to UV irradiation and high temperature
[27]. Such approaches are described in the next sections.
3. Boron, Boron Nitride, and Boron Carbide
While polymers can efficiently reduce the energy of neutrons from cosmic radiation, the resulting low-energy neutrons can react with nuclei in the human body or create errors in electronics. A high absorption of neutrons can be found in materials containing the stable boron isotope
10B, which has a large cross-section to absorb neutrons
[28][29]. This is why Ko et al. embedded boron powder or boron carbide whiskers into polyimide samples and found over 90% absorption of the incident neutrons in a sample of 5 mm thickness, tested with a PuBe thermal neutron source, containing 15% amorphous boron powder, without significant changes of the thermal properties
[30].
Kowbel et al. applied boron fibers as a method to improve mechanical and shielding properties at the same time
[31]. While boron powder can also be used to increase the mechanical properties of a matrix slightly, they found a composite strength higher than 1 GPa for the boron-fiber-reinforced matrix, as compared to values in the order of magnitude of some ten MPa for the pure matrix.
Manzlak et al. embedded boron carbide (enriched
10B
4C) into polypropylene (PP) fibers, which led to a small reduction in tensile strength and modulus, while a double-layer woven fabric of these filaments with a thickness of 0.8 mm resulted in a reduction of the neutron fluence by 42%
[32]. Similarly, Huang et al. embedded boron carbide into a carbon-fiber-reinforced composite and found not only improved thermal and mechanical stability due to the boron carbide filler, but also good neutron shielding, as measured by an Am-Be neutron source and detected by a lithium glass scintillator
[33].
Another often used material is boron-nitride (BN). BN belongs, in the form of fibers or nanotubes, to the materials with high absorption capacity for electromagnetic radiation
[34][35]. An advantage of this material is that boron nitride is generally suggested by NASA as fibrous reinforcement for spacesuits and so on
[36]. Such BN multi-walled nanotubes can be produced with inner diameters of a few nanometers and lengths of a few hundred nanometers
[37].
Kang et al. investigated the neutron cross-section of a polyimide matrix with and without 2 wt% of BN nanotubes and found an increase of 120% upon the addition of the BN nanotubes
[38]. These experiments were carried out by neutron activation analysis, leaving indium foils exposed overnight to ensure saturation of the activation, and afterwards comparing the time-dependent activity after activation with and without shielding materials. These decay curves for foils exposed with or without different shielding materials could be used to calculate the thermal neutron absorption cross-sections of the samples under investigation.
Polyethylene-based thermoplastic composites reinforced with boron nitride were investigated by Herrman et al.
[39]. They embedded BN in injection-molding-grade high-density polyethylene and also tested the samples by neutron exposure of an indium foil with thermal neutrons (<0.5 MeV), with or without shielding of the foil by the BN-composites. The mass absorption cross-section was calculated from the average initial activity of the indium foils. They found a reduced initial radiation activity of the foil, that is, an increased mass absorption, with increasing amount of BN.
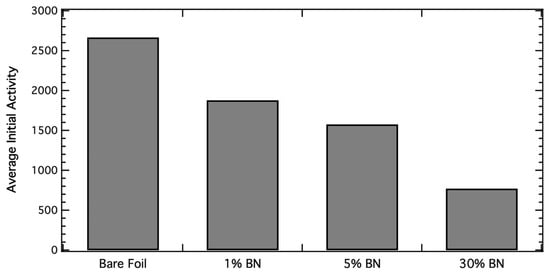
Mani et al. used another approach and combined boron and boron carbide nanoparticles as well as gadolinium nanoparticles with UHMWPE/epoxy composites
[40]. Producing sandwich panels by vacuum-assisted resin transfer molding, they found more than 99% shielding of these composites against neutron irradiation, while the core materials maintained their mechanical and thermo-physical properties after the radiation experiments. Introducing the same nanoparticles into high-molecular-weight polyethylene/epoxy composites resulted in more than 99% shielding performance for all sandwich panels, with boron nanopowder showing the highest radiation-shielding efficiency, as tested with thermalized neutrons and measured by the transmitting neutron flow through the sample
[41][42]. With a similar technique, Ghazizadeh et al. prepared composites from carbon-fiber-reinforced epoxy composites with or without BN nanoparticles and found a positive impact on the mechanical properties of the composites even for small amounts of BN nanoparticles
[43].
As these examples show, boron can be used in a broad variety of compounds and shapes to be embedded in fibers or matrices, especially for shielding of thermal neutrons. There are, however, more materials which can be used in fibrous shape or in combination with different fibrous materials to shield cosmic radiation.
4. Carbon Fibers
Besides polyethylene, carbon materials can also be used to provide shielding from cosmic radiation. Cohen reported on a full-carbon shield which was tested by bombardment with iron nuclei at 1 GeV/nucleon and showed the second-best dose reduction after polyethylene, before aluminum and lead
[44]. Interestingly, the carbon sheet even showed a better overall reduction in radiobiological damage to a lymphocyte cell culture, which was the target of the iron nuclei beam.
Similarly, Wu et al. simulated shielding against 1 GeV/nucleon
56Fe as a typical representative of high-energy galactic cosmic rays, using the Geant4 radiation transport code
[45]. They again found PE to show the best shielding efficiency for a given areal density, followed by water, carbon fibers, and aluminum.
Combining graphite fibers with polyethylene (PE), Emmanuel and Raghavan investigated the possibility of preparing optimized shields for highly elliptical orbit satellites
[46]. While pure graphite alone has better shielding properties than the often used aluminum, its mechanical properties are insufficient, resulting in the necessity to improve them by adding materials with higher atomic number. They found that, ideally, PE as the low-Z material in this composite should be at the surface layer and interact firstly with the incident radiation, in this way enabling the building of a multi-layer composite from PE and graphite which gives better radiation shielding, as simulated with a particle transport simulation code, taking into account solar particles, cosmic rays, protons, and electrons along the highly elliptical orbit. A three-layer shield from UHMWPE and graphite fibers was also patented, however, with the first layer containing UHMWPE and graphite, the second only polyethylene, and the third a ceramic material
[47].
A large simulation comparing the shielding properties of 18 single-element materials and 10 recently used astronautic structural materials against high-energy protons found the elements with low atomic number to be ideally suited, as well as fiber-reinforced polymers, such as carbon-fiber-reinforced polymers
[48].
Besides these simulation-based suggestions, Stehlikova et al. report in-orbit measurements of different carbon-fiber composites, performed in the CubeSat VZLUSAT-1
[49]. The shielding material contains carbon fiber meshes and light elements in the resin. They found a more or less energy-independent shielding for the tungsten reference shield, while the carbon composite shows higher shielding for lower energy (up to 20 keV) of the incident rays and lower values for higher energies. Nevertheless, they mentioned that the areal mass of the carbon shield is one order of magnitude lower than that of the tungsten shield.
Different types of high-energy radiation from a
210Pb source (X-rays, gamma-rays, and high-energy electrons with energy 1.16 MeV) were used to investigate the shielding properties in vacuum of different pitch-based graphite fiber composites, materials which may one day replace the usual aluminum structures in spacecraft
[50]. For ionizing radiation, pure graphite epoxy composites were found to have only 40% of the aluminum mass absorption. Bromine intercalation, however, significantly increased this result to 170% of the mass absorption coefficient of aluminum, and iodine monobromide intercalation even led to 300% of the aluminum mass absorption coefficient, showing the large changes connected with intercalation. Shielding against β particles, on the other hand, was nearly identical for all materials under examination.
Besides purely experimental and purely simulating investigations, Sihver et al. correlated both by simulating with the 3D Monte Carlo Particle and Heavy-Ion Transport code System (PHITS) and measuring with the anthropomorphic phantom “Matroshka”, mimicking a human head and torso and equipped with 6000 radiation detectors, which is located on the ISS
[51]. They found very good agreement between simulated and measured radiation doses, in spite of a simplified model of the shielding of the ISS, with the simulations slightly overestimating the radiation doses.