Battery safety is a prominent concern for the deployment of electric vehicles (EVs). The battery powering an EV contains highly energetic active materials and flammable organic electrolytes. Usually, an EV battery catches fire due to its thermal runaway, either immediately at the time of the accident or can take a while to gain enough heat to ignite the battery chemicals. There are numerous battery abuse testing standards and regulations available globally. Therefore, battery manufacturers are always in dilemma to choose the safest one. Henceforth, to find the optimal outcome of these two major issues, six standards (SAE J2464:2009, GB/T 31485-2015:2015, FreedomCAR:2006, ISO 12405-3:2014, IEC 62660-2:2010, and SAND2017-6295:2017) and two regulations (UN/ECE-R100.02:2013 and GTR 20:2018), that are followed by more than fifty countries in the world, are investigated in terms of their abuse battery testing conditions (crush test).
1. Introduction
To realize a sustainable energy supply, researchers seek to substitute the use of traditional fossil fuels with clean and renewable energy resources. One of the potential solutions is to move from internal combustion engine (ICE) vehicles, i.e., gasoline vehicles, to vehicles that are powered by electricity, or alternative fuels like biofuels, hydrogen, liquefied natural gas (LNG), compressed natural gas (CNG), or hybrid vehicles (a combination of the aforementioned fuels) [1][2][3]. However, research has demonstrated that vehicles powered by electricity, i.e., electric vehicles (EVs) are the most effective solution [4][5][6][7][8][9]. These can reduce environmental pollution and will subsequently help to avoid global warming and climate change [10][11][12][13].
In recent years, globally the automotive industry has noticed a significant deployment of EVs in the market [3][14][15]. For example, in the year 2018, Europe (EU) attained more than one million EVs in the market [16]. Numerous researchers from a companies such as Shell Deutschland and Prognos AG including academicians such as Kugler et al. predicted the increment in the future sales of EVs [17][18]. This increment is not only due to technological advancement but is also policy-driven, as mentioned in the report of “Global EV Outlook 2020” [19]. As per the International Energy Agency (IEA), there will be 125 million EVs around the world by the year 2030 [20], and similar further information regarding the prediction and the future stock of EVs in Germany was researched by Machuca et al. and Kahn [14][21].
According to Spielbauer et. al., it is anticipated that the battery fire incidents and the severity of such incidents will increase in the future due to, (a) the rise in energy density of the new cells that are being developed, and (b) an increasing demand of EVs and the batteries that are used within EVs
[22]. According to Wang et al., Kubjatko, Goodman et al. and Pan et al. EVs facing an accident can mechanically deform, malfunction, or can completely fail
[23][24][25] the battery. Some of the primary reasons that can cause battery failure are
[26]:
- Internal cell short circuit: This kind of severe event can happen abruptly and without any pre-warning. Zhao et. al. and Larsson found that this event can occur because of multiple reasons such as mechanical deformation or manufacturing faults. They also noticed that another reason for an internal short circuit can be the dendrite formation within the cells [27][28]. According to Ahlberg Tidblad [29], this is a particularly disturbing cause because this type of failure occurs in batteries that are complied with industry standards;
- Mechanical deformation and impact: This cause can easily initiate an internal short circuit which consequently leads to a fire. Acute deformation can be due to certain types of crashes or ground surface conditions. Zhu et al. noted that battery packs are susceptible to penetration due to side collisions and road debris impacts [30]. The research conducted by Trattnig and Leitgeb [31] showed that the absolute scenario in a car crash can be the amalgamation of leaking fluid or gases near ignition sources like electrical arcs and/or hot surfaces;
- Charge: The purpose for which the batteries are tailored is to collect a specific amount of energy over a definite period of time. In the instances where limits are surpassed, due to rapid charging or overcharging, the battery performance can degrade, or it can even fail completely [26];
- Discharge: Over discharge occurs when the battery cells are discharged below their manufacturer recommended minimum voltage. During this process, the conductive copper particles are released in the electrolyte, which consequently leads to an internal short circuit of the battery. Usually, battery safety systems are there to stop such situations. However, if such a safety system fails or the battery is abused, there is a possibility of battery failure [32];
- External short circuit: This type of the short circuit also falls under the category of an electric abuse, which can easily destabilise the battery. An external short circuit happens when the battery faces an impact and/or deformation [26];
- High-temperature exposure: In real-time applications, the battery needs to be cooled during its operation: however, if the ambient temperature is higher than the internal temperature, battery decomposition mechanisms are triggered causing the battery to produce extreme levels of heat. This high level of heat can result in an internal short circuit or thermal runaway, which consequently reduces the safety margin [26];
- Thermal runaway: In a battery, when exothermic chemical reactions are producing more heat than is being dissipated, it enters the thermal runaway condition. In case of severe accidents, because of thermal runaway, the battery can emit heat/fumes, catch fire, or in a worst-case scenario explode [6][24][33][34][35][36].
- 1. Internal cell short circuit: This kind of severe event can happen abruptly and without any pre-warning. Zhao et. al. and Larsson found that this event can occur because of multiple reasons such as mechanical deformation or manufacturing faults. They also noticed that another reason for an internal short circuit can be the dendrite formation within the cells [27][28]. According to Ahlberg Tidblad [29], this is a particularly disturbing cause because this type of failure occurs in batteries that are complied with industry standards;
- 2. Mechanical deformation and impact: This cause can easily initiate an internal short circuit which consequently leads to a fire. Acute deformation can be due to certain types of crashes or ground surface conditions. Zhu et al. noted that battery packs are susceptible to penetration due to side collisions and road debris impacts [30]. The research conducted by Trattnig and Leitgeb [31] showed that the absolute scenario in a car crash can be the amalgamation of leaking fluid or gases near ignition sources like electrical arcs and/or hot surfaces;
- 3. Charge: The purpose for which the batteries are tailored is to collect a specific amount of energy over a definite period of time. In the instances where limits are surpassed, due to rapid charging or overcharging, the battery performance can degrade, or it can even fail completely [26];
- 4. Discharge: Over discharge occurs when the battery cells are discharged below their manufacturer recommended minimum voltage. During this process, the conductive copper particles are released in the electrolyte, which consequently leads to an internal short circuit of the battery. Usually, battery safety systems are there to stop such situations. However, if such a safety system fails or the battery is abused, there is a possibility of battery failure [32];
- 5. External short circuit: This type of the short circuit also falls under the category of an electric abuse, which can easily destabilise the battery. An external short circuit happens when the battery faces an impact and/or deformation [26];
- 6. High-temperature exposure: In real-time applications, the battery needs to be cooled during its operation: however, if the ambient temperature is higher than the internal temperature, battery decomposition mechanisms are triggered causing the battery to produce extreme levels of heat. This high level of heat can result in an internal short circuit or thermal runaway, which consequently reduces the safety margin [26];
- 7. Thermal runaway: In a battery, when exothermic chemical reactions are producing more heat than is being dissipated, it enters the thermal runaway condition. In case of severe accidents, because of thermal runaway, the battery can emit heat/fumes, catch fire, or in a worst-case scenario explode [6][24][33][34][35][36].
There are negligible data available in relation to the incidences of EV fires; however, according to Norwegian insurance companies, a study conducted by
[26] the percentage of EV fire accidents is approximate 4.8%, out of the total number of vehicle fire accidents. Moreover, Gehandler et al.
[37] found that on an average one vehicle fire that occurs every year during battery charging in multistorey car parking or big garages. Some of such catastrophic battery incidents around the world are presented in
Table 1.
Year |
Region/Country |
Vehicle |
Incident and Cause |
2010 |
Scandinavia |
Nissan Qashqai |
Vehicle caught fire while charging |
2011 |
China |
Zotye M300 EV |
Vehicle caught fire while driving and hence all-electric taxis were temporary pulled off the streets |
2011 |
USA |
Chevrolet Volt |
Fire emerged due to leaking coolant three weeks after crash test |
2012 |
USA |
General Motor vehicles |
Battery exploded due to incompatible operating cycle and battery prototype during tests |
2012 |
USA |
Fisker Karma |
Rate of fire: Two per thousand. Usually, a vehicle catches fires while it is parked |
2012 |
USA |
Three Toyota Prius and Sixteen Fisker Karma |
During a hurricane, vehicles caught fire when immersed in seawater as it worked as the conductor between both +ve and −ve battery poles |
2012 |
Sweden |
Fiat 500 |
Fire ignited in the engine compartment while charging |
2013 |
France |
Two Bolloré Bluecar |
First vehicle caught fire while parked and the fire spread to the second one as well |
2013 |
Mexico |
Three Tesla Model S |
Vehicle caught fire by hitting road debris, tree and the concrete wall in less than two months. Consequently, Tesla was pushed to reinforce the vehicle construction |
2013 |
Japan |
Mitsubishi Outlander PHEV |
Battery overheating issue identified so production was stopped for five months |
2014 |
Canada |
Tesla Model S |
Vehicle caught fire while parked in the garage and was bought only 4 months prior to the incident |
2015 |
Norway |
EV |
Vehicle faced accident with a train and caught fire after two hours, which took a long time to extinguish |
2016 |
Norway |
Tesla Model S |
Caught fire due to short circuit while charging at supercharger station |
2016 |
France |
Tesla Model S |
Faulty electric connection caused a fire during the test drive |
2017 |
UK |
Smart Fortwo electric drive |
Faulty electricals caused a fire while charging |
2017 |
China |
Tesla Model X |
Vehicle was at high speed and caught fire after the crash. Backseat passengers evacuated via front doors |
2017 |
USA |
Tesla Model X |
Vehicle caught fire after the crash and was re-ignited on the tow truck and third time at the tow yard |
2018 |
Thailand |
Porsche Panamera |
Vehicle was plugged in and was being charged from the house socket when it caught fire |
2018 |
The Netherlands |
Jaguar I-Pace |
Newly delivered vehicle caught fire while parked |
2018 |
USA |
Tesla Model X |
Vehicle caught fire after the crash and was re-ignited within a few days two times, while parked in the tow yard |
2018 |
USA |
Tesla Model X |
Vehicle caught fire after the crash and was extinguished on-site with the help of an extinguisher but was re-ignited two times within a week at the tow yard |
2018 |
USA |
Tesla Model S |
Battery casing was ruptured and the vehicle caught fire immediately after hitting the pole and nearby wall. Fire re-ignited two times, (a) while loading on the tow truck, and (b) at the tow yard |
2018 |
USA |
Tesla Model S |
Battery venting caused a fire while driving |
2018 |
USA |
Tesla Model S |
Fire started in the parking area and was re-ignited in the tow yard |
2018 |
USA |
Tesla Model S |
Vehicle caught fire after the crash which was extinguished swiftly but was reignited at the time of loading on the truck and thereafter at the tow yard |
2018 |
USA |
Tesla Model S |
Parked vehicle caught fire two times in the workshop parking area |
2018 |
USA |
Tesla Model S |
Caught fire during driving and was extinguished swiftly |
2018 |
Thailand |
Porsche Panamera, PHEV |
Caught fire while charging from the home socket. Consequently, the fire was spread throughout the home |
2018 |
Switzerland |
Tesla, BEV |
Vehicle was turned over after crashing with a barrier and immediately caught fire |
2018 |
China & Spain |
Tesla, BEV and BMW i3 REx, PHEV |
Unknown spontaneous ignition caused the fire in the parked vehicle |
2018 |
China |
Zhong Tai, BEV and 3 other BEVs |
Fire was ignited without any accident. Two vehicles caught fire during charging and rest while driving |
2019 |
The Netherlands |
BMW I8 |
Caught fire in the showroom and was quenched with water |
2019 |
China |
3 BJEV minivans |
Companies do not prefer this model anymore as it catches fire while charging |
2019 |
China |
Tesla Model S |
Rapid development of fire was noticed due to battery venting within 30 min of the arrival of a vehicle while it was parked in the garage |
Based on the analysis (causes and comments) of
Table 1 and by
[27][69][70][71], it can be said that EV batteries are prone to failure in the case of accidents, i.e., there is a risk of the battery catching fire immediately after the accident, or it can have a delayed event. Thus, it is important to develop a safer and reliable battery, i.e., correlated risks can be managed to achieve a suitable level of safety on which the consumer can rely
[72][73][74][75]. To develop such a battery, several regulatory bodies around the world have developed various battery standards and regulations. These standards and regulations have a variety of testing procedures known as abuse tests. These abuse testing procedures have various testing conditions and parameters within them to test the batteries.
2. Abuse Testing: Crush Test
While introducing EVs in the market, the manufacturers must show that the vehicle and its components match the safety limits assigned by the regulatory bodies. The battery is one of such components that is considered as a primary source of hazard for EV consumers
[76] and hence, it needs to undergo rigorous safety tests before introducing EVs into the market
[77]. Standards are usually considered as good practice documents. If the standard is not followed then the product manufacturer should justify the different route chosen
[78].
It is important to note that standards encompass a variety of aims and objectives. A specific standard can have the combination of many objectives such as design, performance test, safety design, safety test, environmental protection, classification, and recommendation
[78]. For example, FreedomCAR:2006
[79] and SAE J2464:2009
[80] help to investigate and gather the battery response under severe conditions, i.e., outside the normal operating range, for manufacturers to examine the battery system design failure. On the other hand, standards such as ISO 12405-3:2014
[81] and IEC 62660-2:2010
[82] provide the detailed test procedure to observe the reliability of the battery and also specifies the acceptable safety requirements.
Figure 1 provides an overview of the standard abuse tests, categorised as per the nature of the test conducted and misuse (electrical, chemical, thermal and mechanical). The tests are conducted either on the cell, module, or pack level depending on the respective standard or regulation. Underwriter laboratories have detailed information on each of these abuse tests
[83]. The crash/crush test was marked green as this article focuses on this test.
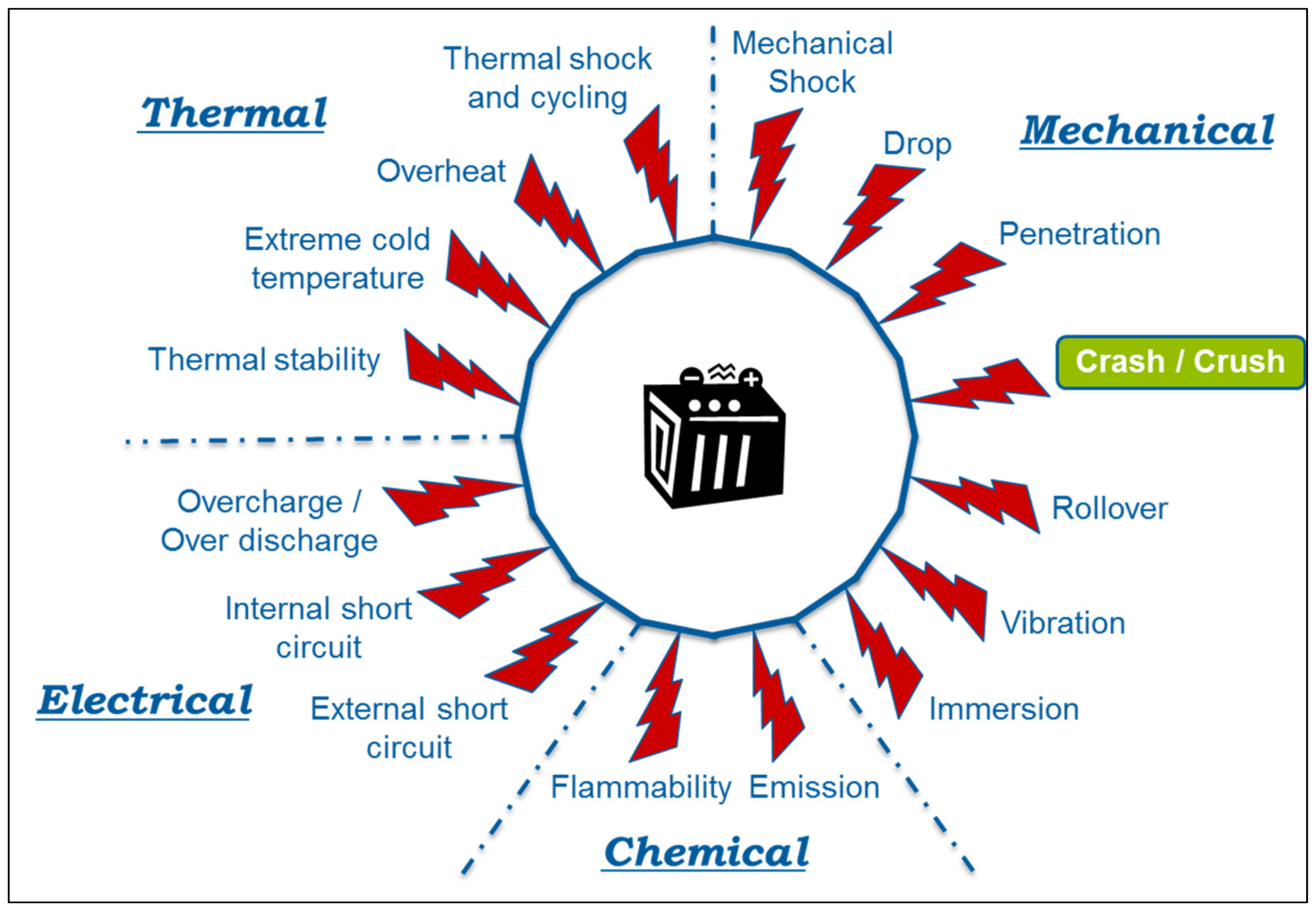
Figure 1. Abuse tests for the battery as per different standards and regulations
[73].
Despite having such a wide variety of abuse tests, EV batteries might catch fire after an accident, i.e., either immediately or erstwhile
[22][84]. It was forecasted by Machuca et al. that such incidents can go up to 135,000 vehicles/year by the year 2030
[14]. The detailed information on battery incidents and handling such incidents are elaborated by
[85]. Considering this forecast and the number/examples of accidents that have happened so far, it can be said that the crush test should be paid more attention and should be investigated in depth
[22].
3. Conclusions
Overall, after analysing multifarious standards and regulations, it can be concluded that energy storage in vehicles has always been associated with several risks. The combustion engine vehicles that are used in today’s world took several decades to reach current safety standards and a similar challenge of time consumption and technological advancement is currently faced by EVs. However, the development time can be significantly shortened by modern technologies, as well as experience from previous and ongoing research.
After analysing the selected standards and regulations, it was identified that the ambiguities need to be removed and clarity can be provided in terms of testing procedures that are dedicated for cell, module, and pack level testing. For example,
Table 29 shows such ambiguity for the selected standards and regulations against the crush parameters such as procedure, crushing speed, SoC, press position, crusher shape and dimensions, and the number of testing samples at the cell, module and pack level. Moreover, further ambiguity needs to be resolved, such as the acceptance criteria mentioned in UN/ECE-R100.02:2013, which should also be mentioned by other standards and regulations.
Table 29. Ambiguity in standards and regulations for crush parameters different levels.
Standards and Regulations |
Crush Parameters 1 Levels |
Cell |
Module |
Pack |
SAE J2464:2009 |
✓ |
✓ |
✓ |
ISO 12405-3:2014 |
× |
× |
✓ |
IEC 62660-2:2010 |
✓ |
× |
× |
FreedomCAR:2006 |
✓ |
✓ |
✓ |
SAND2017-6925:2017 |
✓ |
✓ |
✓ |
GB/T 31485-2015:2015 |
✓ |
✓ |
✓ |
UN/ECE-R100.02:2013 |
× |
✓ |
✓ |
GTR 20:2018 |
× |
✓ |
✓ |
Moreover, it is also concluded that (a) there is a scope of harmonisation of standards and regulations, and the current proposals should be investigated with priority and should be implemented in the market, and (b) augmentation can be performed by considering real-life vehicle crash scenarios, i.e., dynamic behaviour of the vehicle. Future works that can be performed are (a) the study of the impactor material, i.e., cell failure behaviour based on different impactor materials, and (b) comparison between the test outcomes, i.e., the impact of SoC on cell failure behaviour, carried out according to different standards and regulations. Altogether, it can be said if these steps are adopted then certainly battery and EV manufacturers will have significant ease during the manufacturing and approval processes and will also enhance the safety of EV consumers.