With the progression of industrialization and the increasing incidents of crude oil spills, the issue of pollution resulting from oily sewage has become increasingly pressing
[1,2][1][2]. The presence of oil and other contaminants, including toxic organic compounds, in water not only undermines the ecological system and depletes resources
[3,4][3][4] but also poses a major threat to human health
[5,6][5][6]. To solve this problem, promote economic efficiency and sustainably advance. It is crucial to treat and effectively reuse oily wastewater
[7]. Oil–water mixtures can typically be classified into three categories: free oil–water mixtures, oil dissolved in water, and oil–water emulsions
[8]. The presence of oil dissolved in water is generally not deemed necessary for separation. Free oil–water mixtures, which contain larger dispersed droplets (>20 μm), can separate in a static state as a result of thermodynamic instability, with the denser phase settling and the lighter phase floating to the surface. Conversely, oil–water emulsions are thermodynamically stable colloidal dispersions composed of micro/nanoscale droplets (<20 μm) of the dispersed phase in a continuous phase
[9]. The stability of the emulsion droplets is further perpetuated by the presence of surfactants, making them difficult to separate naturally over time. Conventional approaches for treating oily wastewater include physical precipitation, chemical flotation, mechanical centrifugation, etc.
[10]. However, these methods are associated with high costs, low efficiency, and the potential for secondary pollution, limiting their practical application
[2,11,12][2][11][12].
Metal–organic frameworks (MOFs), a novel class of porous materials composed of metal ions and organic ligands
[16,17[16][17][18],
18], hold huge potential in the field of oil–water separation. MOFs show significant advantages over zeolites, activated carbon, and other porous materials in terms of adjusted pore structure and properties
[19,20,21][19][20][21]. Firstly, MOFs have the advantage of easy microstructure construction and pore-size adjustment
[22]. Secondly, their surface wettability can be easily tuned
[23]. Additionally, due to their low density, high porosity, and high surface area, MOFs possess suitable adsorption properties, enabling them to effectively address complex pollutants such as heavy metal ions, dyes, drugs, antibiotics, and other pollutants in wastewater
[24,25,26,27,28,29][24][25][26][27][28][29]. The versatility of MOFs also confers multifunctionality to oil–water separation materials, including photocatalysis
[30] and anti-biological pollution
[31].
2. The Mechanism of Oil–Water Separation
2.1. Basic Theory of Wettability
Wettability, a macroscopic representation of the interaction between a liquid and a solid material, is primarily determined by the surface morphology and chemical composition of the solid material. The contact angle between a liquid droplet’s edge and the surface of the material is used to calculate the wettability of a liquid on a solid surface. Traditionally, materials were considered lyophobic when the contact angle was greater than 90° and lyophilic when the contact angle was less than 90°. However, recent research has suggested that the intrinsic wetting threshold to differentiate between hydrophobic and hydrophilic surfaces should be 65°
[33][32]. Additionally, materials are considered superlyophobic when the contact angle is more than 150° and superlyophilic when the contact angle is less than 5°. These materials with superlyophilic or superlyophobic properties are referred to as special wetting materials
[34,35,36,37][33][34][35][36]. Materials with selectivity for water and oil, as determined by their opposite wettability properties, can be used to separate oil–water mixtures.
In air, the contact angle of a droplet on an ideal smooth solid surface can be expressed by Young model (
Figure 21A), and the contact angle (
θ) can be calculated by Young Equation (1):
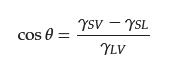
where
γSV,
γSL, and
γLV denote the surface tension between the solid/gas, solid/liquid, and liquid/gas interfaces, respectively.
Figure 21. Schematic diagram of the wetting state of droplets on a solid surface in air: (A) Young model, (B) Wenzel model, and (C) Cassie model. The corresponding state of oil droplets on a solid surface underwater: (D) Young model, (E) Wenzel model, and (F) Cassie model.
In reality, the material surface is often rough. According to Wenzel, a rough surface’s actual contact area is substantially bigger than its apparent contact area (
Figure 21B). He put out an enhanced model to describe the effect of roughness on the wettability of rough surfaces:
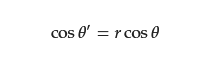
Among them,
θ′ is the contact angle of droplets on the rough surface, and
r is the roughness factor of the solid surface, which is defined as the ratio of the actual solid–liquid contact area to the apparent contact area of the rough surface. For the rough surface,
r > 1, when
θ < 90°, that is, when the material is lyophilic, the rough structure can make the material more lyophilic; when
θ > 90°, that is, when the material is lyophobic, the rough structure makes the material more lyophobic. The contact angle of the droplets on this surface, however, may be determined using the Cassie model when air is trapped in the space between the droplets and the rough structure, forming a solid/liquid/gas three-phase interface (
Figure 21C).

where
θ″ is the contact angle of droplets on the solid–gas multiphase surface, and
f is the ratio of the solid–liquid interface contact area to the total contact area (solid–liquid contact area and gas–liquid contact area).
The Young model, Wenzel model, and Cassie model can not only analyze the wettability of droplets on solid surfaces in the air but also effectively describe the oil–water–solid system (
Figure 21D–F). The oil contact angle (
θOW) on an ideal underwater smooth surface for the oil–water–solid three-phase system can be expressed as:
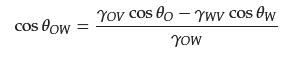
where
θO and
θW are the contact angles of oil and water droplets in air, respectively;
γOV,
γWV, and
γOW are the interfacial tensions at the oil–vapor, water–vapor, and oil–water interfaces, respectively. Therefore, if
γOVcos
θO <
γWVcos
θW, an underwater oleophobic surface can be obtained; when
γOVcos
θO >
γWVcos
θW, an underwater oleophilic surface can be obtained. Most hydrophilic surfaces are underwater oleophobic because the surface tension of water is significantly greater than that of oils or other organic liquids. Hydrophobic/oleophilic surfaces at the solid–air–liquid interface always show lipophilicity at the solid–water–oil interface. Similar to the Wenzel and Cassie models in air, the rough surface can enhance the wetting property of materials underwater environment. Based on the aforementioned research, it is possible to construct the superhydrophobic-superoleophilic and superhydrophilic-underwater superoleophobic materials utilized for oil–water separation by controlling their surface chemical composition and creating the materials’ microstructures.
2.2. Separation of Free Oil–Water Mixture
One of the crucial factors influencing the effectiveness of materials for oil–water separation is the penetration pressure (∆
Pc), which is the highest pressure applied to the surface before the liquid penetrates the membrane pore. For pores with cylindrical geometry, ∆
Pc can be determined by the Young–Laplace Equation (5):
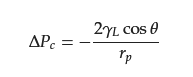
where
γL denotes the surface tension of the liquid,
θ is the contact angle of the liquid in a plane, and
rp denotes the pore radius. In air, if
θ > 90°, ∆
Pc > 0, indicating that a certain external force is generated on the material surface to prevent the liquid from passing through the porous material, and an external pressure must be applied to pass through.
The penetration pressure of oil-in-water ∆
PcW can be calculated from Equation (6) for a three-phase solid–water–oil contact in an aqueous environment as follows:
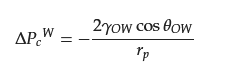
where
γOW denotes the water/oil interfacial tension, and
θOW denotes the underwater oil contact angle. When
θOW > 90°, ∆
PcW > 0, indicating that a certain external force is generated on the material surface to prevent the oil phase from entering the pore space, and the larger
θOW is, the larger the value of ∆
PcW is.
2.3. Separation of Oil–Water Emulsion
For emulsion separation, there are two main effects currently known: the “pore-size sieving” effect and the emulsion-breaking effect, which are shown in
Figure 42. The “pore-size sieving” effect refers to the separation of oil-in-water emulsions using hydrophilic membranes with pore sizes smaller than the particle size of the emulsion. Under the influence of gravity, the oil droplets are intercepted, allowing the water phase to pass through. Similarly, water-in-oil emulsions can be separated using oleophilic membranes with pore that are smaller than the emulsion’s particle size
[39][37]. However, the need for small pore sizes in the “pore-size sieving” effect often results in reduced separation flux, leading to the development of the emulsion-breaking effect. This process involves three main steps: (1) the emulsified droplets are captured by an agglomerated medium under hydrodynamic or other external forces; (2) the droplets combine to form larger droplets through wetting and shear collisions; and (3) the larger droplets are separated from the surface of the agglomerated medium through gravity and buoyancy
[40][38]. By combining the “pore-size sieving” effect and emulsion breaking, emulsions can be separated with relatively larger membrane pore sizes, thus improving the separation flux and efficiency.
Figure 42.
Separation mechanism of free oil–water mixture and oil–water emulsion.
3. Methods to Prepare MOFs-Based Materials for Oil–Water Separation
3.1. In Situ Growth Method
3.1.1. Substrate Pre-Modification Method
The substrate pre-modification method involves modifying the surface of the substrate prior to immersing it in a configured precursor solution for the self-growth of the film. The role of surface modifiers is mainly to anchor metal ions or organic ligands used to generate MOFs. Mussel-inspired polydopamine (PDA) is a widely used surface modifier. It mainly acts as a binder to improve the substrate and is not involved in subsequent reactions. Song et al. used PDA coating to grow Cu-MOF on stainless steel mesh (SSM), which can continuously separate heavy oil–water mixture for more than 160 min with an efficiency of >98.5%
[41][39]. Tannic acid (TA) and Ti
4+ were combined by Wang et al. to create metal phenolic networks (TTN), which were applied to the PVDF membrane’s surface. Then, the as-modified membrane was immersed in Zn
2+ and 2-methylimidazole solution to synthesize ZIF-8 by self-loading. TTN offers general metal chelating affinity (TA-Zn
2+) and thereby can manipulate the even dispersion of ZIF-8 nanocrystals.
3.1.2. Precursor Sacrifice Method
Utilizing some metal resources on the membrane as the precursor, MOFs could be obtained on the membrane directly with the subsequent conversion reaction. Metal oxides and hydroxides are the most used metal precursors in this case because they are easy to react with some acidic organic ligands to form the target MOF.
3.1.3. Crystal Seed Growth
The crystal seed growth method is a process in which MOF crystals are nucleated and grown separately. The substrate is first covered with a crystal seed layer in this procedure. Then, the substrate with the seed layer is placed in a solution containing metal ions and organic ligands, allowing for the secondary growth of MOFs. As an example, a ZIF-8 seed solution was synthesized, and the substrate was immersed in it. This resulted in the growth and crystallization of ZIF-8 on the substrate through a secondary growth process under high-temperature conditions. Finally, further modification with PVA resulted in the formation of a PVA/ZIF-8-coated substrate, which was capable of separating both oil-in-water and water-in-oil emulsions
[45][40].
3.2. Deposition Method
3.2.1. Direct Deposition
The direct deposition method involves the direct synthesis of MOF composite membranes by placing the substrate into a mixture of metal ions and organic ligands. For example, a PP/ZIF-8 composite membrane can be prepared by simply adding polypropylene (PP) non-woven fabric into a mixed solution of zinc nitrate and 2-methylimidazole at room temperature, and it has the ability to separate free oil–water mixtures
[46][41].
3.2.2. Electrochemical Deposition
The electrochemical deposition method, similar to the direct deposition method, involves the rapid growth of MOFs on the substrate through the use of metal cations and organic ligands in the presence of an applied voltage. For example, after only 200 s of applied voltage, Co
2+ and 2-methylimidazole react and accelerate to produce electrochemical deposition that aggregates onto the copper mesh, resulting in the formation of a uniform and dense ZIF-67 film
[48][42]. This method offers advantages such as a short process time, uniform growth, and a high deposition rate.
3.2.3. Layer-by-Layer Self-Assembly
The layer-by-layer (LBL) self-assembly method is a distinctive approach that involves alternating the deposition of metal ions and organic ligands instead of directly mixing them. The substrate can either be modified or left unmodified. The key factors that influence the membrane’s performance are the number of alternating depositions and the concentration of precursors. In a study by Gao et al., UiO-66-NH
2-coated PP membranes with varying thicknesses were prepared using the LBL method. The PP membrane was first soaked in a solution of Zr
4+ ions at high temperature, followed by immersion in a solution of 2-aminoterephthalic acid. By repeating this alternating process, UiO-66-NH
2-coated PP membranes with different thicknesses were obtained
[49][43]. Although the LBL method allows for the controlled synthesis of MOFs membranes, it is a time-consuming process.
3.2.4. Filtration Deposition
The filtration deposition method is a technique for creating functional membranes by depositing solid suspensions on a substrate using vacuum filtration. For example, Zhu et al. first synthesized UiO-66-NH
2 powder using Zr
4+ and 2-NH
2-benzenedicarboxylate by the solvent thermal method, added it to chitosan solution, and attached it to a cellulose membrane through vacuum filtration to obtain a superhydrophilic and underwater superoleophobic membrane, which can effectively separate oil-in-water emulsions and has excellent corrosion resistance
[50][44].
3.2.5. Spin-Coating
The spin-coating method involves coating a substrate with a suspension of MOFs using a spinning instrument. For instance, ZIF-8 nanoparticles were evenly deposited on a polyacrylonitrile (PAN) fiber membrane using the spin-coating method to create a biomimetic inverse desert beetle ZIF-8/PAN composite nanofiber membrane that can effectively separate oil-in-water emulsions
[52][45]. The spin-coating method is simple to operate, but it can be challenging to achieve a uniform distribution of MOFs with a strong attachment to the substrate.
3.3. Blending Membrane Method
In contrast to the above methods of coating MOFs onto the membrane surface, the blending membrane method focuses on creating a composite membrane in which the MOFs are dispersed within the membrane materials. This can be achieved through two main approaches: electrospinning and phase inversion.
3.3.1. Electrospinning
Electrospinning is a process in which droplets are charged and transformed into nanometer-sized fibers through stretching and solidification. The precursor solution is extruded by adjusting the applied voltage and the receiving distance, and the solution is continuously ejected from the tip of the droplet and gathers on the receiver to form a film when the electrostatic repulsion force overcomes the surface tension.
3.3.2. Phase Inversion
Phase inversion is a method of preparing homogeneous polymer solutions, which are then transformed into a three-dimensional macromolecular network gel structure by adding a non-solvent. The resulting structure is solidified into a film, making it a widely used method for the preparation of mixed matrix membranes (MMMs).
4. The Classification of MOFs Used for Oil–Water Separation
4.1. ZIF Series
ZIFs, also known as zeolite imidazolate frameworks, are constructed from transition metals (zinc, cobalt, indium, etc.) with tetrahedral coordination geometry and imidazole-based organic ligands. ZIF series is one of the most extensively used MOFs in the field of oil–water separation.
The effectiveness of oil–water separation using ZIFs-based membranes is found in the pore-size sieving effect, where different substrate sizes are suitable for separating different types of oil–water mixtures.
T
4.2. UiO Series
The UiO (Universitetet I Oslo) series of MOFs are known for their versatility and widespread use in various fields. Among the UiO series, UiO-66 and its derivatives have gained popularity for their effectiveness in oil–water separation. These MOFs have a three-dimensional microporous structure composed of a regular octahedron (Zr
6O
4(OH)
4) containing Zr ions that are connected to 12 organic ligands of terephthalic acid (BDC). The structure consists of central pore cages in the shape of octahedrons and eight smaller tetrahedral corner cages.
4.3. MIL Series
MIL series, also known as Lavahir skeleton series materials, are generally composed of trivalent metal ions (such as aluminum, chromium, iron, etc.) and carboxylic acid ligands. In addition to the extensive adsorption properties of MOFs, Fe-based MOFs can often endow the materials with photo-Fenton catalytic properties.
4.4. Other MOFs
In addition to the ZIF, UiO, and MIL series, other MOFs such as HKUST-1, PCN series materials (containing multiple cub octahedral nanopore cages and forming a pore cage-pore channel-like topology in space), and Cu-MOFs have recently been developed for use in oil–water separation application.
5. Conclusions
Most studies using MOF-based oil–water separation membranes are somewhat flawed, and the following efforts are still needed to solve the environmental problems of wastewater: (1) The long-term performance of MOFs-based membranes has been neglected, especially in continuous oil–water separation processes. Researchers can therefore focus on ways to improve the long-term durability of the membranes; (2) Most MOFs materials are unstable in wet environments due to weak coordination between their own metals and organic ligands. How to improve the stability of MOFs without affecting their structural properties remains to be investigated. (3) The specific wastewater environment is very complex and may contain organic molecules, heavy metals, microorganisms, etc. MOFs-based membranes need to be more stable and fouling resistant in the complex components. Based on this, there is a need for researchers to create materials with better stability and self-cleaning properties. (4) MOFs-based membranes should be used in a wider range of applications, and they must also be able to treat actual wastewater, from municipal wastewater to industrial wastewater, broadening their practical applications. (5) In addition, there is still a lack of longitudinal comparisons of data on the separation efficiency, mechanical and chemical stability, and pollution resistance of MOF-based membranes based on the separation of complex oil–water mixtures.