Energy harvesting, a cutting-edge technology that captures wasted energy from vehicles, constitutes a means to improve the efficiency of electric vehicles. Dissipated energy can be converted into electricity using regenerative energy recovery systems and put to various uses.
1. Potential Energy Sources
In an electric vehicle, energy is stored in the battery, which functions as the vehicle’s primary power source (
Figure 1). The battery is used to power the electric motor, which drives the wheels and propels the car forward
[15][1]. However, some of the energy stored in the battery is dissipated or lost in various sections of the vehicle due to thermal or vibrational causes. These losses can be collected and recycled as alternative energy sources, increasing the total efficiency of the electric vehicle. The interaction between the ground and the wheel, the braking system, the shock absorber, the electric motor and battery, and the aerodynamic drag are all possible sources for energy recovery. These energy sources are depicted in a diagram that illustrates the flow of energy from the battery used in an electric car. The aim of energy recovery is to convert these losses into usable energy that can then be reused to power the vehicle or stored in the battery for later use.
Figure 1. Energy flow in electric vehicle.
Energy flows from the battery to the electric motor, which then converts this electrical energy into mechanical energy to drive the wheels in an electric car. The electric motor is driven by an inverter, which converts the direct current (DC) from the battery to the alternating current (AC) required by the motor. When the vehicle is braking or coasting, the electric engine can function as a generator, converting some of the vehicle’s kinetic energy back into electrical energy. This energy is then stored in the battery and used to power the engine later. Furthermore, the vehicle may have auxiliary systems that require electrical energy to function, such as air conditioning or heating. This energy is derived from the battery as well. In summary, energy flows from the battery to the electric motor in an electric car, with energy captured during braking or coasting and used to recharge the battery.
2. Interaction Ground–Wheel
In a vehicle, the interaction between the ground and the wheel creates a major source of energy loss. Rolling resistance is the force that resists the direction of movement the tire makes on the traction surface during this interaction. Rolling resistance is caused by deformation in the tire when it comes into contact with the ground, and results in a loss of mechanical energy. Fortunately, using suitable technologies, this energy can be captured and transformed into a new source of energy and adding to efficiency. The tire, as the final component of the driveline, is critical in this respect
[16][2]. The study of mechanical energy loss through contact has been a topic of interest for researchers, who aim to find ways to harness this energy for practical use
[17][3].
3. Braking System
Various studies
[18][4] have recorded the conversion of kinetic energy into thermal energy caused by the friction between the brake disc and pads during the braking process. These studies have recorded a wide range of braking temperatures, with temperatures as low as 150 °C reported in works such as
[19,20][5][6]. Temperatures between 150 °C and 300 °C have been measured by others, including
[21[7][8][9][10][11][12],
22,23,24,25,26], while temperatures above 300 °C have been documented by
[27,28,29,30][13][14][15][16]. Furthermore, braking can cause triboelectrification, which provides another possible source of recoverable energy
[31][17]. As a result, the energy recovered from the braking mechanism can be divided into two types: thermal energy and triboelectric energy.
4. Shock Absorber
Another form of energy loss in a vehicle that can be recovered is that of the shock absorber. The shock absorber is critical in delivering a comfortable ride and maintaining vehicle stability. It absorbs road bumps and vibrations, reducing the discomfort for passengers and wear on vehicle components. Because of its internal hydraulic resistance, the shock absorber transforms kinetic energy into heat energy. This heat energy can be recovered and converted into power. Through the piezoelectric effect, the shock absorber can also be used as a power source. The piezoelectric effect is the generation of an electric charge because of mechanical tension exerted on certain materials. As a result, the shock absorber can be integrated into a vehicle as a piezoelectric energy harvester. The car suspension facilitates the transmission of force and torque between the vehicle body and wheels. The automobile suspension, a key component that supports both the vehicle body and the wheels, helps to mitigate the impact caused by uneven road surfaces and guarantees a pleasant driving experience in the vehicle body
[32][18]. Both the tires and the vehicle suspension usually absorb vibrational energy, though the tires only absorb a small amount due to their limited damping ability. The suspension absorbs and dissipates the main amount of vibrational energy
[33][19].
5. Electric Motor and Battery
The main source of power in an electric vehicle is the electric motor. The motor converts the electrical energy from the battery into mechanical energy that propels the car. However, this process is not completely efficient, and some of the electrical energy from the battery is wasted as heat or sound. Furthermore, the battery suffers energy losses due to internal resistance and temperature changes, which impact the capacity. Consequently, the losses from an electric vehicle motor and battery are potential sources of energy that can be recovered and used for other purposes. The heat produced by the battery and electric motor can be used as a source of thermal energy. Several investigations have shown that these components contain heat. Battery temperatures below 40 °C have been reported in references
[34,35,36,37,38,39,40,41][20][21][22][23][24][25][26][27]. Meanwhile, studies such as
[42,43,44,45,46,47,48,49][28][29][30][31][32][33][34][35] measured temperatures ranging from 40 °C to 60 °C, with
[50,51][36][37] recording temperatures higher than 60 °C. Temperature changes in electric motors can be classified into three groups: less than 50 °C, as seen in
[52][38], between 50 °C and 100 °C, as seen in
[53,54,55,56,57,58,59][39][40][41][42][43][44][45] and above 100 °C, as seen in
[60,61,62,63,64,65][46][47][48][49][50][51].The reviews state that operating temperatures of Li-ion batteries typically range from −20 °C to 60 °C, with an ideal range of 20 °C to 40 °C for optimal performance and lifespan. The authors also note that temperature management is critical for preventing thermal runaway and ensuring safe operation of the battery system. Overall, the review supports the idea that careful temperature management is essential for the optimal performance, safety, and lifespan of electric vehicle batteries, and highlights the importance of ongoing research and innovation in battery thermal management to improve the efficiency and sustainability of electric vehicles.
6. Aerodynamic Drag Source
Aerodynamic drag is the resistance to motion produced by the air that surrounds a vehicle. It is a significant contributor to vehicle fuel usage and is caused by the interaction between the vehicle and the air it moves through. Aerodynamic drag can be decreased by streamlining the vehicle shape, reducing its frontal area, and optimizing its body design to minimize airflow turbulence. This reduction in drag results in less energy loss, which leads to lower fuel usage and lower emissions. Engineers can optimize the aerodynamic drag of a vehicle to reduce its effect on fuel consumption by controlling the airflow over the vehicle surface and through the underbody.
Aerodynamic drag happens when a vehicle is in motion and encounters resistance from the air relative to its speed. This opposing force, which causes a loss of momentum, can significantly affect vehicle fuel consumption and emissions. To offset this, aerodynamic drag can be reduced or captured
[63][49]. Recovering and utilizing this dynamic energy would be an asset for improving the total energy efficiency in an electric vehicle.
7. Applicable Technologies
Figure 32 shows the two major forms of energy that can be recovered from an electric vehicle: thermal energy and mechanical energy. There are specific technologies available to successfully recover these sources of energy, which have different levels of efficiency and have undergone simulation or experimental testing.
Tabl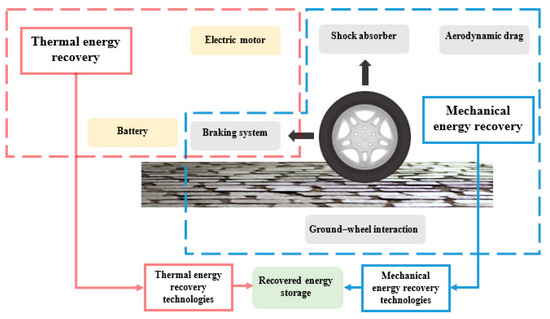
categorizes the various sources of recoverable energy and the technologies most appropriate for capturing them based on the efficiency and the method applied.