In the case of PBF-LB (
Figure 1), the irradiating heat source is a high powered, mirror-actuated laser (typically 100–2000 W and ~1 μm wavelength) that is sufficient to melt and fuse the metal powder layers (typically 30–90 μm thick)
[51][52]. The representative lasers applied in the PBF-LB process include CO2 laser, Nd: YAG laser (neodymium-doped yttrium aluminum garnet laser), and Yb-fiber laser (ytterbium-doped fiber laser)
[51][52][53]. The build chamber is filled with an inert gas (such as argon), and the build substrate onto which the part is built is preheated (preheating temperature can be up to 1200 C
[54][55]) to reduce the thermal gradients between the solidifying layers and the substrate. However, the thermal gradients remain high and PBF-LB parts are prone to high levels of residual stress which, in extreme cases, can cause severe part distortion or fracture. Post-build heat treatments are often applied to relieve stresses
[56]. The PBF-LB process is also commonly referred to by synonymous trademark terms, such as Selective Laser Melting (SLM) and Direct Metal Laser Sintering (DMLS), that have been popularised by machine manufacturers. However, the terminology standardised by the ASTM International is laser powder bed fusion
[57].
In the DED AM process, feedstock material in the form of powder or wire is fed concurrently with an inert oxidisation-shielding gas (such as argon or helium) through a nozzle, which is coaxial with a thermal source, that melts the feedstock material onto a substrate (
Figure 1c). The nozzle is mounted on an articulated robotic arm or gantry system that controls the deposition location of the feedstock material and the layer thickness (typically 200–5000 μm)
[64][65][66]. The DED process is generally operated in an inert environment where the oxygen level is controlled to be within less than 5–10 ppm
[67][68]. However, some oxidation of the deposited material can occur once the shielding gas is removed from the weld if the part temperature remains high. Unlike PBF processes, the DED process allows for the AM of larger parts or for the repair or refurbishment of existing parts with localised material addition to damaged areas
[69][70]. Powder-fed DED processes can concurrently feed different types of powder materials via multiple hoppers, enabling the manufacture of composite materials including functionally graded material (FGM). Variants of DED technology include Laser Metal Deposition (LMD), which uses a laser heat source and can operate with wire and powder feedstock, Electron Beam Additive Manufacturing (EBAM), which uses an E-beam heat source and operates with wire in a vacuum build chamber, and Wire Arc Additive manufacturing (WAAM), which uses an electric arc heat source and operates with wire feedstock.
3. Machinability of Additively Manufactured Ti-6Al-4V
Additively manufactured metal parts typically have a complex, spatially varying thermal history due to the rapid melting and solidification inherent to metal AM processes. This leads to significant differences in residual stresses, surface roughness (
Figure 2) and microstructural characteristics (such as grain size and morphology), which results in different mechanical properties compared to conventionally manufactured parts
[35][71][72]. Surface roughness is a decisive factor that impacts the mechanical properties of the final products. A high surface roughness can induce stress concentration on the surface and adversely affect the fatigue properties
[73]. In general, the surface roughness of additively manufactured Ti alloys is in the range of 10 to 70 μm (Ra), which is significantly larger than that achieved by machining
[39][74][75][76]. These differences can also influence the machinability of additively manufactured parts by affecting the cutting force, surface integrity, and tool wear. In order to improve the machinability of Ti-6Al-4V, a comprehensive understating of these influential factors is critically important.
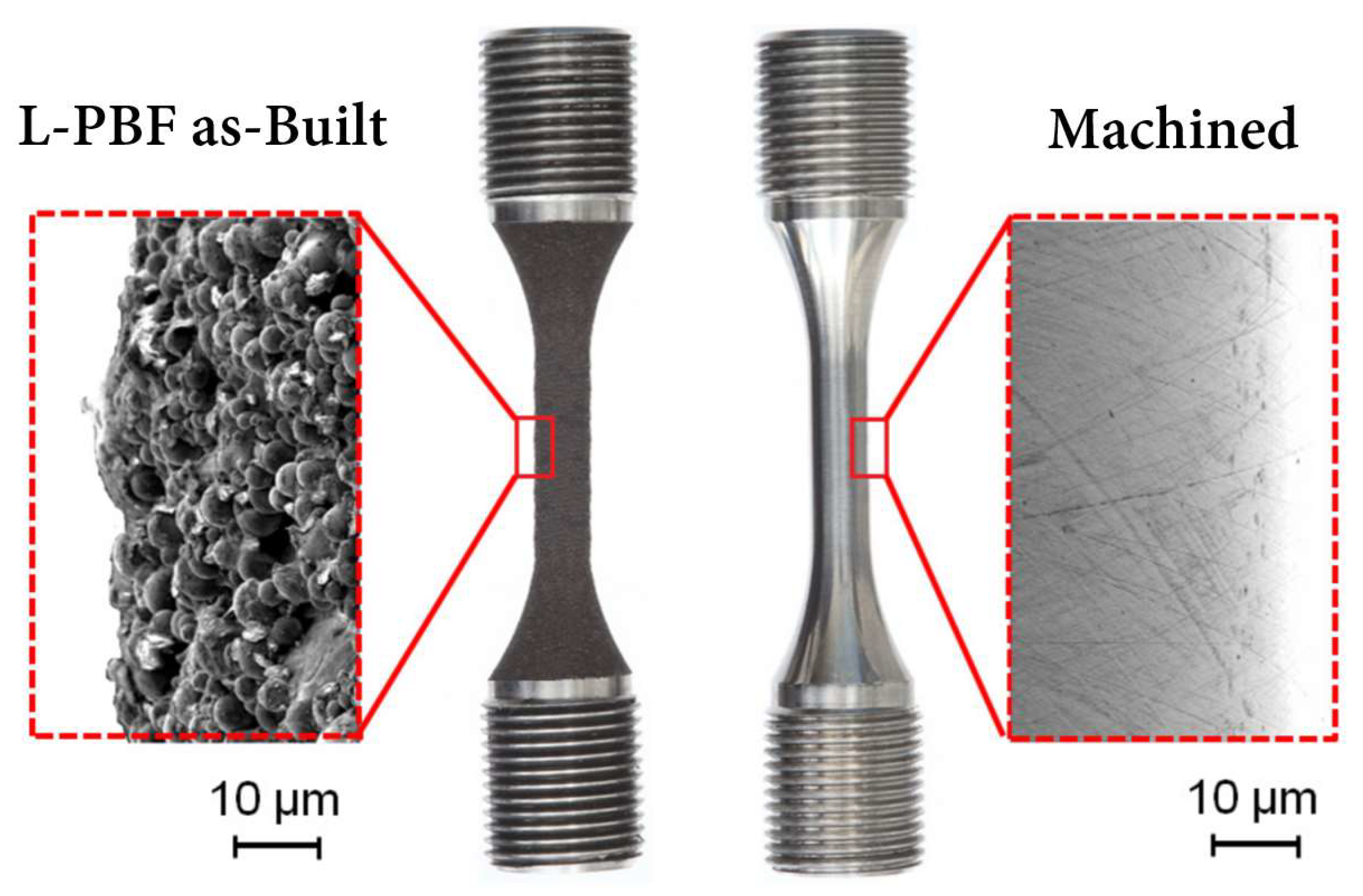
Figure 2. Example PBF-LB surface finish before and after machining process for a Ti-6Al-4V part.
3.1. Cutting Forces in Machining Additively Manufactured Ti-6Al-4V
In order to achieve high machining precision, a cutting tool has to follow specially designed tool paths to minimize dynamic changes in cutting load on the tool
[77][78]. A sudden change of cutting force can cause poor surface integrity of the workpiece, severe tool wear, and premature tool failure. The cutting force generated by the cutting edge is a significant factor in characterising the machinability of titanium alloys
[79]. During the cutting process, the force is exerted on the contact interface between the cutting tool and the chip
[80]. Since additively manufactured Ti alloys have a unique acicular microstructure, their strength and hardness can be higher than those of wrought Ti alloys. The higher yield strength can result in a higher cutting force and a high cutting temperature in the cutting zone, which, in turn, will accelerate tool wear rate. The higher hardness can lead to less plastic flow and induce a lower surface roughness
[81]. The interaction between the cutting tool and workpiece material, as well as the plastic deformation process during the formation of chips, is affected by the enhanced mechanical properties, the changes of which are finally reflected on the cutting force and surface quality.
Various experimental studies have been conducted to explore cutting force in machining additively manufactured Ti alloys. Polishetty et al.
[82] investigated the effect of machining parameters on cutting force and surface roughness of SLM Ti-6Al-4V during the turning process. It was found that higher cutting forces were generated when machining the SLM Ti-6Al-4V alloy due to higher hardness and yield strength. The surface roughness of SLM Ti-6Al-4V was lower because of the high hardness and brittle properties of the material. Shunmugavel et al.
[83] found that higher cutting forces when turning SLM Ti-6Al-4V led to higher cutting temperature and tool/chip wear, resulting in significant adhesive/abrasive wear. By comparing the machinability of SLM and wrought Ti-6Al-4V, they found that the cutting force was closely related to the mechanical strength and hardness of the material
[18], and the change in these factors was the reason that large cutting forces were recorded when machining SLM Ti
[82]. At a cutting speed of 60 m/min, the cutting force was not affected by the tool wear; at 120 m/min, the cutting force increased a little bit when machining both types of parts. However, it rapidly increased when machining SLM Ti alloy at 180 m/min due to the large concentration of wear on the flank face of the insert.
Ming et al.
[84] compared the mechanical properties of SLM titanium alloy using different machining processes under dry and minimum quantity lubrication (MQL) conditions. It was found that chip curling was more obvious when milling forged Ti-6Al-4V due to its better plasticity, which indicated that the forged Ti-6Al-4V resulted in a larger main cutting force compared to SLM Ti-6Al-4V. The main cutting force when machining SLM components decreased when the cutting speed was at 80 mm/min due to the thermal-softening effect. However, when machining the forged Ti-6Al-4V, the main cutting force increased slowly. For additively manufactured products, the grain size/morphology is also an indicator of their performance. Coarse columnar grains may be generated in the AM process due to the ultra-high temperature gradient, which results in the anisotropic and poor mechanical properties of additively manufactured products
[85][86]. An optimisation of the manufacturing process and alloy composition control has to be conducted to obtain finer equiaxed grains to achieve stronger mechanical properties in the additively manufactured components
[87]. Kallel et al.
[88] studied the machinability of Ti-6Al-4V produced by Laser Metal Deposition (LMD). Compared to the wrought Ti-6Al-4V parts, the cutting force when machining LMD-manufactured Ti-6Al-4V was 10–40% higher due to their finer grains, which provided higher yield stress and resistance to plastic deformation. The difference in ductility and microstructure (equiaxed grains and lamellar ones) of the wrought parts and the AM parts
[35] led to the surface roughness of the LMD parts being 18–65% rougher than that of the conventional samples. The compressive residual stress of the LMD parts was 11–30% higher than that of the wrought samples.
3.2. Surface Integrity
Surface integrity of machined parts is influenced by factors such as machining parameters, cooling conditions, microstructure of the materials, tool wear, and so on. Compared with wrought parts, the surface quality of as-built additively manufactured parts is poor. Lizzul et al.
[89] investigated the influence of microstructure on the surface integrity of additively manufactured Ti-6Al-4V fabricated by PBF-LB. According to the analysis of AM-induced microstructure, the material structure, including the α phase layer and the β grains, have a significant effect on the surface roughness of the samples. The AM parameters can impact microstructural anisotropy, which further affects the surface integrity of the as-built parts. The scanning strategy affects the size of prior β grain correlated to the microhardness of the workpiece
[90]. Prior β grain boundaries can impact the crack propagation in AM Ti alloy, which has a significant influence on the tensile and fatigue properties of AM Ti parts
[91]. The different sizes of β grains of the material are induced by the different thermal histories that have occurred on the fused powder layers. The wider β grains are generated by a lower cooling rate, which leads to thicker α lamellae and lower microhardness. The fracture phenomena occur in correspondence to the α-phase layers that are formed along the β grain boundaries upon heat treatment
[38][91]. The α-phase layers formed along the β grain boundaries represent the AM-produced titanium material discontinuity that weakens the material integrity, which benefits material removal during the cutting process (
Figure 3). The samples with a minor β grain width exhibit the highest density of discontinuity in the α-phase layers and show a lower cutting force, resulting in a lower surface roughness. The application of the cryogenic cooling strategy can reduce the surface roughness of the final additively manufactured components.
Figure 3. Microstructure along the build-up direction of the PBF-LB Ti-6Al-4V. The red arrows show the α-phase layers along the prior β grains boundaries.
By studying the machinability of wrought, EBM, and DMLS Ti-6Al-4V, Rotella et al.
[35] found that the surface roughness of the wrought parts was 10–20% lower than that of the additively manufactured parts. A layer of plastically deformed grains was formed below the machined surface and the thickness of the affected layer, which increased with an increase in cutting speed. The thickness of the affected layer was largest when the cutting speed was 110 m/min. Compared to the wrought workpieces, the EBM parts showed better corrosion resistance and higher surface roughness, and they exhibited higher sensitivity to hardening and compressive residual stress, which was induced by machining, because of their higher hardness. It had been found that cryogenically machined Ti-6Al-4V parts fabricated by EBM had deeper affected layers
[92]. The effect of cryogenic cooling was apparent as the thickness of the deformed layer increased on the workpiece surface. However, the plasticity of the material decreased under the cryogenically cooled condition due to the lower cutting temperature, which led to grooved and irregular feed marks on the machined surface. The amount of surface defects increased with an increase in feed rate regardless of the process route. Bordin et al.
[93] investigated the surface integrity of Ti-6Al-4V alloy produced by EBM with different cooling strategies, including dry, wet, and cryogenic cooling. It was observed that the cooling condition did not affect the surface quality regardless of the cutting speed when the feed rate was set at the lowest. The use of liquid nitrogen (LN2) reduced the crater and flank wear as well as the surface roughness of the workpiece. Flaws in the machined surfaces, such as side flow, adhesion, tearing, and jagged feed marks, were found; these flaws were affected by the ploughing action between the cutting tool and the workpiece surface. The side flow of the material was caused by the plastic deformation of the surface materials induced by the tool motion. The long straight grooves were caused by the small fragments of the build-up edge (BUE), owing to the rubbing action between the cutting tool and the workpiece. When these fragments were machined through below the flank face of the cutting tool, the grooves were generated on the underlying material; these small fragments left long straight grooves on the material surface when they passed the bottom of the tool flank face. Additionally, adhered materials were left and welded on the surface during the turning process when the adhered particles were formed (
Figure 4). Similar surface defects, including side flow and adhered material, can also be found when turning wrought Ti alloy
[94]. Cleaner and unbroken surface morphology, as well as randomly oriented micro-scratches induced by chip entanglements, can be observed when the feed rate is 0.1 mm/rev during the wet cutting process (
Figure 5).
Figure 4. Main surface defects after 8 min of turning when adopting the wet, dry, and cryogenic cooling strategies: (a,d) material side flow, double feed marks, long grooves, and micro-particles adhered on the machined surface; (b,e) wider adhered chip fragments and BUE are attached to the machined surfaces; (c,f) the wavy surface topography along the cutting speed direction and the jagged feed mark peak.
Figure 5. Scratches and adhered particles provoked by chip entanglements after 8 min of wet cutting.
Sartori et al.
[95] studied the machining of DMLS-produced Ti-6Al-4V by using cryogenic cooling during the turning process to improve surface integrity (
Figure 6). Compared to dry cutting, a more irregular and jagged surface was produced because of the application of LN2 (
Figure 7). The tearing phenomenon was presented on the DMLS part irrespective of the use of cooling strategy. The application of LN2 resulted in the most significant residual stress in the axial direction and induced a thickening of the layer with compressive residual stress.
Figure 6. The surface defect generated during dry cutting: (a) adhered material and (b) smeared material.
Figure 7. The feed marks and irregularities formed during turning when adopting different cryogenic cooling strategies: (a) 500× and (b) 2000×.
During the machining process, an ubiquitous compressive stress along the surface of additively manufactured parts could be observed
[96]. The cutting region in front of the cutting tool experienced compressive plastic deformation. The compressive stress was generated when the machined surface was squeezed and plastically deformed during the machining process
[97]. Oyelola et al.
[96] adopted X-ray diffraction to determine the compressive stress in the two measurement directions (axial and circumferential directions) of an additively manufactured Ti workpiece. According to the comparison of the compressive stress in these two directions, it was found that the sample machined with a coated insert incurred higher compressive stresses than the sample machined with an uncoated insert in the parallel direction of the circumference. This difference was induced by the thermal effects associated with chip formation as well as the interactions between the edge of the cutting tool and the machined surface. Furthermore, heat treatment is able to homogenise the microstructure of additively manufactured parts. Coarse microstructures and larger grain size induced by heat treatment lead to a reduction in yield stress, ultimate tensile strength, and hardness of the workpiece, which in turn results in a lower machining force and decreased subsurface deformation, eventually improving the surface roughness
[98].