2. Modification of ENMs with Functional Molecules and Their Effect on the MD Process
2.1. Effect of MOFs and Zeolites on ENMs and the MD Process
2.1.1. Aluminum Fumarate (AlFu) Addition
MOF-based ENMs are being widely explored in water treatment applications. MOFs possess unique characteristics such as high porosity and high specific surface area, and they can be functionalized with a variety of nanomaterials so that we can tune the MOF-based membranes as per the need of the MD process application. Leaching of nanomaterials from the polymer matrix is one of the problems faced during the water filtration process. This may lead to contamination of the product water with the nano-sized MOFs. The electrospinning of MOF-based polymer dope solutions followed by pyrolysis under controlled conditions has the potential to resolve the leaching issues
[18], physically trapping them into the nanofibers, which ultimately resolves the issues of chemical compatibility as well the mechanical stability of the resultant membranes
[18][19].
The current research trend on MD membrane fabrication reveals that the optimum incorporation of nano-additives significantly improves the performance of the MD process by improving the aforementioned MD membrane characteristics
[20]. AlFu is a commercially available and widely used MOF for MD membrane fabrication. AlFu-based MOF is inexpensive, and it comes with multiple MD-friendly characteristics, including being hydrophobic, water stable, environmentally friendly, able to be sourced from water and simple aluminum salts, having a permanent three-dimensional highly porous structure and with a large-scale production capacity about 3600 kg/m
3 per day. Therefore, an AlFu MOF is considered a promising agent for wastewater treatment and possibly other MD applications when utilized with ENMs
[21]. AlFu can be incorporated into PVDF-HFP via electrospinning. The observed permeate flux was improved up to 114% during 46 h of continuous MD operation in comparison with neat PVDF-HFP ENMs. The thermal efficiency during the DCMD process was improved with the addition of AlFu MOFs in PVDF-HFP ENMs. The presence of AlFu MOF nanomaterials also enhanced the surface roughness, WCA, LEP, and thereby anti-wetting characteristics of the MD membrane
[22].
Figure 3a shows a schematic diagram of the DCMD process while using AlFu-MOF-incorporated ENMs, revealing systematically ordered pores in MOFs with sizes between 0.6 and 0.7 nm
[19], which offer an additional path for vapor transport and result in enhanced permeate flux
[21]. Moreover, the presence of AlFu MOFs on the surface of ENMs in the form of protrusions enhances the surface roughness, which effectively increases the area for evaporation
[23]. MAF-4 is a hydrophobic nanomaterial and interlayer that can be fabricated by seeding Zn (II) using the in-situ crystallization method. Because of the hydrophobic and anti-fouling characteristics of MAF-4, it has great potential to be utilized for MD.
Figure 3b shows the step-by-step growth of MAF on a poly ether sulfone substrate via self-polymerization of Zn-seeded dopamine
[24][25].
Only a few reports have been published on the application of MOF/MAF nanomaterials in MD membranes. In a recent report, 8% MAF-4 with PVDF could enhance water flux by 60% compared with neat PVDF membrane
[26].
2.1.2. Zeolitic Imidazolate Frameworks (ZIFs) Addition
The surface roughness and hydrophobicity of ENMs can be also enhanced by the addition of zeolites. A schematic representation of ZIF structures is given in
Figure 3c. The zeolites belong to the MOF family that connects their imidazolate group with divalent metal cations
[27]. ZIFs have high thermal resistance, chemical stability, and high porosity. The aforementioned characteristics of ZIFs can be utilized for applications including the fabrication of efficient MD membranes for water reclamation
[28][29]. ZIFs contain organophilic imidazolate linkers, and these offer hydrophobic characteristics
[30]. Additionally, Zeolitic imidazolate framework-71 (ZIF-71) offers enhanced hydrophobic properties due to the presence of methyl (–CH
3) and chlorine (–Cl) entities in their chemical composition
[27].
ZIF-71 NPs incorporated into PVDF-HFP significantly increased the surface roughness and hydrophobicity, yielding a permeate flux of 19.2 L m
−2 h
−1 with a salt rejection of >99.99%, which is 284% and 949% higher compared with the MD flux observed while using various pristine microporous membranes
[29]. The PVDF-HFP ENM only had a WCA of 127.6°, while 0.75% ZIF-71 NP-incorporated PVDF-HFP ENMs showed increased hydrophobic properties with a WCA of 135°, and enhanced chemical and mechanical stability. The DCMD efficiency while using this nanostructured MD membrane was reported as 99.5%
[19].
Figure 3. (
a) Mechanism and effect of AlFu MOF on the DCMD performance
[19] (Reprinted with the permission License No: 5487001092782 15 Febuary 2023, Elseviers). (
b) MAF growth on PES polymer substrate and its conversion to other zeolitic species (MAF-7)
[24] (Reprinted with the permission License No: 5490181160662 15 Febuary 2023, Elseviers). (
c) Crystal structure of ZIF-71: Zn (polyhedral), Cl (green sphere), N (purple sphere), C (white sphere)
[27] (Reprinted with the permission License No: 1324377-1 15 Febuary 2023, RSC Publishing).
2.2. Effect of SiO2, TiO2, and Zinc Oxide (ZnO) on ENMs and the MD Process
Nanomaterial additives such as SiO
2, TiO
2, and ZnO can be directly blended with the electrospinning dope solution, and this is a popular approach to obtain modified ENMs for the MD process
[31][32]. ENMs incorporated with the aforementioned nanomaterials possess enhanced MD membrane characteristics such as WCA, LEP, mechanical strength, narrow pore size distribution, and controlled porosity
[32][33][34][35].
It is showd that the MD membrane characteristics and calculated MD flux while using ENMs incorporated with SiO
2, TiO
2, and ZnO nanomaterials. In general, these NPs have been utilized for various applications such as biomedical, environmental, textile, and water treatment
[36], and their details are discussed in the following section.
2.2.1. SiO2 Addition
SiO
2 NPs have been utilized for various applications because of their size range between 5 to 1000 nm, high adsorption capacity, high specific surface area, unique optical properties, low density, low toxicity level, and biocompatibility. As per the report, the LEP of ENMs with 1% SiO2 was 43% higher than the neat PVDF. It may be because the presence of additional nanomaterials on the membrane surface could reduce the pore size, enhancing the surface roughness and thereby the hydrophobicity and WCA
[37].
Compared with neat hydrophobic PVDF ENMs with a WCA of 92.8°, PVDF ENMs with modified SiO
2 NPs showed increased hydrophobicity with a WCA of 109°. Similar WCA has been reported for PVDF membranes with a 3–4% addition of SiO
2 NPs
[38]. The advantage of superhydrophobicity and the “lotus effect” is not limited to its anti-wetting characteristics, but also applies to the membrane’s anti-fouling properties and self-cleaning characteristics
[39].
At a temperature of 60 °C, the MD water flux while using SiO
2-incorporated PVDF ENM (19.4 L m
−2 h
−1) was 43% higher than that of neat PVDF ENM (13.6 L m
−2 h
−1). Water flux enhancements are also attributed to reduced pore blockage due to the reduced salt deposition or scaling propensity while employing SiO
2 NP-modified ENMs during the MD process testing
[40][41]. In one report, modified SiO
2 NPs were incorporated into a PVDF polymeric matrix to obtain nanocomposite-based PVDF ENMs with a WCA as high as 147.8–161.2°, which was up to a 10.7% increase compared with the pristine PVDF
[32]. Silanes are monomeric silicon compounds such as N-octadecyltrichlorosilane (ODTS), octadecyltrimethoxysilane (OTMS), chloromethyl-octadecyl silane (Cl-DMOS), etc., which are useful for improving the hydrophobic properties of ENMs by lowering their surface energy. The OTMS is an aliphatic long chain of carbon (CH
3(CH
2)
17−) with (-Si-OCH
3)
3 as an anchor group
[42], whereas Cl-DMOS and ODTS possess (-Si-Cl
3)
3 and (-Si-ClCH
2)
3, respectively, as the anchor groups
[43][44]. These silanes have plenty of non-polar CH
3 groups which impart hydrophobic characteristics. Apart from these non-polar groups, the strong electron-withdrawing atoms, viz., oxygen and chlorine in ODTS and Cl-DMOS, result in uneven electron distribution with minimum polarity at the respective sites, which ultimately increases the hydrophobic characteristics
[45][46].
The superhydrophobic features may result in the “lotus effect” and thereby yield self-cleaning characteristics to the modified ENMs
[39]. To achieve this effect, they must have a WCA close to 180° and a relatively lower sliding angle which may allow for the roll-off of water droplets. These properties would enhance the anti-fouling and anti-scaling characteristics of the membrane
[36]. Several other studies have reported increased hydrophobic properties of MD membranes by the addition of SiO
2 NPs and TiO
2 NPs. These nanoparticles cause surface roughness, reduce the pore size, and impart respective functional groups to the surface to inhibit foulants or scalants during the MD process. The surface roughness results in increased WCA, which improves the hydrophobic characteristics of the ENM. This hydrophobic behavior creates air pockets that resist pore wetting and let the water droplets easily roll off over the membrane surface
[4][36].
2.2.2. TiO2 Addition
TiO
2 is one of the key ingredients that has been utilized to fabricate composite membranes for different applications. TiO
2 NPs show different behavior with regard to their potential affinity towards H
2O or any waste effluents present in the water. TiO
2 NPs are multifunctional due to their versatile characteristics such as large specific surface area and easily tunable chemical properties
[47]. The hierarchical structure morphology can be generated by the deposition of TiO
2 NPs using different tuning agents with desired surface properties. Additionally, TiO
2 might offer reactive sites for covalent bonding between hydrolyzed silane coupling agents and hydroxyl groups (OH) available on the TiO
2 surface, as shown in
Figure 4a,b.
The ENMs incorporated with TiO2 NP (38.71 L m−2 h−1) showed 5% and 45% enhanced initial flux compared with neat PVDF-HFP (36.78 L m−2 h−1) and commercial membranes (26.64 L m−2 h−1), respectively. The reason behind this is the optimum pore sizes and higher porosities of neat PVDF-HFP and ENMs incorporated with TiO2, compared to the commercial membranes.
The PVDF-HFP ENMs showed a 5% more porous structure (82.6% porosity) compared with ENMs embedded with the organically modified SiO
2 NPs (78.5% porosity). This slight decline in porosity was associated with the sprayed NPs on the surface of ENMs that somehow blocked the membrane pores. The PVDF-HFP exhibited a WCA of 142°, which is higher than the commercial membrane with a WCA of 118°. This is because of the rougher surface of the randomly deposited non-woven PVDF-HFP ENM. In one report, the authors compared the WCA of PVDF-HFP with dual layer membranes, which showed a 13°-enhanced WCA compared with one with modified TiO
2, which had a WCA of 155° and low sliding angles of less than 20°. Moreover, the prepared superhydrophobic dual-layer membranes showed comparable LEP values compared to the commercial membranes
[48].
Superhydrophobization can be performed by coating fluorosilane molecules onto TiO
2 NPs by a low-temperature hydrothermal process. One of the fluorosilanization agents is 1H, 1H, 2H, 2H-perfluorododecyl trichlorosilane (FTCS), which offers sites of hydroxyl groups in TiO
2 NPs for fluorosilanization and thereby achieves a hierarchical morphology. Hydrophobically modified TiO
2 NPs can either blend with a polymeric dope solution to fabricate ENMs or disperse in a suitable medium and be coated onto ENMs by electrospraying
[47]. The mechanism proposed in
Figure 4a reveals the fluorosilanization of TiO
2 on the surface of PVDF
[47]. FTCS anchors hydrophilic trichlorosilane with chains of hydrophobic fluorinated carbon, which reveals the formation of trisilanols/hydrosilanes with hydrolyzation of the hydrophilic trichlorosilane head in water
[49]. Further,
Figure 4b shows the Si–O–Ti covalent bond formed because of the hydroxyl groups present in trisilanol molecules. These interactions between TiO
2 and PVDF might offer robust, dense, hydrophobic surfaces which can be beneficial for the MD process
[47].
Figure 4. Scheme for the salinization of PVDF by (
a) hydrolyzation using FTCS, or (
b) condensation of trisilanols
[47] (Reprinted with the permission License No: 5497580436300 14 Febuary 2023, Elseviers).
2.2.3. ZnO Addition
ZnO NPs possess good thermal resistance, high surface-to-volume ratio, and anti-bacterial characteristics. In addition, these nanomaterials are considered environmentally friendlier and more economical than TiO
2 and Al
2O
3 when utilized for surface modification of membranes. ZnO may offer anti-wetting, anti-fouling, and anti-scaling characteristics with reduced water sliding angles when treated with organo-silane molecules such as 1H, 1H, 2H, 2H-perfluorooctyltriethoxysilane (FAS). These features of ZnO with FAS offer a stable superhydrophobic surface, which directly indicates its potential to be utilized for MD
[50].
PVDF-HFP with 25% ZnO NPs can be used to fabricate nanostructured ENMs. A stable DCMD flux rate was observed while using a low surface tension feed, with a salt rejection of 99.99% for up to 80 h of continuous operation. A slight compromise in water flux (up to 7% reduction) was observed when compared with neat PVDF-HFP ENMs. The WCA of ZnO NPs with PVDF-HFP ENMs was observed to be as high as 161
°°, and the average pore size was 0.6 μm, which ultimately impacted the LEP of membranes and reached 187 kPa. This report confirms the potential of ZnO utilization for MD applications
[50].
2.3. Effect of CNT, GO, and AC on the MD Membranes and the MD Process
Carbon-based hydrophobic nanomaterials, viz., CNTs, graphene, and activated carbon (AC), are being widely utilized as additives in ENMs to fabricate MD membranes with desired characteristics
[51][52][53].
2.3.1. CNT Addition
Recently, researchers have optimized the concentration of CNTs in a PVDF-HFP polymeric matrix to obtain highly hydrophobic and robust MD membranes. A 0.5 wt% CNT–PVDF-HFP heat-pressed at 150 °C (CNT-150) yields a robust MD membrane with high DCMD permeate flux (16.5–18.5 L m
−2 h
−1), which is 42–50 % higher flux compared with commercially available membranes (11–13 L m
−2 h
−1) at similar operating conditions. ENMs generally show higher MD vapor flux than commercial membranes, which is primarily attributed to their unique porous structure and surface roughness. The porosity of untreated PVDF-HFP ENMs was 89%, while the membrane after heat-press (150 °C) treatment resulted in a decreased porosity (80%) because of the reduction in certain voids and pore size after heat treatment. Conversely, the stress at break and Young’s modulus of the treated ENM was increased due to the compaction of fibers after heat-press treatment. The WCA of PVDF-HFP ENMs was reduced from 135.9° to 123° because of the reduction in surface roughness as a result of the heat-press treatment and the melting of partial nanofibers. Thus, a controlled heat treatment yields robust ENMs with a slight reduction in the porosity and WCA. Additionally, 99.99% of inorganic non-volatile salt rejection can be achieved by using CNT-incorporated electrospun MD membranes during a DCMD process
[51].
2.3.2. GO Addition
Reduced graphene oxide (rGO) is hydrophobic, and it is considered a promising candidate for ENM-based nanocomposite MD membranes
[54][55]. Fine and porous membranes based on GO exhibit a unique permeation pathway for water molecules. The rGO-ENMs have very good mechanical properties, chemical stability, flexibility, anti-fouling properties, and hydrophilicity
[56]. The physicochemical comparison of GO and rGO is shown in
Figure 5b. GO contains -O-, –OH, C=O, and –COOH groups, whereas rGO is a reduced form of GO with reduced hydrophilic characteristics, which is required for the MD process.
The hydrophilicity of GO originates from the hydroxyl and epoxy groups in the basal plane, along with other functional groups such as carbonyl and carboxylic groups
[57]. Octadecyl groups are substituted by GO groups upon functionalization
[48], which results in an active surface area, higher hydrophobicity, higher surface contact angle, and lower surface energy. In a recent report, a commonly used three-stage method was used to fabricate superhydrophobic mixed-matrix PVDF-HFP ENMs that were modified using octadecylamine-reduced graphene oxide (ODA-rGO) and utilized for the MD process. The resultant PVDF-HFP ENMs with ODA-rGO showed a superhydrophobic nature with a WCA of 162°. The contact angles of the superhydrophobic nanofiber membranes containing 0.1 wt% and 0.5 wt% ODA-rGO were measured as 158° ± 1° and 156° ± 3°, respectively, which were about 14.5% and 13% higher than the contact angle of the pristine PVDF-HFP. Beads-on-string morphology was observed due to the agglomeration of ODA-rGO (0.5 wt%) during the elongation of the nanofibers. In addition, the fiber diameter could be tuned by changing the concentration of ODA-rGO in the dope solution
[58].
Additionally, LiCl (0.005 wt%) was used to control the pore size of ENMs followed by a hot-pressing process. The average pore size of ENMs was reduced from 1.30 µm to 0.24 µm, and the LEP was improved from 30.4 kPa to 127.6 kPa in comparison with the pristine ENMs upon heat pressing. The tensile strength of hot-pressed rGO-ENMs was increased by about 26% compared with the neat ENMs
[59].
2.3.3. AC Addition
Nanostructured AC is widely utilized for water treatment applications because of the various available functional groups on its surface, which are beneficial for modifying the surface and its physical and chemical characteristics
[60]. In a recent report, the effect of AC NP-based ENM’s hydrophobicity was studied, which revealed that the AC NPs form a hierarchical structure with micro-wrinkles or protrusions and results in increased surface roughness, ultimately increasing the surface hydrophobic properties. This is because of the result of weave-like surface roughness generated on the ENMs. This results in increased WCA for all samples incorporated with AC.
Figure 5c shows a schematic illustration of an AC-anchored nanofiber structure
[23]. Recently, dual-layer compositions with hydrophobic and hydrophilic layered membranes were prepared and utilized for the DCMD process.
The selective hydrophobic PVDF-HFP ENMs were prepared with varying AC NP concentrations from 0 to 3.0 wt% along with other hydrophilic support layers
[23]. Overall MD performance was improved with the composition of 1.5 wt% NPs, yielding a water vapor flux of 45.6 L/m
2 h which is 9% higher compared with the MD flux while using commercially available PTFE membranes (41.8 L/m
2 h) with no compromise in the salt rejection (99.99%) during the MD process. These resultant membranes have relatively wider pores, which contributed to an increase in the porosity by ~20% compared with the commercial PTFE membrane. The higher porosity of these fabricated ENMs is beneficial for reducing mass transfer resistance and leads to better permeation flux during the MD process. The ENMs exhibit relatively lower LEP values (1.21–1.36 bar) than the commercial PTFE membrane due to their larger pore size. However, the LEP values of these ENMs are quite comparable with other results obtained for MD membranes reported in the literature
[61][62][63][64][65], which is considered to be adequate for DCMD applications.
L-type and H-type are two kinds of ACs. H-type ACs are positively charged when treated under water or strong acids and thus possess a hydrophobic character. On the other hand, L-type ACs are neutralized by strong bases and possess hydrophilic properties
[66]. Typical oxygen-containing surface functional groups in AC are depicted in
Figure 5d, and these oxygen-containing surface functionalities are the routes for achieving desired surface properties during membrane fabrication
[67].
Figure 5. (
a) CNT-incorporated nanofibers and structure
[53] (Reprinted with the permission License No: 5475271453015 24 January 2023, Elseviers). (
b) Conversion of GO to rGO
[68]. (
c) Protrusion effect on WCA on ENMs produced by AC (
d) Chemical structure of ACs.
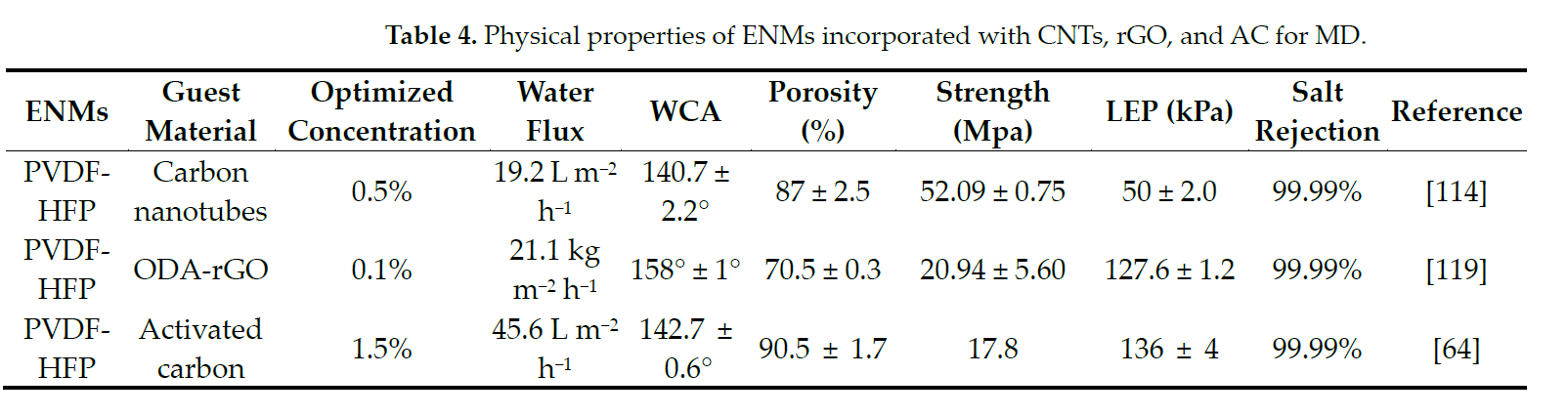
5. Wetting, Fouling, and Scaling Behavior of Modified Electrospun MD Membranes
Pore wetting, membrane fouling, and scaling are technical challenges in MD process that reduce the efficiency of the process and the shelf life of the membrane. Horseman and co-workers have described state-of-the-art insights on the fundamental mechanisms and mitigation strategies for wetting, scaling, and fouling in the MD process. Practical MD processes often involve complex feed solutions and the simultaneous occurrence of wetting, scaling, or fouling phenomena. As per this report, most of the studies separately focus either on a single mechanism (wetting/fouling/scaling) or multiple mechanisms. They emphasize the importance of mitigation strategies in the MD process by understanding the fundamental and complex mechanisms of fouling and scaling. As per their recommendation, the MD process study should be aim at pretreatment, operation, and membrane development to address the multiple failure mechanisms when using real feed solutions with more complex foulants and scalants [127].
There are many reports on the fabrication of fouling- or scaling-resistant hollow-fiber and flat-sheet MD membranes. Many efforts from the researchers are reported to mitigate the temperature polarization (TP) or concentration polarization (CP) phenomenon and thereby mitigate the wetting and scaling issues in the MD process. Some of the polarization mitigation techniques are: employing spacers, bubbling or micro-bubbling, patterned
membranes, flashing the feed, localized heating, etc. [128–134].
Kim et al. reported a flux enhancement as high as 43% by introducing feed and permeate spacers with a hydrodynamic angle of 90° during a DCMD process test. A study on the introduction of innovative swirling-flow microbubbles into a DCMD module resulted in a 37% flux enhancement. An 87% performance enhancement was reported during a DCMD process while using a corrugated membrane. Flashing the feed solution in a VND process yielded a 3.5-fold increase in the water permeate flux by mitigating the TP phenomenon. A report on the introduction of localized heating in an MD module demonstrated
a reduction in heat loss and the TP effect [135]. Most of these mitigation strategies were not employed using electrospun MD membranes, and there is a research gap in this area of understanding the heat and mass transport mechanisms and MD process performance. Recently, researchers have become more interested in the fabrication of modified electrospun MD membranes with anti-scaling and anti-fouling characteristics by incorporating nanomaterials or by chemical modifications [10,77,136–141]. Table 5 shows a variety of electrospun MD membranes having anti-fouling/anti-scaling properties.
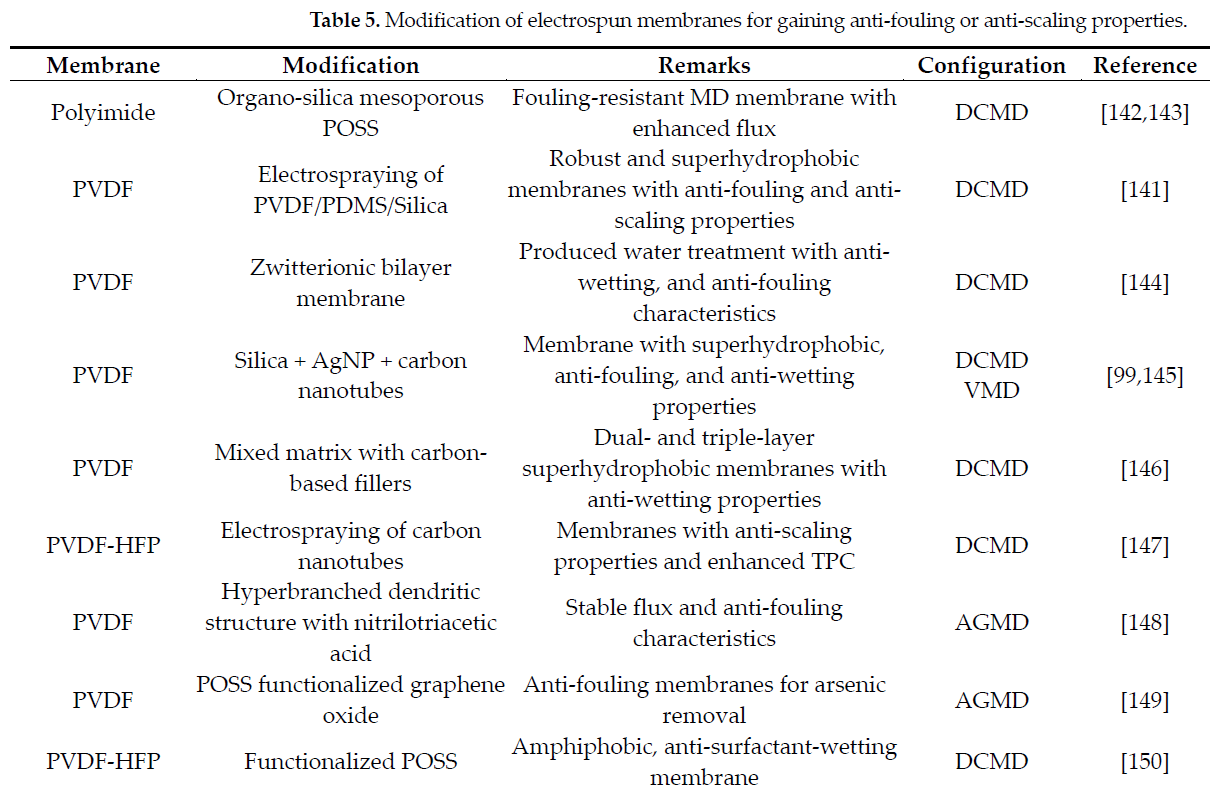
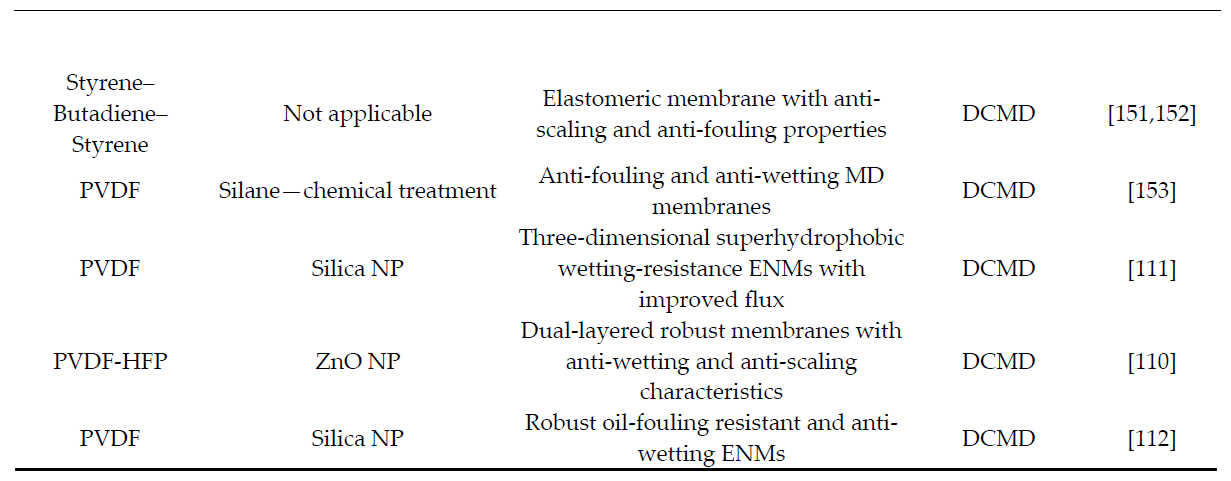
From the above table, most of the reported works use PVDF electrospun membranes modified with nanoparticles such as silica, silver, POSS, graphene oxide, and carbon nanotubes. The presence of nanoparticles in the electrospun membranes enhances membrane characteristics such as mechanical strength, LEP, and water contact angle along with the anti-wetting, anti-fouling and/or anti-scaling properties of the membrane. Most of the reported works demonstrate the blending of the nanomaterials along with the electrospinning dope solution before the membrane fabrication [147,154].
In the electrospun membranes obtained from these blended dope solutions, the majority of the nanomaterials are distributed in the bulk rather than on the membrane surface. So a minimum amount of used nanomaterials would be available to impart antifouling or anti-scaling properties to the membrane. Instead of blending the nanomaterials with the polymeric dope solution, if the nanomaterials can coat the membrane surface in the second step in an efficient way, most of them can be available in the antibacterial or anti-scaling action during the water-treatment process. Dispersion of a homogeneous
nanomaterial solution on the membrane surface by electrospraying is recommended as a robust method for fabricating nanocomposite membranes [147].
Nanostructured composite membranes with other possible hydrophobic electrospun non-woven substrates [155,156] and other nanomaterials having anti-bacterial or antifouling properties have to be explored for MD applications. Detailed failure mechanisms due to multiple fouling or scaling phenomena have to be explored with the help of experimental investigation and computational fluid dynamics. Membrane-integrated 3D spacers could be another area to be explored to mitigate membrane fouling and scaling propensity [157,158].
6. Conclusions and Future Outlook
This review article emphasizes the importance of tuning MD membrane characteristics by incorporating the optimum quantity of nanostructured materials into
ENMs. Variable tuning parameters that have to be kept in mind during an electrospinning process to fabricate defectless ENMs are summarized. Enhancements in the MD membrane characteristics upon the addition of nanomaterials such as MOFs, zeolites, SiO2, TiO2, ZnO, CNT, GO, and AC are discussed. MD process performance based on water vapor flux and developments in the fabrication of anti-wetting, anti-fouling, and anti-scaling ENMs by incorporating various nanofillers are also discussed in this article. ENMs are comparatively economical when a small number of NPs are incorporated into a polymer solution for electrospinning; however, the optimization of several parameters, optimum selection of NPs, and the need for well-planned studies still need to be addressed [78].
Electrospinning is a versatile approach for membrane fabrication but there are still many improvements to be made. Electrospinning can be directly performed on different types of collectors and solutions with alcohol as a non-solvent or on sonicated solutions, which may directly react faster because of their finer diameter. These approaches may offer the direct formation of superhydrophobic ENMs with special morphologies, ultimately yielding high flux and better MD performance with self-cleaning membrane characteristics [97]. Recycled RO membranes, RO feed spacers and RO permeate spacers from discarded RO membrane modules have been used as ENM supports for the MD process and compared to the performance by Jorge et al. [159]. ENMs fabricated from recycled plastics have not yet been employed for MD process testing. Similarly, various polymers with low surface energy are available but have not yet been investigated for MD. A variety of NPs and surface functionalization have been reported for other applications, but there is a big research gap to be explored in their incorporation or respective chemical treatments of ENMs for MD [153]. Modified ENMs with chemical vapor deposition (CVD), physical vapor deposition (PVD) and plasma treatment for enhancing MD membrane characteristics have to be explored. Advanced MD configurations also need to be explored with novel pristine ENMs and blended composite and modified MD membranes prepared via an electrospinning process [61]. Electrohydrodynamic atomization of nanomaterials to coat membrane surfaces to tune the surface characteristics is rarely explored [160]. So far, the application of ENMs in the MD process has been limited to lab-scale investigations. Pilot-scale and large-scale electrospun MD membranes have to be fabricated and tested. Apart from that, more scientific modeling and simulation tools are very important to understand the heat and mass transport mechanisms during the MD process and to validate the experimental data. These tools will also help to up-scale the lab-scale membrane module and process to a large-scale system.
Author Contributions: M.K.—Conceptualization, original draft preparation, data curation, writing,
and editing. L.F.—Conceptualization, original draft preparation, data curation, supervision, reviewing,
and editing. N.H.—Supervision, project administration, reviewing, editing, and funding acquisition.
All authors have read and agreed to the published version of the manuscript.
Funding: This work was jointly sponsored by the New York University Abu Dhabi (NYUAD) and
Tamkeen under the NYUAD Research Institute Award (Project CG007). All the experiments were
conducted using the research facilities at the NYUAD Water Research Center.