Because of their thermal and mechanical mismatch with typical glass materials, the fabrication of optical fibers from semiconductors is a considerable challenge for the field of materials science. As a result, the platform for optical fibers has been restricted to materials that are consistent with the typical fiber drawing techniques for an extended period. In 2006, a chemical deposition approach was used to create the initial example of a crystalline semiconductor optical fiber. As a result of this endeavor, different methods have been utilized in the fabrication of semiconductor optical fibers. Each of these methods has its own set of benefits and drawbacks. Since there have been no standardized techniques for fabricating these fibers, their production is relatively costly.
1. Material Fabrication
The production of fabrication begins with material fabrication. Commonly used methods for fabricating semiconductors, such as silicon, germanium, and selenium, include Czochralski (CZ) growth, float zone (FZ) growth, laser-heated pedestal growth (LHPG), and liquid phase epitaxy (LPE).
CZ growth is the most popular approach to fabricating single-crystal silicon
[1]. A single crystalline charge is heated over its melting point to form a melt, then a silicon crystal seed is inserted into the melt, and the crystal is progressively removed from the melt and rotated in the opposite direction to the melting crucible
[2]. Key factors to control the fabrication process include the seed and crucible rotation rates and the seed's pull rate
[3]. In the early phase of CZ growth, the pull rate is large, and the fabricated crystal is small in diameter (3–4 mm), which is dubbed the “neck” of the crystal. CZ growth was first utilized by Dash for producing dislocation-free crystals, and its use has become prevalent in the industry
[3].
FZ growth is an alternate and straightforward way of producing a bulk semiconductor crystal of homogeneous composition. If it is possible to create a feed rod with a uniform composition, then a steady-state condition might be created by selecting the growth parameters in such a way that the composition in the melt spontaneously controls the growth temperature
[4]. For FZ growth, an inert gas or vacuum atmosphere is employed, and silicon’s surface tension enables a melt zone to be translated vertically down a high-purity rod
[5]. While reducing convection, magnetic forces stabilize the melt, and temperature gradients may reach tens of Kcm
−1 [6][7]. During oxide crystal formation in optical furnaces
[8], average bulk growth rates are mm per minute, and the greatest FZ temperature gradients are on the scale of 500–1500 Kcm
−1 [8]. These characteristics are similar to fiber recrystallization. Carbon and oxygen residuals in FZ silicon boules are very small (on the order of 1016 cm
−3), but in the case of fibers, the existence of oxide cladding may prevent impurities from being reduced to a small amount.
The production of oxide fibers has shown to be the most successful use of LHPG
[9]. Temperature gradients for the LHPG technique can reach 104 Kcm
−1, which is comparable to the values that have been reported for CO
2 laser treatment of fibers
[10][11][12], even though the unconstrained surface may results in undesirable diameter and surface quality variations. In the production of the quartz suspension fibers used as gravity wave detectors
[13][14], a more sophisticated version of this optical technology is utilized. This technique is now commercially accessible for the tapering of optical fibers. Tapering stations have been effectively employed in the recrystallization of silicon core fibers
[15][16], which has led to the production of crystalline cores with exceptionally high optical quality.
Since its development by Nelson in 1963, LPE has been used to build thin layers of III-V, II-VI, and IV-V1 alloys for material research and device applications
[17]. LPE structures have been utilized to make several electronics and OE. For example, GaAs/GaA1As double-heterostructure (DH) laser diode room-temperature CW lasing
[18][19]. CW operation of DH lasers radiating beyond 1 μm was initially accomplished using LPE material in InP/InGaAsP
[20], GaAsSb/GaA1AsSb
[21], and GaSb/GaA1AsSb
[22]. Studies of LPE literature are crucial in systems where the starting semiconductor charge is disproportioned, e.g., pulling InGaSb core fibers
[23]. Sb filaments were detected in the as-drawn fibers, and this excess metal functioned as a recrystallization solvent
[24]. Intentionally introducing an excess binary system material may produce a crystallization process similar to LPE in a closed vessel where oxidation issues are decreased. Crystal growth rates are often greater with fibers than with LPE, and few studies of a gradient perpendicular to the growth front for the latter method report maximum values of 25 K cm
−1 [25][26]. Despite varied circumstances, LPE expertise may be applied to the fiber core and used to explore novel materials and solvent combinations for traveling zone expansion.
2. Semiconductor Optical Fiber Fabrication Process
2.1. Thermal Drawing
Thermal drawing is one of the most commonly employed techniques to fabricate semiconductor optical fibers. The fabrication process should meet some of the following requirements. First, cladding materials should possess high viscosity to resist stretching stress. The viscosities and expansion coefficients of amorphous materials should be comparable to prevent deformation of the interface. Second, the temperature window during the fabrication process needs to be large enough to prevent amorphous materials from crystallizing. Last, chemical reactions during thermal drawing must be utilized to create novel materials during fabrication or to prevent fabrication. For example, the reaction between Al and silica can be utilized to create silicon core fibers
[27].
A preform is heated using a drawing tower furnace with a temperature that is 50–100 °C higher than the preform cladding glass transition temperature; the preform is drawn by a capstan while the materials within it are softened. Consequently, a fiber with a diameter of
Df is fabricated. The consequent fiber has the same geometry as the preform.
Df can be adjusted by the preform diameter
Dp, preform feeding speed
vf, and drawing speed
vd [28]. This relationship is demonstrated as follows:
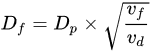
A unique technique using drawing towers for producing semiconductor core fibers is referred to as the molten core method (MCM). The selection criteria for the MCM are similar to the criteria for thermal processing, while semiconductors are confined in cladding material and melt during heating. The MCM can be used to fabricate a variety of unconventional core materials with amorphous or crystalline features. Using the MCM to fabricate semiconductor optical fibers, core materials are placed in a tube that acts as the cladding material; then, through drawing towers, the tube is pulled in a thin robe. After drawing, the core gradually solidifies as the temperature drops; thus, a fiber is fabricated using the MCM. Because of the inconsistent cooling speed, the core might be amorphous or polycrystalline. The light propagation loss in the polycrystalline core optical fiber increases as the scattering loss increases
[5]. As a result, postprocessing techniques are needed to enhance the fiber light conducting performance.
2.2. High-Pressure Chemical Vapor Deposition
HPCVD is a hybrid method of engineering disciplines to integrate semiconductors and metals into MOFs. High-pressure chemical vapor disposition (HPCVD) is currently developed to deposit semiconductor nanowires, coaxial heterojunctions, and other patterned structures inside fibers
[29]. High-pressure flow at the MPa level can eliminate mass-transport constraints because the fibers’ high tensile strength overcomes the constraints of mass transport
[30]. In addition, by considering pores in a MOF template as small chemical reactors, which can be injected into different chemical precursors, it is possible to deposit uniform, thick, and annular deposition on the heated pore walls across lengths ranging from centimeters to meters
[31].
As the functional materials inside fibers can be chemically deposited in independent stages, enabling fibers to possess design flexibility, fibers fabricated by the HPCVD technique can be further utilized to design fiber-integrated devices, including photoconducting detectors
[32], fibers for infrared laser transmission
[33][34][35], fibers for thermal sensation
[36], radial fiber lasers, and wearable 2D and 3D array light detectors
[37]. Although the length of fiber fabricated by HPCVD does not seem to be as scalable as that manufactured by drawing, semiconductor layers of 10 m in length have been accomplished, and larger lengths are conceivable
[38]. In addition, HPCVD is extensible for deposition in several fibers using a single high-pressure precursor source, possibly enabling the concurrent fabrication of up to hundreds of fiber devices.
3. Postprocessing
As the core states are mostly polycrystalline or amorphous in fibers after thermal drawing, postprocessing is frequently necessary to increase the material quality or optimize the fiber shape to fully harness the fibers’ potential. Postprocessing techniques can enhance the performance of semiconductor optical fibers by increasing the crystallinity of semiconductors inside or by reducing element contamination, such as oxide contamination from glass cladding. All postprocessing procedures, except for techniques aimed at reducing element contamination, rely on either thermal annealing or melt-recrystallization to heat a sample
[39]. Common techniques used to enhance the multifunctional performance of fibers include thermal annealing
[40], rapid photothermal annealing (RPP)
[10], the interfacial modifier method
[41], and laser treatment
[42].
3.1. Thermal Annealing
Thermal annealing is a process for controlling the characteristics of materials via crystal formation. During the process, materials do not remelt or recrystallize but rather have controlled nucleation of crystals, during which flaws are removed, and grain sizes are increased
[39]. Thermal annealing can control the orientations of crystals that are produced, which may be crucial for certain purposes, such as nonlinear optics. Thermal annealing and rapid photothermal annealing are the two most common annealing techniques utilized for semiconductor optical fibers
[43][44]. To effectively grow large crystal grains inside fibers, the technique involves two steps. First, fibers are heated to a low temperature of approximately 530 °C for 3 days to control nucleation site numbers, and second, the fibers are heated to approximately 1300 °C for 10 min. Compared with the pre-annealed fiber, the resulting fibers exhibited a much lower dislocation density and optical loss
[45]. Herein, crystal sizes were restricted to 100 µm. Typically, thermal annealing is performed to transform amorphous semiconductor core material generated by the HPCVD technique into crystalline material. Moreover, both the absorption spectra and temperature performance can be changed by thermal annealing, as the technique can shift the bandgap of semiconductors and enhance the PL intensity
[46]. It has been observed that SiGe alloy fibers produced by thermal drawing were subsequently annealed in a box furnace with a controlled heating rate
[40]. Due to grain-to-grain diffusion, the homogeneity of the fiber core and the optical performance of the fiber was enhanced.
3.2. Rapid Photothermal Processing
The rapid thermal processing (RTP) technique that is dominated by quantum effects is referred to as rapid photothermal annealing (RPP). RPP allows semiconductor devices to be treated at temperatures that are lower than those required by RTP. As a result, RPP can produce semiconductor optical fibers with improved performance. The high throughput of RPP, in conjunction with its low processing temperature, offers new possibilities for devices such as solar cells, silicon integrated circuits, and flat panel displays
[47]. Photons with wavelengths of less than approximately 400 nm are essential to witness quantum phenomena. Quantum effects have several positive consequences for RPP. First, the bulk and surface diffusion coefficients are increased. Second, less time is spent in each cycle of processing. Third, there is a significant decrease in the number of microscopic flaws, which results in improved performance
[47][48]. In the case of RPP, the bulk and surface diffusion coefficients are greater than those of RTP and standard furnace processing. Additionally, quantum photo effects have a crucial role in ion implantation
[49]. Regarding performance, reliability, and yields, RPP will deliver a significant improvement over other production processes. RPP makes available materials that have consistent microstructures and built-in dependability
[48].
3.3. Laser Treatment
Laser treatment of semiconductors inside optical fibers is a very adaptable technique that can be utilized to change the semiconductor material in a variety of ways. For instance, CO
2 laser processing has been utilized to heat fibers and recrystallize fiber cores, thereby resolving the uneven segregation issue of semiconductor alloys during nonequilibrium solidification and improving optical transmission behavior
[10] by accurately regulating the heating temperature and cooling speed to produce single-crystal semiconductor materials
[11]. This technique allows the fabrication of semiconductor core fibers of any length with low loss. Similar techniques have been employed to reduce the optical loss of germanium core fibers
[50]. In contrast to conventional annealing techniques, the semiconductors of fiber are regionally heated to a molten state and then recrystallized under precise control as the fiber is scanned past the laser’s focal point
[39]. Unlike tapering methods, which must equally heat the core and cladding materials, laser processing allows for selective heating of either the core or the cladding, depending on the selected wavelength.
Two primary heating methods have emerged concerning laser treatment. The direct optical absorption of the laser beam was the first method shown to successfully heat and melt the core. A laser source with photon energy larger than the semiconductor’s electronic bandgap is utilized since this kind of laser can pass through the cladding material but is significantly absorbed by the core through electronic absorption. By adjusting the scan rate, the strain and the electronic bandgap of the material may be manipulated. The second method involves the use of heat carried from the cladding to melt the semiconductor. For silica cladding fibers, CO
2 lasers are commonly employed as the source since they can be absorbed by the cladding material. This technique allows for the development of single crystals with cm-scale lengths and high aspect ratios with minimal strain
[11][51]. Both methods may be used in combination, with energy being absorbed by the core and cladding in a single manufacturing step.
3.4. Interfacial Modifier
The utilization of an intermediate layer between the semiconductor core and the silica cladding can reduce tension, expel pollutants, and establish a gradient index of refraction
[52]. A suitable interfacial material should meet the following guidelines. First, the material should be oxide to reduce chemical sophistication; second, the material should form a eutectic with a semiconductor inside the fiber and possess a softening point that is higher than the semiconductor material to alleviate tension; last, the metal ion of the oxide should be less electronegative than the semiconductor to aid oxygen scavenging from the core
[41]. Calcium oxide meets the aforementioned characteristics and is often employed in the purification of silicon
[53], similar to other alkaline earth oxides. CaO reacts with water to create hydroxides; hence, a preform with a CaO layer on the interior of the silica may be prepared using an aqueous process. Further studies of NaO, BaO, SrO, and MgO were conducted with varying degrees of success: SrO and NaO, as well as NaO-BaO mixes, were the least successful, leading to deformation of the glass–silicon interface or immense voids in the core, while CaO and CaO-MgO blend behaved the best. Prior research mostly focused on the mechanical and microstructural qualities of the material. The optical characteristics of the fibers may be enhanced by using more pure raw materials
[41].
This entry is adapted from the peer-reviewed paper 10.3390/bios12100882