1. Introduction
Currently, one of the main global trends in the development of the energy industry is the shift to renewable energy resources (RES). Wind and solar power plants are widely used. At the moment, the total generation of electricity using RES in the world is only 3%
[1][2]. However, in the next few decades, many European countries, Japan, the USA, Canada, and China are planning to significantly increase this number in order to reduce emissions of toxic substances and greenhouse gases in the production of electricity
[3][4]. To implement such a large-scale ambitious task, it will be necessary to create storage systems that ensure the alignment of energy production and consumption schedules
[5][6]. The structure of existing energy systems will be subject to significant transformation.
One of the possible scenarios for the energy industry development is the shift to hydrogen energetics
[7][8][9]. A popular concept implies the production of hydrogen from renewable energy resources during off-peak loads, followed by effective utilization of the stored energy. It is possible to transport hydrogen from the place of production to the place of consumption through existing gas pipelines
[10][11]: hydrogen will be mixed with natural gas. Further the fuel blend can be sent to thermal power plants for subsequent combustion to generate electricity.
Since the cost of hydrogen produced according to the technology described above will be significant, it is advisable to carry out its subsequent combustion at the most efficient CCGT units. There is a number of ways to improve CCGT unit efficiency. Most of the known ways provide an increase in the electrical network efficiency by 0.6–3.6%. Their implementation usually requires capital cost increases, and sometimes the maneuverability and reliability of the power facility suffers. Therefore, the implementation of various methods or their combinations is not always economically feasible.
The basic method for increasing CCGT efficiency is to increase the initial temperature of the gas turbine cycle. Thus, an increase in the temperature at the gas turbine inlet (TIT) by 100 °C leads to an increase in the power unit efficiency by 0.9–1.5%
[12]. It is worth remarking that the available nickel alloys can operate at temperatures below 900 °C, and the cooling system efficiencies are close to their limits
[13]. In this regard, a further increase in CCGT useful electrical efficiency by increasing the GTU initial temperature is problematic.
An alternative approach to increasing CCGT efficiency is to increase the degree of flue gas heat utilization. In particular, increasing the pressure of the heat carrier in the waste heat boiler increases the heat recovery efficiency and, thus, increases the net generation of electricity in the steam turbine plant
[14]. In addition, it is possible to use superheating to improve energy efficiency
[15]. Increasing the heat carrier pressure and introducing reheating can reduce heat carrier thermal potential loss.
The introduction of an additional pressure circuit in the waste heat boiler with lower parameters makes it possible to efficiently utilize supplementary heat
[16]. The maximum amount of recuperated heat in this case is limited by the minimum flue gas temperature, which is determined by the condition of steam saturation and low-temperature corrosion of the rear heat recovery surfaces in the presence of sulfur in the fuel, as well as the waste heat boiler efficiency.
A promising way to reduce flue gas losses for CCGT is the transition to trinary cycles, which are combined cycle gas turbine units with integrated circuits on low-boiling heat carriers
[17]. For example, CCGTs with ORC are considered in the study by
[18]. Through the use of NK-36ST GTU with a single-circuit waste heat boiler, the utilization of low-grade heat in the ORC makes it possible to achieve net CCGT efficiency of more than 60% at a cooling water temperature in the low-grade cycle below 0 °C.
The use of trinary cycles was also considered in the article by
[19]. It was found in the work that the shift from a single-circuit CCGT to a three-circuit plant allows for increases in the electric power from 213.4 MW to 222.7 MW and increases in the net efficiency by 2.14%. The net efficiency of a trinary single-circuit power plant is 0.45% higher than that of a CCGT with a double-circuit waste heat boiler.
With an increase in the hydrogen volume fraction in the fuel, the concentration of water vapor in the exhaust gases also increases, which will increase the energy released during H2O condensation. This energy can be usefully utilized in additional corrosion-resistant heating surfaces of the waste heat boiler, which will increase the plant efficiency.
2. Analysis of the Energy Performance of a Methane–Hydrogen GTU
According to the simulation results, it was found that an increase in the hydrogen content in the fuel was accompanied by a decrease in the Wobbe index and the power unit’s auxiliaries (
Figure 1). According to the graph (
Figure 1a) it can be seen that under these conditions, without design changes, the operation of burners and nozzles in the combustion chamber can be carried out with a volume fraction of hydrogen in the fuel mixture not exceeding 80% (33% H
2 in fuel mass flow). The Wobbe index at this concentration is 43.3. With a further increase in the proportion of H
2 in the composition of the fuel, traditional burners may experience a problem with the distribution of the specific heat flow, which leads to the danger of separation and flashback of the flame at the mouth of the burner with further extinction of the torch
[20]. In turn, the increase in the auxiliaries (
Figure 1b) was due to an increase in the volumetric flow rate of the fuel blend, leading to an increase in the power of gas booster compressors by 2.8 MW.
Figure 1. The influence of the volume fraction of hydrogen on the performance of gas turbines.
The minimum of the Wobbe index curve is associated with the low density of hydrogen, due to which with an increase in the volume fraction of hydrogen above 80%, an intense hyperbolic increase in the volumetric thermal power occurs (
Figure 2c) and a linear decrease in fuel density (
Figure 2b).
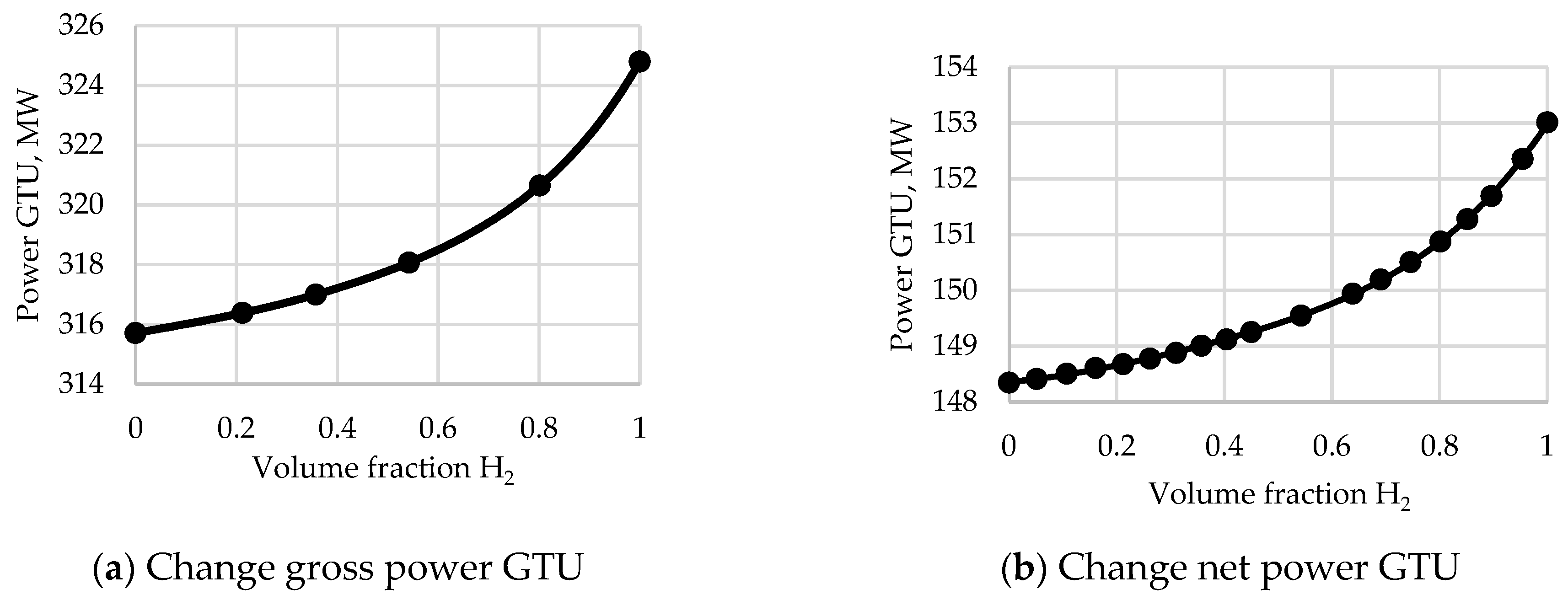
Figure 2. Dependence of GTU energy parameters on the volume fraction of hydrogen.
It was found that with an increase in the volume content of hydrogen in the fuel mixture from 0 to 100%, the GTU output electric power increased from 315.7 to 324.8 MW (Figure 2a), and the total output power increased by 4.7 MW (Figure 2b), which was due to an increase in the heat capacity of the working fluid with an increase in the concentration of water vapor. At the same time, the net calorific value increased from 55 MW to 120 MW, and the flow rate decreased by 2.35 times, due to which the GTU net efficiency increased (Figure 2c).
The change in gas turbine power was due to an increase in the concentration of water vapor during the combustion of H2, which is illustrated in Figure 3a. It was found that with a change in the chemical composition from 55% to 100% of the volume fraction of hydrogen, the increase in the heat capacity of the working fluid at the gas turbine inlet was 2.5 times greater than at its outlet (Figure 3b).
Figure 3. Influence of the volume fraction of hydrogen on the thermodynamic properties of the working fluid.
Figure 4 illustrates the effect of the methane–hydrogen blend chemical composition on the amount of carbon dioxide in the combustion products. It was revealed that the shift to hydrogen fuel completely disposed the production of electricity from carbon dioxide emissions.
Figure 4. Effect of hydrogen volume fraction on carbon dioxide emissions.
3. Comparative Analysis of Energy Performance of Binary and Trinary CCGTs Operating on Methane–Hydrogen Fuel
With an increase in the volume fraction of water vapor, the volume of combustion products increased by 2.9% due to the fact that the expansion process occurred with a constant difference in entropies, and the temperature of the working fluid at the turbine outlet dropped. Figure 5a shows that an increase in the hydrogen concentration in the fuel from 0% to 100% caused a decrease in the temperature of the working fluid at the inlet to the waste heat boiler by 3.4 °C.
Figure 5. Dependence of the temperature of the working fluid and the output power on the hydrogen volume fraction.
When shifting from methane to hydrogen fuel, the amount of heat supplied to the waste heat boiler increased, due to which the consumption of water vapor and the power of the steam turbine increased by 0.8 MW (Figure 5b). It is worth noting that due to the presence of the second circuit and the condensate gas heater, the capacity of the binary CCGT unit was higher than that of the trinary unit by 7.5 MW.
The research showed (Figure 6) that the use of the organic Rankine cycle in a trinary cycle with a single-circuit waste heat boiler made it possible to generate an additional 6.3 MW of electrical energy when operating on clean natural gas. The use of hydrogen fuel increased electricity generation by 10.3 MW.
Figure 6. Dependence of the ORC output power on the hydrogen volume fraction.
The sharp increase in electricity generation in the ORC cycle was associated with an increase in the concentration of water vapor (Figure 7a), due to which more thermal energy was released during the H2O phase transition, which was utilized in the low-boiling cycle. However, due to technical limitations of the utilized heat exchanger, the working fluid should not have a temperature below 41.8 °C, due to which the operation of the trinary cycle up to 75% of the content of the hydrogen volume fraction in the fuel is carried out outside the range of the water vapor condensation point (Figure 7b).
Figure 7. Thermodynamic characteristics of the working fluid at the outlet from the OCR.
With a further increase in the hydrogen concentration in the fuel, the partial pressure of water vapor increased. Due to this, after the hydrogen volume fraction in the fuel exceeded 75%, the dew point temperature reached 42 °C. The specific humidity of the exhaust gases depending on the hydrogen volume fraction in the fuel is shown in Figure 7c.
An increase in the concentration of hydrogen in the fuel increased the volume fraction of water vapor in the working fluid, which caused an increase in the heat input to the ORC and, accordingly, the generation of electricity at the plant. When comparing the efficiency of three different thermal circuits of CCGT (Figure 8), it can be seen that the greatest increase in power was observed in the trinary cycle due to the previously described phenomenon, and with an increase in the utilized energy of water vapor, the efficiency of the plant also increased.
Figure 8. Comparison of energy efficiency when operating on methane–hydrogen fuel of a double-circuit and single-circuit CCGT.
This entry is adapted from the peer-reviewed paper 10.3390/inventions7030073