Porcelain enamel is an inorganic-type coating, which is applied to metals or glass for both decorative and functional purposes. This coating is a silica-based solidified glass mass obtained by high-temperature firing (temperature can range between 450 and 1200 °C depending on the substrate). Porcelain enamel coatings differ from ceramic coatings mainly by their glass structure and dilatation coefficient, and from organic paints mainly by the inorganic nature of the matrix and the chemical bond that exists between the coating and the substrate.
Porcelain enamel is one of the most popular industrial coatings for the protection of metal artifacts, as it gives the coated substrates high-quality physical, chemical, and aesthetical properties. This coating was developed in ancient times to decorate precious objects as if to imitate the shining of precious stones. Only with the advent of the First Industrial Revolution, in the 18th century, enamel began to arise interest as a low-cost coating for many functional applications; this way, technical enameling was rapidly developed. Porcelain enamel is a material with ancient origins, but it is still appreciated for high-duty applications where good corrosion protection, chemical, and external agents’ resistance is required. In addition to that, enamel can efficiently protect the covered substrate, maintaining its aesthetical properties unchanged in time.
Proto-Enamel
The first people to make extensive use of what can be considered the true precursor of enamel are the Egyptians. Many archaeological findings of amulets and jewels testify the incredible ability of Egyptians in creating beautiful “faience” objects
[1]. The Egyptian faience is a no-clay and quartz-based ceramic displaying surface vitrification with colors varying from white to blue and green. All the faience-made objects were created by cast molding: the powdered quartz was mixed with alkali, calcite lime, and water; then, the object underwent a heating treatment that allowed the formation of an inner siliceous body covered by a vitreous surface layer of soda-lime
[2][3]. This way, Egyptians were able to create objects and jewels with a shining appearance and beautiful colors. From Egypt, this art was transmitted to the people of the Eastern Mediterranean Sea thanks to the close commercial interactions that existed at that time.
Origins of Enamel
The cradle of enameling can almost certainly be identified in the Mediterranean Sea. The first real enameled objects have been found in a Mycenaean tomb in Cyprus and date back to the 13th century BC: the most remarkable examples of these archaeological findings are represented by the famous Kouklia gold rings and the Kourion golden royal scepter, both dating back to the Cyprus Golden Age period
[4]. All the objects created in this historical period are decorated with colorful enamels arranged in small metallic cells, and they can be considered as the first examples of “cloisonné” enameling
[4][5].
The Cloisonné and Champlevé Enameling Techniques
The art of enameling rapidly spread in the Eastern world, where the cloisonné technique was the only enameling method used. Other important cloisonné archaeological findings can be attributed to the Assyrian Empire around 650 BC, a period in which Assyria controlled territories, as Cyprus, where enameling was already developed
[6]. From that moment onwards, the cloisonné enameling spread towards east, and toward the western Mediterranean Sea. The Scythians, an Iranian warrior people, brought the art of enameling to the Caucasian area and to Siberia as well
[7]. On the other side, the diffusion of enameling toward Europe was favored by the presence of the Phoenicians, who established close commercial relationships with colonies in Spain and Magna Grecia. The enameling of metals spread in Europe only around 500 BC, as some Etruscan jewel findings can testify
[8]. The diffusion of the cloisonné technique in Europe suffered a rapid decline with the success of the barbarian invasions, but it was reborn in Byzantium around the 600 AC for the decoration of icons
[4]. Here, the cloisonné technique reached its maximum splendor, thanks also to the great experience of goldsmiths, who used to work with small metal artifacts and successfully applied this skill to the production of enameled artifacts. A remarakable example of the cloisonné technique is represented by the golden enameled altarpiece in the Basilica of San Marco
[9]. The cloisonné technique was the most important enameling method until the end of 13th century, and its diffusion gave rise to several enameling schools in Spain, Italy, France, and Germany.
Differently to the cloisonné method, the champlevé technique consists in carving the metallic substrate, applying the enamel powder in the obtained carves, and then firing the whole object to obtain a smooth and glossy surface. This technique has been known since the 3rd century BC by the Celts, who used it to decorate small bronze objects by enameling
[10][11]. The Romans played an important role in the diffusion of this technique, but the champlevé method flourished only at the end of the 11th century in Conques (France), where it was used for enameling of copper. In the following years, new artistic schools were born all over Europe, in Cologne (Germany), Silos (Spain), and Liege (Belgium), but the artistic school of Limoges, which flourished around 1130, was the only one that survived over centuries
[12].
From the Renaissance Onwards
From the 13th century onwards, Limoges became the most important center for artistic enameling of all Europe. Enameled objects started to be produced as luxurious decorations objects, and they definitively lost the religious character that had been characterizing the enameled production over the centuries
[13]. There, in Limoges, new techniques flourished around the 14th century: the “enamel-paint” and the “grisaille” techniques
[14]. In the first case, matte enamels were used as if were colors on a canvas, whereas in the latter case, the enameler only used black and white enamels, firstly preparing a black background and then applying several layers of white enamel to create a wide range of gray shades and a relief effect. During the 15th and 16th century, the production in Limoges reached high-quality standards, and it was renowned all over Europe. In the next centuries, the production of enameled objects started to be relegated to clocks, ornaments, and small decoration objects only, thus decreeing the definitive decay of artistic enameling. Despite this, enameling would soon be reborn under a new form, to become commonly used in the everyday life of Western families. Many enameled decorative objects from different centuries and countries are conserved at the ARtCHIVIO Museum in Ponte San Pietro (BG), Italy, where the C.K.I Association (Creativ—Kreis—International) preserves and spreads the culture of artistic enameling.
Figure 1 shows some examples of cloisonné and champlevé artworks.
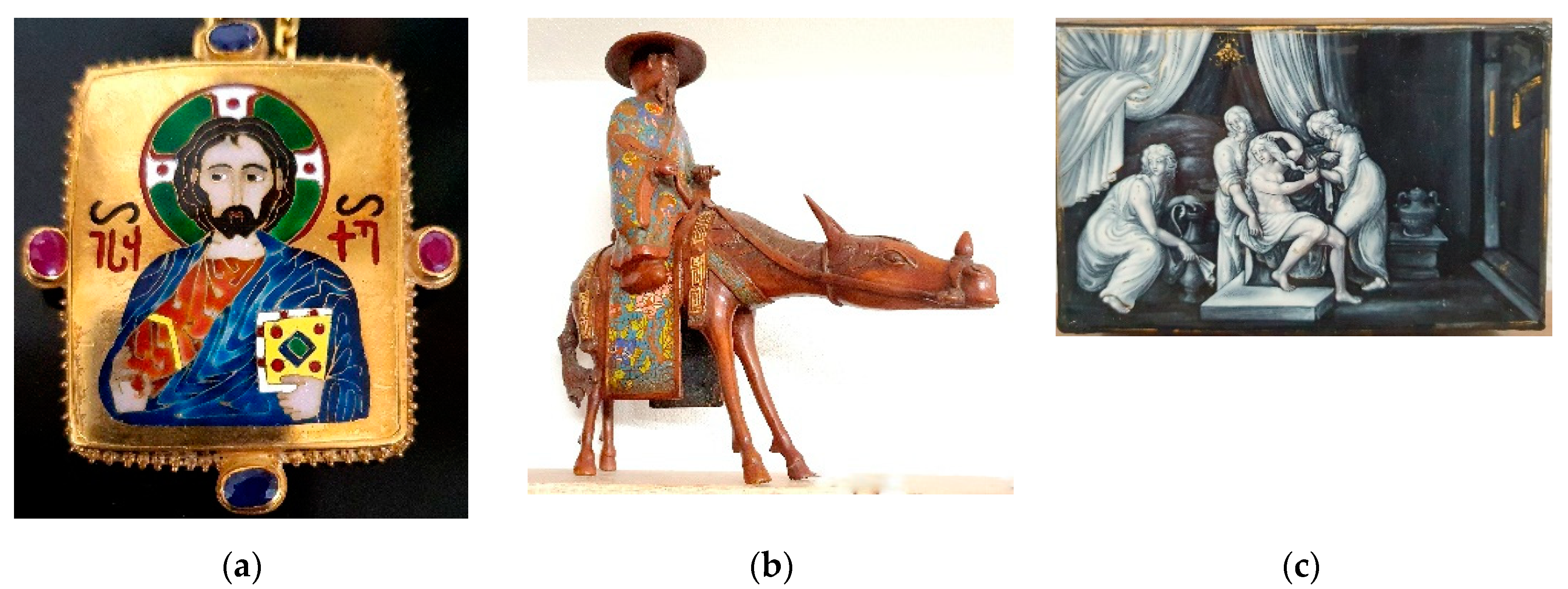
Figure 1. Examples of decorative enameled objects preserved and exhibited at the ARtCHIVIO museum in Ponte San Pietro (BG), Italy: (a) cloisonné enamel on gold icon in byzantine style, end of 20th century; (b) Champlevé enamel on bronze two-pieces statue, end of 19th century; (c) Enamel peint representing “Psyche’s toilet” by Jules Sarlandie, end of 19th century. Image courtesy of ARtCHIVIO museum, Ponte San Pietro (BG), Italy.
The Era of Technical Enameling
With the advent of the First Industrial Revolution, enamels started to be applied to substrates as iron and cast iron. The development of industrial enameling was so closely linked to the advances in metallurgy and chemistry of the late 18th century that the enameling industry was attracting the best chemists of the time. Although it is known that in the second half of the 1700s some industries were patenting the first enameling processes on steel sheets, it was only in 1851 that the first manual on technical enameling was published. At that time, iron sheets were obtained by the hammering of cast iron to produce the first enameled plates. Around 1870, the almost total enamel production was limited to cast iron hollow ware
[15], but in the following years, it was possible to produce high-quality cast iron pans, which were white enameled both inside and outside
[16].
In the second half of the 19th century, enameling faced different technical problems, such as the lack of pure raw materials and the development of new production methods for steel, but on the other side, many advancements were achieved, such as the discovery of new production methods for pigments. Probably, one of the most important discoveries in this field was represented, using clay to keep the powdered enamel in suspension in water: this way allows applying the enamel simply by painting, spraying, or the immersion method. This way, it was possible to produce more durable enamels at lower costs. Around the year 1900, Mr. John C. Reed introduced the machine molding of bath tubes, which boosted the sanitary enameling industry
[17]. In the same years, the introduction of antimony compounds as opacifiers in dry coat enamels is considered an important achievement
[17]. The enamel industry boomed some years after World War I, in the USA, and the manufacturing of refrigerators, stoves, sanitary ware, and household objects grew very rapidly, but it suddenly stopped with the advent of World War II, when enameling plants were converted to the treatment of war materials. In 1942, the development of titanium-based white enamels gave a great boost to the rebirth of the enameling industry, and new products, such as chimney pipes, dishwashers, cooking hobs, and water heaters started to be enameled
[18]. In the following decades, the enamel industry continued to evolve, also thanks to the development of new deposition techniques, which made it possible to obtain better quality products in an increasingly efficient way. Nowadays, enamel is commonly applied to many everyday use objects, but it is also used for the covering of panels for architectural applications.