Modern Methods of Construction with Offsite Manufacturing is an advancement from prefabricated technologies that existed for decades in the construction industry, and is a platform to integrate various disciplines into providing a more holistic solution. Due to the rapid speed of construction, reduced requirement of labour and minimised work on site, offsite manufacturing and prefabricated building systems are becoming more popular, and perhaps a necessity for the future of the global construction industry. The approach to the design and construction of prefab building systems demands a thorough understanding of their unique characteristics.
A prefabricated (prefab) building, by definition, is where an entire building or an assembly of its components is manufactured at an offsite facility and assembled onsite from self-sustained volumetric modules or separate panels. Prefabrication has existed in construction for many decades in various forms such as dry wall systems, structural insulated panels (SIP), prestressed beams, prefabricated roof trusses, prefabricated reinforcement cages, etc.
[1][2][3]. Modern Methods of Construction (MMC) with Offsite Manufacturing (OSM) have arisen to integrate these various technologies into a more holistic and systematic solution, and most modern prefab manufacturers will cater for various architectural designs with prefab units (modules or panels) of creative geometries and innovative connection systems. Such prefab units are mass produced in factories with upskilled specialist workmanship, and at times with automation and robotics in an offsite manufacturing facility, transforming the traditional site-based and labour-intensive approach to construction. Prefab building units have been widely used for residential, commercial and public infrastructure, post-disaster structures and many other applications around the world. Particularly in Australia, the use of modular construction in public infrastructure is a highlight in applications such as railway stations, schools, hospitals, police stations, childcare facilities, etc.
[4].
Offsite-manufactured prefabricated building systems are built in three main types of construction, as listed below:
-
Modular (volumetric) construction: manufacturing of fully self-contained units in an offsite facility to be transported to site to be assembled to form a complete structure.
-
Panelised construction: manufacturing of flat panel units in an offsite facility to be transported to site to be assembled to form a complete structure.
-
Hybrid prefab construction (semi-volumetric): combining both panelised and modular methods. Compact modular units (pods) are used for the highly serviced and more repeatable areas such as kitchens and bathrooms, with the remainder of the building constructed using panels or modules.
As shown in Figure 1, prefab structures can be built out of steel, timber (including engineered wood products), concrete or a combination of these. The two main benefits of prefab construction are speed of construction and reduced labour compared to traditional methods of construction. Some of the other benefits and features of prefab construction are as follows:
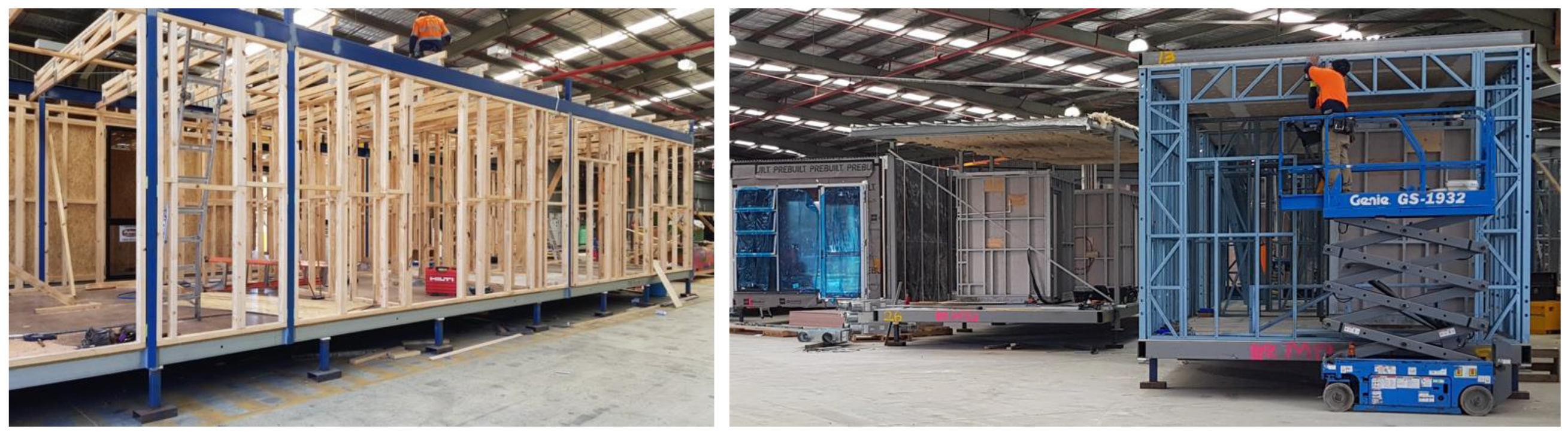
Figure 1. A steel modular unit with softwood wall frames (left) and a steel corner supported modular unit with a cold formed light-gauge steel wall frame (right), showing various materials used in prefabricated construction.
-
The reduced need for labour, especially for skilled trades such as welding, enables the construction process to move away from being a labour-oriented operation to a more process-oriented manufacturing and assembly process. This allows construction projects to achieve reduced on-site congestion, waste and pollution.
-
The prefab units, especially volumetric modules, can be removed from the main structure for future reuse or relocation. The reusability of prefab units contributes significantly to prefab buildings having a much lower life cycle energy
[5].
-
Enables construction to commence earlier than usual, as prefab panels or modules can be manufactured in the factory while onsite preparation and foundations works get underway concurrently.
-
Prefab construction at present reduces construction time by at least 50% from a site-intensive building
[6]. This ensures that the client of the project starts generating revenue much earlier than usual.
-
The construction process is significantly less vulnerable to adverse weather, resulting in an even faster construction.
Panelised units are loadbearing in nature, and most of these are integrated with insulation, cladding and internal plasterboards. Structural insulated panels (SIP) are a popular prefabricated panel type in use, especially in countries like Australia. Structural systems of modular buildings are developed using two main types of modules according to their load transfer mechanisms
[7], namely:
- 1 Loadbearing modular structural systems—The perimeter wall structure of the module carries adequate stiffness and continuous connectivity to transfer the gravity loads to the modules below. The roof beams and floor beams are often assisted by stud columns to add stiffness to the walls. This wall stiffness contributes to resistance against racking actions that are experienced during temporary loading scenarios such as moving and handling inside factories, loading and unloading to and from trucks during transportation and during onsite lifting and handling. This system is only feasible for low-rise applications due to the nature of loadbearing systems.
- 2 Corner-supported modular structural systems—Corner columns in the module take up the floor loads and transfer them to the columns below. This system is also capable of resisting horizontal loads such as earthquake and wind forces—as long as the connections are designed properly, with adequate stiffness, and complying to design standards—thus ideal for multi-storey applications. In most current modular applications, a structural system such as this, with columns and structural connections, is made from steel.
As discussed above, most multi-storey modular buildings found around the world are assemblies of corner-supported modules that are laterally connected to a cast in situ concrete core. This in situ core effectively acts as the primary lateral load resisting element and, in many of these, the floors are poured with concrete after installing the modules. Although these methods are innovative and do save construction time initially, they do not characterise the structures as purely modular nor provide them with the previously mentioned benefits of modular construction. Gunawardena et al.
[8] introduced a new concept of an advanced corner-supported structural system, where the shear core of the building could be formed by special modules with infill concrete walls. This would allow a multi-storey building to be constructed using corner-supported modules that could later be dismantled to construct other buildings elsewhere. Since then, similar concepts have realised into prefab structural systems in high-rise modular buildings such as the La Trobe tower in Melbourne, Australia
[2].