The attitudes of residents towards new construction methods (e.g., a wooden additional floor) have an important role in the spread of these practices
[59]. Moreover, the positive attitude of residents is a critical aspect in the effective execution of extensive refurbishment
[60]. In this sense, the survey by Karjalainen et al.
[25] showed that participants generally assessed the construction of wooden additional floors positively and thought that it would contribute to the attractiveness of the residential area.
The combustibility of timber may limit its use as a construction material in Finland, as in many countries, due to constraints on building regulations
[61][62][63]. Various studies have been carried out recently on the fire behavior of wooden buildings around the world, aiming to provide fundamental data on the safe use of wood (e.g.,
[64]). As a result of extensive testing, new fire design concepts and models were developed, and existing advanced knowledge in the fire design area of wooden structures together with technical precautions, especially well-equipped fire services and sprinkler systems, ensure the safe use of wood in a wide range of applications as seen in the building code relaxations introduced in recent years
[65]. In this sense, fire safety engineering and performance-based design offer benefits and challenges for the use of timber in buildings, where the performance-based approach is primarily based on the use of fire engineering principles, calculations, and modeling instruments (e.g., structural models, thermal models) to meet building regulations, considering fire modeling, full-scale structural fire experiments, and experience from fire accidents in timber structures
[66][67][68][69]. Additionally, the following considerations stand out in terms of the implementation of fire safety design in wooden structures
[70][71][72][73]: Manual firefighting, sprinklers, encapsulation, fire retardants, fire performance and fall-off times of protective systems, the fire performance of connections between structural timber elements, details to prevent the internal spread of fire, external fire spread in the same building, and quality assurance. Furthermore, timber and steel structures have some similarities and differences in terms of fire safety measures
[65][74]. Some fire regulations, such as those in Canada, encourage full encapsulation of timber frames to ensure equivalent fire safety to the non-combustible steel frame structure. In terms of performance-based design, performance-based formulations of requirements for timber structures can be considered to provide a fire-safety equivalent to regulatory steel structures. Regarding structural modeling, wooden structures are usually easier to model than steel structures because the wood has poor thermal conductivity and does not undergo considerable thermal expansion. In the manual fire extinguishing strategy, the fire risk will be greatly reduced if immediate action is taken to contain the fire, and this reduction in fire load is adjusted for steel frames. This method is also permissible for timber structures. Moreover, in terms of external fire spread in the same building, timber facades can also be used as fire-resistant facade cladding in steel structures.
Issues with wooden structures, especially sound insulation and moisture, require special insulation and protection techniques. To obtain good air-borne sound insulation, the partitioning wall and intermediate floor structures should be built in layers and the layers should be separated from each other so that the sound does not pass through the structure
[75][76]. On the other hand, humidity issues lead to both reduced durability and mold growth, which can affect indoor air quality and have adverse health consequences
[77]. The best strategy for providing a moisture-resistant structure is to ensure that the wood is not exposed to water or high relative humidity for extended periods. Neglecting moisture safety can mean a high risk of damage, with extensive costs and consequent time delays for research, decontamination, or material replacement
[78].
Wood-based composite materials and wood frame-based hybrid structures are among the important topics in today’s wood construction literature. In general, owing to the destruction of forest resources and recently developed technologies for wood-based composite materials in particular, engineered wood products have gradually replaced traditional materials for residential construction
[79]. These materials are produced from similar materials based on wood products, e.g., timber or lumber processed into boards, or wood chips
[80], and the residential and commercial building construction industry is among the areas where wood-based composites are most in-demand
[81][82]. On the other hand, the idea of hybrid structures that combine multiple materials, such as timber, along with steel and/or concrete, is gaining increasing acceptance in the engineering community
[83]. Moreover, hybridizing timber with other structural materials is one of the most popular approaches for designing high-rise timber buildings
[84][85][86][87] as in the case of Brock Commons Tallwood House (Vancouver, BC, Canada, 2017)
[88].
The three critical components of timber frame construction are the floor, the roof, and the load-bearing wall, which have significant effects on occupants’ comfort. The wood floor, the most common system component, is in frequent physical contact with building inhabitants
[89]. The dynamic movement of people or objects caused by defects or deficiencies in the structural performance of the floor can cause occupant discomfort. Movements, e.g., walking, running, jumping, can create structural vibrations on the wooden floor, which adversely affect the efficiency of work and quality of life
[90]. However, environmental excitation and impact excitation vibration tests as well as comfort analyses of timber floors offer solutions to these undesirable situations
[91]. In addition, particularly nowadays, when standard structures are supported by contemporary technologies such as wooden floors combined with underfloor heating, it is necessary to meet technical guidelines and specifications during the operation of the floor as a whole
[92]. Moreover, in line with the ‘smart building’ concept, wood, namely wood flooring, is used as an ideal material to be applied in triboelectric nanogenerators for large-scale applications in smart houses
[93]. This ensures that mechanical energy (for example, the movements of residents) is directly converted into useful electricity
[94][95][96][97].
Although there are numerous research studies on different construction solutions with the use of engineered timber products with related technical features (e.g.,
[98][99][100][101][102][103][104][105][106][107][108][109]), several studies have focused on the use of wood as a building material from the viewpoint of construction professionals (e.g.,
[110][111][112][113][114][115][116][117][118][119]) and consumers or users (e.g.,
[120][121][122]). On the other hand, to date, there has been a limited number of studies on wooden additional floor applications, especially in the housing construction industry.
This entry maps out, organizes, and collates scattered information on the current state of the art, as well as benefits and challenges of wooden additional floor projects with their different stages, focusing on the case of Finland, and presents it in an accessible and understandable discourse for non-technical readers. This entry also provides a methodical literature analysis on international peer-reviewed studies and research projects. By highlighting the advantages and opportunities of these sustainable practices, the entry will contribute to an increase in the awareness of wooden additional floor construction, which has many advantages and therefore help to gain more widespread use in Finland and other countries.
In this entry, timber or wood refers to engineered timber products
[123][124], e.g., cross-laminated timber ((CLT) is a wood panel product made from gluing together layers of solid-sawn lumber), laminated veneer lumber ((LVL) is produced from veneer and is designed for structural framing where high strength and rigidity are required), and glue-laminated timber (glulam) ((GL) consists of layers of dimensional lumber glued together with durable, moisture-resistant structural adhesives).
The remainder of this entry is composed as follows: First, a literature survey is provided. This was followed by a section on the benefits, challenges, and drawbacks of wooden additional floor construction. Finally, the conclusions and prospects of the research are presented.
2. Literature Survey
As mentioned above, there are a limited number of studies on wooden additional floor construction. Among them, Karjalainen et al.
[29] analyzed the different stages of wooden additional floors in old apartments from the standpoint of housing and real estate firms in Finland via interviews with involved professionals. Their result indicated (a) meticulous scrutiny of commercial conditions was critical to a profitable investment; (b) a change in the city plan, finding a suitable contractor, and involving an expert were among the highlights; (c) for the feasibility phase, the importance of parking space, load-bearing capacity, and compatibility with building regulations was emphasized; (d) during the project planning phase, attention was drawn to the importance of current building regulations and building rights concerning taxes and fees; (e) during the implementation planning process, city plan changes and different tender conditions came to the fore; and (f) effective information sharing between parties was a critical parameter for the successful completion of the construction phase.
Similarly, highlights of the study by Karjalainen et al.
[125] were (a) the feasibility study emphasized the property’s condition and potential targets for improvement, as well as relevant codes and regulations in force; (b) construction cost, profit, and sales of building rights were among the issues that were frequently discussed during the project planning phase; (c) building rights, changes in the city plan, and conditions of the company managing the property were reported as significant issues during the implementation planning phase, and (d) regular and frequent updating of building occupants on the progress of the construction process was the backbone of the construction phase.
On the other hand, Karjalainen et al.
[26] conducted a survey and discussed the residents’ approach to wood facade renovation and additional floor construction from Finnish residents’ standpoint. Their study highlighted the following regarding additional floor construction: (a) Residents’ attitudes were mostly positive; (b) younger and more educated people approached these practices much more positively; (c) respondents generally thought that additional floor construction will increase the attractiveness of residential areas; and (d) apartment owners positively appreciated the housing association’s decision for additional floors to finance the facade refurbishment.
Soikkeli and Sorri
[19], Soikkeli et al.
[23], and Soikkeli
[24] presented a research project (Finnish national research project, User- and Business-oriented Suburb Renovation Concept [KLIKK]) targeted to develop an industrial-scale, viable, and effective method for refurbishing and implementing additional floors to old apartment buildings. The technical solutions that form part of the concept were actively taking advantage of the opportunity offered by the new Finnish fire codes for the use of timber structures during renovations.
Cronhjort et al.
[25] discussed obstacles and benefits for the utilization of wood-based approaches for infill development and building extensions in Finland by examining architecture and engineering master’s theses. Their findings highlighted (a) there was a potential for infill development in the Finnish municipalities; (b) the applicability of vertical extensions that increase the functionality and quality of life was also demonstrated; (c) the added value of using timber-based prefabricated solutions in each case was shown; and (d) environmental, financial, and social advantages of infill construction, which is one of the Finnish national targets in provincial and land use, were evident in the case studies.
In addition, there are several studies on the vertical extension of buildings conducted in other countries. Prominent among these studies, Leskovar et al.
[126] aimed to verify the effect of a structural lightweight wood–glass upgrade module and building a vertical extension on the energy efficiency of the selected renovated building concerning the relationship between the volume sizes of the existing building and different types of upgrade modules in Slovenia. The results showed great potential to reduce the energy consumption of existing inefficient buildings and simultaneously addressed the problem of urban sprawl by enabling the concentration of usable floor space in urban centers. Sundling et al.
[127] evaluated and compared four refurbishment approaches to find an economically feasible model using life cycle profit analysis and life cycle impact assessment, based on a study of six similar buildings constructed in Gothenburg (Sweden) in 1971. The findings showed that vertical extension promotes the energy-efficient renovation of buildings, and the combination of low energy and vertical extension has the highest return on investment and lowest environmental impact. Artes et al.
[128] focused on the regeneration of city centers by identifying high proportions of the buildable area remaining on roofs (approximately 2500 buildings making up 800,000 square meters of buildable area in Barcelona, Spain) using two-dimensional panels and three-dimensional partitioning made of wood and steel. Their construction methods made it possible to undertake the upgrading of existing buildings and to provide, in at least seven cases, new high-quality homes that improved the quality of life for the community. Dind et al.
[129] introduced the Workspace project aiming to develop a new prefabricated timber structure system tailored to the vertical extension of existing office buildings through a pilot project carried out in Lausanne (Switzerland). The results allowed the technical and architectural suitability of the system to be validated, particularly in terms of its typological flexibility and economic feasibility, with prefabrication, transportation, and assembly of large elements and a building in operation, in a dense urban context.
3. Wooden Additional Floor Construction
Additional floors (
Figure 4) increase the building height and the number of building stories or change the shape of the roof, as one of the most effective ways to cover real estate development and renovation processes by increasing energy efficiency and functionality
[25]. The benefits, challenges, and drawbacks of additional floor construction can be summarized as follows
[23][24][25][26][27][28][130][131][132][133][134][135]:
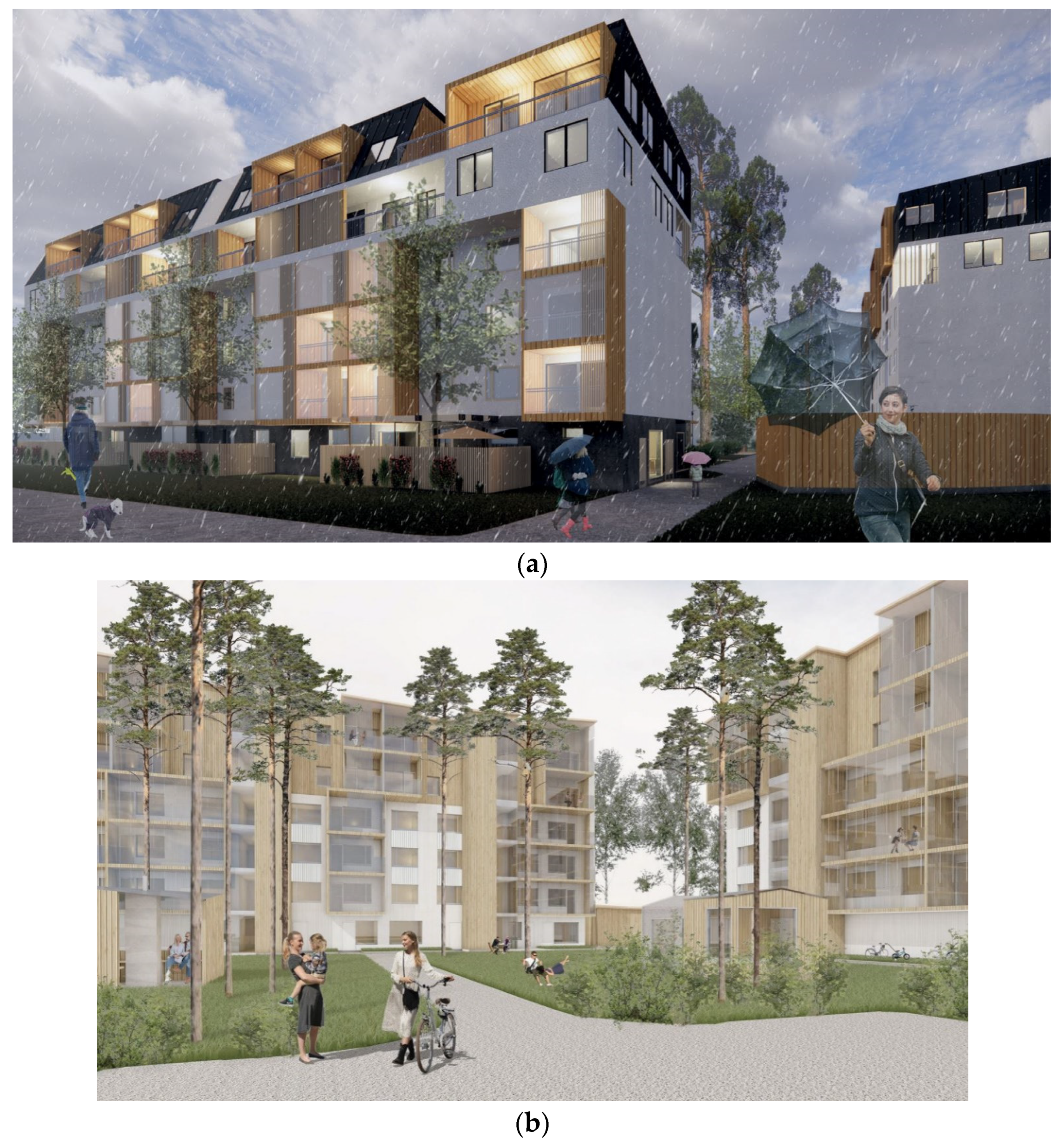
Figure 4. Wooden additional floor project examples: (a) An example where the shape of the roof has changed (Image courtesy of Samu Rantanen, Elissa Helminen, and Linnea Lindberg); (b) an example where the shape of the roof has not changed (Image courtesy of Johanna Partanen, Laura Lamberg, and Riina Hagren).
- As an efficient and environmentally friendly construction method, it provides beneficial development of the building stock and increases the income of property owners.
- Renovation and upgrading of old building stock were more beneficial in terms of the carbon footprint than new construction and demolition. For example, Huuhka et al. [27] reported that renovation and upgrading works with additional floors have a 20% lower negative impact on the environment in terms of carbon footprint compared to new construction and demolition.
- Additional floor construction provides short-term income to housing companies by selling the building rights or areas of additional floors. Revenues from additional floors could be used to cover the renovation cost of the old building.
- Additional floors considerably increase the total floor area without significantly affecting the total energy consumption of the upgraded building.
- As energy-efficient passive structures, additional floors can substantially improve the energy efficiency of existing buildings, especially if the upper floors have not been renovated for a long time.
- Additional floors improve the appearance of the building and can have a substantial impact on the architectural impression.
- Considering that the renovation process is a slow and uncomfortable process for the residents, the construction of an additional floor using prefabricated elements minimizes this discomfort of the building occupants and speeds up the process.
- To minimize disturbance to residents, it makes sense to build wooden additional floors from box-like module elements. However, module elements are difficult to design and construct because the upper ceiling tile cannot usually be loaded, so the loading must be aligned with the load-bearing walls below the floor, which may be few in number.
- To manage the renovation costs and use the insufficient autumn and winter capacities of the housing factories, wooden additional floor projects, especially during the winter months, face difficulties in the construction site conditions, especially in humidity control.
- Additional floor construction, which not only ensures energy efficiency but also brings the existing building to modern standards, is a complicated process consisting of several stages mentioned below that are technically more difficult.
- The socio-economic consequences of densification due to additional floors were brought to the agenda in several studies (e.g., [133][134][135]).
- Increased use of infrastructure, green space, and common appliances can be considered as the drawbacks of additional floor construction.
The construction of a wooden additional floor can be divided into four main stages
[29][125]: (i) The feasibility phase, (ii) project planning, (iii) implementation planning, and (iv) construction. During the feasibility phase, construction professionals and real estate sectors are contacted, and construction conditions of additional floors are evaluated. At the project planning stage, the project conditions, course, and scope of the project are determined. During implementation planning, steps are taken to enhance the construction plans and expand the building rights, allowing the construction of additional floors. The terms and conditions of the city plan change, building rights, and the company managing the property are among critical issues for this phase. As the final stage, the construction of wooden additional floors begins. Effective flow of information between residents and stakeholders and the appointment of a representative of the housing or real estate firm to join site meeting organizations and discuss suitable schedules for the construction process are important considerations at this stage.
4. Conclusions and Prospects
This entry aimed to map out, organize, and collate scattered information on the current state of the art, as well as benefits and challenges of wooden additional floor projects with their different stages, focusing on the case of Finland, and presents it in an accessible and understandable discourse for non-technical readers.
Endorsing positive market development, informing people about efficient energy use and energy savings from building refurbishments including the construction of additional floors, providing different forms of financial support for these sustainable practices, conducting more research and creating more investment, and encouraging new modes of energy contracts are actions that play important roles for future applications of additional floor construction.
In terms of both building construction technology and tendering procedures, wooden additional floor projects have great development potential. Especially with regard to construction technology, the use of prefabricated wooden elements, e.g., volumetric modular elements, can make construction faster and reduce construction-related disturbances, which is a major problem for building occupants, contributing to the diffusion of additional floor construction, as in Finland. For example, the experience and expertise gained in these projects, which have become widespread in the last ten years in the Tampere region of Finland, paved the way for further improvement in contract and technical-based issues
[29][125].
All stages of wooden additional floor projects need dedication and investment, as well as advanced communication and collaboration between all relevant stakeholders and housing or real estate professionals. This entry will contribute to the increase in awareness of the construction of wooden additional floors, which has environmental, financial, energy-efficient, and aesthetic benefits in Finland and other countries.