CO2 has been highly emitted to the environment, with the distribution of 25% being from electricity and heat production, 24% from agriculture, forestry, and other land usages, 21% by industry, 14% from transportation, 10% by other energies, and 6% from building. CO2 removal from natural gas is needed due to issues such as corrosion, catalyst poisoning and its effects on lowering the heating value of fuel. Several mass-transfer technologies can be used for this purpose, namely, membrane, absorption, adsorption and cryogenic. Membrane-based separation methods are more energy-efficient than heat-driven separations. Membrane-based separation uses 90% less energy than its distillation counterpart.
1. Introduction
CO
2 has been highly emitted to the environment, with the distribution of 25% being from electricity and heat production, 24% from agriculture, forestry, and other land usages, 21% by industry, 14% from transportation, 10% by other energies, and 6% from building
[1]. Natural gas is the lowest-carbon-emitting fuel compared to crude oil and coal
[2], where the CO
2 emission is less by ~26% with the same amount of energy produced
[3]. Despite this, CO
2 removal from natural gas is needed due to issues such as corrosion, catalyst poisoning and its effects on lowering the heating value of fuel
[3][4][5][6][7]. Several mass-transfer technologies can be used for this purpose, namely, membrane, absorption, adsorption and cryogenic
[8]. However, membrane-based separation methods are more energy-efficient than heat-driven separations. Membrane-based separation uses 90% less energy than its distillation counterpart
[9]. The traditional method for CO
2 capture is based on amine absorption, but this process requires high energy, incurs high capital and operating cost, and poses corrosion and environmental issues in addition to some operational issues
[3][10][11]. The membrane has been found to reduce the energy cost of CO
2 separation from amine absorption and adsorption
[12]; hence, it has been vastly studied for this application.
Membrane units are significantly smaller in size than the conventional plants at the same capacity, hence they are suitable for offshore natural gas application
[13]. Membranes have been used for industrial gas applications for over 35 years since the first membranes were commercialized for natural gas CO
2 removal in the 1980s
[14]. Since then, the continuous evolution of gas-separation membranes has produced USD ~1 billion in sales. It is estimated that worldwide membrane market growth is very steady, at approximately 10 to 15% per year
[15], and 60% of the membrane gas separation market has been dominated by nitrogen removal from air and natural gas CO
2 separation
[16]. At present, the rapid growth of the membrane market is being driven by technological advancements in polymer science and membrane process engineering
[17].
Table 1 lists the polymeric membrane producers for CO
2 separation.
Table 1. Polymeric membrane producers for CO
2 separation available in the market
[11].
Producer
|
CO2 Separation Process
|
IGS (Generon membrane)
DIVEX GLOBAL (Helipur membrane)
|
CO2/H2
CO2 from N2/Ar/O2
|
UOP—A Honeywell Company (-)
|
CO2/H2
|
AIRRANE Co, Ltd. (Hollow fiber polysulfone (PSF)-based membrane)
|
CO2 from CH4/H2/N2
|
CYNARA (Cellulose triacetate (CTA) based)
|
CO2 from natural gas
|
MEDAL (Polyaramide based)
GRACE, SEPAREX (Cellulose acetate (CA)
MTR (Perfluoro polymers based)
PBI Performance Products, Inc. (Hollow fiber Celazole®PBI based)
|
CO2/H2
|
AIR Liquide S.A. (-)
|
CO2 from biogas/natural gas
|
EVONIK Industries AG (Sepuran® membranes)
Compact Membranes Systems, Inc. (Fluoropolymer based)
|
CO2 from biogas
CO2/CH4, CO2/N2
|
The potential of polymeric membrane technology as a separation system for specific high CO
2 gas fields, when compared to other competing solutions, depends on the feed flow, operating conditions, the target purity and location of the project
[18][19][20]. The membrane offers great advantages as a green technology due to its lower energy consumption, no chemical solvent usage, simple operation and maintenance, and high reliability. In addition it is modular, hence easy for expansion, it being energy-efficient, and it have a compact module design
[6][11] which is crucial for offshore operation. On top of that, the membrane process response time is basically instantaneous, hence troubleshooting can be very quick, and the rapid start-up can be achieved
[20]. Membrane-based gas separation favours bulk removal when only modest purity is needed and the source feed gas is at high pressure, while the retentate stream is the sales gas product
[21], at high pressure for the ease of transport.
Several large-scale membrane separation processes have already been installed at offshore platforms with
[22] the CO
2 contaminant in the range of 5 to 70% in the crude natural gas
[17]. Depending on the target, a certain percentage of the hydrocarbon loss is required from the membrane to meet the flare BTU (British Thermal Unit) number to avoid using sales gas as the flare fuel gas. In this case, polymeric membrane possesses high productivity, and lower purity is required for separation, so membrane area and cost could be reduced. Some might target very stringent outlet CO
2 percentages depending on the pipeline specifications. As an example, U.S. pipeline specifications are <2% CO
2, 7 lb H
2O/MMscfd, 4 ppm H
2S, dew point of <−20 °C and heating value of 950–1050 Btu/scf
[23]. Unfortunately, there are only few polymers that have both high permeability and selectivity since most polymeric materials have a trade-off relationship according to the Robeson plot
[24]. A commercially attractive membrane must possess excellent separation efficiency with high permeance and selectivity, be stable for long-term operation duration, have high strength, and be able to withstand high temperatures and various contaminants. It also needs to have high resistance to aging and plasticization as well as being easily and cheaply manufactured into different sizes and shapes of membrane modules
[25].
2. Commercial Polymeric Membrane for Gas Separation
For natural gas separation systems using glassy polymeric membranes, cellulose and sulfone-based materials are the pioneers used for commercial membranes. Although these polymers still dominate the market, more polymers such as polycarbonates (PCs), polyimide (PIs), sulfonated polysulfone (sPSF), polyetherimide (PEI), and polyamides (PA) have also been introduced commercially
[26]. Reported CO
2 pure gas permeabilities and CO
2/CH
4 ideal separation factor at 35 °C and 2 atm for PSF are 5.6 Barrer and 22, for cellulose acetate (CA) they are 6.6 Barrer and 33, for PIs they are 7–20 Barrer and 58 to 102, while for tetrabromo-PC they are 4.2 Barrer and 32, respectively
[27]. The features of the polymeric membrane affect the attraction of various gas molecules within the membrane differently, which affects the gas solubility. Membrane fabrication will influence the polymer structure matrix, and the amount of free volume will influence diffusivity
[11]. The diffusivity–selectivity can be boosted by enhancing free volume and by modification of its distribution, while the solubility can be improved by introducing CO
2-philic groups
[24]. The incorporation of various Lewis bases, such as ether and carbonyl oxygen, promotes physical interaction due to higher polarity, thus producing higher CO
2 solubility
[17].
Many high-performance polymers have been formulated, but very few can be applied commercially, mainly due to physical aging and plasticization issues
[25]. Traditional glassy gas-separation membrane polymers have low free volume, such as CA, PI and PSF. Hence, they possess low gas flux and high gas-separation factors during high-pressure applications. On the other hand, rubbery membranes such as poly(ethylene oxide) (PEO), poly(amide-6-b-ethylene oxide) (Pebax
®), poly(dimethyl siloxane) (PDMS), polyvinyl alcohol (PVA), and polyvinylamine (PVAm) have lower selectivity than glassy membranes despite having high permeability
[15], which limits their applicability in gas separation membrane application. Polymer structural characteristics are governed by their physical and chemical properties. Side groups, molecular weight, the polymer chain’s flexibility, chain interactions and Tg (glass transition temperature) are characteristics that impact the performance efficiency of the membrane, including its chemical, thermal and mechanical stability. The nature and number of side groups in the polymer chain are linked to the rigidity percentage of the main chain. Functional groups such as heterocycles, aromatics, and long side chains, can decrease the polymer chain’s flexibility. The availability of nitrogen and oxygen attached to the main-structure carbon atom enhances the chain flexibility. The introduction of aromatic groups into the main chain of the polymer results in flexibility reduction due to the decrease in chain rotation. This leads to chemical and thermal stability, a higher glass transition temperature and a chain rigidity characteristic
[28]. The more flexible the polymer chains, the higher the permeability, since the chain dynamic can affect the transport properties and the separation performance, but this is usually coupled with robustness and durability issues. Polymer Tg and molecular weight can be related to polymer interchain forces and interactions between the chain, which define the polymer state
[4].
2.1. Cellulose Acetates (CA)
Semicrystalline CA is a green material that is relatively cheap because its raw material comes from a variety of renewable resources such as recycled paper, cotton, sugarcane, and wood
[11]. The pioneer in commercial membrane applications for natural gas processing is based on CA and its derivatives. Since the mid-1980s, CA for reverse osmosis membranes has been modified and commercialized for CO
2 separation from CH
4 [14]. Cellulose tri-acetate (CTA) membranes occupy 80% of the global market for natural gas removal because of their peculiar properties of low cost, ease to process, higher durability, long term reliability, high pressure resistance, and competitive gas-separation performance
[29]. CA polymers with different degrees of acetylation can be dissolved using organic solvents, since acetylation significantly decreases hydrogen bonding, enabling them to be fabricated using the phase-inversion process. Its membrane permeability is directly related to the acetylation percentage. Enhancing the acetylation (1.75 to 2.85), improves its CO
2 productivity to 6.56 from 1.84 Barrer, while maintaining the CO
2/CH
4 separation factor in the range of 33 to 35. This enhancement results from the change in polar hydroxyl groups (-OH) to bulky acetate groups (-COCH
3) (refer to
Table 2a), which reduces its density hence generating more free volume
[23]. The different steric hindrance and electronegativity of hydroxyl (HO-) and acetate (CH
3COO-) groups in CA affect the volumetric, mechanical, and gas-separation properties
[30].
Table 2. Chemical structure and Tg for various polymers.
No.
|
Polymer Name
|
Tg (°C)
|
Chemical Structure
|
(a)
|
Cellulose &
Cellulose
Tri-Acetate
(CTA)
|
185
|

|
(b)
|
Polysulfone
(PSF)
|
182
|

|
(c)
|
Polyethersulfone (PES)
|
222
|

|
(d)
|
Poly trimethyl phenylene ethersulfone (TPES)
|
NA
|

|
(e)
|
Polyetherimide—PEI
(Ultem®)
(BPADA-PPD) [31]
|
199
|
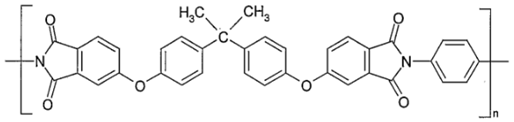
|
(f)
|
Polyimide—PI
(Matrimide® 5218)
(BTDA-DAPI)
|
313
|
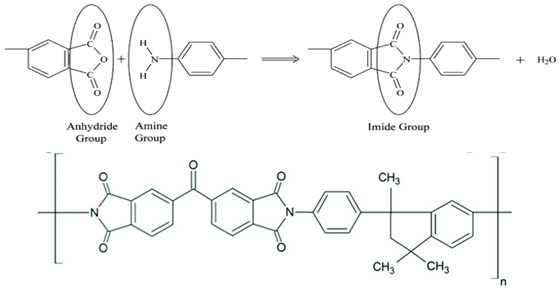
|
(g)
|
Polyamide-imide—PAI
(Torlon)
|
281
|

|
(h)
|
6FDA-based polyimide
|
348
|
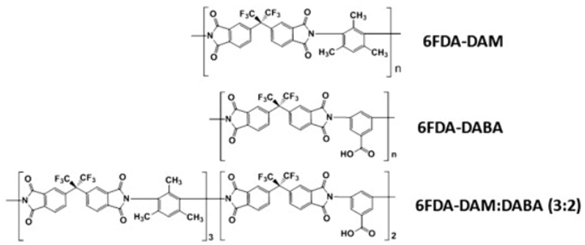
|
(i)
|
Polycarbonate
Bisphenol Z & A
(BPZ-PC & BPA-PC)
|
175
&
151
|
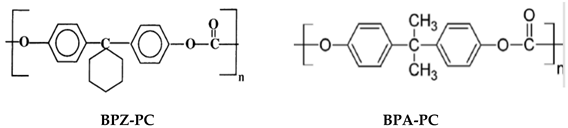
|
(j)
|
Polymer of intrinsic microporosity-1
(PIM-1)
|
442
|
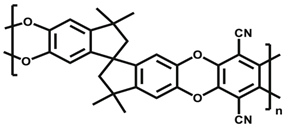
|
(k)
|
Hyflon
|
194
|
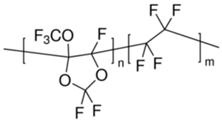 |
The major limitation of CA is its susceptibility towards CO
2 plasticization
[23], vulnerability to the presence of water due to its hydrophilicity, and having some interactions with some hydrocarbons such as acetone and aromatics
[11], which will damage and dissolve the membrane. Their CO
2/CH
4 selectivity reduces to <20 under high pressure of >25 atm and mixed-gas conditions due to a plasticization effect, as shown in
Figure 1, which leads to excessive methane loss
[27][32]. Eliminating all these contaminants will prolong membrane lifespan. Nevertheless, it is also claimed that CA membranes are robust to aromatic hydrocarbons
[14]. CTA can maintain its high performance under actual operating conditions for separation with heavy hydrocarbons due to its high CO
2/CH
4 solubility selectivity, which may not be affected by the plasticization induced by the heavy hydrocarbons. The high CO
2/CH
4 solubility selectivity in CTA can be further improved by lowering the operating temperature, though the polymer plasticization by the heavy hydrocarbons becomes more significant due to their increased solubility at lower temperatures
[33].
Figure 1. CA membrane performance trend for CO
2/CH
4 mixed gas
[34].
CO
2 plasticization pressure of CA is not changed with different degrees of acetylation. Sanders et al.
[23] mentioned that CO
2 changes the structure of the more highly acetylated membrane more significantly, as shown in hysteresis studies, due to the higher CO
2 solubility. Compared to the hydroxyl–hydroxyl, the intermolecular network that grips the available polymer chains is lesser in the acetylated membrane, therefore the effort to improve the permeability results in lower strength. Some studies harnessed the benefit of the controlled plasticization effect to enhance the FFV (fractional free volume) of the membrane during fabrication. While CO
2 is plasticizing the membrane, it modifies the area between CA chains to locate more gas. After the CO
2 is permeated, the polymer chain will maintain in this new transformed state. The membrane properties due to this conditioning are time-dependent, with more pronounced effects happening with longer membrane exposure to the high-pressure CO
2 [14]. Cynara
® hollow fibres (Schlumberger™, Houston, TX, USA) and Separex
® spiral-wound (UOP, Honeywell™, Des Plaines, IL, USA) are commercial CA-based membranes
[34], that have been used in high CO
2 concentration offshore operations.
2.2. Polysulfones (PSF)
A basic PSF unit consists of a sulfonic group, an ether group, one or more aryl groups, and other functional groups, as illustrated in
Table 2b. This thermoplastic polymer has high mechanical properties, remarkable thermal characteristics with a high glass transition temperature, is stable in oxidizing environments, and has a higher plasticization pressure (~27 bar partial pressure of CO
2). It also has significant resistance to acid and base environments in specific concentrations and temperatures
[35]. PSF has low free volume, less regularity, lower bulky density, resistance to molecule rotation, a rigid backbone, and has high heat-deflection temperature
[23]. In 1979, Monsanto fabricated the first membrane separation system using PSF hollow fibres
[36], and it was later commercialized for water removal by Air Products, under the trade name ‘Prism’
[37].
Researchers also favour polyethersulfones (PES) which have linear and shorter chain structures, as shown in
Table 2c, where the tighter structure yields higher selectivity than PSF. In addition, PES has higher temperature resistance, allowing it to be applied continuously at a higher operating temperature of 200 °C without causing serious damage to its properties. Ether–oxygen, in its structure, provides CO
2 binding. However, PES has low permeability and a faster aging rate, making it unsuitable for commercial use
[38][39]. To resolve these issues, substituting phenyl rings with symmetric bulky groups such as methyl could effectively enhance its gas permeability. Bulkier groups, namely hexafluoro isopropylidene, are used to substitute the isopropylidene bridging moiety to enhance its free volume, making the polymers much more permeable
[23]. A novel PES has been manufactured by substituting one diphenyl sulfone unit in the main chains with a bulky and rigid 1,2,4-trimethylbenzene moiety, as shown in
Table 2d. The new TPES (poly trimethyl phenylene ethersulfone) has a superior permeability and higher aging resistance. The addition of this moiety creates additional free volume, restricting chain movement and relaxation, hence it displays a slower aging behaviour. The TPES membrane is said to have similar gas-separation efficiency to Matrimid
[38].
2.3. Polyimides (PIs)
Pis have been proven useful as gas-separation membranes because of their outstanding combination of properties such as unusually high permeabilities and permselectivities. Structure modifications have been made extensively with the incorporation of both aliphatic and aromatic moieties, to enhance its solubility
[40] in typical membrane casting solvents. Certain members of the PI family are resilient to chemical attack and stable to temperatures above 400 °C
[41].
Table 2e,f,h shows some imide polymer structures prepared via the condensation reaction of an aromatic anhydride group with an aromatic amine
[31]. CO
2/CH
4 and CO
2/N
2 separation can be effectively accomplished using PI membranes
[25]. PI membranes possess higher permeability and selectivity than CA membranes, with a 40% area reduction and 75% improvement in CO
2 removal
[37]. However, like CA, an imide-based material called Matrimid may plasticize and undergo physical aging when applied to feed with condensable gas such as CO
2. On top of its superior performance beyond the 2008 Robeson plot, the 6FDA-PI has an elongation break, and a Young’s modulus value lower than CA. It has been hypothesized that there is a trade-off trend among gas transport and mechanical properties
[36]. Even though Pis have high performance and rigid polymer backbones, they are severely attacked by plasticization of CO
2 and trace heavy hydrocarbon components at high pressure
[42]. Some studies indicate that Pis are more susceptible to plasticization compared to CA, since they are more sensitive to structural changes resulting from their more ordered structure. To ensure acceptable membrane life, extensive pretreatment processes are needed, since it is affected by aromatic hydrocarbon even at low concentrations. It has been found that the separation performance of Matrimid 5218 reduction between single-gas testing and binary gas is larger than CA, which is 33% for CO
2 permeance and 20% for selectivity (10 mol% CO
2/90 mol% CH
4, 7.5 bar and 35 °C). In another study, when the feed pressure is increased from 5 to 50 bar, selectivity of Matrimid declined by ~45% in a 55 mol% CO
2/45 mol% CH
4 mixture
[27]. This is why CA retains its presence in the market despite its low performance, in addition to its cheaper cost
[14]. Several types of treatments such as cross-link, blending, semi-interpenetrating network, and thermal rearrangement have been performed for different PIs in order to increase the plasticization pressure
[3].
In addition to the PI membrane’s performance deterioration under mixed-gas conditions, its polymer material is relatively expensive, thus making it less attractive for commercial application
[43]. The advancement in composite spinning technology has helped in the economical production of these membranes, where it can be applied in very small amounts as a skin on top of cheaper support material
[37]. It has been stated in many works of literature that the next most potential polymer material that can be commercialized to replace the lower performance of CA membrane for gas separation is the improved and modified PI-based material. Those imides which incorporate the -6FDA group possess significantly high CO
2 permeability values
[25].
Table 2h illustrates some of 6FDA-based PIs. PIs such as 6FDA-DAM:DABA 2:1, Matrimid
®, and Ultem
® have plasticization pressures of 11, 12 and 28 bar, respectively. Torlon
® has a higher plasticization resistance, where CO
2 permeance can be maintained almost constantly up to ~84 bar, due to the establishment of N–H groups hydrogen bonding with either N–H or C=O groups
[25], as shown in
Table 2g.
2.4. Polycarbonates (PCs)
PC-based membranes are advantageous for gas removal because of their shape and size-selective properties. At severe temperature and pressure conditions, the mechanical and chemical stability of the membrane is questioned
[44]. Hence, this polymer needs to be modified. The substitution of many functional groups with aromatic hydrogens is the most-used modification method
[23]. The chemical structure of PC is shown in
Table 2i. Tetrabromo bisphenol A-PC (TB-BisA-PC) has been used for gas-separation applications by Innovative Gas Systems (IGS) or Generon. It is the most selective polymer available for air separations, with O
2/N
2 selectivity and O
2 permeability of 7.5 and 1.83 Barrer, respectively
[23]. Its four hydrogen atoms in the benzene ring are substituted in proportion by bromine atoms. The incorporation of stronger cohesive forces from polar halogens leads to more compressed packing and lessens the mobility, which is believed to be essential in polymer gas diffusion. The commercial TB-BisA-PC is anticipated to be a polyestercarbonate copolymer, where the polymer backbone comprises ester and carbonate linkages
[23]. Among the tetra-substituted PCs, TB-BisA-PC has the lowest free volume, the highest Tg, density, diffusion, and gas permeability
[23].
Based on the four main types of commercial polymers described above, each of them has its own advantages and limitations. More works need to be conducted to modify the polymers to cover and improve the limitations for more successful applications in the field with long-term stability. For CO2/CH4 removal from natural gas at high pressure, improvements needed specifically for the CA type are to improve on its selectivity and CO2 plasticisation pressure. For PSF, improvements are needed on its permeability and robustness towards heavy hydrocarbon and aromatics. For polyimides, improvements are needed on its CO2, heavy hydrocarbon, and aromatic plasticization- and aging-resistance. For polycarbonate, improvements are needed regarding its selectivity and resistance towards heavy hydrocarbons and aromatics.
2.5. Transport Mechanism for Gas Separation Membrane
There are five mechanisms of transport for gas-separation membranes, namely solution diffusion, Knudsen flow, surface diffusion, capillary condensation and molecular sieving. Solution diffusion is the one applied for dense membranes and thin skin selective layers (skin thickness between 0.1 to 1 μm) of asymmetric glassy gas-separation membranes. Diffusion happens in order to attain equilibrium, from higher concentrations to lower ones, and this leads to system entropy increases. The thermodynamic differences between the two membrane sides serve as the driving force
[37].
One parameter that associates with the variations in polymer gas transport is the FFV. This represents the open volume in polymer chains for gas molecules to pass through
[45]. Glassy membranes are used below its glass transition temperature, hence the polymer chains are improperly packed, leading to space between them
[37]. Changes in polymer structure do not consistently affect gas transport behaviour but can significantly influence solubility and diffusivity by changes in the Tg and FFV. Diffusion coefficients decrease with increasing penetrant size, while solubility is related to the condensability of the penetrant
[45]. In order to separate a component in a particular feed mixture, the polarity of one component must be close to the polarity of the membrane. Polarity is one of the polymer properties that contributes considerably to the membrane separation performance specifically via solubility factor, which is very dependent on the nature of the polymer
[37].
Gas solubility within the rubbery polymer matrix, follows Henry’s Law and is linearly proportional to the partial pressure, or fugacity. Dual-mode models and partial/total immobilization models represent the gas transport behaviour in glassy polymers below Tg
[37]. The dual-mode sorption parameters relate to several factors, namely the Tg, FFV and gas permeability, which is the diffusivity and solubility. The free volume is related to nonequilibrium structure existing in the polymer, formed during the membrane fabrication. As the temperature is increased, the excess free volume which is in the nonequilibrium state increases, and the Tg increases. The higher the free volume, the higher the gas solubility for the particular polymer and the higher Tg, and the solubility of condensable gas also increases exponentially
[46]. At low vapour activity, dual-mode sorption occurs, where hydrocarbons are adsorbed into the polymer matrix. At more than 0.5 vapour activity, higher permeability has been found to be related to dilation and plasticisation of the polymer. Plasticisation has been found to happen at the particular plasticizer amount for specific polymers. The reduction in gas permeability might initially be partially due to “pore blocking”, “competitive sorption” or “anti-plasticisation” phenomenon, where the free space is occupied by hydrocarbon and aromatics such as toluene, which obstruct the flow path
[29]. In the partial immobilization model, it was assumed that not all gas molecules sorbed are mobile and contribute to the gas transport. This model also includes the term to account for competitive sorption
[47].
Advanced dual-mode sorption models such as the Flory–Huggins and Guggenheim–Andersonde–Boer model have been established
[29]. The simplistic membrane model that does not account for such complex effects can deviate more than 20% from a more rigorous approach. Miandoab et al.
[47] has developed a mathematical model for membrane performance that incorporates fugacity-dependent permeabilities, competitive sorption, penetrant blocking and plasticization effects. The model also considers nonisothermal operation and includes real gas behaviour and concentration polarization. Importantly, the model simultaneously considers plasticization caused by water vapor (H
2O) and carbon dioxide (CO
2).
Temperature and pressure significantly affect the gas transport behaviour in polymers. By increasing pressure, the solubility will also increase, while opposite effect is seen when the temperature is increased. Diffusivity for noninteracting, low-sorbing gases is largely independent of pressure, while for highly sorbing gases, the diffusivity is dependent on pressure
[45]. The factors affecting the gas-separation membrane transport, including the gas and polymer properties with the operating conditions, should be carefully evaluated to attain stable performance of polymeric membranes for real applications.
This entry is adapted from the peer-reviewed paper 10.3390/membranes12010071