Capsule-based dry powder inhalers (cDPI) use a hard capsule that contains a powder formulation which consists of a mixture of a micronized drug and a carrier usually the lactose, known for its good lung tolerance. The capsule is either inserted into the device during manufacturer or by the patient prior to use. After perforating, opening or cut the capsule in the device, patients take a deep and rapid breath to inhale the powder, using air as the vector of drug displacement. The system is simple, relatively cheap and characterized by a lower carbon footprint than that of pressurized metered dose inhalers.
1. Introduction
Pressurized metered-dose inhalers (pMDIs), dry powder inhalers (DPIs) and nebulizers are the main categories of inhaled drug delivery systems, each class with its unique strengths and weaknesses
[1]. This classification is based on the physical state of the formulation as well as on the type of device used to meter, deliver and aerosolise the dose of product to the lungs. pMDIs and DPIs, containing a suspended or dissolved drug in a propellant or a drug as in dry powder form, are the most widely used drug delivery systems for lung disease treatment. The delivery of pharmacological agents by inhalation is a critical issue in obstructive airway diseases such as asthma and Chronic Obstructive Pulmonary Disease (COPD).
The development of the first commercially available inhaler, in the form of a pMDI, dates back to 1956. Although this was an innovation for the therapy of pulmonary diseases, concerns arose around the 1970s when the contribution of chlorofluorocarbon (CFC) propellants to the depletion of the ozone layer led to their substitution by more environmentally friendly hydrofluoroalkane (HFA) gases, still used nowadays
[2]. These inhalers generate a drug aerosol upon actuation and the drug is suspended or solubilized in the propellant. In the case of suspension pMDIs, the high variability and inconsistency of the emitted dose when the inhalers are not shaken properly suggest the importance of following the leaflet instructions and of training the patient on this topic
[3]. Moreover, the coordination between the device actuation and inhalation is a key element for the efficacy of particle deposition in the lung and for the overall disease treatment.
With the aim of overcoming pMDI limitations, DPIs were developed and for the first time placed on the market in the late 1960s, when Fisons (Ipswich, UK) developed the Spinhaler
® device, which used two pins to create opposing holes in the sidewall of the body of a gelatin capsule loading the powder dose
[4]. Subsequent DPIs have used either pairs of pins, to make single holes in the sidewalls (HandiHaler
®, Boehringer Ingelheim, Germany) or in the domed ends (RS01
® Plastiape, Lecco, Italy; Breezhaler
® Novartis, Basel, Switzerland; Turbospin
® PH&T, Milan, Italy), or two sets of four pins (RS00 Plastiape, Lecco, Italy; Aerolizer
® Novartis, Basel, Switzerland), to make multiple holes in both domed body and cap. In each of these devices, the insertion of the needle into the capsule wall is a manual mechanical process controlled by the patient. Alongside the puncture mechanism, the separation of the body from the capsule cap has also been proposed for opening the capsule (Twister
® Aptar, Crystal Lake, IL, USA, Rotahaler
® Cipla, Mumbai, India) as well as cutting the capsule with a blade (PowdAir
®, H&T Presspart, Blackburn, UK).
Figure 1 illustrates cDPIs with different capsule opening and piercing mechanisms.
Figure 1. Different types of capsule-based dry powder inhalers with corresponding capsule perforation or opening mechanism; from the top: RS01, HandiHaler, Podhaler and Twister.
Once the contents of the capsule have been made available for its release, the patient’s inhalation act generates turbulent air flows in the inhaler, which cause the capsule to move and release the powder contained therein. Around the 1980s, the Italian company ISF was the first to patent an inhalation device that caused the capsule to rotate around its minor axis
[5]. To date, this spinning mechanism is still the most efficient in releasing and deaggregating the powder that leaves the capsule driven by centrifugal force
[6]. This capsule movement was then included in improved Plastiape devices and in some developed later by other companies.
DPIs are mainly used in the treatment of respiratory diseases such as asthma, COPD and, more recently, cystic fibrosis. The active medicament as a dry powder is delivered using a device that enables its aerosolization in a suitable aerodynamic size for lung deposition (less than 5 microns) and an adequate delivery to the lung. Currently commercially available DPIs are passive devices since they rely on the patient’s inspiratory effort to provide the required energy to overcome the interparticle forces; few DPIs are active devices since they use other sources of energy. Because DPIs breath-actuated devices, the need to synchronize the actuation with inspiration is eliminated. However, DPIs show a device-specific airflow resistance, and this often demands a relatively high inspiratory effort, which might be a hurdle for patient with severe asthma or chronic obstructive pulmonary diseases, the elderly or the very young
[7]. Therefore, the performance of each DPI can be affected by the patient’s inspiratory flow, and the turbulence produced inside the device, which uniquely depends on the technical characteristics of the device.
2. Types of Dry Powder Inhalers
DPI devices vary widely in design and can be classified as single-unit and multi-unit types of devices. In a single-unit dose inhaler DPI, the powder is loaded in a mono-dose compartment as a cartridge, or more commonly as a hard capsule. This category can be classified into three groups by the method by which the capsule shell is opened to release the powder: puncturing with needles, cutting with blades or detaching the cap from the body of the capsule. The first two can be further sub-divided by the number and types of the pins and blades used. The majority of DPIs in use today use sets of either two or eight pins to penetrate the capsule shell wall. During the aerosolization, airflow streams enter via appropriate device inlets in the capsule chamber. In this way, under the inhalation airflow, the capsule starts moving and the powder is released through the pierced holes. The size 3 capsule is the size most used in the pharmaceutical industry for the development of capsule-based DPIs; however, hydroxypropyl methylcellulose (HPMC) capsules of larger volume were recently investigated for their ability to deliver a high powder dose (120 mg) of tobramycin during a succession of inhalations
[8].
Critical elements in capsule-based DPI efficiency are the choice of an appropriate device, formulation expertise, technology for precision encapsulation and optimum packaging. The capsules are opened by puncturing with needles, detaching the cup from the body of the capsule or cutting by thin blades in the device to release the powder formulation upon inspiration. Capsules pierced by needles must be capable of being punctured efficiently, without cracking and losing fragments. Depending upon the design, capsules may be rotated laterally or axially in a symmetric airstream to facilitate the release of the drug to the patient. Specific attributes and characteristics are required for the successful administration to the lungs of inhalation therapies by capsule-based DPIs. Powder emission from cDPIs is affected by intrinsic resistance of the device, capsule opening and motion such as rotation, shaking and vibration. Hole size, and the capsule chamber volume may also influence the performance of the product. The inspiratory flow necessary to achieve a therapeutic effect is critical with DPIs; however, most patients with severe respiratory diseases have a weak inspiration flow. For this reason, the good practice of making two separate inhalations from the same dose is often recommended to ensure the inhalation of the whole of the dose
[9]. Despite this inconvenience, capsule-based inhalers have a very positive response at low flow rates.
All currently available passive DPI systems are driven solely by patient’s inspiratory effort to disperse drug powders. Airflow through the device creates shear and turbulence; when the patient activates the DPI and inhales, air enters into the powder bed, which is fluidized and directed to the patient’s airways. Drug particles are then separated from the carrier particles: the former are carried deep into the lungs, while the latter impact in the oropharynx and are cleared
[10]. Different DPIs have different intrinsic inhalation resistances that govern the resulting peak inhalation flow generated by the patient. This implies that a threshold inspiratory force is required to aerosolize, de-agglomerate and disperse the powder formulation and to achieve an effective drug deposition. The specific resistance to inhalation of each depends of the physical design of the device and is measured as the square root of the pressure drop across the device divided by the flow rate through the device. The current DPI designs have airflow resistance values ranging from about 0.02 to 0.07
[11]. To produce a fine powder aerosol with increased delivery to the lung, DPIs with low, medium or high intrinsic resistance require inspiratory flows of >90 L/min, 50–60 L/min and <50 L/min, respectively. Notably, due to the increased pressure drop across the device, high resistance DPIs tend to produce a greater lung deposition than those with low intrinsic resistance
[11]. Namely, the increase in resistance means that low air flow rates are reached inside the inhaler, and this leads to particles which, given their relative low speed, are less subject to impact mechanisms in the upper airways.
The Breezhaler device is an example of a capsule-based DPI characterized by a low internal airflow resistance with a value of 0.02
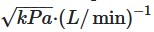
. Because of its low intrinsic resistance, it requires high inspiratory flow rates (100 L/min) to obtain a 4 kPa pressure drop. The flow rate values that are precisely established to standardize the in vitro characterizations of the devices are not always achieved in real life. However, an efficient device must be able to maintain the predetermined performance even at flow rate values around the optimal range. In this regard, Breezhaler delivered consistent doses even to COPD patients who generated a peak inspiratory airflow of approximately 90 L/min through the device
[12][13]. In general, patients prefer DPIs with low resistance to those with high resistance
[14]. In addition, Janssens et al.
[15] have shown that, irrespective of the presence of airway obstruction, 30% and 12.5% of an elderly population were not able to reach the minimum peak inspiratory flow of 45 L/min when using the medium- to high-resistance Turbuhaler DPI and the low-resistance capsule-based DPI Aerolizer. Keeping this in mind, patients would benefit the choice of low resistance DPIs, which are relatively insensitive to variations in peak inspiratory flow at low flow levels about 40–50 L/min. The ERS/ISAM taskforce on inhalers
[16] recommends patients “
to inhale forcefully from the beginning of inspiration, as deeply as possible, and to continue to inhale for as long as possible”. Indeed, with a DPI, forceful inhalation disperses the micronized drug from the lactose-based carrier into a fine particle dose. The turbulence of the air flow generated in the device is directly related to the resistance of the inhaler and to the flow rate generated by the patient's inhalation act. Turbulence is the driving factor for the deaggregation of the powder and the generation of the fine particle dose.
The higher the airflow, the higher the powder dispersion generating a fine particulate, although high airflow may lead to a higher deposition of the powdered drug in the large airways and, as a result, to a lower dose in small airways
[11]. On the other hand, low airflow increase deeper lung deposition of the powdered drug, although too low an airflow (such as that occurring in patients with severe airway obstruction) can limit deposition by affecting powder disaggregation and dispersion
[11].
Multi-unit DPIs deliver single doses from pre-metered blisters, disks, or tubes. Multiple-dose DPIs have a reservoir that contains a bulk amount of powder formulation and a mechanism to meter and deliver a single dose with each actuation by the patient
[17]. The dose is ready for its extraction by the activation of the device, which requires few maneuvers by the patient. It is agreed that the simpler the device, the lower the risk of error during use. Capsule-based DPIs require that single doses are individually loaded into the inhaler immediately before use, a maneuver potentially inconvenient for some patients and that does not allow direct counting of the remaining doses.
Then, the powder content of the capsule must be made available for release by a second patient maneuver: by pressing specific buttons on the device, the capsule shell is perforated or opened. Hence, the inhalation process must be continued or repeated until the capsule is emptied depending on the patient’s breathing profile. This maneuver may result in under-dosing and high dose variability. In addition, properly loading the cDPIs requires a sequence of steps that may not be easy for children or for elderly patients with reduced dexterity. In contrast, a study on usability of the cDPI Breezhaler has shown that patients found the device comfortable and easy to use and were confident of the medication being taken correctly when using the device
[18]; however, the methodology to assess preference and satisfaction for an inhaler was assessed for a limited time interval by means of a non-validated methodology. Asthma and COPD patients
[19][20] displayed no or fewer errors when using multiple-dose DPIs, such as the Ellipta, which require three steps to take the medication compared to the capsule-based DPI Handihaler or Breezhaler, which require eight steps to inhale the medication. These findings suggest that a DPI with a more intuitive design and requiring fewer steps to take the medication could be suitable for most patients.
Whatever the type, the DPI is more complex than the conventional dosage forms; it is a combined delivery system where its overall clinical performance is affected by its three main players: the patient, the formulation and the device. For this reason, in the pharma sector, the development of this type of product has moved away from the traditional Quality by Testing towards the Quality by Design approach, by which the only way to assure the quality of a product is by controlling its manufacturing process
[21][22].
3. Formulation Aspects of DPI
The device and formulation must be compatible so that the formulation is easily delivered to the patient’s lungs. The formulation for DPIs usually consists of the API alone or the micronized API and an inert carrier such as lactose or mannitol. DPI formulation needs to be easily emitted from the device; it is important that it remains free flowing from the manufacture stage to the inhalation by the patient. For these natures of blends, the relationship between the formulation and the device is very important and the properties of the capsule are essential. DPI formulations tend to have a hygroscopic characteristic and the presence of moisture can potentially cause a change in powder flow properties. In this respect, a primary packaging capable of protecting the API, formulation and device from environmental humidity is required. Usually, inhalation capsules are packaged in blisters due to the high protection of this packaging. However, in some markets, inhalation capsules are packaged in 30 single-unit pill containers (for example Rotacaps (Cipla, Mumbai, India). On the other hand, when the powder tends to degrade or decompose easily, blisters that contain aluminum both in the plastic part of the cavities and in the lidding sheet are used. Insulin spray-dried powder showed to maintain good aerodynamic performance when filled in HPMC capsules and packaged Alu-Alu blister up to 6 months at room temperature conditions
[23]. These findings open up the possibility to administer the daily therapy of diabetic patients without the need to refrigerate the product.
One advantage of the use of hard gelatin capsules is the higher potential for oxidation in HPMC capsules than in hard gelatin capsules. Hard gelatin capsules have demonstrated excellent protection against oxygen in comparison with HPMC material. Although powder formulations are less of a concern in this respect, the formulator can easily overcome the issue by choosing the right packaging to protect the powder from oxygen
[24].
For both types of capsules that are chosen, it is always recommended that chemical compatibility between the API, excipients and the capsule be established as a first step to ensuring a promising formulation.
4. Capsule for Inhalation: Composition and Production Aspects
There are two choices in capsule polymers that can be used for DPI formulations: hard gelatin capsules or HPMC capsules. Figure 2 shows the step of capsule process production, described here for the two types of material employed.
Figure 2. Capsule process production (courtesy supplied by Qualicaps).
In the specific case of inhalation therapy, the capsule dissolution or disintegration test are not critical attributes. Further specifications such as moisture diffusion and permeability, physical and mechanical performance in a puncturing or cutting action or lubricant content on the inner surface should be evaluated. Finally, capsules for inhalation need a more stringent microbiological specification than that of standard oral capsules because their contents are directly inhaled into the lungs. The acceptance criterion based upon the total aerobic microbial count (TAMC) is <100 CFU/g according to Ph.Eur. 10th Edition.
Gelatin and HPMC are different with respect to their chemical and physical attributes, and the choice between the materials is ultimately based on the least amount of interaction between the formulation and capsule shell. Table 1 reports a list of commercial products where the powder dose is packaged with gelatin or HPMC capsules. Several sets of single or combined therapies for asthma or CPD are available, such as long-acting beta (2) agonist (LABA)/long-acting muscarinic antagonist (LAMA), LABA/inhaled chorticosteroids (ICS) or the recently approved Enerzair (Novartis) triple combination LABA/LAMA/ICS.
Table 1. Currently marketed single-dose capsule-based DPIs. The list is organized in alphabetical order according to the marketed device employed for product aerosolization.
Device
|
Company
|
Commercial Product Name
(Drug Delivered)
|
Type of Capsule
|
Aerolizer®
|
Novartis
|
Foradil (FF)
Foradil Combi (FF, SS)
Miflonide (BUD)
|
Gelatin
|
Breezhaler®
|
Novartis
|
Atectura (IDC, MF)
Enerzair (IDC, GPB, MF)
Miflonide (BUD)
Onbrez (IDC)
Seebri (GPB)
Ultibro (IDC, GPB)
|
HPMC
HPMC
Gelatin
Gelatin
Gelatin
HPMC
|
Handihaler®
|
Boehringer Ingelheim
|
Spiriva (TB)
|
Gelatin
|
Podhaler®
|
Mylan
|
TOBI (Tobramycin)
|
HPMC
|
Powdair®
|
H&T Presspart
|
Ventofor Combi Fix (BUD) (FF)
|
Gelatin
|
Rotahaler®
|
Cipla
|
Asthalin (SS)
Budecort (BUD)
Duolin (LS-IPB)
Duova (TB, FF)
Foracort (FF, BUD)
Levolin (LS)
Seroflo (SX FP)
Triohale (ciclesonide, FF, TB)
|
-
-
Gelatin
Gelatin
Gelatin
Gelatin
Gelatin
Gelatin
|
RS00
|
Kleva
|
Forcap (FF)
|
Gelatin
|
Zentiva
|
Formolich (FF)
|
Italchimici
|
Kurovent (FF)
|
RS01®
|
Adamem
|
Zafiron (FF)
Fluxiton (FP)
|
Gelatin
HPMC
|
Allertec Hellas
|
Formaxa (FF)
|
Gelatin
|
Baush Health
|
Forastmin (FF)
|
HPMC
|
Chiesi Farmaceutici
|
Bronchitol (Mannitol)
|
Gelatin
|
Deva
|
Brontio (TB)
Foterol (FF)
Foterol-B (FF, BDP)
Respiro (FP, SX)
Rolasym (FF, BUD)
Sebraler (GPB)
|
Gelatin
|
Exeltis
|
Fludalt Duo (FP, SX)
Tioumit (TB)
|
HPMC
Gelatin
|
Galephar Nederland
|
Busalair (BUD, SX)
|
Gelatin
|
Lek-Am
|
Pulmoterol (SX)
|
Gelatin
|
Lupin
|
Budamate Forte (FF, BUD)
Budate (BUD)
Duomate (FF, BDP)
Esiflo (FP, SX)
Formoflo (FF, FP)
Lupinhaler (TB)
Salbair (LS)
Salbair-I (LS, IB)
|
Gelatin
|
Polpharma
|
Oxodil (FF)
|
HPMC
|
Stada
|
Formoterol (FF)
|
HPMC
|
Spinhaler®
|
Aventis
|
Sodium cromoglycate
|
Gelatin
|
Turbospin®
|
Teva
|
Colobreathe (colistimethate sodium)
|
Gelatin
|
Twister®
|
Shanghai Sine Promod Pharmaceutical
|
Budesonide DPI
|
-
|
Zonda®
|
Teva
|
Braltus (TB)
|
HPMC
|
BDP: Beclomethasone dipropionate; BUD: Budesonide; FF: Formoterol fumarate; FP: Fluticasone propionate; GPB: Glycopirronium bromide; IDC: Indacaterol maleate; IP: Ipratropium bromide; LS: Levosalbutamol; MF: Mometasone furoate; SS: Salbutamol sulphate; SX: Salmeterol xinafoate, TB: Tiotropium bromide.
This entry is adapted from the peer-reviewed paper 10.3390/pharmaceutics13111936