Fossil free future for track work machinery indicates the possibility of achieving zero direct emissions during maintenance and construction work in railways by switching to alternative drives. Current railway track work machinery is mainly operated with diesel fuel. As a result, track maintenance of Austrian Federal Railways (OeBB) amounts to nearly 9000 t CO2 equivalent per year according to calculations from Graz University of Technology. OeBB’s total length of railway lines only accounts for 0.56% of the world’s length of lines. This indicates huge potential for mitigating greenhouse gas emissions considering the need for track maintenance worldwide. Environmental concerns have led to the introduction of alternative drives in the transport sector.
1. Introduction
In regard to climate change, anthropogenic CO
2 emissions play a crucial role. In order to limit a further rise in temperature, global goals to reduce greenhouse gas emissions (GHG) were defined in the Paris Agreement [
1]. The European Green Deal should help achieve these goals and serves as a roadmap for creating a sustainable, competitive economy with the goal of reducing net greenhouse gas emissions to zero by 2050 [
2].
Today, 94% of the energy required for the European Union’s (EU) transport sector still originates from oil resources [
3]. Globally, the transport sector is responsible for around one quarter of CO
2 emissions from fuel combustion, (wherein rail accounts for 4.2%), another 38.4% arises from the energy industry’s own use, commercial and public services, residential and others, and the remaining 36.9% originates from manufacturing industries and construction [
4].
In 2009, an analysis of 40 countries showed that the global construction industry was responsible for 23% of the world’s CO
2 emissions across its entire supply chain [
5]. Around 6% of the 23% are direct emissions from activities on construction sites, predominantly through the combustion of fossil fuels (mainly gasoline, diesel, other petroleum products, and light fuel oil) to power machinery and equipment. The remaining 94% are indirect emissions (e.g., energy needed for the provision of products). In the European Union, the share of national GHG emissions from construction non-road mobile machinery (NRMM) amounts to 1.06% on average [
6]. In 2007, 2% of the total CO
2 emissions from transport in the European Union originated from construction equipment [
7].
The share of GHG emissions of railway track work machinery is considered neither in statistics from the transport nor the construction sector. However, this sector should not be neglected. Current track work machinery is predominantly powered by diesel engines. As a result, track maintenance of the Austrian Federal Railways (OeBB) amounts to more than 8800 t CO2 equivalent per year (Figure 1) according to calculations from the Institute of Railway Engineering and Transport Economy (Graz University of Technology).
Figure 1. GHG emissions of track maintenance of Austrian Federal Railways per km (
a) and per year (
b) according to calculations from the Institute of Railway Engineering and Transport Economy (Graz University of Technology).
The comparison of GHG of different track work (Figure 1a) shows that formation rehabilitation and ballast-cleaning machines have the highest impact per kilometer by far. Ballast-cleaning machines, for example, excavate the whole ballast bed, clean as much ballast as possible for on-site reuse, and add new ballast to renew the ballast bed completely. Thus, these machines are heavy, fuel intensive, and are slower in their working progress compared to other types of track work machinery.
In terms of annual GHG emissions (
Figure 1b), tamping (including dynamic track stabilizing and a share of tamping of turnouts which is performed with track-bound work machinery) has the highest environmental impact. This is because tamping is by far the most frequently executed track work in Austria, with approximately 1000 km per year being done. Since this calculation does not consider conventional tamping of turnouts, it can be assumed that GHG emissions are even higher. Based on OeBB’s overall passenger transport in 2019 [
8] and specific emission values for different modes of transport in Austria [
9], the following can be concluded: Austrian Federal Railways’ annual track maintenance corresponds to roughly 6.1% of the overall passenger transport emissions for 2019, which is equivalent to approximately 50 million km of direct car emissions or to direct emissions from 35,000 short distance flights. Moreover, the OeBB’s total length of railway lines only accounts for 0.56% of the length of lines of the world’s railway network [
10]. Since track work trains operate in most countries around the world, this indicates that there is huge potential for mitigating GHG emissions.
Currently, various regulations applicable to diesel engine emissions to reduce pollutant emissions (i.e., carbon monoxide, hydrocarbons, NOx, PM) are in place around the world, some of which have been harmonized [
11]. Although diesel drives have come under pressure, it is assumed that they will continue to be used in sectors such as railways [
12]. On the contrary, local driving bans for diesel vehicles that might be imposed in the future could change tender conditions [
13]. Furthermore, policies, political incentives, action plans and roadmaps have been introduced and (governmental) funds for scientific research have been received throughout the last decade in different regions worldwide. They aim to achieve the decarbonization of the transport sector and implementation of alternative propulsion technologies in order to ensure sustainable mobility in the future. These alternative solutions for conventional fossil fuels range from electrification over hydrogen-based solutions to gaseous fuels and biofuels to synthetic fuels.
In contrast to the transport sector, sustainable goals in the construction sector are less clear [
6]. However, governments and stakeholders are increasingly aware of the pollution and emissions caused by the sector. Green procurement in the construction sector is being increasingly emphasized [
14]. In order to have more sustainable construction sites, some countries are introducing legislative measures [
15,
16], and the industry is also taking the initiative [
17,
18].
Explicit decarbonization strategies developed by European governments or railways reflect the consciousness of reducing the environmental impact in the rail sector [
12,
19,
20,
21,
22,
23,
24,
25,
26]. Most of these strategies aim to substitute diesel traction within the next 15 to 20 years. It is noteworthy that Norway and Switzerland have also set goals for track work construction machinery [
23,
24].
In sum, the environmental impact of track work machinery is not to be neglected, neither in the rail nor in the construction sector. Procurements aiming to reduce carbon emissions or emission targets have an impact on the introduction of alternative drives. The vote on the EU climate law in October 2020 will probably lead to even more ambitious targets [
27]. Considering climate targets set by decision-makers, it can be assumed that demand for zero emission rail vehicles and construction machinery will rise in the future, and that track work machinery will be subject to more stringent regulations in the near future as well. As track work trains are fuel-intensive, decarbonization could lead to the essential mitigation of environmental impacts, thus contributing to an ecological railway system.
2. Literature Review
2.1. Status Quo of Track Work Machinery
Track work trains operated in most countries around the world are predominantly powered by diesel engines. GHG emissions due to fuel combustion of track work machinery are not included in current environmental statistics of the transport or construction sector and are widely ignored in environmental strategies. Decarbonization goals so far exist only in Norway and Switzerland [
23,
24]. Alternative propulsion technology in the sector of track work machinery is limited to a few models (
Table 1).
Table 1. Overview of alternative powered track work machinery.
|
Manufacturer |
Models |
Power Source |
Status-Quo |
Source |
Machines |
Geismar |
VMB-E (similar to MTW of P&T) |
battery or catenary |
offered in website portfolio |
[28] |
Geismar |
V2R-CGR maintenance vehicle |
diesel-battery |
offered in website portfolio |
[28] |
Harsco |
Utility Track Vehicle (UTV) |
catenary-battery |
framework contract to supply vehicles for DB |
[29] |
Linsinger |
Rail milling train |
fuel cell |
|
[30] |
Plasser & Theurer |
BDS 2000 E3 |
diesel-catenary |
First-ever hybrid track work machinery, in operation at work sites in Switzerland and Austria |
[31,32] |
Plasser & Theurer |
09-4 × E3 Dynamic Tamping Express |
diesel-catenary |
Plasser & Theurer |
HTW 100 E3 |
diesel-battery |
first-ever battery powered vehicle in the industry (2017) |
[31,32,33] |
Plasser & Theurer |
Unimat 09-32/4S Dynamic E3 |
diesel-catenary |
in operation at work sites in Austria |
[31] |
Plasser & Theurer |
Unimat 09-4 × 4/4S E3 |
diesel-catenary |
Railcare |
Multi-Purpose Vehicle |
battery |
recently unveiled for operation in Sweden |
[34,35] |
Windhoff |
Rail transport wagon |
not yet defined (battery or fuel cell) |
contract to deliver three dual power vehicles |
[36] |
Tools |
Geismar |
Battery-Powered Portable Tamper |
battery |
|
[28] |
Geismar |
Battery-Powered Abrasive Rail Saw |
battery |
|
[28] |
Robel |
Rail Drilling Machine |
battery |
first prototypes showcase In-House Exhibition in 09/2019 |
[37] |
Robel |
Rail Band Saw |
battery |
Robel |
Impact Wrench |
battery |
Robel |
Vertical Tamper |
battery |
Robel |
Rail Cutter |
battery |
Robel |
Rail loading system |
supercapacitor |
prototype presentation at IAF 2017 |
[38] |
Up to now, alternative solutions for track work machinery are mostly hybrid systems rather than stand-alone solutions. Smaller (lighter) track maintenance tools (e.g., portable tampers), which run on battery power alone are an exception to the above. Despite the fact that manufacturing companies are increasingly developing machinery with alternative propulsion systems, the variety of products is small compared to the amount of different track work machinery that exists.
Track Work Machinery Compared to Other Modes of Transport
Track work machinery are tailor-made products. Additionally, the lack of interoperability in railways (e.g., different railway electrification systems) and the fact that track work machinery operates in different countries around the world complicates the application of one single alternative propulsion solution. Some machinery (e.g., welding machines) require peak power for a very short time, while others work on continuous power. The fact that duty cycles and operation patterns distinguish between different types of machinery is also valid for NRMM, as reviewed by Lajunen [
39] and influences the choice of the alternative drive solution. Furthermore, track work machinery shows huge differences in working power. Installed nominal power of different machine types from Plasser & Theurer ranges from less than 100 kW for material logistics like MFS 100 to above 2000 kW required by RU800S used for track renewal and ballast bed cleaning [
40]. It can be concluded that the power range of track work machinery lies within the area of several modes of transport (
Figure 2). Thus, it requires a cross-market analysis to understand the opportunities and challenges of a specific alternative propulsion technology and learn from the trends and experience of other modes of transport.
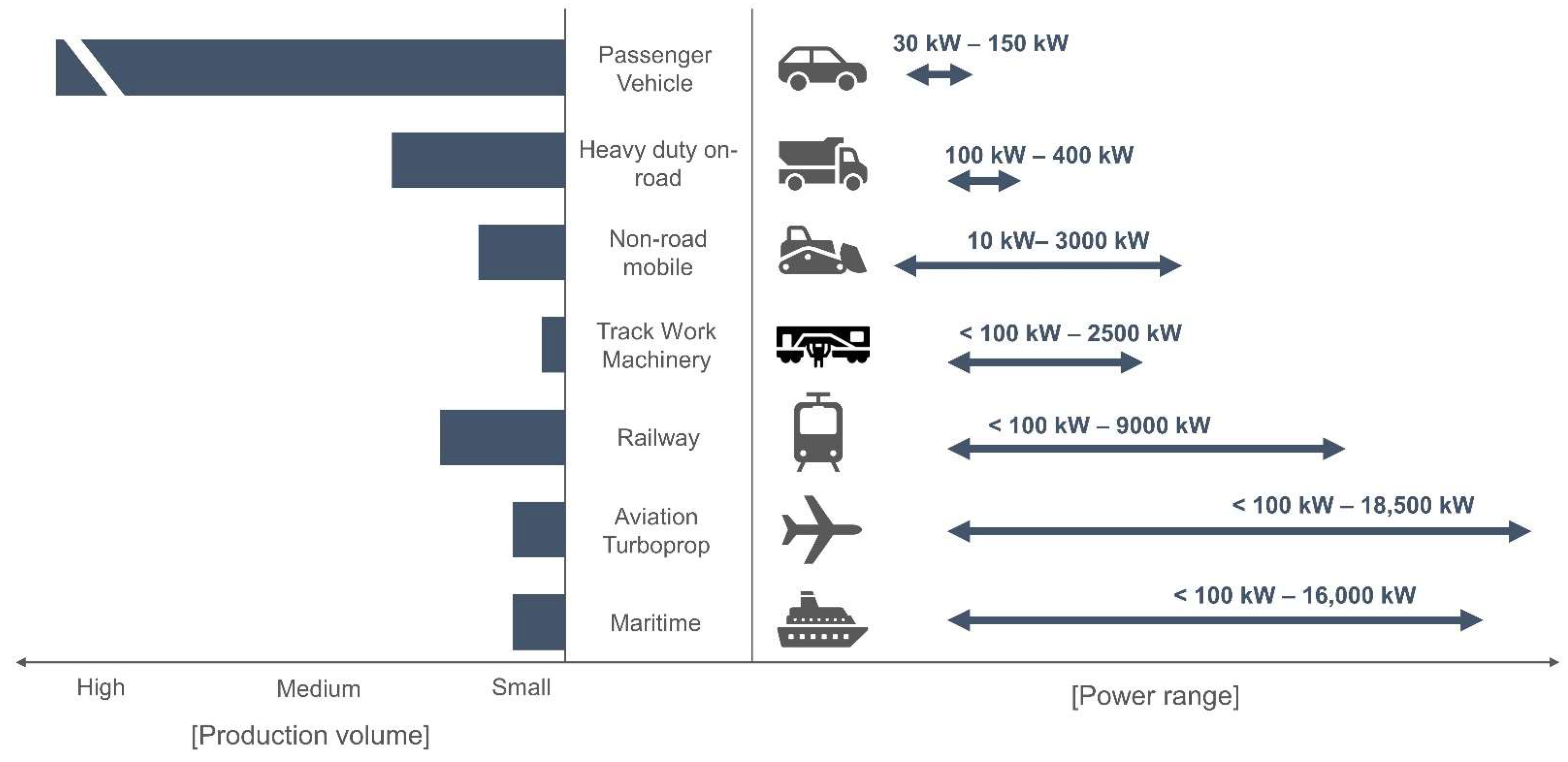
Figure 2. Power range and production volume of different modes of transport based on information from various sources [
39,
41,
42,
43,
44,
45,
46,
47].
Track work machinery is a niche product. The literature does not refer to it specifically and it is unclear whether it is assigned to the rail or the construction sector. Today, the majority of diesel locomotives are diesel-electric [
48], while construction machinery (like track work machinery) is mostly diesel-hydrostatic or diesel-hydrodynamic [
49]. Thus, the technological concepts for powertrains and transmissions used in the construction sector could be applied to track work machinery. Regarding the primary power source, track work machinery is highly influenced by market trends in the rail sector. This is because implementing alternative solutions depends on the infrastructure for supplying energy (e.g., charging or refueling). Therefore, a special focus must be put on rail vehicles and construction machinery.
2.2. Overview of Alternative Propulsion Technologies
Today, there is a strong trend towards electrification via on-board energy storage systems (ESS) using batteries. The automotive sector, in particular, drives battery technology development in the passenger transportation sector [
50]. In the public transportation sector, electrification has been state-of-the-art (e.g., in rail transport: overhead catenary, third rail) for decades.
In addition to batteries, fuel cells also allow for electrification of vehicles. Hydrogen is very well suited for electricity generation with fuel cells (FC)—in fuel cell electric vehicles (FCEV), hydrogen usually combines with oxygen in a fuel cell, consequently generating electricity that powers an electric motor [
51]. Just like batteries they can provide propulsive power or work as a range-extender [
52].
Lithium-ion (li-ion) battery technologies, namely LMO (lithium-manganese-oxide), LFP (lithium-iron-phosphate), NCA (lithium-nickel-cobalt-aluminum-oxide) and NMC (lithium-nickel-manganese-cobalt-oxide), as well as conventional lead-acid and nickel-metal hybrid batteries are the dominant battery technologies in the field of passenger vehicles [
50,
51,
52,
53]. LFP are also popular in buses [
54]. However, current automotive technology is not fully transferable to other sectors, notably due to technical properties [
55,
56,
57]. For instance, ESS in the rail sector face high requirements in terms of ambient temperature [
13], specific energy/energy density which influence on-board weight/space [
58,
59], as well as safety and approval regulations (e.g., fire protection, tunnel safety) [
13,
60,
61].
According to the
alternative drive rail data pool, the dominating battery technology in railway vehicles is li-ion based, notably NMC, LFP, or LTO (lithium-titanate). Nickel-cadmium and lead-acid batteries are also used but less common. NCA technology, which is popular in the automotive sector, has not been identified for any railway project. It is assumed that this is due to currently used li-ion technology in railways which perform better in terms of safety than NCA [
62]. NMC batteries offer high energy density and high specific energy as opposed to LFP and LTO [
62]. LFP and LTO outperform NMC in terms of thermal stability [
62]. A top advantage of LFP is its low cost [
40].
Battery technologies for excavators, wheel and underground loaders comprise NMC [
63,
64,
65,
66], Nano-NMC [
67,
68], LFP [
65,
66,
67,
68,
69], NCA [
67] and LTO batteries [
66,
67,
68,
69,
70]. Battery technology, specifically for heavier machinery—similar to heavy-duty on-road vehicles—still requires further development [
71].
According to the information from currently available trainsets, characteristics of hybrid components show the following: Fuel cell trains with a traction power of 380–700 kW require a fuel cell power range from 130 to 400 kW and battery capacity from 20 to 240 kWh. Similar information can be found in the literature [
13], where the maximum power of fuel cells is 500 kW for freight and passenger trains, and maximum battery capacity is 310 kWh. For construction machinery, battery capacity varies with machinery type. Battery capacity in small excavators (<7 t) ranges from 20 to 60 kWh [
63,
67,
72,
73]. Standard excavators (7 t < 45 t) require a higher capacity, but usually less than 300 kWh [
64,
69,
73,
74].
Gaseous fuels represent a further development of conventional fuels and can be used in internal combustion engines (ICE) [
75]. One type is liquefied petroleum gas (LPG) which “is obtained during natural gas and oil extraction, or as a by-product of being manufactured during the refining of petroleum” [
75]. When obtained from fossil fuels (natural gas), they come in form of CNG (compressed natural gas) or LNG (liquefied natural gas), [
76]. Bio-derived alternatives are sourced from renewables or feedstock through different processes (anaerobic digestion, gasification or through methanization of hydrogen made via electrolysis) [
77]. Alternative fuels like biodiesel or ethanol are known as biofuels and produced from biomass [
78].
Another substitute for diesel are the so-called synfuels—they are specifically designed and can be produced from renewable sources [
79]. They can be obtained from different sources, such as natural gas (Gas to Liquid, GtL), biomass (Biomass to Liquid, BtL), vegetable oils and fats (Hydrogenated Vegetable Oil, HVO) or through the conversion of hydrogen to hydrogen-based fuels, like synthetic methane or ammonia [
80,
81].
2.3. Consolidation and Comparison
It can be observed that all modes of transport are committed to reducing emissions and are increasingly considering alternative propulsion technologies. Experience from the rail and construction sector can thus be partly transferred to track work machinery.
In comparison to the rail sector, battery-electric only technology is much more established in the construction sector, but limited to electric construction machinery with cables, handheld equipment, or smaller machines. By contrast, fuel cell technology is at a very early stage of development (with the exception of forklifts). The battery range used in railways is comparable to that of heavier construction machinery, whereas Nano-NMC batteries were not able to be identified for rail vehicles. Very few models with alternative drives exist for track work machinery (Table 1). Similar to the rail sector, solutions for track work machinery tend toward bi-mode and hybrid systems rather than stand-alone solutions. Smaller (lighter) track maintenance tools, which run on battery power alone, are manufactured by Geismar and Robel (e.g., portable tampers, tools for replacing a closure rail or rail loading system).
2.3.1. Opportunities
The main advantages of electrified vehicles are their higher energy-efficiency and decreased noise pollution compared to internal combustion engines [
51]. They have zero tailpipe emissions since GHG emissions are accounted for in the production steps of electricity [
54]. A huge advantage of electrification and green energy is that less air and noise pollution is emitted at construction sites [
6]. Moreover, electric construction machinery needs less maintenance [
6] and studies on excavators show that electric machinery could have a lifetime that is 50% longer compared to diesel machinery [
106].
The opportunities of hydrogen lie in zero local emissions when used in fuel cells (waste product is water) and higher efficiency compared to ICE plus higher specific energy and higher driving ranges (over 500 km) compared to batteries [
53]. A big advantage of gaseous fuels is their possible use in established ICE and the fact that they can be transported on existing CNG and LNG refueling infrastructure [
54].
2.3.2. Challenges
A general challenge is the lack of charging and refueling infrastructure [
116]. Large-scale deployment of battery or fuel cell technology in vehicles requires specific infrastructure, e.g., hydrogen distribution logistics, refueling stations or overhaul [
117,
118]. When transferring technology from the construction sector to track work machinery, the following must be considered: track work takes place on “moving” construction sites, which complicates recharging/refueling compared to conventional construction machinery.
Another challenge is posed by the end-of-life of components, like batteries [
13,
119]. Currently, legislative measures are taken regarding recyclability/end-of-life, e.g., reviewing of Battery Directive 2006/66/EC [
51], or other similar regulative documents [
120].
Carbon intensity depends on the electricity mix of the specific country—higher efficiency in using brown energy reduces environmental impacts (e.g., exhaust cleaning), whereas the aim should be to use green energy in order to contribute to reducing the environmental impact.
An environmental challenge for hydrogen is the production process. Two thirds of today’s hydrogen production comes from natural gas [
81]. Other eco-friendlier production processes are being explored. They range from electrolysis (established alternative which however only accounts for 2% of the production process and depends on the electricity mix) to solar energy to split H
2O thermally (still at laboratory scale) and modified biomass gasification trials at Graz University of Technology [
81,
121]. A further challenge is related to space requirements for storage [
122] due to the low volumetric energy density of hydrogen [
123].
Recently, contradictory statements on GHG emissions and particulate matter (PM) have been published for gaseous fuels [
124]. Until now it was believed that they decrease emissions [
77,
125,
126]. However, recent studies state the opposite. Despite these contradictory statements, further (mid-term) use is still expected in the transport sector due to high energy densities [
103], e.g., in railways [
127,
128] or aviation [
111]. Critics fear that synfuels relocate the problem rather than present a solution, especially where a great amount of fuel is required, like in railways [
13]. This is because of energy-intensive production processes and the exploitation of resources [
80,
129]. Another challenge for synfuels is large-scale implementation with low costs and renewable energy [
79].
2.4. Summary
Solutions for alternative propulsion technologies are still in their infancy, regardless of the mode of transport. This can be attributed to the aforementioned barriers such as lack of technology verifications (insecurity for customers), limited product availability (economies of scale), lack of regulatory structures, safety and security concerns, on-board weight and space requirements, lack of infrastructure including refueling, recharging, equipment for overhaul and impacts on life cycle (resources, electricity mix, recyclability). Another barrier is the economic feasibility of the development phase [
130]. It can be assumed that these barriers will be overcome in the future, due to continuously rising tenders and procurements as well as technological progress and more stringent regulative boundary conditions.
With regard to track work machinery, the process of research and development of alternative propulsion technologies and their application has just started. While trends to certain alternative solutions in certain other transport segments can already be observed, the question as to which alternative drive solutions would be the best for track work machinery remains unsolved and depends on the type of machinery.
This entry is adapted from the peer-reviewed paper 10.3390/su132011444