Voltage surge protection devices (SPDs) or surge arresters rely on metal oxide varistors (MOVs) to safeguard electrical equipment in consumer electronics and industrial electric power systems against the destructive temporary overvoltages (TOVs) resulting from transient switching surges or lightning strikes. The primary function of voltage-sensitive MOVs in SPDs is to prevent the damage caused by high-energy transients by clamping or eliminating them when a surge occurs. These MOVs are mounted in parallel with the components that they are designed to protect.
1. Introduction
MOVs are sintered ceramic materials typically manufactured in a disc shape that resembles a right circular cylinder, although rectangular or hexagonal prism shapes with flat surfaces are reported less frequently
[1]. MOVs are complex, multicomponent systems that consist of a semiconducting oxide
[2] such as zinc (II) oxide (ZnO)
[3][4][5][6], tin (IV) oxide (SnO
2)
[7][8], or titanium (IV) dioxide (TiO
2)
[9][10] as the main component (>90 mol.%), and multiple MO additives as minor components.
The role of MO additives is to enhance the performance of MOVs through a synergistic effect
[11]. For example, Bi
2O
3 [12][13], V
2O
5 [14][15], and Pr
6O
11 [16] are varistor-forming oxides (VFOs) or nonlinearity inducers that can form solid solutions with other MOs. Varistor-enhancing dopants (VEDs) act as grain growth inhibitors and densification enhancers and are selected from rare earth oxides (REOs) such as Er
2O
3 [17][18][19], Gd
2O
3 [20], Dy
2O
3 [21], Sm
2O
3 [22], Y
2O
3 [22][23][24], La
2O
3, and CeO
2 [25], among others.
Transition element oxides (TEOs) such as Co
2O
3 [26], Co
3O
4 [27], Cr
2O
3 [5][28], NiO
[29][30], CuO
[31], MnO
[32], MnO
2 [33][34], Mn
3O
4 [24][35], Nb
2O
5 [25][36], Fe
2O
3 [37], ZrO
2 [38], WO
3 [39], and other MOs (In
2O
3 [40][41], Al
2O
3 [40], Sb
2O
3 [3][27], B
2O
3 [42], SiO
2 [43], etc.), as well as TiO
2 [44] and SnO
2 [45], are used as VEDs. However, it is a challenge to determine the distinct contribution of each MO dopant in multicomponent MOVs that exhibit complex structures
[11]. Moreover, the properties of MOVs depend on the type and content of dopants, as well as the thermal history of the MOVs.
Small-sized MOV discs (cylindrical blocks) with a diameter × height of Ø8–20 mm × 1–4 mm are typically used in voltage SPDs for high-voltage applications in consumer electronics. MOV discs of larger sizes (diameter × height of Ø20–120 mm × 20–50 mm) can be used to equip surge arresters for electric power systems with switching voltages of a few kV
[46].
MOVs display significant nonlinearity in the current–voltage (I–V) curves and the current density–electric field (J–E) curves, respectively. The main regions of the I–V curves of MOVs are as follows: (i) the prebreakdown or leakage region (I < 10 μA), (ii) the nonlinear region or normal varistor operation (10 μA < I < 1 kA), and (iii) the upturn region (I > 1 kA)
[47][48]. At low currents, MOVs can reach very high resistance (≤10 GΩ) in the leakage region, which varies with temperature and frequency. At high currents, low resistance equal to the bulk resistance of ZnO grains (1–10 Ω) can occur in the upturn region
[47][49]. In the nonlinear region (conduction mode), MOVs can achieve a high energy absorption capability. Normal varistor operation begins at a threshold or breakdown voltage (V
B) at a current of 1 mA, denoted as V
1mA, when α can reach a maximum value
[48][49][50]. An α value greater than 30 suggests good contact between ZnO grains
[49], while an α value less than 10 indicates poor boundary junctions between ZnO grains, resulting in unsatisfactory electrical (E–J) characteristics of MOVs
[49][51].
Table 1 summarizes the critical parameters and functions of MOV devices, along with several typical values of the electrical parameters.
Table 1. Critical parameters and functions of MOV devices (adapted from [52]).
Parameter
|
Function
|
Comments
|
Reference
|
Nonlinear coefficient (α)
|
Protective level
|
Typical α values in the low-current region are 20–70. The increase in temperature and pressure to which the MOV device is subjected in service causes a decrease in α values.
|
[52][53]
|
Nonlinear voltage (V)
|
Voltage rating
|
It is the threshold or breakdown voltage (VB) at a current of 1 mA. Typical EB values are in the range of 2–5 kV/cm.
|
[5][52]
|
Leakage current (IL)
|
Watt loss/operating voltage
|
DC IL values ≤ 100 μA for small-sized MOV discs, and ≤200 μA for large-sized MOV discs equipping electric power and telecommunication SPDs; AC IL = IR + IC.
|
[52][54][55]
|
Lifetime
|
Stability
|
Generated power (PG) < dissipated power (PD).
|
[52]
|
Energy absorption capability (E)
|
Survival of the electrical components
|
E depends on the size of MOV discs; a high surface-to-volume ratio of the MOV discs leads to a high E.
|
[52][55]
|
Reliable MOVs have to exhibit high nonlinearity (α) and energy absorption capability, a low leakage current (IL) or leakage current density (JL), and long-term stability [56]. Low IL and JL values can avoid thermal runaway, while satisfactory stability and aging behavior are preserved, besides reduced electric power consumption [5]. However, we do not expect MOVs with the highest nonlinearity to have the highest energy absorption capability [56]. Furthermore, high EB can improve surge protection and ensure the reduction of the device size in HV power systems. Nonetheless, the EB increase can decrease the nonlinearity (α) and increase IL and JL. Therefore, state-of-the-art studies of ZnO-based varistors commonly report values of α < 60, JL > 1 μA/cm2, and EB of 2–5 kV/cm [5].
2. Preparation Methods of Elemental MOs and Composite Powders for MOVs
Elemental metal oxide (EMO) powders and MOV composite powders composed of EMOs (ZnO, VFO, and MO additives) are typically obtained by (i) solid-phase, (ii) liquid-phase, and (iii) gas-phase methods
[54]. Each method has advantages and disadvantages (
Table 2) that influence the characteristics of the developed powders (
Figure 1).
Figure 1. Schematic illustration of the dependence between the preparation methods and properties of EMO and MOV powders.
Table 2. Preparation methods of EMO and MOV powders, along with their advantages and disadvantages
[54][57][58][59][60][61][62][63][64][65].
Preparation Methods of EMO and MOV Powders
|
Advantages
|
Disadvantages
|
- (i)
-
Solid-phase methods:
- ▪
-
Mechanical homogenization/milling of constitutive powders by using tumbling ball/rod mills, low- or high-energy planetary ball mills, high-speed vibration ball mills, attrition mills, or cryogenic mills
|
- ✓
-
Extensive use on a laboratory and industrial scale;
- ✓
-
Relatively inexpensive production costs;
- ✓
-
Broad range of nano- or microparticle sizes and MO suppliers
|
- ➢
-
Difficulties in obtaining a uniform and narrow grain size distribution;
- ➢
-
Inadequate compositional homogeneity of powder mixtures;
- ➢
-
Powder contamination from the milling tools, atmosphere, among others;
- ➢
-
High milling time
|
- (ii)
-
Liquid-phase methods:
- ▪
-
Chemical methods (sol–gel, combustion synthesis, precipitation or coprecipitation, and subsequent calcination of powders);
- ▪
-
Solvent vaporization (atomization and spray drying, flame spray pyrolysis, freeze-drying);
- ▪
-
Metal–organic polymeric methods, microemulsion
- (iii)
-
Gas-phase methods: Chemical vapor oxidation methods
|
- ✓
-
Some methods involve industrial scalability;
- ✓
-
Reasonable control of shape and chemical composition;
- ✓
-
High purity of the synthesized powders;
- ✓
-
Adequate homogeneity of composite powders
|
- ➢
-
Expensive production costs;
- ➢
-
Challenges in the mass production of powders at low costs;
- ➢
-
Wet-chemical methods require large volumes of liquid;
- ➢
-
Distinct methods need a significant number of additional stages;
- ➢
-
Occurrence of powder agglomeration in some conditions;
- ➢
-
Difficulties in controlling evaporation rate and grain growth rate;
- ➢
-
Specific equipment for synthesis
|
The solid-state method (mechanical homogenization/milling of powders) is a classical method applied on a laboratory scale and in the industry
[54][57]. However, producing MOV composite powders with high purity, uniformity, and a narrow grain size distribution is difficult.
The liquid-phase methods include sol–gel methods
[58][59], the precipitation or coprecipitation and subsequent calcination of powders
[57], hydrothermal methods
[60][61], atomization and spray drying, and flame spray pyrolysis
[62]. These methods can yield reasonable control of the content and shape of MOV powders. However, a challenge is to achieve mass production at low costs. Similar issues can occur in the gas-phase methods, including chemical vapor oxidation methods
[54][63]. Combustion synthesis is an alternative technique with a simple and energy-efficient setup for producing doped ZnO ceramic powders with a controlled composition for the manufacturing of sintered MOVs
[54][64].
3. Preparation Methods and Major Assessment Criteria of ZnO-Based MOVs
MOV ceramic materials can be prepared using various powder metallurgy (PM) techniques that involve pressing MOV powders and consolidating them by sintering.
The sintering process can be classified as conventional or non-conventional, as shown in
Figure 1 [66]:
- ➢
-
conventional sintering (CS), which includes solid-phase sintering (CS-SPS), reactive sintering (CS-RS), and liquid-phase sintering (CS-LPS);
- ➢
-
assisted sintering involving hot pressing (HP) or hot isostatic pressing (HIP);
- ➢
-
rate-controlled sintering (RCS) by using (i) active nanoparticles (NPs); (ii) spark plasma sintering (SPS), which is an electric-field-assisted process; (iii) microwave sintering (MWS), or (iv) pulsed magnetic field (PMF) processes.
Figure 1. Schematic illustration of the dependence between the microstructure, composition, and other technical characteristics of MOVs and various PM processing techniques. Reprinted from reference
[66], published under an open access Creative Commons Attribution (CC BY 4.0) license (
https://creativecommons.org/licenses/by/4.0/ (accessed on 17 December 2022)). Copyright © 2019 The Authors.
The primary assessment criteria of MOVs should consider several factors, including technical assessment criteria related to the microstructure and characteristics of MOVs in accordance with relevant standards. Additionally, it is important to consider the impact on the environment and human health caused by the raw materials and waste generated during the production, processing, utilization, and recycling of MOVs. Compliance with relevant regulations, such as the Restriction of Hazardous Substances (RoHS) in Electrical and Electronic Equipment (EEE) directives in the European Union (EU) and Waste EEE regulations, must also be considered. Lastly, economic assessment criteria should also be taken into account, including expenses for raw materials, consumables, auxiliary materials, labor, and energy consumption.
Hassazadeh et al.
[67] proposed effective solutions to eliminate and reduce solid, liquid, and gaseous industrial wastes produced during the manufacture of MOV discs used in lighting surge arresters, resulting in environmental enhancements and improved electrical characteristics of MOVs.
4. Liquid-Phase Sintering (LPS) of ZnO-Bi2O3- and ZnO-V2O5-Based Systems
ZnO-Bi
2O
3-based systems are typically sintered at high temperatures, ranging from 1100 °C to 1400 °C, for up to 24 h. This is necessary to achieve a homogeneous microstructure and adequate varistor characteristics. Sintering below 1100 °C can lead to MOVs with an inhomogeneous microstructure, reduced and irregular grain growth of ZnO, a high breakdown field, low nonlinearity, and unsatisfactory repeatability of electrical characteristics, as reported in
[68]. The non-ohmic behavior of MOVs is conferred by the electrostatic potential barriers, known as double Schottky barriers (DSBs), which are created during cooling at the GBs of ZnO
[69][70][71][72].
The growth rate of ZnO grains during the sintering of ZnO-Bi
2O
3-based systems is highly dependent on the Bi
2O
3 content. Adding 0.05 mol.% Bi
2O
3 can lead to the abnormal growth of ZnO grains in direct contact with Bi
2O
3 due to incomplete wetting
[73]. However, an amount of 0.05–1 mol.% Bi
2O
3 improves ZnO grain growth and enhances the densification of ZnO-Bi
2O
3-based systems by liquid-phase sintering (LPS). This is because Bi
2O
3 melts at 825 °C, and the eutectic temperature of the binary ZnO-Bi
2O
3 systems is around 740 °C
[74][75]. When the Bi
2O
3 content exceeds 1 mol.%, diffusion paths are generated through the liquid phase, reducing ZnO grain growth
[73]. Therefore, ZnO-Bi
2O
3-based systems have a specific content of 0.5–1 mol.% Bi
2O
3 in MOV formulations
[3][73].
The liquid phase localized at the GBs improves diffusion development, and ZnO grain growth increases due to a solution-precipitation process governed by a phase-boundary reaction mechanism. However, a continuous Bi-rich skeleton adjoining ZnO grains can generate a supplementary current, leading to a higher leakage current
[76]. Additionally, an increase in the mass loss of ZnO-Bi
2O
3-based varistors occurs with the formation of the eutectic liquid, suggesting the vaporization of Bi
2O
3, which increases with the sintering temperature and dwell time
[75].
Bi
2O
3 has high volatility and considerable reactivity during LPS above 1000 °C, affecting the microstructure and performance of the ZnO-Bi
2O
3 systems
[77][78]. When the volatilization of Bi
2O
3 is not prevented (e.g., by sealed sintering with Al
2O
3-covered crucibles), unsuitable GB layers can result
[77]. The liquid phase can enhance GB mobility, but the formed intragrain pores can decrease the sintered density of MOVs
[74]. Lower-density MOVs (RD < 95% of TD) can yield defects such as spherical holes, indicating inadequately joined grains, leading to a decrease in the mechanical strength of MOVs
[79].
ZnO-Bi
2O
3 multilayer varistors are typically sintered at high temperatures (above 1000 °C) and co-fired with inner electrodes such as Ni
[80], Pd, or Pt alloys
[81]. The use of ZnO-V
2O
5 systems as an alternative to ZnO-Bi
2O
3 systems offers the advantage of sintering at lower temperatures (800−900 °C) to create DSBs, along with co-firing with an Ag inner electrode on each circular surface because the melting temperature of Ag is 960 °C
[82][83][84].
An amount of V
2O
5 ≥ 0.5 mol.% improves the densification of ZnO-V
2O
5-based varistors by LPS, as V
2O
5 melts at 681 °C, and the eutectic temperature of the binary ZnO-V
2O
5 system is around 600 °C
[85][86]. However, ZnO-V
2O
5-based systems with V
2O
5 content over 2 mol.% usually exhibit unsatisfactory varistor properties due to excessive secondary phases formed at the GBs between ZnO grains. On the other hand, V
2O
5 content of less than 0.1 mol.% does not promote the LPS mechanism at 825−900 °C, hindering the densification of MOVs
[87].
The prominent roles of MO additives in the varistor characteristics consist of influencing the ZnO grain growth process during the sintering stage and the dewetting features of the liquid phase during the cooling stage. Furthermore, introducing dopants into the host lattice of the ZnO crystal structure changes the electronic defect states that govern the overall MOV features
[11].
5. Polymorphisms of Bi2O3 and V2O5
The main polymorphisms of Bi
2O
3 are the stable phases α and δ, along with the metastable phases β and γ. The phase transitions in Bi
2O
3 depend on various factors, such as the heating temperature (720–900 °C), cooling rate (1–16 °C/min), heating time (2–4 h), and atmosphere (air, oxygen, or argon), leading to different oxygen content in Bi
2O
3 [88].
Mielcarek et al.
[89] reported on all the polymorphic phases of Bi
2O
3 in ZnO-Bi
2O
3-based systems. The formation of the α-Bi
2O
3 phase at GBs or triple grain junctions (TGJs) occurs upon cooling MOVs
[90]. The α- to γ-Bi
2O
3 phase transition occurs during the annealing of sintered MOVs, while the α- to δ-Bi
2O
3 transition at the GBs or TGJs is produced by the presence of metal dopants (e.g., Al, Si, etc.) in MOVs, or by quenching.
The type and content of the polymorphs of Bi
2O
3 in MOVs depend highly on the sintering temperature, dwell time, heating/cooling rate, and the composition of ZnO-Bi
2O
3-based varistors
[76][91]. The δ- and β-Bi
2O
3 phases are good ionic conductors, promoting the oxygen migration from the GBs, but the γ- and α-Bi
2O
3 phases are low ionic conductors. The α-Bi
2O
3 phase yields p-type electronic conductivity at room temperature (RT), while the δ-Bi
2O
3 phase has ionic conductivity with oxide ions as the majority charged carriers
[77]. The polymorphs of Bi
2O
3 influence the existence and content of oxygen at the interface across ZnO grains, affecting the behavior of MOVs in service
[89].
V
2O
5 exhibits multiple polymorphic phases (α, β, γ, δ, β′ or ζ, γ’, δ′, ρ′, and ε′), from which the α phase is the most thermodynamically stable and commercialized phase
[92]. Detailed information on the polymorphs of V
2O
5 is reported in references
[92][93][94]. The metastable states of V
2O
5 result from the preparation conditions (temperature and pressure), along with a few limitations (surface confinement, tensile/compressive stress, electrochemical intercalation/deintercalation (reversible), etc.).
The polymorphs of V
2O
5 exhibit crystal structures with distinct atomic arrangements (V–O connectivity) and different bonding motifs (strength). Thus, the electronic structure and the energy band gap are variable for each polymorph of V
2O
5 and can be adjusted in the range of semiconductor materials
[93] for the intended application.
6. Crystallographic Defects and Doping of ZnO
Crystallographic defects are essential characteristics in designing MO semiconductors, such as ZnO, TiO
2, SnO
2, In
2O
3, and so on
[95][96].
In multicomponent ZnO-based varistors, bulk, surface, and interfacial defects can occur between ZnO and multiple MO additives. The interfacial defects are similar to the surface defects, and can be composed of point defects (vacancies and foreign metal doping), volume defects (voids and disorders), or end of line defects (screw or edge dislocations), as well as planar defects (GBs and twin boundaries)
[95]. Grain boundaries are the most commonly reported planar defects in ZnO, along with point defects.
The primary native defects found in ZnO are Zn vacancies (V
ZnO), O vacancies (V
O), Zn interstitials (Zn
i), O interstitials (O
i), Zn antisites (Zn
O), and O antisites (O
Zn). In Zn antisites, Zn can substitute for O, while, in O antisites, O can substitute for Zn. Kröger–Vink notation is the standard notation for defects in ionic crystals, and an example of defect formation in ZnO-V
2O
5-based systems is given in reference
[97].
A ZnO semiconductor usually has an n-type structure in which negatively charged electrons (e
−) are the majority charge carriers, while positively charged holes (h
+) are the minority charge carriers. The n-type conductivity of semiconductors is caused by structural point defects (vacancies and interstitials) and extended defects (surface conduction, dislocations, stacking faults, and grain boundaries)
[98].
The factors related to the dopants, such as their formation and ionization energy, and the solubility of dopants, define the effects of MO doping on ZnO semiconductors
[99]. In multicomponent ZnO-based varistors, each introduced dopant in the host lattice of the ZnO crystal structure can act as a donor (e.g., Y ions from Y
2O
3, Mn ions from Mn
3O
4)
[23][35][100] or an acceptor (e.g., Mn ions from MnO
2)
[100], or both (e.g., Mn ions with various valence states)
[100], depending on the ionic radius and relative valency of the guest (dopant) metal ions and host (ZnO) ions
[11].
Adding insoluble MOs such as Bi
2O
3, In
2O
3, Cr
2O
3, NiO, Nb
2O
5, and Ta
2O
5, among others, and REOs (e.g., Dy
2O
3, La
2O
3, Gd
2O
3, Nd
2O
3, Er
2O
3, Y
2O
3, Sm
2O
3, etc.) with a larger ionic radius than that of ZnO can generate varistor behavior in ZnO-based systems. This addition causes the metal oxides to segregate at the ZnO GB regions and create donor states to enhance electron conduction among n-type ZnO grains
[101][102].
MOs with lower ionic radii than that of ZnO, such as CoO, Mn3O4, MnO2, V2O5, Ga2O3, and others, are also added to ZnO-based systems to improve their electrical properties. This is achieved by forming more donor states, which enhances electron conduction and increases the nonlinearity of the varistors. The reduction of the leakage current occurs by decreasing the number of defects in the MOVs caused by the reduced ionic radii of the MO dopants.
In ZnO-based MOVs, the nonlinear behavior is attributed to the presence of GBs in the polycrystalline ceramic materials. The GBs act as barriers for current flow and can be considered as a network of DSBs and/or ohmic contacts. The composition and distribution of metal impurities and dopants at the GBs affect the potential barrier height and width, which, in turn, determines the electrical properties of the varistors.
The difference between the ZnO-V
2O
5 and ZnO-Bi
2O
3 systems in GBs lies in the distribution of the dopant, either vanadium (V
5+) or bismuth (Bi
3+), within the ZnO-based varistor material. In the ZnO-V
2O
5 system, vanadium (V
5+) is incorporated into the GBs in such a way that leads to the formation of donor states, since the ionic radius of V
2O
5 (0.054 nm) is lower than that of ZnO containing Zn
2+ (0.06 nm)
[103]. These donor states can trap electrons, leading to a nonlinear response of the ZnO-V
2O
5 varistor material to an applied voltage. On the other hand, in the ZnO-Bi
2O
3 system, bismuth (Bi
3+) is distributed more uniformly throughout the GBs since the ionic radius of Bi
2O
3 (0.103 nm) is larger than that of ZnO containing Zn
2+ (0.06 nm)
[103]. Therefore, the resulting ZnO-Bi
2O
3 varistor material has a different nonlinear response.
To control the ZnO grain growth during sintering and improve the performance of MOVs, binary ZnO-Bi
2O
3 systems are doped with grain growth modifiers or spinel-forming dopants such as Sb
2O
3, SnO
2, TiO
2, In
2O
3, Mn
3O
4, Al
2O
3, and Sb
2O
5, among others, with oxidation states (+III, +IV, +V) greater than +II of ZnO with Zn
2+ ions
[44][50][73][104][105][106]. These dopants enhance the donor states and reduce the barrier height at the GBs, which further improves the electrical performance of MOVs. The introduction of spinel-forming dopants into the ZnO crystal structure results in growth defects, such as inversion boundaries (IBs), which show inverted c-axis polarity across distinct crystal planes in ZnO grains
[44][50][73][104][107]. Nonetheless, IBs do not form in pure ZnO crystal
[50].
Researchers have reported two main IB nucleation mechanisms for ZnO-based varistors doped with IB-forming dopants
[73][104]. The first IB nucleation mechanism occurs for dopants with a +III oxidation state and is governed by Zn vacancy (V
Zn) diffusion. On the other hand, all IB-forming dopants exhibit the second IB nucleation mechanism, which is based on surface nucleation and growth. This mechanism is governed by the chemisorption of the IB-forming dopants on Zn-deficient (0001) basal surfaces of the wurtzite ZnO crystal structure
[73].
The solid-state reaction between ZnO and IB-forming dopants generates IBs at lower temperatures and activation energies than those of the spinel phase origination. Low content (e.g., 0.1 mol.%) of IB-forming dopants creates a small number of IB nuclei and a coarse-grained microstructure. Conversely, high content (≥2 mol.%) of IB-forming dopants creates an increased number of IB nuclei and a fine-grained microstructure
[73].
The existence of IBs in commercial ZnO-based varistors results in enhanced varistor properties
[107]. These IBs cross virtually every ZnO grain feature, predominantly the C
− planes in the GBs, and improve the I-V characteristics. Higher reactivity between the Bi
2O
3-rich liquid phase and the solid ZnO phase in the vicinity of the IB-forming dopant can improve ZnO grain growth in ZnO-Bi
2O
3-based systems. The IB-forming dopant/Bi
2O
3 ratio determines the phase equilibrium and the temperature of Bi
2O
3-rich liquid-phase generation. However, the effect of IB-forming dopants in ZnO-V
2O
5-based systems is scarcely addressed.
7. Electrical Properties of the Selected ZnO-Based Systems
Figure 3, Figure 4 and Figure 5 present the variations in the breakdown field (EB), nonlinear coefficient (α) in the low-current region, and leakage current density (JL) with the sintering temperature of MOVs from ZnO-0.5 mol.% V2O5-based systems.
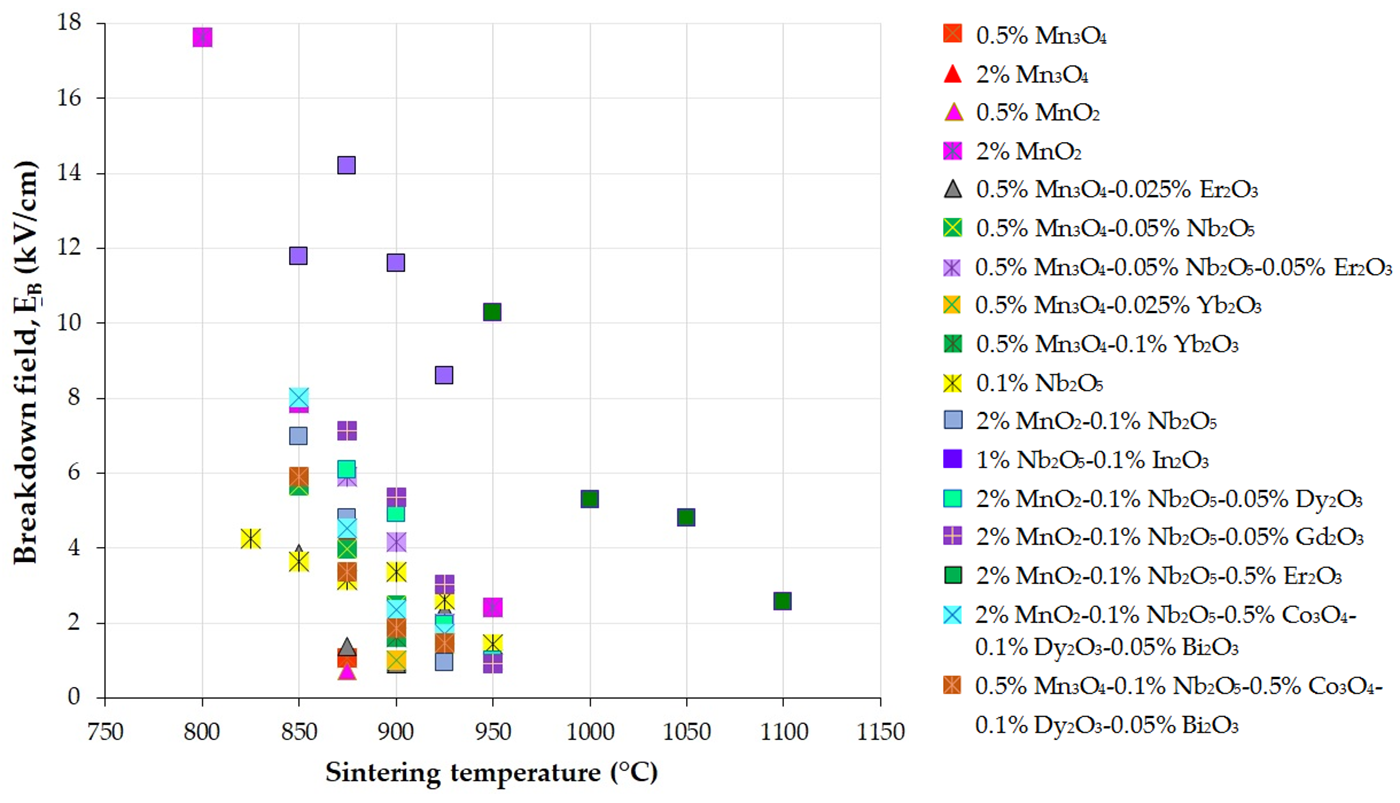
Figure 3. Variation in the breakdown field (EB) with the sintering temperature of MOVs from the ZnO-0.5 mol.% V2O5-based systems doped with various MOs (mol.%). The data plotted in the figure were collected from references [24][33][41][82][100][108][109][110][111][112][113][114][115][116].
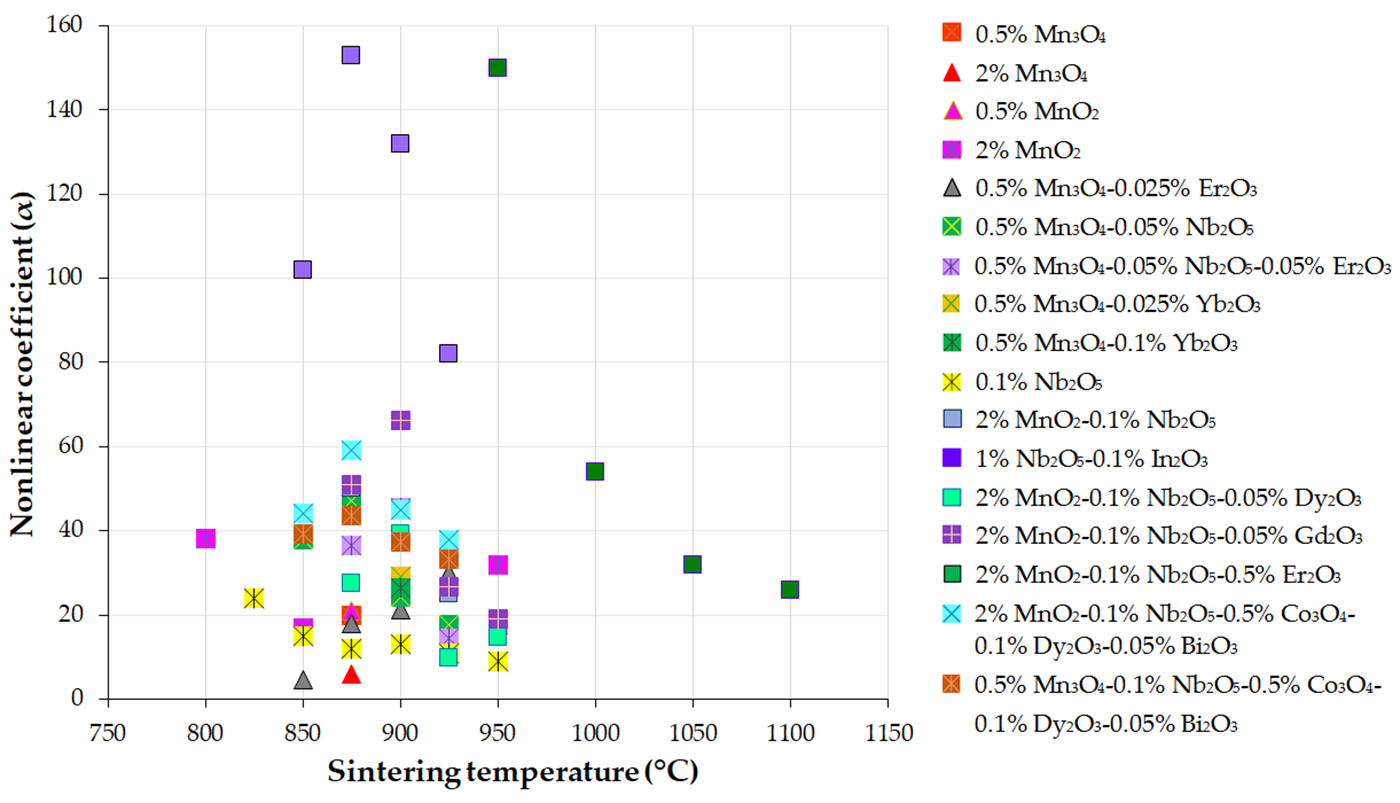
Figure 4. Variation in the nonlinear coefficient (α) in the low-current region with the sintering temperature of MOVs from the ZnO-0.5 mol.% V2O5-based systems doped with various MOs (mol.%). The data plotted in the figure were collected from references [24][33][41][82][100][108][109][110][111][112][113][114][115][116].
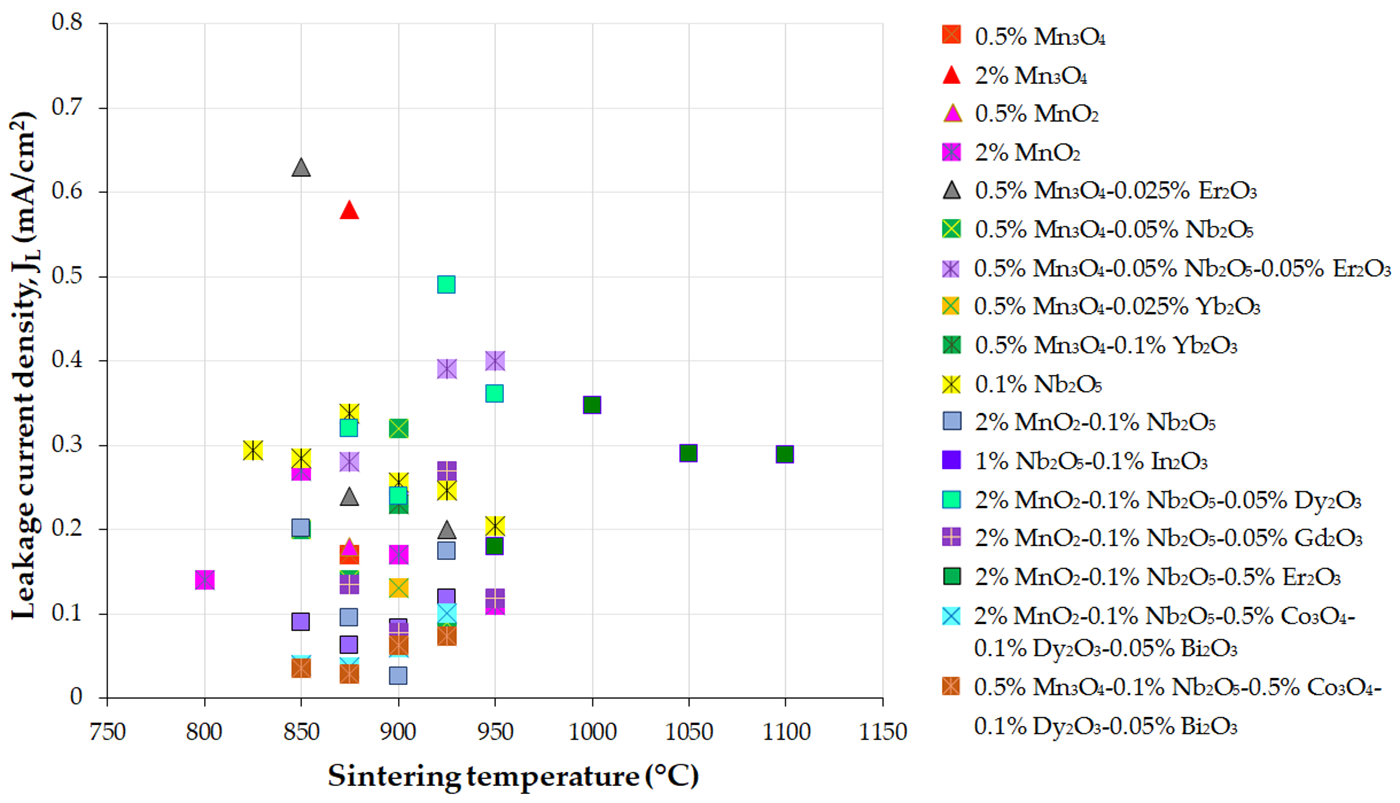
Figure 5. Variation in the leakage current density (J
L) with the sintering temperature of MOVs from the ZnO-0.5 mol.% V
2O
5-based systems doped with various MOs (mol.%). The data plotted in the figure were collected from references
[24][33][41][82][100][108][109][110][111][112][113][114][115][116].
The decrease in E
B with an increase in sintering temperature (
Figure 3) is attributed to the reduction in the number of GBs across the thickness of the MOV disc due to the increase in the mean ZnO grain size and the corresponding decrease in the breakdown voltage drop per GB
[33][35][41][81][109][117][118]. In contrast, the increase in E
B is caused by the decrease in the mean ZnO grain size, leading to an increase in the number of GBs
[119].
The nonlinearity (α) of the MOVs from the ZnO-based systems is greatly dependent on the electrical potential barrier height (Φ
B) at the GBs. Φ
B is expressed as the absolute value of the difference between the Fermi energy levels in the GB (E
FB) and the ZnO grains (E
FG) (E
FB < E
FG)
[5].
During the sintering process of ZnO-based systems, point defects occur at the GBs, which relocate the E
FB to a higher position in the band gap energy (E
g). This shift in E
FB creates DSBs (depletion zones at either side of the GBs), resulting in the formation of potential barriers
[5][46]. Furthermore, changes in the sintering temperature can modify the interface state density (N
s) at the GBs, causing the defect ions (native or additive donors) to move toward the GBs and generate more active GBs
[113].
Doping ZnO grains with small amounts of MOs (e.g., MnO
2, Mn
2O
3, In
2O
3, Sb
2O
3, Cr
2O
3, etc.), in ZnO-based systems, can increase the Fermi energy levels in the ZnO grains (E
FG), causing a shift in the band gap energy (E
g). This leads to an improvement in Φ
B, resulting in better nonlinearity (higher α) and a lower I
L or J
L compared to pure n-type ZnO semiconductors with a direct E
g of ~3.37–3.4 eV at RT
[2][96][120], which exhibit very low nonlinearity and almost equal Fermi energy levels in the GBs and ZnO grains
[5].
The enhancement in nonlinearity (α) with increasing sintering temperature (
Figure 4) was attributed to the variation in the Schottky barrier height, which changes with the electronic states at the GBs during sintering when defect ions are promoted near the GBs
[112]. Therefore, the decrease in the Φ
B at the GBs led to the reduction in the α values as the sintering temperature varied
[113].
Table 3 demonstrates that ZnO-V
2O
5 systems with lower amounts of MO additives exhibit comparable or even superior electrical characteristics to the selected ZnO-Bi
2O
3-based systems when sintered at lower temperatures. This suggests that manufacturers can use less MO dopants and lower sintering temperatures to produce high-performance ZnO-V
2O
5-based varistors, leading to savings in raw materials and energy costs
[73].
Table 3. Critical electrical parameters of MOV devices from several ZnO-V2O5-based systems with good varistor properties compared to those of some relevant ZnO-Bi2O3-based systems.
MOV System Type (mol.%)
|
State
|
Pp, Ts/DT (PM Process)
|
EB (kV/cm)
|
α
|
IL (μA)
|
JL (mA/cm2)
|
MOV Producers
|
Reference
|
ZnO-V2O5-based systems
|
ZnO-0.5% V2O5-0.5% Mn3O4
|
Initial
|
80 MPa, 900 °C/3 h (SSS)
|
1.07
|
20
|
−
|
0.170
|
Semiconductor Ceramics Laboratory, Department of Electrical Engineering, Dongeui University, Republic of Korea
|
[100]
|
Stressed
|
0.96
|
11
|
−
|
0.480
|
ZnO-0.5% V2O5-0.5% Mn3O4
|
Initial
|
80 MPa, 900 °C/3 h (SSS)
|
0.72
|
27
|
−
|
0.042
|
[100]
|
Stressed
|
0.99
|
20
|
−
|
0.210
|
ZnO-0.5% V2O5-0.5% Mn3O4-0.1% Yb2O3
|
Initial
|
100 MPa, 900 °C/3 h (SSS)
|
1.64
|
26.3
|
−
|
0.230
|
[24]
|
Stressed
|
1.65
|
25.2
|
−
|
−
|
ZnO-0.5% V2O5-1% Nb2O5-0.1% In2O3
|
Initial
|
500 MPa, 875 °C/1 h (SSS)
|
14.2 ± 0.1
|
153 ± 7
|
−
|
0.062
|
Variable Energy Cyclotron Centre and Homi Bhabha National Institute, India
|
[41]
|
Initial
|
500 MPa, 900 °C/1 h (SSS)
|
11.6 ± 0.2
|
132 ± 8
|
−
|
0.083
|
ZnO-0.5% V2O5-0.5% Mn3O4-0.05% Bi2O3
|
Initial
|
100 MPa, 825 °C/3 h (SSS)
|
6.027
|
31
|
− |
0.043
|
Semiconductor Ceramics Laboratory, Department of Electrical Engineering, Dongeui University, Republic of Korea
|
[81]
|
ZnO-0.5% V2O5-0.5% Mn3O4-0.1% Bi2O3
|
Initial
|
3.357
|
24.9
|
− |
0.052
|
ZnO-Bi2O3-based systems
|
ZnO-1% Bi2O3-1% Sb2O3-0.75% MnO2-1% Co2O3-0.5% Cr2O3-1% Sb2O3, 1.2% SiO2-0.2% Al2O3-0.005-0.02% In2O3
|
Initial
|
~39 MPa 1200 °C/2 h (SSS)
|
3.56–4.34
|
52–60
|
−
|
0.002–0.004
|
State Key Laboratory of Control and Simulation of Power System and Generation Equipment, Department of Electrical Engineering, Tsinghua University, China
|
[40]
|
ZnO-0.5% Bi2O3-1% Sb2O3-0.5% CoO-0.5% MnO2-0.5% Cr2O3
|
Initial
|
~33 MPa 1350 °C (SSS)
|
1.35
|
50
|
−
|
−
|
Matsushita Electric Industrial Co., Japan (actual Panasonic)
|
[3]
|
Initial
|
1100 °C/1 min and 850 °C/1 h (MW-TSS)
|
10.7
|
40
|
58
|
−
|
PPG-CEM, Federal University of São Carlos, Brazil
|
[121]
|
Commercial ZNR 10K 270 (ZnO-Bi2O3-MO dopants)
|
Initial
|
NA
|
0.22
|
≤11
|
−
|
0.070
|
Matsushita Electric Industrial Co., Japan (actual Panasonic)
|
[122]
|
Commercial ZNR 10K 470 (ZnO-Bi2O3-MO dopants)
|
Initial
|
NA
|
0.42
|
≤25
|
− |
0.013
|
Commercial GEMOV 27Z 1 (ZnO-Bi2O3-MO dopants)
|
Initial
|
NA
|
0.27
|
≤16
|
−
|
0.035
|
General Electric Co., USA
|
Commercial (ZnO-Bi2O3 + MO dopants)
|
Initial
|
1095 °C/2.5 h (SSS)
|
1.85
|
27
|
17
|
−
|
Unknown producer
|
[76]
|
ZnO-Bi2O3-Sb2O3-Co3O4-Mn2O3-NiO-B2O3-Al2O3
|
Initial
|
95 MPa, 1115 °C/5 h (SSS)
|
1.79
|
56
|
3.4
|
−
|
Tridelta Parafoudres S.A. and UMR CNRS-UPSINP, France
|
[76]
|
This entry is adapted from the peer-reviewed paper 10.3390/ma16103725