1. Introduction
Food packaging protects food from contamination and physical damage, maintains its freshness, improves its shelf-life, and gives relevant information about its contents
[1][2]. Despite its effectiveness, conventional food packaging poses some concerns, such as food spoilage, since plastic itself has no effect on microorganism contamination, as well as excessive production of fossil-based plastic—this sector being one of those that employ this type of material most heavily, food packaging representing more than 40% of total plastic production
[3]. Since fossil-based plastic is inherently non-renewable and non-biodegradable and its production has been massively increasing in the last seven decades (from 2 million tons in 1950 to 367 million tons in 2020)
[3][4], new alternative materials for the manufacture of food packaging have been sought.
One emerging set of alternatives that have been studied as potential solutions to the above-mentioned problems are bio-based food packaging films functionalized with compounds of natural origin, since they are characterized by both biodegradability and renewability, in addition to active and/or intelligent functions
[5][6][7]. In the production of these bio-based films, different methodologies may be employed depending on the purpose in question, the most common methods being solvent casting, layer-by-layer assembly, and extrusion. Moreover, additive manufacturing technologies, also known as “3D printing” have been, although scarcely, used in the production of bio-based films and other types of bio-based packaging. Considering the importance of food packaging, its current drawbacks, and the potentialities of 3D printing, the objective of this review is to explore progress in the production of bio-based films by conventional methodologies and additive manufacturing and to investigate how this technology can contribute for the development of bio-based sustainable primary food packaging.
2. Novel Materials for Food Packaging Films: Biopolymers and Additives
As alternatives to conventional plastic-based packaging, bio-based polymer films have been explored as potential candidates for the development of food packaging. Regarding the advantages over conventional petroleum-based food packaging, these bio-based films can decrease carbon dioxide levels, do not release dangerous substances into the environment, can be degraded by naturally occurring bacteria, can reduce the amount of waste generated, and are non-toxic
[8][9]. Furthermore, the main materials used in the preparation of these films, that is, the biopolymers, are generally abundant in nature and can be derived from plenty of sources, namely, microorganisms, plants, animals, and food/agricultural wastes. Examples of biopolymers used in food packaging applications are summarized in
Figure 1.
Figure 1. Bio-based polymers used in food packaging applications.
In addition to biopolymers for bio-based films, there is an increasing interest in compounds of natural origin, such as extracts and essential oils, as additives in the production of food packaging. When these natural compounds are incorporated into polymeric films, they can provide active properties, such as antioxidant, antimicrobial, and scavenging properties, that are crucial for food packaging, due to food deterioration and microbial contamination, which can produce off-flavors, lead to food spoilage, and cause food-borne diseases
[7][10][11]. The active substances present in these compounds differ in composition and quantity and can be divided according to their structures and modes of action: phenols and phenolic acids, quinones, flavones and flavonoids, tannins, coumarins, terpenoids, alkaloids, and lectins and polypeptides
[12]. In terms of antimicrobial activity, the modes of action of these substances can vary and include leakage from the bacterial cell, cell-shape damage, the destruction of cell walls, and alterations to membrane composition, among other mechanisms
[12][13]. In addition to active properties, these compounds have also been used to provide extra and/or intelligent properties in films, such as sensitivity to pH changes; improved mechanical, thermal, optical, and barrier properties; and sensing abilities, among others
[7]. In sustainable food packaging, the incorporation of these compounds can lead to the development of active materials that, in addition to being biodegradable/sustainable, can also increase food shelf life, reduce microbial contamination, and give information on food freshness
[10]. Many natural compounds, such as natural extracts and essential oils, have been studied for the above-mentioned properties. Some examples of natural products that have been employed as sources of antioxidant and/or antibacterial compounds in bio-based food packaging include extracts of cranberries, cabbage, amaranth leaves, rosemary, cinnamon, broccoli, kale, and others, as presented
[14][15][16][17][18][19].
3. Main Methods Used in the Production of Bio-Based Films
In the production of bio-based films, the methodology employed depends on the film application and on the objectives. In brief, the fundamental step in processing any biopolymer film involves solubilizing and/or melting a biopolymer mixture, which is followed by the implementation of the desired technique [20]. Some of the most common methods for the production and application of bio-based films include the solvent casting method, layer-by-layer assembly, and coating and extrusion methods, which are briefly described in Table 1 and Figure 2 [21][22]. Some of these methods are limited to lab scale, while others can be scaled up for industrial settings.
Table 1.
Main methods for preparation of biopolymer-based films
-
Method
|
Main Characteristics
|
Solution casting
|
The film-forming solution is cast on a surface (e.g., a Petri dish), appropriately dried, and the formed film is peeled off;
The simplest method for film preparation;
The conditions used are relatively mild;
Time-consuming;
Limited to lab scale;
|
Coating
|
The film-forming solution is directly applied onto the food by means of dipping, spraying, or brushing and dried afterwards in appropriate conditions;
Often applied on fresh food;
Materials must be of food grade if the coating is meant to be eaten;
Some applications in the food industry (mostly wax coatings);
|
Layer-by-layer assembly
|
Based on the deposition of alternating layers;
Deposition can be achieved either by submersion in or spraying the film-forming solutions on the food;
Potential for industrial applications, though currently it is mostly limited to lab scale;
|
Extrusion
|
The mixture containing the biopolymer is poured into an extruder system, which produces a uniform film at the end of the process;
Faster and less energy-demanding than the solution casting method;
Produces films with superior mechanical and thermal properties;
Conditions may be aggressive for biopolymers;
Can be scaled up for industrial settings;
|
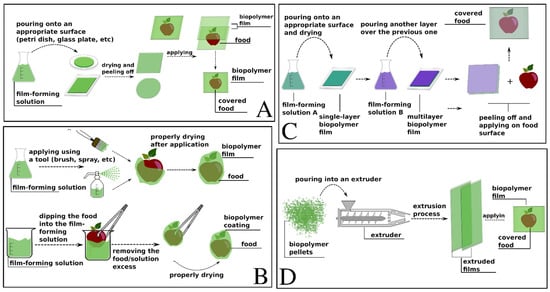
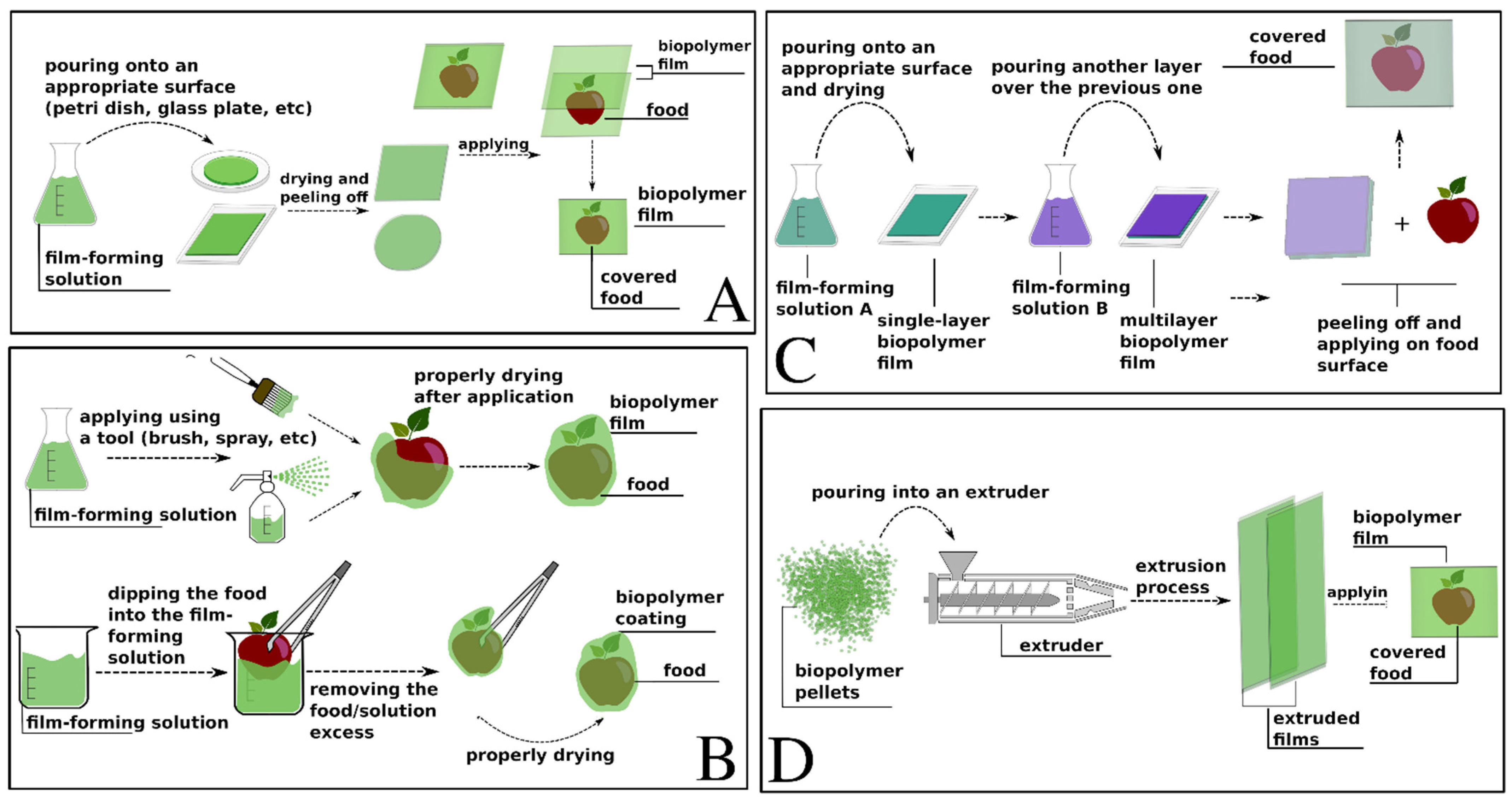
Figure 2.
Conventional methods for the production of bio-based films. (
A
) Solution casting. (
B
) Coating. (
C
) Layer-by-layer assembly. (
D) Extrusion
) Extrusion.
4. Three-Dimensional Printing of Food Packaging and Films
Three-dimensional printing or additive manufacturing (AM) is a relatively new technology that has been revolutionizing a range of industries, research, and the overall manufacturing of new products because of its advantages, such as the reduction of manufacturing times, the possibility of producing complex shapes and parts, and the potential for innovation, and it has also been, although scarcely, used as a means to develop bio-based packaging materials. With this set of technologies, solid models are fabricated through the layer-by-layer deposition of raw materials, followed by their solidification, and it is possible to work with powder-based, liquid-, and solid-state feedstocks, depending on the chosen technology
[23][24][25][26].
In general, the 3D printing process can be described as a sequence of steps, the first one being the generation of a computer-aided design of the desired object, followed by its conversion into a 3D object file, which will be read by the slicing software and built on the platform afterwards
[24]. The principle of operation and type of 3D printing can vary depending on the application. In total, there are seven standardized processes (or techniques) that 3D printing is based on: binder jetting, directed energy deposition, material extrusion, material jetting, powder bed fusion, sheet lamination, and vat photopolymerization
[25][27]. These processes differ in terms of the type and the state of the raw material used, in the degree of detail of the printed object, and in the fundamentals behind the printing process. According to Zhou et al., among the cited methods, material jetting, powder bed fusion, vat photopolymerization, and material extrusion are the most suitable techniques for printing 3D objects made of soft materials, such as polymers, and they will be briefly summarized below
[27]..
4.1. Vat Photopolymerization
In vat photopolymerization, the 3D object is created by the solidification of a photopolymer resin when it is hit by light. In this process, a liquid photo-reactive polymer, which is contained in a vessel, is selectively cured by a UV light coming from a light source, forming a thin-layer cured polymer as a result
[25]. The main 3D printing techniques that are based on this principle are stereolithography (SLA) and digital light processing (DLP), mainly differing in the sources of light
[27]. The main advantages of vat photopolymerization are the high degree of accuracy and the smooth surface of the produced 3D object. Drawbacks include the need to use supports during the printing process and the inherent natures of the photopolymers employed as raw materials, such as their physical fragility and susceptibility to sunlight, which limit the range of applications of these products and make them less durable.
4.2. Material Jetting
Similar to vat photopolymerization, in material jetting, the object is formed by the solidification of a photo-sensible resin, but unlike the previous technique, this method is based on the deposition of tiny droplets of the photopolymer resin on the build platform, followed by their solidification by ultraviolet light
[25]. This technique is regarded as the most accurate 3D printing technique and can produce objects with smooth surfaces and high degrees of detail. Analogous to vat photopolymerization, the main drawbacks of material jetting are related to the intrinsic properties of the raw materials, including the poor mechanical properties and the susceptibility to sunlight of the produced objects
[24].
4.3. Powder Bed Fusion
The powder bed fusion process is based on the fusion of a powder-based material by a laser or an electron beam
[25]. In this mode of operation, a thin layer of powder (e.g., a metal, ceramic, polymer, or composite) is distributed on the build platform and a laser automatically fuses layers of the material. This technology includes three printing techniques: electron beam melting (EBM), selective laser sintering (SLS), and selective heat sintering (SHS). The EBM and SHS techniques are mainly employed with metals, whereas SLS is employed for polymer materials (Redwood et al., 2017). The resolution of SLS is inversely proportional to the particle size, and it is preferable to use low-thermal-conductivity polymers as raw materials due to their stability in the fusing step
[27]. Among its advantages, SLS produces objects with isotropic natures, making them stronger and more resistant than other printing technologies, such as FDM. In addition, SLS has a high degree of accuracy and, unlike vat photopolymerization, does not require extra supports to build objects
[24].
4.4. Material Extrusion
Material extrusion is one of the most widely used 3D printing processes. The principles of this technique can be divided into two main groups based on whether the raw material is melted or not
[28]. The technology based on the melting of a material is known as fused filament deposition modeling (FDM) and uses thermoplastics in the form of thin filaments as raw materials
[25][27]. Another technology is direct ink writing (DIW), which is based on the extrusion of viscoelastic materials by means of pneumatic (air or pressure) or mechanical (screw- and piston-based) action, followed by the curing of the extruded material using photopolymerization or thermal processes
[27][28]. Among the cited techniques, FDM is the most common method used in 3D printing. In FDM, a solid filament is extruded through a heated nozzle, melted, and selectively deposited on the build platform where it solidifies, forming a layer of the object. The advantages of this technique include the low costs of the materials and machines, the easy mode of operation, and a broad range of workable materials
[23].
The main limitation of extrusion-based 3D printing is related to the anisotropic nature of the produced objects, that is, the fragility of objects in one of their directions. The rheological and thermal properties of the material employed are also critical and depend on the nature of the extrusion process. Additionally, as is often the case with other AM technologies, it is likely that the final object will require some post-treatment to remove undesirable layer lines, the formation of which is inherent to the layer-by-layer building process
[24][23]. Representations of the four described additive manufacturing techniques are presented in
Figure 3.
Figure 3. Three-dimensional printing techniques suitable for working with polymers. (A) Material extrusion. (B) Powder bed fusion. (C) Vat photopolymerization. (D) Material jetting.
5. Perspectives on AM in the Production of Bio-Based Films
In the field of food packaging, the additive manufacturing technologies can be very advantageous since it could be used to develop complex food packaging materials (e. g. multilayered functional films and core-shell structures with active compounds). Additionally, there is an increasing interest in biopolymers for additive manufacting feedstock, which could also be beneficial in the production of sustainable food packaging by this technology. However, among the technologies presented, material extrusion seems to be the most appropriate for developing bio-based films and other materials for food packaging applications using either filaments or gels. Despite the fact that powder bed fusion technologies use polymers as feedstocks, no studies on the production of films using these materials were found. Other technologies discussed herein, such as vat photopolymerization and material jetting, seem not to be suitable for the production of bio-based food packaging due to the use of resins as their main materials, which are often non-compatible with food safety. Additionally, the objects produced with these technologies are known for having characteristics undesirable in films, such as brittleness and sensitivity to UV light. Extrusion-based technologies have a broader range of workable materials in comparison with resin-based AM technologies. Additionally, unlike powder bed fusion, extrusion-based 3D printers allow for working with biopolymers in solid (FDM) and gel–liquid (DIW) states, making them more versatile tools for working with bio-based polymers than the other AM technologies discussed herein. Some exemples of biopolymers that might be used to produce sustainable packaging films by material extrusion techniques include lactic acid-based polymers, lignin, alginate, chitosan, and starch[29][30][31]. Among them, chitosan is the most employed to develop sustainable food packaging by means of this technology, as presented in Table 2.
Table 2. Studies on development of sustainable polymeric food packaging by means of 3D printing
Studies on development of sustainable polymeric food packaging by means of 3D printing.
-
Polymer/Active Compounds and Fillers
|
Proposed Application
|
Properties
|
Ref.
|
Chitosan and starch/lemongrass essential oil and mulberry anthocyanin
|
Food packaging
|
Color-changing properties;
Antibacterial effect
|
[32]
|
Chitosan/tea polyphenols and halloysite nanotubes
|
Food packaging
|
Good antioxidant and antibacterial activity;
Improved mechanical properties
|
[33]
|
Bio-based plastic “Ecoflex”/silica–carbon–silver nanoparticles
|
Food packaging
|
Bacteriostatic effect
|
[34]
|
Gelatin/zinc oxide and clove essential oil
|
Food packaging
|
Improved mechanical properties and antibacterial activity
|
[31]
|
Chitosan and cellulose/blueberry anthocyanin and
methylcyclopropene
|
Food packaging
|
Color changing properties and preservation ability
|
[35]
|