1. Introduction
With the rapid development of the Internet of Things (IoT) and artificial intelligence (AI) for a smart world, distributed sensing systems, which are the foundation of the fourth industrial revolution, are the most important developments in hardware in the era. The continuous development and prosperity of distributed sensing systems rely on distributed renewable sources of energy such as solar power, wind power, and mechanical vibration
[1]. The triboelectric nanogenerator (TENG) developed by Z. L. Wang’s team to harvest random mechanical energy is a promising new energy source in the new era because triboelectric electrification is ubiquitous with a wide selection of materials
[2]. Compared to externally powered sensors, the development of self-powered active sensors powered by TENG is revolutionary. In addition, TENG has many other advantages such as an abundant choice of materials, low assembly requirement, and flexibility
[3], making it suitable for many application areas, including energy harvesting, environmental protection, wearable electronics, robotics, and self-powered sensors
[4].
An important part of TENG applications is sensing that focuses mainly on active mechanical and chemical sensors in the early stages. Additionally, early TENG can actively detect the static and dynamic processes from mechanical agitation with potential smart skin applications
[5]. With the in-depth study of TENG sensing in its working principle, material selection, processing technology, system integration, surface treatment, and back-end algorithms by researchers, the application fields of TENG sensing are gradually expanding, especially fluid dynamics sensing. Fluids, including gases and liquids, account for two of the three phases of matter and tend to flow, meeting the working principle of TENG: mechano-driven. Most importantly, fluid dynamics sensing is urgently needed in industry and academia. In particular, local fluid sensing is difficult and limited to traditional sensors.
Fortunately, with advantages for ordinary TENGs (discussed later in this section) and TENGs as fluid dynamics sensors, fluid dynamics sensing can be better realized. For example, the self-powered characteristics of TENG can simplify the sensor structure, so that the disturbance of the sensor for the flow field is reduced. In addition, the diversity of material choices and the sensitivity to external stimuli give TENG an advantage over other existing sensing schemes in complex fluid environment sensing.
2. Introduction of TENG
Coupling the triboelectric effect and electrostatic induction, TENG was first invented by Wang’s group in 2012 to generate electricity through harvesting environmental mechanical energy that is ubiquitous but often wasted. More specifically, the electricity is converted by electrostatic induction through the electric field change, which is induced by mechanical separation after triboelectric or contact electrification transfers electrons from one surface of contacting materials to another according to the quantum mechanical transition model
[6]. The model states that when two materials approach an atomically close distance, electrons move toward the lowest available states due to strongly overlapping electron waves. The electron transfer model could be extended from solid–solid to liquid–solid, liquid–gas, and even liquid–liquid cases
[7].
2.1. Principle of TENG
The fundamental physics model of TENG was presented according to Maxwell’s displacement current in 2017
[4][8][9][10]. The displacement current is from a transient electric field and media dielectric polarization and drives the conversion of mechanical energy into electricity. Mainly due to the independence of the surface charges on the electric field, a new term
Ps, known as the Wang term, is added to Maxwell’s equations to explain TENG’s working mechanism
[4]. The displacement current density (
JD) is then expanded as follows:
TENG can be categorized into four basic modes according to their electrodes and motion patterns: vertical contact separation, lateral sliding, single-electrode, and freestanding triboelectric-layer modes (
Figure 2)
[13]. In general, electrons are transferred back and forth from one electrode to another (generating electrical current) due to the change of electrical field caused by the mechano-driven location change of triboelectric materials. The electron transfer is slightly different for the single-electrode mode (
Figure 2c) since it has only one electrode: the only electrode exchanges electrons with the ground. Each mode has its advantage in energy harvesting, manufacturing, and robustness
[3][13]. In addition, the various motion patterns give more flexibility to the sensors’ working mechanism, design, and manufacturing. For example, the single-electrode mode for the TENG as a sensor may give the lowest energy output and thus signal-to-noise ratio (SNR) but can sense the object directly with the easiest setup since the triboelectric material, possibly the object being sensed (e.g., liquid), does not necessarily belong to the system. The displacement current model of contact separation mode and the equivalent electrical circuit model is described in
Figure 2e,f, respectively.
2.2. Advantages of Ordinary TENG
In addition to multiple modes of operation, ordinary TENG has many other advantages, including wide material availability, lightweight, low cost, and high efficiency even at low operating frequencies. In addition, its sensitivity to external incentives and self-powered characteristics also broaden its scope of application.
3. TENG for Fluid Dynamics Sensing
In physics and engineering, fluid dynamics is a branch of fluid mechanics that describes the flow of fluids, including aerodynamics (study of gases in motion) and hydrodynamics (study of liquids in motion). Here, we divide the fluid dynamics parameters that may be sensed by TENG sensors icould be divided into two groups by scale: large- and local-scale properties. The large-scale properties include ambient fluid motions, such as wind, rain, and water wave, and their speed, direction, and pressure; the local-scale properties include the flow pattern and force under various situations on the local scale, such as laminar and turbulence flow and their development, boundary layer and its separation, flow pattern around immersed bodies, rotational fluid such as vortex, and streamlines in the local flow field (Figure 1).
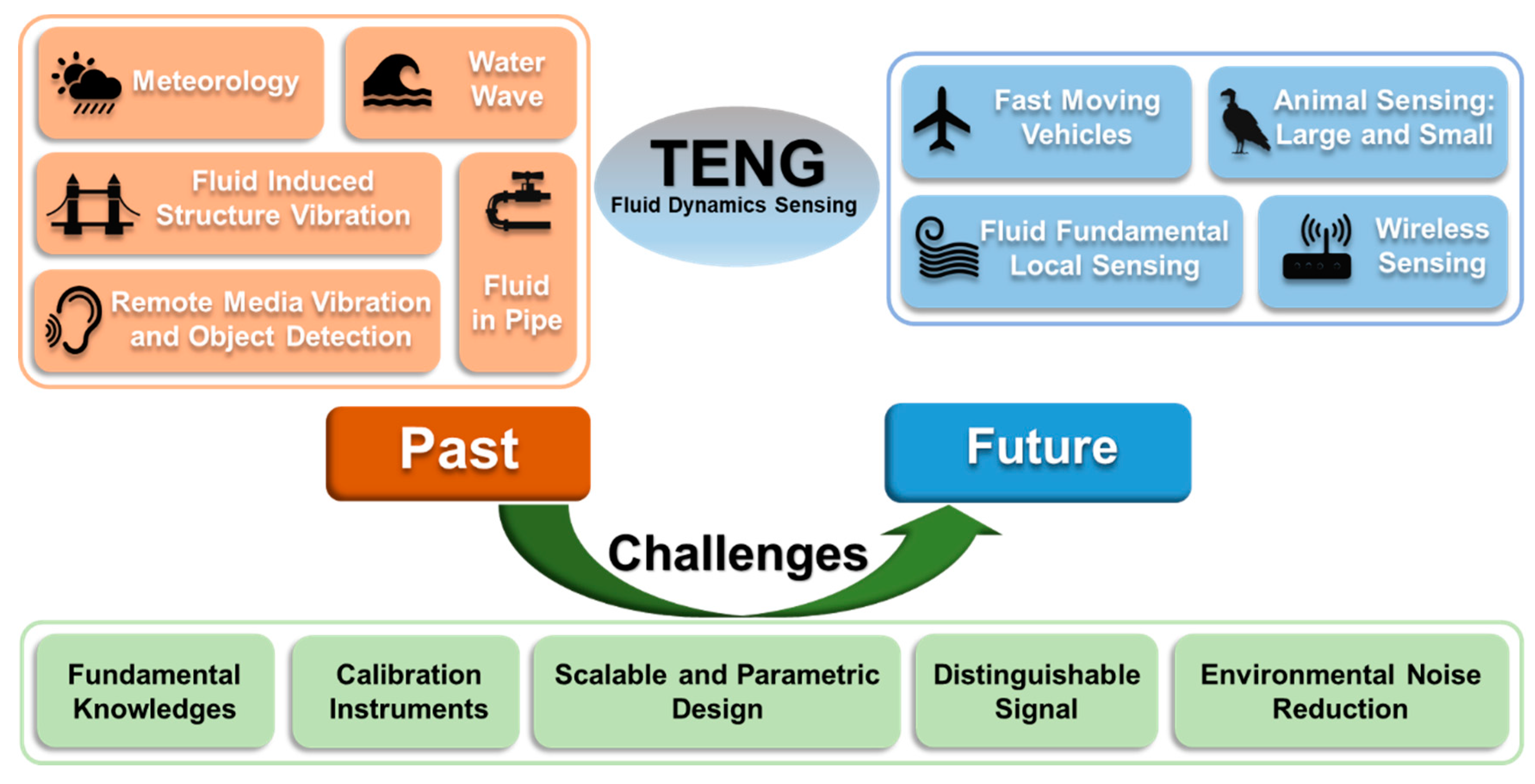
Figure 1. Opportunities and challenges of triboelectric nanogenerators for fluid dynamics sensing, from traditional fields to future technologies.
However, to reveal the full potential of TENG for fluid dynamics sensing,
it we needis necessary to take advantage of TENG
, and and ultimately fill the gaps and meet the needs of industry and academia. In academia, alternative methods are needed to measure the in situ local fluid situations, e.g., vortex, boundary layer, and turbulence transition. The most reliable method to observe fluid dynamics is optical techniques, such as particle image velocimetry (PIV) and Schlieren imaging. However, these techniques require a sophisticated setup and critical experimental environment in the laboratory, making them not suitable for multi-scale field measurements, which play very important roles in the validation and application of fundamental theories.
In industry, especially aerospace, non-invasive sensors are in large demand, for flight safety, flight data acquisition, and aircraft design optimization by monitoring the local in situ fluid situation in real flight. The critical parameters include aircraft airspeed, friction drag force, vortex and boundary layer separation near the wing surface, and wing vibration. However, most of the traditional sensors need power with cables that will increase the weight. In addition, since most third-party sensors are not pre-designed in the body, the power supply and cables of the sensors will expose to the extreme atmosphere, creating a difficult scenario for high-speed aircraft because the fast-moving air may damage the cables, which also in turn disturb the airflow field and thus the flight condition and safety. As for light-weighted unmanned aerial vehicles (UAV), the increased weight from the whole sensor system could be another critical problem for efficient flight. Thus, the industry craves suitable sensors with the features of lightweight, plug-and-play, in situ, and battery-less, so that significant progress can be made in the aerodynamics theory development, aircraft design, and safety monitoring.
Fortunately, TENG sensors have the potential to fulfill some of the above needs in fluid dynamics sensing thanks to the following advantages: self-powered sensing, wireless signal transfer, scalability, material diversity, and flowability (
Figure 2). TENGs can actively generate electrical signals and have the potential to generate enough power to save and even transmit signals by the TENG alone, making the sensor setup and maintenance much easier than the conventional ones. Tao et al. designed a hierarchical honeycomb-structured structure for morphing airplane energy harvest, claimed as the first TENG used for aircraft, showing the feasibility of energy harvesting and self-powered sensing in the aerospace industry
[14].
Figure 2. Schematics of advantages and future applications of TENGs for fluid dynamics sensing.
Furthermore, with the feasibility exploration and approach development of wireless transmission of TENG signal in air and water
[11][12][15][16], even if the TENG is not powerful enough to run the whole system, the sensing signal can be also possibly received without any power supply and the need of signal pre-amplification. Wang et al. summarized TENG-based self-powered wireless communication into four major types of technological routes: tribo-induced electromagnetic wave generation, tribo-induced light propagation tuning, triboelectrification-induced electroluminescence, and tribo-assisted spectrometry, collectively known as tribophotonics
[12].
In addition to signal generation and transferring, the adaptive design and easy manufacturing, thanks to its simple working mechanism and various working modes, endow TENGs with strong scalability, meaning that the complexity and difficulty of manufacturing are not heavily affected by the size of the devices. Many design techniques are highly scalable by avoiding the use of unscalable parts, such as traditional joints, screws, nuts, and gears. For example, compliant mechanism design can reduce parts, joints, and production processes, making it advantageous in the fabrication of micro-mechanisms
[17]; origami and kirigami design
[18] can easily transform a device into a 3D structure with the desired function from a 2D design, which is convenient for industrial-level and TENG friendly precision manufacturing techniques such as laser cutting, pre-stretching, printed circuit board (PCB), and microelectromechanical systems (MEMS).
Consequently, the scalability gives TENG sensors better chances to form an array
[19] and get applied to the microenvironment. For example, a rationally designed TENG can locate within the flow boundary layer and provide valuable local information for flow fundamental research. In addition, an array of such sensors can even deliver more comprehensive information in high spatial and temporal resolution
[20]. In addition, TENG sensors with good scalability (better if with wireless communication) can be used for biological monitoring, data acquisition, and learning, where
wpeople can learn deeper and better from nature, especially its fluid-related phenomenon
[21][22], e.g., flying of birds and swimming of fishes, allowing
uspeople to have innovations and breakthroughs in the engineering development for machines, vehicles, and robotics
[23][24]. Of course, this influence has already penetrated deep into the TENG field
[25][26][27]. For an instance, the study of seal whisker (vibrissa) suppressing vortex-induced vibrations provides
uspeople with a possible solution to increase the SNR (signal-to-noise ratio) for a TENG array system of object-induced vortex detection
[28]. However, the investigation tools and approaches to study nature are limited. Tiny, lightweight, and scalable TENG sensor arrays will make a difference in the in situ fluid dynamics monitoring of living beings.
The material diversity that offers a wide selection of materials is another unique feature of TENG sensors, especially for fluid dynamics sensing. Fluids may contain a variety of physical and chemical phenomena that make most sensors difficult to deploy and function. The situation is much better for TENG sensors, as almost any two materials can generate a high or low triboelectric signal so that
wright mate
can choose the right ones from rials can be chose from the large material library to suit specific, possibly extreme, and multi-physics environments (e.g., high temperature, pressure, electrical noise, bending, and friction environments) with better physicochemical performance such as high chemical resistance, hydrophobic/hydrophilic, temperature resistance (e.g., titanium–tantalum alloy), fatigue resistance, and shape memory (e.g., nitinol alloy), and light-weighted but high strength (e.g., carbon fiber). For example, similar to the flutter-type speed sensor, a thin metal foil, which can flow along with air, can be used as the fluttering material to sense high wind speed in high-temperature situations (e.g., airspeed sensing for aircraft) instead of polymer films, which are fragile with low-temperature resistance.
Another important property of TENGs for fluid dynamics sensing is flowability, which means that the TENG can conform to and move along with the moving fluid, making it very unique in the fluid sensing field. Most of the traditional sensors are fixed rigidly and cannot move with the fluid. A moving along sensor can give detailed and valuable in situ information on the fluid local status including vortex
[29][30], boundary layer separation, and turbulence, which are some of the most difficult subjects for fundamental fluid research and critical for the field of fasting moving vehicles such as aircraft and submarine. As for those traditional fixed sensors for fluid dynamics, only the related but indirect parameters can be measured to calculate the interested parameters with many assumptions and simplifications. For example, the MEMS skin sensors for aircraft measure the fluid-related parameters, such as pressure and temperature, and indicate the flow turbulence and stall status indirectly through calculation with mathematical algorithms
[31][32].