Human–robot interaction (HRI) is a broad research topic, which is defined as understanding, designing, developing, and evaluating the robotic system to be used with or by humans. This paper reviews the variable admittance (VA) control for human–robot co-manipulation tasks, where the virtual damping, inertia, or both are adjusted. An overview of the published research for the VA control approaches, their methods, the accomplished collaborative co-manipulation tasks and applications, and the criteria for evaluating them are presented and compared. Then, the performance of various VA controllers is compared and investigated. Furthermore, the perspectives, necessity, influences, and expectations of the HRI for future robotic systems, are discussed.
1. Introduction
The robot’s cooperation with the human in industrial, service, co-manipulation, and medical applications
[1][2] could enhance the effectiveness of both the human and the robotic system. Collaborative robots are used for humans’ assistance, and this leads to an increase in their capabilities in three issues: the precision, the speed, and the force. Furthermore, the robots can reduce the human operator’s stress or tiredness and therefore improve the working conditions. In the cooperation, the human operator contributes in the following points: the experience, the knowledge for task executing, the intuition, ease of adaptation and learning, and the ease of understanding of the strategies of control
[3][4].
Many robotics applications and varieties of tasks lead to the necessity for developing variable parameter controllers for accomplishing the robotic task. The controllers should be adjusted depending on the human collaborator’s intention as well as the changes of environment (e.g., the payload of the robot). Therefore, friendly robots with humans are performed.
2. Compliance Control (Impedance/Admittance)
Understanding the compliant behavior is not a new problem in robotics. This is relevant when the robot interacts with the environment, particularly if the environment is only and partly known. In this subsection, the impedance control and the admittance control of the robot are presented and discussed. Compliance control (impedance or admittance)
[5][6][7] is always used as a control system so as to implement a dynamic relationship between the robot and human. In admittance control
[8], a good position or velocity controller (trajectory tracking controller) and an external force sensor should be found. The force sensor is not required for the impedance controller when the inertia is not shaped. The robot’s dynamic behavior is adjusted by tuning the virtual damping, inertia, and stiffness instead of independently controlling whether the position or the force. The main important points that compare the impedance and admittance controllers are presented in
Table 1. Furthermore, the concept and the implementation of both controllers is shown in
Figure 1.
Figure 1.
The concept or the implementation of the admittance and impedance controller (
a
) Admittance Control and (
b
) Impedance Control.
Table 1.
Comparison between admittance controller and impedance controller of the robot.
The advantages and properties of impedance and admittance control can be shown in a better way by comparing them with other modes of control such as force control, position control, and hybrid control.
Table 2 presents this comparison depending on the work presented by Song et al.
[14].
Table 2.
Comparison between the different schemes of control. This comparison is done based on ref.
.
The dynamic relationship between the applied forces or torques by the human operator to the robot end-effector and its displacement or velocity is presented using the following equation
[5][6][7],

F
=
M
d
V
˙
a
+
C
d
V
a
where, Va∈R6 represents the velocity in the directions of the Cartesian coordinate system, Md∈R6×6 is defined as the positive definite matrix that represent the virtual inertia. Cd∈R6×6 is defined as the positive definite matrix that represent the virtual damping. F∈R6 is the vector of the applied forces and torques by the human. The term K is the virtual spring and is usually omitted from Equation (1).
Equation (1) can be rewritten in the general form as follows:
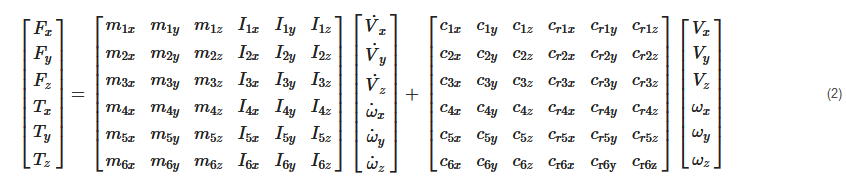
F
x
F
y
F
z
T
x
T
y
T
z
=
m
1
x
m
1
y
m
1
z
I
1
x
I
1
y
I
1
z
m
2
x
m
2
y
m
2
z
I
2
x
I
2
y
I
2
z
m
3
x
m
3
y
m
3
z
I
3
x
I
3
y
I
3
z
m
4
x
m
4
y
m
4
z
I
4
x
I
4
y
I
4
z
m
5
x
m
5
y
m
5
z
I
5
x
I
5
y
I
5
z
m
6
x
m
6
y
m
6
z
I
6
x
I
6
y
I
6
z
V
˙
x
V
˙
y
V
˙
z
ω
˙
x
ω
˙
y
ω
˙
z
+
c
1
x
c
1
y
c
1
z
c
r
1
x