Computational fluid dynamics (CFD) is a powerful numerical analysis approach in solving various engineering and environment problems. It is a simulation technique that uses numerical equations and digital computers for iterative methods to model and to predict various heat, mass, and momentum transfer and fluid flow problems for the optimization of designs. Concentrated solar power (CSP) is a promising technology for harnessing and utilizing a clean and sustainable source of energy. CSP consists of a solar concentrator that collects and intensifies the heat energy from the Sun and a solar receiver that converts the heat generated to produce electrical energy.
1. Introduction
Concentrated solar power (CSP) is a promising technology for harnessing and utilizing a clean and sustainable source of energy. CSP consists of a solar concentrator that collects and intensifies the heat energy from the Sun and a solar receiver that converts the heat generated to produce electrical energy. Despite its recent adoption and acceptance from both the scientific communities and energy investors, solar power still accounts for a very small percentage of total energy use
[1]. The challenge in the optimal design of CSP is to make the technology more cost-efficient and environmentally friendly. With the advancement of numerical modeling software and computational hardware, most of the design problems in CSP technology have recently been solved using computational fluid dynamics (CFD).
Previous reviews have reported the application of CFD in the field of solar energy. Al-Abidi et al.
[2] reviewed the various phase-changing materials (PCMs) in solar photovoltaic (PV) ventilation and the application of CFD in the evaluation of its heat transfer behavior. Liu et al.
[3] recently reviewed the different models and equations used to describe the PCM composites. Yadav and Bhagoria
[4] conducted a review on the assessment of the heat transfer and the fluid flow of numerous solar air heaters using CFD. A solar air heater is a technology that converts solar energy into thermal energy and is usually integrated into solar PV panels. Kasaeian et al.
[5] provided a comprehensive review of previous experimental, analytical, and simulation studies (which include the CFD approach) related to solar chimney applications. Moreover, Nadda et al.
[6] presented a review of studies that investigate the application of jet impingement in increasing solar PV efficiency. The investigation approaches include experimental, CFD, and mathematical modeling. Chen et al.
[7] published a bibliometric review on the development of concentrated solar power technologies but did not mention any use of CFD modeling. Only a few reviews were found which discussed the application of CFD modeling in concentrated solar power technologies and focused on a parabolic trough. As an example, Yılmaz and Mwesigye
[8] performed a comprehensive review on several computational approaches that include CFD in the design of parabolic trough solar collectors. Olia et al.
[9] and Bellos et al.
[10] also presented a review on the application of nanofluids with CFD modeling in the enhancement of the thermal performance of parabolic trough technology. However, for solar dish technology with CFD modeling, no prior bibliometric review has yet been presented.
1.1. Concentrated Solar Power
1.2. Concentrated Solar Power
Concentrated solar power (CSP) is based on the principle of photons coming directly from the Sun being concentrated and collected instead of just being scattered by the Earth’s atmosphere. Direct normal irradiance is the technology’s major energy source
[11][13]. Throughout the years, CSP technology has been proven to have a significant share in the production of renewable sources of sustainable electricity
[12][13][14,15]. The heat energy from the Sun is collected through optical systems or solar concentrators such as highly reflective mirrors and then concentrated in a receiver that contains heat transfer fluid (HTF). The HTF in the receiver is heated, causing a rise in temperature, by absorbing the concentrated radiation. Then, the heated HTF is used for either electricity production through thermal cycles or as a heat source for industrial and commercial applications
[13][15]. There are four main types of CSP technology, namely, parabolic trough collector (PTC), solar tower, parabolic dish (or solar dish), and linear Fresnel reflector (LFR). These four are classified into two groups based on the manner of focusing the solar energy: (1) the line focusing systems, as in the case of PTC and LFR, or (2) the point focusing systems, which are for solar tower and solar dish
[14][16].
Figure 1 shows the illustration of these four types of CSP technologies.
Figure 1. Concentrated solar power technologies.
Concentrated solar power technologies.
1.2. Computational Fluid Dynamics
1.3. Computational Fluid Dynamics
Computational fluid dynamics (CFD) is a powerful numerical analysis approach in solving various engineering and environmental problems. It is a simulation technique that uses numerical equations and digital computers for iterative methods to model and predict various heat, mass, and momentum transfer and fluid flow problems for the optimization of designs
[4]. CFD is an accepted methodology by the scientific and engineering communities to design various types of renewable energy technologies
[15][17]. There are three main stages of the CFD study, as shown in
Figure 2: pre-processing, processing, and post-processing. The pre-processing stage includes geometry creation, material assignment, mesh generation, and assignment of load and boundary conditions. After that, the governing equations such as the Navier–Stokes equation and the set of algorithms are computed and automatically processed by computers. Finally, the obtained results are visualized and interpreted during the post-processing stage.
Figure 2. Computational fluid dynamics stages.
Computational fluid dynamics stages.
2. The CFD Modeling of Solar Dish System
2.1. The Semantic Network of Keywords and Authors
In this section, the contents of published journal articles relevant to the topic of computational fluid dynamics modeling of solar dish are analyzed. A review paper by Hachicha et al.
[14][16] presented content analyses on the numerical models of the other types of CSP, which are central receiver or solar tower and parabolic through concentrator (PTC), but not on the solar dish type of CSP. This
res
earchtudy concentrates on the CFD modeling of the solar dish. Out of 80 published articles yielded from the Scopus database related to CFD modeling of CSP as of 1 December 2020, only 23 of these are specific to the solar dish system.
Figure 3 shows the semantic network of keywords and
researcheauthors of articles specific to the solar dish system with CFD modeling with their corresponding published year. There are three categories identified and subject to content analysis, namely, solar receiver with helical absorber tube, volumetric solar receiver (VSR) with porous absorber, and the rest which did not belong to either of the two were categorized as others. They were classified based on the type of solar receiver used in the solar dish system.
Table 1 shows the extracted data of the solar collector and receiver, which include the collector size and reflectivity, the solar irradiance used, the type of receiver configuration, the size of the receiver cavity (including porosity for volumetric solar receiver), the tube size for tubular absorber, and the receiver material.
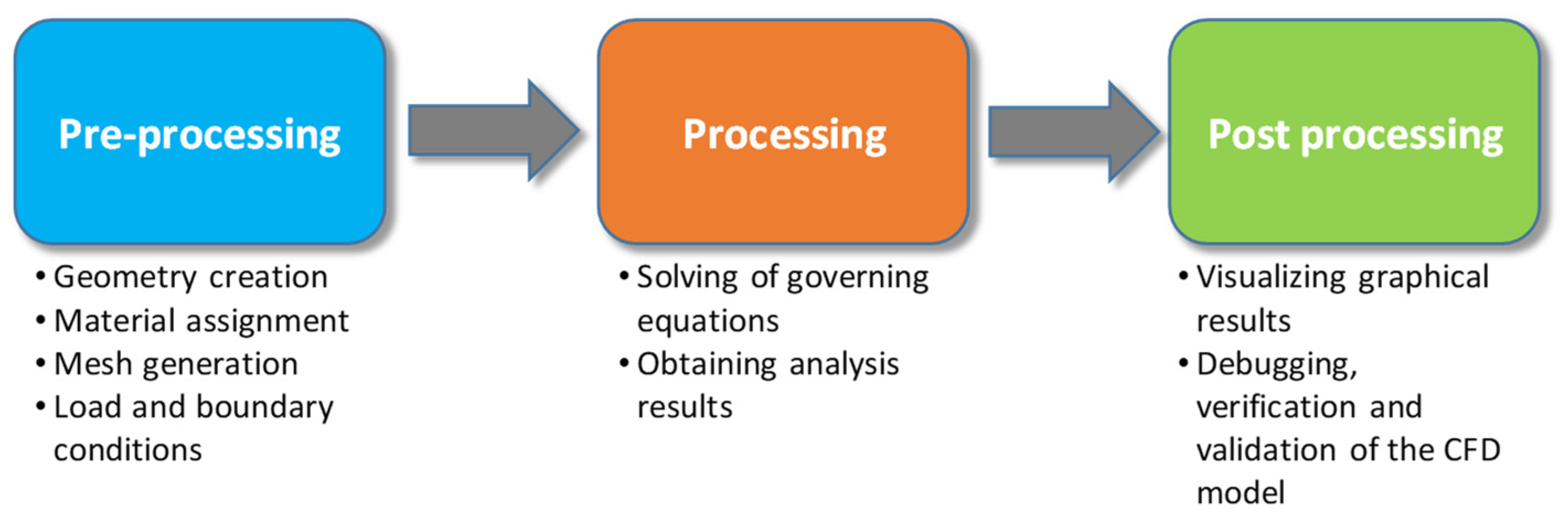
Figure 3. The semantic network of the keywords and authors based on the Scopus search keywords “computational fluid dynamics” and “solar dish” or “parabolic dish” (1 December 2020).
Table 1. Solar dish and receiver data.