It is a well-known fact that to manufacture an automobile tire more than 200 different materials are used, including high-carbon steel wire. In order to withstand the affecting forces, the tire tread is reinforced with steel wire or other products such as ropes or strands. These ropes are called steel cord. Steel cord can be of different constructions. To ensure a good adhesive bond between the rubber of the tire and the steel cord, the cord is either brass-plated or bronzed. The reason brass or bronze is used is because copper, which is a part of these alloys, makes a high-strength chemical composition with sulfur in rubber. For steel cord, the high carbon steel is usually used at 0.70–0.95% C. This amount of carbon ensures the high strength of the steel cord. This kind of high-quality, unalloyed steel has a pearlitic structure which is designed for multi-pass drawing. To ensure the specified technical characteristics, modern metal reinforcing materials for automobile tires, metal cord and bead wire, must withstand, first of all, a high breaking load with a minimum running meter weight. At present, reinforcing materials of the strength range 2800–3200 MPa are increasingly used, the manufacture of which requires high-strength wire. The production of such wire requires the use of a workpiece with high carbon content, changing the drawing regimes, patenting, and other operations. At the same time, it is necessary to achieve a reduction in the cost of wire manufacturing. In this context, the development and implementation of competitive processes for the manufacture of high-quality, high-strength wire as a reinforcing material for automobile tires is an urgent task.
1. Introduction
Over the past, relatively short, time, the range of reinforcing materials for car tires has undergone significant change. Firstly, this can be explained by the increased requirements for automobile tires, which are now more stringent for mileage, weight, imbalance (power non-uniformity), and so on (
Figure 1)
[1]. To ensure the elevated technical characteristics of tires, the modern metal cord and bead wire have to withstand a high breaking load with minimum mass of a running meter (linear density), have a sufficient level of bond strength with rubber, and have an increased resistance to fatigue failure under applied loads. To date, special attention is paid to such indicators as the level of residual torsion, straightness, and deflection arrow, which directly affect the manufacturability of the rubber cord sheets’ (bead rings) technological processing on modern rubber lines.
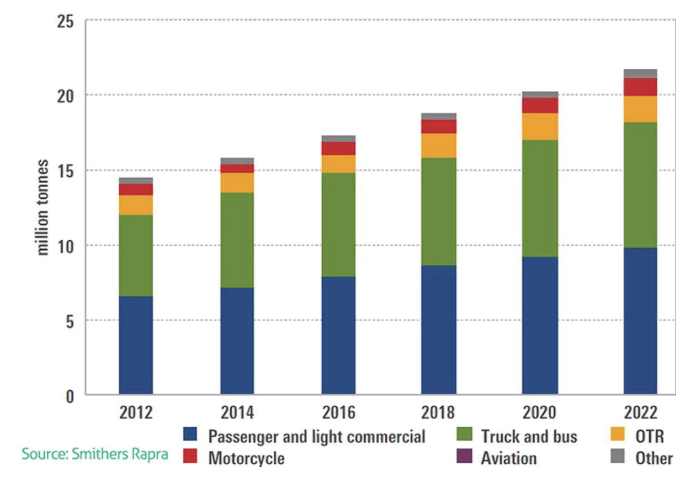
Figure 1. Manufacturing of tires for different applications. Reprinted from ref.
[1].
The idea of increasing the strength of reinforcing materials for automobile tires and decreasing the volume weight was justified in 1979 through the experience of such leading manufacturers of metal cord and bead wire as Bekaert (Belgium), Goodyear, Firestone (USA), Michelin (France), Bridgestone (Japan), and Pirelli» (Italy)
[2]. But the more active process of the substitution of normal-strength reinforced materials for high-strength materials started at the beginning of the 1990s.
While designing new constructions of high-strength steel cord and wires for reinforcing the bead rings of tires, different companies have developed technologies for production wire for high-strength reinforcing materials. The most progressive technologies of manufacturing bead wire were produced in Japan.
At the moment, reinforcing materials of high strength are increasingly used instead of materials with normal tensile (NT) 2400–2800 MPa. They are divided into the following groups: high tensile materials (HT) 2800–3200 MPa and super tensile (ST) materials 3200–3500 MPa. Furthermore, the increase of tensile strength promotes an increased endurance strength of brass-plated wire for metal cord, especially compact beam structures for reinforcing the car tire carcass (
Figure 2)
[3].
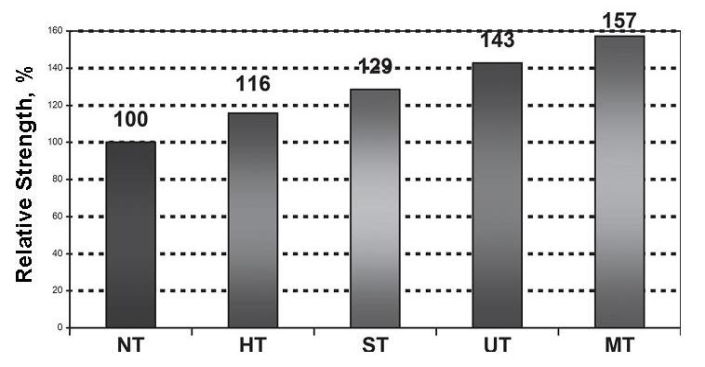
Figure 2. Change of wire strength depending on its group. Reprinted from ref.
[3].
Figure 3 shows the level of tensile strength of materials which are used for metal cord manufacturing
[4].
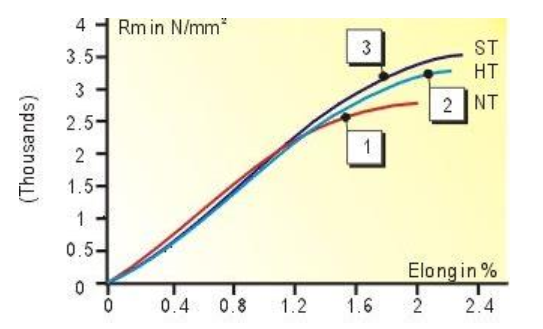
Figure 3. Tensile test data for 0.175 mm diameter filaments for (1) normal products, (2) high tensile grade, and (3) an experimental super-high tensile grade. Reprinted from ref.
[4].
At present time the tendency to increase the tensile strength of steel cord is observed as shown in
Figure 4 [5][6][7][8].
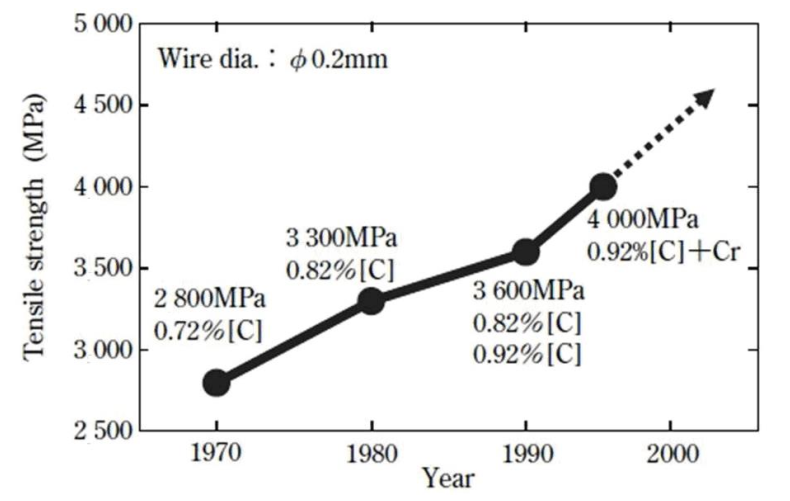
Figure 4. Trend of high tensile strength of steel cord. Reprinted from ref.
[7].
The tensile strength of metal cord with a diameter of 0.20 mm was 2800 MPa in the 1970s, 3300 MPa in the 1980s, and reached a high strength of 3600 MPa in the early 1990s. The increase of speed and the increase in highway transport demanded a raise in the level of tensile strength to higher values
[6][7].
In addition to high tensile strength, the wire for modern reinforcing materials must have a high range of ductile (fatigue) properties. As for metal cord, this condition is necessary to ensure the processability of the double twisting method of high-speed laying. At the level of the HT group (approximately 3000–3200 MPa) thin brass-plated wire with 0.2–0.35 mm in diameter must withstand a certain amount of forward and backward twists. Otherwise, the quality of the finished steel cord (fatigue endurance) and the productivity of the lay process are sharply reduced.
The aim of this paper is to describe the peculiarities of the manufacturing process of the high-carbon steel wire which is used as the reinforcing material for automobile tires. A general description of the technological process is given in
Section 2, which also contains information about special aspects of every technological operation of the manufacturing process. This overview can help the reader to learn about those technological techniques which are necessary in order to produce high-carbon steel wire with the desired exploitation properties. The main tendencies for the improvement of high-carbon steel manufacturing process are denoted in the conclusion.