石墨烯材料在储能、生物材料、光电器件等领域具有多种优异性能和应用。随着纳米技术的进步,石墨烯纳米材料以其高阻隔结构在新型纳米腐蚀涂层领域显示出其优势。此外,聚氨酯还因其优异的耐化学性、机械性能和耐候性而广泛应用于防腐涂料领域。将石墨烯纳米材料与传统聚氨酯(Graphene material has a variety of excellent properties and applications in energy storage, biomaterials, photoelectric devices, and other fields. With the progress of nanotechnology, graphene nanomaterials have shown their advantages in the field of new nano-corrosion coatings with their high barrier structure. In addition, polyurethane is also widely used in the field of anti-corrosion coatings due to its excellent chemical resistance, mechanical properties, and weathering resistance. The preparation of composite coatings by combining graphene nanomaterials with traditional polyurethane (PU)涂料相结合制备复合涂料,为新型防腐涂料的研发开辟了一条新途径。 ) coatings has opened up a new way for the research and development of new anticorrotic coatings.
1.石墨烯材料 Graphene Material
石墨烯是一种碳异质结构。它是具有Graphene is a carbon heterostructure. It is a monolayer of flat plates of carbon atoms with sp2 杂化轨道的单层碳原子平板,密集排列成蜂窝状结构hybridization orbitals, densely packed in a honeycomb structure [1]. Its structure is shown in Figure 1. The graphene material has ultra-high strength with a Young’s modulus [of 8about ]。其结构如图1所示。石墨烯材料具有超高强度,杨氏模量约为1 TPa [[2]. It also has a high thermal conductivity 9of ]。它还具有约about 5300 W/m/K [[3] and an ultra-high surface 10area ]的高导热率和of 2630 m2/g 2[4]. /gGraphene [materials 11have ]的超高表面积。石墨烯材料具有化学惰性many [excellent 12properties ]、热稳定性such [as 13chemical ]、不透气性inertness [[5], 14thermal ]stability 等许多优异性能][6], 和韧性。研究人员利用这些特性尝试将石墨烯材料用于各种应用。其中,保护涂层领域的学者已经开始尝试将石墨烯作为保护涂层体系的一部分,并初步证明石墨烯及其衍生物可以改善聚合物纳米复合材料的物理性能[gas 15impermeability [7], 16and ]。石墨烯纳米复合涂层在材料腐蚀防护方面的应用潜力巨大,将引领新型涂层的发展。
目前,有机防腐涂料中常有还原石墨烯(G)、还原氧化石墨烯(RGO)、GO、官能团改性石墨烯以及基于上述石墨烯的复合材料。GO是石墨烯的氧化物。与纯石墨烯相比,GO具有更多的含氧官能团。此外,GO具有比石墨烯更活泼、易于化学改性、生产成本低、可大批量生产等诸多特性。GO含有四个主要的含氧官能团:羟基、环氧化物、羰基和羧基。此外,它还含有少量的酯类、醚类和酚类[esearchers have used these properties 17to ]。羟基和环氧基团主要分布在try GOto 的片层上,而羰基和羧基基团主要位于 GO 的边缘[use graphene materials 18]。其分子结构如图2所示。由于存在大量含氧基团,GOfor 在水溶液和极性溶剂中可以保持稳定。与石墨烯相比,GO具有更高的化学稳定性,可作为合成石墨烯复合材料的前驱体和支撑载体。其特点是易于功能化,可控性高。
图various 2applications. GOAmong them, scholars in the field of protective coatings have started to experiment with graphene as part of protective coating systems and have initially demonstrated that graphene and its derivatives can improve the physical 的分子结构。
GO和石墨烯的分子结构差异是一把双刃剑,有利也有弊。石墨烯几乎全部由properties of p2杂化碳原子组成,但olymeric nanocomposites [8][9]. GO不仅含有raphene nanocomposite coatingsp2杂化区,还含有大量sp3杂化区。在结构上,GO在其边缘和表面具有含氧基团,但也带来了一定的缺陷。它在力学性能、电性能、导热性能、表面性能等方面与石墨烯完全不同。石墨烯的优异性能归功于其高度共轭的结构。然而,GO have great potential for application in material corrosion protection and will 中的含氧官能团和受损的孔隙严重破坏了这种高度共轭的结构,使得lead GO 的能力不如石墨烯 [to the development 19of ,new 20]。coatings.
GO作为石墨烯重要的含氧衍生物,其结构存在许多晶格缺陷,导致其导电、导热等性能下降。因此,难以将其应用于对其结构完整性有严格要求的纳米复合材料的制备中。然而,GO在制备具有优异力学性能、耐磨性、吸附性能等纳米复合材料方面仍有很大优势。大量含氧基团的存在使GO在水分散性、两亲性、度数等方面具有显着优势。可修饰性以及与聚合物基质的相容性。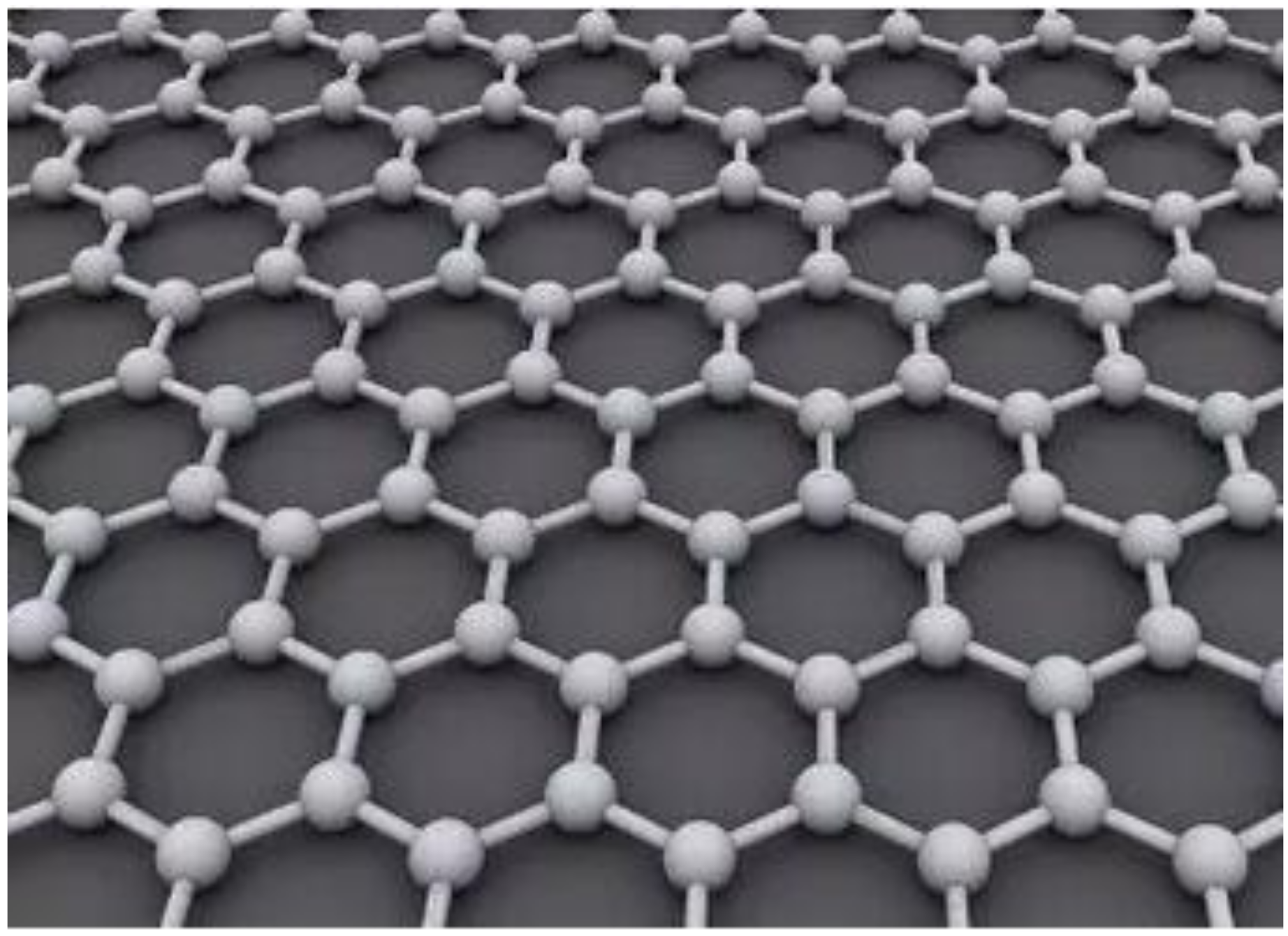
Figure 1. Schematic diagram of graphene structure.
RAt present, reduced graphene (GO是通过还原剂还原、热还原、电化学还原等一系列方法处理GO得到的。在这个过程中,氧化引起的结构损伤在还原GO的过程中得到部分修复,使还原后的GO比GO更坚固。还原GO的过程实际上是修复石墨烯的共轭结构以恢复GO性能的过程[), reduced graphene 21oxide ]。因此,为了克服GO的结构缺陷,研究人员通常将GO作为前驱体材料制备石墨烯基复合材料,通过化学还原制备(RGO。然后,通过与其他基材混合来制备复合材料。), GO的还原过程如图3所示, functional group-modified graphene, and composites based on the above graphene are often applied in organic anti-corrosive coatings. GO还原制备的R is an oxide of graphene. Compared with pure graphene, GO在边缘和表面保留了各种丰富的含氧官能团,这使得它比纯石墨烯材料更容易进行化学改性,从而提高了其与其他基板的相容性。
图 has more oxygen-containing functional 3groups. In addition, GO 的减少。
2.has many properties such as 涂层制备工艺
2.1。激光熔覆技术
激光熔覆技术是将所需合金粉末同时、瞬间熔化和快速凝固,在基体表面非常薄,在基体上形成致密的冶金结合熔覆合金层。激光熔覆由于熔覆层组织精细,提供了广泛的熔覆材料选择,可用于实现高耐腐蚀性、高耐磨性、高硬度等性能要求。激光熔覆的主要生产方法分为预设熔覆法和同时送粉法[being 52]。预置法工艺流程长,工序复杂,镀层均匀性差,对激光功率要求高,结合剂分解容易造成包覆层污染,可能形成气孔、开裂等缺陷。同步送粉的优点是工艺比较简单,可以自动控制,效率高,已在多家企业推广应用。目前,超高速激光熔覆技术非常流行。与普通激光熔覆技术相比,超高速激光熔覆技术形成的组织更精细;但在熔覆过程中,存在未熔颗粒和熔覆层表面光斑热量分布不均等缺陷。为了提高包层的表面质量,需要进行后处理。白等人。[[more 53active ]采用高速激光熔化制备铁基涂层,并对涂层外表面进行强力旋压,结果表明,强旋压涂层比未处理涂层具有更高的耐腐蚀性能。张等人。[than 54graphene, ]easy 制备了石墨烯增强的 Ti6Al4V 复合涂层,石墨烯与 Ti6Al4V 基材具有良好的结合。
2to chemically modify, low production cost, and can be mass produced.2. GO contains four main oxygen-containing functional 电子束熔炼技术
电子束熔覆技术采用高能电子束射入材料;能量瞬间沉积在涂层表面,产生热量使涂层材料熔化,基体部分熔化,基体与涂层结合形成涂层,改善了材料的表面性能。电子束涂层是通过热喷涂、粘结剂、压制等加工方法在涂层材料表面施加;预涂一层合金粉末涂层,厚度从几微米到几毫米不等,具有特殊的物理化学性能;然后用高能量密度电子束照射和扫描涂层材料表面。处理后的涂层瞬间熔化并与基材融合形成新的合金层,从而获得与设计要求相适应的结构和性能。涂层的结构和性能与设计要求相适应,即具有耐磨、耐腐蚀、耐高温氧化的涂层[55groups: ]。王等人。[hydroxyl, 56epoxide, ]carbonyl, 采用电子束熔覆制备单层、双层和三层 WC-40Co 涂层,并分析了涂层的耐磨性和耐腐蚀性,表明涂层的耐磨性随着熔覆层数的增加而增加。并可达到基材耐磨性的11.5倍。单、双层涂层的耐腐蚀性能优于基体,但三层涂层的表面有明显的裂纹损伤。
2.3.and carboxyl groups. In addition, 热喷涂技术
热喷涂技术包括火焰喷涂、等离子喷涂it [contains 57small ]、激光喷涂amounts [of 58esters, ]]等。利用热源将材料在高速气体的帮助下雾化,将其喷射在基材表面并迅速冷却并沉积成具有一定功能的涂层技术。热喷涂技术一般可以制备抗氧化、耐腐蚀、耐磨等涂层。热喷涂技术已广泛应用于航空航天、海洋领域、汽车领域、石油化工等领域。热喷涂的涂层材料可以选择金属、合金、陶瓷和复合材料。热喷涂技术可用于广泛的基材和涂层,对尺寸和形状没有限制,工件变形小。在喷涂过程中,对基材性能的影响很小,涂层厚度控制范围大,涂层厚度通常达到100-400μm,但在零件面积较小的喷涂中,经济性较差。热喷涂制备涂层时,基体表面的清洁度和粗糙度会影响结合性能,因此在喷涂前通常对基体进行表面清洗和粗化处理。穆齐卡·卢卡什等人。[[ethers, 59and ]phenols 使用三种不同的喷涂方法制备金属涂层:双丝电弧喷涂[10]. (TWAS)、火焰喷涂 (FS) 和高速氧气燃料喷涂 (HVOF)。Fhe hydroxyl and epoxy groups arati Tahmineh 等人。[e mainly distributed on the sheet of GO, while the carbonyl and carboxyl groups are mainly located at the edges 60of ]GO 使用大气等离子喷涂和高速氧燃料作为铜-石墨烯纳米片复合涂层,开发了一种多功能和可扩展的表面工程技术。结果表明,与没有涂层的铜表面相比,有涂层的铜表面的耐腐蚀性能提高了89%。
2[11].4. Its 钎焊技术
钎焊是一种材料连接方法,可以在基材和添加材料之间形成紧密的冶金结合。与其他焊接方法相比,钎焊技术更适合在单晶高温合金上制备涂层。钎焊最大的特点是焊接温度低,母材不熔化,减少了再结晶和升温的可能性;钎焊工艺利用熔融钎料的润湿和凝固作用与基材连接,因此强度高于喷涂层[molecular 61structure ]。然而,在钎焊过程中,Cis 和shown Siin 元素在界面处的扩散和反应会使结构不稳定。王等人。[Figure 2. 62]GO 通过调整can Cr 含量来控制 Si 或 C 扩散到基材中的量,改善了单晶高温合金上真空钎焊 NiCr-Cr3C2 涂层的性能。
2.5.remain stable in aqueous solutions and polar solvents 气相沉积技术
气相沉积技术分为物理气相沉积(PVD)和化学气相沉积(CVD),作为一种新型绿色涂层技术,PVD以其硬度高、耐磨性好、摩擦系数低,化学性能稳定,耐热、抗氧化。通过PVD技术保护基体免受腐蚀,涂层必须与腐蚀介质和基体材料有良好的屏蔽和隔离作用,涂层本身必须在腐蚀介质中稳定并保持较低的腐蚀速率。可以通过选择合适的化学成分来提高涂层的耐腐蚀性能,减少生长和制备缺陷以获得致密均匀的涂层结构,增加涂层厚度,63due ]。江等人。[to 64the ]presence 通过 PVD 将纯 Mg 薄膜层压到热浸镀 Zn-55Al-1.6Si 钢上,改变 Ar 气体压力和沉积。结果表明,Mof a large number of oxygen-containing groups. Compared with g膜的叠层增强了耐腐蚀性,这受到Mraphene, GO has hig膜厚度的显着影响,尤其是横截面的2-10倍。
化学气相沉积her chemical stability and can be used as a precursor and (CVD)support 是一种将各种气体引入反应室的技术,在反应室中,在基板表面发生化学反应,并将所得的固体产物沉积在表面上以形成薄膜。这些气体包括可形成薄膜元件的气态反应物或液态反应物蒸气,以及其他反应气体。为了通过carrier CVDfor 获得特定的薄膜,需要选择合适的反应方法并确定温度、气体成分、浓度和压力等参数 [the synthesis 65of ]。纳迪姆·阿米尔等人。[graphene 66]composites. 在It 1200 °C 的 CVD 设备中,通过硼粉和氨气的化学反应,在低碳钢基材上沉积氮化硼基涂层。结果表明,氮化硼纳米片涂层的耐盐性比裸露的低碳钢高六倍。萨米拉·纳格迪等人。[is characterized by easy functionalization 67and ]high 在大气压下对钼和铂进行了石墨烯的化学气相沉积,结果表明石墨烯表现出良好的保护性能,可用作腐蚀屏障。controllability.
Figure 2. Molecular structure of GO.
The molecular structure differences between GO and graphene are a double-edged sword, with both advantages and disadvantages. Graphene consists almost entirely of sp2 hybridized carbon atoms, but GO contains not only sp2 hybridized regions, but also a large number of sp3 hybridized regions. Structurally, GO has oxygen-containing groups on its edges and surfaces, but it also brings certain defects. It is completely different from graphene in terms of mechanical properties, electrical properties, thermal conductivity, and surface properties. The excellent properties of graphene are due to its highly conjugated structure. However, the oxygen-containing functional groups and damaged pores in GO severely disrupt this highly conjugated structure, making GO less capable than graphene [12][13].
As an important oxygen-containing derivative of graphene, GO has many lattice defects in its structure, leading to degradation of its electrical conductivity, thermal conductivity, and other properties. Therefore, it is difficult to apply it in the preparation of nanocomposites that have strict requirements for its structural integrity. However, GO still has great advantages in the preparation of nanocomposites with excellent mechanical properties, wear resistance, adsorption properties, etc. The presence of a large number of oxygen-containing groups gives GO a significant advantage in terms of water dispersibility, amphiphilicity, degree of modifiability, and compatibility with a polymer matrix.
RGO is obtained by treating GO using a series of methods such as reductant reduction, thermal reduction, and electrochemical reduction. In this process, the structural damage caused by oxidation is partially repaired during the reduction of GO, making the reduced GO stronger than GO. The process of reducing GO is actually a process of repairing the conjugated structure of graphene to restore the properties of GO [14]. Therefore, in order to overcome the structural defects of GO, researchers usually use GO as a precursor material in the preparation of graphene-based composites and prepare RGO by chemical reduction. Then, the composites are prepared by mixing with other substrates. The reduction process of GO is shown in Figure 3. The RGO prepared by GO reduction retains various rich oxygen-containing functional groups at the edges and surfaces, which makes it easier to be chemically modified than pure graphene materials, thus improving its compatibility with other substrates.
Figure 3. Reduction of GO.
2. Coating Preparation Processes
2.1. Laser Cladding Technology
Laser cladding technology is the simultaneous, instantaneous melting and rapid solidification of the required alloy powder with the very thin surface of the substrate, forming a dense metallurgical bonded clad alloy layer on the substrate. Laser cladding offers a wide choice of cladding materials due to the fine organization of the cladding layer, which can be used to achieve high corrosion resistance, high wear resistance, high hardness, and other performance requirements. The main production methods of laser cladding are divided into the pre-set cladding method and the simultaneous powder feeding method [15]. The pre-setting method has a long process flow, complex procedures, poor coating uniformity, high laser power requirements, and the decomposition of the bonding agent can easily cause contamination of the clad layer, which may form defects such as porosity and cracking. The advantage of synchronous powder feeding is that the process is relatively simple and can be controlled automatically with high efficiency, which has been popularized and applied in many enterprises. Currently, ultra-high speed laser cladding technology is very popular. Compared with ordinary laser cladding technology, ultra-high speed laser cladding technology forms finer tissues; however, there are defects caused by unmelted particles and uneven heat distribution of the spot on the surface of the clad layer during the cladding process. To improve the surface quality of the cladding layer, post-treatment is required. Bai et al. [16] prepared iron-based coatings by high-speed laser melting and strongly spun the outer surface of the coatings, and the results showed that the strongly spun coatings exhibited higher corrosion resistance than the untreated coatings. Zhang et al. [17] prepared graphene-reinforced Ti6Al4V composite coatings with good bonding of graphene to the Ti6Al4V substrate.
2.2. Electron Beam Melting Technology
Electron beam cladding technology uses high energy electron beam into the material; the energy is instantly deposited on the surface of the coating, generating heat to make the coating material melt, the substrate partially melts, and the substrate and coating combine to form a coating, improving the surface properties of the material. Electron beam coating is applied to the surface of the coating material by thermal spraying, binder, press, and other processing methods; pre-coating a layer of alloy powder coating with thickness ranging from a few microns to a few millimeters and with special physicochemical properties; and then using high energy density electron beam to irradiate and scan the surface of the coating material. The treated coating instantly melts and fuses with the substrate to form a new alloy layer, thus obtaining the structure and properties compatible with the design requirements. The structure and properties of the coating are compatible with the design requirements, i.e., a coating with wear resistance, corrosion resistance, and high temperature oxidation resistance [18]. Wang et al. [19] prepared single-, double-, and triple-layer WC-40Co coatings by electron beam cladding and analyzed the wear resistance and corrosion resistance of the coatings, which showed that the wear resistance of the coatings increased with the number of cladding layers and could reach 11.5 times the wear resistance of the substrate. The corrosion resistance of the single- and double-layer coatings was better than that of the substrate, however, the surface of the triple-layer coating was significantly damaged by cracks.
2.3. Thermal Spraying Technology
Thermal spraying technology includes flame spraying, plasma spraying [20], laser spraying [21], etc. The use of a heat source to atomize the material with the help of high-speed gas will be sprayed on the surface of the substrate and quickly cooled and deposited into a certain function of the coating technology. Thermal spraying technology can generally prepare anti-oxidation, corrosion resistance, wear resistance, and other coatings. Thermal spraying technology has been widely used in aerospace, marine field, automotive field, petrochemical field, etc. The coating materials for thermal spraying can be chosen from metals, alloys, ceramics, and composites. Thermal spraying technology can be used for a wide range of substrates and coatings, with no restrictions on size and shape and little deformation of the workpiece. In the spraying process, the influence on the performance of the substrate is small, the coating thickness control range is large, and the coating thickness usually reaches 100–400 μm, but in the spraying of smaller areas of the parts, the economy is poor. When preparing coatings by thermal spraying, the cleanliness and roughness of the substrate surface affects the bonding properties, so the substrate is usually subjected to surface cleaning and roughening processes before spraying. Muzika Lukáš et al. [22] prepared metal coatings using three different spraying methods: twin-wire arc spraying (TWAS), flame spraying (FS), and high-speed oxygen fuel spraying (HVOF). Forati Tahmineh et al. [23] used atmospheric plasma spraying and high speed oxygen fuel as a Cu-graphene nanosheet composite coating to develop a multifunctional and scalable surface engineering technique. The results showed that the corrosion resistance of Cu with the coating was improved by 89% compared to the Cu surface without the coating.
2.4. Brazing Technology
Brazing is a material joining method that enables a tight metallurgical bond to be formed between the base material and the additive material. Compared with other welding methods, brazing technology is more suitable for the preparation of coatings on single crystal high temperature alloys. The most important feature of brazing is that the welding temperature is low and the base material does not melt, reducing the possibility of recrystallization and warming; the brazing process uses the wetting and solidifying effect of the molten brazing material to connect with the base material, so the strength is higher than that of spray coatings [24]. However, the diffusion and reaction of C and Si elements at the interface during the brazing process can destabilize the structure. Wang et al. [25] improved the performance of vacuum brazed NiCr-Cr3C2 coatings on single crystal high temperature alloys by adjusting the Cr content to control the amount of Si or C diffusion into the base material.
2.5. Vapor Deposition Technology
Vapor deposition technology is divided into physical vapor deposition (PVD) and chemical vapor deposition (CVD), and as a new green coating technology, PVD is widely used in mechanical, electronic, and optical industries because of its high hardness, good wear resistance, low friction coefficient, stable chemical properties, and heat and oxidation resistance. To protect the substrate against corrosion by PVD technology, the coating must be well shielded and isolated from the corrosive medium and the substrate material, and the coating itself must be stable in the corrosive medium and maintain a low corrosion rate. The corrosion resistance of coatings can be improved by selecting the appropriate chemical composition, reducing the growth and preparation defects to obtain a dense and uniform coating structure, increasing the coating thickness, using a multilayer film structure, pre-treating the coating, and adding a transition layer [26]. Jiang et al. [27] laminated pure Mg films onto hot-dip coated Zn-55Al-1.6Si steel by PVD, varying the Ar gas pressure and deposition. It was found that the lamination of Mg film enhanced the corrosion resistance, which was significantly affected by the thickness of Mg film, especially for the cross section by a factor of 2–10.
Chemical vapor deposition (CVD) is a technique in which various gases are introduced into a reaction chamber where a chemical reaction occurs on the surface of a substrate and the resulting solid products are deposited on the surface to form a thin film. These gases include gaseous reactants or vapors of liquid reactants that can form thin film elements, as well as other reaction gases. In order to obtain specific thin films by CVD, it is necessary to select the appropriate reaction method and to determine parameters such as temperature, gas composition, concentration, and pressure [28]. Nadeem Aamir et al. [29] deposited boron nitride-based coatings on mild steel substrates by chemical reaction of boron powder and ammonia gas in a CVD apparatus at 1200 °C. It was shown that the salt resistance of the boron nitride nanosheet coating was six times higher than that of bare mild steel. Samira Naghdi et al. [30] performed chemical vapor deposition of graphene on molybdenum and platinum at atmospheric pressure and showed that graphene exhibited good protective properties and could be used as a corrosion barrier.
2.6. 表面复合离子处理技术
2.6. Surface Composite Ion Treatment Technology
Surface composite ion treatment is a surface treatment process that combines two or more surface technologies to prepare composite coatings, film layers, and composite modified coatings. It includes ion implantation compounded with coating technology, laser or electron beam compounded with vapor deposition technology, and plasma spray compounded with laser technology. In ion-beam-assisted deposition processes, ion bombardment can increase the density of the film, eliminate or reduce the inherent stresses in the film layer, and improve the properties of the film layer, and a wide transition zone between the film atoms and the substrate atoms can be obtained by ion bombardment, which is extremely beneficial for improving the film/substrate bond. Xu et al. [31] deposited in situ graphene/silicon carbide composite coatings with <111> orientation by laser chemical vapor deposition using hexamethylsilane as a precursor. The study of the growth mechanism showed that the photolytic effect of the laser played an important role in the deposition process.
表面复合离子处理是结合两种或多种表面技术制备复合涂层、膜层和复合改性涂层的表面处理工艺。包括离子注入结合镀膜技术、激光或电子束结合气相沉积技术、等离子喷涂结合激光技术。在离子束辅助沉积工艺中,离子轰击可以增加薄膜的密度,消除或降低薄膜层的固有应力,改善薄膜层的性能,使薄膜原子与薄膜之间的过渡区变宽。可以通过离子轰击获得衬底原子,这对于改善薄膜/衬底的结合非常有利。徐等人。[ 68]使用六甲基硅烷作为前体,通过激光化学气相沉积原位沉积具有<111>取向的石墨烯/碳化硅复合涂层。生长机理的研究表明,激光的光解效应在沉积过程中起重要作用。The coating preparation process is not only related to the characteristics of the coating itself, but also influenced by a variety of factors, such as the type of substrate, the performance of the coating, the type of application environment, and the functional requirements of the coating. With the advancement of science and technology, the coating preparation process and technology are developing rapidly in the direction of intelligence, efficiency and advancement. All the preparation processes introduced above can prepare anti-corrosion coatings, and at present, thermal spray technology, laser cladding technology, and vapor deposition technology are more widely used.
涂层的制备工艺不仅与涂层本身的特性有关,还受多种因素的影响,如基材的类型、涂层的性能、应用环境的类型、涂层的功能要求等。涂层。随着科学技术的进步,涂料制备工艺和技术正朝着智能化、高效化、先进化的方向快速发展。以上介绍的所有制备工艺都可以制备防腐涂层,目前应用比较广泛的是热喷涂技术、激光熔覆技术和气相沉积技术。
三、结论与展望3. Conclusions and Prospect
石墨烯材料在涂料领域具有巨大的应用潜力。GO作为一种纳米填料,可以有效提高PU涂层的力学性能和防腐性能。由于GO表面存在大量含氧官能团,可直接作为纳米填料添加到PU基体中。然而,由于它们的强相互作用,复合材料的性能会降低。因此,GO的修改是必不可少的。改性GO能与PU基体发生更好的反应,在PU基体中具有更好的分散性,因此复合材料的性能会显着提高。GO在PU涂料中的应用已经取得了长足的进步和发展,但在GO的应用方面仍有大量的研究工作要做。Graphene materials have great application potential in the coating field. GO, as a nano-filler, can effectively improve the mechanical properties and anti-corrosion properties of PU coatings. Due to the large number of oxygen-containing functional groups on the surface of GO, it can be directly added to the PU matrix as a nano-filler. However, the performance of the composite will be reduced because of their strong interaction. Therefore, modification of GO is essential. Modified GO can react better with the PU matrix and have better dispersion in the PU matrix, so the performance of the composite material will be significantly improved. Considerable progress and development has been made in the application of GO in PU coatings, but there is still a lot of research that needs to be done on the application of GO.